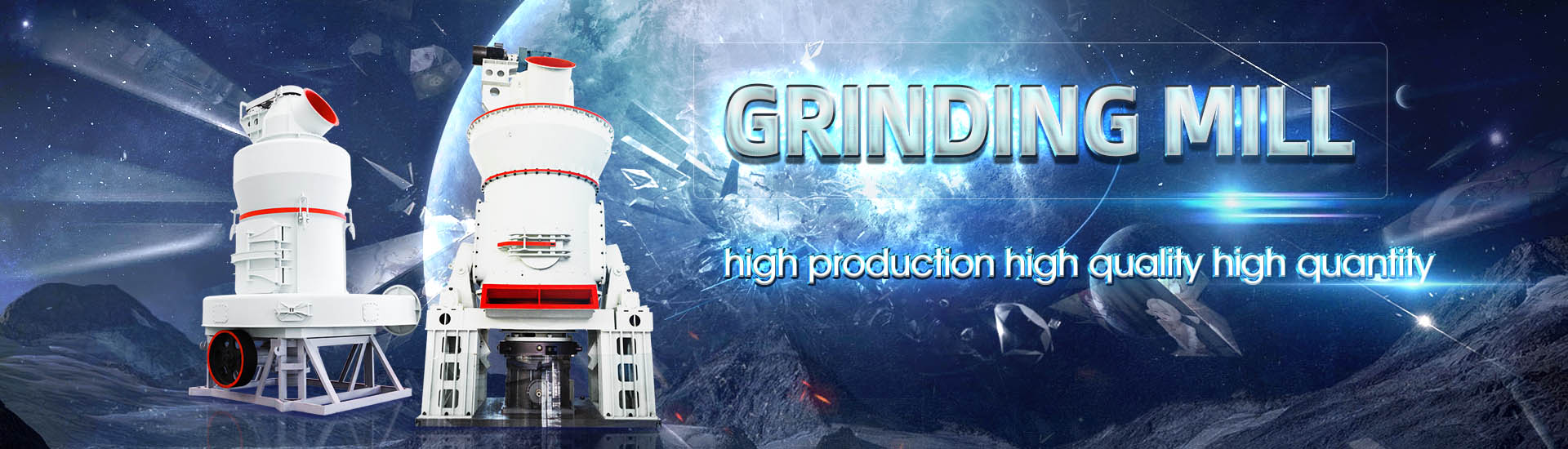
Recover lithium mica iron after slag quenching
.jpg)
Research articleRecycling of lithium slag extracted from
2020年7月1日 In this paper, the effects of LS from lithium mica on mineral composition and properties of white Portland cement were studied It provides a theoretical basis for utilization of LS from lithium mica2024年8月5日 To address these challenges, this study introduces a closedloop recovery process for spent ternary cathode materials, employing sulfurassisted roasting to achieve A mild and efficient closedloop recycling strategy for spent lithium 2024年10月1日 The efficient and selective recovery of Li from lithiumcontaining smelting slag is crucial for the shortprocess recycling of SLIBs [30] Dang [31] achieved outstanding selectivity Selective extraction of Li and Mn from spent lithiumion 2024年6月5日 The key to recovering waste LiFePO 4 (LFP) is the recovery of lithium; however, the effective and synchronous recovery of phosphorus and iron resources still needs to be Efficient recovery of phosphorus and iron from the lithium
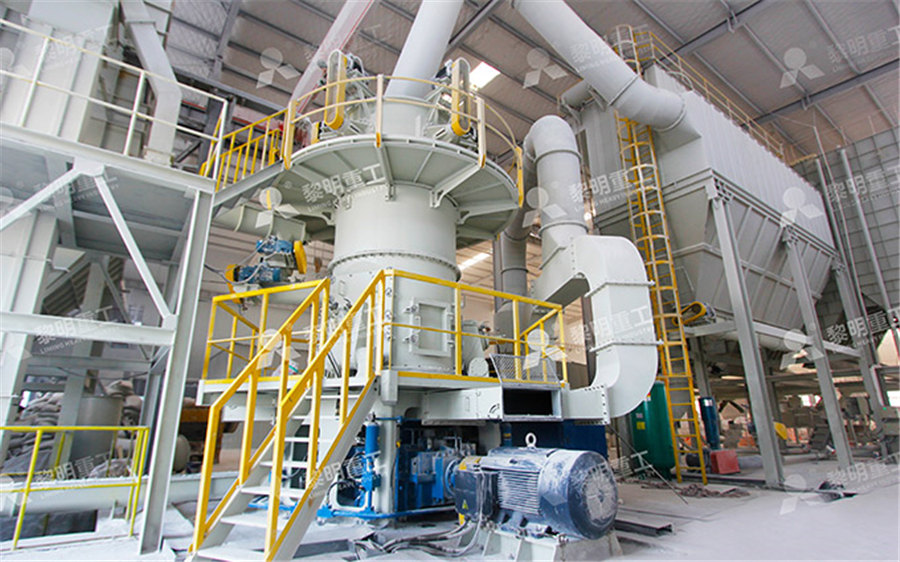
Recovery of Valuable Metals from Spent LithiumIon
2017年5月25日 The process includes five main procedures: (1) pretreatment of spent LIBs by roasting at 800 °C for 2 h; (2) production of Co–Ni–Cu–Fe–Mn alloy and manganeserich slag 2013年1月1日 This paper investigates mineral processing techniques for the extraction of lithium rich mineral concentrates, in order to recycle lithium hence making it a sustainable source for future(PDF) Recovery of lithium rich mica from mineral 2021年8月23日 A textbook example for such approaches is lithium recovery from black mass by the COOLprocess, which had been proven unparalleled effective in processing zinnwaldite, a lithium ore 10 Here, after separating and Recovery of Al, Co, Cu, Fe, Mn, and Ni from 2023年6月1日 Improving the recovery efficiency of Li is currently a key technical bottleneck in the recycling of spent lithiumion battery; priority recovery of Li before nickel and cobalt Preferential Recovery of Lithium Based on Mineral Phase
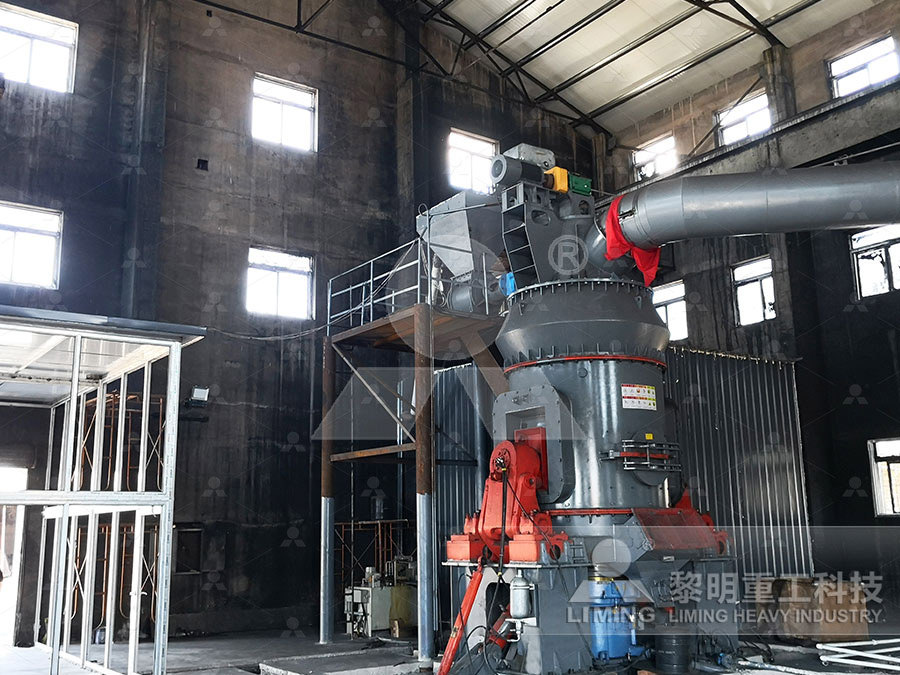
Pyrometallurgical LithiumIonBattery Recycling:
2020年11月26日 The promising results show technically feasible reaction temperatures of 800 ∘C to 1000 ∘C and high recovery potentials for nickel, cobalt and manganese Furthermore, the slagging of lithium was largely prevented 2024年7月29日 Recycling lithium (Li) from spent lithiumion batteries (LIBs) due to the depletion of natural resources and potential toxicity is becoming a progressively favourable measure to Earlystage recovery of lithium from spent batteries via CO2023年1月11日 Lithium slag is a byproduct of lithium carbonate industry; in the past decades, due to ascending demand of lithium salts, emission of this kind of solid waste is dramatically increased and Mechanism and assessment of the pozzolanic activity of 2024年10月10日 The integration of lithium into technological applications has profoundly influenced human development, particularly in energy storage systems like lithiumion batteries With global demand for lithium surging alongside Critical Review of Lithium Recovery Methods:
.jpg)
Solidification and heat transfer of molten steel slag particles
2022年12月8日 The air quenching process is a simple traditional onetime treatment process of molten steel slag, which not only is safe and efficient, but also creates great conditions for waste heat recycling The process of air quenching is to use highpressure air to strike molten steel slag The molten steel slag is broken into small droplets [13,14,15 2012年7月31日 Blast furnace (BF) slag, which is the main byproduct in the ironmaking process, contains large amounts of sensible heat To recover the heat, a new waste heatrecovery system—granulating molten BF slag by rotary multinozzles cup atomizer and pyrolyzing printed circuited board with obtained hot BF slag particle—was proposed in this study The feasibility Waste Heat Recovery from Blast Furnace Slag by Chemical 2023年5月4日 However, at present, the average recovery rate of waste heat resources per ton of steel in China's iron and steel industry is less than 26%, while the sensible heat recovery rate of various molten Development of waste heat recovery technology from steel slag2017年5月15日 The presently used approaches for the recovery of spent LIBs like pyrometallurgical process can effectively recover nickel, cobalt, and copper, while lithium is usually lost in slag Bioleaching process as an alternative method of extraction and recovery of valuable metals from the primary and secondary resources has been attracting a large Lithium recovery from lithiumcontaining micas using sulfur oxidizing
.jpg)
An approach towards utilization of waterquenched blast furnace slag
2022年8月1日 Resource utilization of waterquenched blast furnace slag (BFS) for recovery of valuable metals such as titanium, magnesium, and aluminum are strategic issues for the iron and steel industry's longterm development This study proposed a sustainable strategy for simultaneous Ti, Mg, and Al extraction from waterquenched BFS using the ammonium sulfate 2023年1月11日 Lithium slag (LS) is an industrial waste discharged from smelting process of lithium products using spodumene or lepidolite [12] Present researches have demonstrated that LS is mainly consist of amorphous silicon dioxide (SiO 2) and aluminum oxide (Al 2 O 3), which provides positive effect on its pozzolanic activity [13], [14]In recent years, the rapid Mechanism and assessment of the pozzolanic activity of 2023年1月11日 The current energy consumption and waste emission are mainly produced from the process of cement manufacturing Lithium slag (LS), a solid waste from lithium smelting, has been utilized as concrete additives with a low rate of approximately 10 %, and the remaining nearly 90 % of LS are stored as industrial solid waste, which not only occupies large amounts Mechanism and assessment of the pozzolanic activity of 2023年2月1日 As lithium has a very low Clark (around 20 ppm) (Robb, 2005), knowing lithium occurrences is mandatoryMain lithium deposits are brines (also known as salars) and hard rock mineral deposits (Gruber et al, 2011, Kesler et al, 2012, Penner, 1978)Recovery of lithium from brines implies different techniques such as precipitation, adsorption or solvent extraction Froth flotation of lithium micas – A review ScienceDirect
.jpg)
Recycling of lithium slag extracted from lithium mica by
2020年7月1日 The tantalumniobium ore in Yichun of Jiangxi province is one of the most important lithium ore resources in China With the rapid development of Chinese new energy industry, the market demand for lithium salt is increasing day by day, leading to a significant increase in the production capacity of lithium mica (MorenoBrieva and Marín, 2019; Liu et al, DOI: 101080/2024 Corpus ID: ; Efficient recovery of phosphorus and iron from the lithium extraction slag by the leaching precipitation method @article{Tu2024EfficientRO, title={Efficient recovery of phosphorus and iron from the lithium extraction slag by the leaching precipitation method}, author={Tao Tu and Xiuyuan Yu and Efficient recovery of phosphorus and iron from the lithium 2012年7月31日 sary to dry the slag to produce cement To recover the sensible heat of BF slag, three key problems should be considered: (I) the dry granulation of BF slag without consuming water, (II) increasing the recovery rate of the waste heat efficiently, and (III) the usage of the slag particles after heat recovery On this topic of BF slag, manyWaste Heat Recovery from Blast Furnace Slag by 2024年8月21日 In general, pyrometallurgical, hydrometallurgical, and biohydrometallurgical techniques as well as direct regeneration approach are available to recycle spent LIBs [17], [27]Green and practical separation of lithium and iron phosphate has consistently been an issue in recycling used lithiumion batteries because the intrinsic property of olivinestructure LFP A facile route for the efficient leaching, recovery, and
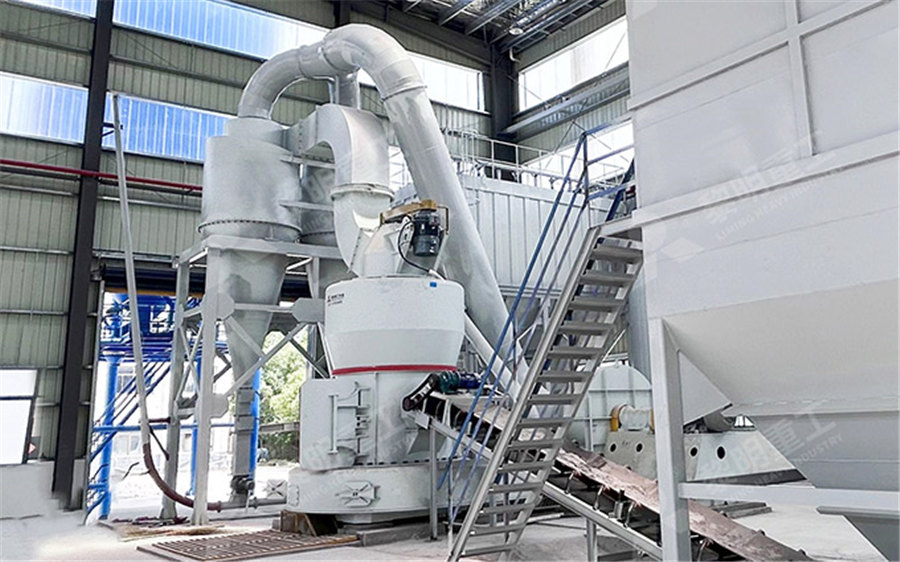
RESEARCH OVERVIEW ON RECOVERY OF WASTE HEAT
2020年2月27日 waste heat recovery process of liquid slag into dry centrifugal granulation process and waste heat recovery process After dry centrifugal granulation, the temperature of blast furnace slag particles was about 900°C Then the particles entered the packed bed for heat transfer, resulting in hot air of 500600°C [5]2024年6月1日 Among them, lithium iron phosphate (LFP) batteries are safe at high operating temperatures The batteries can be stored for a longer time and remain incombustible during recycling or mechanical damage [5]Hence, LFP batteries have gained increasing importance as a potential replacement for LIBs for the applications that require high voltagedischarge rates at Selective recovery of lithium from spent LiFePO4 powders The recycling of Li from secondary sources was one of the important means to alleviate the imbalance between supply and demand of Li resources [[21], [22], [23]]Secondary resources with high Li content were mainly spent lithiumion batteries, alumina electrolysis slag and so on [[24], [25], [26]]Recovery of Li from spent lithiumion batteries was widely reported in literaturesLithium recovery from an alumina electrolysis slag leaching 2005年2月1日 Steelmaking slag, an important metallurgical byproduct, is composed of a large amount of valuable components, including CaO, Fe t O, MnO, and MgO, all of which are required in the steelmaking (PDF) Industrial uses of slag The use and reuse of iron and
.png)
A review on recycling of lithiumion batteries to recover
2022年12月1日 This process has the benefit of reducing the solvent investment After lithium stripping (using 01 M Na 2 CO 3 solution), the recovery of Co 2+ is achieved by using 05 M H 2 SO 4 in the form of CoSO 4 solution [136] With 50% saponified 04 M Cyanex 272 at pH 6, twostage countercurrent operation with O/A ratio of 2, the prediction of the 2024年10月1日 The efficient and selective recovery of Li from lithiumcontaining smelting slag is crucial for the shortprocess recycling of SLIBs [30]Dang [31] achieved outstanding selectivity for lithium with a recovery rate of 9387 % by employing a mixture of K 2 CO 3 and Na 2 CO 3 for roasting with lithiumcontaining simulated slag (CaOAl 2 O 3SiO 2)However, current studies Selective extraction of Li and Mn from spent lithiumion 2012年7月31日 Blast furnace (BF) slag, which is the main byproduct in the ironmaking process, contains large amounts of sensible heat To recover the heat, a new waste heatrecovery system—granulating molten Waste Heat Recovery from Blast Furnace Slag by CDQ is an excellent technology to recover the sensible heat of the hot coke which would be wasted if wet quenching technology is used About 80% hot coke sensible heat, which accounts 35–40% of the energy consumption of coke oven, can be recovered about 135 GJ heat per ton coke []To some extent, environmental pollution can be reduced as a result of avoiding the use Waste Energy Recovery Technology of Iron and Steel
.jpg)
Waste Energy Recovery Technology of Iron and
2017年1月1日 Blast Furnace Slag Quenching Water Waste Heat Recovery A large amount of high temperature molten slag in the iron making (which is called BF slag) should be quenched by the water, which is a and granulating heat recovery device was built at Fushan Iron Works [2] When the temperature is decreased from 1500°C to about 300°C, the heat recovery rate can reach 40~45% Air Quenching and Granulation Vibrating Fluidized Bed Heat Recovery Process The Ural Iron and Steel Research Institute of Russia has developed a slag treatment process Development of waste heat recovery technology from 2023年1月1日 DOI: 102139/ssrn Corpus ID: ; Mechanism and Assessment of the Pozzolanic Activity of MeltingQuenching Lithium Slag Modified with Mgo @article{He2023MechanismAA, title={Mechanism and Assessment of the Pozzolanic Activity of MeltingQuenching Lithium Slag Modified with Mgo}, author={Yan He and Kang Qian and Mechanism and Assessment of the Pozzolanic Activity of 2017年5月25日 We have previously demonstrated a new pyrometallurgicalbased method to recover valuable metals from spent lithiumion batteries However, there was no indepth work on the extraction of valuable metals from polymetallic alloy and manganeserich slag obtained after smelting reduction In this paper, two new technologies were investigated, with one combining Recovery of Valuable Metals from Spent LithiumIon
.jpg)
Waste Energy Recovery Technology of Iron and Steel
2017年8月28日 recover the sinter sensible heat and the Organic Rankine Cycle (ORC) system to recover the waste heat from blast furnace slag quenching water were introduced, and the significance and feasibility were analyzed Fig 1 The general methods and application fields of waste energy recovery in domestic industries 4 X Zhang et alWater quenching blast furnace slag (WQBFS) is widely produced in the blast furnace iron making process It is mainly composed of CaO, MgO, Al2O3, and SiO2 with low contents of other metal elements Treatment procedure of water quenching blast furnace slag2024年11月11日 Different decommissioned lithium iron phosphate (LiFePO 4) battery models and various recycling technologies resulted in lithium extraction slag (LES) with multiple and complex compositions, necessitating ongoing experimentation and optimization to recover iron phosphate (FePO 4)This work proposes a onestep precise selective precipitation strategy for Precise recovery of highlypurified iron phosphate from complex lithium 2013年12月1日 Molten slag exhausted with critically high temperature of about 1450–1550 °C is a potential resource of energy and raw materials Water quenching is a traditional heat recovery technology A review of waste heat recovery technologies towards molten slag
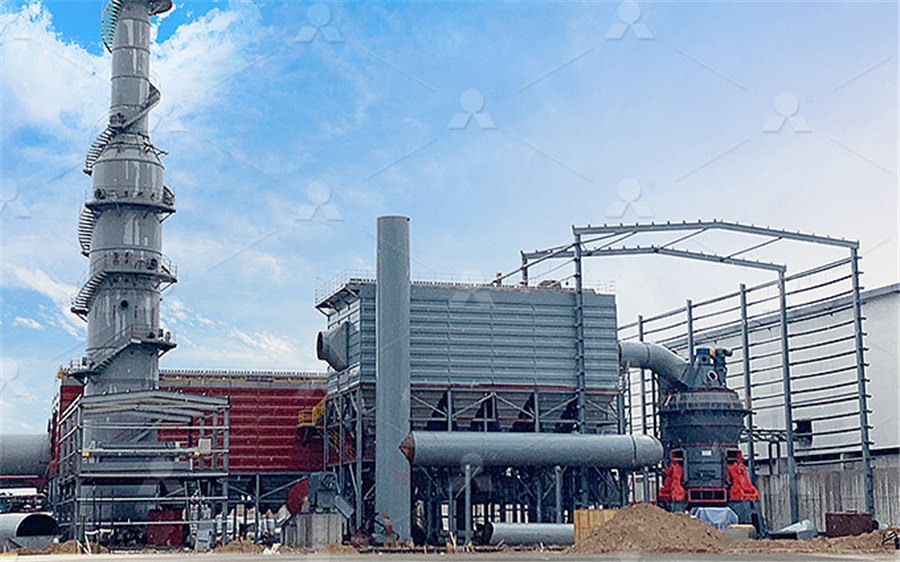
Mechanism and assessment of the pozzolanic activity of
2023年1月11日 Lithium slag is a byproduct of lithium carbonate industry; in the past decades, due to ascending demand of lithium salts, emission of this kind of solid waste is dramatically increased and 2024年10月10日 The integration of lithium into technological applications has profoundly influenced human development, particularly in energy storage systems like lithiumion batteries With global demand for lithium surging alongside Critical Review of Lithium Recovery Methods: 2022年12月8日 The air quenching process is a simple traditional onetime treatment process of molten steel slag, which not only is safe and efficient, but also creates great conditions for waste heat recycling The process of air quenching is to use highpressure air to strike molten steel slag The molten steel slag is broken into small droplets [13,14,15 Solidification and heat transfer of molten steel slag particles 2012年7月31日 Blast furnace (BF) slag, which is the main byproduct in the ironmaking process, contains large amounts of sensible heat To recover the heat, a new waste heatrecovery system—granulating molten BF slag by rotary multinozzles cup atomizer and pyrolyzing printed circuited board with obtained hot BF slag particle—was proposed in this study The feasibility Waste Heat Recovery from Blast Furnace Slag by Chemical
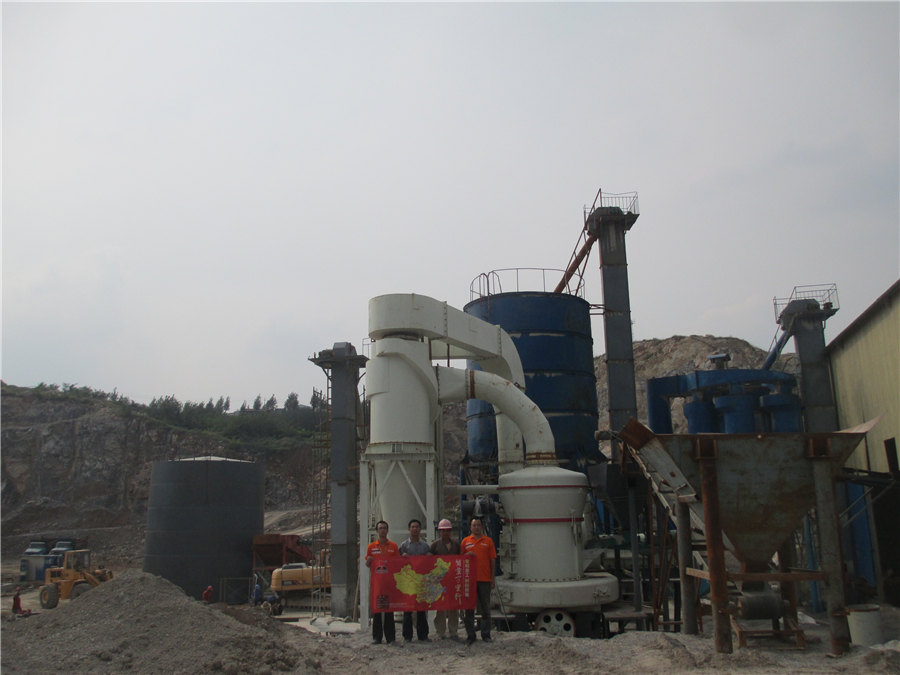
Development of waste heat recovery technology from steel slag
2023年5月4日 However, at present, the average recovery rate of waste heat resources per ton of steel in China's iron and steel industry is less than 26%, while the sensible heat recovery rate of various molten 2017年5月15日 The presently used approaches for the recovery of spent LIBs like pyrometallurgical process can effectively recover nickel, cobalt, and copper, while lithium is usually lost in slag Bioleaching process as an alternative method of extraction and recovery of valuable metals from the primary and secondary resources has been attracting a large Lithium recovery from lithiumcontaining micas using sulfur oxidizing 2022年8月1日 Resource utilization of waterquenched blast furnace slag (BFS) for recovery of valuable metals such as titanium, magnesium, and aluminum are strategic issues for the iron and steel industry's longterm development This study proposed a sustainable strategy for simultaneous Ti, Mg, and Al extraction from waterquenched BFS using the ammonium sulfate An approach towards utilization of waterquenched blast furnace slag 2023年1月11日 Lithium slag (LS) is an industrial waste discharged from smelting process of lithium products using spodumene or lepidolite [12] Present researches have demonstrated that LS is mainly consist of amorphous silicon dioxide (SiO 2) and aluminum oxide (Al 2 O 3), which provides positive effect on its pozzolanic activity [13], [14]In recent years, the rapid Mechanism and assessment of the pozzolanic activity of
.jpg)
Mechanism and assessment of the pozzolanic activity of
2023年1月11日 The current energy consumption and waste emission are mainly produced from the process of cement manufacturing Lithium slag (LS), a solid waste from lithium smelting, has been utilized as concrete additives with a low rate of approximately 10 %, and the remaining nearly 90 % of LS are stored as industrial solid waste, which not only occupies large amounts 2023年2月1日 As lithium has a very low Clark (around 20 ppm) (Robb, 2005), knowing lithium occurrences is mandatoryMain lithium deposits are brines (also known as salars) and hard rock mineral deposits (Gruber et al, 2011, Kesler et al, 2012, Penner, 1978)Recovery of lithium from brines implies different techniques such as precipitation, adsorption or solvent extraction Froth flotation of lithium micas – A review ScienceDirect