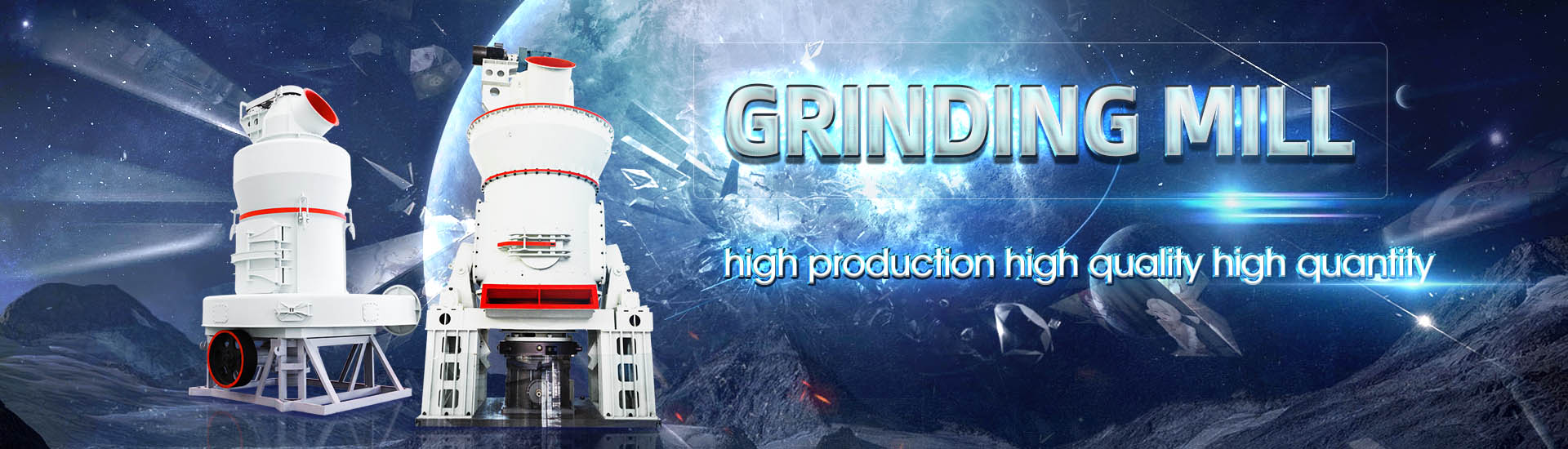
Current status of cement plant coal grinding process New dry cement powder making process
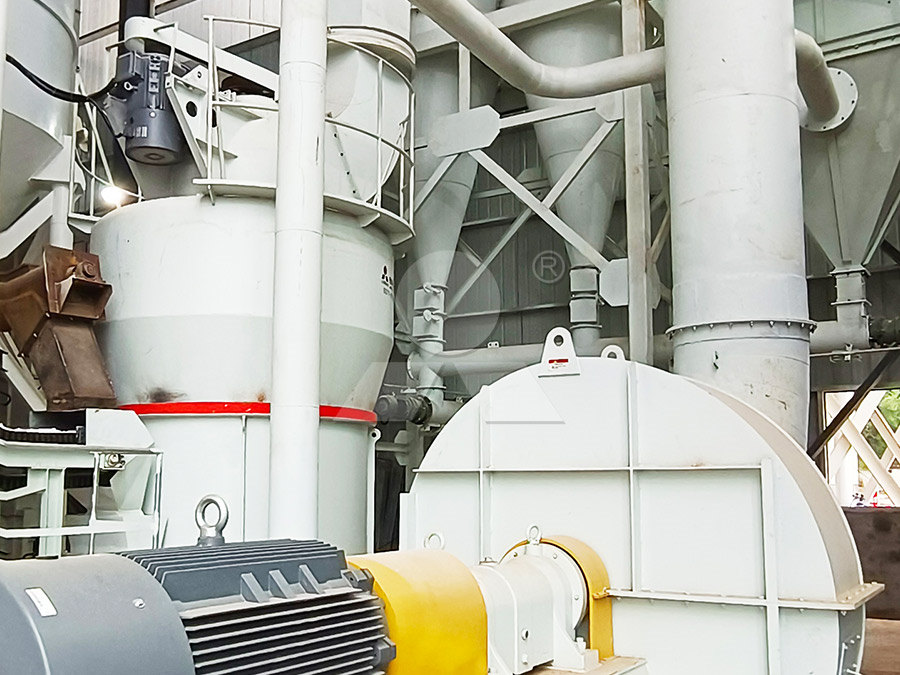
Modernizing cement manufacturing in China leads to
2022年11月17日 The cement manufacturing process mainly includes four steps: resource extraction, raw material preparation, clinker calcination, cement grinding 17,18, and fossil fuel 2023年11月1日 Current stateoftheart grinding in cement plants consists of a separate raw meal grinding device and at least one comminution aggregate for cement grinding For The cement plant of tomorrow ScienceDirect2023年10月13日 According to the World Cement Association, global cement production is expected to reach 82 billion tonnes by 2030 6, 7, 8, 9 Thus, in Western Europe 9, 10, the Global database of cement production assets and upstream 2024年3月1日 Additionally, the optimization of cement clinker composition is a crucial step toward reducing the environmental impact Cement plants have used new grinding equipment, Toward smart and sustainable cement manufacturing process
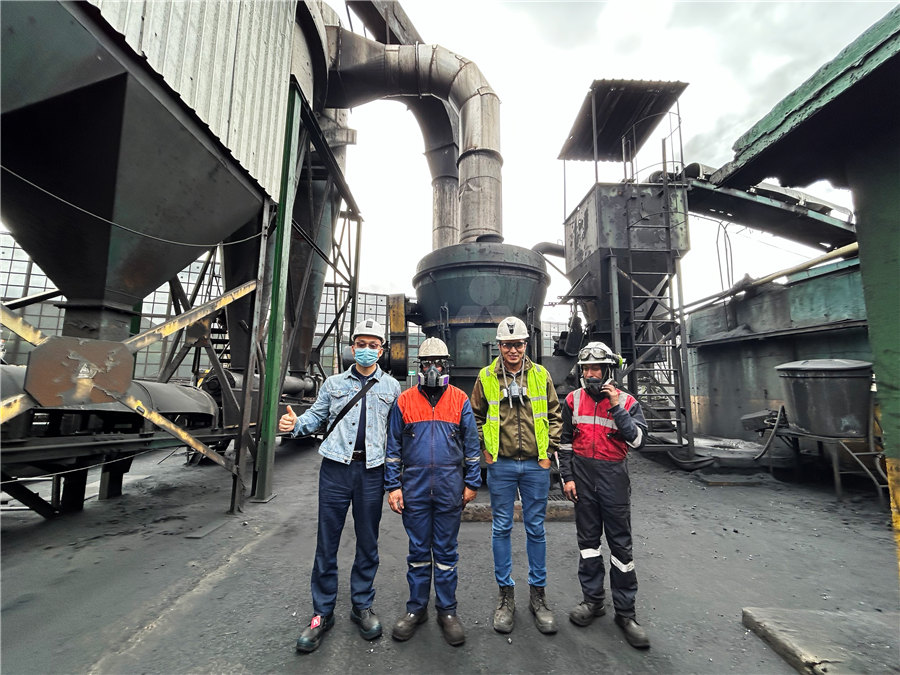
Historical air pollutant emissions and future sustainable
2 天之前 The adoption of advanced new dry process cement production technology (ie, dry with preheater and precalciner) has become increasingly prevalent in recent years due to its 2016年3月1日 Coal provides around 90% of the energy consumed by cement plants around the world, despite the environmental harm caused by its combustion It takes 200 450kg of coal Coal for cement: Present and future trends Global Cement2024年7月11日 To bridge this knowledge gap, we present an annual intensity dataset of energy and CO 2 emissions at plantlevel for Guizhou’s ordinary Portland cement industry, which Plantlevel intensity of energy and CO2 emissions for Portland cement 2020年5月14日 Carboncured concrete This technology injects CO 2 captured during cement production to accelerate the curing process and “lock in” CO 2 in the end product Current lowcarbon cement technologies can sequester up to Laying the foundation for zerocarbon cement
.jpg)
Grinding process optimization IEEE Xplore
2017年6月19日 Today's cement plants can now be designed with the onemill concept for both raw material and cement grinding The advantages of the modular vertical roller mill 2023年1月1日 The utilization of coal in the cement and concrete industries takes three basic forms: (1) as a fuel in the production of cement clinker; (2) ash produced by burning coal in Coal utilization in the cement and concrete industriesMost commonly used mills for coal grinding in cement plants are closed circuit air swept (Single chamber) ball mills and vertical mills Ball Mill: Single chamber ball mills (with classifying liners and dam ring) with drying chamber and static or dynamic separator are commonly existing for coal grinding in cement plant for one or more kilns as Coal Grinding Cement Plant OptimizationBurning: In this operation, the slurry is directly fed into a long inclined steel cylinder called a Rotary kilnIn this kiln there are 3 different zones shown in fig below Cement Manufacturing Process Flow Chart (i) Drying Zones: In the wet Manufacturing of Cement By Dry and Wet
.jpg)
Cement Manufacturing Process The
2018年8月28日 Proportioning of raw material at cement plant laboratory Now cement plant grind the raw mix with the help of heavy wheel type rollers and rotating table Rotating table rotates continuously under the roller and brought 2023年10月13日 The different ingredients that are mixed with the clinker are mostly byproducts from other industries such as from blast furnaces, or fly ash from coal power plants 18 This grinding process is Global database of cement production assets and upstream 2023年11月1日 The design of the cement grinding system is also focused on “energy saving”, because the cement grinding part accounts for about 45% of the electricity consumption in the cement plant There are many cement grinding system processes to choose from, including open flow grinding, ordinary closed circuit grinding, pregrinding, combined 8 Tips For Cement Plant Design Cement Manufacturing Process2016年10月5日 1 Introduction Cement is an energyintensive industry in which the grinding circuits use more than 60 % of the total electrical energy consumed and account for most of the manufacturing cost []The requirements for the cement industry in the future are to reduce the use of energy in grinding and the emission of CO 2 from the kilns In recent years, the production EnergyEfficient Technologies in Cement Grinding
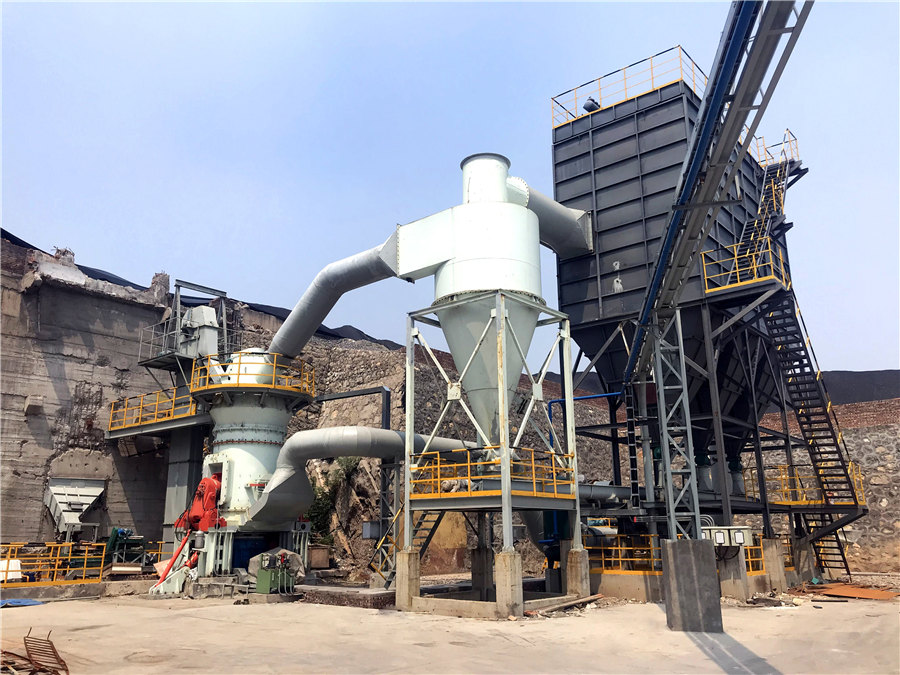
How Cement is Made Cement Manufacturing Process
2024年11月16日 The last stage of making cement is the final grinding process In the cement plant, there are rotating drums fitted with steel balls Clinker, after being cooled, is transferred to these rotating drums and ground into such a fine powder that each pound of it contains 150 billion grains This powder is the final product, cementThe comparison data between the wet process cement production line and the new dry process cement production line shows that with the same rotary kiln size (diameter), the production capacity of the cement kiln which adopts the predecomposition production process increases more than 200%, the output rises from 2777kg /m3 to 20082kg /m3, and Cement Making Process Cement Production Process Cement Plant2023年7月10日 Cement manufacturing is a significant industrial activity that plays a vital role in the construction sector However, the process of cement production is associated with various environmental Cement Manufacturing Process and Its Environmental Impact2020年2月1日 Nowadays, ball mills are used widely in cement plants to grind clinker and gypsum to produce cement In this work, the energy and exergy analyses of a cement ball mill (CBM) were performed and Energy and exergy analyses for a cement ball mill of a new
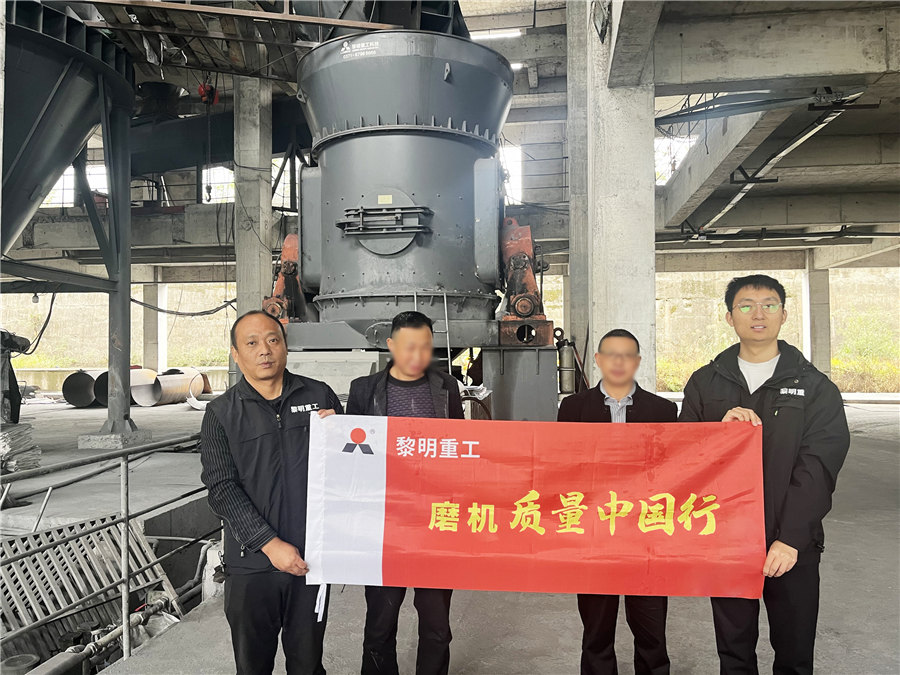
Cement Manufacturing Process: Know
2024年9月10日 Steps of Cement Manufacturing The steps involved in cement manufacturing are as follows: Quarrying: Raw materials such as limestone and clay are extracted from quarries or mines; Crushing and Grinding: The High grinding efficiency For the structure, of the cement mill, we adopt the advanced obstructing equipment for internal powder, add the activated device to the fine grinding chamber, and there is the special grate plate at the end of the Cement Grinding Unit Cement Grinding Plant2019年1月3日 Clinker grinding technology is the most energyintensive process in cement manufacturing Traditionally, it was treated as "low on technology" and "high on energy" as grinding circuits use more than 60 per cent of total energy Clinker grinding technology in cement 5 天之前 The Fig1 show the flow diagram of the dry process of the manufacture of cement 1 Dry Process In the dry and semidry process the raw materials are crushed in a dry state Then, they are processed in grinding mill, dried and reduced to very fine powderlike That dry power is further blended, corrected for the right composition and mixed Manufacturing of Portland Cement – Process and Materials
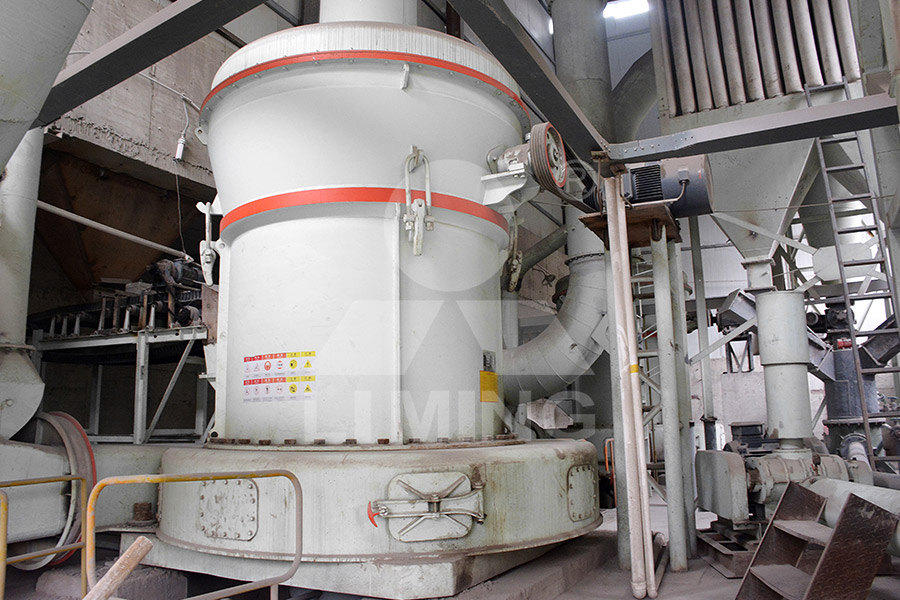
Cement Roller Press Roller Press In Cement Plant Roller
The cement roller press has a high energy utilization rate and remarkable energysaving effect in the material grinding process In a cement plant, a cement roller press is a kind of important cement equipment used for clinker grinding It is usually combined with a cement ball mill to form a highefficiency cement grinding system because the The ball mill is a traditional coal pulverizer machine, which has been widely used since it was invented In the cement plant, the new dry process cement manufacturing requires the moisture content of coal powder to be 05% ~ 15%, while that of raw coal is 15% ~ 40%Coal Mill in Cement Plant Vertical Roller Mill AirSwept Grinding aids also serve to reduce coating problems in cement storage and enhances cement strengths GRINDING MILLS Mills will be selected according to type most suitable for required capacity and duty and for overall power consumption Cement grinding operation may be performed in one of the following mill setups Ball and tube millsCement Grinding Cement Plant Optimization2024年11月23日 Cement Extraction, Processing, Manufacturing: Raw materials employed in the manufacture of cement are extracted by quarrying in the case of hard rocks such as limestones, slates, and some shales, with the aid of blasting when necessary Some deposits are mined by underground methods Softer rocks such as chalk and clay can be dug directly by Cement Extraction, Processing, Manufacturing Britannica

New approach suggests path to emissionsfree cement
2019年9月16日 Caption: In a demonstration of the basic chemical reactions used in the new process, electrolysis takes place in neutral water Dyes show how acid (pink) and base (purple) are produced at the positive and negative electrodes A variation of this process can be used to convert calcium carbonate (CaCO3) into calcium hydroxide (Ca(OH)2), which can then be 2021年2月8日 Process heat overview Clinker, and clinker substitutes, are the active components that confer cement its binding properties Producing traditional cement clinker is an extremely energy and CO 2 intensive process In the EU, 90% of clinker is now made via the more energy efficient dry clinkermaking process (2) Older, less efficient wetDeep decarbonisation of industry: The cement sector6 天之前 Reiner Bachthaler, Axians, explores how safety training apps can lead to safer and more efficient logistics processes at cement plants Tarmac and The Greensand Trust have recently come together to celebrate 30 years of heathland restoration at Rammamere Heath, near Rushmere Country Park, Heath and Today's cement news updates from around the world World Cement2022年12月23日 The text has been organized into five parts describing: (i) the manufacture process of Portland cement, (ii) the chemical composition and hydration reactions involving a Portland cement, (iii) the (PDF) An Insight into the Chemistry of
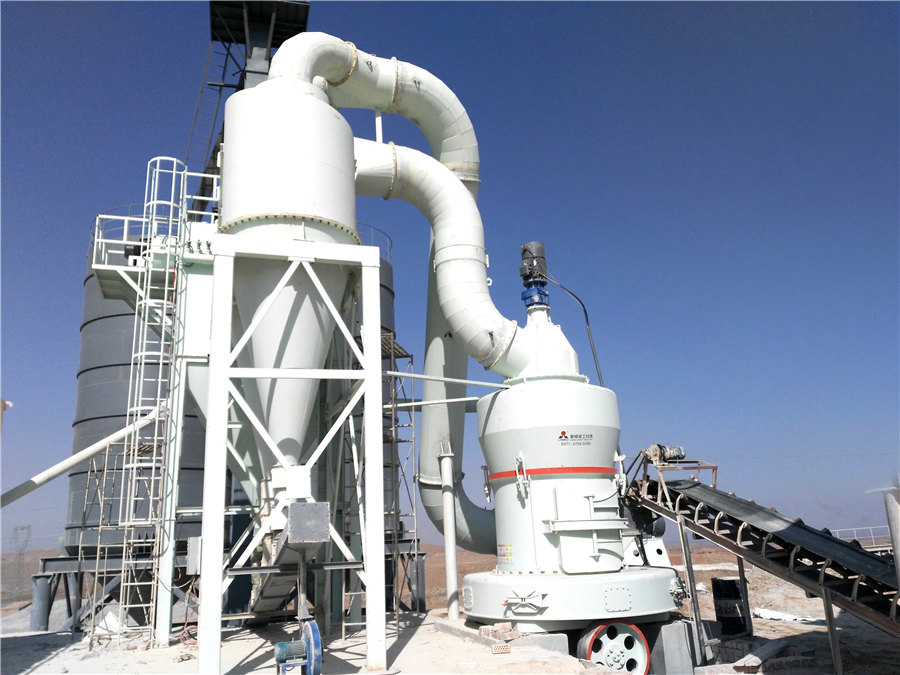
Dry Process of Cement Manufacturing Semidry
2022年4月8日 The main difference between the dry process and wet process of cement manufacture is the way in which the raw materials are prepared before they are fed into the kiln In the dry process, the raw materials are ground and 2 天之前 15 Cement plant construction and valuation 244 1 New plant construction – 2 Project management – 3 Cement plant investment costs – 4 Project phases – 5 Plant valuation Section B – Process calculations and miscellaneous data B1 Power 262 1 Specific power consumption 2 Power conservation – 3 Threephase power – 4The Cement Plant Operations Handbook International 2023年8月29日 Limestone grinding 125 1300 2600 Coal grinding 25 310 730 High pressure grinding rolls High pressure grinding rolls can be used as premill in open circuit or as a finish mill in a close circuit mode The comminution of the material to be ground in the high pressure grinding roll takes place under very high pressure in a bed of materialsOptimizing Electrical Energy Consumption In Cement 2019年8月26日 The new dryprocess cement production line technology was developed in the 1950s So far, in Japan, Germany and other developed countries, the production rate of new dryprocess cement clinker with suspension preheating and predecomposition as the core accounted for 95% A suspension preheating and precalcining kiln was commissioned in 1976New dry process cement production line process LCDRI CN
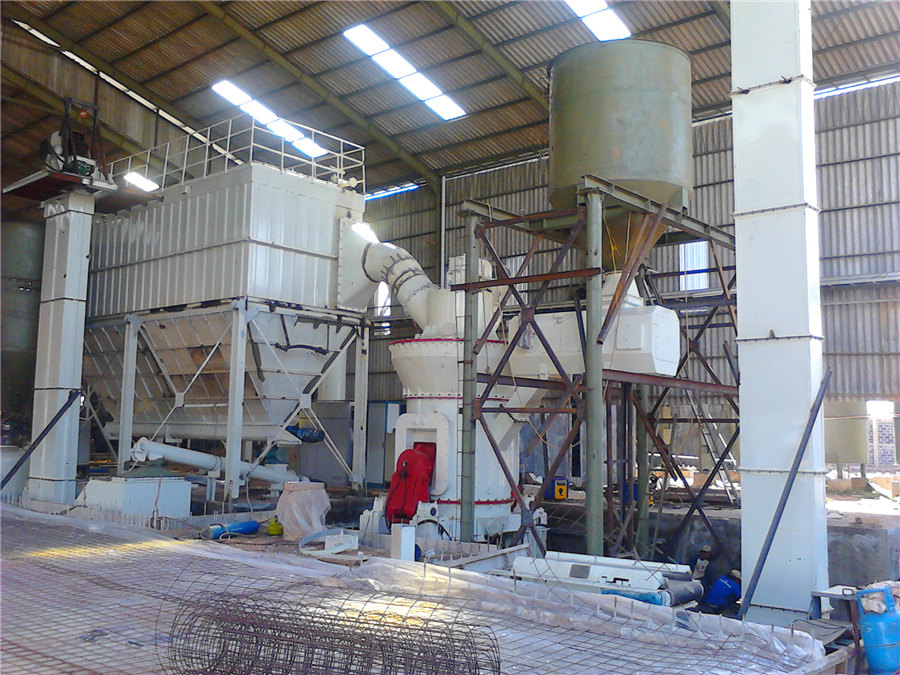
Everything you need to know about clinker/cement Grinding
Everything you need to know about clinker/cement Grinding if You read and understand this article , you will be ready to be a cement grinding area manager FEED AND FEED SYSTEM Feed Temperature Plants with satellite coolers have high clinker temperatures: eg Cumarebo, Oujda Exit satellite cooler 200250°C Exit grate cooler 100150°C2020年7月4日 13 Coal Mill Building The coal mill building houses the mill for grinding lumpy coals This fine ground coal is used for burning in the kiln The mills used for coal grinding and drying are either trumbling mills (tube mills) or roller mills 14 Cement Mill and Bag House Clinker, along with additives, is ground in a cement millBASIC CEMENT PLANT LAYOUT – Process Cement Forum The Cement 2016年10月5日 In this chapter an introduction of widely applied energyefficient grinding technologies in cement grinding and description of the operating principles of the related equip‐ ments and comparisons over each other in terms of grinding efficiency, specific energy consumption, production capacity and cement quality are given A case study per‐ formed on a EnergyEfficient Technologies in Cement Grinding2022年11月17日 Owing to rapid advances in cement manufacturing technology (CMT), China has utilized three major cement kilns in recent decades 6, including shaft kilns, other rotary kilns (eg, wetprocess Modernizing cement manufacturing in China leads to
.jpg)
Coal Grinding Cement Plant Optimization
Most commonly used mills for coal grinding in cement plants are closed circuit air swept (Single chamber) ball mills and vertical mills Ball Mill: Single chamber ball mills (with classifying liners and dam ring) with drying chamber and static or dynamic separator are commonly existing for coal grinding in cement plant for one or more kilns as Burning: In this operation, the slurry is directly fed into a long inclined steel cylinder called a Rotary kilnIn this kiln there are 3 different zones shown in fig below Cement Manufacturing Process Flow Chart (i) Drying Zones: In the wet Manufacturing of Cement By Dry and Wet 2018年8月28日 Proportioning of raw material at cement plant laboratory Now cement plant grind the raw mix with the help of heavy wheel type rollers and rotating table Rotating table rotates continuously under the roller and brought Cement Manufacturing Process The 2023年10月13日 The different ingredients that are mixed with the clinker are mostly byproducts from other industries such as from blast furnaces, or fly ash from coal power plants 18 This grinding process is Global database of cement production assets and upstream
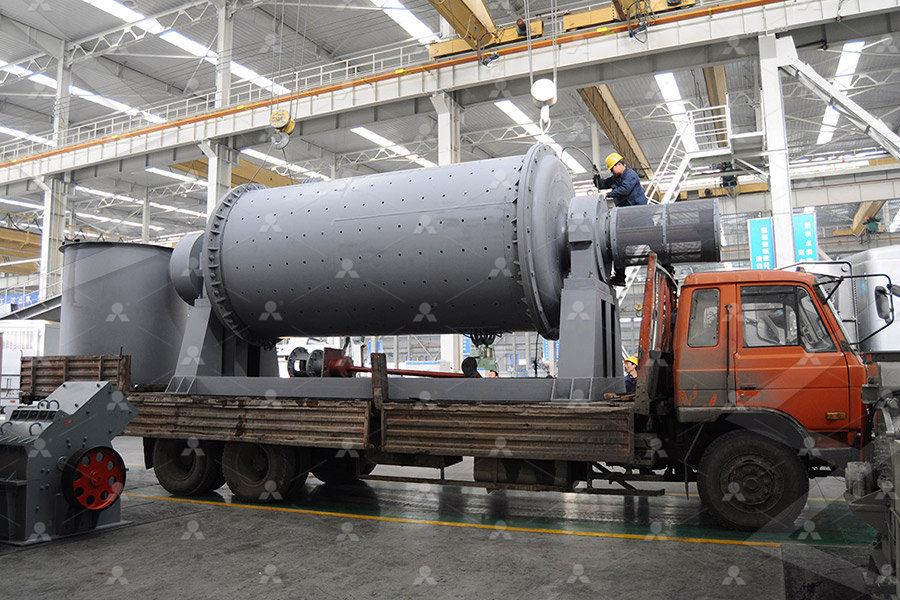
8 Tips For Cement Plant Design Cement Manufacturing Process
2023年11月1日 The design of the cement grinding system is also focused on “energy saving”, because the cement grinding part accounts for about 45% of the electricity consumption in the cement plant There are many cement grinding system processes to choose from, including open flow grinding, ordinary closed circuit grinding, pregrinding, combined 2016年10月5日 1 Introduction Cement is an energyintensive industry in which the grinding circuits use more than 60 % of the total electrical energy consumed and account for most of the manufacturing cost []The requirements for the cement industry in the future are to reduce the use of energy in grinding and the emission of CO 2 from the kilns In recent years, the production EnergyEfficient Technologies in Cement Grinding2024年11月16日 The last stage of making cement is the final grinding process In the cement plant, there are rotating drums fitted with steel balls Clinker, after being cooled, is transferred to these rotating drums and ground into such a fine powder that each pound of it contains 150 billion grains This powder is the final product, cementHow Cement is Made Cement Manufacturing ProcessThe comparison data between the wet process cement production line and the new dry process cement production line shows that with the same rotary kiln size (diameter), the production capacity of the cement kiln which adopts the predecomposition production process increases more than 200%, the output rises from 2777kg /m3 to 20082kg /m3, and Cement Making Process Cement Production Process Cement Plant
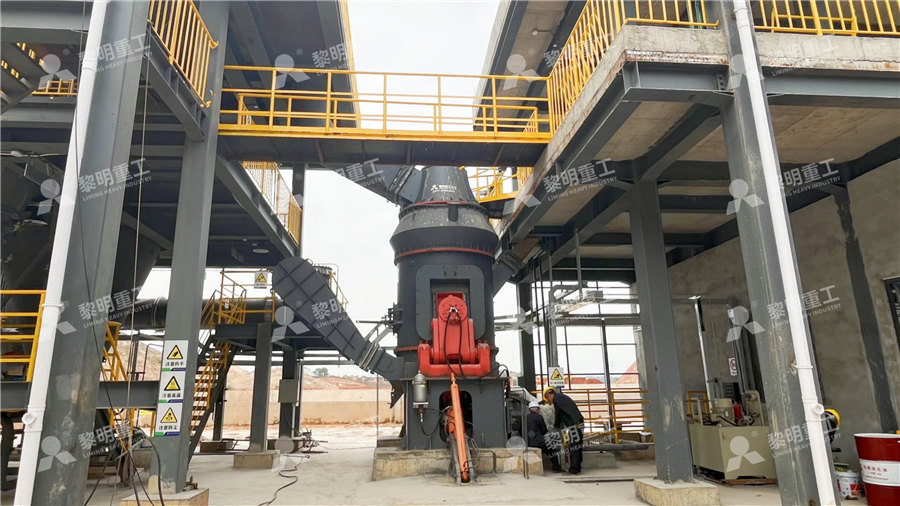
Cement Manufacturing Process and Its Environmental Impact
2023年7月10日 Cement manufacturing is a significant industrial activity that plays a vital role in the construction sector However, the process of cement production is associated with various environmental 2020年2月1日 Nowadays, ball mills are used widely in cement plants to grind clinker and gypsum to produce cement In this work, the energy and exergy analyses of a cement ball mill (CBM) were performed and Energy and exergy analyses for a cement ball mill of a new