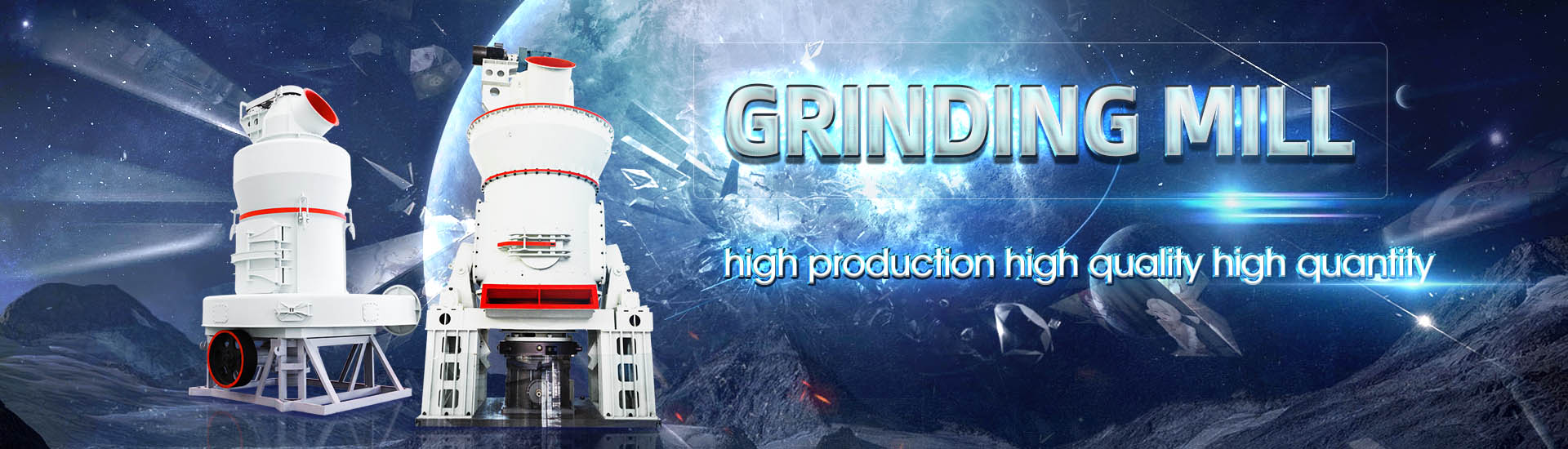
H P1163Dyn coal mill optimization operation analysis
.jpg)
Analysis of the Coal Milling Operations to the Boiler Parameters
Abstract: Fuel and firing system purposely to deliver light fuel oil or coal as one of the primary elements of fuel in an ideal condition for combustion to take place in the boiler combustion 2015年11月1日 Optimization of mill operation: The proposed model can be helpful for optimizing the working point of the mill Several possible objective functions can be – minimizing the A unified thermomechanical model for coal mill operationFig 14 Flow field after optimization of HP mill 中速磨壳体 旋转气流 旋转叶片 图15 优化后HP 磨煤机上部流场俯视图 HP coal mill upper flow field 412 中部流场优化 利用中央进风装置将一部 中速磨煤机制粉系统优化技术研究及应用2012年5月1日 The paper presents development and validation of a coal mill model to be used for improved mill control, which may lead to a better load following capability of power plants Derivation and validation of a coal mill model for control

Analysis of the Coal Milling Operations to the Boiler Parameters
2020年4月2日 The results indicate the optimum arrangement of the mill operation with minimum boiler parameters affectsFactors affecting the operation of boiler safety, economy and environment is complex, involving the furnace combustion process optimization adjustment, slagging in the furnace, dust, Coalfired Utility Boiler Operation Factors Analysis and The dynamic leveling of pipeline is to measure the flow deviation of airpowder between pipelines in real time by the pressure difference method under the premise of realizing airpowder 中速磨煤机制粉系统优化技术研究及应用2023年5月23日 As the vital auxiliary machine of the coalfired power plant, monitoring the realtime operating status of coal mills is critical to the secure and stable operation of the power Health indicator construction and application of coal mill based on
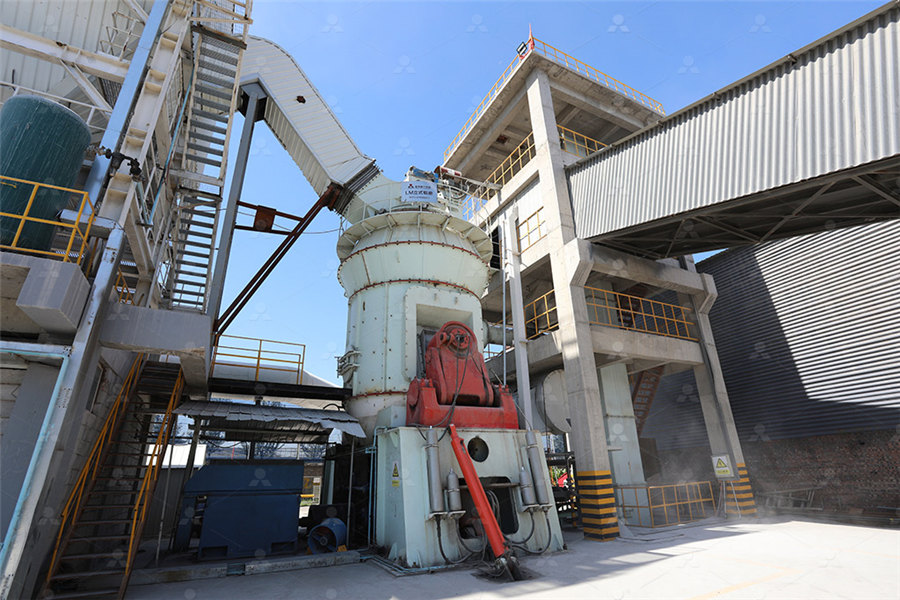
An investigation of performance characteristics and energetic
2020年8月12日 To understand the performance of a vertical roller coal mill, the real operational tests have been performed considering three different coal sources Obtained results indicate 2020年8月12日 To understand the performance of a vertical roller coal mill, the real operational tests have been performed considering three different coal sources Obtained results indicate An investigation of performance characteristics and energetic 2014年3月1日 Apart from these studies, Parham and Easson (2003), Ulusoy and Igathinathane (2016), Wei et al (2014) and Bilirgen (2005) conducted modeling and flow optimization analysis for the existing Breakage and separation mechanism of ZGM coal mill based 2020年10月9日 In order to obtain the optimal operation parameters of a SAG mill, in this paper, the discrete element method (DEM) is used to simulate the breakage process of the particles by controlling three Operation Analysis of a SAG Mill under Different
.jpg)
(PDF) Optimization and analysis for palm oil mill
2019年1月1日 Optimization and analysis for palm oil mill operations via inputoutput optimization model Steve Z Y Foong 1 , Viknesh Andiappan 2 , Raymond Tan 3 , and Denny K S Ng 1,*Coalfired Utility Boiler Operation Factors Analysis and Optimization Measures To cite this article: Henan Li 2018 IOP Conf Ser: Earth Environ Sci 170 View the article online for updates and enhancements Related content Circulating Fluidized Bed Boiler Oxygenenriched Combustion Technology Application Research Henan LiCoalfired Utility Boiler Operation Factors Analysis and Optimization Optimization and transformation of 300MV units steel ball coal mill system is 69 m³/h under the normal operation industrial analysis of coal into furnace during the Optimization and transformation of 300MV units steel ball coal mill 2020年4月7日 PDF Monitoring and diagnosis of coal mill systems are critical to the security operation of power plants The traditional datadriven fault diagnosis Find, read and cite all the research Modeling of Coal Mill System Used for Fault Simulation
.jpg)
Pulveriser Mill Performance Analysis Optimisation in Super
in the mining or coal processing operations Fig3 Mill fuel piping connections to furnace II COAL MILL SPECIFICATIONS PERFORMANCE ANALYSIS Typical Coal Pulveriser Mill Details in 660 MW SuperCritical [3] Unit is as given in table Table No 1 Table1 Coal mill Type Bowl Type Mediumspeed Coal mill Number of Mills 6set/ boiler2006年4月1日 Through optimization analysis, the robust parameter settings are 15068 kpa, 01814373 kpa, and 30%, and the optimal output is ash 8499%, which yields 6954%, meeting the requirements of (PDF) Coal preparation plant optimization: A critical review of in the mining or coal processing operations Fig3 Mill fuel piping connections to furnace II COAL MILL SPECIFICATIONS PERFORMANCE ANALYSIS Typical Coal Pulveriser Mill Details in 660 MW SuperCritical [3] Unit is as given in table Table No 1 Table1 Coal mill Type Bowl Type Mediumspeed Coal mill Number of Mills 6set/ boilerPulveriser Mill Performance Analysis Optimisation in Super 2014年3月1日 JKMRC of Queensland University is the only reported research team who got the samples from the industrial mill and analyzed the actual operation condition of the coal mill [13], [14] Comparing to the E ball mill of Tarong power plant in Australia, the mediumspeed mills have several significant advantages, which are widely used recentlyBreakage and separation mechanism of ZGM coal mill based on
.jpg)
Coal IJSER
Optimization Control for Coal Mill Fault Diagnosis in CoalFired Steam Power Plant Ronny Cahyadi Utomo1, 2, a) In the operation of 4 coal mill units, delays and selfcombustion often occurred due to using LowRank Call on the analysis of primary air 2023年10月11日 The Effect of Surface Finish and Fillet Design on Tie Rod Shaft Lifetime at Coal Mill Plant Operation October 2023; DOI technique for the stress analysis needed in shape design optimizationThe Effect of Surface Finish and Fillet Design on Tie 2014年12月31日 The reserves of natural gas, an important clean fuel, are recognized to be relatively limited compared to coal [1], [2]In 2013, according to a report from the International Energy Agency (IEA) [2], the global reservestoproduction ratio of conventional gas was in the range of 55–60 years while the global reservestoproduction ratio of coal was in the range of Coal to SNG: Technical progress, modeling and system optimization 2022年3月25日 Under a given production running condition, the electricity current intensity of the coal mill decreases from 479 AM to 465 AM, which is a remarkable achievement for the coal mill running process(PDF) A Modeling and Optimizing Method for Electricity Current
.jpg)
Derivation and validation of a coal mill model for control
2012年5月1日 Coal fired power plants are heavily used due to large and long lasting coal resources compared with oil or natural gas An important bottleneck in the operation of this particular kind of plants, however, is the coal pulverization process, which gives rise to slow takeup rates and frequent plant shutdowns (Rees Fan, 2003)In typical coal fired power plants, 2023年9月1日 SOx removal and emission characteristics of WFGD system applied in ultralow emission coalfired power plants Case Stud Therm Eng, 28 (2021), Article View PDF View article View in Operation optimization and costs analysis of the wet desulfurization system in an ultrasupercritical coalfired power plants Environ Operation analysis and its performance optimizations of the 2022年5月31日 Mineral crushing is the main source of energy consumption in mineral processing According to statistics, this consumption accounts for about 35–50% of the total cost of the mine (Curry et al, 2014), or even higherIt may also account for 18% of the global electrical energy consumption (NapierMunn, 2015)More efficient crushing equipment needs to be Analysis of vertical roller mill performance with changes in 2023年2月27日 Optimization Analysis of Power CoalBlending Model and Its Control System Based on Intelligent Sensor Network and Genetic Algorithm February 2023 Journal of Sensors 2023(6):111(PDF) Optimization Analysis of Power CoalBlending Model and

Breakage and separation mechanism of ZGM coal mill based
2014年3月1日 Also, Özer inverstigated the classification operation in a coal pulverizing VSM and evaluated classification efficiency based on settling velocities of particles [9,10] Wei et al calculated the air classifier efficiency in a ZGM coal mill by the fitting method, and its classification mechanism was revealed [11]For the [O] and [OH] groups, the partial equilibrium method is used Fuel type NO is mainly generated by the pyrolysis and oxidation reaction of nitrogen in fuel, which is theCombined operation mode of subcritical Wflame boiler and coal mill During normal operation, the mill pressure drop is predominately proportional to the primary air differential pressure Wenjian Cai, Hongbo Liu(2009), “Coal mill control and optimization using a multilayer structure”, Global Home » SWOT articles » SWOT Analysis of HM SWOT Analysis of HM fan boy download Download free PDF (PDF) Modeling and Control of Coal Mill Academia2013年3月1日 Therefore, for coal mill control the application of NMPC is a recommended solution 8 Conclusions In the present paper, the modeling of a vertical roller pressure coal mill was addressed As a result, a nonlinear model has been developed and validated to predict the coal mill behavior during start up and normal operationNonlinear coal mill modeling and its application to model
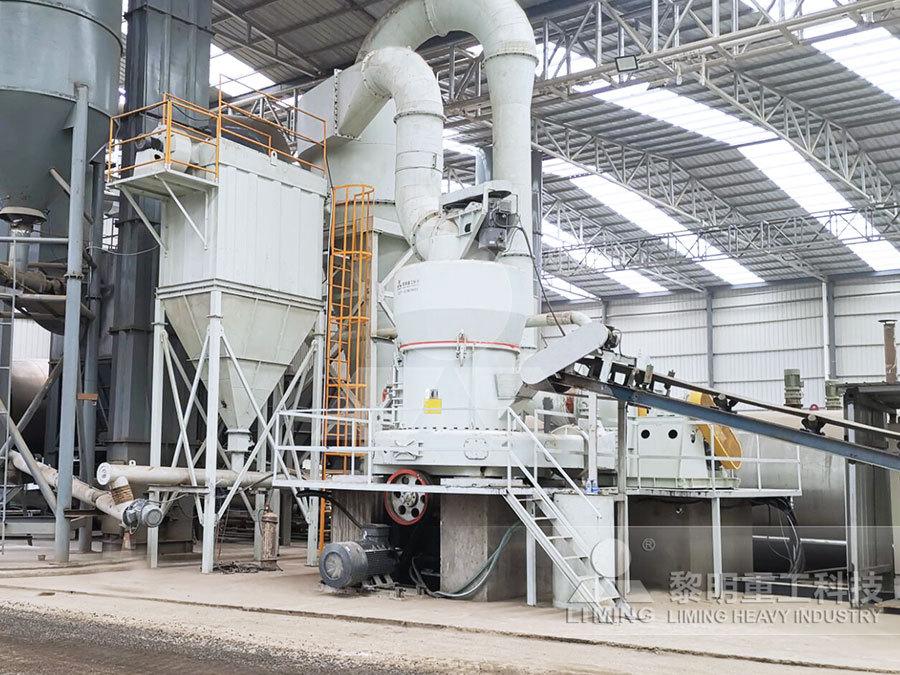
Full MinetoMill Optimization Continuous
2023年10月16日 Chapada's open pit coppergold mine and processing plant commenced operation in 2007 As mining has progressed deeper the ore hardness has increased, adversely impacting plant throughput2011年10月1日 According to analysis, coal mill and primaryair fan are the two main energy consumption The Modeling and Operation Optimization Strategy for the Pulverizing System of Medium Speed Mill EnergySaving and Optimization of Pulverizing System in Coal 2018年12月12日 The production cycle of opencast coal mines generally includes drilling, blasting, loading, hauling and coal preparation activities Individual optimization of these activities does not mean that the whole system is optimized This paper proposes a cost model considering all activities in mining cycle and systemwide approach to minimize the total mining cost of A systemwide approach to minimize the operational cost of 2018年7月1日 Factors affecting the operation of boiler safety, economy and environment is complex, involving the furnace combustion process optimization adjustment, slagging in the furnace, dust, corrosion and wear, such as process, and the flue gas temperature deviation, temperature deviation, and the coal pulverizing system and other auxiliary system safe and Coalfired Utility Boiler Operation Factors Analysis and Optimization
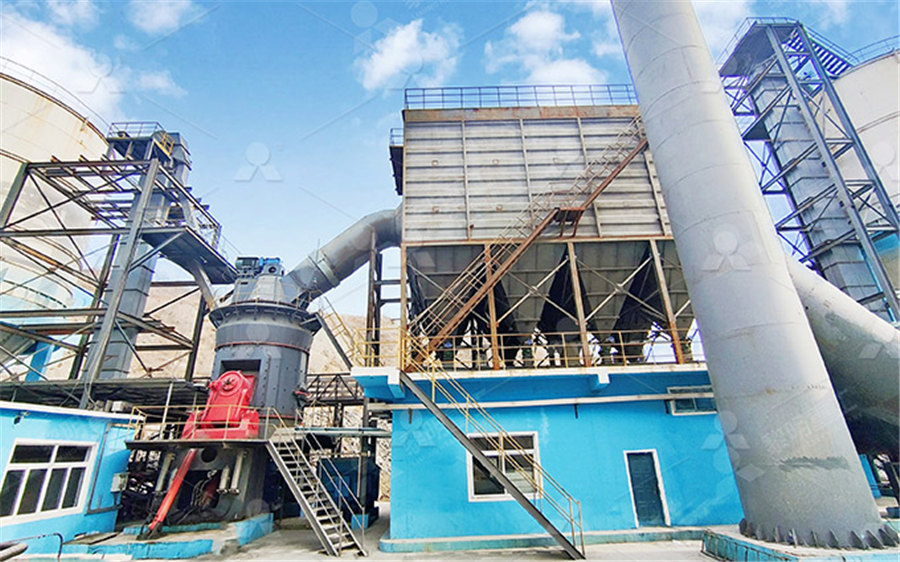
(PDF) Operation and Maintenance of Coal Handling System in
2011年12月31日 Dual drums head actuations Fig3 Head and tail actuations 1 actuation drums one; 2 coupling; 3 peed reducer; 4 motor; 5 fluid coupling; 6 actuations drum two2009年9月20日 A control oriented model was then developed by Fan (1994) and Fan and Rees (1994) In 2009, coal flow and outlet temperature of mill were modelled using mass and heat balance equations for startup Modeling and Parameter Identification of Coal Mill2024年1月5日 Thermodynamic analysis and operation strategy optimization of coupled molten salt energy storage system for coalfired power plant Author links open overlay panel Bo Li, Yue Cao, Peak shaving operational optimization of supercritical coalfired power plants by revising control strategy for waterfuel ratio Appl Energy, 216 Thermodynamic analysis and operation strategy optimization of DOI: 101016/japt2023 Corpus ID: ; Operation parameters multiobjective optimization method of large vertical mill based on CFDDPM @article{Huang2023OperationPM, title={Operation parameters multiobjective optimization method of large vertical mill based on CFDDPM}, author={Rongjie Huang and Yao Ma and Hao Li and Chunya Sun and Jun Liu and Operation parameters multiobjective optimization method of
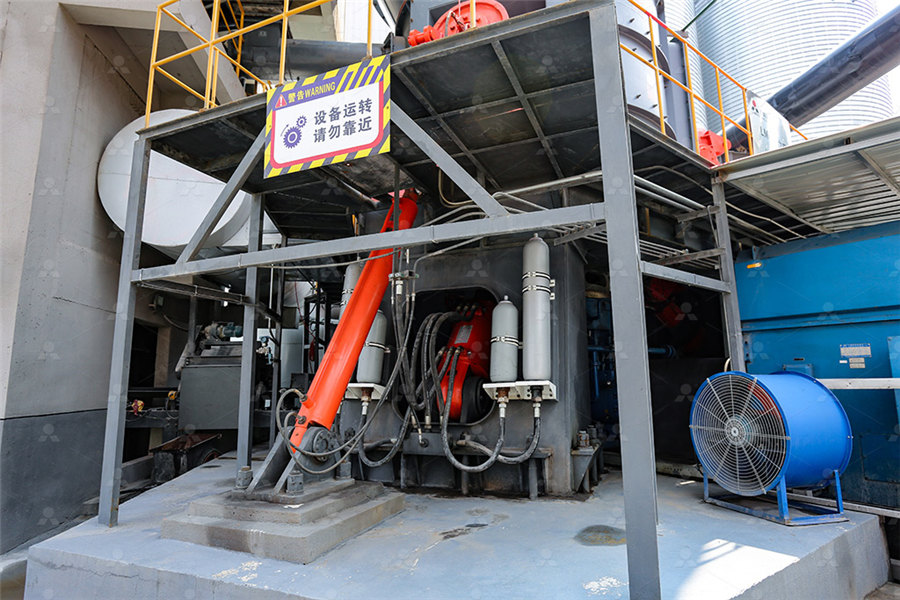
(PDF) Study the kinetics involved in solid state reduction of mill
2021年2月1日 Based upon the analysis the optimized parameters obtained were temperature (at 1000 °C), mill scale to coal ratio (minimum 1:3), time (minimum 180 min), and mill scale size (minimum 425 to 600 µm)Multiobjective Optimization of Coal Mill Outlet Temperature Control Using MPC Zengji Zhang1, Yicheng Zhang2, Wei Shen2, BOE Xukang Lyu3,∗ 1Sinoma International Engineering Co, Ltd, Nanjing, Jiangsu, China 2College of Computer Science and Technology, Zhejiang SciTech University, Hangzhou, Zhejiang, China 3Zhejiang New Rise Digital Technology Co, Ltd, MultiObjective Optimization of Coal Mill Outlet Temperature Gas flow through mill (m 3 /h) or mill fan power (kw) Mill DP, or inlet/outlet draft (mmH2O) Separator DP (mmH 2 O, mbar) and temperatures (0 C) Bag filter DP (mmH 2 O, mbar), Temperature (0 C) Coal Mill Safety parameters: Position of Explosion vents Operational readiness of quick shutoff dampers Inertization section readiness (N2, CO2 Coal Grinding Cement Plant Optimization2017年1月1日 An increase of over 10% in mill throughput was achieved by removing the ball scats from a single stage SAG mill These scats are non spherical ball fragments resulting from uneven wear of balls (PDF) Performance optimization of an industrial ball mill for
.jpg)
Operation Analysis of a SAG Mill under Different Conditions Based on
2020年10月9日 As one of the machines widely used in mining, a semiautogenous grinding (SAG) mill can significantly improve the roughing efficiency of rock But the SAG mill still faces the obstacles of significant energy consumption and empirical operation parameters In order to obtain the optimal operation parameters of a SAG mill, in this paper, the discrete element 2022年7月26日 Aiming at the typical faults in the coal mills operation process, the kernel extreme learning machine diagnosis model based on variational model feature extraction and kernel principal component analysis is offered Firstly, the collected signals of vibration and loading force, corresponding to typical faults of coal mill, are decomposed by variational model Fault Diagnosis of Coal Mill Based on Kernel Extreme Learning1997年8月1日 Analysis of coal Mill Dynamic Characteristics Technical University of Denmark Zhao, H (1995) Analysis, Modelling and Operational Optimization of District Heating Systems which controls the air to coal ratio in a predefined range for efficient coal grinding, coal moisture drying and mill operation safety (Fig2b Analysis of coal Mill Dynamic Characteristics Under Normal and A mill’s heat balance evaluation was done using an Excel spreadsheet to evaluate the mill drying capacity constraint Coal analysis was done on hard grove grind ability, abrasive indices and calorific value of coal The effect of low calorific value coal was observed on mill’s response to match the boiler energy requirementsPerformance optimisation of vertical spindle coal pulverisers
.jpg)
A statistical analysis and optimization of Indian coal grinding in a
S Gautam et al: A statistical analysis and optimization of Indian coal grinding in a laboratory ball mill 52 wet methods was found using BoxBehnken design and ANOVA MATLAB code and Microsoft Excel were used to regress from the model Standard Bond grindability test for coal The Bond grindability test is a closed loop