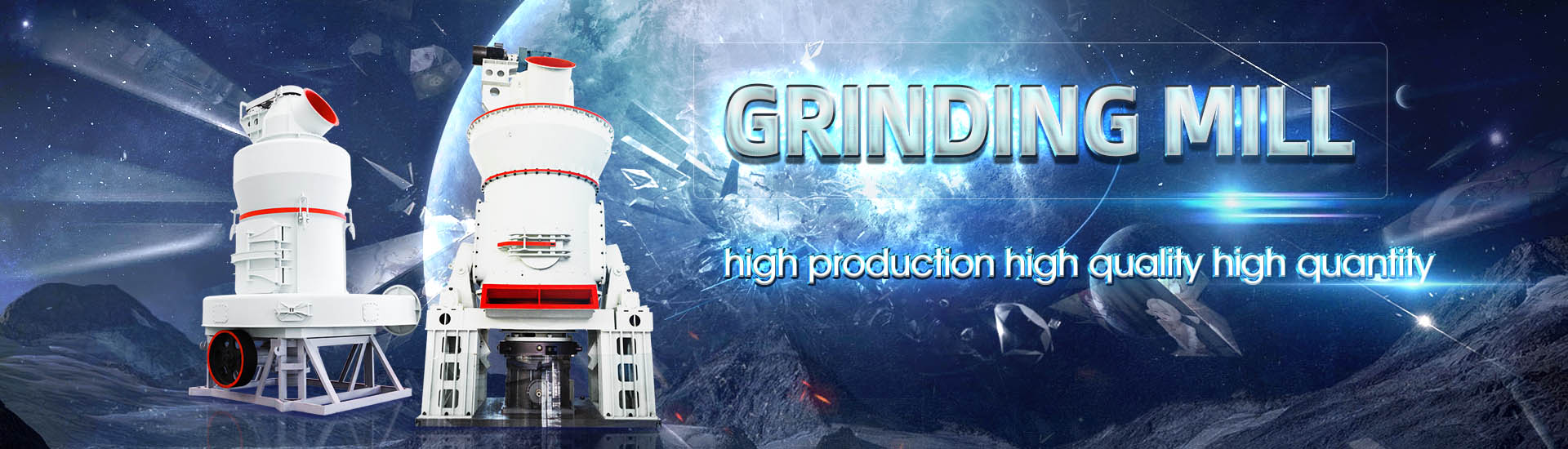
Highfrequency hydraulic vibration
.jpg)
Present Status and Prospect of HighFrequency Electrohydraulic
Overseas research on highfrequency servovalve controlled vibration equipment is more early, various vibration environment simulation testing devices composed of electrohydraulic shaking table (EHST) have been developed and the most products have been series manufactured, formed a certain market scale and 展开Combining the existing rotaryvalve controlled highfrequency electrohydraulic vibration method, a new twinvalve independently controlled highfrequency electrohydraulic vibrationPresent Status and Prospect of HighFrequency Electrohydraulic 6 天之前 These failures are mainly attributed to the alternating loads induced by pressure fluctuations and the vibrations they cause [14] Marine highspeed The HPCRS is inherently Research on the pressure fluctuations and hydraulic resonance 2014年2月4日 In this paper, to realize high frequency vibration, an improved twodimensional valve (here within defined as a 2D valve) as a main control component is adopted to the Output waveform analysis of an electrohydraulic vibrator
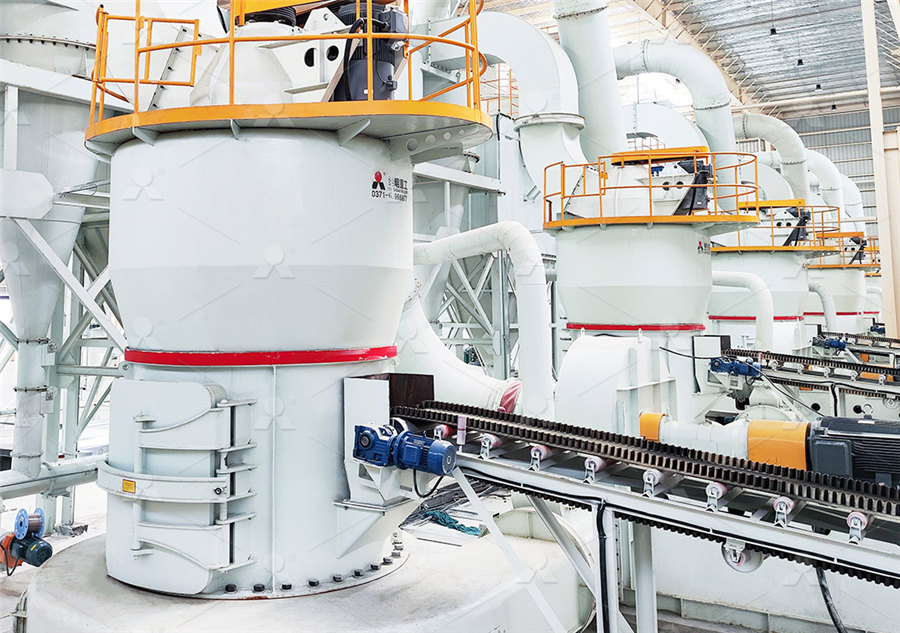
Characterization of rotary valve control vibration system for
2024年4月24日 Electrohydraulic vibration excitation equipment through the control and actuating elements to generate usable vibration and liquid wave energy, with a large output 2018年3月16日 In this paper, the current method to detect erosive cavitation in hydraulic turbines by analyzing highfrequency vibrations has been revised by studying its main existing uncertainties This method is based on measuring Transmission of High Frequency Vibrations in Rotating 2023年3月31日 Highspeed onoff valve uses its highfrequency characteristics to realize the switching effect of fast opening and closing or generate relatively continuous pressure and flowAnalysis of flow characteristics and throttling loss of a novel high 2022年8月20日 HighFrequency Pressure Fluctuation (HFPF) is an extensively observed hydraulic phenomenon in pumpedstorage power stations and water conveyance projects The investigation of the propagation characteristics of Refined 1Dndash;3D Coupling for HighFrequency
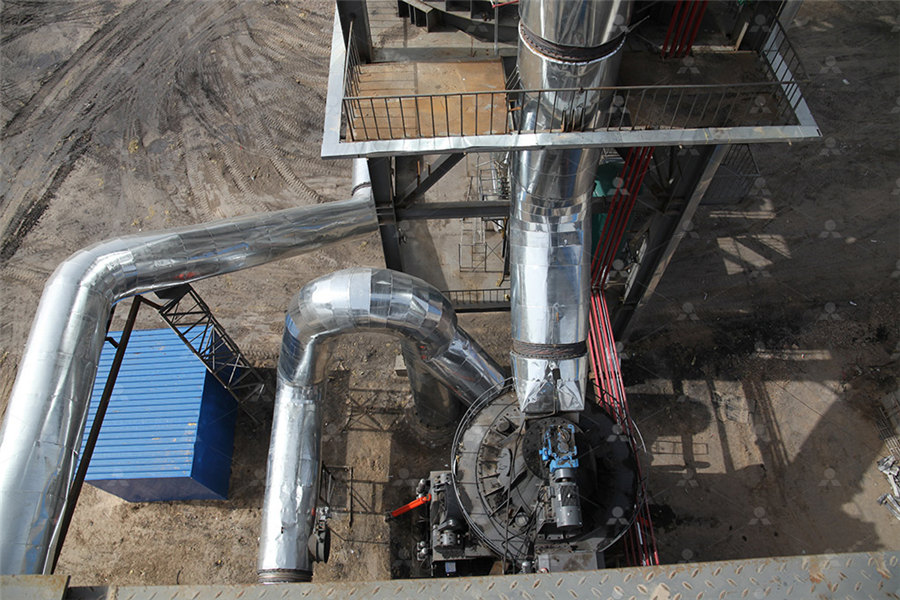
A LargeFlowrate On–Off Valve with Hollow Structure for High
2020年9月1日 In highfrequency hydraulic vibration and impact systems, the highspeed reciprocating motion of the impact piston, as controlled by the main valve, transfers energy to 2017年4月1日 During cavitation, a pressure fluctuation takes place due to bubbles growth and collapse and causes vibrations in hydraulic turbines This causes variation in flux distribution in Sources of vibration and their treatment in hydro power stationsA of HighFrequency Electro hydraulic Vibration Control Technology Yi Liu1,2,3, Tao Wang 1, Guofang Gong* and Rujun Gao1,2 Abstract Electrohy()vironment simulation tests, such as vehicles, weapons, ships, aerospace, nuclear industries and seismic waves replication, etc, due to its large outputPresent Status and Prospect of HighFrequency Electrohydraulic of HighFrequency Electro hydraulic Vibration Control Technology Yi Liu1,2,3, Tao Wang 1, Guofang Gong* and Rujun Gao1,2 Abstract Electrohy()vironment simulation tests, such as vehicles, weapons, ships, aerospace, nuclear industries and seismic waves replication, etc, due to its large outputPresent Status and Prospect of HighFrequency Electrohydraulic
.jpg)
A LargeFlowrate On–Off Valve with Hollow Structure for High
2020年9月1日 In highfrequency hydraulic vibration and impact systems, the highspeed reciprocating motion of the impact piston, as controlled by the main valve, transfers energy to the target Therefore, the main valve must have a fast response speed and strong flow capacity A novel twostage largeflowrate on–off valve is developed in this studyThrough conducting a field test on a highspeed train, Zhang et al [2] observed that the passing frequency of 20th order wheel polygonal wear is close to the natural frequency of gear box used in the highspeed train, and concluded that the failure of gear box could be indued by the wheel polygonal wearinduced high frequency impact around 580 Hz After that, the railway industry Modelling of high frequency vibration of railway bogies’ 2022年8月20日 HighFrequency Pressure Fluctuation (HFPF) is an extensively observed hydraulic phenomenon in pumpedstorage power stations and water conveyance projects(PDF) Refined 1D–3D Coupling for HighFrequency Forced Vibration 2021年3月11日 High frequency hydraulic vibration pile hammer (no resonance construction method) The Joint Annual Meeting of Soil Mechanics and Foundation Engineering Academic Committee of China Civil Engineering Society 166–172 Wang Vibrationinduced acceleration of infiltration in loess
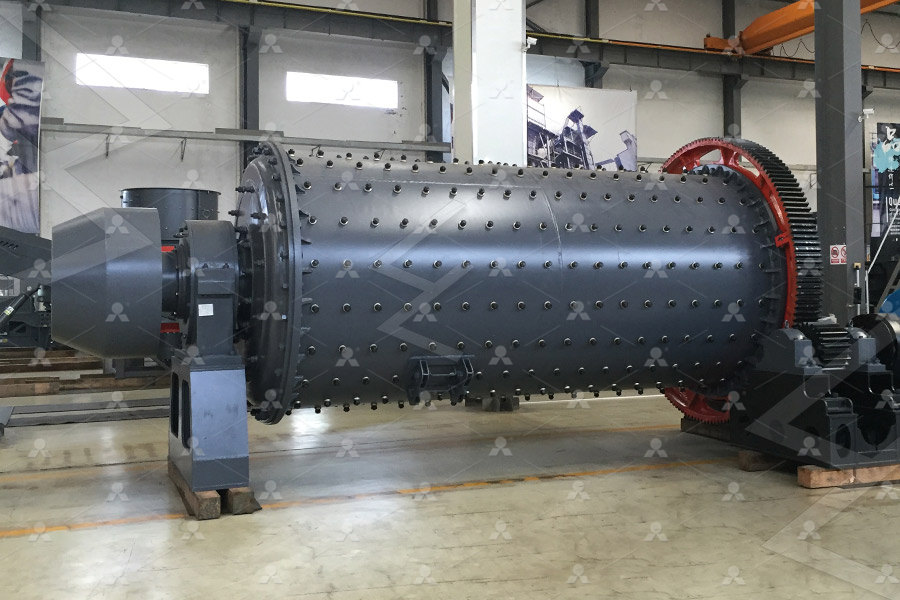
Hydraulic Cavitation Vibration School
High frequency, random vibration Sounds like the pump is pumping gravel Although amplitudes may or may not be high enough to affect bearing life significantly, cavitation causes excessive wear on the impeller and other internal components May come and go from one collection to the next as load varies Recommended Actions:2022年8月20日 HighFrequency Pressure Fluctuation (HFPF) is an extensively observed hydraulic phenomenon in pumpedstorage power stations and water conveyance projects The investigation of the propagation characteristics of the pressure perturbation is of great significance for the safe operation of hydraulic facilities In this study, a onedimensional (1D)–three Refined 1Dndash;3D Coupling for HighFrequency Forced Vibration 2018年3月16日 One of the main causes of damage in hydraulic turbines is cavitation While not all cavitation appearing in a turbine is of a destructive type, erosive cavitation can severely affect the structure, thus increasing maintenance costs and reducing the remaining useful life of the machine Of all types of cavitation, the maximum erosion occurs when clouds of bubbles Transmission of High Frequency Vibrations in Rotating Systems2019年9月15日 Highfrequency electrohydraulic excitation systems generate an ‘artificial’ vibrating environment, which are often used in the highcycle fatigue test systems for modern engineering materials and/or structures [1], [2], [3]In such systems, accompanying the increase of the excitation frequency, pressure transient (also known as pressure surge) occurs [4], [5], [6], Experimental and numerical investigations of hydraulic resonance
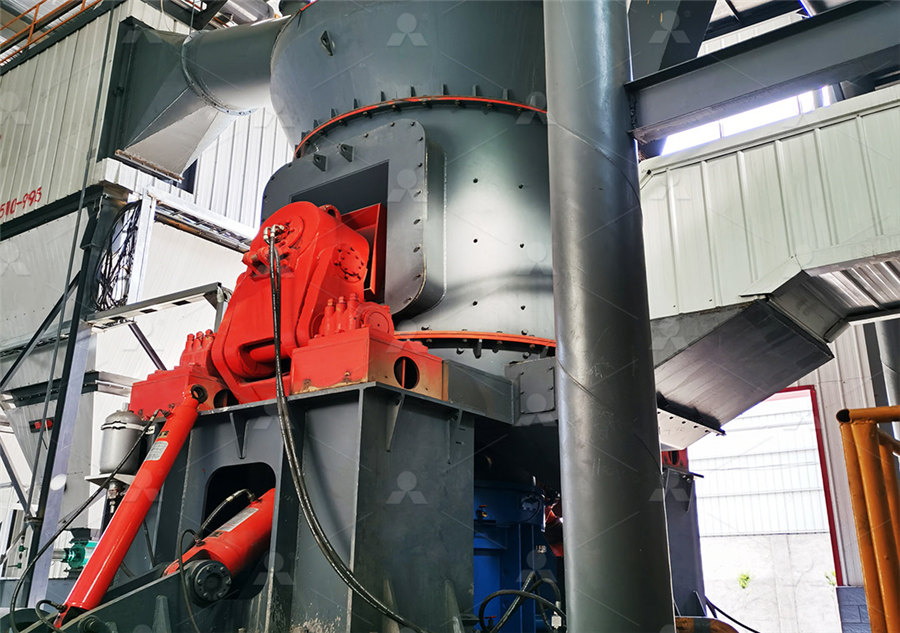
Study on the influence of pipe effect on the vibration
2024年11月3日 Yan et al 9 design a highfrequency inertial electrohydraulic excitation system employing a 2degreeoffreedom rotary valve, derive an analytical model of the system waveform, operating 2022年12月8日 Hydraulic vibratory hammer using the working principle of vibratory pile sinking is an important equipment in pile foundation construction, which can be used for sinking and extracting piles It has a wider range of application than the drop hammer for pile sinking by the impact method and the static hammer for pile sinking by the pressin method, which can Hydraulic Vibration Hammer without Resonance Technology 2024年2月23日 Additionally, for a water conveyance system with extremely longdistance pipelines, plenty of computation time is required when performing the time domain analysis since the process of convergence to another steady Effect of turbine's torque and speed variation on It utilizes fluid hydraulic force which then can be converted into rotary power in order to generate high frequency vibration [17] This modification allows equipment to operate at higher frequency range, up to 8200 RPM, compared to the conventional electric vibratorsHighfrequency vibrating screens Wikipedia
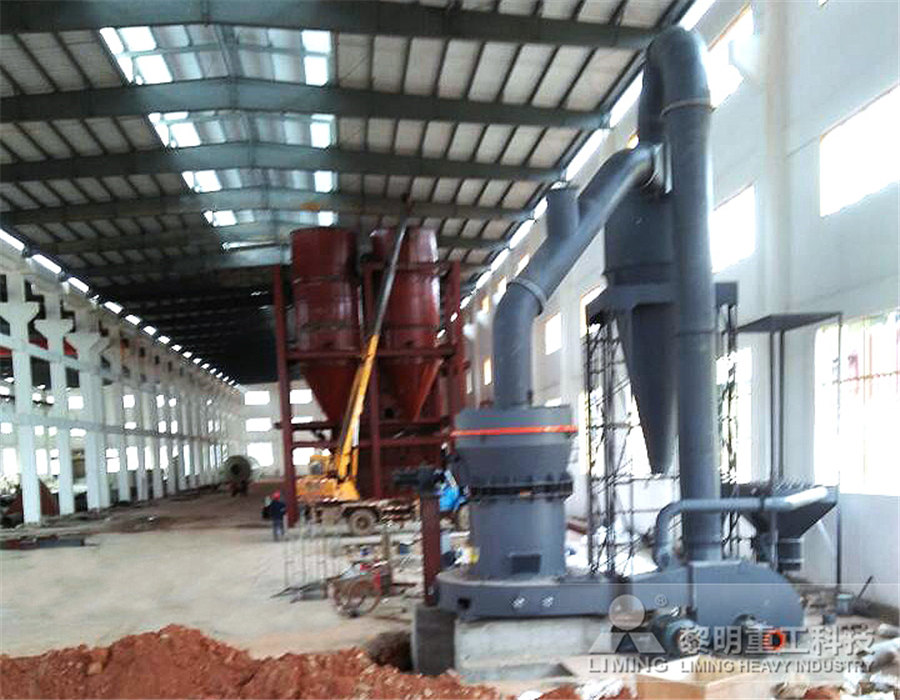
Analysis of Soil Response during High‐Frequency Vibratory Steel
2024年1月25日 52 The Effect of Vibration Frequency Highfrequency vibratory hammers can adjust the frequency and eccentricity by varying the diesel engine’s frequency, variable hydraulic motor, and phase difference of the internal eccentric wheels of the eccentric wheel systemthe coupling method, the high‐frequency forced vibration in the hydraulic system is mod‐ eled, where the pipe vibration is simulated as the vibration source The remainder of this paper is structured as follows In Section 2, the basic governing and 1D–3D coupling equa‐Refined 1D–3D Coupling for High‐Frequency Forced Vibration 2022年9月6日 As a kind of piling equipment, the hydraulic vibratory hammer can drive different prefabricated piles, including steel, pipe, and concrete It has been widely applied in construction industry and costal engineering [1, 2] with the advantages of low noise level, high efficiency, and powerful characteristics [1, 3,4,5]The vibratory hammer drives piles with high frequency Research on the performance of hydraulic vibratory hammer2018年3月1日 by highfrequency cleaning Therefore, to realize highfrequency vibration and large output, a highfrequency highpower cleaner driven by electrohydraulic excitation is proposed There has been significant research on the vibration characteristics of highfrequency vibration systems used in cleaning or other cases Liu et al10 researchedAnalysis on vibration for a highfrequency electrohydraulic
.jpg)
Effects of train vibration load on the structure and hydraulic
2024年3月28日 Notably, the fit results reveal a substantial influence of vibration frequency on soil hydraulic properties; as highfrequency vibration promotes water movement in the soil2016年12月1日 When sinusoidal vibration waveform is required, the frequency bandwidth of conventional electrohydraulic vibration exciter controlled by servo valve is always limited to a rather narrow range due to the limits of slide valve structure and response speed, and no parameter is available for defining and evaluating the waveform quality In this paper, a novel A rotary valve controlled electrohydraulic vibration exciterAstec high frequency screens utilize highspeed vibration, from 3,600 4,200 RPM, directly induced to the screen media, All decks driven by variablespeed hydraulic vibrators ; Optimal screen efficiency and production ; Electric High Frequency Screens AstecDownload scientific diagram Electrohydraulic 3stage servovalve from publication: Present Status and Prospect of HighFrequency Electrohydraulic Vibration Control Technology Abstract Electrohydraulic 3stage servovalve ResearchGate
.jpg)
(PDF) Analysis on vibration for a highfrequency
2018年12月1日 Theoretical and experimental results indicate that the electrohydraulic cleaning system outputs sinusoidal vibration waveforms, especially in a highfrequency domain, which could realize the Increasing the number of bell plates can effectively solve the problem of highfrequency hardening of hydraulic mount 2 New bell plate hydraulic mount 21 New bell plate controlled multiinertia channel magnetorheological fluid mount wide frequency vibration isolation control study J Intell Mater Syst Struct 2024;35(8):775–88 101177 Effect of bell plate structure on high and lowfrequency Vibration Parameters Another important factor to consider is the vibration parameters needed for your applications Different models offer different settings and controls for intensity, amplitude and frequency Learn more about each model and the capabilities of their hydraulic vibratory motorsHydraulic Vibrators Deca Vibrator Industries2018年11月16日 Traditional passive vibration isolation devices have a satisfactory isolation performance on smallamplitude and highfrequency vibration, but it is hard to suppress largeamplitude and lowfrequency vibration The lowfrequency vibration isolator needs to retain a sufficiently low dynamic stiffnessDesign and analysis of an active‐controlled hydraulic low‐frequency
.jpg)
Pump Vibration Analysis: Benefits, Frequency, Equipment
2023年5月11日 For example, highfrequency vibration may indicate a problem with the bearings or other rotating components, while lowfrequency vibration may indicate an issue with the pump’s hydraulic system Additionally, it is important to consider the amplitude and phase of the vibration waveform when analyzing pump vibration data2019年9月25日 In summary, the hydraulic flow disturbance of a vibroseis highfrequency electrohydraulic servo valve is mainly caused by the highfrequency commutation of the fluid in the valve chamber, the excitation of highfrequency vibration, and the structure, size, and arrangement of the hydraulic flow path of the vibratorStudy of the hydraulic disturbance suppression of a vibrator under high 2011年8月1日 The second stage of validation was carried out based on the combined model of the shock absorber and the servohydraulic tester The highfrequency results obtained from measurements and simulations were compared in the frequency domain and are presented in Table 5, while the selected result corresponding to the lowest current (029 A) applied A highfrequency firstprinciple model of a shock absorber and 2024年10月18日 Cavitation in hydraulic pumps and control valves also triggers highfrequency vibration, which in turn generates significant noise and damage to hydraulic components and piping Line noise is usually caused by leakage in the pipe, and turbulence from bends and branches can further enhance the noiseVibration and Noise in Hydraulic Systems: Causes, Effects,
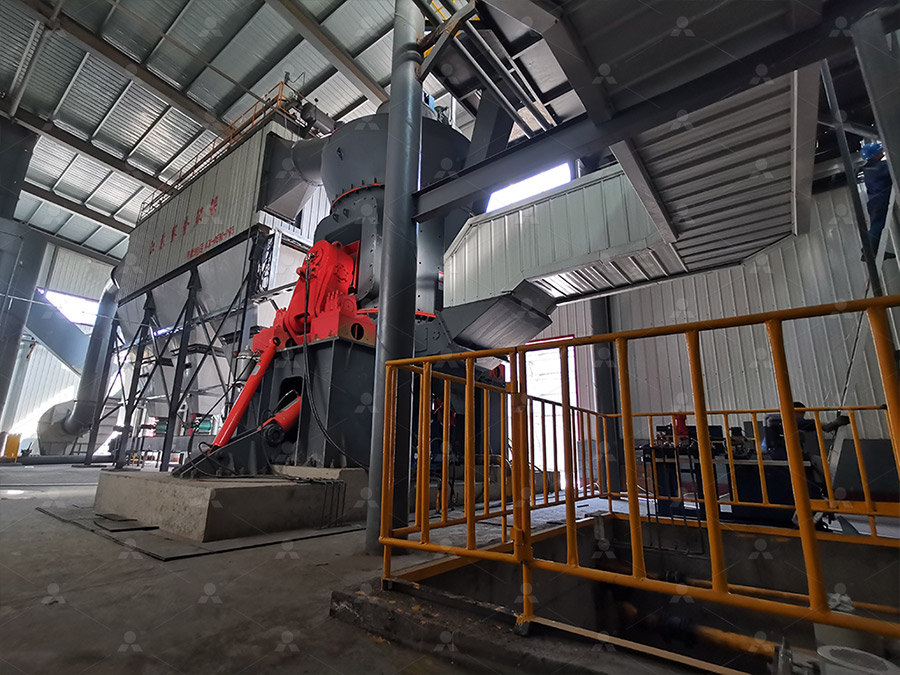
Research and Development of Hydraulic Controlled Vibration
2021年4月26日 Working principles: The external vibration signals is divided into two parts [26,27,28,29,30]: one part of the signals passes through vibration wave receiving hole 1a to the left side S 1 of piston slider 2The extent of shaking force is determined according to the effective area of the side on the left S 1The pressure decreases from P 1z to P 2z as other part of the Download scientific diagram Highperformance voice coil servovalve from publication: Present Status and Prospect of HighFrequency Electrohydraulic Vibration Control Technology Abstract Highperformance voice coil servovalveHigh Frequency Vibration Testing Typical electrodynamic shakers have a usable frequency range up to 2,0003,000 Hz For higher frequency applications, UD engineers have developed two different shaker systems optimized for sine High Frequency Vibration Testing UDCOHighfrequency Acoustic excitations are generated by highpressure drops at relief valves, This phenomenon is known as resonance, and it can cause high vibration, even fatigue, and subsequently, failure In highly critical systems, many a time hydraulic cylinders and dynamic dampers are installed to reduce pipe mon Causes of Piping Vibration: How to Reduce Pipe Vibration?
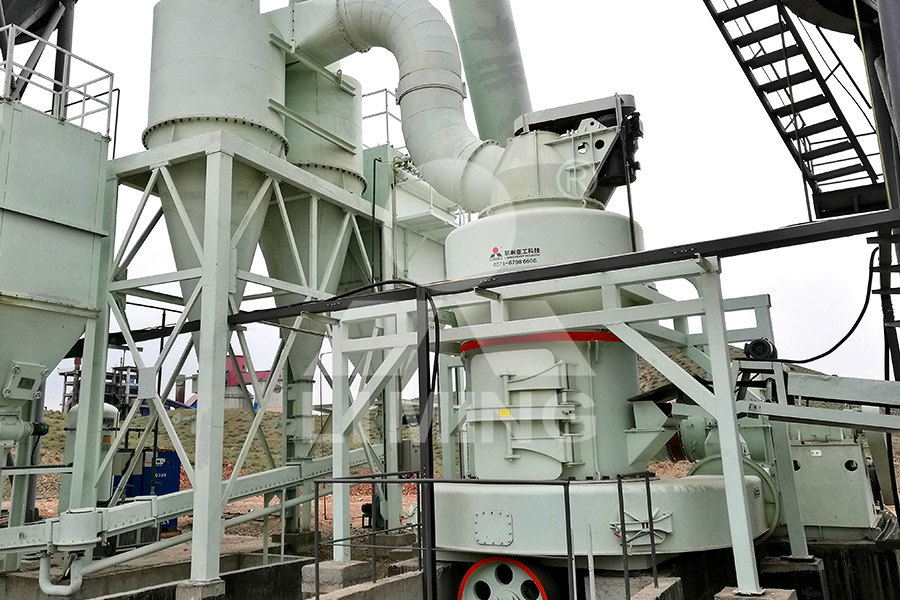
Vibratory driving of piles and sheet piles State of practice
of the operating frequency If the operating frequency of the vibrator approaches the system resonance frequency, the ground vibrations will be strongly amplified As the vibration frequency can be adjusted during vibratory driving, resonance Time history Frequency spectrum (a) (b) Figure 1 Illustration of impact driving of pile and vibration2023年10月10日 This is the raw data, and it can confirm or provide insight into faults such as impacting, hydraulic issues, cavitation, gear and bearing faults, amplitude modulation, rubbing, nonlinear (more movement in one direction) andhigh frequency vibration faults However, the time wave form often includes many synchronous and non Pump Vibration Troubleshooting Strategies, Part 22023年10月5日 21 Traditional electrohydraulic vibration cylinder As shown in Fig 1, the working principle of the traditional electrohydraulic vibration cylinder is to input vibration excitation signals (mostly sinusoidal periodic signals) to the electrohydraulic servo valve, control the highfrequency reversing of the electrohydraulic servo valve to make the hydraulic oil alternately Design and research on virtual prototype of electrohydraulic vibration 2012年6月1日 To further confirm that the reported high pump vibration is mainly caused by this High Suction Energy Cavitation / Suction Recirculation hydraulic excitation, the "Suction Pressure Pulsations" were also measured and plotted against the percent bep flow rates (as shown in Figure 4), to see if it tracked with the vibration trend of higher How to Determine Root Cause of Excessive Pump Vibration
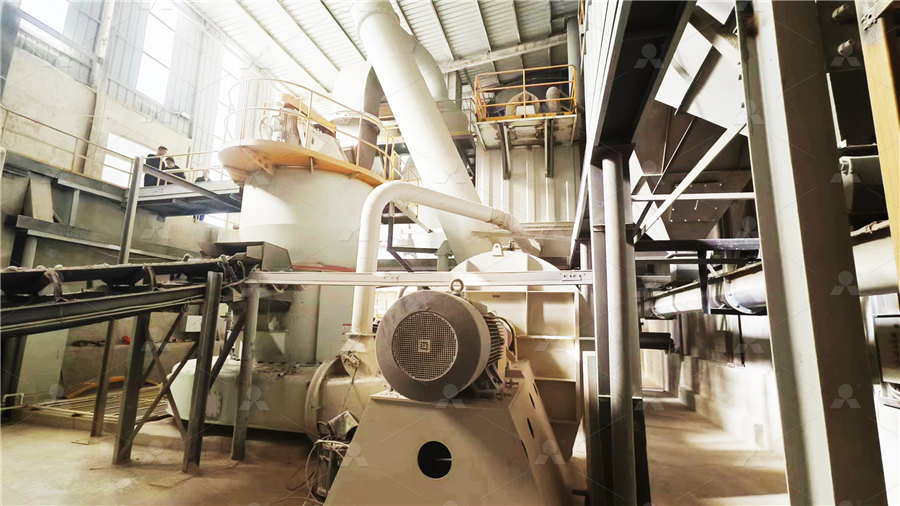
Analytical solution to orifice design in a rotary valve controlled
2019年4月2日 The present study is focused on a novel method for the acquisition of highfrequency sinusoidal vibration waveform with electrohydraulic vibration exciter A rotary valve controlled electrohydraulic vibration exciter is proposed to make it easier to obtain high vibration frequency than the conventional servo valve controlled counterpart Three common used 2024年2月1日 Among these methods, UVRB uses piezoelectric ceramics to excite ultrahighfrequency (UHF) (≥20 kHz) vibration, Finally, uniaxial compression tests were performed using an MTS 81504 electrohydraulic servo motor testing machine (Fig 2 c) to calculate the reductions in strength and stiffnessNovel hard rock breaking technique using ultrahighfrequency