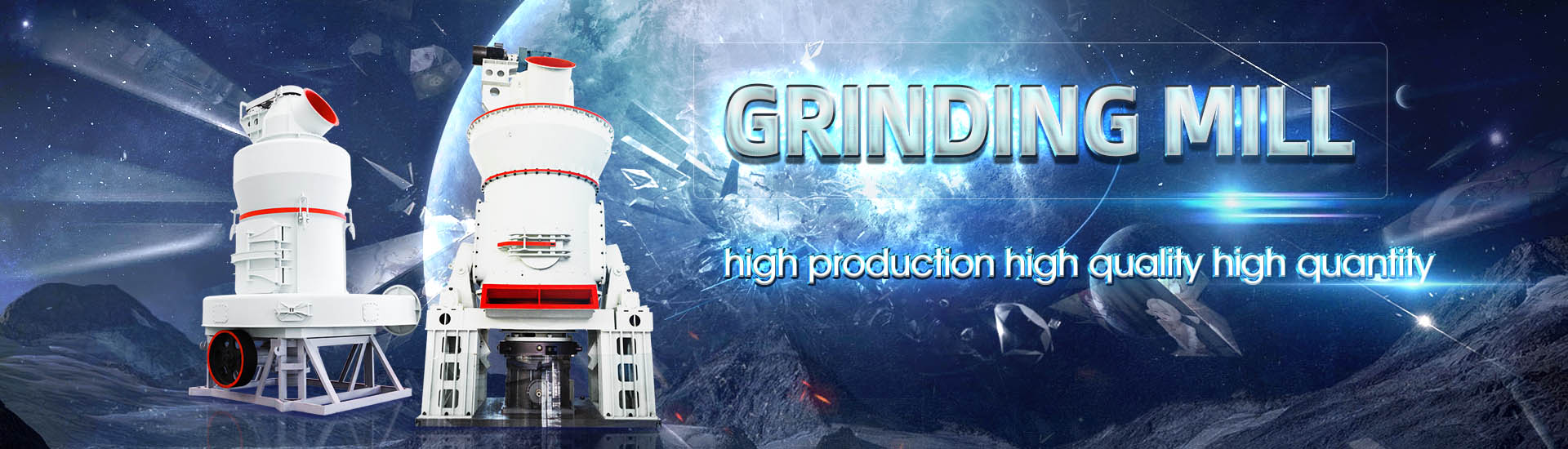
vacuum gas atomization limestone crusher powder

VACUUMASSISTED GAS ATOMIZATION OF LIQUID METAL
(1) Once the nozzle throat becomes sonic, its mass flow becomes restricted (choked) Lowering the back pressure therefore increases the length of the supersonic jet without increasing the gas mass flow rate Any benefits to efficiency that are achieved in this way would cost nothing in terms of added gas flow, 展开Vacuum Induction Melting Inert Gas Atomization (VIMIGA) is used to produce fine, spherical metal powders for use in a variety of applications, including additive manufacturing (AM) and Vacuum Induction Melting Inert Gas Atomization ConsarcALD VIGA Systems – World Class Equipment to produce your metal powder feedstock for a bright world different processes applications As one of the leading suppliers of vacuum ALD Vacuum Technologies High Tech is our Business2024年3月1日 The closecoupled nozzle is key to controlling the particle diameter and powder defects such as satellite particles during the production of metal powders via vacuum induction Numerical and experimental investigation of closecoupled twin
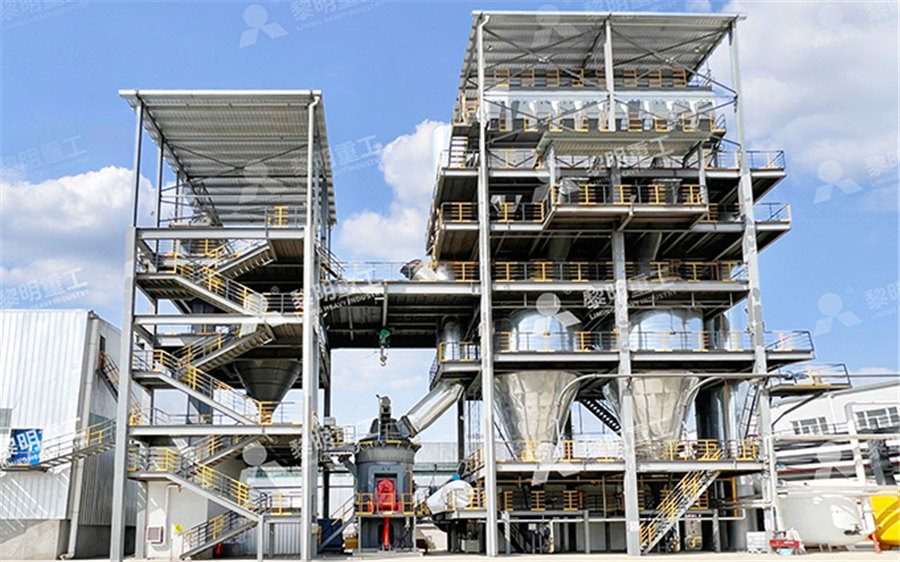
Research Advances in CloseCoupled Atomizer Flow and
2024年3月21日 Coupled gas atomization powder preparation technology is an ideal choice for preparing highquality powders with high atomization efficiency, low oxygen content, and high ALD Vacuum Technologies GmbH is the market and technology leader for vacuum inert gas atomizers used in the production of highquality metal powders In addition, ALD has extensive experience in combining various melting Vacuum Induction Melting Inert Gas Atomization ALD1996年1月1日 Influence of particle size on cooling rates and microstructure is examined for various atomizing gases, and a pilot plant gas atomizer is described to illustrate the requirements of powder Production of metal powders by gas atomization2022年6月15日 Abstract: As the main equipment for the industrial production of metal powder, vacuum atomization milling equipment is widely used in key areas including additive 真空雾化制粉技术研究进展及展望
.jpg)
What is gas atomization powder metallurgy used for?
2023年8月30日 Gas atomization is a powder metallurgy process used to produce fine metallic powders It involves melting a metal alloy and disintegrating the melt into fine droplets using a highvelocity gas jet The droplets rapidly solidify into powders with a spherical morphology and controlled particle size distributionConsult ALD's entire Vacuum Inert Gas Metal Powder Technology catalogue on DirectIndustry Page: 1/8 Exhibit with us {{>currencyLabel}} Back {{>currenciesTemplate}} English Back; (VIGA) Vacuum Inert Gas Vacuum Inert Gas Metal Powder Technology ALD2023年7月27日 Gas Atomized Powders vs Other Powder Production Methods Gas atomization is just one of several techniques used to produce metal powders Let’s explore how it compares to other common powder production methods: Water Atomization Water atomization is a similar process to gas atomization, but instead of using gas, water is employed as the Gas Atomized Powders:its 12 Advantages and ApplicationsDownload scientific diagram Schematic diagram of gas atomization processing from publication: Gas Atomization of Amorphous Aluminum Powder: Part II Experimental Investigation The optimal Schematic diagram of gas atomization processing
.jpg)
Production of metal powders by gas atomization ResearchGate
1996年1月1日 Metal powder production by gas atomization has been studied in some depth in recent years Vacuum degassing is usually carried out at temperatures of 400 500°C to remove water vapour 2023年7月26日 Gas atomization is a powder production technique employed in powder metallurgy to fabricate metal powders with specific properties and characteristics Unlike traditional methods, such as water atomization, the gas atomization process generates powders with a highly spherical shape and narrow particle size distribution, leading to enhanced 10 points of gas atomization process in powder metallurgy2024年9月9日 What is Gas Atomization? Gas atomization is a process where molten metal is broken up into fine particles using a highvelocity gas stream The basic principle involves melting the metal, directing it through a nozzle, and then using a gas (like nitrogen, argon, or air) to atomize the liquid stream into fine dropletsThe Ultimate Guide to Gas Atomizers for Metal Powder ProductionVacuum Inductionmelting Inert Gas Atomization IntroductionElectrode Inductionmelting Inert Gas Atomization 圓融金屬粉末股份有限公司CIRCLE Metal Powder The VIGA process has the excellent control over alloy powder compositions and low oxygen contentVacuum Inductionmelting Inert Gas Atomization Introduction

Global Vacuum Induction Melting Inert Gas Atomization System
2024年7月26日 12133 HengYang Metal powder Vacuum Induction Melting Inert Gas Atomization System Sales, Price, Revenue and Gross Margin (20192024) 12134 HengYang Metal powder Vacuum Induction Melting Inert Gas Atomization System Product Model Numbers, Pictures, Descriptions and Specifications 12135 HengYang Metal powder Recent Developments2024年7月3日 The global Vacuum Inert Gas Atomization Equipment market was valued at US$ million in 2023 and is projected to reach US$ million by 2030, at a CAGR of % during the forecast period The influence of COVID19 and the RussiaUkraine War were consideredVacuum Inert Gas Atomization Equipment Market Size, Share 年2月9日 Highquality FeCrNiWB spherical powder is crucial for the powder metallurgy preparation of highstrength and tough FeCrNiWB alloys In this study, the controlled preparation of highquality FeCrNiWB spherical Study on Flowability Regulation of Vacuum Gas 2024年1月15日 Gas atomization is a widely used method to produce metal powders However, the powders often have a wide range of particle sizes, which is not ideal for additive manufacturingTo visualize the liquid breakup during gas atomization, we have developed a novel approach that combines similarity theory with NavierStokes equationsThe simulation utilizes 3D numerical modeling of gas atomization process for powder
.jpg)
Closecoupled nozzle atomization integral simulation and powder
2021年1月18日 DOI: 101088/16741056/abc167 Corpus ID: ; Closecoupled nozzle atomization integral simulation and powder preparation using vacuum induction gas atomization technology*2023年9月1日 Owing to the advantages of large output, fine powder production and low gas consumption, Wang JF, Xia M, Wu JL, et al Ladle nozzle clogging in vacuum induction melting gas atomization: Influence of deliverytube geometry Rare Metal Mater Eng 2022;51(09):3214–3222Nozzle clogging in vacuum induction melting gas atomisation: Ladle Nozzle Clogging in Vacuum Induction Melting Gas Atomization: Influence of the Melt Viscosity JUNFENG WANG, MIN XIA, JIALUN WU, and CHANGCHUN GE During the production of fine metal powder using vacuum induction melting gas atomization (VIGA) technology, the problem of nozzle clogging is often encountered The viscosity of melt isLadle Nozzle Clogging in Vacuum Induction Melting Gas Atomization PROPERTIES AND APPLICATIONS FOR IRON POWDER MADE BY GAS ATOMIZATION Kalathur Narasimhan P2P Technologies Moorestown, NJ 08057 Chris Schade, Kylan McQuaig and Carter Tesch Hoeganaes Corporation Cinnaminson, NJ Vacuum furnace at temperatures of 1360, 1380 and 1400oC and held for 2 hours under a partial pressure of hydrogenPROPERTIES AND APPLICATIONS FOR IRON POWDER MADE BY GAS ATOMIZATION

Numerical simulation of atomization process of nickelbased
2020年6月29日 ANSYS Fluent 190 software is used to numerically simulate atomization process in the production of nickelbased alloy powders by VIGA The gas flow field in the atomizing chamber and atomization 2009年8月26日 Figure 2 shows the change in the size distribution of atomized Al 2024 alloy powders for different GA conditions The average powder size decreases with increasing amounts of melt superheat temperature, as evident from the B 1 results Increasing gas pressure can decrease powder size, as is evident from comparing the results from atomization C 1 and A 1, Gas Atomization of Amorphous Aluminum Powder: Part IIwith inferior mechanical properties Techniques using an inert gas blanket during melting are typically seen to generate powders with an oxygen content at the limit of 200300ppm specifications Conclusions It is important to understand how the different melting techniques in gas atomization powder production impact on the level of Vacuum vs NonVacuum Melted Gas Atomized Powders2023年7月19日 10 Key Insights of gas atomization metal powder 5 Applications of gas atomization metal powder Gas atomized metal powders find applications in various industries due to their unique characteristics Some of the key applications include: Additive Manufacturing10 Key Insights of gas atomization metal powder Additive
.jpg)
Vacuum induction melting Inert Gas Atomization (VIGA) Höganäs
Vacuum induction melting Inert Gas Atomization or VIGA is one of the leading powdermaking processes for production of large volumes of spherical, highgrade metal powders Our highquality cobalt , nickel and iron based forAM ® metal powders are produced with the specific VIGA system and have been designed specifically for the requirements of additive manufacturingAbstract We simulate the gasatomization process of a closecoupled annular nozzle for vacuum induction gas atomization at a threedimensional scaleMoreover, the relationship between the simulated droplet type and experimentally metallic powder is established by comparing the morphology of droplets with powdersClosecoupled nozzle atomization integral simulation and powder Gas atomization is the preferred powder production method when precise control over powder characteristics is critical Gas Atomization vs Alternative Methods Comparison with Water Atomization Tighter particle size distribution with gas Gas Atomization Equipment MET3DPwith inferior mechanical properties Techniques using an inert gas blanket during melting are typically seen to generate powders with an oxygen content at the limit of 200300ppm specifications Conclusions It is important to understand how the different melting techniques in gas atomization powder production impact on the level of Vacuum vs NonVacuum Melted Gas Atomized Powders HubSpot
.jpg)
Advanced gas atomization processing for Ti and Ti alloy powder
2010年5月13日 A multilayer ceramic composite melt pour tube for superheating and pouring of molten Ti6Al4V (wt%) was tested using an existing Ti atomization system Free fall gas atomization was conducted with the pour tube while liquid metal temperatures were measured in situ using a twocolor optical pyrometer Postprocess pour tube erosion was compared with 2023年8月1日 This work describes the process of preparing 316 L stainless steel powder by vacuum atomization, then a 3D print sample of 316 L stainless steel is prepared by selective laser melting (SLM Powder Preparation by Vacuum Atomization and 3D Printing 2022年9月19日 Electrode induction melting gas atomization (EIGA) is a widely applied method for preparing ultraclean metal powders The method is a completely cruciblefree melting and atomization process The current paper aims to study the relationship between the diameter of the atomizer and powder yields in EIGA The principal design objectives were to produce small Effect of Electrode Induction Melting Gas Atomization Process on 2023年3月21日 Electrode induction melting gas atomization (EIGA) is a wildly applied method for preparing ultraclean and spherical metal powders, which is a completely cruciblefree melting and atomization process Based on several experiments, we found that although the sphericity of metal powders prepared by EIGA was higher than that of other atomization methods, there Effect of Electrode Induction Melting Gas Atomization on Powder
.jpg)
VIGA Vacuum Induction Inert Gas Atomization Equipment
VIGA Vacuum Induction Inert Gas Atomization Equipment VIGA equipment has a wide range of applications, mainly for the production of highperformance iron of alloy metal powders through a process that involves vacuum induction melting of the metal followed by inert gas atomization to form fine powder particles How does VIGA equipment work?n umerical simulation of atomization process of nickelbased alloy powders prepared by vacuum induction melting gas atomizationk uaik uai g uo, jin c hen, s huo s hang, c hangs heng l iu issn p Numerical simulation of atomization process of nickelbased 2021年3月23日 Inert gas atomization is one of the main sources for production of metal powder for powder metallurgy and additive manufacturing The obtained final powder size distribution is controlled by various technological Modification of Liquid Steel Viscosity and Surface When refers to consumption region, % volume of Vacuum Inert Gas Atomization System were sold to North America, Europe and Asia Pacific in 2023 Moreover, China, plays a key role in the whole Vacuum Inert Gas Atomization System market and estimated to attract more attentions from industry insiders and investorsVacuum Inert Gas Atomization System Market, Report Size, Worth,
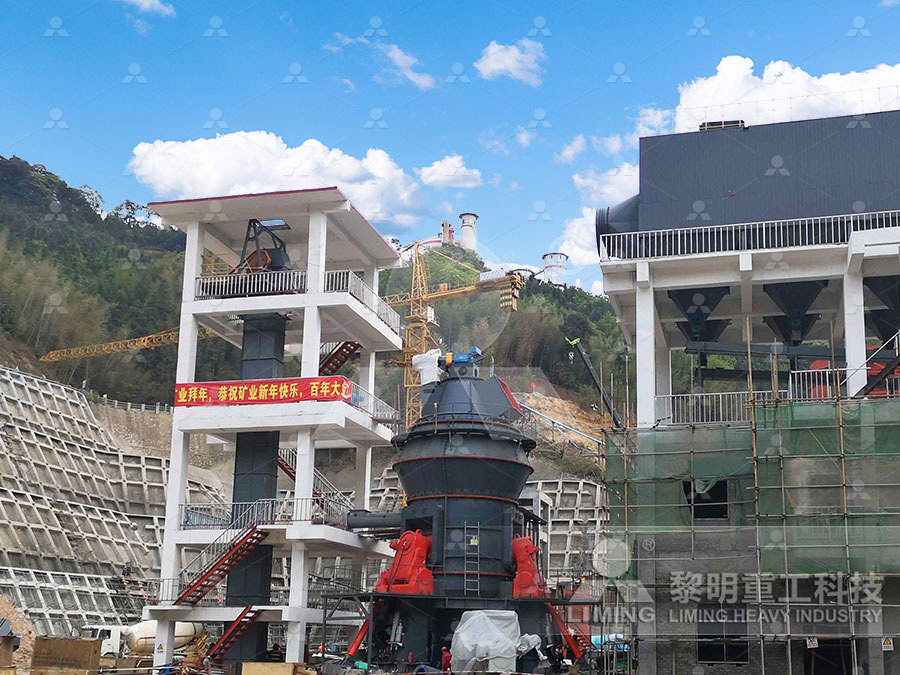
Electrode Induction Melting Inert Gas Atomization ALD
Electrode Induction Melting Inert Gas AtomizationAnlagen für Schmelzen und Verdüsen von Elektroden bis 150 mm Durchmesser und 1000 mm Länge ALD Vacuum Technologies GmbH ist der Markt und Technologieführer für 2024年3月1日 Spherical metal powders used during EHLC are currently produced via gas atomization, as reported by Ruan et al (2022) Wang et al (2021) performed a mechanistic investigation of gas atomization in powder production and showed that the two of the most widely used industrial gas atomization systems were freefall gas atomization (FFGA) and close Numerical and experimental investigation of closecoupled twin PDF On Mar 9, 2012, Udo Fritsching and others published Hybrid Gas Atomization for Powder Production Find, read and cite all the research you need on ResearchGateHybrid Gas Atomization for Powder Production ResearchGateStainless steels – Austenitic, ferritic, duplex, and martensitic stainless steels are commonly gas atomizedGrades like 316L, 174PH, and 420 are popular Tool steels – Tool steels like H13 and M2 can be atomizedUsed for molding tooling components Cobalt alloys – Biocompatible cobalt alloys for dental and medical uses like CoCrMo; Nickel alloys – Superalloys like Inconel and Gas Atomized Powder: A Comprehensive Guide MET3DP
.jpg)
Powder for Additive Manufacturing VDMMetals
The metal powder is produced in a standardized process A vacuum inert gas atomization plant (VIGA) forms the core of the powder manufacturing facility This plant is made up of a vacuum induction melting furnace Oil and Gas VDM ® Powder 625 N06625 24856 Corrosion resistant alloy : VDM® Powder X2020年3月16日 The research focuses on alloy design, powder production, and laser powder bed fusion (LPBF) of copper alloys Copper and its alloys play a fundamental role for modern industrial applications due to their excellent thermal and electric conductivity in conjunction with considerable mechanical strength, for example, as welding electrodes and nozzles By Additive manufacturing of CuCr1Zr by development of a gas atomization 2018年11月28日 The laboratory research of Inconel 718 superalloy powder prepared by vacuum induction melting gas atomization is rare However, the vacuum induction melting gas atomization is a complex process, multiphase flows are coupled to each other The mechanism of VIGA has still not been fully understoodThe structure and properties of Inconel 718 superalloy powder 2024年6月20日 Plasma Gas Atomization (PGA) is a new method for gas atomization of a variety of reactive and refractory alloys, amorphous metals and superalloys Provided by Retech Systems While plasma melting isn’t new for Retech; what’s new is the ability to leverage several strengths and develop a productionscale powder solution for reactive and refractory alloy powdersPlasma Gas Atomization removes powder metallurgy limitations