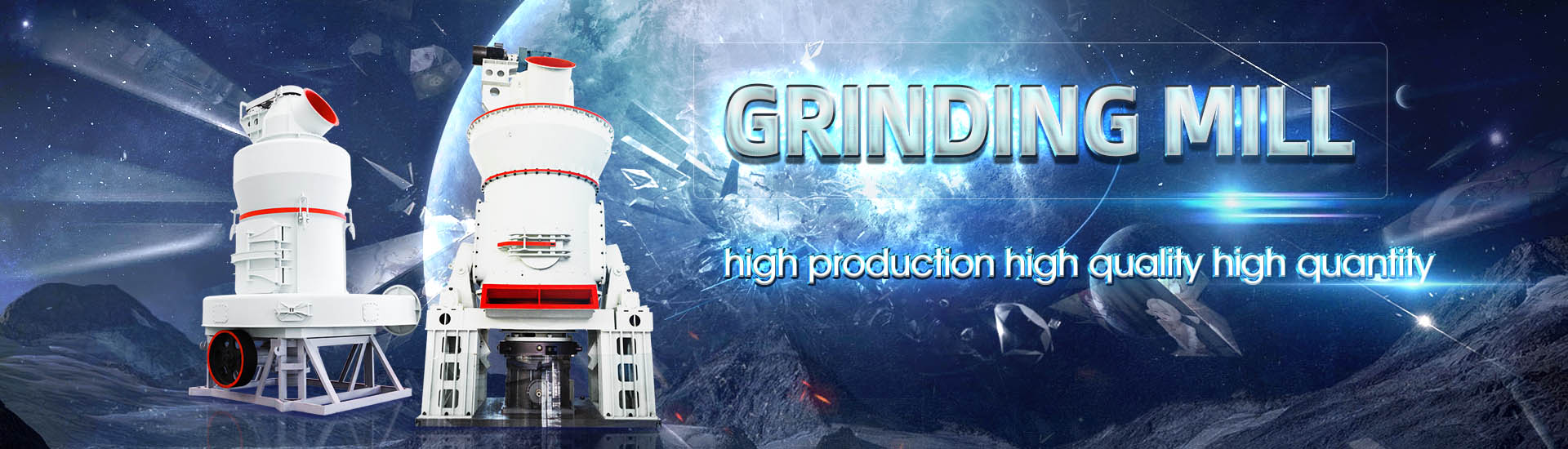
Electrolytic aluminum waste slag grinding machine Ore grinding machine operating procedures
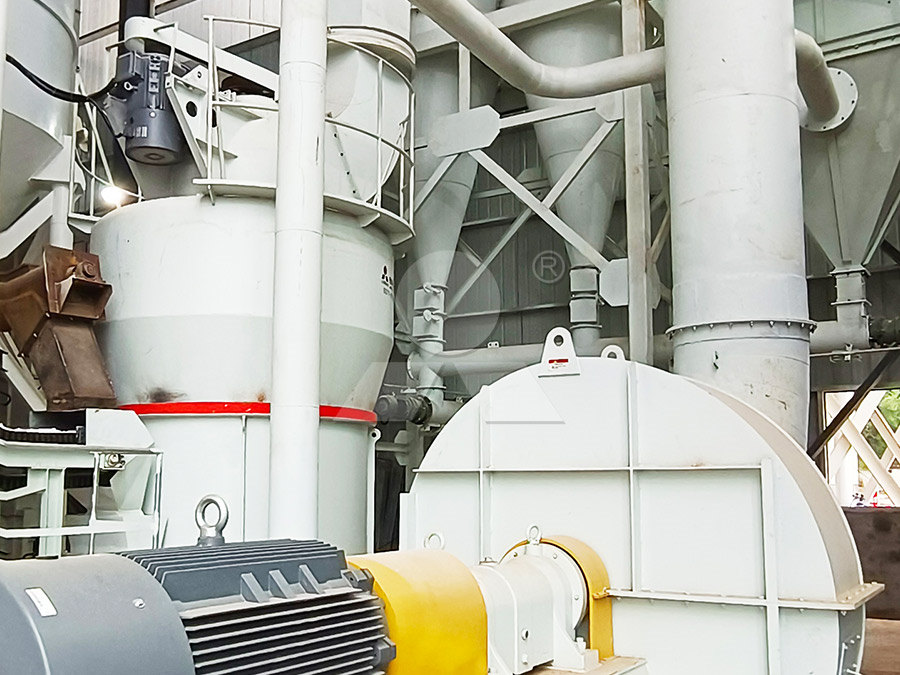
Research Progress of Electrolytic Aluminum Overhaul Slag Disposal
2023年4月25日 This article analyzes and summarizes the composition and hazards of the overhaul slag and the current development status of domestic and international electrolytic 2023年3月12日 The selective comminution of carbon and cryolite particles in carbon anode slag can be effectively achieved with grinding pretreatment However, the optimization study of (PDF) Recovery of Carbon and Cryolite from Spent Carbon Anode 2023年8月1日 The main components of overhaul slag are aluminum and silicon oxides These components could be dissolved in the molten cryolitebased salt system (ie, electrolyte) in the Dissolution behavior of overhaul slag from aluminum reduction 2022年10月10日 In this work, electrolytic aluminum carbon anode slag was separated by flotation Using the selectivity index ( SI ) as an indicator, the influencing factors of the carbon Recovery of carbon and cryolite from spent carbon anode slag of

Efficient lithium recovery from electrolytic aluminum slag via an
2024年2月1日 The electrolytic aluminum industry generates a large amount lithium (Li)containing electrolytic aluminum slag (EAS) annually, and this can result in severe 2024年5月23日 Here, we review carbonrich solid wastes with focus on sources and hazards, detoxification, separation, recovery, recycling and disposal Treatment techniques include The recycling of carbonrich solid wastes from aluminum 2020年8月1日 Here, we discuss the influence of different processing parameters on electrolytic refining of aluminum alloy and investigate the mechanism of extracting Al from coarse AlSi Recovery of aluminum from waste aluminum alloy by low 2022年4月13日 Here we propose a solidstate electrolysis (SSE) process using molten salts for upcycling aluminium scrap The SSE produces aluminium with a purity comparable to that of A solidstate electrolysis process for upcycling aluminium scrap
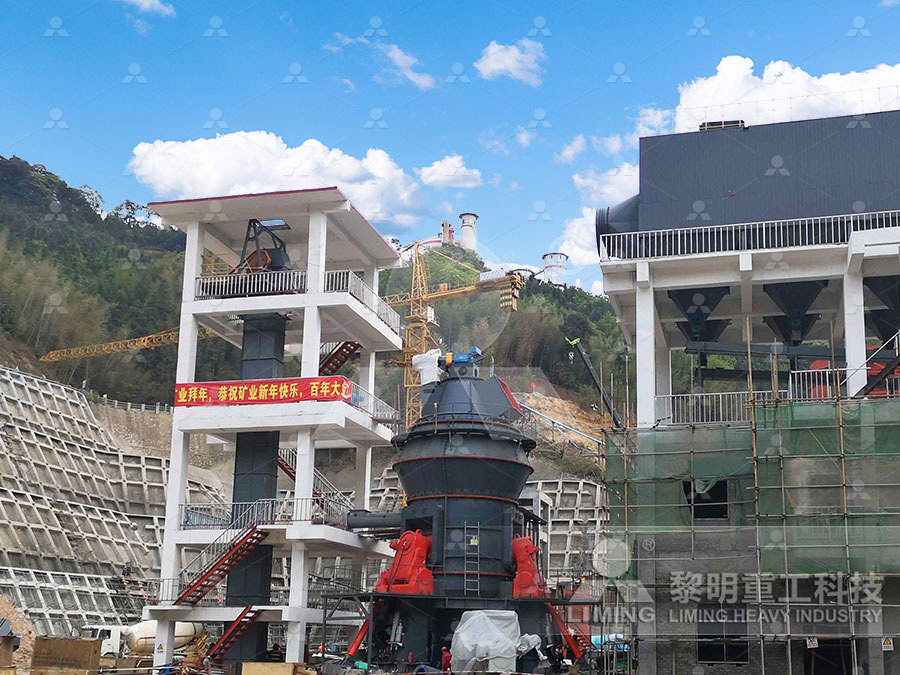
Selective comminution and grinding mechanisms of spent carbon
In this study, grinding characteristics of spent carbon anode from aluminum electrolysis in both ball mill and rod mill were analyzed, and compared based on the utilization of the selectiveWhat Is Grinding Slag Removal? Slag is a specific type of sand that’s traditionally made from steel It often forms as a coarse waste product resulting from deburring or smelting processes To remove slag, metal processing facilities require grinding and slag removal Slag grinding processes efficiently remove all of the heavy slag produced Grinding Slag Removal Apex Machine Group2022年1月10日 The recovery of spent carbon anode (SCA) materials plays important roles in environment protection and resources recycling, while this cannot be efficiently achieved without liberationSelective comminution and grinding mechanisms of A Closer Look at ECG (Electrochemical Grinding) In comparison to electrochemical machining, electrochemical grinding is relatively similar Basically, it is a combination of an electrochemical process and a grinding What You Need To Know About Electrochemical
.jpg)
Grinding Machine: Definition, Parts, Working Principle, Operation
2021年5月5日 The Grinding Machine is another most important machine in the manufacturing Industry Today we will study the Definition, Parts, Working In this article I There are four commonly used abrasive materials for the surface of the grinding wheels are Aluminum oxide, silicon carbide, cubic boron nitride (CBN), and diamondJune 2022; ARCHIVE Proceedings of the Institution of Mechanical Engineers Part C Journal of Mechanical Engineering Science 19891996 (vols 203210) 236(2):1107(PDF) A comprehensive review on the grinding process: 2024年1月23日 Basic Grinding Machines: Entrylevel grinding machines, suitable for smallscale operations or less complex tasks, typically range from $5,000 to $20,000 MidRange Grinding Machines: These machines, offering more features and greater precision, are generally priced between $20,000 and $60,000What is Grinding: Definition, Process, Types Specifications2022年10月10日 The comprehensive recovery and utilization of electrolytic aluminum spent carbon anode slag (Hereinafter simplified as “carbon anode slag”) are therefore necessary Flotation is a physical separation method used to separate particles by using the difference in surface property of particles ( Chen et al, 2022 ; Ni et al, 2022 )Recovery of carbon and cryolite from spent carbon anode slag of
.jpg)
Research on Using Carbide Slag to Mineralize the Carbon Dioxide
2024年2月2日 Calcium carbide slag is a difficult industrial waste to treat Millions of tons of calcium carbide slag are piled up in China yearly, occupying a large amount of land and easily causing secondary pollution []The main component of calcium carbide slag is Ca(OH) 2, with 71–95% content []Therefore, the current recycling methods of calcium carbide slag mainly 2024年1月27日 H3: Grinding Machine History and Developments from Ancient Times to Modern Days The evolution of grinding machines is marked by several key developments: Ancient Times: The origins of grinding can be traced back to ancient civilizations where What is a Grinding Machine: Definition, Types, Componentsfor electrolytic aluminum waste is proposed This mode is to pulverize the electrolytic aluminum waste, and then mix the crushed electrolytic aluminum waste with the raw coal of the circulating fluidized bed boiler [6], then send it to the circulating fluidized bed boiler for combustion In this study, a mixed combustion experiment ofResearch on the Coprocessing of Mixed Electrolytic Aluminum Waste 2020年4月7日 ZG35Cr25Ni20 electrolytic aluminum slag grab, with its excellent high temperature resistance and corrosion resistance, is unique in the electrolytic aluminum industry The grapple is made of highquality 310S heatresistant steel castings, which maintain excellent stability in hightemperature environments, ensuring that the grapple can operate stably in Electrolytic Aluminum Slag Grab Sino Machine
CFB石灰石脱硫剂制备——磨机公众号12.8 推送案例(8)53.jpg)
Chapter 17: Grinding Methods and Machines
2020年6月29日 Grinding, or abrasive machining, once performed on conventional milling machines, lathes and shapers, are now performed on various types of grinding machines Grinding machines have advanced in design, 2021年8月27日 The grinding wheel is the most important and unique part of the electrochemical grinding machine It is connected to the negative terminal of the power supply and acts as the cathode The grinding wheel is made of Electrochemical Grinding: Definition, Parts or The aluminum dross skimming from the smelting furnace is called primary aluminum dross, which is graywhite in appearance, mainly composed of a mixture of metallic aluminum and aluminum oxide, and the aluminum content can reach 15%~ 70%, also known as “white aluminum dross”; secondary aluminum dross is the waste after the primary aluminum dross is extracted from Aluminium dross processing/Brightstar Aluminum Machinery2024年2月1日 The electrolytic aluminum industry generates a large amount lithium (Li)containing electrolytic aluminum slag (EAS) annually, and this can result in severe environmental pollution and wasting of Li resources This paper proposes a method for recovering Li from the slag using AlCl 3 as the leaching agent The effects of the leaching temperature, AlCl 3 Efficient lithium recovery from electrolytic aluminum slag via an
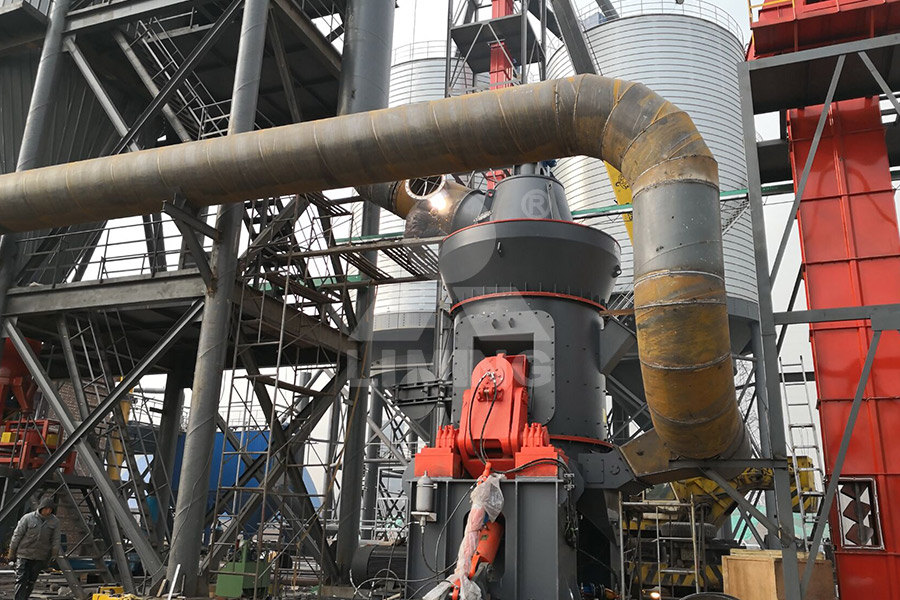
(PDF) A study of the solidification and stability mechanisms of
2022年9月1日 DSC spectra of different types of parent glass (Exo: exothermic direction; T g : glass transition temperature; T c : crystallization temperatures; GC18: Sample number)2024年1月31日 Additionally, machine breakdowns often pose threats to the safety of workers Consequently, it is crucial to optimise the control of slag grinding systems, whether from a system optimisation control or safety production perspective 6 Researchers such as Johan et al, 7 Kang et al, 8 Umucu et al, 9 Wang K et al, 10 and Lin et al 11 have made significant contributions Intelligent process control system for predicting operating 2022年10月1日 Request PDF Cocombustion characteristics of electrolytic aluminum waste and coal The electrolytic aluminum waste, which would inevitably be produced from the electrolytic process in the Cocombustion characteristics of electrolytic aluminum waste A stamp mill is a grinding machine where the grinding action takes place by falling weights The ore from the crushers varying in size from 10 to 60 mm is fed with water in the stamp mill A stamp is a heavy iron pestle 3–5 m long and about 7 cm in diameter carrying a weight 200–400 kgGrinding Machine an overview ScienceDirect Topics
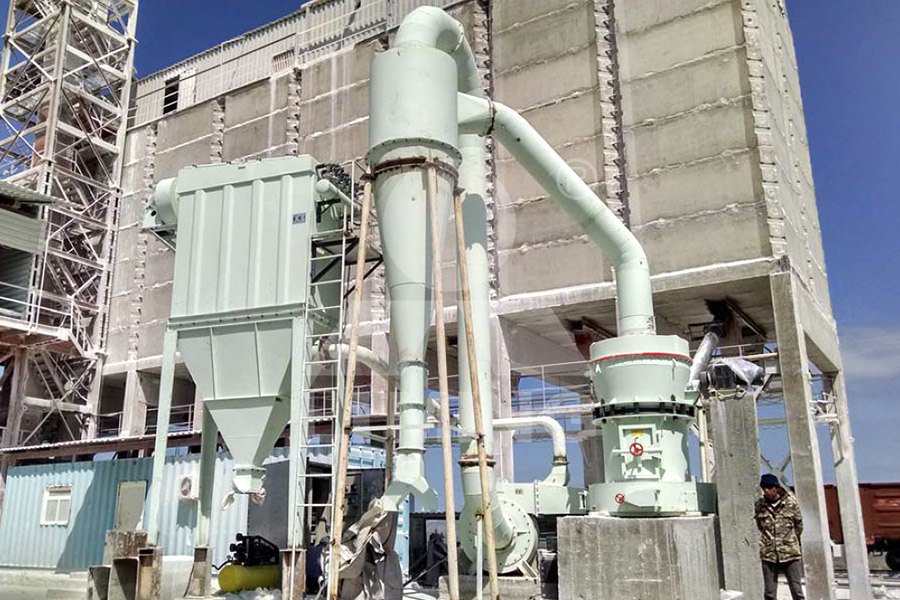
Grinding SpringerLink
2022年2月28日 Generally, grinding process efficiency can mainly be improved by either improving the grinding behavior of the material being ground or enhancing the grinding machines Recently, the use of additives socalled grinding aids, which is applied in a small amount of 001–025 wt% related to the mass of product, has reduced these problems and been 2022年2月1日 The system offered by KHD Humboldt Wedag for slag grinding is the most energy efficient grinding machine Special features of the circuit include includes Roller Press (RP 16170/180), Vseparator (VS 80/20) and the well Towards Sustainability: Slag Grinding CircuitsElectro Chemical Grinding (ECG) Electrochemical grinding combines both electrolytic action (90%) and physical grinding (10%) to provide precision, burrfree and stressfree results Owing to the electrolytic reaction, ECG eliminates Electro Chemical Grinding TE Connectivity, CUCECG combines abrasive grinding and electrochemical erosion producing a more efficient, costeffective, and burrfree part Be sure to read our latest electrochemical grinding solutions by visiting our Case Studies page Review frequently asked questions below, our electrochemical grinding machine offerings, as well as our Customer Care SolutionsFAQs About Electrochemical Grinding (ECG) Glebar
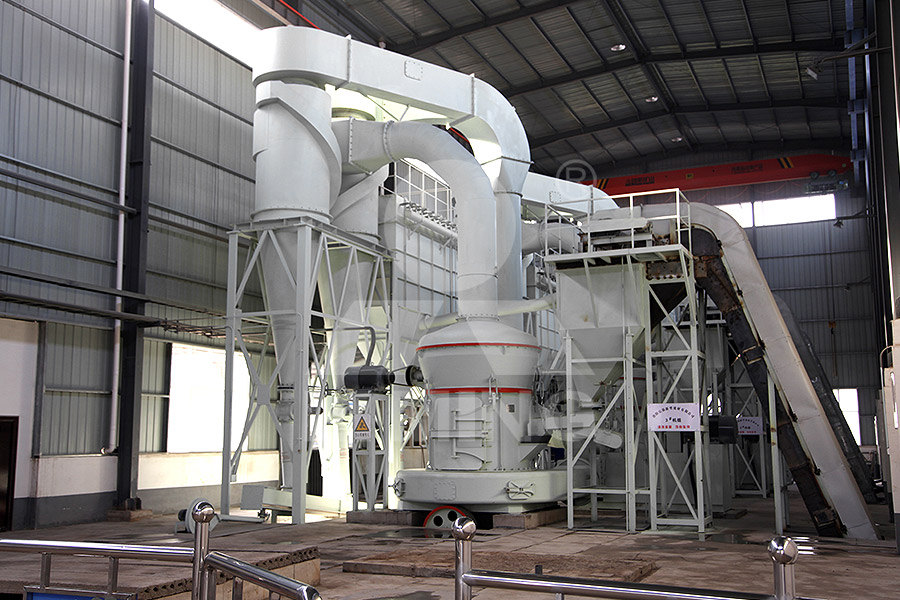
Study on Harmless and Resources Recovery Treatment Technology of Waste
2012年12月31日 The paper provides a brief introduction in the physical and chemical properties of waste aluminum cathodes, and its harmless treatment technology and resource comprehensive utilization technologyRecovery of carbon and cryolite from spent carbon anode slag of electrolytic aluminum by flotation based on the evaluation of selectivity index Yemin Wang1, Xuexia Wang1* and Muhammad Bilal2 1Department ofMiningEngineering, Shanxi Instituteof Technology,Yangquan,China,2Department of Mining Engineering, Balochistan University of Recovery of carbon and cryolite from spent carbon anode slag of2024年6月6日 In Electrochemical grinding, the metalbonded grinding wheel is filled with a nonconductive abrasive The grinding wheel acts as a cathode and the workpiece acts as an anode The electrolyte, which is usually sodium nitrate, sodium chloride, and potassium nitrite, with a concentration of 0150 to 0300 kg/liter of waterElectrochemical Grinding: Parts, Working, Application, AdvantagesOur slag grinding machines are designed to not only remove the slag or dross, but also to remove any mill scale left on the part They are equipped with a hard durometer contact drum, a course abrasive sanding belt, and high horsepower motors to aggressively grind heavy steel platesMetal Solutions Apex Machine Group
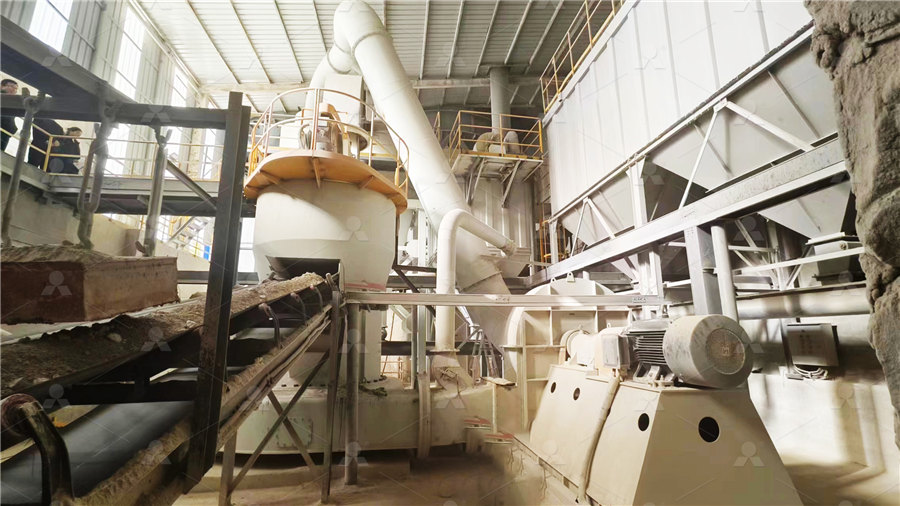
Intelligent process control system for predicting operating
2024年1月31日 Request PDF Intelligent process control system for predicting operating conditions of slag grinding machines: a data mining approach for improved efficiency and energy savings This study 2014年1月1日 Experimental setup for ELID grinding of silicon wafer, proposed by Ohmori, H; Nakagawa, T Mirror Surface Grinding of Silicon Wafers with Electrolytic Inprocess Dressing Ann CIRP 1990, 39 (1 Electrolytic InProcess Dressing (ELID) Grinding for Nano 2021年10月1日 Currently, the HallHeroult method is adopted for industrial aluminum smelting, with alumina as the raw material and cryolite as the solvent (Tarcy et al, 2011)According to statistics, China's primary aluminum output was 3708 million tons in 2020, of which the capacity of using domestic bauxite to produce alumina accounts for approximately 47% (National A novel approach for lithium recovery from waste lithium Slag Grinding Machine (1882 products available) ADV 508SR800 flame cutting and plasma cutting plate sheet grinding heavy slag removal machine for metal $25,00000 $38,00000 Min Order: 1 setSimple Ore Extraction: Choose A Wholesale slag grinding machine
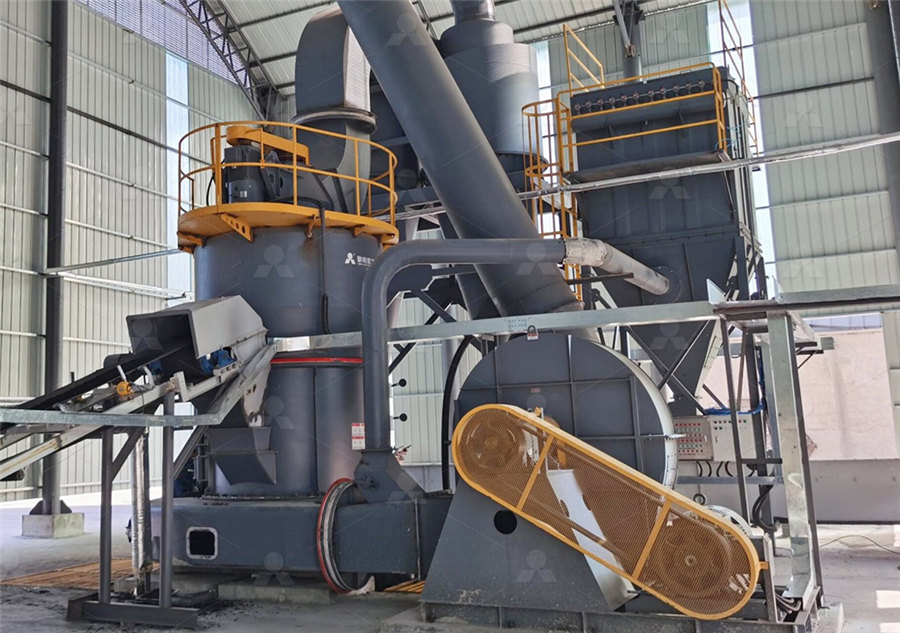
News How to choose the electrolytic manganese powder grinding
The special adaptability design for manganese ore grinding mainly focuses on the following aspects: 1) Improve the swing mode and contact area, improve the crushing energy and efficiency; 2) Largescale machine, high output, adapt to the requirements of largescale production; 3) Optimize the transmission 4) Realtime monitoring and management of the 2023年10月1日 Abundant carbon resides in spent cathode carbon (SCC) of aluminum electrolysis and its highpurity carbon powder is conducive to highvalue recyclingHarmless recovery and utilization of electrolytic aluminum spent 2022年2月19日 Recycling waste containing rare earth has always been a research hotspot The molten salt electrolysis process of rareearth metals and alloys generates a large amount of waste slag, which contains high rareearth content and, thus, has very considerable recovery value However, the high content of fluorine in rareearth molten salt slag brings challenges to the Recovery of RareEarth Elements from Molten Salt Electrolytic Slag Stedman impact crushers, mills, and grinders are used in nearly every mineral, ore, and mining applicationWhether you are processing iron ore, coal, rock, salt, wood chips, or clay – to name a few – we have your solution to size reduction with our mineral crushing machines industrial ore slag crushersIndustrial Ore, Mineral, Slag Crusher Stedman Machine
.jpg)
Recycling and utilization of the aluminum ash and slag Mineral
2020年11月23日 The recycle process of aluminum ash and slag The aluminum ash and slag is ground by mill and then feed to separator to get the metal aluminum and aluminium oxide After grinding, the aluminum slag is ground into powder, but because of the malleable properties of metal aluminum, the shape is changed, it is pressed into sheets Doing size 2024年4月17日 Recycling plays an important role in today's world due to its considerable contributions to mitigating energy concerns and environmental challenges One of them is dross recycling from aluminum (Al) cast houses Unlike other recyclable materials, dross has an abundance of components, including rare earth elements, heavy metals, ferrous, and recycled Aluminum dross: aluminum metal recovery and emerging 2023年3月1日 Aluminium dross (categorised as 10 03 21 group by European Waste Catalogue) (Mahinroosta and Allahverdi, 2018a, LópezDelgado et al, 2014) is a waste generated in smelters and casters when oxygen comes into touch with molten aluminium and reacts with it to form oxide phases on the surface of the metal poolThe oxide layer floats on the surface and soaks On trending technologies of aluminium dross recycling: A reviewWe offer various types of machinery for the removal of very heavy burrs from OxyAcetylene Cutting, Plasma Cutting and Drilling for the removal with or without surface grinding (leave scale on to prevent weld spatter sticking), with or without Slag Grinding GE Machinery Applications for metal finishing
.jpg)
Enhanced flotation separation of aluminum electrolysis anode slag
2024年3月1日 One of the main electrolytic aluminum production costs is the consumption of carbon anodes, and carbon anode slag is a common hazardous waste in the aluminum industry