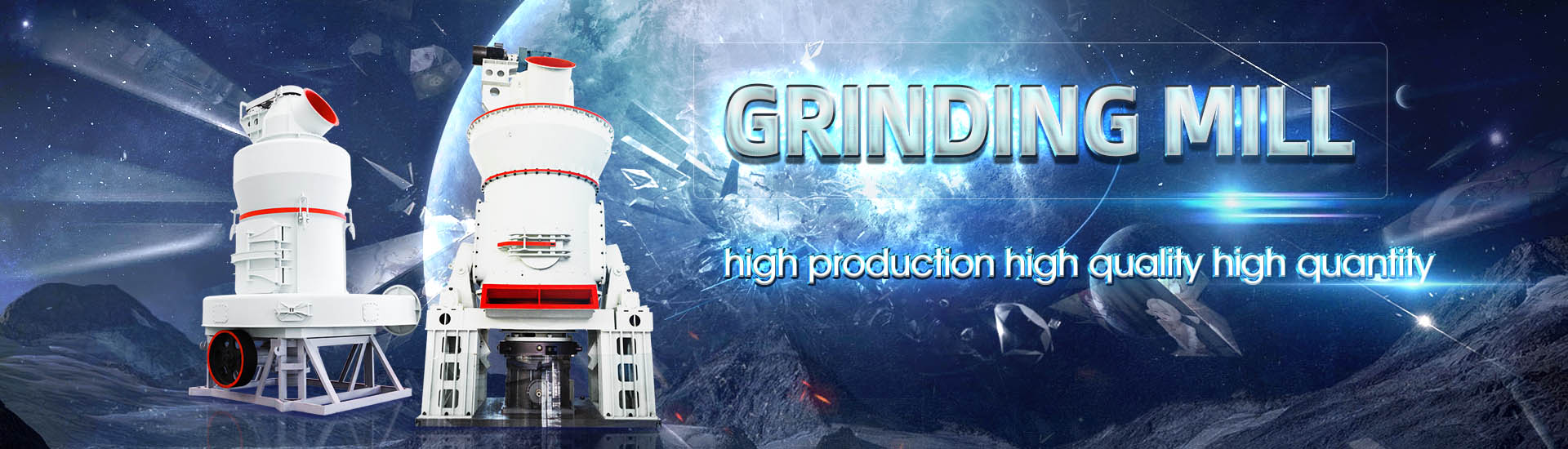
The crushing method used by the crocodile ore mill is
.jpg)
(PDF) SIZE REDUCTION BY CRUSHING
2017年3月4日 Crushing is the first step of mineral processing where the ore/rocks from the mine site is fed into the mechanical equipment in order to reduce the size of masses for subsequent usage by2023年7月20日 Moist grinding, a special grinding method, is used to prepare pellets for smelting According to the grinding medium features, ore grinding is mainly classified into ball grinding Ore Grinding SpringerLink2023年12月1日 In comparison to pressure crushing, the principle used here is impact crushing In this process, the crushed material is picked up by a fast moving rotor, greatly accelerated SIZE REDUCTION BY CRUSHING METHODS By2017年3月4日 Size Reduction is mainly done through crushers and mills Crushing and grinding are the two primary comminution processes Crushing is normally carried out on the "runofm ine" ore(PDF) SIZE REDUCTION BY GRINDING METHODS
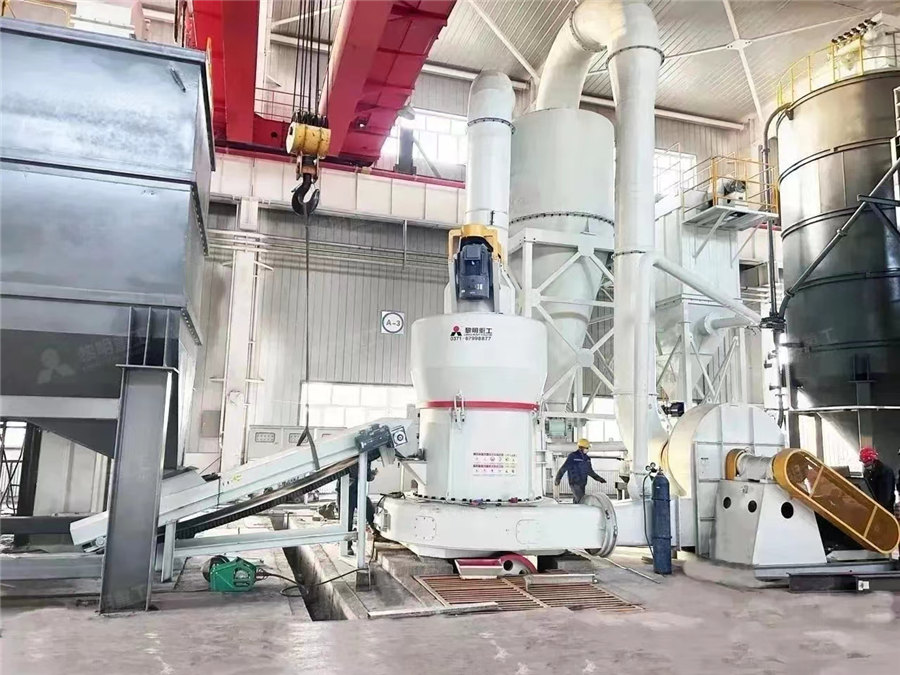
Reengineering of the ore preparation production
The process of material pieces or grains reduction by destruction under the influence of external mechanical forces, depending on the size of the final product, is called crushing or grinding 2023年7月22日 Ore crushing is the process of breaking, splitting, extrusion, impacting, and grinding of large solid ore with external force to reduce the particle size of large ore materialsOre Crushing SpringerLink2023年7月27日 Ball grinding process is a grinding method of crushing ore with ballshaped grinding medium in the grinding mill In the ball grinding process, because the steel ball has Ball Grinding Process SpringerLink2022年1月19日 comminution is to reduce the size of the ore The two predominant methods are crushing and grinding Crushing, the first process step after blasting in the mine, is used to EBOOK Three factors that determine the wear life and
.jpg)
Roll Crushers ScienceDirect
2016年1月1日 Roll crushers consist of two or more adjacent rolls placed parallel to each other and rotated in opposite directions Single roll crushers are also available which rotate a single 2016年1月1日 Spherical balls or cylindrical rods are mostly used as the grinding media These media cascade within a mill and impinge on the ore, thus providing a crushing action As the Size Reduction and Energy Requirement ScienceDirectWhen iron ore is extracted from a mine, it must undergo several processing stages Six steps to process iron ore 1 Screening We recommend that you begin by screening the iron ore to separate fine particles below the crusher’s CSS The six main steps of iron ore processing2016年1月17日 The use of hammer mills is in the field of softer minerals, such as gypsum, barytes and limestone, and particularly where the presence of clay would most definitely exclude the use of crushing machines in which fracture Crushing Mineral Processing 911Metallurgist
.jpg)
(PDF) Optimization Capabilities for Crushing
2022年4月26日 methods that could be used to create a reliable simulation platform f or crushing plant optimization studies Different data associa ted with crushing plants are also studied2015年8月3日 Compared to existing ore sensing methods, MWI has the potential to penetrate deeper into rock particles and to be used as a supplementary method for analyzing those ores with high contrast in (PDF) Overview of Mineral Processing Methods ResearchGateWet semiselfgrinding mills of WSGM type (Fig 2) are used, mainly, in the first stage of grinding in a twostage mode The use of large mills allows to exclude the stages of medium and fine crushing, and in some cases of large crushing [15] Selfgrinding mills (SGMs) and SSGMs are usually used to grind initial ore or the firstReengineering of the ore preparation production 2023年7月3日 Therefore, this method is known as gravity separation This method is frequently used when the ore particles are heavier than the earthy or rocky gangue particles For example: this method is used for oxide ores such as hematite, tin stone and native ore of Au, Ag, etc The powdered ore is fed into a stream of running water when the lighterCrushing, Grinding and Concentration of the Ore
.jpg)
EBOOK Three factors that determine the wear life and
2022年1月19日 mill grinds the largesized ore and then a secondary mill grinds the ore from a small size to the desired size The breakage mechanisms that mills use are impact (for coarse grinding), and attrition and abrasion (for finer sizes) These forces not only grind the rock, but they also subject the mill to substantial wear and tear Applying these2023年7月22日 The ore crushing process includes four types: ore coarse crushing, ore medium crushing, ore fine crushing, and ore superfine crushing Ore coarse crushing is a process of crushing ore blocks with a feeding particle size of 500–1500 mm to 125–400 mm The maximum crushing ratio of coarse crushing is about three The main force in the coarse Ore Crushing SpringerLink21 小时之前 carried out by size reduction performed by crushers and grinding mills The ore lumps from the mines have the lump size of 10 100 cm while the individual minerals have grain sizes below 01 mm Hence, the first step in any ore dressing plant is to aim at liberation by size reduction or comminutionLECTURE NOTES ON Mineral Processing (3rd Semester The present study investigated a novel method of alkaline ferricyanide leaching to extract palladium (Pd) from a Western Australian disseminated platinumgroup metal (PGM) oxide ore that bears Ni The extractive metallurgy of South Africa's platinum ores
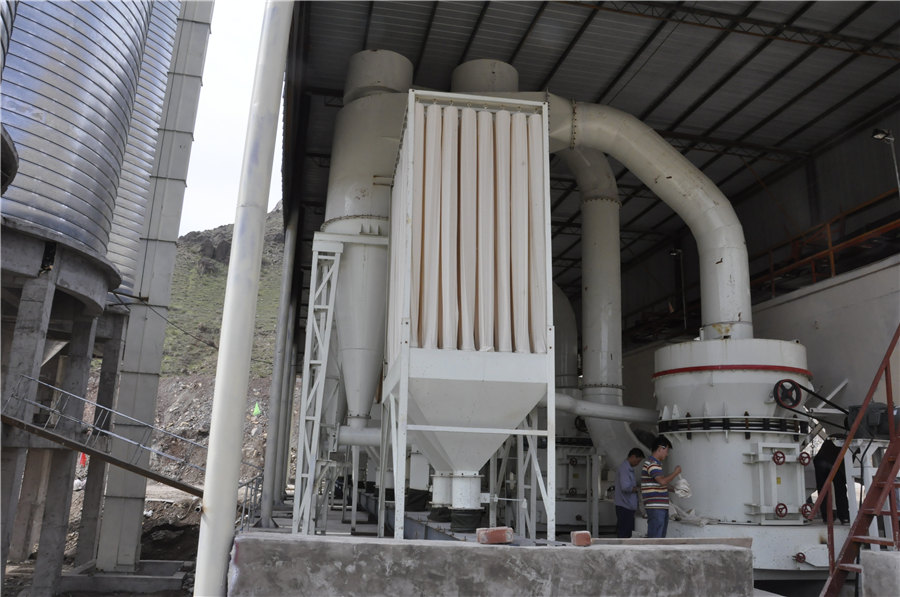
The Ultimate Guide to Ball Mills Miningpedia
2019年8月14日 • Central discharge ball mill: the inlet of medium unloading ball mill is at both ends, and the outlet is in the middle of the ball mill 4 According to the ore discharge of ball mill: • Overflow ball mill: Discharge the ore through hollow shaft • Grid ball mill: Discharge the ore through the plaid plate2021年1月12日 As a part of its investigation into runofmine ore fragmentation, Highland Valley Copper discovered the role of primary crushing in the optimisation of mill feed size Image analysis methods were used to quantify the effect of feed size on mill throughput and showed the inpit crushers toThe Importance of Primary Crushing in Mill Feed Size 2014年1月1日 The article presents a method to combine crushing plant simulation and optimisation with quality and economic considerations in order to successfully study alternative configurations of the plant Factors affecting the performance of crushing 2020年10月9日 In order to obtain the optimal operation parameters of a SAG mill, in this paper, the discrete element method (DEM) is used to simulate the breakage process of the particles by controlling three Operation Analysis of a SAG Mill under Different Conditions Based on
制粉-10.25公众号.jpg)
Unlocking the Secrets of Gold Ore Mill: A Comprehensive
Through historical advancements in techniques and equipment used in gold ore milling processes like crushing, grinding, classification, cyanidation, flotation, gravity separation methods, and more recently developed technologies like bacterial oxidation for refractory ores or resininpulp technology; significant improvements have been made in 2017年4月10日 In this bulletin the subject of ore dressing is approached from the economic rather than from the technological standpoint, and the supporting data have been compiled with a view to their bearing upon the economic exploitation of ore deposits Results obtained are stressed rather than the details of processes and the physics and chemistry involved For Ore Dressing Methods 911Metallurgist2012年6月1日 on mill dimensions, the type of the mill (overflow or grate discharge), the speed of rotation, the mill loading, the final product size required from a given feed size(PDF) Grinding in Ball Mills: Modeling and Process Control4 天之前 The key to the efficiency of the IsaMill™ is the ability to use fine media While tower mills are typically limited to 1012mm fresh media sizing, the IsaMill™ can use media as small as 1mm This results in significantly more surface area IsaMill Technology Used in Effecient Grinding Circuits
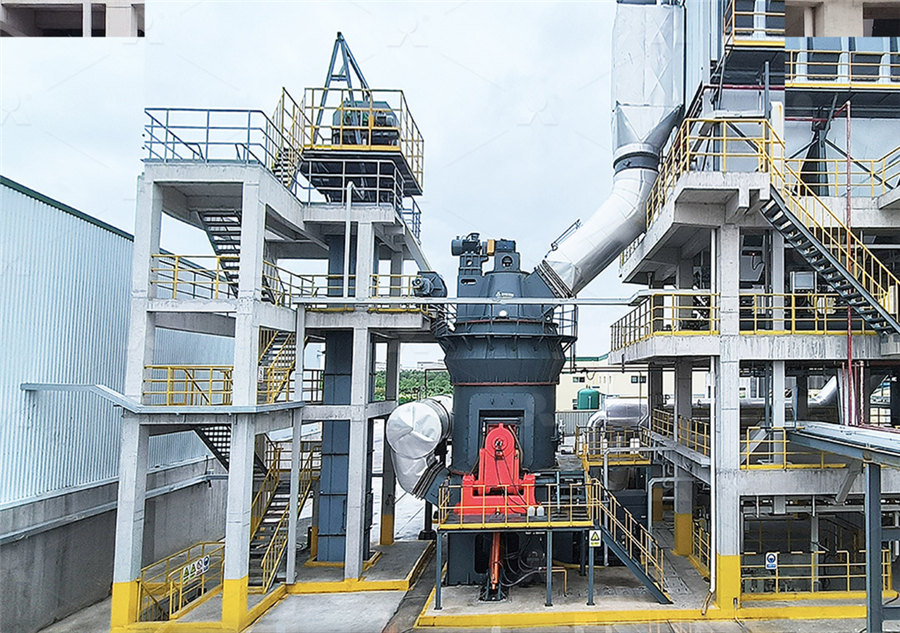
AMIT 135: Lesson 5 Crushing – Mining Mill Operator Training
This means that the number of crushing stages can be reduced depending on the feed size accepted by primary grinding stage Image of a “Classical” 3stage ore crushing prior to rod mill [image: (13551)] Diagram of Typical 12 stage ore crushing prior to AGSAG mill [image: (13552)] Calculation of Reduction Ratio in Crushing2024年6月28日 The results demonstrate that the crushing efficiencies of ore crushing particles, raw material crushing particles, and cement crushing particles can respectively reach 807%, 7015%, and 8027% Energy Efficiency Measurement of Mechanical Crushing 2023年6月30日 Over the last few decades, the demand for energyefficient mineralprocessing methods has continued The necessity to develop energyefficient technologies for the mineral industry will increase in the future, Modeling and Improving the Efficiency of 2016年6月8日 The gold cyanidation process is the most important method ever developed for extracting gold from its ores The reasons the widespread acceptance of cyanidation are economic as well as metallurgical It usually Gold Cyanidation Process 911Metallurgist
.jpg)
Estimation of Grinding Time for Desired Particle Size
2020年1月3日 22 Grinding Studies Two kinds of mills, BBM and LBM, were used to achieve the desired P 80 passing percentage of 150 μm with an acceptable range of hematite liberation (> 75%) at optimum grinding time The BBM is a standard ball mill having a length and diameter of 300 mm × 300 mm with smooth liner as shown in Fig 2A rotating drum is attached to a Jaw crusher is mainly used for medium particle size crushing of ore and bulk materials, Ball mill: Ball mill is a more commonly used and efficient grinding equipment It is suitable for grinding ore such as iron ore, gold ore, copper ore and leadzinc ore and other metal beneficiation, used to grind the ore to below 0075mm for subsequent Crushing and grinding process of copper ore Crusher Plant2016年2月29日 SAG mills, rod mills and ball mills are the classical pieces of grinding equipment employed in gold recovery plants There is an increasing trend to employ SAG mills (semiautogenous mills) in place of secondary and tertiary crushing and primary grinding The most common type of rod mill is the overflow mill There are two typed of ball mills usedGold Extraction Recovery Processes 911Metallurgist2024年1月1日 The ore crushing process includes four types: ore coarse crushing, ore medium crushing, ore fine crushing, and ore superfine crushing Ore coarse crushing is a process of crushing ore blocks with a feeding particle size of 500–1500 mm to 125–400 mm The maximum crushing ratio of coarse crushing is about three The main force in the coarse Ore Crushing SpringerLink
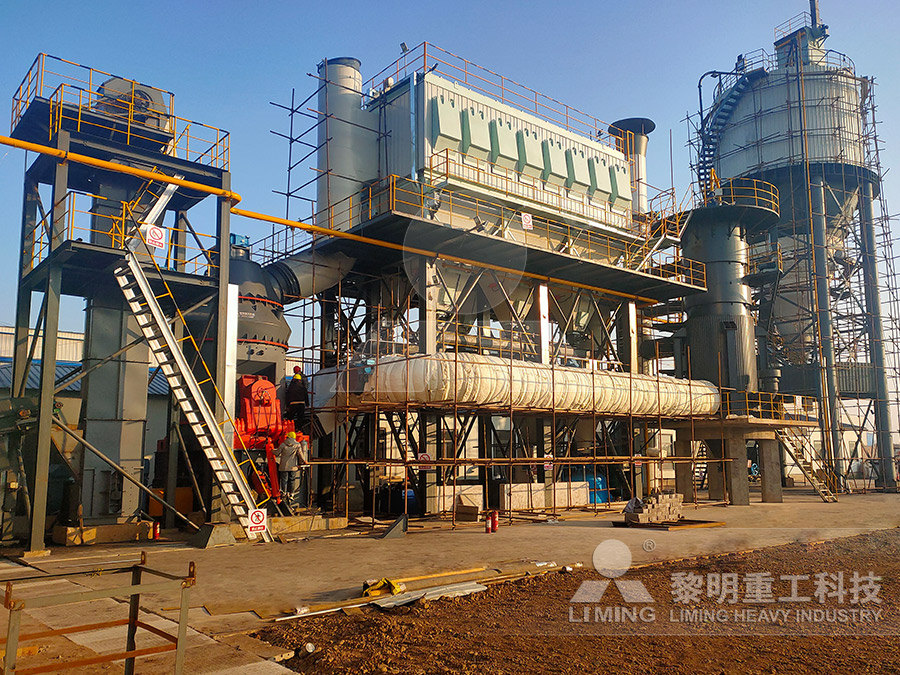
An Evaluation on the Impact of Ore Fragmented by Blasting
2022年2月17日 A model is presented to determine the loading capacity as a method of crushing the rock caused by the blasting In this model, parameters leading to reoperating costs are predicted MR; Faramarzi, F Study of the effect of blast pattern design on autogenous and semiautogenous mill throughput at golegohar iron ore mine In Proceedings 2013年1月3日 Cyanide is a lixiviant, or reagent that is used to leach, often in tanks, gold from a solid matrix and form a gold cyanide complex Carboninpulp (CIP) is the sequential leach then absorption of gold from ore During the CIP stage, pulp flows through several agitated tanks where sodium cyanide and oxygen have been added to dissolve gold Gold CIL CIP Gold Leaching Process Explained CCD2015年4月9日 Wet or dry product – Products which can be accepted in a wet state, such as slurries, can be milled wet which save power and reduce dust related problems As a general rule, only tumbling mills are used for wet grinding, although other mills can be used for wet grinding in certain circumstancesGrinding Mills and Their Types IspatGuruMinerals Engineering 21(3), 5–9] an approach was described which enabled the specific energy of tumbling mills such as Autogenous (AG), Semiautogenous (SAG) and ball mills to be estimated from Predicting the overall specific energy requirement of crushing
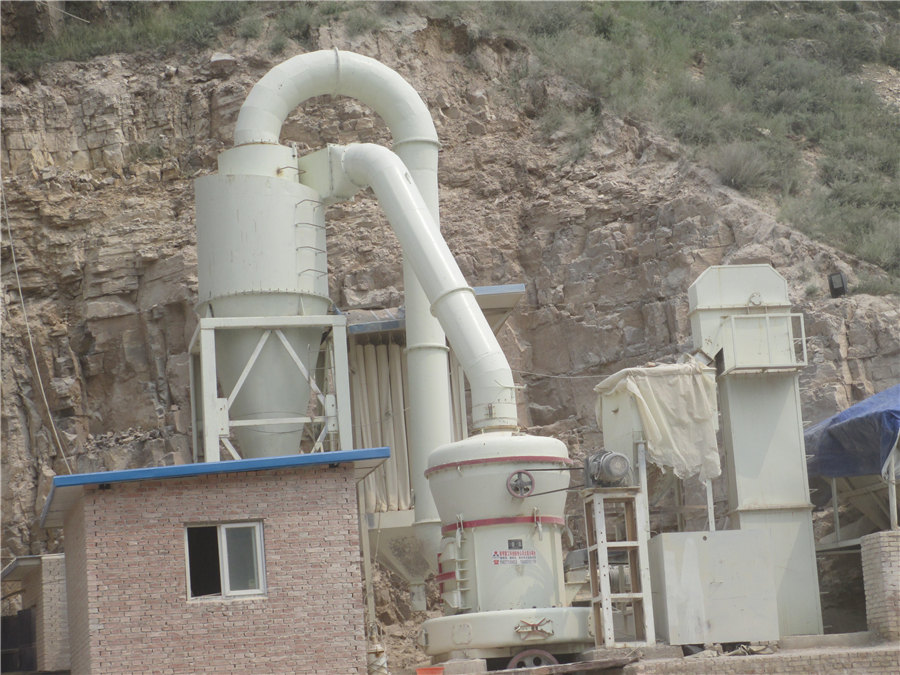
The six main steps of iron ore processing
When iron ore is extracted from a mine, it must undergo several processing stages Six steps to process iron ore 1 Screening We recommend that you begin by screening the iron ore to separate fine particles below the crusher’s CSS 2016年1月17日 The use of hammer mills is in the field of softer minerals, such as gypsum, barytes and limestone, and particularly where the presence of clay would most definitely exclude the use of crushing machines in which fracture Crushing Mineral Processing 911Metallurgist2022年4月26日 methods that could be used to create a reliable simulation platform f or crushing plant optimization studies Different data associa ted with crushing plants are also studied(PDF) Optimization Capabilities for Crushing 2015年8月3日 Compared to existing ore sensing methods, MWI has the potential to penetrate deeper into rock particles and to be used as a supplementary method for analyzing those ores with high contrast in (PDF) Overview of Mineral Processing Methods ResearchGate
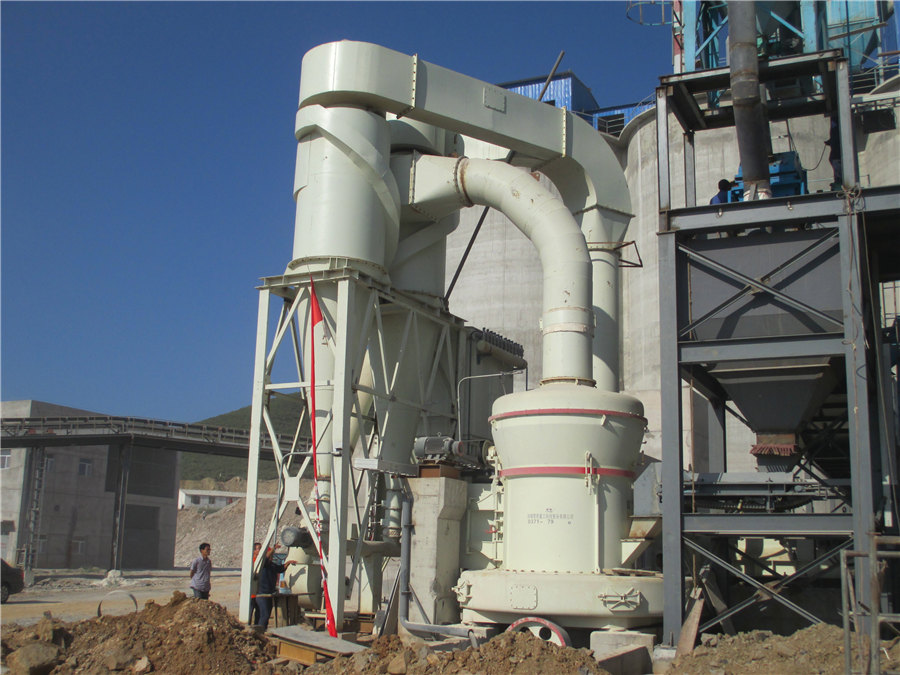
Reengineering of the ore preparation production
Wet semiselfgrinding mills of WSGM type (Fig 2) are used, mainly, in the first stage of grinding in a twostage mode The use of large mills allows to exclude the stages of medium and fine crushing, and in some cases of large crushing [15] Selfgrinding mills (SGMs) and SSGMs are usually used to grind initial ore or the first2023年7月3日 Therefore, this method is known as gravity separation This method is frequently used when the ore particles are heavier than the earthy or rocky gangue particles For example: this method is used for oxide ores such as hematite, tin stone and native ore of Au, Ag, etc The powdered ore is fed into a stream of running water when the lighterCrushing, Grinding and Concentration of the Ore2022年1月19日 mill grinds the largesized ore and then a secondary mill grinds the ore from a small size to the desired size The breakage mechanisms that mills use are impact (for coarse grinding), and attrition and abrasion (for finer sizes) These forces not only grind the rock, but they also subject the mill to substantial wear and tear Applying theseEBOOK Three factors that determine the wear life and2023年7月22日 The ore crushing process includes four types: ore coarse crushing, ore medium crushing, ore fine crushing, and ore superfine crushing Ore coarse crushing is a process of crushing ore blocks with a feeding particle size of 500–1500 mm to 125–400 mm The maximum crushing ratio of coarse crushing is about three The main force in the coarse Ore Crushing SpringerLink
.jpg)
LECTURE NOTES ON Mineral Processing (3rd Semester
21 小时之前 carried out by size reduction performed by crushers and grinding mills The ore lumps from the mines have the lump size of 10 100 cm while the individual minerals have grain sizes below 01 mm Hence, the first step in any ore dressing plant is to aim at liberation by size reduction or comminutionThe present study investigated a novel method of alkaline ferricyanide leaching to extract palladium (Pd) from a Western Australian disseminated platinumgroup metal (PGM) oxide ore that bears Ni The extractive metallurgy of South Africa's platinum ores