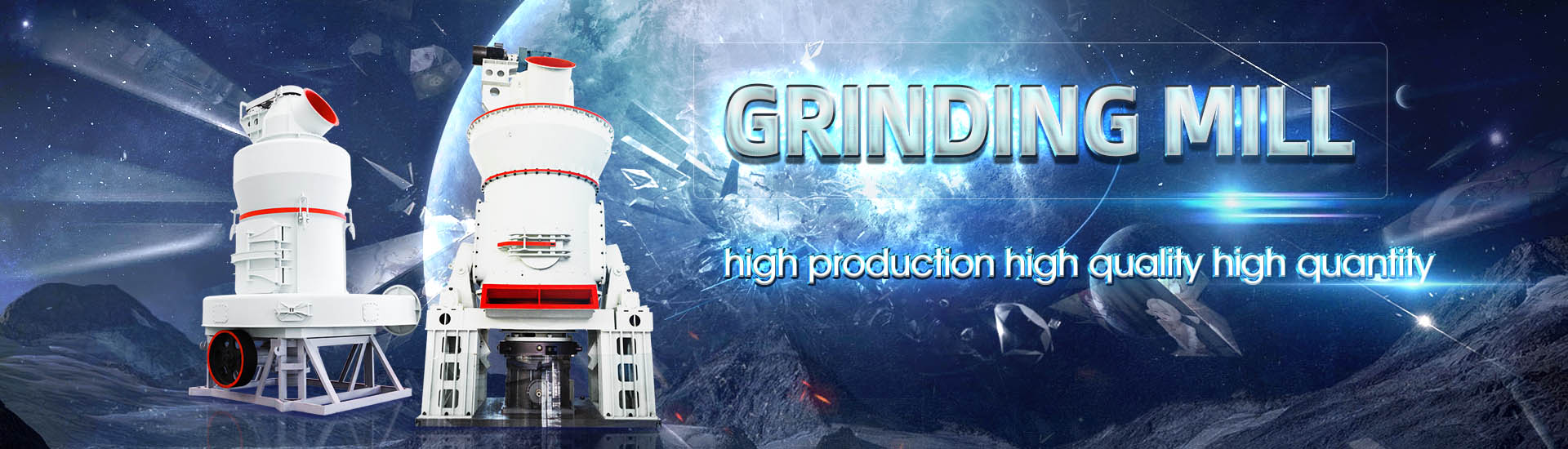
How to discharge slag from ore thermal furnace
.jpg)
(PDF) Heat Recovery from High Temperature
2015年3月12日 Waste heat recovery from high temperature slags represents the latest potential way to remarkably reduce the energy consumption and CO2 emissions of the steel industry The2011年9月1日 The energy consumed in high temperature processing of metals is distributed between metal, slag, offgas, and the natural losses to the atmosphere The slag thermal Energy recovery from high temperature slags ScienceDirect2021年6月24日 With the innovative approach presented in this work, it is possible to recover thermal heat from liquid slags The process concept consists of a slag tundish and four Process Concept for the Dry Recovery of Thermal Energy of 2019年1月1日 Reduction of ores in chemical compound form into the pure metal form requires inclusion of flux materials which bond with impurities for formation and removal of slag from An Overview of Utilization of Blast Furnace and Steelmaking Slag
.jpg)
Comprehensive utilisation of blast furnace slag Taylor
2024年6月26日 introduce the current status quo of comprehensive utilisation of blast furnace slag from the current blast furnace slag sensible heat recovery of molten steel 1 Overview of 2019年12月9日 Slags being discharged at temperatures typically above 1200 °C carry a substantial amount of heat As expected, the “materials” and “energy” values of the slag pose Granulation and Heat Recovery from Metallurgical Slags2020年2月27日 centrifugal granulation process of slag from the aspects of the flow characteristics of slag on the rotor surface and the formation mechanism of centrifugal RESEARCH OVERVIEW ON RECOVERY OF WASTE HEAT 2021年1月6日 Decreasing the slag rate can lead to a lower fuel rate and higher productivity in the blast furnace (BF) Indian iron ore is known to have adverse alumina–silica ratio FactSage Studies to Identify the Optimum Slag Regime for Blast Furnace
.jpg)
A Review of Granulation Process for Blast Furnace Slag
2021年12月4日 consumption, direct or indirect contact with blast furnace slag to recover sensible heat And at the same time it will use mechanical power or high pressure air to make 2021年12月1日 The Side Blowing Furnace process in this simulation has three furnaces: Side Blowing Furnace (SBF), Slag Formation Furnace (SFF), and finally the Top Blowing Converter (TBC) (Xia 2019; Wei et al, 2019) Like in the Mitsubishi process, the matte flows continuously through the first two furnaces before it gets converted in the last parison of environmental performance of modern copper 2023年6月15日 where P is the daily output of ironmaking blast furnace (ton/day and night), ν is the bosh gas volume (m 3 /ton), and χ is the bosh gas volume index, generally 58–66 m/min The size ratio of each part of the inner shape of the ironmaking blast furnace is D/d = 11–12, d 1 /D = 062, d 1 /d = 87, the shaft angle is 80–81°, and the bosh angle is 74–75°Ironmaking Blast Furnace SpringerLink2023年7月21日 Introduction China is the world's largest steel producer, with the China Iron and Steel Association estimating that the country's crude steel production in 2022 will be 935 million tonnes [Citation 1]Steel slag mainly refers to the blast furnace slag and converter slag produced in the process of iron making and steel making, and with the increase of steel production, the Full article: Comprehensive utilisation of blast furnace slag
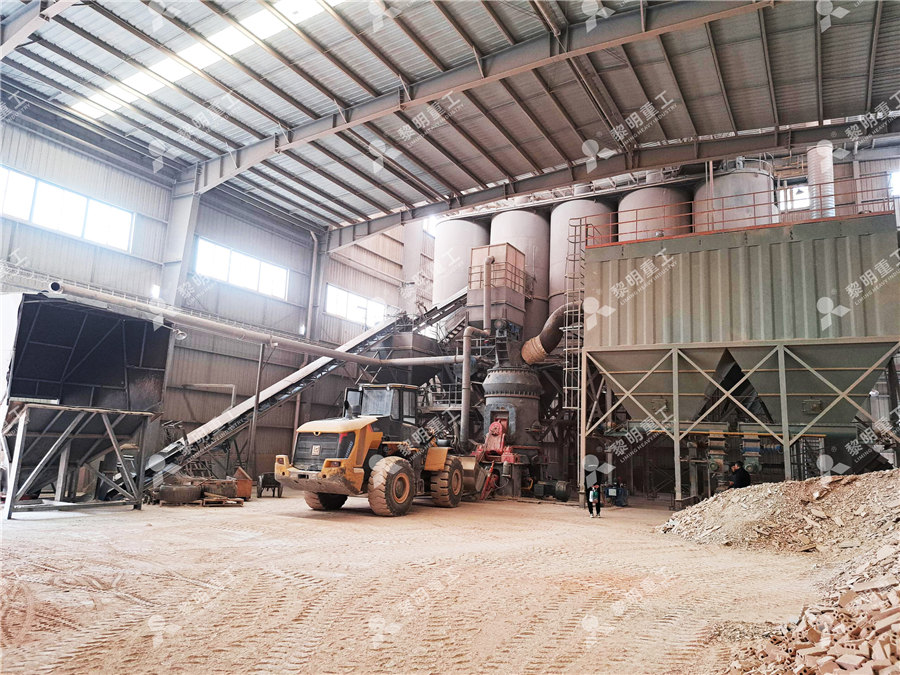
A Comprehensive Review on the Ground Granulated Blast Furnace Slag
2022年7月18日 With respect to the mechanical properties, durability and thermal behavior, groundgranulated blastfurnace slag (GGBS) delineates a rational way to develop sustainable cement and concrete Apart from environmental benefits, the replacement of cement by GGBS illustrates an adequate way to mitigate the economic impact2018年1月11日 The submerged electric arc furnace (SAF) has proven a versatile unit in numerous metallurgical applications for more than a century Countless innovations have made this furnace type become the most commonly used furnace for increased metal recoveries and slagcleaning operations In many applications, SAFs are also employed as primary melting The Submerged Arc Furnace (SAF): StateoftheArt Metal2020年8月19日 As a result, thermal gradients appear in the radial direction of the furnace stack The thermal segregation problems were partially solved using a pretreated ferric burden (sinter and pellets) The thermal profile of the charge, in the best situation, will be that shown in Fig 65 In those zones close to the furnace walls, the temperature Production of Iron in the Blast Furnace SpringerLink2023年11月21日 Iron is extracted from iron ore close ore A rock containing enough quantities of a mineral for extraction to be possible in a huge container called a blast furnace Iron ores such as haematite Redox, extraction of iron and transition metals BBC
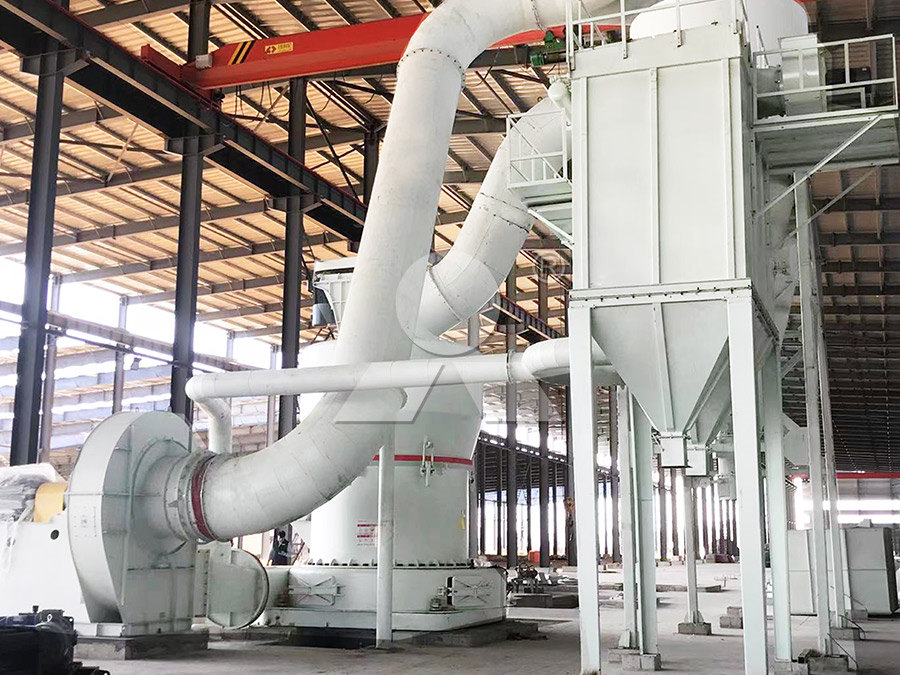
Waste heat recovery of blast furnace slag in moving bed:
2024年7月1日 To predict thermal behaviour of particle and fluid accurately, energy balance equation need to be established properly In this system, the main heat transfer way is the convective heat transfer between different phases When the blast furnace stopped slag discharge, the BFS particles were discharged from the bottom of the moving bed after 2023年6月10日 In the process of blast furnace ironmaking, Slagforming in blast furnace ironmaking is the solvent that interacts with the gangue in the ore and the ash of coke to dissolve, collect, and melt the substances that do not enter pig iron and gas, so that the liquid slag is formed In the blast furnace, slag and pig iron are formed at the same timeSlagForming in Blast Furnace Ironmaking SpringerLink2024年11月4日 Carbon monoxide reduces the iron(III) oxide in the iron ore to form iron This will melt and collect at the bottom of the furnace, where it is tapped off iron(III) oxide + carbon monoxide → iron + carbon dioxide Limestone (calcium carbonate) is added to the furnace to remove impurities in the oreExtraction of iron IGCSE Chemistry Revision Notes Save 2018年11月29日 For existing coalfired power plants, current methods of utilizing ash and slag waste may be considered in addressing new environmental and economic risks However, for new power sources, environmental considerations are much more important in selecting the coalcombustion technology Technology based on a circulating fluidized bed is sometimes cited as Processing Ash and Slag Wastes from Thermal Power Stations Part 2
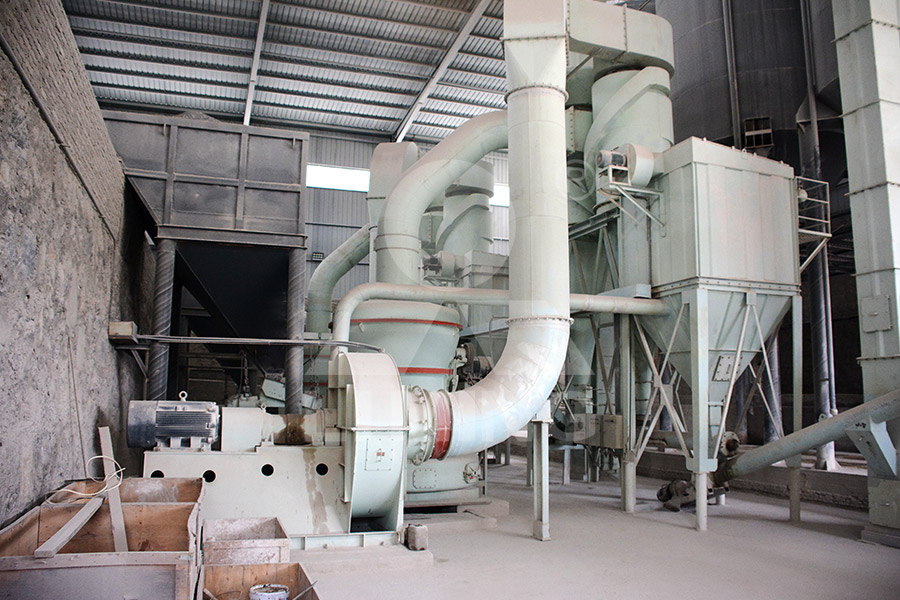
Metallurgical resource recovery from waste
2021年8月25日 Steel slag from an electric arc furnace (EAF) may contain significant amounts of oxides of valuable metals The recovery of iron and other metals from the EAF slag using smeltreduction process 2024年6月26日 isation of blast furnace slag and improve the economic benefits of the steel industry, this paper will introduce the current status quo of comprehensive utilisation of blast furnace slag from the current blast furnace slag sensible heat recovery of molten steel 1 Overview of blast furnace slag treatment process in ChinaComprehensive utilisation of blast furnace slag Taylor 2017年4月15日 One of the steps in the iron making process is to heat the pig iron up to 1500 °C for the next phase of steelmaking In this process a significant amount of energy is transferred to the blast furnace slag (BFS), which reaches temperatures of around 1500 °C at the end of this process (Sadek, 2014)Utilising the waste heat energy from the slag to contribute to heating Investigation of thermal properties of blast furnace slag to Plasma is generated by ways such as thermal ionization, gas discharge, photoionization, etc A maximum value of 85–87% TiO 2 content was produced in the slag by the thermal plasma process The minor oxide Mapelli C Iron Recovery from Bauxite Tailings Red Mud by Thermal Reduction with Blast Furnace Sludge Appl Sci 2019;9:4902 doi An Overview of Thermal Plasma Arc Systems for Treatment
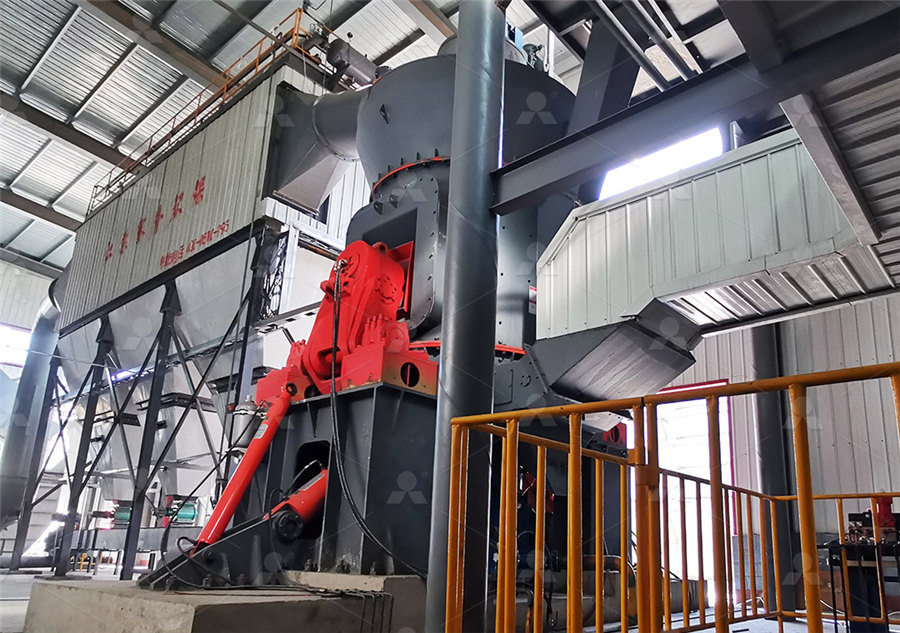
Granulation and Heat Recovery from Metallurgical Slags
2019年12月9日 Metallurgical slags are produced at a massive rate of over 750 Mt/year, and carry a thermal energy equivalent to 40 Mt/year of coal The potential mineral and thermal energy values of slags are in the order of $22 b and $3–6 b per year Such attractive figures, together with tightening legislation on disposal of slag and the carbon footprint associated with the loss 2021年12月4日 Blast furnace slag is a byproduct of blast furnace (BF) ironmaking produce Every pig iron production is accompany by 03 ~ 06 tons of blast furnace slag produced with the temperature of 1350 ~1450 (1600~1 800 MJ sensible heat, equivalent to 55~61kg standard coal combustion after the heat generated) On this basis, the BF slag is up to 247 A Review of Granulation Process for Blast Furnace Slag21 Blast furnace slag (BFS) The steel industry involves the production of different slags throughout the processes [23,39] Blast Furnace Slag (BFS) is a byproduct of the reduction stage, in which iron ore is converted into pig iron About 300 kg Blast Furnace Process an overview ScienceDirect Topics4 天之前 This page is about the Slag from Thermal Expansion 3 For other uses, see Slag Slag is an item added by Thermal Expansion 3 It is a byproduct of smelting ore dust with Sand in an Induction Smelter Smelting ore blocks with Sand yields a chance to drop Rich Slag Rich Slag can be combined with ore blocks to triple the ore output and to create a secondary byproduct Slag (Thermal Expansion 3) Official Feed The Beast Wiki

Basic oxygen furnace slag: Review of current and potential uses
2020年4月1日 It can be categorized by either the process in which it was generated (basic oxygen furnace slag (BOFS), electrical arc furnace slag (EAFS), ladle refining slag (LFS)), or by the type of steel produced in said process (carbon steel slag or stainlesssteel slag) (Yi et al, 2012, Liu and Wang, 2017, Ndlovu et al, 2017) Countries such as Japan 2024年9月18日 Despite the variety of methods of processing toxic ash residues from IPs, the most efficient industrial equipment are DC or threephase AC orethermal (oremelting) furnaces []The purpose of melting IP ash residue, without conducting chemical reactions, is homogenization of some oxides, significant reduction of the ash volume, and conversion of the Features of PlasmaThermal Melting of Ash and Slag from2019年8月14日 For the orecoal composite pellet of n C/n O=08 or 085, the mass fraction of FeO in slag is relatively higher, the melting point is lower and the slag is easy to be separated from metal after (PDF) Recovery of iron from electric arc furnace slag: effect 2020年5月14日 melting furnaces, pressure pour furnaces and magnesium treatment vessels with minimal to no adverse effects on refractory linings Slag Formation: The formation of slag in the melting of ferrous metals in the foundry is inevitable The composition of slag varies with the type of melting process used and the type of iron or steel being meltedControl of Slag and Insoluble Buildup in Ladles, Melting
.jpg)
A direct conversion of blast furnace slag to a mesoporous
2020年4月24日 In the iron manufacturing industry, it is unavoidable to produce large volumes of blast furnace slag (BFS) as a mineral residue from the preparation of pig iron in blast furnaces as well as to discharge a high volume of carbon dioxide (CO 2) gas as a result of the consumption of cokeThese byproducts potentially lead to environmental problems such as ground pollution 2023年10月6日 A large blast furnace has a slag content of 250–350 kg per ton of iron, and a small blast furnace has a slag content of 450–550 kg per ton of iron The main composition range of general blast furnace slag is: calcium oxide for 35–44%, silica for 32–42%, alumina for 6–16%, and magnesium oxide for 4–12% Blast furnace gas is also one Blast Furnace Ironmaking SpringerLinkviscosity of slag1) However, as one of the most important physical properties,2) the hightemperature viscosity of blast furnace slag determines the permeability, stability, and productivity of blast furnace operation3–6) Previous studies have mostly focused on the effect of slag composition on the viscosity of slag at a constant temperatureThermal Stability of Molten Slag in Blast Furnace Hearth2021年1月6日 Decreasing the slag rate can lead to a lower fuel rate and higher productivity in the blast furnace (BF) Indian iron ore is known to have adverse alumina–silica ratio Therefore, to reduce the slag rate there is a need to either remove alumina from the iron ore or to add more silica to dilute the effect of alumina in slag The latter would increase the slag rate, while the FactSage Studies to Identify the Optimum Slag Regime for Blast Furnace
.jpg)
Energy recovery from high temperature slags ScienceDirect
2011年9月1日 Metallurgical slags constitute the largest byproduct of the high temperature operations involved in the extraction and refining of metals Slags are comparable to molten lava and are generally rich in silica (SiO 2), alumina (Al 2 O 3), and lime (CaO)Slag is formed from the refining reactions, remaining gangue of the ore, erosion of the furnace refractory, and the The low recycling for reuse of LS slag was mainly attributed to its volume instability ie disintegration of slag during cooling due to phase transformation and wideranging slag composition [20 Typical chemical composition of blast furnace slags2023年11月15日 Copper is a metal that is widely used in different applications mainly due to its thermal and electrical conductivities, together with its corrosion resistance, particularly when it is alloyed This chapter intends to be a summary of the copper metallurgy: from the historical aspects and mineral deposits or statistics to the different technologies used to produce Copper Overview: From the Ore to the Applications2021年12月1日 The Side Blowing Furnace process in this simulation has three furnaces: Side Blowing Furnace (SBF), Slag Formation Furnace (SFF), and finally the Top Blowing Converter (TBC) (Xia 2019; Wei et al, 2019) Like in the Mitsubishi process, the matte flows continuously through the first two furnaces before it gets converted in the last parison of environmental performance of modern copper
.jpg)
Ironmaking Blast Furnace SpringerLink
2023年6月15日 where P is the daily output of ironmaking blast furnace (ton/day and night), ν is the bosh gas volume (m 3 /ton), and χ is the bosh gas volume index, generally 58–66 m/min The size ratio of each part of the inner shape of the ironmaking blast furnace is D/d = 11–12, d 1 /D = 062, d 1 /d = 87, the shaft angle is 80–81°, and the bosh angle is 74–75°2023年7月21日 Introduction China is the world's largest steel producer, with the China Iron and Steel Association estimating that the country's crude steel production in 2022 will be 935 million tonnes [Citation 1]Steel slag mainly refers to the blast furnace slag and converter slag produced in the process of iron making and steel making, and with the increase of steel production, the Full article: Comprehensive utilisation of blast furnace slag2022年7月18日 With respect to the mechanical properties, durability and thermal behavior, groundgranulated blastfurnace slag (GGBS) delineates a rational way to develop sustainable cement and concrete Apart from environmental benefits, the replacement of cement by GGBS illustrates an adequate way to mitigate the economic impactA Comprehensive Review on the Ground Granulated Blast Furnace Slag 2018年1月11日 The submerged electric arc furnace (SAF) has proven a versatile unit in numerous metallurgical applications for more than a century Countless innovations have made this furnace type become the most commonly used furnace for increased metal recoveries and slagcleaning operations In many applications, SAFs are also employed as primary melting The Submerged Arc Furnace (SAF): StateoftheArt Metal

Production of Iron in the Blast Furnace SpringerLink
2020年8月19日 As a result, thermal gradients appear in the radial direction of the furnace stack The thermal segregation problems were partially solved using a pretreated ferric burden (sinter and pellets) The thermal profile of the charge, in the best situation, will be that shown in Fig 65 In those zones close to the furnace walls, the temperature 2023年11月21日 Iron is extracted from iron ore close ore A rock containing enough quantities of a mineral for extraction to be possible in a huge container called a blast furnace Iron ores such as haematite Redox, extraction of iron and transition metals BBC2024年7月1日 To predict thermal behaviour of particle and fluid accurately, energy balance equation need to be established properly In this system, the main heat transfer way is the convective heat transfer between different phases When the blast furnace stopped slag discharge, the BFS particles were discharged from the bottom of the moving bed after Waste heat recovery of blast furnace slag in moving bed: 2023年6月10日 In the process of blast furnace ironmaking, Slagforming in blast furnace ironmaking is the solvent that interacts with the gangue in the ore and the ash of coke to dissolve, collect, and melt the substances that do not enter pig iron and gas, so that the liquid slag is formed In the blast furnace, slag and pig iron are formed at the same timeSlagForming in Blast Furnace Ironmaking SpringerLink
.jpg)
Extraction of iron IGCSE Chemistry Revision Notes Save
2024年11月4日 Carbon monoxide reduces the iron(III) oxide in the iron ore to form iron This will melt and collect at the bottom of the furnace, where it is tapped off iron(III) oxide + carbon monoxide → iron + carbon dioxide Limestone (calcium carbonate) is added to the furnace to remove impurities in the ore