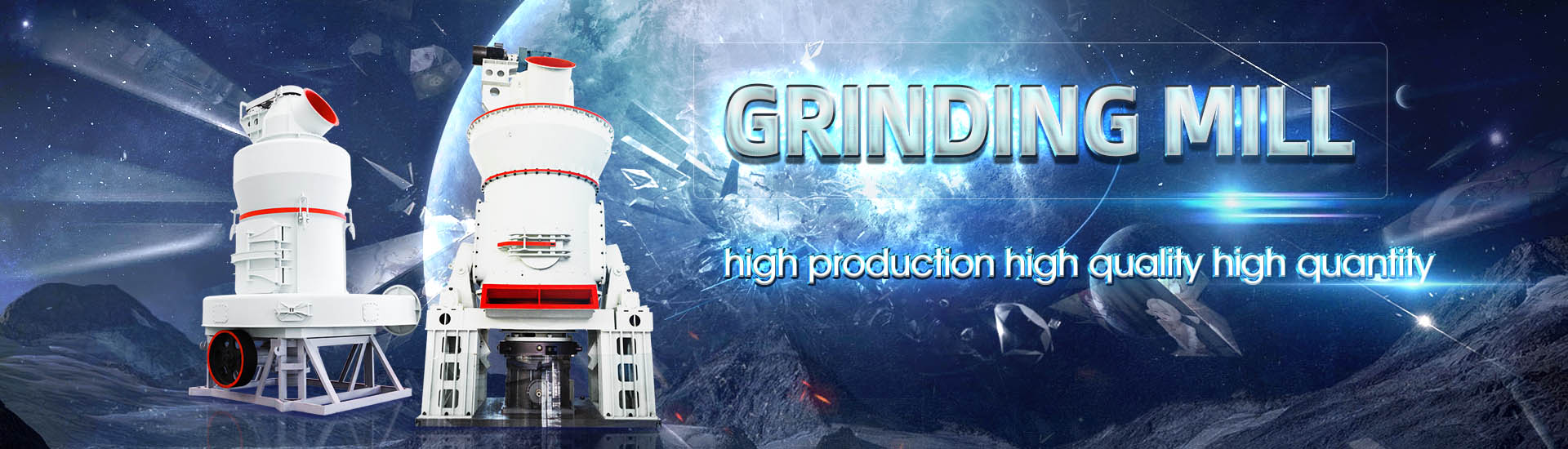
600 ore How big a reducer should a grinding mill be equipped with
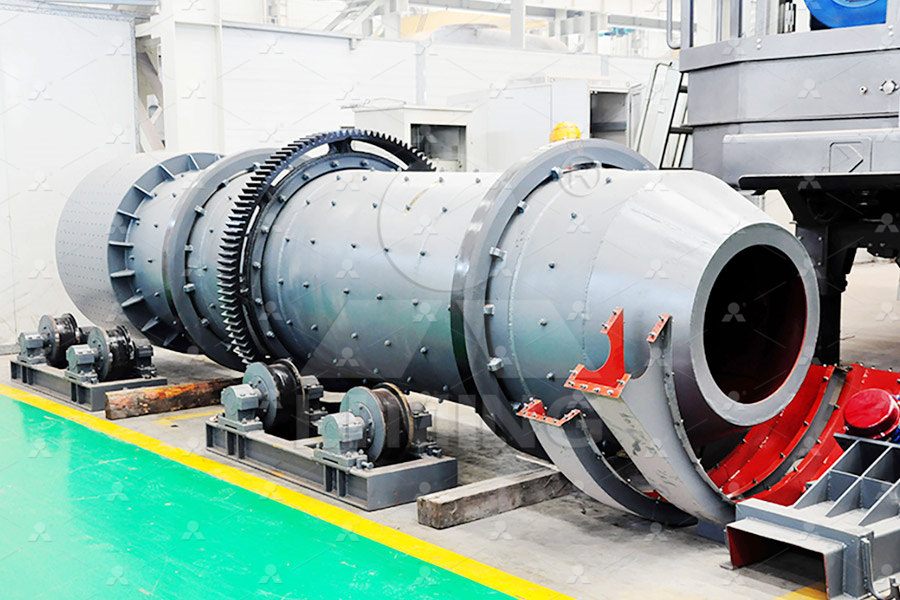
(PDF) SIZE REDUCTION BY GRINDING METHODS
2017年3月4日 Size Reduction is mainly done through crushers and mills Crushing and grinding are the two primary comminution processes Crushing is normally carried out on the "runofm ine" ore slurriedThe feed must enter at a uniform controlled rate and should be precrushed to a maximum particle size of about 12 mm Attrition mills grind from 1/2 to 8 ton/h to products that will pass a 200mesh screenSize Reduction1: Grinding – Unit Operations in 2020年11月11日 This article introduces roller mills and explains how they efficiently grind friable materials to a uniform final particle size while using relatively little energyRoller mills: Precisely reducing particle size with greater 2023年1月1日 It can be concluded that the ball mill should be operated with the optimum media size and higher mill speed for efficient grinding for PGE bearing chromite ore in ball mill Size reduction performance evaluation of HPGR/ball mill and
.jpg)
Fine Grinders, Hammer Mills, and More for
If your application needs reduction, whether 6inch to submicron size, choose from Prater’s superior fine grinders, air classifying mills, hammer mills, and lump breakers to meet all of your industrial processing needs We have been 2017年4月1日 Pilot plant test results with various ores showed that low energy consumption feature of vertical roller mills is applicable to the ore industry Grinding test results for zinc ore Operational parameters affecting the vertical roller mill 2016年1月1日 The crushers are normally fed with rocks, up to about 1 m in size, while the grinders are usually fed with rocks crushed down to a maximum size of about 50 mm Larger Size Reduction and Energy Requirement ScienceDirect2024年10月13日 Grinding mills operate on the principle of breaking down ore particles into smaller sizes through the action of abrasion The primary types of grinding mills include ball Understanding the operation of grinding mills in the mining
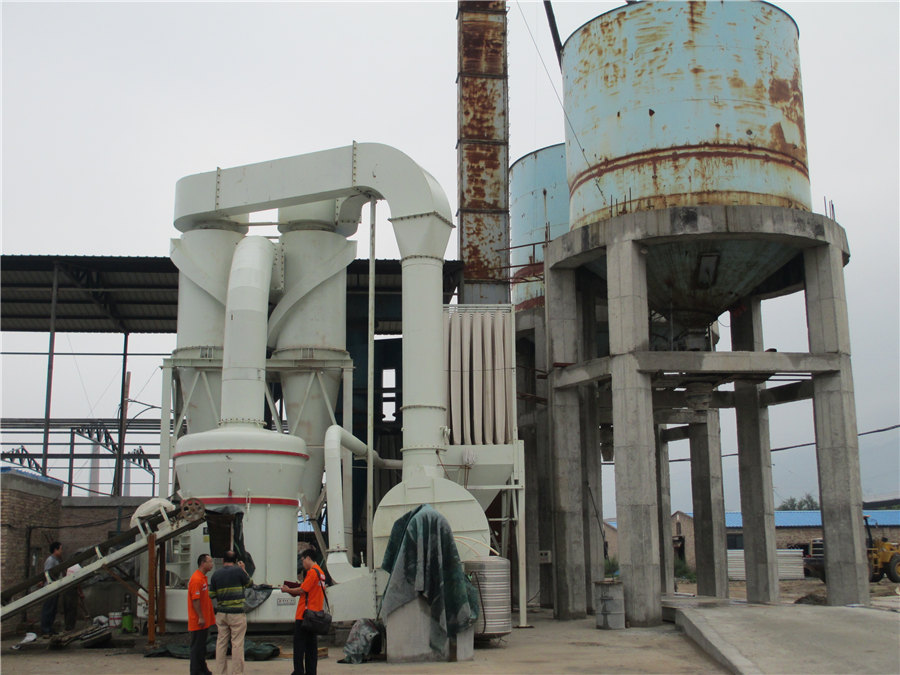
Ball Mill (Ball Mills Explained) saVRee saVRee
Ball mills are employed in the comminution stage as grinding machines (size reduction) The purpose of grinders in the mining industry is to reduce the feed material size in order to liberate the minerals from the barren rock Ball mills 2017年10月3日 Share with Facebook; Share with Twitter; Share with Google+; Share with LinkedIn; Posted: October 3, 2017 Grinding Mills Types, Working Principle Applications The purpose of this article is to explain the usage of Grinding Mill Types, Working Principle Ball sizes that are used in grinding should be large enough to break the largest and hardest ore particles Optimal ball sizes depend on the feed/product size ratio, mill dimensions, and breakage kinetics parameters Usually, larger balls grind coarser ore particles efficiently and smaller balls grind fine particles more efficiently [59](PDF) Grinding Media in Ball MillsA Review Academia2015年8月6日 Slurry characteristics can be manipulated and tested to determine their effect on grinding efficiency There are three mill slurry characteristics which you should note The % fines in the rod mill feed For the purposes of rod mill performance analysis, “fines” can be arbitrarily defined as particles finer than 75 microns (200 mesh)Ball Rod Mill Density – How Water Impacts Grinding
.jpg)
Ball Mill (Ball Mills Explained) saVRee saVRee
Ball Mill Introduction There are three main stages to mineral processing in the mining industryThese are: Comminution (crushing and grinding); Beneficiation (separation and concentration); Smelting and refining; Ball mills are employed in the comminution stage as grinding machines (size reduction)The purpose of grinders in the mining industry is to reduce 2016年7月8日 The Work Index values listed in Table I and II apply directly to a wet grinding overflow type rod mill 75 feet in diameter in open circuit; and to a wet grinding overflow type ball mill 75 feet in diameter in closed circuit with a rake classifier at 250% circulating load, and with 80% or more of the feed passing 4 meshEquipment Sizing: Crusher or Grinding Mill 911Metallurgist2007年7月1日 Adjustment to ball size could lead to significant improvement in grinding mill throughput (McIvor, 1997)The Bond’s equation for ball sizing (McIvor, 1997) can help in selecting the ball size for a given ore and grinding millBall mill simulations with ball wear modelling can also be used to identify the optimum ball size (Concha et al, 1992) for a given applicationShould the slurry density in a grinding mill be adjusted as a 2016年4月22日 In all ore dressing and milling processes, including flotation, cyanidation, gravity concentration, and amalgamation, it is necessary to crush and grind, often with rob mill ball mills, the ore in order to liberate the minerals In the chemical and process industries, grinding is an important step in preparing raw materials for subsequent treatmentBall Mill Rod Mill Design 911Metallurgist
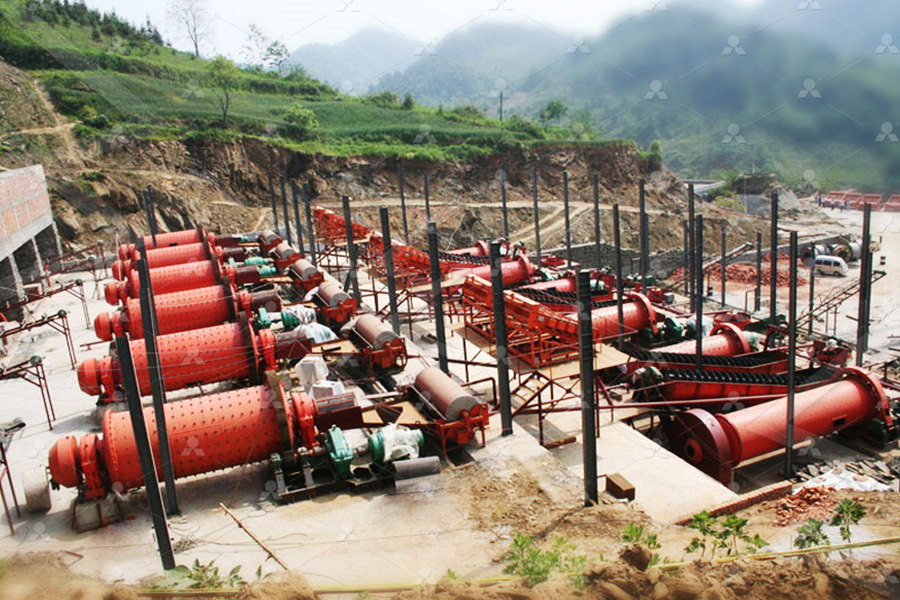
Roller mills: Precisely reducing particle size with greater
2020年11月11日 microns The roller mill’s ability to reduce materials to a uniform particle size provides more control of product characteristics and minimizes waste, as shown in Figure 1 The mill’s controlled reduction action requires less energy than other grinding methods, improving production efficiency and saving energy dollars2017年2月13日 In all ore dressing and milling Operations, including flotation, cyanidation, gravity concentration, and amalgamation, the Working Principle is to crush and grind, often with rod mill or ball mill, the ore in order to liberate the minerals In the chemical and process industries, grinding is an important step in preparing raw materials for subsequent treatmentBall Mills 911Metallurgist2015年7月28日 A mill full of grinding media and ore is very heavy, to have this great weight brought up to its running speed puts a great strain on the electrical motor and require a great surge of electrical power In many mines, care has to be taken not to start the larger circuits at the same time A power failure will result, possibly plugging or Grinding Mill Gear Assembly 911Metallurgist2012年6月1日 As the cylinder starts to rotate, the grinding balls inside the cylinder crush and grind the feed material, generating mechanical energy that aids in breaking bonds, activating the catalyst, and (PDF) Grinding in Ball Mills: Modeling and Process Control
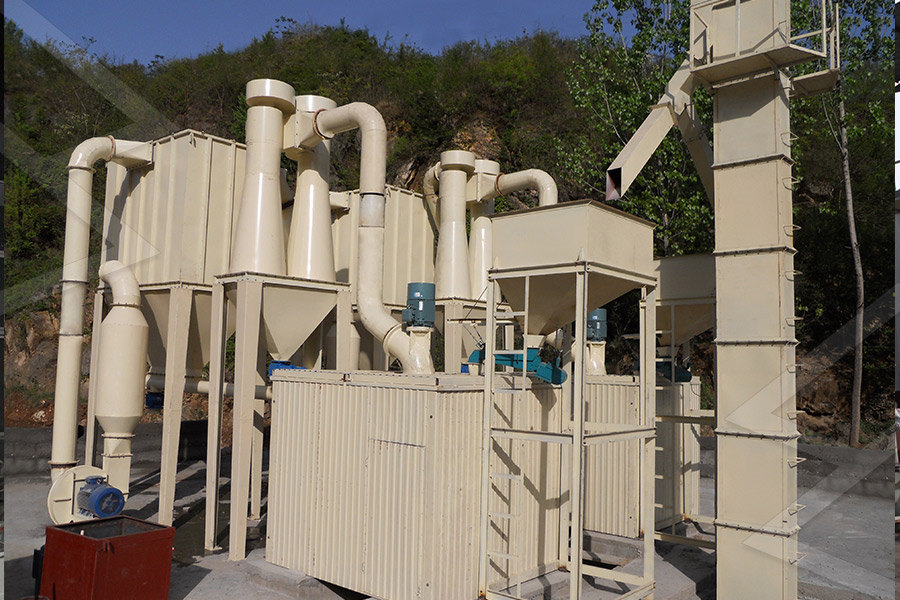
Should the slurry density in a grinding mill be adjusted as a
2007年7月1日 The Bond’s equation for ball sizing (McIvor, 1997) can help in selecting the ball size for a given ore and grinding mill Ball mill simulations with ball wear modelling can also be used to identify the optimum ball size (Concha et al, 1992) for a given application However the usual practice is to conduct full scale trials during which the 2017年10月25日 For fine grinding (normal rod mill product) mill efficiency and rotational speed are less interdependent (Gow et al, 1934), and therefore slightly reduced speeds may be desirable in order to provide a suitable balance between maximum power rating for a given size of equipment, and provision for future speed up to accomodate a capacity increase Recommended Ball Mill Speed Liner ConfigurationThe rock and grinding media are placed in the mill and rotated, causing the grinding media to tumble and crush the rock into smaller pieces The mill operates in a closed circuit with screens that size the ore and send it back to the mill for further grinding The product from the mill is then sent to a cyclone for separation of the desired A Comprehensive Guide to SAG Mill Operation ball mills 2017年6月2日 Table Source: Wikipedia (Crushers) Cone crushers use a spinning cone that gyrates in the bowl in an eccentric motion to crush the rock between the cone surface, referred to as the mantle, and the crusher bowl linerGyratory crushers are very similar to cone crushers, but have a steeper cone slope and a concave bowl surface As the gap between the bowl liner How it Works: Crushers, Grinding Mills and Pulverizers
.jpg)
Rod Mills: Efficient Grinding Solutions for Mining
2016年6月1日 The Steel Head Rod Mill (sometimes call a bar mill) gives the ore dressing engineer a very wide choice in grinding designHe can easily secure a standard Steel Head Rod Mill suited to his particular problem The successful operation of any grinding unit is largely dependent on the method of removing the ground pulp2013年4月1日 However, a lot of academic applications have been developed using Matlab/Simulink R le Roux et al (2013) proposed and validated a novel and simple nonlinear model, Sbárbaro (2010), Liu and Analysis and validation of a runofmine ore grinding mill 2020年3月20日 Ball mill: When the particle size of the product is less than 05mm, the grinding effect of the ball mill is greater than that of a rod mill of the same specification SAG mill: The SAG mill has a wide range of feeding particle sizes and can process larger minerals, but at the same time, its output particle size is relatively largerWhat’s the Difference Between Ball Mill, Rod Mill and SAG Mill?2017年7月26日 The power drawn and reduction achieved to the grinding mill feed will be maximized The grinding mill output will vary considerably with the Work Index If the feed size was 13,000 micrometers for the same grind production size, theoretical output from Fig (21) would change from about 90,000 tons per day on the 13 Work Index down to 65,000 How Ball Mill Ore Feed Size Affects Tonnage Capacity
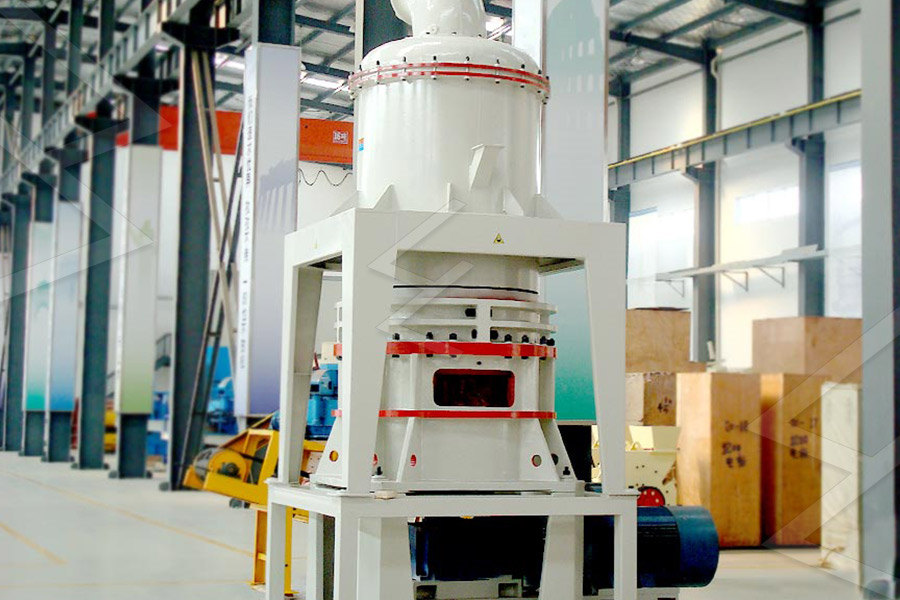
A Review of the Grinding Media in Ball Mills for Mineral
2023年10月27日 The ball mill is a rotating cylindrical vessel with grinding media inside, which is responsible for breaking the ore particles Grinding media play an important role in the comminution of mineral High pressure grinding mill, also known as high pressure roller mill, can grind nonflammable and explosive materials with Mohs hardness not greater than 93 and humidity below 6%Its main components include main engine, reducer, YGM High Pressure Grinding Mill2023年10月10日 Types of Grinding Mills Grinding mills play a crucial role in the mining process, as they are responsible for reducing large chunks of ore into smaller particles that can be further processed There are various types of Understanding the SAG Mill in Copper Ore Step 1: Mill overload power •Determine a set of operating conditions that reflects the maximum “overloaded” condition that the mill should be able to handle: –SAG mills: 20% v/v ball charge, 30% v/v filling and 78% critical speed with worn liners –Ball mills: 36% v/v filling and 78% critical speed with worn linersChoosing the Right Motors for your Mills
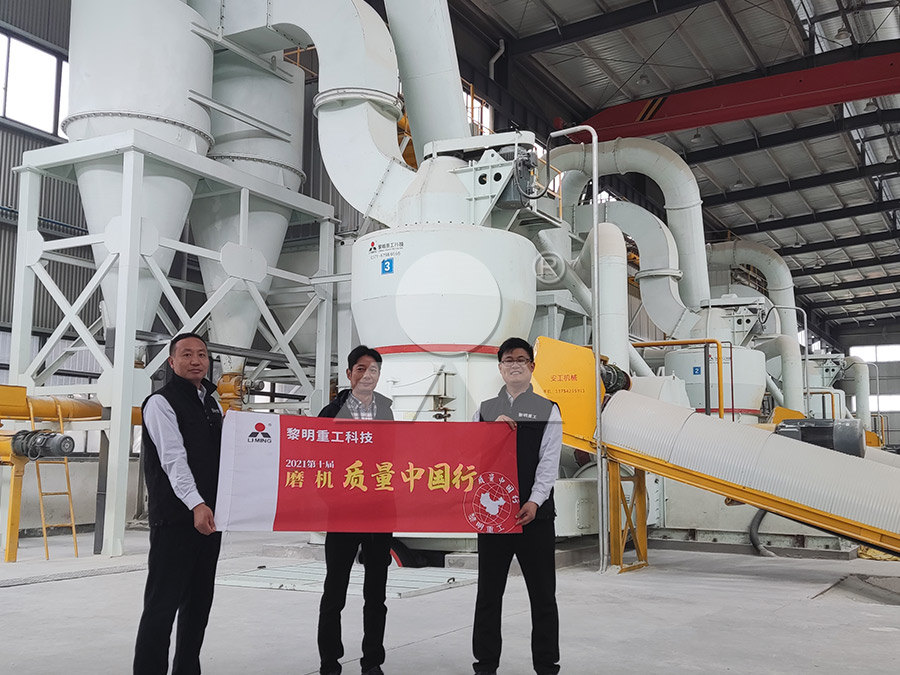
(PDF) A comparison of wear rates of ball mill grinding media
2016年1月1日 In wet grinding practice, highstress abrasion occurs over a small region when ore particles are trapped between the grinding balls and the mill liner, and the load is sufficient to fracture 2023年4月30日 Ball mill is a type of grinding equipment that uses the rotary cylinder to bring the grinding medium and materials to a certain height and make them squeeze, impact, and grind and peel each other to grind materials rotating part, and transmission part (speed reducer, small drive gear, motor, and electric control) The cylinder is generally Ball Mill SpringerLink2013年8月3日 In Grinding, selecting (calculate) the correct or optimum ball size that allows for the best and optimum/ideal or target grind size to be achieved by your ball mill is an important thing for a Mineral Processing Engineer AKA Metallurgist to do Often, the ball used in ball mills is oversize “just in case” Well, this safety factor can cost you much in recovery and/or mill liner Calculate and Select Ball Mill Ball Size for Optimum Grinding2018年4月17日 Mill Sizing: After laboratory and pilot plant testing confirm the feasibility of autogenous or semiautogenous grinding, it can be used to establish the exact grinding circuit and mill sizeIn the pilot plant tests, the tare power of the pilot plant mills should be determined before and after each test run The tare power should be for the empty millAutogenous and SAG SemiAutogenous Mill Design Calculations
.jpg)
CLUM Ultrafine Vertical Grinding Mill
The internal uses PLC intelligent control, the external uses the touch screen to display and adjust the system parameters in real time Modular excuses are reserved, and the scalability is strong, which can quickly realize the connection of the frontend grinding aid adding system, the backend powder modification system and the packaging system to ensure the automatic control of the 2019年11月26日 SAG mills grinding media includes some large and hard rocks, filled rate of 9% – 20% SAG mill grind ores through impact, attrition, abrasion forces In practice, for a given ore and equal processing conditions, the AG milling has a What’s the Difference Between SAG Mill and Ball Mill2018年8月17日 SemiAutogenous Mills/ SAG Mills (primary grinding mill) — these mills use grinding balls with forces of attrition, impact, and abrasion between grinding balls and ore particles that result in Grinding Mills — Types, Working Principle Applications2017年10月3日 Share with Facebook; Share with Twitter; Share with Google+; Share with LinkedIn; Posted: October 3, 2017 Grinding Mills Types, Working Principle Applications The purpose of this article is to explain the usage of Grinding Mill Types, Working Principle
.jpg)
(PDF) Grinding Media in Ball MillsA Review Academia
Ball sizes that are used in grinding should be large enough to break the largest and hardest ore particles Optimal ball sizes depend on the feed/product size ratio, mill dimensions, and breakage kinetics parameters Usually, larger balls grind coarser ore particles efficiently and smaller balls grind fine particles more efficiently [59]2015年8月6日 Slurry characteristics can be manipulated and tested to determine their effect on grinding efficiency There are three mill slurry characteristics which you should note The % fines in the rod mill feed For the purposes of rod mill performance analysis, “fines” can be arbitrarily defined as particles finer than 75 microns (200 mesh)Ball Rod Mill Density – How Water Impacts GrindingBall Mill Introduction There are three main stages to mineral processing in the mining industryThese are: Comminution (crushing and grinding); Beneficiation (separation and concentration); Smelting and refining; Ball mills are employed in the comminution stage as grinding machines (size reduction)The purpose of grinders in the mining industry is to reduce Ball Mill (Ball Mills Explained) saVRee saVRee2016年7月8日 The Work Index values listed in Table I and II apply directly to a wet grinding overflow type rod mill 75 feet in diameter in open circuit; and to a wet grinding overflow type ball mill 75 feet in diameter in closed circuit with a rake classifier at 250% circulating load, and with 80% or more of the feed passing 4 meshEquipment Sizing: Crusher or Grinding Mill 911Metallurgist
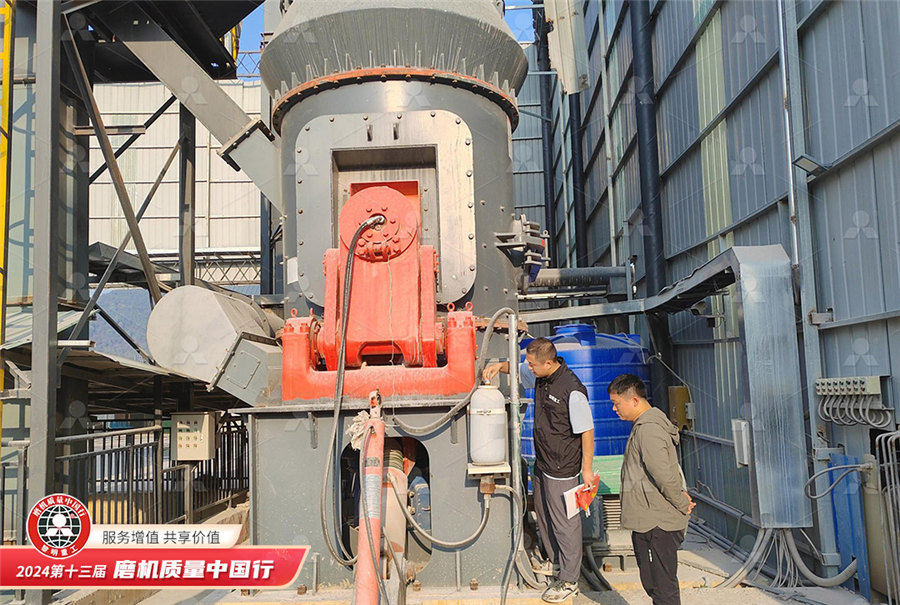
Should the slurry density in a grinding mill be adjusted as a
2007年7月1日 Adjustment to ball size could lead to significant improvement in grinding mill throughput (McIvor, 1997)The Bond’s equation for ball sizing (McIvor, 1997) can help in selecting the ball size for a given ore and grinding millBall mill simulations with ball wear modelling can also be used to identify the optimum ball size (Concha et al, 1992) for a given application2016年4月22日 In all ore dressing and milling processes, including flotation, cyanidation, gravity concentration, and amalgamation, it is necessary to crush and grind, often with rob mill ball mills, the ore in order to liberate the minerals In the chemical and process industries, grinding is an important step in preparing raw materials for subsequent treatmentBall Mill Rod Mill Design 911Metallurgist2020年11月11日 microns The roller mill’s ability to reduce materials to a uniform particle size provides more control of product characteristics and minimizes waste, as shown in Figure 1 The mill’s controlled reduction action requires less energy than other grinding methods, improving production efficiency and saving energy dollarsRoller mills: Precisely reducing particle size with greater 2017年2月13日 In all ore dressing and milling Operations, including flotation, cyanidation, gravity concentration, and amalgamation, the Working Principle is to crush and grind, often with rod mill or ball mill, the ore in order to liberate the minerals In the chemical and process industries, grinding is an important step in preparing raw materials for subsequent treatmentBall Mills 911Metallurgist
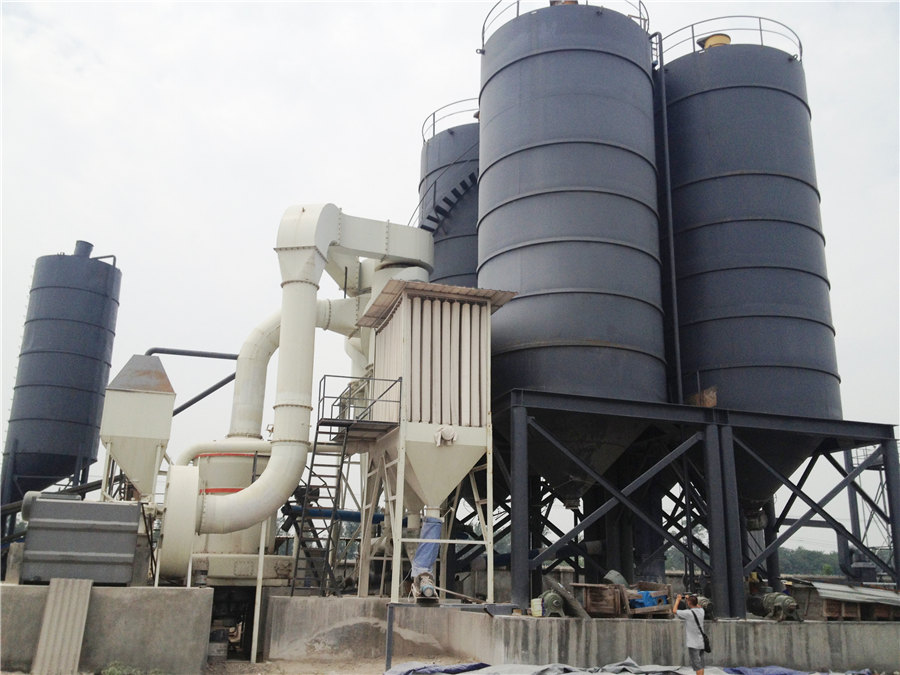
Grinding Mill Gear Assembly 911Metallurgist
2015年7月28日 A mill full of grinding media and ore is very heavy, to have this great weight brought up to its running speed puts a great strain on the electrical motor and require a great surge of electrical power In many mines, care has to be taken not to start the larger circuits at the same time A power failure will result, possibly plugging or