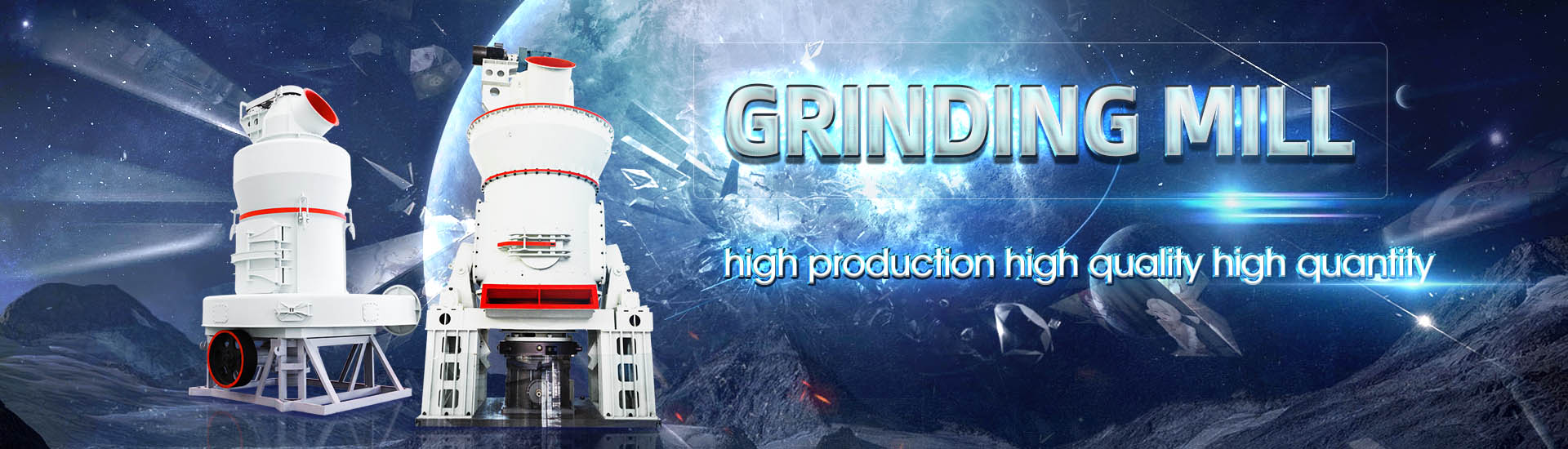
Mine alkaline furnace lining material powder making process equipment
.jpg)
Induction Furnace Melting SpringerLink
2024年1月1日 Alkaline furnace lining is made of magnesia with magnesium oxide content more than 85%, used for smelting of special steel and nickelbased alloy Generally, the crucible is made of tamped lining, and refractory materials with appropriate particle size ratio are 2017年3月14日 To do it right, here are five primary tips for maximum furnace lining efficiency: 1 Use IR thermography to inspect the existing lining — Ensuring lining quality is critical to protecting the structure from excess heat and Ensuring Furnace Lining Efficiency Foundry 2017年6月3日 Hightemperature metallic materials or alloys used in process heating equipment (furnaces, heaters, ovens, kilns, etc) have significant effect on thermal efficiency, productivity and operating cost of the equipment These materials are used in burners, electrical heating Materials Selection Considerations for Thermal Process 2022年3月1日 The design of lightweight wear linings is crucial in terms of the energy and resource efficiency of industrial furnaces and quality of final products This review aims to present a systematic overview of the design, fabrication, properties, and application of lightweight wear Design, fabrication and properties of lightweight wear lining

Innovative Refractory Technology for Coreless Induction
2023年6月22日 This paper will discuss a completely new generation of refractories and address care of structural components, installation, sintering and optimal operation of coreless induction furnaces to significantly improve the lining life This reduces total melting costs while providing Capital Refractories offer a full range of coreless induction furnace linings, topping and patching products for a wide range of steels and high temperature alloys A range of air setting, chemically bonded high strength materials and dry Coreless Induction Furnace Linings Capital 2023年10月5日 Acid furnace lining is made of quartz sand with silica content more than 98% It has low melting point and poor stability, usually in melting and holding of nonferrous metals and cast iron Alkaline furnace lining is made of magnesia with magnesium oxide content more Induction Furnace Melting SpringerThere are several different types of mechanical furnace which are used in the mining industry worldwide Reverbatory furnaces isolate the material from coming into contact with the fuel, but not the combustion gasesUsing Furnaces to Improve Mining Processes
.jpg)
Induction Furnace Melting SpringerLink
2024年1月1日 Induction furnace melting is a process of melting metal by using electromagnetic induction to produce eddy current heating in metal materials in induction furnace, also called induction melting It has low melting point and poor stability, usually in melting and holding of nonferrous metals and cast iron Alkaline furnace lining is made of 2022年7月14日 effects Article [20] is relatively comprehensive, but it eval uates the application of alkaliactivated cementitious materials in mortar and concrete rather than filling Therefore, it is very necessary to make a systematic and comprehensive summary of the research on alkaliactivated cementing materials for mine filling in recent yearsResearch and Application Status and Development 2020年5月21日 Whether from the shape of the material or the thermal insulation performance of the lining, they are essentially made of carbon material lining A new furnace lining, the use and maintenance of good furnace lining life can be as long as more than 10 years, the use and maintenance is not good, furnace lining life less than a year or even just a Analysis of 6 causes of lining damage in hot furnace of 2023年2月15日 The whole lime production line includes: mining, crushing, screening and calcinating Mining highquality limestone First, limestone is quarried from mines with the help of big machines and blasting In this stage, limestone with big blocks which are not suitable for putting in a kilnLime Production Process and Required Equipment Fote
.jpg)
(PDF) REACTOR SYSTEMS SELECTION, SIZING AND
2020年3月26日 of Process Equipment Design REACTOR SYSTEMS SELECTION, SIZING AND TROUBLESHOOTING (ENGINEERING DESIGN GUIDELINES) Page 14 of 86 Rev: 01 May 2014 Induction furnace melting is a process of melting metal by using electromagnetic induction to produce eddy current heating in metal materials in induction furnace, also called induction melting It has low melting point and poor stability, usually in melting and holding of nonferrous metals and cast iron Alkaline furnace lining is made of Induction Furnace Melting SpringerLink2017年5月30日 4 Select the right material for furnace rebuilds Some repairs identified by infrared thermology scanning can be too large to address online, and instead, the unit must be shut down for a furnace reline or process heater reline In this scenario, it is important to select the right refractory materials to facilitate a successful furnace rebuildEnsuring Effective Furnace Lining Efficiency Thermal Processing2024年2月19日 The third phase of the smelting process of traditional Electric arc furnace steel making, refining and alloying in one furnace, including the melting period, oxidation period and reduction period In the furnace, the melting of scrap steel, dephosphorization, decarburization, degassing, etc of the molten steel must be completed Remove inclusions and raise Traditional Electric arc furnace steelmaking smelting process
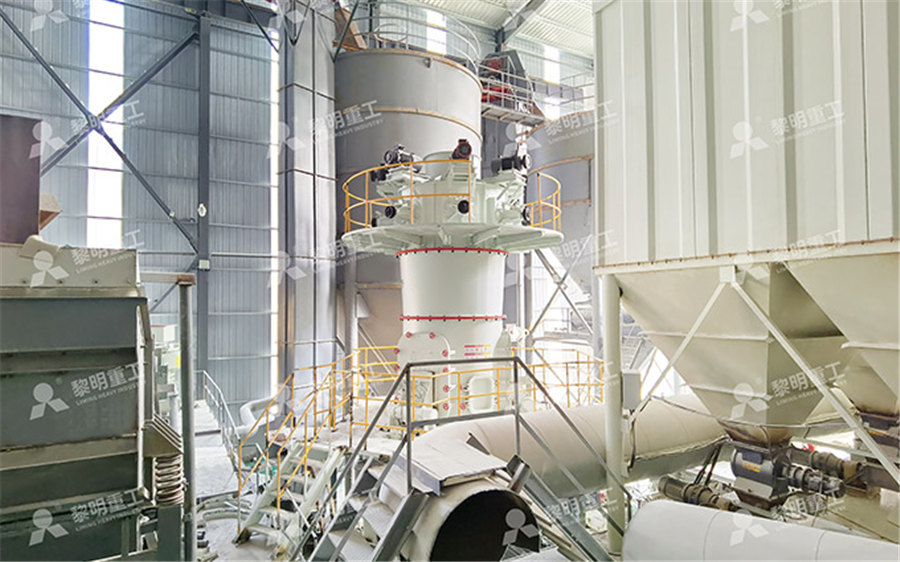
(PDF) Alkaline carbonates in blast furnace process
2014年10月1日 Alkalis (K and Na compounds, Kobayashi et al, 1979) enter in the blast furnace with the charge materials (should be limited to 2530 kg alkalis/ton pig iron, Kurunov et al, 2009 or 2585 kg 2024年11月22日 How to make fine aluminum powder Centrifugal atomizing for aluminum Powder Centrifugal atomizing metal powder making machine is an important machinery for manufacturing metal powder, which is playing more and more part because of the controllability of the size as well as the shape of the powder and its low production cost Centrifugal atomizing metal powder making machine cdocast2022年7月8日 Alkaline furnace lining materials are dry ramming materials made of fused or highpurity magnesia, powder, aluminum magnesium spinel powder and sintering agent Its particle size distribution conforms to the theory of How to choose the refractory materials for the 2022年11月29日 5 New process and new materials of furnace lining materials ① In the traditional lining materials, ultrafine powder (mostly in a few microns) can improve the corrosion resistance and thermal shock stability of lining What are the types of lining materials for
.jpg)
Metal powder manufacturing equipment
Complete metal powder manufacturing with sintering Metal powder blends are delivered for fabrication in the form of briquettes Blend the alloys and materials in a mixer to ensure a uniform particle distribution Then compact the mixture at 2023年6月22日 furnace: To achieve consistent lining life of coreless induction furnaces, these play very important roles • ATop/Bottom Blocks: Need to check every time before lining to make sure it has tightened properly and in good shape/condition Bad Condition of both top and bottom blocks (Reference Figure 2) directly affects the performance of Innovative Refractory Technology for Coreless Induction Fig 1 Installed refractory lining of a coreless induction furnace The characteristics of the lining material needed for consistent lining life include (i) thermal characteristics which means that it has to withstand the stresses developed by thermal cycles during the furnace operation, (ii) chemically inert to metal being melted, (iii) structural strength under operating conditions, (iv) high Induction Furnace Refractory Lining with Silica Ramming Mass2022年3月1日 The design of lightweight wear linings is crucial in terms of the energy and resource efficiency of industrial furnaces and quality of final products This review aims to present a systematic overview of the design, fabrication, properties, and application of lightweight wear lining refractoriesDesign, fabrication and properties of lightweight wear lining
.jpg)
The processing and application of talc ALPA Powder Equipment
2021年7月9日 Talc is finally applied in powder form, therefore, fine grinding and ultrafine grinding are one of the necessary processing techniques for talc Talc has a Mohs hardness of 1, which is naturally crushable and has good grindability At present, the processing of ultrafine talc powder mainly adopts a dry processSmelting Process 1) The Furnace Lining Materials Required Shall Be Selected According to the Type of Smelting Steel Some steel grades are only suitable for smelting in alkaline furnaces When smelting high manganese steel grades and alloys in an acid furnace, (MnO) will combine with SiO2 in the furnace lining to form a low melting point Induction Furnace Steel Making Hani Metallurgy2023年10月6日 The smelting process of blast furnace is carried out in the shaft furnace of a closed countercurrent reactor and heat exchanger The complex physical changes and chemical reactions are completed in the process of the countercurrent movement of the charge and gas in which the raw materials containing iron oxide (sinter, pellets, etc), coke, slag flux (limestone) Blast Furnace Ironmaking SpringerLinkQueen Elizabeth I knows this well Just think she used so many cosmetics and makeup containing toxic materials, especially leadbased face powder, that she even died from them Today fortunately, you no longer need lead to make face powder Simply mix pigments, fillers, dry and wet binders, and compress the mixture using a powder compacting pressFace powder making equipment Making
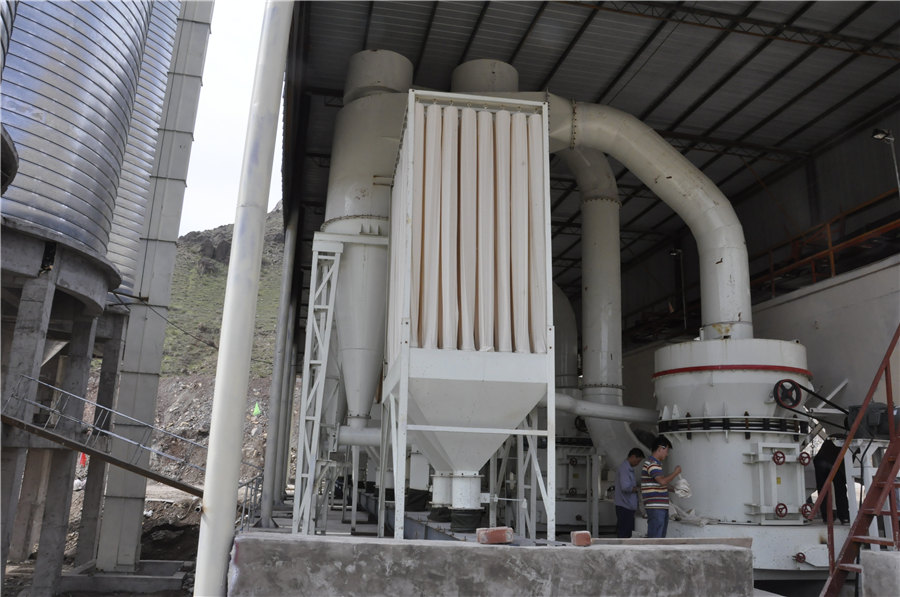
Aluminium melting furnace lining
2019年12月27日 chemical reactions with aluminium lining material, mechanical damage during cleaning oven to remove slag from the walls and hearth of the furnace and; thermal shock, that arise when loading charge The lining in the 2017年6月3日 Process Equipment Introduction Hightemperature metallic materials or alloys used in process heating equipment (furnaces, heaters, ovens, kilns, etc) have significant effect on thermal efficiency, productivity and operating cost of the equipment These materials are used inMaterials Selection Considerations for Thermal Process 2023年1月6日 Where T n is the thickness of the nth layer, V p is the Pwave speed, α is the thermal correction factor, β is the shape correction factor, and f is the frequency of the reflection Up until recently, this is the extent to which AUE signals were collected are processed However, recent advancements in data collection, data processing, and information visualization have Imaging the Remaining Refractory Lining in Operating FurnacesInduction furnace lining procedure determines the quality of the furnace and the efficiency of the production process The induction furnace lining plays the role of containing the molten metal, isolating the contact between the molten metal and the outer structure of the lining such as the coil, and protecting the furnace body during the work of the induction furnaceInduction Furnace Lining Procedure – Melting Hani
.jpg)
Powder Manufacturing Equipment Making
Powder processing technology conditions these primary materials to create a vast range of products, from chemicals and foods to pharmaceuticals and ceramics Which powder technology do you need? Select your production process2022年5月23日 The ratio of the precursor to solid SS was kept constant at 9:1 [37], where 0 to 50 wt% BFS was substituted by the bioleached SMTs in an incremental value of 10 wt%Based on the study of Luukkonen et al [38], the optimal water/binder and sand/binder weight ratios were fixed at 035 and 2, respectivelyA detailed mix design is given in Table 2, in which BFS, Incorporation of bioleached sulfidic mine tailings in onepart alkali 2020年10月19日 According to the raw materials and smelting furnace need different acid and alkaline divided into lining, our factory is using acidic lining Play lining, is to use the material such as quartz sand, the furnace wall do a layer isolation smelting furnace materials and within the induction coils, protect the induction coilsHow to improve the induction furnace lining lifeThe nearly 5,000 known minerals on earth share some characteristics to be classified as minerals – they are inorganic, solid, naturally occurring elements and have a particular chemical formula and an ordered internal geometric structureMineral Processing Equipment Making

Mining Mineral Processing Equipment FEECO
6 天之前 Mining and Mineral Processing Capabilities Mining and Mineral Processing Capabilities Brochures MinExpo 2016 Activated Carbon in Gold Cyanidation Recovery FEECO Mining Capabilities Mining Minerals Industry Mineral Processing Mineral Processing Equipment, Rotary Drum FEECO Mining Capabilities Brochure2013年12月1日 For the production of suitable sized feed materials (40+15mm) for Blast Furnace, during comminution process (crushing, grinding and screening) of the Run of Mines (ROM) generates a lot of fines Technological Changes in Blast Furnace Iron Making in India 2024年1月1日 Induction furnace melting is a process of melting metal by using electromagnetic induction to produce eddy current heating in metal materials in induction furnace, also called induction melting It has low melting point and poor stability, usually in melting and holding of nonferrous metals and cast iron Alkaline furnace lining is made of Induction Furnace Melting SpringerLink2022年7月14日 effects Article [20] is relatively comprehensive, but it eval uates the application of alkaliactivated cementitious materials in mortar and concrete rather than filling Therefore, it is very necessary to make a systematic and comprehensive summary of the research on alkaliactivated cementing materials for mine filling in recent yearsResearch and Application Status and Development
.jpg)
Analysis of 6 causes of lining damage in hot furnace of
2020年5月21日 Whether from the shape of the material or the thermal insulation performance of the lining, they are essentially made of carbon material lining A new furnace lining, the use and maintenance of good furnace lining life can be as long as more than 10 years, the use and maintenance is not good, furnace lining life less than a year or even just a 2023年2月15日 The whole lime production line includes: mining, crushing, screening and calcinating Mining highquality limestone First, limestone is quarried from mines with the help of big machines and blasting In this stage, limestone with big blocks which are not suitable for putting in a kilnLime Production Process and Required Equipment Fote 2020年3月26日 of Process Equipment Design REACTOR SYSTEMS SELECTION, SIZING AND TROUBLESHOOTING (ENGINEERING DESIGN GUIDELINES) Page 14 of 86 Rev: 01 May 2014 (PDF) REACTOR SYSTEMS SELECTION, SIZING ANDInduction furnace melting is a process of melting metal by using electromagnetic induction to produce eddy current heating in metal materials in induction furnace, also called induction melting It has low melting point and poor stability, usually in melting and holding of nonferrous metals and cast iron Alkaline furnace lining is made of Induction Furnace Melting SpringerLink
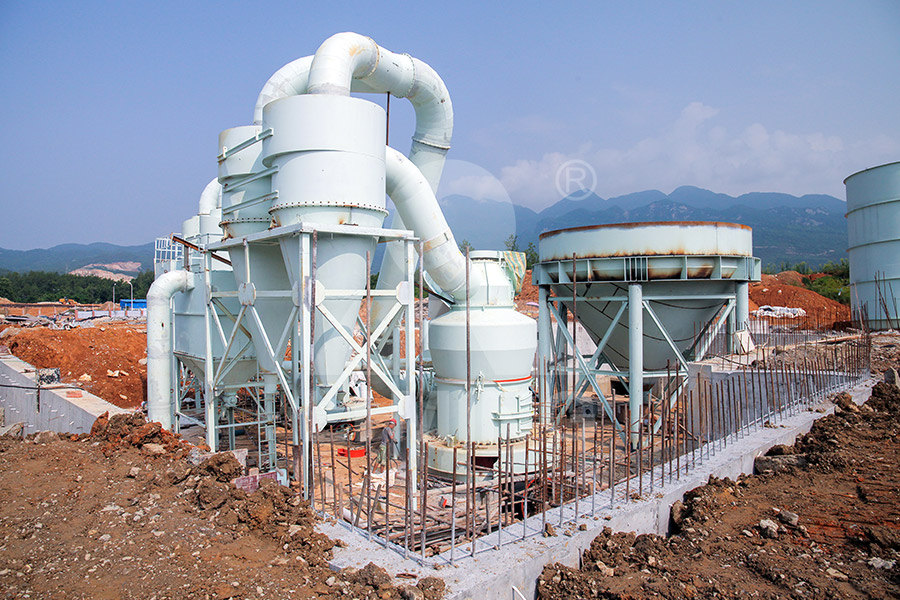
Ensuring Effective Furnace Lining Efficiency Thermal Processing
2017年5月30日 4 Select the right material for furnace rebuilds Some repairs identified by infrared thermology scanning can be too large to address online, and instead, the unit must be shut down for a furnace reline or process heater reline In this scenario, it is important to select the right refractory materials to facilitate a successful furnace rebuild2024年2月19日 The third phase of the smelting process of traditional Electric arc furnace steel making, refining and alloying in one furnace, including the melting period, oxidation period and reduction period In the furnace, the melting of scrap steel, dephosphorization, decarburization, degassing, etc of the molten steel must be completed Remove inclusions and raise Traditional Electric arc furnace steelmaking smelting process2014年10月1日 Alkalis (K and Na compounds, Kobayashi et al, 1979) enter in the blast furnace with the charge materials (should be limited to 2530 kg alkalis/ton pig iron, Kurunov et al, 2009 or 2585 kg (PDF) Alkaline carbonates in blast furnace process2024年11月22日 How to make fine aluminum powder Centrifugal atomizing for aluminum Powder Centrifugal atomizing metal powder making machine is an important machinery for manufacturing metal powder, which is playing more and more part because of the controllability of the size as well as the shape of the powder and its low production cost Centrifugal atomizing metal powder making machine cdocast