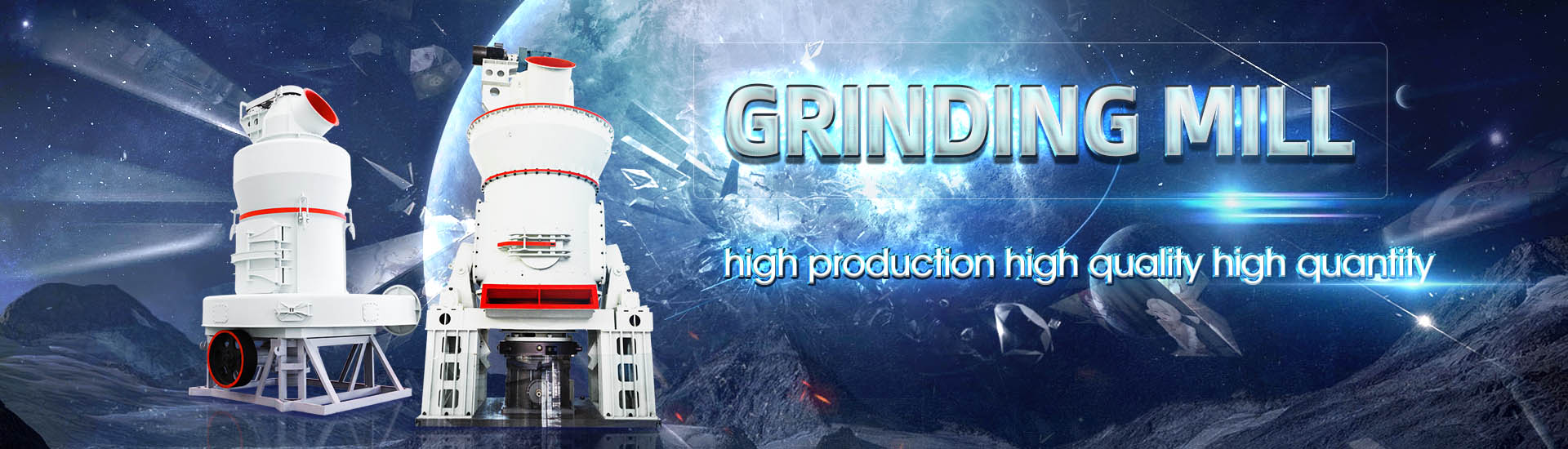
Ball mill production of limestone output
.jpg)
A Technical and Economic Comparison of Ball Mill Limestone
2021年10月13日 In South Africa, Eskom’s Kusile Power Station utilizes conventional wet ball milling to grind highgrade limestone (96% CaCO 3) to 95% passing 45 µm prior to use in the FGD scrubber For future FGD installations under consideration, the high energy cost 2023年7月14日 The Gravimetric feeder feeds limestone to Wet ball mill system The Wet Ball Mill system consists of Wet Ball Mill, Wet Ball Mill Lubrication system, Mill circuit tank with an TECHNICAL SPECIFICATION OF WET BALL MILL Grinding in ball mills is an important technological process applied to reduce the size of particles which may have different nature and a wide diversity of physical, mechanical and chemical Grinding in Ball Mills: Modeling and Process Control2018年8月15日 CaO porosity and solidstate diffusion of CO 2 during carbonation are enhanced by EMAX ball mill This work analyzes the relevant influence of milling on the CO 2 capture Effect of milling mechanism on the CO2 capture performance of limestone
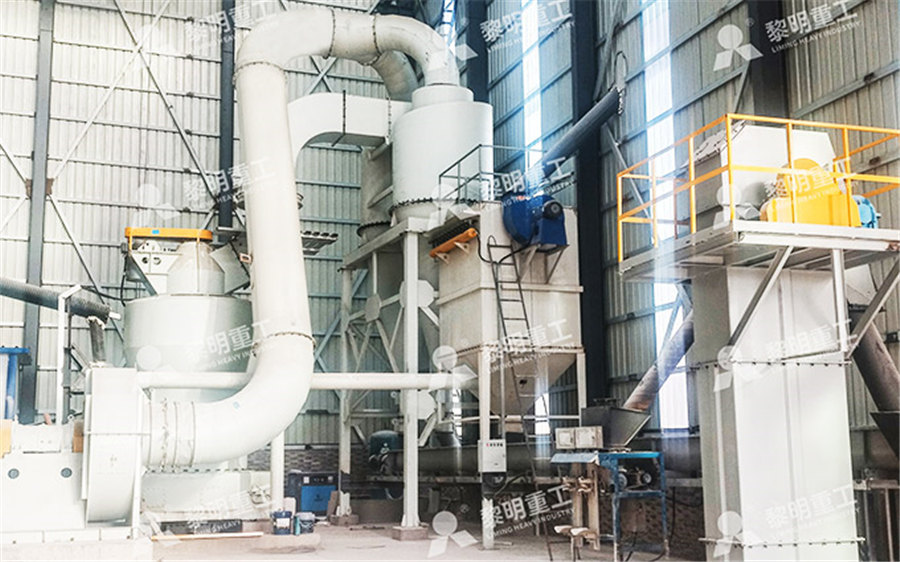
Energy and exergy analyses for a cement ball mill of a new
2020年5月1日 Nowadays, ball mills are used widely in cement plants to grind clinker and gypsum to produce cement In this work, the energy and exergy analyses of a cement ball mill 2021年10月13日 In South Africa, Eskom’s Kusile Power Station utilizes conventional wet ball milling to grind highgrade limestone (96% CaCO3) to 95% passing 45 µm prior to use in the A Technical and Economic Comparison of Ball Mill Limestone 2023年4月13日 The effect of ball size and interstitial filling on the performance of dry ball mill grinding was investigated for a limestonetype brecciated uranium ore The optimum grinding Optimization of Ball Mill Grinding of a LimestoneType 2014年1月10日 The dry grinding of limestone in a planetary ball mill was investigated as a function of the diameter of the grinding balls and the revolution speed of the mill The tests Particle size distribution and structural changes in limestone ground
.jpg)
A Technical and Economic Comparison of Ball Mill
2021年10月13日 In South Africa, Eskom’s Kusile Power Station utilizes conventional wet ball milling to grind highgrade limestone (96% CaCO 3) to 95% passing 45 µm prior to use in the 2017年1月1日 An increase of over 10% in mill throughput was achieved by removing the ball scats from a single stage SAG mill These scats are non spherical ball fragments resulting from uneven wear of balls (PDF) Performance optimization of an industrial Grinding in ball mills is an important technological process applied to reduce the size of particles which may have different nature and a wide diversity of physical, mechanical and chemical characteristics Typical examples are the various ores, minerals, limestone, etc The applications of ball mills are ubiquitous in mineralGrinding in Ball Mills: Modeling and Process Control2017年8月4日 Since for the ball mill design we are using 80% passing, the required value of C2 for the ball mill will be equal to120 C3 is the correction factor for mill diameter and is given as; 𝐶𝐶3 = 244 𝐷𝐷 02 (3) However, it is important to note that C3 =0914 vessel used in producing the ball mill was got from aDesign, Construction and Performance Analysis of a 5
.jpg)
What is Limestone Grinding Mill SBM Mill Crusher
2023年5月15日 This mill, also known as the Raymond Roller Mill, is a common choice for limestone grinding It works by rotating a grinding ring or roller around a fixed shaft, allowing the material to be ground by the rolling and crushing action between the grinding parts Ball Mill A ball mill is a cylindrical device used to finely grind materials2023年2月15日 High temperature of the ball mill will affact the efficiency 3 For every 1% increase in moisture, the output of the ball mill will be reduced by 8% 10% 4 when the moisture is greater than 5%, the ball mill will be unable to perform the grinding operation 5 The bearing of the ball mill is overheated and the motor is overloaded Reasons17 Signs of Problems with Ball Mills: Quickly Remove Hidden Troubles2016年4月11日 Modeling And Simulation Of A Closed Loop Ball Mill Grinding Circuit Proceedings of IRF International Conference, Chennai, India, 20th April 2014, ISBN: 978938 10 II DYNAMICS OF THE BALL MILL GRINDING CIRCUIT product Blaine measured in cm²/g and the rejects Fig1 In a continuous ball mill grinding circuit, the ball millMODELING AND SIMULATION OF A CLOSED LOOP BALL 2012年6月1日 As the cylinder starts to rotate, the grinding balls inside the cylinder crush and grind the feed material, generating mechanical energy that aids in breaking bonds, activating the catalyst, and (PDF) Grinding in Ball Mills: Modeling and Process Control
.jpg)
Picture: Loesche GmbH, Germany CEMENT SikaGrind®
2024年7月1日 than ball mills, even if the ball mill is combined with a roller press This and further arguments led to the increased share of VRM for the grinding of finished cement Taking into account that VRM usually have a bigger output than ball mills, it can be declared that the major part of the cement production with newly installed mills comes from They provide a range of machinery for lime production plants, including crushers, ball mills, lime kilns, coolers, and other related equipment, which covering everything from raw material preparation to calcination, cooling, and packaging It is known for the expertise in the cement and lime industry and aim to help clients achieve efficient Lime Production Line for HighOutput Lime Production PlantBrief introduction The ball mill is the key equipment for crushing the material after it is crushed Ball mills are widely used in cement, silicate products, new building materials, refractory materials, fertilizers, ferrous and nonferrous metal beneficiation and glass ceramics and other production industries, dry or wet grinding of various ores and other grindable materialsBall Mill SBM Ultrafine Powder Technology2024年11月23日 Ceramic ball mill: Uses ceramic balls as the grinding media 4 By lengthtodiameter ratio of the drum Ball mill: A typical ball mill has a drum length that is equal to or 15 times the drum diameter Tube mill: A mill with a Highquality Ball Mill with Low price for Kinds of
.jpg)
Grinding in Ball Mills: Modeling and Process Control
Grinding in ball mills is an important technological process applied to reduce the size of particles which may have different nature and a wide diversity of physical, mechanical and chemical characteristics Typical examples are the various ores, minerals, limestone, etc The applications of ball mills are ubiquitous in mineralBall mills grind materials like cement, limestone, gypsum, and slag, ensuring reliable output and consistent quality Achieving high output efficiency is essential for maintaining uninterrupted production, while energysaving designs help Ball Mills Manufacturer JXSC2022年5月22日 The production of fine and ultrafine limestone particles in grinding mills has an impor a standard unit was used as output By applying the life cycle impact assessment method EnergyModel and Life CycleModel for Grinding Processes of Limestone 2022年7月26日 From Production side: to maintain production with a mill output around ~150 mTph; DESCRIPTION During this field trial, we have compared CHRYSO ® ICARE technology to a conventional product in terms of mill output and we have adjusted limestone addition and fineness/blaine targetsCASE STUDY: OPTIMIZATION OF CLINKER CONTENT IN LIMESTONE

Factors That Can Impact the Limestone Grinding Process
Q: What is the output size of ground limestone powder? A: The output size of ground limestone powder depends on the type of machine used for grinding Typically, the particle size ranges from a few microns to several hundred microns The output size can be adjusted by changing the machine’s grinding settings Q: What is the production 5 天之前 than ball mills, even if the ball mill is combined with a roller press This and further arguments led to the increased share of VRM for the grinding of finished cement Taking into account that VRM usually have a bigger output than ball mills, it can be declared that the major part of the cement production with newly installed mills comes from SikaGrind® for vertical roller mills2024年1月16日 Limestone is a relatively common stone material, which is used in various industries However, today we are discussing how to choose a ball mill equipment for a 500mesh limestone grinding production line with a daily output of 450 tonsSelection of 500 tons of limestone ball mill with daily output 2022年5月22日 The introduction of stirred ball mills becomes a good alternative that allows the production of required ultrafine limestone particles while reducing specific grinding work It can be marked that a stirred ball mill can be an effective equipment in limestone processing facilities when all stages of development are completedEnergyModel and Life CycleModel for Grinding Processes of Limestone
.jpg)
How to optimize your limestone milling operation for better output
2024年10月13日 Limestone milling operations play a crucial role in the production of limestone powder, which is widely used in various industries To achieve optimal output, it is essential to optimize the limestone milling process Selecting the right milling technology is crucial for achieving optimal output Traditional ball mills are less energy Wide product range: For meeting various requirements from different clients, our cement mill range from cement ball mill, vertical cement mill, Raymond mill, coal mill in cement plant, etc Strong production ability: AGICO CEMENT has a Cement Mill Cement Ball Mill Vertical Cement 2017年2月13日 The apparent difference in capacities between grinding mills (listed as being the same size) is due to the fact that there is no uniform method of designating the size of a mill, for example: a 5′ x 5′ Ball Mill has a working Ball Mills 911Metallurgist5 天之前 The limestone grinding production line is a production process for the fine processing of limestone raw materials The limestone grinding production line grinds limestone into powders of different fineness through crushing, grinding, classification, and other processes to meet the needs of different fields This production line covers the complete process from raw material Limestone Grinding Mill Plant TAYMACHINERY
.jpg)
(PDF) Optimization of inmill ball loading and slurry solids
2012年12月1日 The inmill load volume and slurry solids concentration have significant influence on the ball mill product size and energy expenditure Hence, better energy efficiency and quality grind can only 2021年6月29日 Nowadays, ball mills are widely used in cement plants to grind clinker and gypsum to produce cement The research focuses on the mill speed as well as air classifier speed effect on the two Effects of Mill Speed and Air Classifier Speed on 2017年7月26日 The finer you crush, the higher your ball mill tonnage and capacity will be The important of crushing your ore and rock fine and properly is often forgotten The finer you crush, the higher your ball mill tonnage and capacity will be If the feed size was 13,000 micrometers for the same grind production size, theoretical output from Fig How Ball Mill Ore Feed Size Affects Tonnage Capacity2023年9月22日 chemical industries are subjected to grinding in ball mills [1–3] The specic energy consumption for these materials typically ranges from 5 to 50 kWh/ton Thus, the ball mills consume an enormous amount of energy The energy eciency of the ball mill being as low as 1% or less [2], there is considerable incentive to improve the energy eciencySelected Advances in Modelling of Size Reduction in Ball
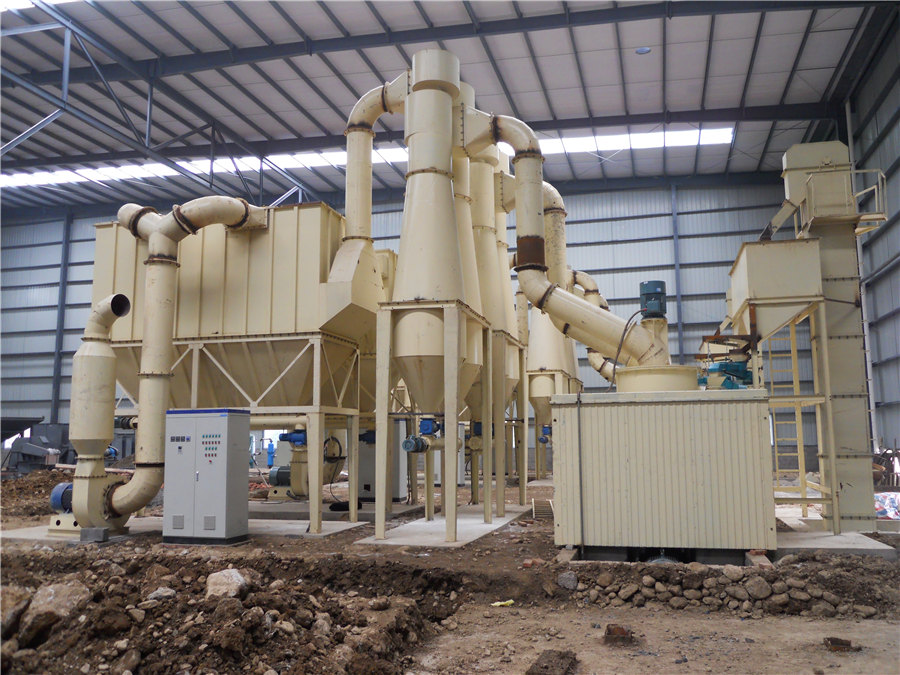
Performance Evaluation of Vertical Roller Mill in Cement
2024年1月3日 Performance Evaluation of Vertical Roller Mill in Cement Grinding: Case Study ESCH Cement Plant D Altun, NA Aydogan, O Altun, AH Benzer2022年12月22日 Limestone Ball mill can devide into 2 types, wet ball mill and dry ball mill Ball mill is a mineral processing machine for milling the materials into powders after they are crushed It is widely applied to the production of cements, silicate products, building materials, fireproof materials, fertilizers, glass, ceramics as well as nonferrous Limestone Ball MillThe characteristic tumbling motion of these mills has given them the name ‘tumbling mills’, which include the ball mill, tube mill and rod mill Ball mills are horizontal rotating cylindrical or conical steel chambers, approximately one third to half full of steel, alloy steel or iron balls, like that shown in Fig 410 A–C , or flint stonesBall Mill an overview ScienceDirect Topics2017年1月1日 An increase of over 10% in mill throughput was achieved by removing the ball scats from a single stage SAG mill These scats are non spherical ball fragments resulting from uneven wear of balls (PDF) Performance optimization of an industrial
.jpg)
Grinding in Ball Mills: Modeling and Process Control
Grinding in ball mills is an important technological process applied to reduce the size of particles which may have different nature and a wide diversity of physical, mechanical and chemical characteristics Typical examples are the various ores, minerals, limestone, etc The applications of ball mills are ubiquitous in mineral2017年8月4日 Since for the ball mill design we are using 80% passing, the required value of C2 for the ball mill will be equal to120 C3 is the correction factor for mill diameter and is given as; 𝐶𝐶3 = 244 𝐷𝐷 02 (3) However, it is important to note that C3 =0914 vessel used in producing the ball mill was got from aDesign, Construction and Performance Analysis of a 5 2023年5月15日 This mill, also known as the Raymond Roller Mill, is a common choice for limestone grinding It works by rotating a grinding ring or roller around a fixed shaft, allowing the material to be ground by the rolling and crushing action between the grinding parts Ball Mill A ball mill is a cylindrical device used to finely grind materialsWhat is Limestone Grinding Mill SBM Mill Crusher2023年2月15日 High temperature of the ball mill will affact the efficiency 3 For every 1% increase in moisture, the output of the ball mill will be reduced by 8% 10% 4 when the moisture is greater than 5%, the ball mill will be unable to perform the grinding operation 5 The bearing of the ball mill is overheated and the motor is overloaded Reasons17 Signs of Problems with Ball Mills: Quickly Remove Hidden Troubles
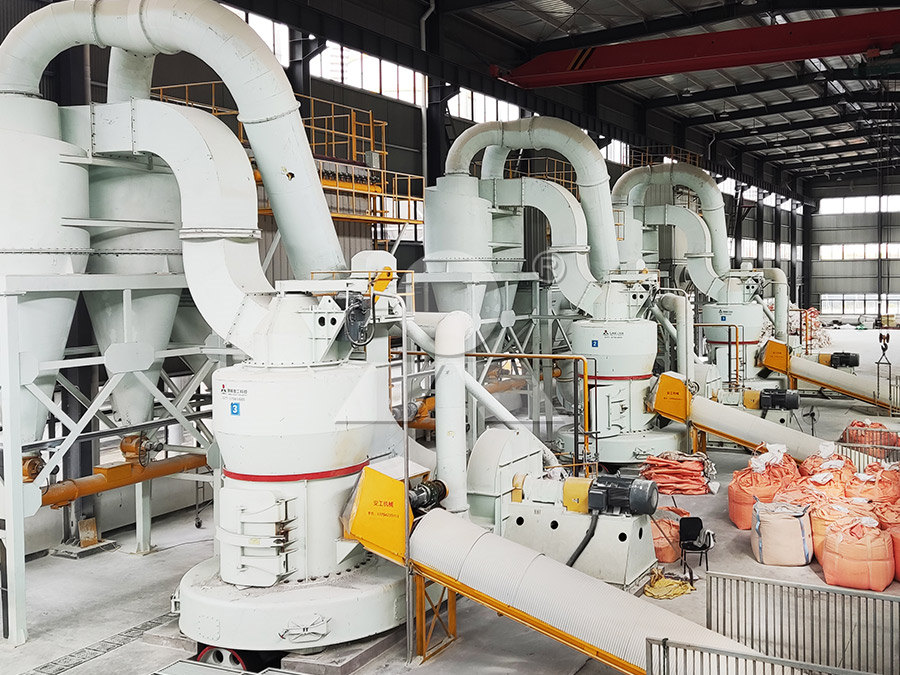
MODELING AND SIMULATION OF A CLOSED LOOP BALL
2016年4月11日 Modeling And Simulation Of A Closed Loop Ball Mill Grinding Circuit Proceedings of IRF International Conference, Chennai, India, 20th April 2014, ISBN: 978938 10 II DYNAMICS OF THE BALL MILL GRINDING CIRCUIT product Blaine measured in cm²/g and the rejects Fig1 In a continuous ball mill grinding circuit, the ball mill2012年6月1日 As the cylinder starts to rotate, the grinding balls inside the cylinder crush and grind the feed material, generating mechanical energy that aids in breaking bonds, activating the catalyst, and (PDF) Grinding in Ball Mills: Modeling and Process Control2024年7月1日 than ball mills, even if the ball mill is combined with a roller press This and further arguments led to the increased share of VRM for the grinding of finished cement Taking into account that VRM usually have a bigger output than ball mills, it can be declared that the major part of the cement production with newly installed mills comes from Picture: Loesche GmbH, Germany CEMENT SikaGrind® They provide a range of machinery for lime production plants, including crushers, ball mills, lime kilns, coolers, and other related equipment, which covering everything from raw material preparation to calcination, cooling, and packaging It is known for the expertise in the cement and lime industry and aim to help clients achieve efficient Lime Production Line for HighOutput Lime Production Plant
.jpg)
Ball Mill SBM Ultrafine Powder Technology
Brief introduction The ball mill is the key equipment for crushing the material after it is crushed Ball mills are widely used in cement, silicate products, new building materials, refractory materials, fertilizers, ferrous and nonferrous metal beneficiation and glass ceramics and other production industries, dry or wet grinding of various ores and other grindable materials