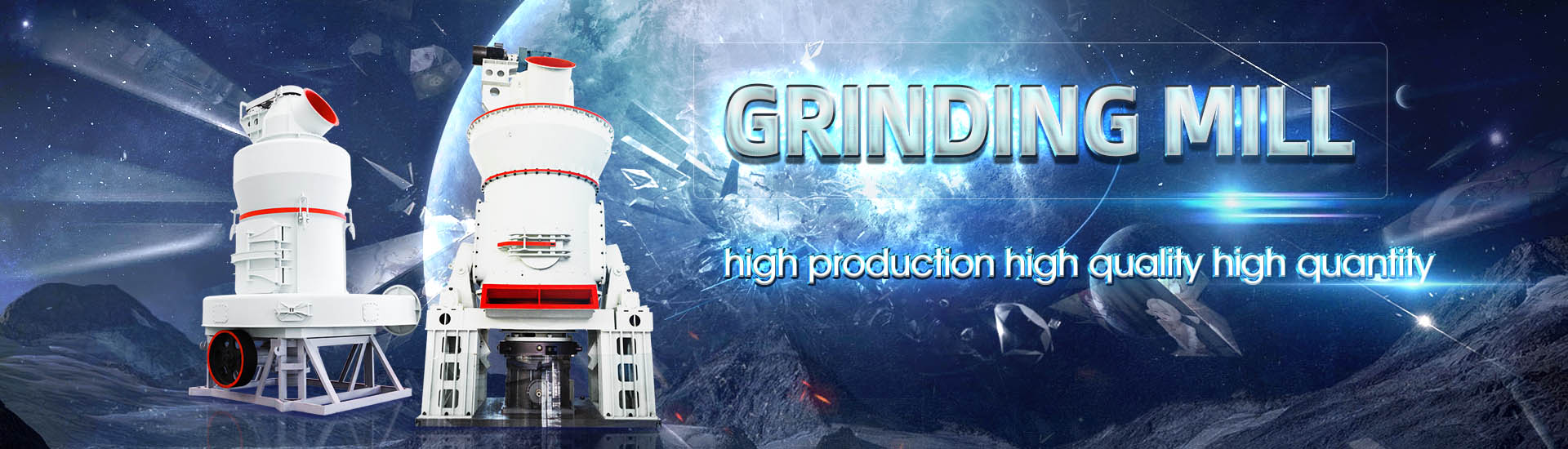
Equipment air flow mill fault maintenance
.jpg)
Mill Maintenance Methods Miller Magazine
2018年5月8日 One of the first things to examine when a mill is experiencing poor results is the maintenance MAINTENANCE METHODS Adequate maintenance program can be achieved 2022年8月29日 Researchers are finding new methods for better analysis of faults and reliability from traditional statistical methods to applying artificial intelligence With the advancement of Industry 40, theA Review of Reliability and Fault Analysis 2015年8月1日 Substantial savings, owing to reduced maintenance costs and production losses, can be achieved through fewer mill choking incidents, fewer mill runbacks, optimal mill Review of control and fault diagnosis methods applied to coal mills 2022年7月5日 Maintenance in mills, periodic replacement of parts and consumables with predetermined useful life in order to reduce the possibility of malfunctions during the operation Maintenance management in mills Miller Magazine
.jpg)
Occurrence of faults at the "Mill A" equipment [Carbol
An example of the occurrence of faults for "Mill A" equipment is shown in Fig 4 The different types of failures showed two different time intervals for their These elements are2024年11月26日 As per other material processing equipment, the key to maximizing performance for an air classification mill is keeping the machine wellmaintained To keep an Essential Maintenance Tips for Air Classification Mills2021年10月18日 Conditionbased maintenance (CBM) has attracted significant interest from the research community in recent years This paper provides a review on CBM of industrial Technology development and commercial applications of industrial fault 2022年11月30日 In this paper, a fault diagnosis method combining CWT and dualattention guided feature fusion network is proposed to solve the problem of uneven data distribution in Intelligent fault diagnosis of rolling mills based on dual
.jpg)
Fault Detection And Diagnostics In Equipment
2024年4月11日 The objective of Fault Detection and Diagnostics in the context of equipment maintenance is to optimize maintenance costs while still improving the reliability, availability, maintainability and safety (RAMS) of the equipment2024年4月11日 via GIPHY Fault evaluation is a significant element of the overall process as it aims to understand the severity of the faultThis helps reliability engineers provide equipment validation and calculate the risk of Fault Detection And Diagnostics In Equipment 2024年5月1日 Thermal units are expensive assets in the power industry It is essential to maintain the wellbeing of thermal units Coal mill is one of the important auxiliary equipment of thermal power units [6]Before the coal is blown into the furnaces of power plants, the coal mill crushes the coal and dries itDual fault warning method for coal mill based on2022年8月29日 With the advancement of Industry 40, the mining industry is steadily moving towards the predictive maintenance approach to correct potential faults and increase equipment reliabilityA Review of Reliability and Fault Analysis
.jpg)
Research on fault diagnosis of coal mill system based on the
2020年9月1日 For modelbased fault diagnosis method, it first needs to establish a mathematical model of the coal mill Odgaard et al [2] used a simplified energy balance equation to monitor and diagnose abnormal energy flow in the coal mill Andersen et al [3] designed a Kalman filter to estimate the moisture entering and leaving the coal mill, thereby identifying whether the 2015年8月1日 Substantial savings, owing to reduced maintenance costs and production losses, can be achieved through fewer mill choking incidents, fewer mill runbacks, optimal mill operation, and rapid diagnoses of mill faults [5]Over the years, considerable research has been carried out for improving the operation of coal mills using better controls and diagnosing faults in mills at Review of control and fault diagnosis methods applied to coal mills 2023年12月18日 Efficient fault reporting is a cornerstone of proactive maintenance strategies, enabling organizations to address issues swiftly and maintain optimal operational performance Whether you are managing a manufacturing facility, a fleet of vehicles, or a complex infrastructure, a robust fault reporting system is essential for identifying and rectifying The Importance of Fault Reporting in Maintenance FaultFixersThe fault detection under predictive maintenance in ball bearing uses the sensor data and advanced analytics techniques to proactively identify faults, enabling timely maintenance actions and preventing equipment failures The AI algorithms, such as Autoencoders, Artificial Neural Network (ANN), and Random Forest (RF) classification, enable the AIEnabled Fault Detection for Predictive Maintenance of
.jpg)
Fault detection for mining and mineral processing equipment
2001年9月16日 Fault detection is a technique being applied in the mining commodities industry to lower operating costs and improve machine reliability and efficiencyThe mining, aggregates and cement industries are looking to contain and reduce costs in the face of longterm market price declines in their products Over the past seven years, for example, the average USThe air flow throu gh mill is necessary for several reasons First of all the air tran sports the material inside of the mill and the product out of the mill to the bag filter For the first start and after cleaning for maintenance purposes the mill and the weigh feeder have to be loaded with limestone This is done by starting the machines PROCESS TRAINING for operators of Vertical RAW Mills2022年5月31日 As shown in Fig 6, the primary air flow rate and the coalair mixture outlet temperature of the coal mill started to decline in a form of up and down oscillation at 510 am The decreasing tendency of the primary air flow rate and the coalair mixture outlet temperature is extremely obvious from 510 am to 936 amA brannew performance evaluation model of coal mill 2023年2月13日 Also, by having the platform detect AND identify the fault, maintenance teams can be more efficient targeting the problem areas versus spending time diagnosing predictive maintenance can identify patterns and Predictive Maintenance in Pulp and Paper Mills
.jpg)
Predictive maintenance in mining industry: grinding mill case
2022年1月1日 Illustration of a predictive maintenance scheme for automatic washing equipment, and demonstration of the chal lenges encountered when conduct ing a predictive maintenance re search Classification of the specific industrial applications based on six algorithms of machine learning and deep learning (DL), and compare five performance metrics 2021年1月28日 ABSTRACT Process monitoring and fault diagnosis (PMFD) of coal mills are essential to the security and rel iability of the coal fired power plant However, traditional methods have difficulties A Novel MultiMode Bayesian Method for the Process Monitoring and Fault The Maintenance of Rolling Mill Equipment; Technical Progress of Highspeed Wire Rod Mills; Failure Analysis of Vibration Fault of Rolling Mills January 31, 2023; Hot Rolled Steel Plate and Cold Rolled Steel Plate October 21, 2022; Short Stress Rolling Mills August 11, 2022;Rolling Mill Common Faults and Maintenance2023年11月13日 The reliable operation of highspeed wire rod finishing mills is crucial in the steel production enterprise As complex systemlevel equipment, it is difficult for highspeed wire rod finishing mills to realize fault location and realtime monitoring To solve the above problems, an expert experience and datadrivenbased hybrid faultExpertExperienceandData
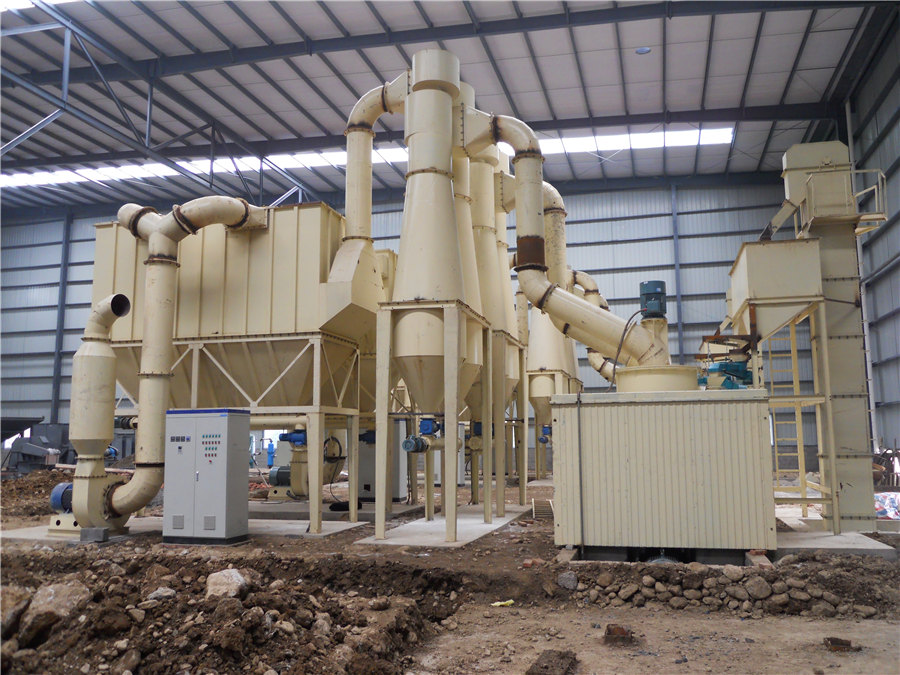
(PDF) A new modelbased approach for power plant Tubeball mill
Thermal process analysis Fig 3 Illustration of mass flow the mill by the feeders at a mass flow rate of Wc By tumbling the raw coal Mc with a charge of steel balls, the pulverized coal Mpf is produced and carried out by the warm air flow to the mill outlet with a mass flow rate of Wpf2024年9月4日 Efficient and convenient datadriven methods are gradually widely used in equipment operation and maintenance, and how to construct datadriven models with excellent performance is a matter of concern In this paper, a fault early warning framework for coal mills based on causality and LSTM model is proposed, which consists of three steps A Fault Early Warning Method for Coal Mills Based on2024年4月1日 With the rapid development of China's modern industry, the proportion of largescale equipment in modern enterprises is also increasing As a kind of largescale crushing equipment widely used in industry, the intelligent operation of vertical mill has become a research hotspot of scholars at home and abroad Because the daily maintenance cannot find the faults Summary of intelligent fault diagnosis technology for vertical mills2024年8月5日 Ball mills play a critical role in modern industrial production, and issues with their bearings directly impact production efficiency and equipment maintenance costs Traditional methods for bearing fault detection require using fault samples to learn the mechanism, but this can damage equipment and result in high costs This paper proposes a bearing fault detection Ball mill fault detection system based on autoencoder neural
.jpg)
Milling Operations: Reviewing maintenance strategies
2022年5月30日 In the 1970s and earlier, maintenance often was based on equipment needs or demands Differed maintenance often resulted in emergency repair activity, which often resulted in collateral damage requiring considerable time and expense to correct The primary mill maintenance goal should be to ensure the milling asset is available for 2022年8月30日 Equipment failures aren’t easily detectable and often go unnoticed In other cases, companies simply lack efficient planning methods for ensuring that ongoing maintenance is performed Tracking equipment and 5 Causes Of Equipment Failure And How To 2021年7月11日 the Mikro ACM® Air Classifying Mill requires routine inspection and maintenance to continuously operate at peak performance The internals of the mill should be inspected periodically for wear and preventative maintenance should be carried out on a systematic timetable Hosokawa’s AftermarketAir Classifying Mill hmicronpowder2023年11月23日 automated and robust fault detection methodologies With the rapid development of machine learning technologies, datadriven machine learning methods have provided new solutions for ball mill fault detection These methods leverage extensive data from different operational states of bearings to autonomously learn fault mechanisms,Convolutional AutoEncoding Network arXiv
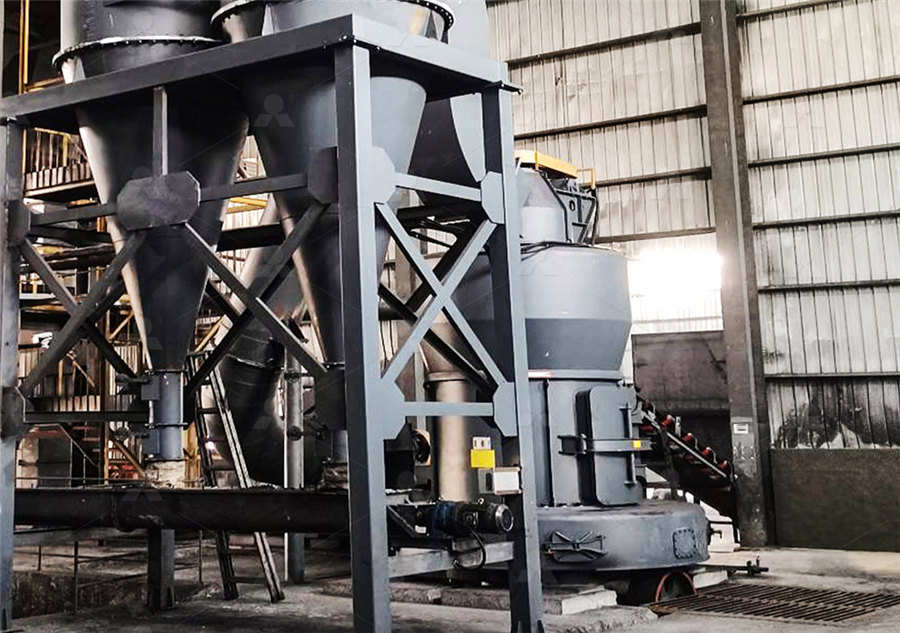
Equipment Maintenance: 5 Causes of Failure, and How to
2023年7月14日 Equipment failures can be devastating to the smooth functioning of operations, leading to costly downtime, decreased output, and frustrated stakeholders But a strong equipment maintenance strategy can prevent failures and less equipment downtime to keep your facilities running strong Many companies rely on equipment2023年10月1日 (a) ((ApplicationofModel 2023年10月20日 a (!a)) ((!) #) # =)] % ‖" = ($,)" #,’! "! ")! " + " "! ! $ % ’ ’, # • %, %’!, and •A novel multimode Bayesian method for the process A cement mill grinds the hard, nodular clinker from the cement kiln into the fine grey powder that is cement It is the last core equipment in the cement making process This paper demonstrates the use of Infinite Uptime’s autodiagnostics features to help detect faults for complex gear train assembly used to drive the cement millfault diagnosis for cement mill infinite uptime
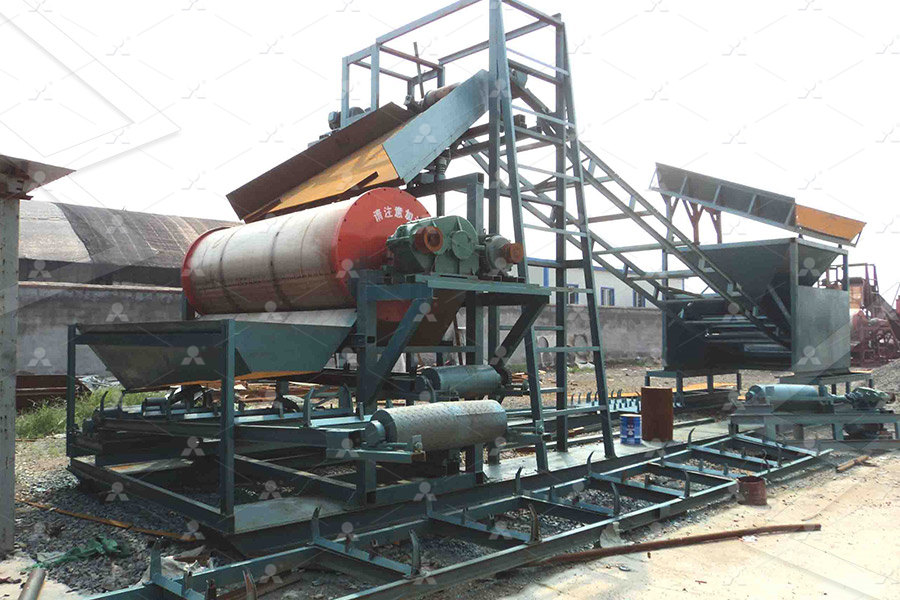
(PDF) Application of ModelBased Deep Learning Algorithm in Fault
2020年8月14日 The coal mill is one of the important auxiliary engines in the coalfired power station Its operation status is directly related to the safe and steady operation of the units2023年6月25日 Common faults: high speed shaft bearing damage, high speed shaft bevel gear tooth broken, high speed shaft two bearings between the interval sleeve loose, parallel axis external tooth spline shaft and internal tooth spline sleeve surface wear, equipment vibration Fault maintenance: invite the professional maintenance team to perform onsite Large Vertical Mill Reducer Maintenance shyychinaThe Maintenance of Rolling Mill Equipment; Technical Progress of Highspeed Wire Rod Mills; The vibration fault of the rolling mill equipment rotor and its causes show that the rotor is always in running state in rolling mill machinery construction, and the vibration fault is very common Rolling Mill Equipment Fault Analysis Steel Rolling Mill 2024年4月11日 via GIPHY Fault evaluation is a significant element of the overall process as it aims to understand the severity of the faultThis helps reliability engineers provide equipment validation and calculate the risk of Fault Detection And Diagnostics In Equipment
.jpg)
Dual fault warning method for coal mill based on
2024年5月1日 Thermal units are expensive assets in the power industry It is essential to maintain the wellbeing of thermal units Coal mill is one of the important auxiliary equipment of thermal power units [6]Before the coal is blown into the furnaces of power plants, the coal mill crushes the coal and dries it2022年8月29日 With the advancement of Industry 40, the mining industry is steadily moving towards the predictive maintenance approach to correct potential faults and increase equipment reliabilityA Review of Reliability and Fault Analysis 2020年9月1日 For modelbased fault diagnosis method, it first needs to establish a mathematical model of the coal mill Odgaard et al [2] used a simplified energy balance equation to monitor and diagnose abnormal energy flow in the coal mill Andersen et al [3] designed a Kalman filter to estimate the moisture entering and leaving the coal mill, thereby identifying whether the Research on fault diagnosis of coal mill system based on the 2015年8月1日 Substantial savings, owing to reduced maintenance costs and production losses, can be achieved through fewer mill choking incidents, fewer mill runbacks, optimal mill operation, and rapid diagnoses of mill faults [5]Over the years, considerable research has been carried out for improving the operation of coal mills using better controls and diagnosing faults in mills at Review of control and fault diagnosis methods applied to coal mills
.jpg)
The Importance of Fault Reporting in Maintenance FaultFixers
2023年12月18日 Efficient fault reporting is a cornerstone of proactive maintenance strategies, enabling organizations to address issues swiftly and maintain optimal operational performance Whether you are managing a manufacturing facility, a fleet of vehicles, or a complex infrastructure, a robust fault reporting system is essential for identifying and rectifying The fault detection under predictive maintenance in ball bearing uses the sensor data and advanced analytics techniques to proactively identify faults, enabling timely maintenance actions and preventing equipment failures The AI algorithms, such as Autoencoders, Artificial Neural Network (ANN), and Random Forest (RF) classification, enable the AIEnabled Fault Detection for Predictive Maintenance of2001年9月16日 Fault detection is a technique being applied in the mining commodities industry to lower operating costs and improve machine reliability and efficiencyThe mining, aggregates and cement industries are looking to contain and reduce costs in the face of longterm market price declines in their products Over the past seven years, for example, the average USFault detection for mining and mineral processing equipmentThe air flow throu gh mill is necessary for several reasons First of all the air tran sports the material inside of the mill and the product out of the mill to the bag filter For the first start and after cleaning for maintenance purposes the mill and the weigh feeder have to be loaded with limestone This is done by starting the machines PROCESS TRAINING for operators of Vertical RAW Mills
.jpg)
A brannew performance evaluation model of coal mill
2022年5月31日 As shown in Fig 6, the primary air flow rate and the coalair mixture outlet temperature of the coal mill started to decline in a form of up and down oscillation at 510 am The decreasing tendency of the primary air flow rate and the coalair mixture outlet temperature is extremely obvious from 510 am to 936 am