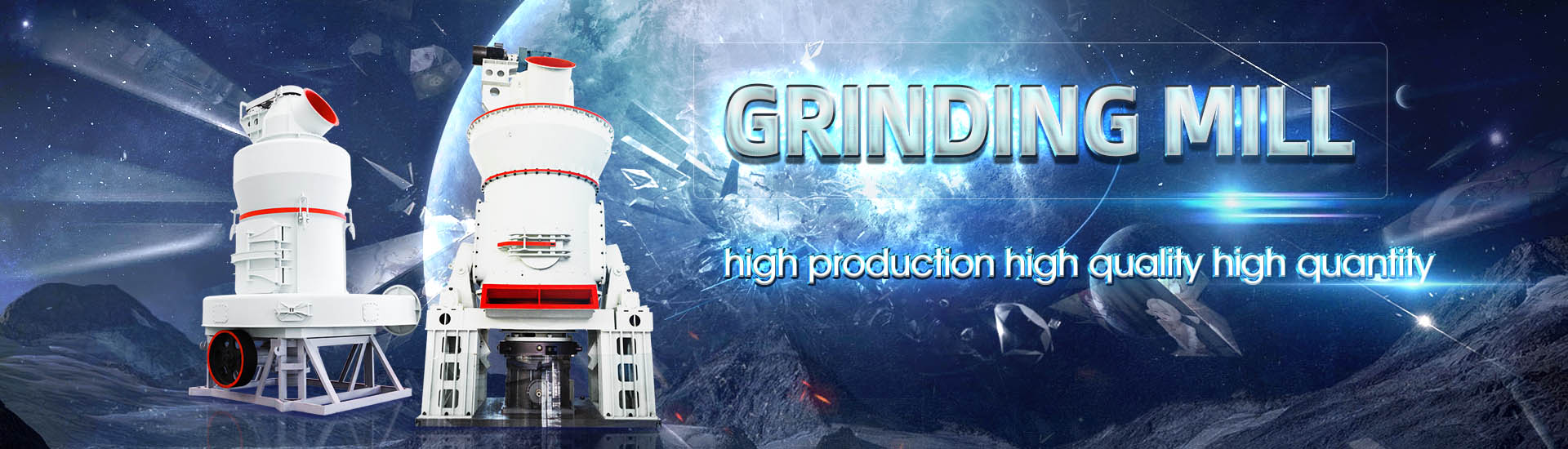
Cement mill process management
.jpg)
The Cement Plant Operations Handbook International
2 天之前 The Cement Plant Operations Handbook is a concise, practical guide to cement manufacturing and is the standard reference used by plant operations personnel worldwide From forecasting and planning, scheduling and optimizing work assignments, to dispatching work to maintenance and field crews, work order processing, and performance measurement, all activities require a consistent, organized and Cement manufacturing operations management 1987年8月1日 Cement manufacturing process is now operated with the aid of various control systems, such as raw meal composition control, kiln control and mill control Those systems Optimization of Cement Manufacturing Process ScienceDirect2021年3月12日 Ball mill optimisation As grinding accounts for a sizeable share in a cement plant’s power consumption, optimisation of grinding equipment such as ball mills can provide BALL MILLS Ball mill optimisation Holzinger Consulting
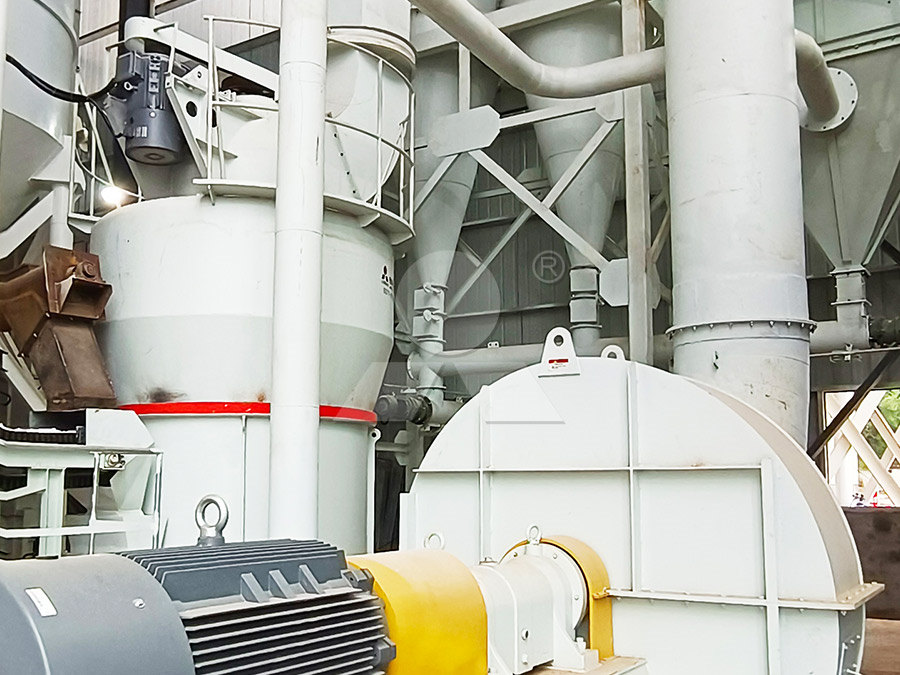
(PDF) Process Automation of Cement Plant
2012年4月30日 The objective of this article is the development of a novel raw material mix proportion control algorithm for a cement plant raw mill, so as to maintain preset target mix proportion at the raw2023年6月19日 Cement is paramount for economic development and poverty reduction in emerging markets Along with aggregates and water, cement is the key ingredient in the IMPROVING THERMAL AND ELECTRIC ENERGY 2024年5月22日 The cement production process 1 The Quarry: The cement production process begins with the extraction of limestone and clay from the quarry 2 Crusher and PreBlending: A practical guide to improving cement manufacturing 2019年8月26日 Cement Manufacturing and Process Control 41 Cement Manufacturing: Basic Process and Operation To design the Refractory for the lining of different equipments in a Chapter 4 Cement Manufacturing and Process Control
.jpg)
Cement Manufacturing—Technology, Practice, and
2021年11月17日 A cement manufacturing process is well suited for coprocessing of wastes from different sources Wastes need to be converted into alternative fuels and raw materials 2020年10月30日 Dirk Schmidt and Eugen Geibel, KIMA Process Control, discuss how the methods of HighLevel Control (HLC) have been used in the cement industry in the early 2000s and control ever more complex closedloop Highlevel control in cement production World Chemical process industries are running under severe constraints, and it is essential to maintain the endproduct quality under disturbances Maintaining the product quality in the cement grinding process in the presence of clinker Predictive Controller Design for a Cement Ball 2021年3月12日 process Together with ball charge composition, both tools – liners and media – can be optimally adjusted for the application They can then fulfil the Figure 2: ball mill tools and comminution process Figure 1: ball mill communition process chain Ball charge management grinding Ventilation and cooling Operation and controlBALL MILLS Ball mill optimisation Holzinger Consulting
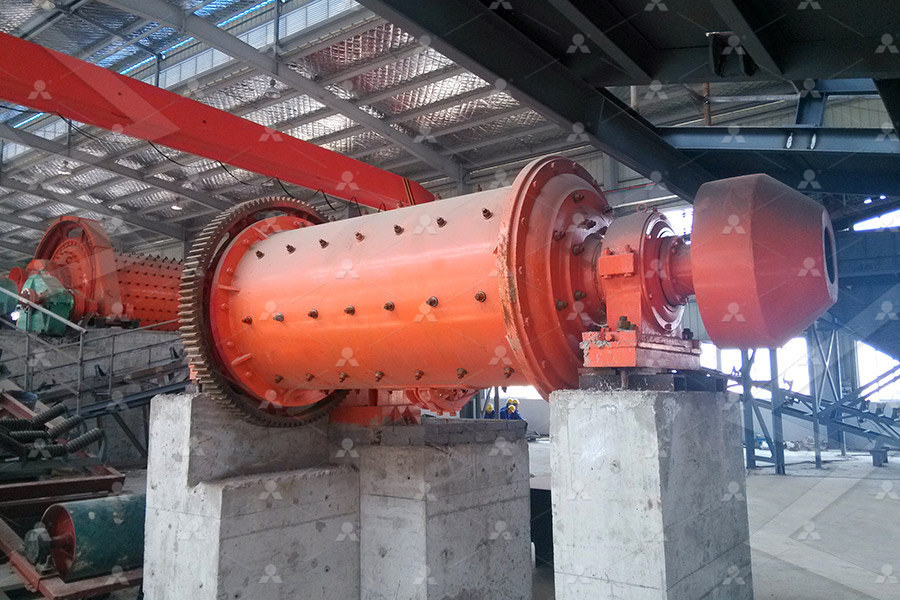
The cement mill Understanding Cement
Cement manufacturing brief description of a cement mill Cement clinker is usually ground using a ball mill This is essentially a large rotating drum containing grinding media normally steel balls As the drum rotates, the 2023年6月19日 251 Process Control and Management in Finish Grinding 24 252 Replacing a Ball Mill with a Vertical Roller Mill, HighPressure Grinding Rolls, 257 HighEfficiency Fans for Cement Mill Vents 34 ii Improving Thermal and Electric Energy Efficiency at Cement Plants: International Best Practice 26 IMPROVING THERMAL AND ELECTRIC ENERGY 2014年3月1日 Based on a dynamical model of the grinding process in closed circuit mills, efficient efforts have been made to optimize PID controllers of cement milling The process simulation is combined with an autoregressive model of the errors between the actual process values and the computed ones Long term industrial data have been used to determine the Optimizing the control system of cement milling: process 2023年8月29日 separators, grinding rolls, vertical roller mills, 5 stage suspension preheater with precalcinators etc can help in achieving substantial energy savings as outlined in the following sections Typical power consumption per tonne of cement in different unit operations is given below Cement Mill 33% Raw Mill 24% Kiln 23%Optimizing Electrical Energy Consumption In Cement
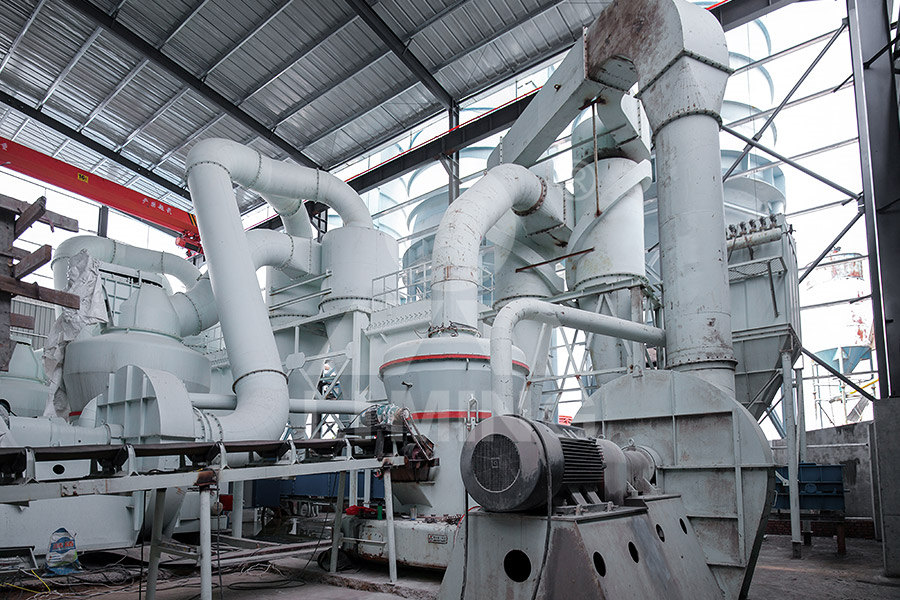
PROCESS DIAGNOSTIC STUDIES FOR CEMENT MILL
2013年3月13日 PROCESS DIAGNOSTIC STUDIES FOR CEMENT MILL OPTIMISATION CASE STUDY VK Batra*, D Bhaskara Rao** and Raju Goyal*** Holtec Consulting Private Ltd, New Delhi Group Manager *** Manager The various types of grinding systems currently being used for cement grinding in a cement plant are:Providing Consistent Results With Advanced Vertical Cement Mill Technology Magotteaux’s advanced vertical cement mill technology ensures consistent results by providing precise control over the grinding process, enabling the production of highquality cement with minimal variations in finenessMoreover, our use of advanced materials and innovative designs ensures that our Vertical Cement Mill Magotteaux6 Raw material mill This takes places in vertical steel mill, which grinds the material through the pressure exerted by three conical rollers Which roll over a turning milling table Horizontal mills, inside which the material is pulverized by means of steel balls, are also used in this phaseCement Production: How Cement Is Manufactured CEMEX UKThe grinding process in cement mills consumes a significant amount of energy and has a direct impact on the overall efficiency of the mill By optimizing the grinding process, cement manufacturers can achieve higher productivity and lower energy consumption Let’s explore some practical strategies with realworld figures and numbers:Cement Mill Optimization: Practical Strategies for Enhanced
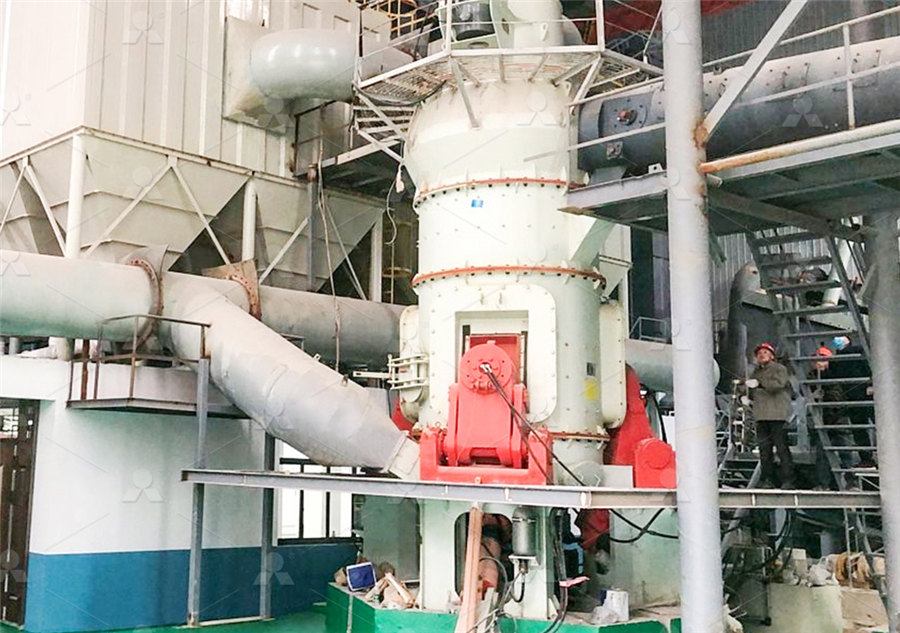
Cement Manufacturing—Technology, Practice, and
2021年11月17日 Pozzolanic and other minerals are fed to the cement mill Being a process in which a large quantum of materials get processed and produced in a continuous mode at hightemperature gas retention times, cement kilns can have a large capability of utilizing a variety of materials Practice, and Development In: Sustainable Management of Wastes The power ingesting of a grinding process is 5060% in the cement production power consumption The Vertical Roller Mill (VRM) reduces the power consumption for cement grinding approximately 3040% associated with other grinding mills The process variables in cement grinding process using VRM are strongly nonlinear and having large time delay characteristics PROCESS CONTROL FOR CEMENT GRINDING IN VERTICAL ROLLER MILL The seminar offers classroom instruction from FLSmidth specialists and case studies based on real situations at different cement plants Work sessions are scheduled to allow for an interactive study of the design, function, and evaluation of pyroprocess systems in a cement plantCement Production Seminar: Pyroprocess FLSmidth CementThe efficiency and quality of the raw milling process significantly depend on maintaining optimal moisture levels High moisture content can lead to operational inefficiencies, increased energy consumption, and issues with product quality Successful Moisture Management in Cement Plants 51 Case Study: Rotary Dryer Implementation in a Raw Mill Moisture Content Management: A Comprehensive
.jpg)
A practical guide to improving cement manufacturing
2024年5月22日 The cement production process 1 The Quarry: The cement production process begins with the extraction of limestone and clay from the quarry 2 Crusher and PreBlending: The material is then crushed to reduce particle sizes and blended to reduce variability in composition 3 Raw Mill and Kiln: Raw materials and additives are2024年1月18日 The use of fossil fuels such as coal, natural gas, and oil is common in cement production, both as a fuel for the kiln and as a source of heat for other parts of the process which leads to CO2 emitted by combustionHowever chemical reactions happening in the kiln (calcination) are also responsible for up to 60% of the total of emissions of the Cement Production Demystified: StepbyStep Process and Our Process Management systems transform process and quality data into realtime operations intelligence Products Products Crushing OK™ Raw and Cement Mill Alternative fuels storage Feedex® Overhead Reclaimer Belt weighfeeders Smart Linear Feeder (SLF) Rotor weighfeeders DRW rotor weighfeederProcess data management and insights FLSmidth CementTokyo Japan 1986 OPTIMIZATION OF CEMENT MANUFACTURING PROCESS G Nakamura, T Aizawa and K Nakase Onoda Cement Co, Ltd, 117, Toyosu Kotoku, Tokyo,japan Abstract Cement manufacturing process is now operated with the aid of various control systems, such as raw meal compositi on control, kiln control and mill controlOptimization of Cement Manufacturing Process ScienceDirect
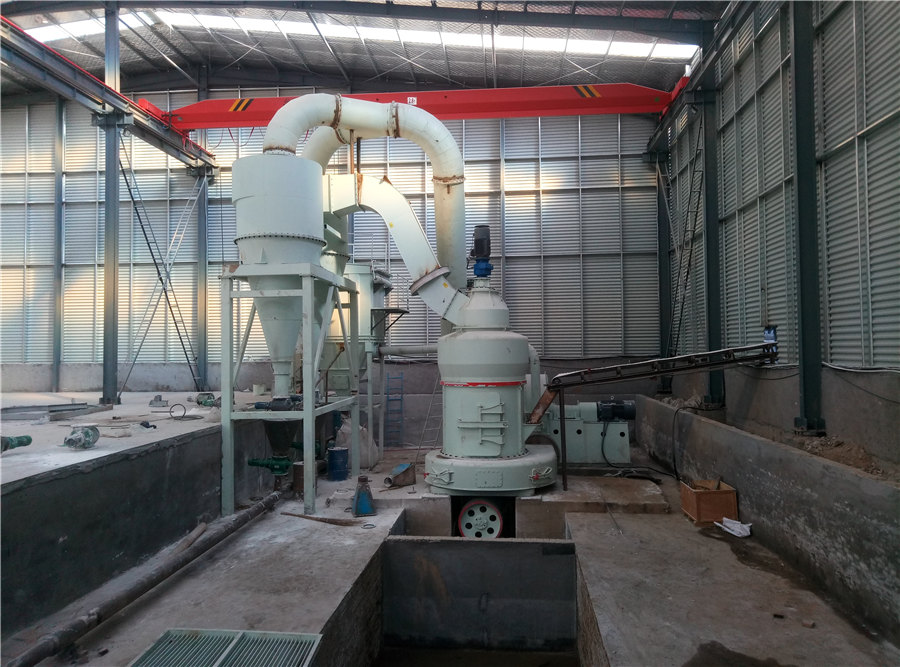
Review on vertical roller mill in cement industry its
2021年1月1日 In dry process technology, crushed limestone and raw materials are ground and mixed without addition of water Dry and semiwet processes are more energyefficient The wet process requires 028 tons of coal and 110 kWh to produce one ton of cement, while the dry process requires only 018 tons of coal and 100 kWh of energy [4]2021年1月28日 “Holderbank” Cement Seminar 2000 Process Technology Roller Mills ¢ Material circulation: The material, which flows over the dam ring is caught by the vertical gas flow from the nozzle ring and lifted up Coarser particles fall back to the grinding table and finer ones are swept up to the separator for being classifiedHolderbank Cement engineering bookSpecifically designed for the challenges faced by the cement industry, our ECS/ProcessExpert solution the software commonly referred to as "PXP" is your platform for improved performance Based on stateoftheart process Process control and optimisation FLSmidth The cement plant has production machines with high noise level The noisy environment will arise risks on workers The purpose of this study was to determined noise level and its effect on workers in a cement plant The noise intensity was measured at three area of the plants ; raw mill, cement mill, and sillo raw mix(PDF) Environmental and Occupational Noise Management Process in Cement
.jpg)
Strategising Dust Management Indian Cement
2024年4月17日 ICR delves into the multifaceted aspects of dust control in cement manufacturing, from environmental and health hazards to regulatory standards and innovative technologies By exploring dust generation sources, 2020年9月16日 It has also recently implemented an advancedprocesscontrol tool for kiln flame and cement mill management The plant has a central control room for monitoring all plant operations, and operators huddle daily to review shift results on a digital screen The maintenance department feeds manual inspection logs into a reliability tool, which Digitization and the future of the cement plant McKinsey2021年6月1日 The cement production process passes through numerous workstations, including crushing raw materials, grinding raw materials, burning the materials in a rotary kiln, grinding cement in the mills Implementation of Lean Manufacturing in a Cement Industry5 天之前 The Fig1 show the flow diagram of the dry process of the manufacture of cement 1 Dry Process In the dry and semidry process the raw materials are crushed in a dry state Then, they are processed in grinding mill, dried and reduced to very fine powderlike That dry power is further blended, corrected for the right composition and mixed Manufacturing of Portland Cement – Process and Materials
.jpg)
Ball mills FLSmidth Cement
An inefficient ball mill is a major expense and could even cost you product quality The best ball mills enable you to achieve the desired fineness quickly and efficiently, with minimum energy expenditure and low maintenance With more than 4000 references worldwide, the FLSmidth ball mill is proven to do just thatPart Three: Raw Mill Process of Raw Mill The proportioned raw material is feed first to a grinding mill In the mill, particles ground in to very fine sizes In the grinding unit, drying, grinding and mixing takes place simultaneously Hot gas from clinker burning unit is passed into the grinding unit to assist the drying and grinding processCement Manufacturing Process INFINITY FOR CEMENT EQUIPMENT2023年7月10日 Cement manufacturing is a significant industrial activity that plays a vital role in the construction sector However, the process of cement production is associated with various environmental Cement Manufacturing Process and Its Environmental Impact2024年9月1日 hardest materials The OK™ cement mills are available in all sizes 0 100 200 300 400 500 600 700 800 OK 776 OK 434 OK 484 OK 404 OK 524 OK 716 OK 816 OK 666 OK 614 OK 564 OK ™ cement mill production and slag grinding production (t/h) OK 283 OK 373 OK ™ cement mill and slag grinding Actual capacity depends on product fineness OK™ CEMENT MILL
.jpg)
Predictive Controller Design for a Cement Ball
Chemical process industries are running under severe constraints, and it is essential to maintain the endproduct quality under disturbances Maintaining the product quality in the cement grinding process in the presence of clinker 2021年3月12日 process Together with ball charge composition, both tools – liners and media – can be optimally adjusted for the application They can then fulfil the Figure 2: ball mill tools and comminution process Figure 1: ball mill communition process chain Ball charge management grinding Ventilation and cooling Operation and controlBALL MILLS Ball mill optimisation Holzinger ConsultingCement manufacturing brief description of a cement mill Cement clinker is usually ground using a ball mill This is essentially a large rotating drum containing grinding media normally steel balls As the drum rotates, the The cement mill Understanding Cement2023年6月19日 251 Process Control and Management in Finish Grinding 24 252 Replacing a Ball Mill with a Vertical Roller Mill, HighPressure Grinding Rolls, 257 HighEfficiency Fans for Cement Mill Vents 34 ii Improving Thermal and Electric Energy Efficiency at Cement Plants: International Best Practice 26 IMPROVING THERMAL AND ELECTRIC ENERGY
.jpg)
Optimizing the control system of cement milling: process
2014年3月1日 Based on a dynamical model of the grinding process in closed circuit mills, efficient efforts have been made to optimize PID controllers of cement milling The process simulation is combined with an autoregressive model of the errors between the actual process values and the computed ones Long term industrial data have been used to determine the 2023年8月29日 separators, grinding rolls, vertical roller mills, 5 stage suspension preheater with precalcinators etc can help in achieving substantial energy savings as outlined in the following sections Typical power consumption per tonne of cement in different unit operations is given below Cement Mill 33% Raw Mill 24% Kiln 23%Optimizing Electrical Energy Consumption In Cement 2013年3月13日 PROCESS DIAGNOSTIC STUDIES FOR CEMENT MILL OPTIMISATION CASE STUDY VK Batra*, D Bhaskara Rao** and Raju Goyal*** Holtec Consulting Private Ltd, New Delhi Group Manager *** Manager The various types of grinding systems currently being used for cement grinding in a cement plant are:PROCESS DIAGNOSTIC STUDIES FOR CEMENT MILL Providing Consistent Results With Advanced Vertical Cement Mill Technology Magotteaux’s advanced vertical cement mill technology ensures consistent results by providing precise control over the grinding process, enabling the production of highquality cement with minimal variations in finenessMoreover, our use of advanced materials and innovative designs ensures that our Vertical Cement Mill Magotteaux
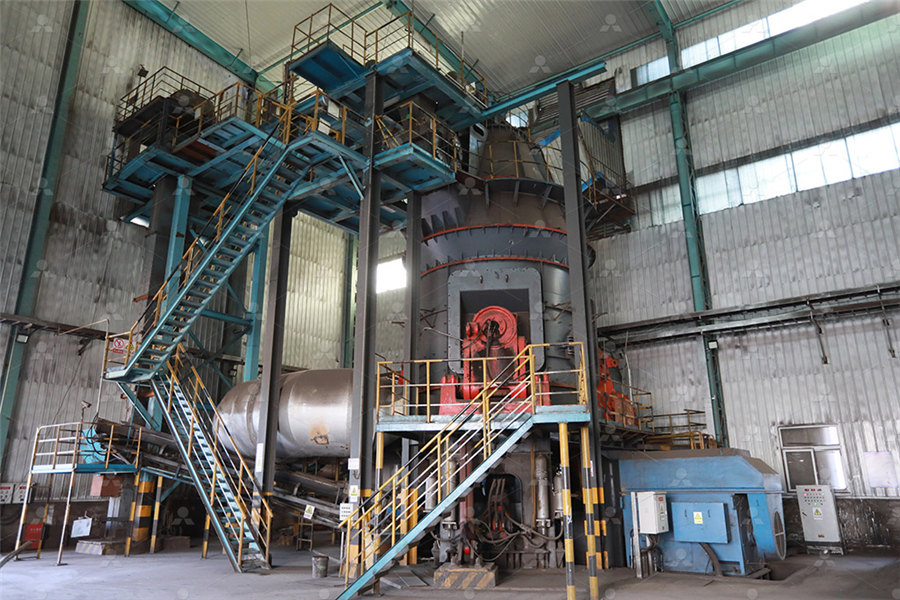
Cement Production: How Cement Is Manufactured CEMEX UK
6 Raw material mill This takes places in vertical steel mill, which grinds the material through the pressure exerted by three conical rollers Which roll over a turning milling table Horizontal mills, inside which the material is pulverized by means of steel balls, are also used in this phaseThe grinding process in cement mills consumes a significant amount of energy and has a direct impact on the overall efficiency of the mill By optimizing the grinding process, cement manufacturers can achieve higher productivity and lower energy consumption Let’s explore some practical strategies with realworld figures and numbers:Cement Mill Optimization: Practical Strategies for Enhanced