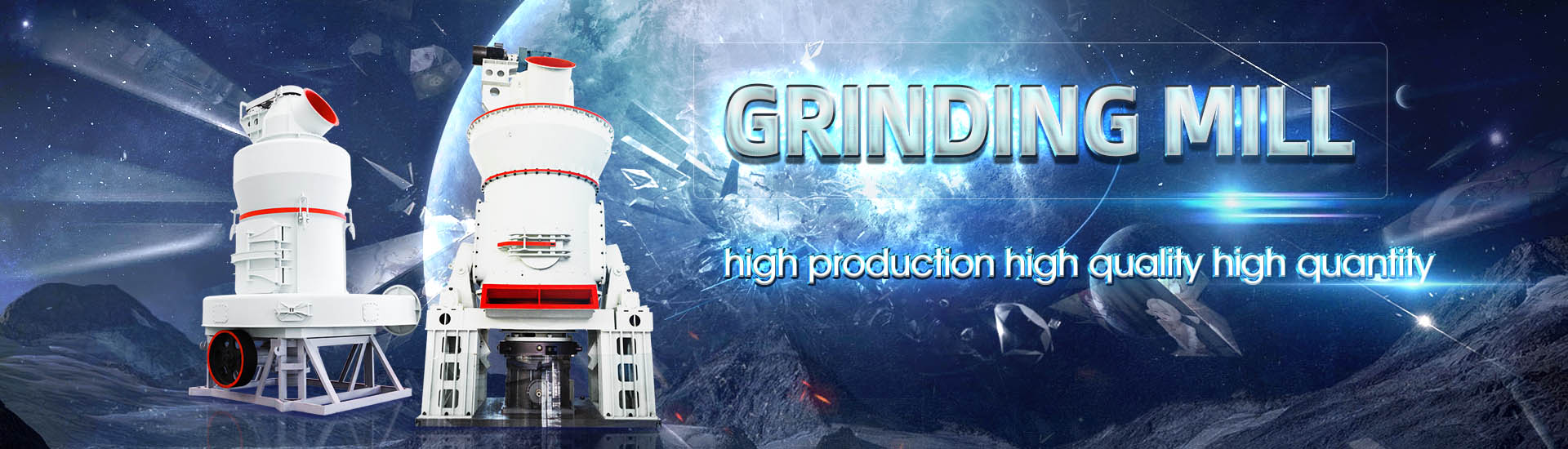
Sintered ore processing equipment process flow
.jpg)
Application of deep learning in iron ore sintering process: a
2024年3月16日 The flow of the iron ore powder sintering process is summarised below According to specifications, a range of raw materials comprising pulverised iron are combined with a certain amount of fuel and melting agent, then thoroughly combined, granulated, and 2017年2月16日 The present paper reviews the sintering process that the mixture follows, once granulated, when is loaded onto the sinter strand There, (PDF) Iron Ore Sintering: Process ResearchGate2017年3月24日 Sintering is a thermal agglomeration process that is applied to a mixture of iron ore fines, recycled ironmaking products, fluxes, slagforming agents, and solid fuel (coke) The Iron Ore Sintering: Process: Mineral Processing and Extractive 2018年9月25日 In this chapter, a methodology for simulating the sintering process of iron ore is presented In order to study the process parameters and inner phenomena, a mathematical Modeling Sintering Process of Iron Ore IntechOpen
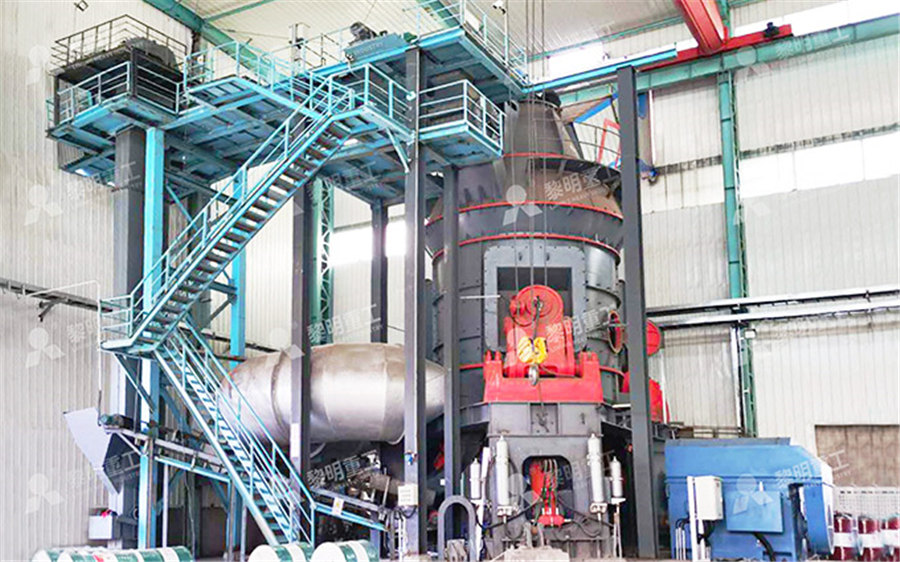
Model of an iron ore sinter plant with selective waste gas
2022年3月1日 Sintering of iron ores is an enormous energyintensive and resources consuming process Introducing a selective waste gas recirculation (SWGR) to the sintering process 2020年8月19日 The sintering process can be defined as a thermal agglomeration process that is applied to a mixture of iron ore fines, recycled ironmaking products, fluxes, slagforming Sintering SpringerLink2022年1月1日 Sintering is the most economic and widely used agglomeration process to prepare iron ore fines for blast furnace use In this chapter, the sintering process is first Iron ore sintering ScienceDirect2023年6月8日 Iron ore sintering is the iron ore powder agglomeration process that changes fine iron ore powder into the lumpy ironbearing raw material used for blast furnace ironmaking Iron Ore Sintering SpringerLink
.jpg)
Iron ore sintering Part 1 Theory and practice of
2013年8月1日 Sintering is a process by which a mixture of iron ores, fl uxes and coke is agglomerated in a sinter plant to manufacture a sinter product of a suitable composition, quality and2015年1月1日 Sintering is the most economic and widely used agglomeration process to prepare iron ore fines for blast furnace use In this chapter, the sintering process is first Iron ore sintering ScienceDirect2023年12月23日 Sintering is a thermal agglomeration process that is applied to a mixture of iron ore fines, recycled ironmaking products, fluxes, slagforming agents, and solid fuel (coke) The purpose of the Iron Ore Sintering: Process ResearchGate2024年3月20日 Explore the intricate steps involved in the sintering process of iron ore Discover how raw materials are transformed into a highquality final product, enhancing industrial efficiency A vacuum is created under the Iron Ore Sintering Process: Transforming Raw
.jpg)
Sintering Process an overview ScienceDirect Topics
14th International Symposium on Process Systems Engineering Haoran Li, Tong Qiu, in Computer Aided Chemical Engineering, 2022 21 Process description The sintering process is an important thermochemical process in the blast furnace ironmaking system It involves the heating of fine iron ore with flux and coke fines or coal to produce a semimolten mass that 2013年8月1日 Sintering is a process by which a mixture of iron ores, fl uxes and coke is agglomerated in a sinter plant to manufacture a sinter product of a suitable composition, quality and granulometry to be Iron ore sintering Part 1 Theory and practice of the sintering process2015年1月1日 Like other sintering processes, iron ore sintering converts iron ore fines of often − 8 mm sizing into larger agglomerates, namely, sinter, between 5 and 50 mm particle size, which possess the physical and metallurgical characteristics and gas permeability required for efficient blast furnace operationAs shown in Figure 141, iron ore sintering is carried out in three Iron ore sintering ScienceDirect2022年2月28日 The present work proposes a novel process to sinter porous iron ore (porosity ~23–24%) with enhanced productivity and quality The iron ore is preprocessed in the presence of calcined lime for the temporary closure of pores, which further prevents water absorption during the granulation process in drum in the presence of water The calcined lime coated iron ore A Novel Sintering Process for Porous Iron Ore Sintering with
.jpg)
Identification of working conditions and prediction of FeO
2024年6月4日 The iron oxide (FeO) content had a significant impact on both the metallurgical properties of sintered ores and the economic indicators of the sintering process Precisely predicting FeO content possessed substantial potential for enhancing the quality of sintered ore and optimizing the sintering process A multimodel integrated prediction framework for FeO 2019年7月19日 So, the sintering process main objectives are to increase the size of ore additives to a level acceptable to the blast furnace for improving permeability of burden inside the BF; to form a strong agglomerate with high bulk reducibility; to remove volatile matter like CO 2 from carbonates, H 2 O from hydroxides, and sulfur from sulfide type of ore fines along with Sintering: Most Efficient Technologies for Greenhouse 2024年3月6日 Proportioning is an important part of sintering, as it affects the cost of sintering and the quality of sintered ore To address the problems posed by the complex raw material information and numerous constraints in the sintering process, a multiobjective optimisation model for sintering proportioning was established, which takes the proportioning cost and TFe Optimal proportioning of iron ore in sintering process based 2022年12月31日 This sintered ore will be relatively more porous under the same conditions during actual sintering Ore D was nearly completely melted by 1325 °C and the temperature range of the melting process was very narrow, which was unfavorable in the actual sintering process Iron Ore E (Fig 5 (e)) had no noticeable morphological changes before 1300 Experimental study on melt and flow characteristics and pore
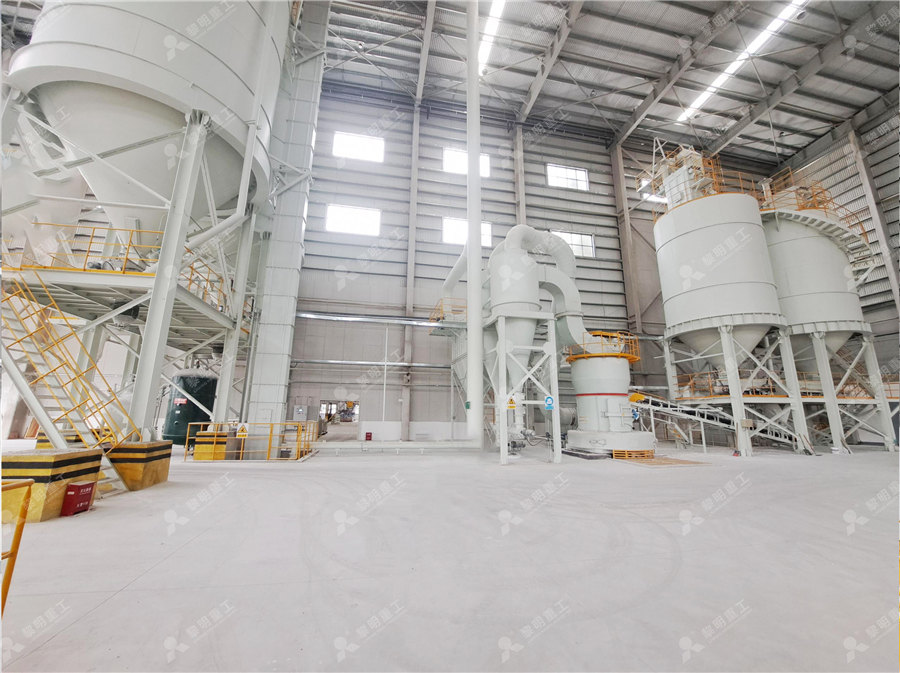
Copper Ore Processing Plants, Flow And
5 天之前 Copper industrial minerals include: natural copper, chalcopyrite, chalcocite, tetrahedrite, azurite, malachite, etc Chalcopyrite (a compound of copper, sulfur, and iron) is mined mainly, followed by chalcocite and bornite If 2022年1月1日 The volume percent of remnant ore in the sintered tablet, that is, the volume of nucleus particles that have not reacted over the sintering period, provides a measure of the “assimilability” of the ore nucleus particles Intensified granulation process flow with a vertical wet ball mill equipment installed in the NSC Wakayama No 5 Iron ore sintering ScienceDirect2024年1月1日 Iron ore sintering is the iron ore powder agglomeration process that changes fine iron ore powder into the lumpy ironbearing raw material used for blast furnace ironmaking Hightemperature process and addition of alkaline flux will improve metallurgical performance of ironbearing raw materialIron Ore Sintering SpringerLink2022年3月1日 The sintering process can be described by four zones: 1) A sintered zone (top) for describing the heat exchange between gas phase and solid phase of the sintered material, 2) a reaction zone involving chemical reactions, solidification, and porosity changes, 3) a decomposition zone including thermal decomposition of carbonates, and 4) a raw mix Model of an iron ore sinter plant with selective waste gas
.jpg)
Magnesite Ore Processing: Separation and Calcination
2023年5月12日 However, for lowgrade magnesite ore, it is necessary to use reasonable beneficiation methods and technological processes to obtain highpurity magnesite according to the characteristics of the ore As a professional ore equipment manufacturer, Ftmmachinery can design magnesite production lines and provide solid equipment for magnesite 2017年3月24日 Sintering is a thermal agglomeration process that is applied to a mixture of iron ore fines, recycled ironmaking products, fluxes, slagforming agents, and solid fuel (coke) The purpose of the sintering process is manufacturing a product with the suitable characteristics (thermal, mechanical, physical and chemical) to be fed to the blast furnaceIron Ore Sintering: Process: Mineral Processing and Extractive 2016年10月28日 Sintering is an agglomeration process that fuses iron ore fines, fluxes, recycled products, slagforming elements and coke The purpose of sintering is to obtain a product with suitable (PDF) Iron Ore Sintering: Raw Materials and Granulation2020年10月1日 Iron ore sinter plants are energyintensive components of integrated iron and steel production (see Table 1), where the iron ore fines (5 mm) lump sinter cakes with greater gas permeability, which are the most important burden materials for iron making in blast furnaces (BFs) [7]The main process is shown in Fig 2 and described in Recent progress in sustainable and energyefficient technologies
.jpg)
Recent Trends in the Technologies of the Direct Reduction
2023年4月5日 The blast furnace and direct reduction processes have been the major iron production routes for various iron ores (ie goethite, hematite, magnetite, maghemite, siderite, etc) in the past few decades, but the challenges of maintaining the iron and steelmaking processes are enormous The challenges, such as cumbersome production routes, scarcity of 4 天之前 The process of mining for silver is broken down into three steps: removing ore from the earth, breaking it down and then flushing the silver from ore The first step involves drilling holes in the silverrich areas geologists have previously pinpointed and then inserting dynamite sticksSilver Mining Processing Equipment Flow Chart Cases2016年4月27日 The problem involved in Manganese Ore Processing deals with the production of acceptable specification grades of manganese concentrates at a maximum recovery of the total manganese from ores having variable Manganese Ore Processing 911Metallurgist2020年8月19日 The sintering process can be defined as a thermal agglomeration process that is applied to a mixture of iron ore fines, recycled ironmaking products, fluxes, slagforming agents, and solid fuel (coke) with the objective of obtaining a product with the suitable characteristics (thermal, mechanical, physical, and chemical) to be fed to the blast furnaceSintering SpringerLink
.jpg)
Sintering: A Step Between Mining Iron Ore and
2019年6月11日 World resources are estimated to be greater than 800 billion tons of crude ore containing more than 230 billion tons of iron The only source of primary iron is iron ore, but before all that iron ore can be turned into steel, it PDF On Jul 11, 2018, Sandra Lúcia de Moraes and others published Iron Ore Pelletizing Process: An Overview Find, read and cite all the research you need on ResearchGate(PDF) Iron Ore Pelletizing Process: An Overview ResearchGate2020年8月21日 Manganese is considered a relatively rare metal as concentrations of it in ore of commercial importance are geographically limited In nature, manganese is found in the form of oxides, carbonates, and silicates Manganese ores are complex in the sense that they not only consist of a complex oxide mineral assemblage but these minerals are also very finely inter From Ore Body to High Temperature Processing of Complex 2023年12月1日 As a preprocessing of blast furnace ironmaking, the iron ore sintering process accounts for 6–8% of the total energy consumption in the steel industry The application of gas fuel in the sintering process of iron ore was first proposed by JFE Steel Company in Japan The sintered ore yield and shatter strength first increase and then Application of a clean fuel produced by electrolysis in iron ore
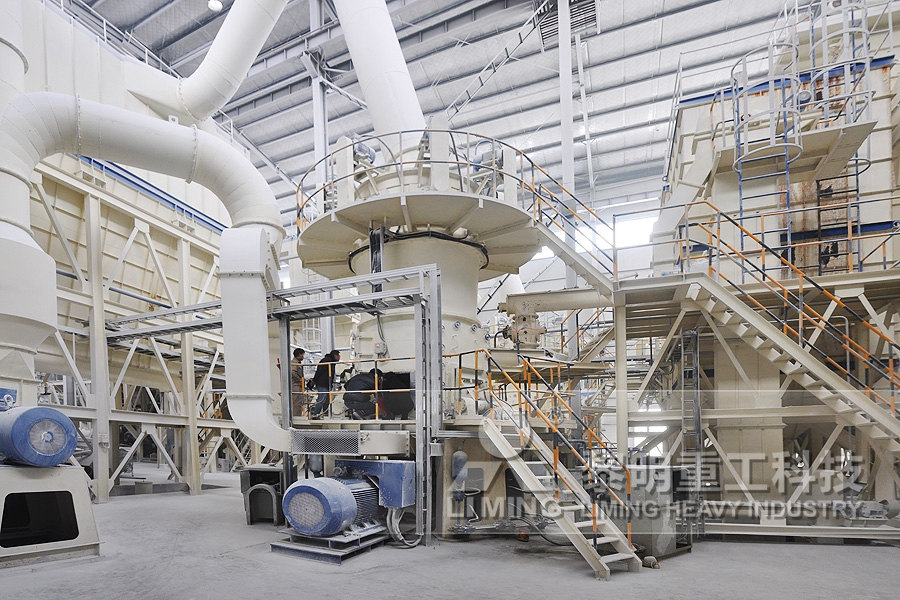
A Novel Sintering Process for Porous Iron Ore Sintering
2022年8月12日 have shown a signicant improvement when the pot sintering experiments are performed through the proposed process Keywords iron ore Preprocessing Granulation Fluxes, sinter properties Sintering process 1 Introduction The sinter mix contains various materials such as iron ore, ux, solid fuel, plant return sinter nes, plant generated2024年6月10日 This paper presents the results of laboratory experiments to study the effect of the consumption of gaseous fuel (natural gas) supplied into a sintered charge layer on sintering process indicators and sinter quality under the charge conditions of the Ural Steel Company at charge layer heights of 350 to 500 mmIt was established that an increase in the consumption Sintering process with gaseous fuel injection into the sintered 2024年2月15日 Steel making using the integrated blast furnace (BF) process route is still the dominant steel production method covering 70% of worldwide steel production and iron ore sintering is one of the most important iron sources within this process, which represent 70–80% of charged ironbearing materials into modern BF []Inside this route, sinter plants offer unique New Measurement Techniques Describing the Sinter Process2023年5月21日 In complex industrial processes such as sintering, key quality variables are difficult to measure online and it takes a long time to obtain quality variables through offline testing Moreover, due to the limitations of testing frequency, quality variable data are too scarce To solve this problem, this paper proposes a sintering quality prediction model based on multi A Soft Sensor Model of Sintering Process Quality Index
.jpg)
Iron Ore Sintering: Process ResearchGate
2023年12月23日 Sintering is a thermal agglomeration process that is applied to a mixture of iron ore fines, recycled ironmaking products, fluxes, slagforming agents, and solid fuel (coke) The purpose of the 2024年3月20日 Explore the intricate steps involved in the sintering process of iron ore Discover how raw materials are transformed into a highquality final product, enhancing industrial efficiency A vacuum is created under the Iron Ore Sintering Process: Transforming Raw 14th International Symposium on Process Systems Engineering Haoran Li, Tong Qiu, in Computer Aided Chemical Engineering, 2022 21 Process description The sintering process is an important thermochemical process in the blast furnace ironmaking system It involves the heating of fine iron ore with flux and coke fines or coal to produce a semimolten mass that Sintering Process an overview ScienceDirect Topics2013年8月1日 Sintering is a process by which a mixture of iron ores, fl uxes and coke is agglomerated in a sinter plant to manufacture a sinter product of a suitable composition, quality and granulometry to be Iron ore sintering Part 1 Theory and practice of the sintering process
.jpg)
Iron ore sintering ScienceDirect
2015年1月1日 Like other sintering processes, iron ore sintering converts iron ore fines of often − 8 mm sizing into larger agglomerates, namely, sinter, between 5 and 50 mm particle size, which possess the physical and metallurgical characteristics and gas permeability required for efficient blast furnace operationAs shown in Figure 141, iron ore sintering is carried out in three 2022年2月28日 The present work proposes a novel process to sinter porous iron ore (porosity ~23–24%) with enhanced productivity and quality The iron ore is preprocessed in the presence of calcined lime for the temporary closure of pores, which further prevents water absorption during the granulation process in drum in the presence of water The calcined lime coated iron ore A Novel Sintering Process for Porous Iron Ore Sintering with 2024年6月4日 The iron oxide (FeO) content had a significant impact on both the metallurgical properties of sintered ores and the economic indicators of the sintering process Precisely predicting FeO content possessed substantial potential for enhancing the quality of sintered ore and optimizing the sintering process A multimodel integrated prediction framework for FeO Identification of working conditions and prediction of FeO 2019年7月19日 So, the sintering process main objectives are to increase the size of ore additives to a level acceptable to the blast furnace for improving permeability of burden inside the BF; to form a strong agglomerate with high bulk reducibility; to remove volatile matter like CO 2 from carbonates, H 2 O from hydroxides, and sulfur from sulfide type of ore fines along with Sintering: Most Efficient Technologies for Greenhouse
.jpg)
Optimal proportioning of iron ore in sintering process based
2024年3月6日 Proportioning is an important part of sintering, as it affects the cost of sintering and the quality of sintered ore To address the problems posed by the complex raw material information and numerous constraints in the sintering process, a multiobjective optimisation model for sintering proportioning was established, which takes the proportioning cost and TFe 2022年12月31日 This sintered ore will be relatively more porous under the same conditions during actual sintering Ore D was nearly completely melted by 1325 °C and the temperature range of the melting process was very narrow, which was unfavorable in the actual sintering process Iron Ore E (Fig 5 (e)) had no noticeable morphological changes before 1300 Experimental study on melt and flow characteristics and pore