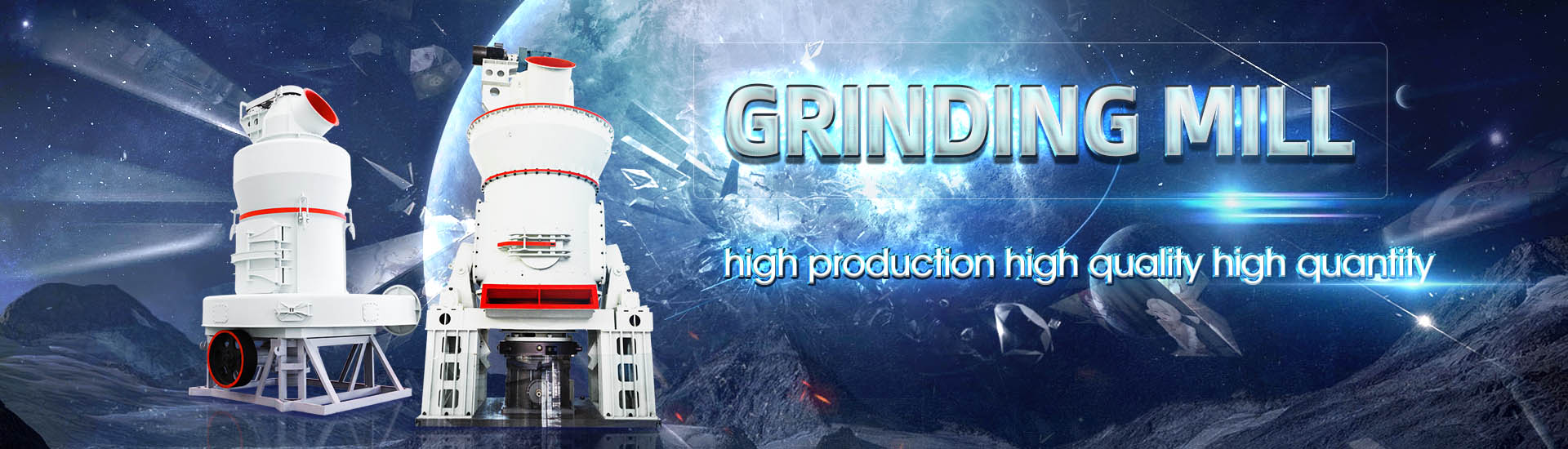
Casting process of fly ash aerated block
.jpg)
MANUFACTURING PROCESS OF AAC BLOCK
2017年9月17日 AAC blocks are light weight Aerated Autoclave Concrete Block It is manufactured through a reaction of aluminium powder and a proportionate blend of lime, cement, and fly ash or sand2020年7月15日 The Autoclaved aerated concrete (AAC) is a product of fly ash which is mixed with lime, cement, and water and an aerating agent The AAC is mainly produced as(PDF) Analysis of Autoclaved Aerated Concrete (AAC) Autoclaved Aerated Concrete (AAC) is versatile light weight concrete and they are generally used as blocks The study of AAC replacing natural sand by fly ash is investigated Design AAC mix Study and Experimentation of Autoclaved Aerated Concrete by 2023年7月7日 In the order to harness the potential of recycled industrial waste, specifically fly ash, for productive purposes Cement: Portland cement is commonly the preferred choice Autoclaved Aerated Blocks – IJERT International Journal of
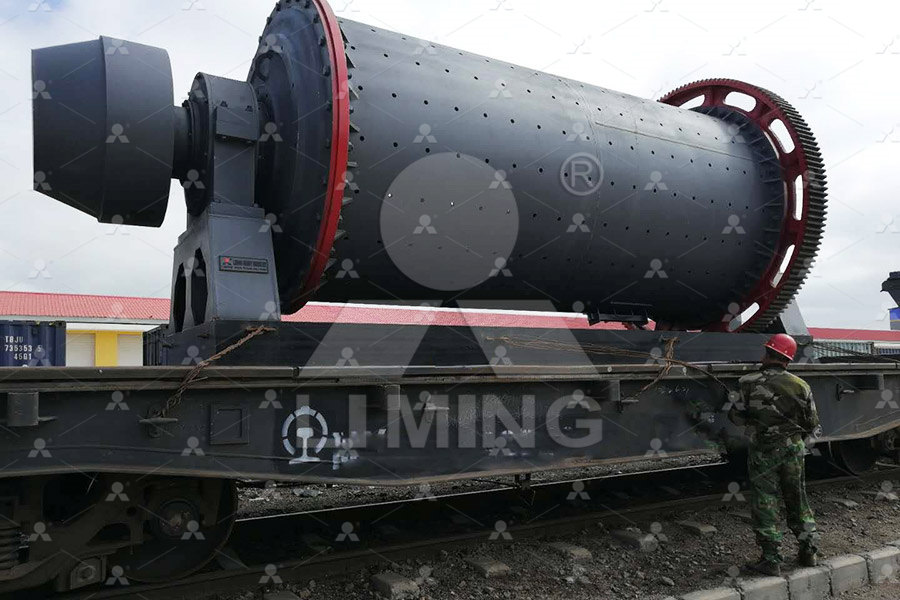
Investigating the characteristics of alkaliactivated fly ash
Sodiumbased alkaline activators are utilized to activate the fly ash Two diferent curing temperatures are employed, 60 °C and 85 °C The properties of the block, such as strength, 2015年1月1日 This paper presents the results of microstructure monitoring and physical and mechanical tests on samples of fly ash aerated concrete based on high temperature and Development of Microstructure of the Fly Ash Aerated2024年10月22日 This study explores the utilization of these waste streams in developing sustainable construction materials, focusing on fly ashbased geopolymers and incorporating Mechanical, microstructural, durability, and energy analysis of fly 2020年6月24日 AAC Blocks manufacturing process Flow chart for Autoclaved Aerated Concrete production, ie AAC blocks manufacturing process: AAC blocks manufacturing process Step1: Preparation of raw materials Raw materials AAC Blocks Manufacturing Process Civil
.jpg)
Experimental Analysis of Aerated Concrete Block
form bottom ash and fly ash Fly ash is the material that is carried off with the flue gases, where it is collected and can be stored in silos for testing and beneficial use Fly ash can be classified into classes Class F fly ash normally produced by burning anthracite or bituminous coal Usually it has less than 5% of CaO2023年8月4日 AAC blocks are ecofriendly because fly ash recycles waste and reduces carbon footprint Faster Construction Process: AAC blocks‘ huge size and ease of installation make building projects faster and cheaper Cost Aerated Concrete Blocks: Building with InnovationSand slurry is mixed with other ingredients just like fly ash slurry 6 CASTING AND RISING AAC blocks manufacturing process involves casting, rising and precuring Once desired mix of raw materials is ready, it poured is in molds This process has different names It is called casting, pouring or molding For current discussion, we’ll call A STUDY OF AUTOCLAVED AERATED CONCRETE BLOCK AS A 2019年6月23日 With the rapid development of construction industry, consumption of concrete block has increased rapidly in China As a kind of green building material and resource comprehensive utilization product, autoclaved aerated fly ash and concrete block have better performance in terms of heat preservation, sound insulation, and fire resistance However, Life cycle assessment of autoclaved aerated fly ash and concrete block
.jpg)
Autoclaved Aerated Blocks International Journal of Engineering
Autoclaved Aerated Blocks Basavachetana Gudugurmath 1, Prajwala M 2, Divya L 3, Hemantha R 4 essential for the production of AAC blocks is fly ash, which plays an essential role in the manufacturing Fig 9 Mould Casting • Drying: The drying process of concrete is Most of the AAC companies in India use fly ash to manufacture AAC blocks Fly ash is mixed with water to form fly ash slurry Slurry thus formed is mixed with other ingredients like lime powder, cement, gypsum and Aluminum powder in quantities consistent with the recipe Alternately sand can also be used to manufacture AAC blocks A ‘wet’Study and Experimentation of Autoclaved Aerated Concrete by using Fly Ash2020年7月15日 The Autoclaved aerated concrete (AAC) is a product of fly ash which is mixed with lime, cement, and water and an aerating agent The AAC is mainly produced as cuboid blocks and prefabricated panels(PDF) Analysis of Autoclaved Aerated Concrete (AAC) Blocks Process Flow The AAC block manufacturing process involves the A dosing and mixing unit is used to form the correct mix to produce Autoclaved Aerated Concrete (AAC) blocks Fly ash/sand slurry is pumped into a gypsum and aluminium is poured in moulds Moulds can be of various sizes depending upon installed capacity Before casting, Process Flow MEPCO
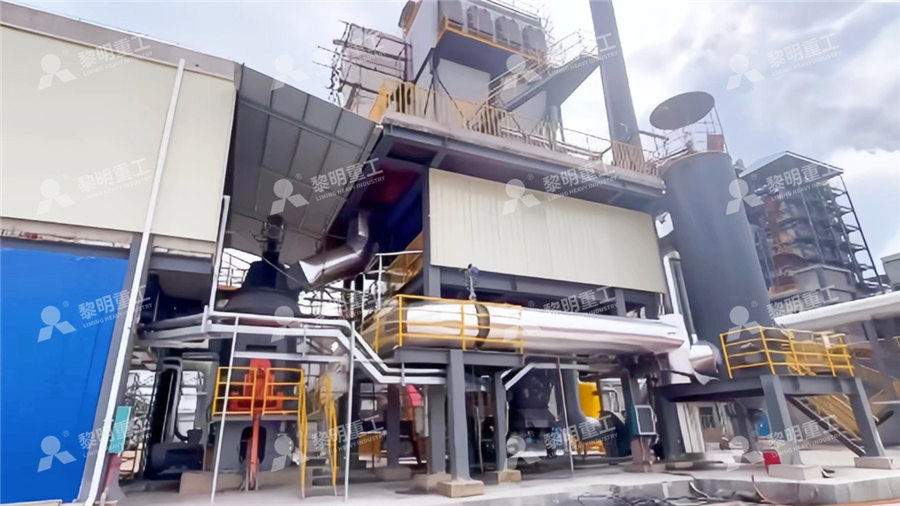
Autoclaved Aerated Concrete: Difference Between Sand And Ash
2022年8月15日 Conclusion Autoclaved sand aerated concrete has certain advantages compared with autoclaved ash aerated concrete After all, sand aerated block is an updated alternative to traditional fly ash aerated block, and its advantages mainly lie in higher strength, and a greater improvement in seepage resistance, drying shrinkage, etc2023年7月12日 Autoclaved aerated concrete (AAC) was invented in 1920s AAC is composed of lime, cement, sand, fly ash and aluminum powder, which is the component that plays an important role in creating air Improvement on manufacturing processing time of AAC Block2021年8月1日 This paper presents comparative analysis of clay bricks and fly ash based autoclaved aerated concrete (AAC) block properties, methodology, process and material required for preparing fly ash based (PDF) Comparison of Fly Ash Based (AAC) Block and Clay Bricks 2022年9月13日 Even though fly ash is perceived as waste, it has a magic ingredient called reactive silica in it One of the principal constituents, about 65%, of aerated concrete in India is fly ash However, we must remember that all fly 6 Simplified Steps Of AAC Block Manufacturing Ecorex
.jpg)
(PDF) Manufacturing Process of Aac Block Academia
International Journal of Advance Research, Ideas and Innovations in Technology, 2019 The lightest masonry material available in today's market is AAC blocks (Autoclaved Aerated Concrete Blocks) whose density is about 1/3 rd times of the clay bricks and fly ash bricks and about 1/5 th times of the Concrete because of its foamlike structure made up of 80% of air voids while they deep grinding of quicklime, cement, gypsum, aggregate (fly ash), so that the fineness of the specific surface area of 4000 cm 2/ g or more, promote more active ingredients to participate in the reaction, improve the strength of autoclaved aerated blocks, and because of deep grinding, the slurry prepared by raw materials is more viscous, more favorable to the stability of pouringFLY ASH AAC BLOCK PLANTAAC BLOCK Get contact details address of companies manufacturing and supplying Fly Ash Bricks, Fly Ash Blocks, Grey Fly Ash Bricks across India IndiaMART Fly ash bricks making process; Fly ash bricks; Advantages Grey acc solid ash bricks; Rectangular autoclaved aerated concrete blocks; Fly ash bricks 230x110x70, 9 in x 4 in x 3 in; A garde Fly Ash Bricks Fly Ash Blocks Latest Price, Manufacturers2023年4月17日 Fly ash employed in the current experiment is depicted in Fig 1 Fly ash testing was conducted in accordance with the testing procedure outlined in IS 3812: 2013 PartI [9] The chemical characteristics of fly ash are shown in Table 2 In the current experiment, fly ash with a specific gravity of 22 and a specific surface area of 350 m 2 /kg Investigation on properties of autoclave aerated concrete using
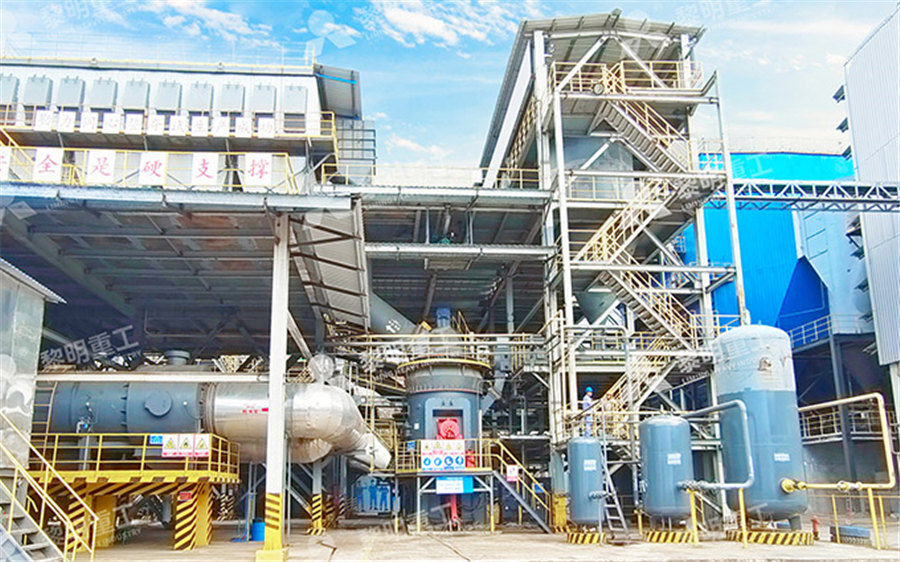
AAC America's Best Block Inc
AAC blocks are made from natural materials such as sand, lime and cement They do not emit pollutants, toxins, or byproducts In fact, America’s Best Block is using the byproduct fly ash as one of its blocks components, making its blocks even more environmentally friendlyDosing Mixing: A dosing and mixing unit is used to form the correct mix to produce Autoclaved Aerated Concrete (AAC) blocksFly ash/sand slurry is pumped into a separate container Once the desired weight is poured in, pumping is stopped Similarly lime powder, cement and gypsum are poured into individual containers using screw conveyorsAn Overview on AAC Block Manufacturing ProcessConecc Concrete Solutions Pvt Ltd is the leading manufacturer of Autoclaved Aerated Concrete (AAC) blocks in Karnataka AAC blocks are also known as Fly ash / Lightweight Brick/Block Conecc prides itself on maintaining the highest level of customer service and supportLightweight AAC Blocks Manufacturer in Karnataka India Conecc2024年6月16日 When it comes to modern construction materials, AAC blocks and fly ash bricks are two popular choices Both materials offer unique benefits and are used for various applications Composition and Manufacturing Process AAC Blocks: Autoclaved Aerated Concrete (AAC) blocks are made from a mixture of cement, lime, sand, water, Understanding the Differences: AAC Blocks vs Fly Ash Bricks
.jpg)
AAC Blocks: Manufacturing Process, Benefits, and Application
Aerated Autoclaved Cement/Concrete Blocks (AAC Block) Cellular concrete, which was developed in 1920, has addressed the need for an artificial material with properties akin to those of wood It avoided some of its drawbacks, such as its water absorption and maintenance requirements, and was lightweight and perforable or cutWith the rapid development of construction industry, consumption of concrete block has increased rapidly in China As a kind of green building material and resource comprehensive utilization product, autoclaved aerated fly ash and concrete block have better performance in terms of heat preservation, sound insulation, and fire resistanceLife cycle assessment of autoclaved aerated fly ash and concrete block 2015年12月31日 In recent years the evaluation of Uvalue for buildings materials has been seen Since 1st January 2014 Uvalue can’t be higher than 0,25 [W/m2K], but since 2017 this value will be 0,23 and 0,20 (PDF) Autoclaved Aerated Concrete based on Fly Ash in Density The production process for NAAC blocks involves mixing cement, water, and an aluminium agent to form slurry The slurry is then poured into Proportions are taken for Non Autoclaved Aerated Blocks Fly ash =50% Cement: 40% Lime: 7% Gypsum: 3% Aluminium Powder: 008% after 24 hrs of Casting After Demoulding kept specimensEvaluation of Bagasse Ash as a Substitute for Fly Ash in the
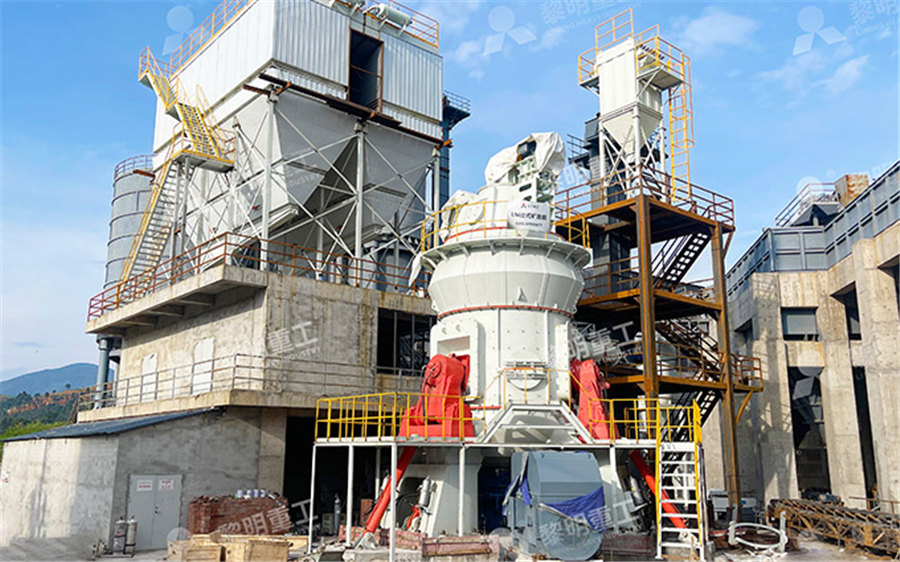
(PDF) Technological Properties of Fly AshBased ResearchGate
2021年2月23日 Fig 31 The schematic drawings showing the process from fly ash to f ly ashbased geopolymer cement/concrete (Zhuang et al, 2016) Fig 32 shows the different patterns of aluminosilicate chains 6 天之前 Let's delve into autoclaved aerated concrete, exploring its composition, manufacturing process, and the advantages that make it a preferred choice in contemporary construction Composition of AAC blocks AAC blocks are primarily composed of fly ash, cement, lime, gypsum and aluminium powderWhat is an Autoclaved Aerated Concrete (AAC) block?2024年9月23日 It forms a hard substance that binds the fly ash and sand particles It contributes to the comprehensive strength of the fly ash and makes it suitable for loadbearing applications The use of cement enhances the durability of fly ash bricks It makes them resistant to weathering and harsh chemicals Fly Ash Brick Manufacturing ProcessA Comprehensive Guide on How to Make Fly Ash Bricks2018年10月24日 This research work was done to show comparative study residential building while considering dead and live load using AAC block or fly ash and a clay brick for G+5 building was done The use of AAC blocks offers an innovative solution to the construction industry associated with preserving environmental issues In this work, also an attempt has been made A review on cost analysis of building construction by using
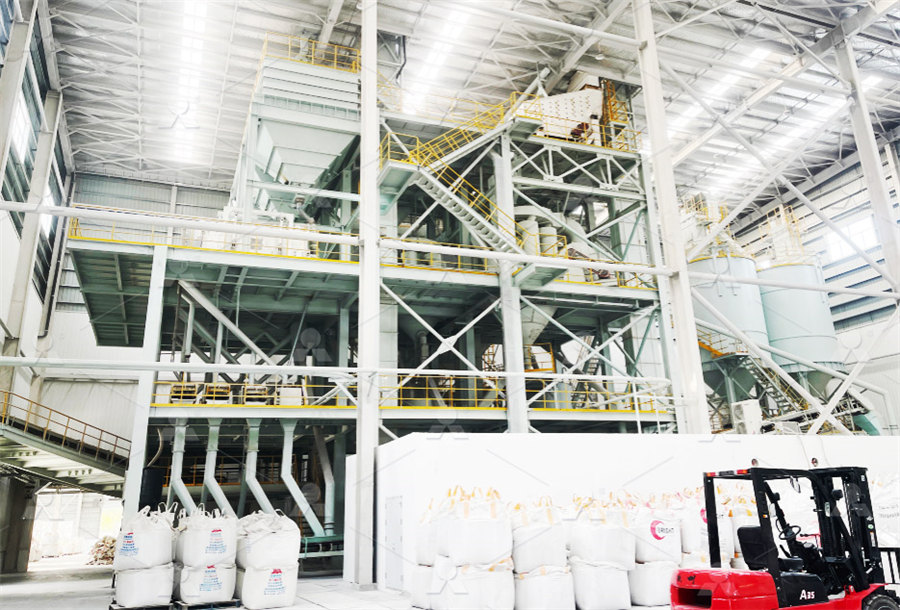
What Is The Common AAC Block Raw Material Ratio? CNBM
2023年7月11日 AAC block raw material consists of fly ash or sand, cement, lime, gypsum, aluminum powder, water, etc The AAC block raw material proportion is important to the quality of finished products This article introduced the AAC block raw materials and the ratio of them in production You will also discover how the ratio of raw materials affects the manufacturing of 2023年4月24日 Abstract This study investigates the use of bagasse ash as a partial replacement for fly ash in the production of non autoclaved aerated concrete (NAAC) blocks The study aimed to determine the optimal percentage of bagasse ash to replace fly ash in NAAC blocks this study demonstrates that bagasse ash can be used as a partial replacement for fly ash in the Evaluation of Bagasse Ash as a Substitute for Fly Ash in the 2021年2月23日 According to the previous report by Ling and Teo [], Siram [] and Xu et al [], there are still uses an OPC cement and clay as a source material in making lightweight bricksEven in the production of commercial lightweight masonry units, which are cellular lightweight (CLC) blocks and autoclaved aerated concrete (AAC) had utilized OPC cement Technological Properties of Fly AshBased Lightweight Springer2024年6月13日 Fly Ash: The use of fly ash, a byproduct of coal combustion in power plants, in AAC block manufacturing both utilises a waste material and reduces the requirement for raw material, thus embodying the principle of the What Are Aerated Concrete Blocks Should You Use
.jpg)
Comparison of Autoclaved Aerated Concrete (AAC) Blocks and
2023年10月1日 Concrete hollow blocks (CHB) have been used worldwide, especially in the Philippines, due to their costsaving and lightweight features Moreover, the energyefficient CHB promotes faster 2014年8月1日 The resulting incineration bottom ash aerated geopolymers show comparable properties to the control aluminum aerated geopolymers, with a density of as low as 860 kg/m³ and corresponding Rheological properties of aerated cement pastes with fly ash 2 K Hussin email: R Ahmad email: A A Kadir Faculty of Civil Engineering and Built Environment, Universiti Tun Hussein Onn MalaysiaChapter 3 Technological Properties of Fly AshBased Lightweight The raw materials used for preparation of AAC blocks are fly ash, cement, gypsum, lime and aluminum powder Being aerated, AAC contains 50 60 % of air, leading to concrete during process Aerated concrete blocks are available in different dimensions and various thicknesses Dimensions for these blocks which are commonly usedA REVIEW PAPER ON LIGHT WEIGHT AUTOCLAVE AERATED CONCRETE BLOCK
.jpg)
Production of autoclaved aerated concrete by using municipal
Life cycle assessment of autoclaved aerated fly ash and concrete block production: a case study in China Environ Sci Pollut Res, 26 (25) (2019), pp 2543225444 Chlorides removal and control through waterwashing process on MSWI fly ash Procedia Environ Sci, 31 (2016), pp 560566 View PDF View article View in Scopus Google Scholar2017年5月22日 The use of AC block also reduces the requirement of materials up to 50%Aerated concrete can produce a light weight, environmentally friendly, lower coefficient of thermal expansion, mould resistance, reduced dead weight and good sound insulation as a result of air voids within aerated concrete this block no coarse aggregates in its mixture the blocks Experimental Analysis of Aerated Concrete Block – IJERT2020年5月28日 Unlike brick manufacturing process which uses previous top layer agricultural soil, AAC uses Fly Ash (65% of its weight), thus provides the most constructive solution to the nation’s fly ash utilization problem Main process flow of Autoclaved Aerated Concrete AAC Blocks Plant Production Line It has the advantages from the process: 1Hongfa Automatic AAC ALC Autoclaved Aerated Concrete Sand Fly Ash Block