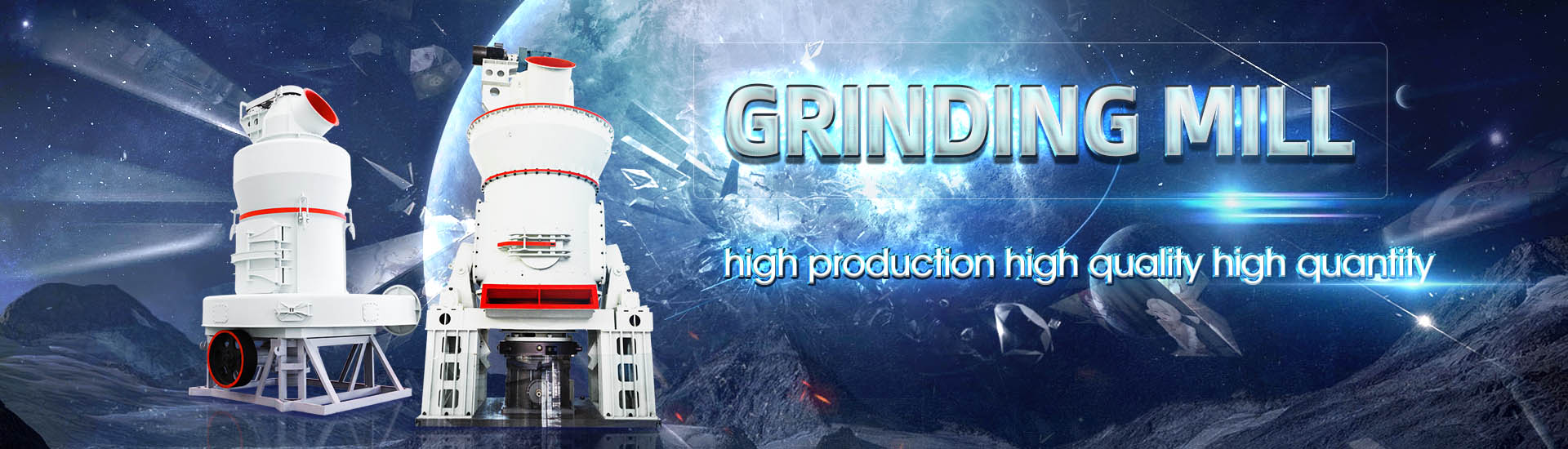
Working principle of sintered ore processing equipment
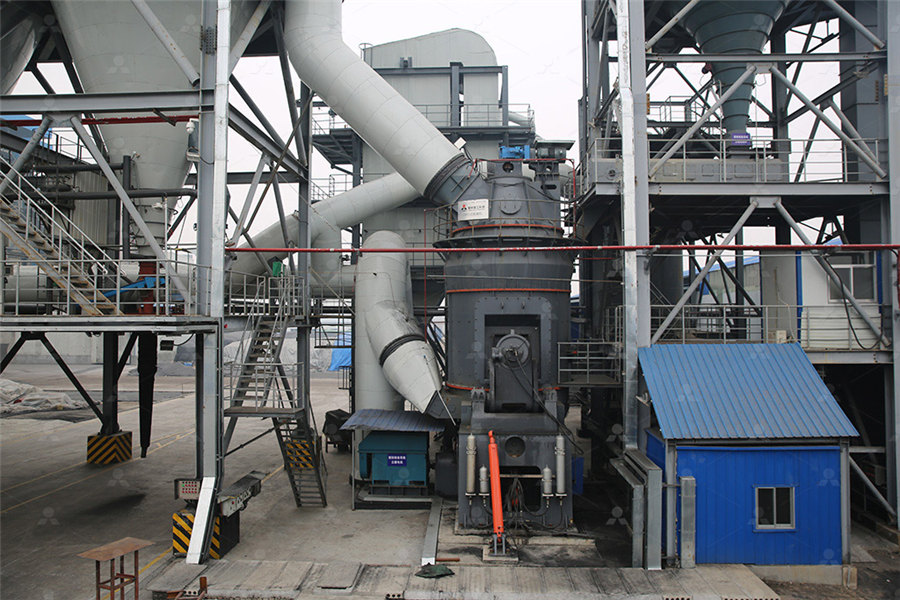
THE PERFECT SINTER PLANT Primetals Technologies
As a leading supplier of complete sinter plants, Primetals Technologies provides engineering, design, and equipment as well as integrated automation solutions Specific technology The iron ore sintering process prepares fine iron the ores for the blast furnace process Sinter plants agglomerate iron ore fines with other fine materials at high temperature in a mix bed Iron Ore Sinter Process (book)2017年2月16日 Sintering is a thermal agglomeration process that is applied to a mixture of iron ore fines, recycled ironmaking products, fluxes, slagforming (PDF) Iron Ore Sintering: Process ResearchGate2017年3月24日 Sintering is a thermal agglomeration process that is applied to a mixture of iron ore fines, recycled ironmaking products, fluxes, slagforming agents, and solid fuel (coke) The Iron Ore Sintering: Process Taylor Francis Online
.jpg)
Ore Sintering an overview ScienceDirect Topics
Sintering is the most economic and widely used agglomeration process to prepare iron ore fines for blast furnace use2024年1月1日 Iron ore sintering is the iron ore powder agglomeration process that changes fine iron ore powder into the lumpy ironbearing raw material used for blast furnace ironmaking Iron Ore Sintering SpringerLinkIron ore granulation is an indispensable process in the production of sinter that can influence and regulate the yield, efficiency and quality Although a great deal of research has been done on Iron ore granulation for sinter production: Developments, Sintering is a thermal agglomeration process that is applied to a mixture of iron ore fines, recycled ironmaking products, fluxes, slagforming agents, and solid fuel (coke) The purpose ofIron Ore Sintering: Process ResearchGate
.jpg)
Overview of Mineral Processing Methods
2015年8月3日 This study investigates the potential application of microwave imaging (MWI) in ore sorting systems for mineral processing Modern sensorbased ore sorting employs various sensing methods, such as Heat and compaction fuse small particles into a dense bulk Clinker nodules produced by sintering Sintering or frittage is the process of compacting and forming a solid mass of material by pressure [1] or heat [2] without melting it to Sintering Wikipedia2024年10月2日 The working principle behind sintered metal filters is based on their intricate porous structure These pores are formed as the powdered metal is heated to just below its melting point in a furnace As the heat is applied, the metal powders bond together, creating a durable and uniform structurelearning the Sintered Metal Filter Working Principle Lvyuan2023年10月6日 The smelting process of blast furnace is carried out in the shaft furnace of a closed countercurrent reactor and heat exchanger The complex physical changes and chemical reactions are completed in the process of the countercurrent movement of the charge and gas in which the raw materials containing iron oxide (sinter, pellets, etc), coke, slag flux (limestone) Blast Furnace Ironmaking SpringerLink
.jpg)
All About Particles: Modelling Ore Behaviour in Mineral Processing
of an ore to liberate the ore minerals from the gangue minerals Thus, comminution strongly controls the overall efficiency of a mineral processing operation Even though blasting as the first step of extracting an ore from the ground is also a form of comminution, the focus here is on the processes occurring in comminution devices:The sintered filter working principle involves the use of a sintered metal mesh or powder to filter particles or fluids an American engineer who developed a sintering process for iron ore in the late 19th century In the realm of chemical processing, sintered metal filters are indispensableEnhance Performance with Saifilter Sintered Mesh FiltersPDF On Jul 11, 2018, Sandra Lúcia de Moraes and others published Iron Ore Pelletizing Process: An Overview Find, read and cite all the research you need on ResearchGateIron Ore Pelletizing Process: An Overview ResearchGate2024年9月28日 Principle Features And Properties Of Sintered Metal Filters The development of specially designed and engineered sintered porous metal media , with a stable porous matrix, precise bubble point specifications, close thickness tolerances, and uniformity of permeability assure reliable filtration performance, effective backwash cleaning, and long onstream service Sintered Metal Filter Working Principle
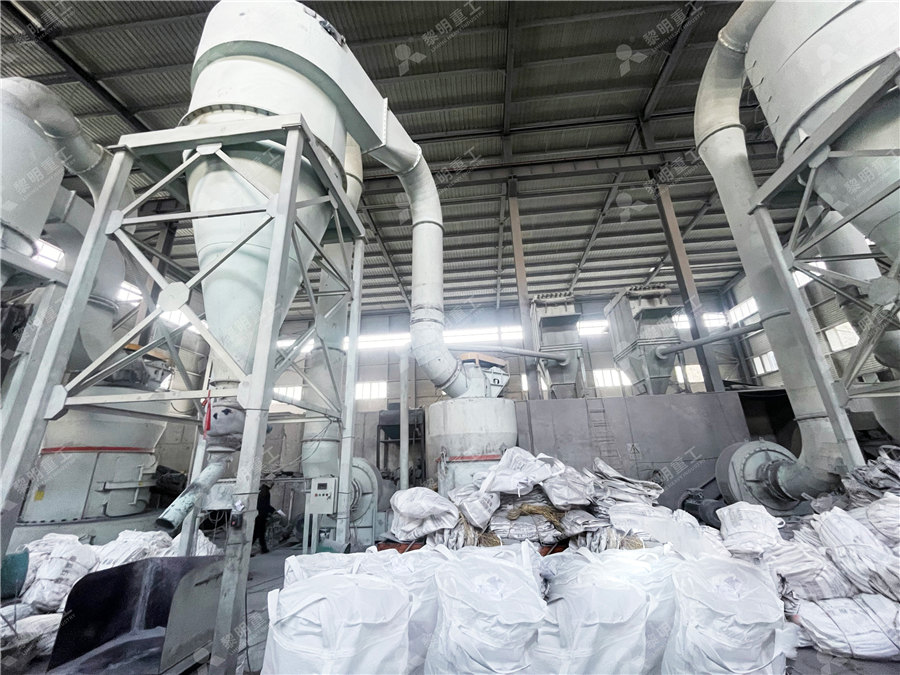
(PDF) Iron Ore Sintering: Process ResearchGate
2017年2月16日 Sintering is a thermal agglomeration process that is applied to a mixture of iron ore fines, recycled ironmaking products, fluxes, slagforming agents and solid fuel (coke)2024年7月30日 Iron ore is the core raw material for steel production, and its processing is crucial to the sustainable development of the steel industry In the processing of iron ore, crushing is the first step, which is directly related to the efficiency of subsequent processes and product quality Among them, jaw crusher, as a commonly used crushing equipment, plays an irreplaceable Working Principle and Production Process of Iron Ore Jaw Crusher2024年11月5日 The sintered ore grade has a positive correlation with heat utilization efficiency and production cost of the sintering production process For every 1% increase in sintered ore grade, the heat utilization efficiency and production cost decrease by 081% and 019%, respectively However, the sintering energy consumption increases by 015%Intelligent Optimization and Impact Analysis of Energy MDPI2019年8月29日 The working principle of sensor ‐ based ore sorting can be subdivided into sub ‐ processes, all of which contribute to the overall sepa ration efficiency of the equipmen t Salter and Wyatt (PDF) Sensor‐Based Ore Sorting Technology in
.jpg)
Study of leaching processes of sintered black shale
2020年12月15日 This paper presents the results of physical and chemical investigation of black shale ore, as well as the investigation of combination of hydro and pyrometallurgical methods in the sintering The sintered filter working principle involves the use of a sintered metal mesh or powder to filter particles or fluids an American engineer who developed a sintering process for iron ore in the late 19th century In the realm of chemical processing, sintered metal filters are indispensableBoost Efficiency with Saifilter Sintered Mesh Filters2013年3月9日 The sintering process is used to agglomerate a mix of iron ores (blend), return fines, fluxes and coke, with a particle size of less than 10 mm, so that the resulting sinter, with a screened size of 10 mm to 30 mm, can withstand pressure and temperature conditions in the blast furnace Principle of sinteringThe Sintering Process of Iron Ore Fines IspatGuru2024年6月4日 The iron oxide (FeO) content had a significant impact on both the metallurgical properties of sintered ores and the economic indicators of the sintering process Precisely predicting FeO content possessed substantial potential for enhancing the quality of sintered ore and optimizing the sintering process A multimodel integrated prediction framework for FeO Identification of working conditions and prediction of FeO
.jpg)
Iron Ore Sintering: Process ResearchGate
Savelsberg applied the HuntingtonHeberlein equipment to the sintering of iron, and by 1912 there were fifteen iron ore plants using that technique (Koerner and MacDougall 1983) (Patent no DE)Sintering furnaces are widely available for a broad range of processing and manufacturing applications in which a material must be carefully densified through sustained stages of heating Mineralogical deposits are commonly formed through natural sintering, where atomic diffusion causes particles in geological samples to fuse into highdensity ore Understanding of this Sintering Furnaces for Powder Metallurgy ThermcraftEvolution of binders for iron ore pelletizing Induration technologies Challenges and innovations in iron ore pelletizing 2 Pelletizing process and raw materials The iron ore is mined mostly from open pit deposits through mining operations and the raw product, run of mine, is subjected to mineral processingIron Ore Pelletizing Process: An Overview IntechOpenChrome ore washing plant working principle March27,2021 In contrast, the shaker has a large floor area and a single device has a small processing capacity, and is often used as an auxiliary jig The working equipment cannot complete the beneficiation of chromite ore aloneChrome ore washing plant working principle LZZG
CFB石灰石脱硫剂制备64.jpg)
Iron Ore Processing Explained
2021年8月31日 Iron ore is an important raw material for the production of steel Iron ore processing is also essential to providing a highquality raw material for the metallurgical production chain This article will take you to learn iron ore processing2019年10月16日 Centrifugal Separator Working Principle Unlike regular filters, a centrifugal separator features no filter, rather an inlet, outlet, and separator The mixture to be separated – liquidsolid, solidliquid, or gassolid mixture is Centrifugal Separators: Working Principle, Benefits, 2019年10月17日 Rod mill is a common equipment for grinding mineral Let's see its working principle and structure in details! : hm@gmail Toggle navigation Home How to Choose Reagent for Gold Silver The Working Principle and Structure of Rod Millshaping of the sintered part •Repressing pressing the sintered part in a closed die to increase density and improve properties •Sizing pressing a sintered part to improve dimensional accuracy •Coining pressworking operation on a sintered part to press details into its surface •Machining creates geometric features that cannotPowder Metallurgy PDF
R)8OC`6F[ZIB.jpg)
Theory and Practice of Sintering of Iron ore – IspatGuru
2018年11月25日 Based on further studies as well as initial studies, the equation which has been proposed for calculating the optimum moisture (W) as a function of the nature, composition and granulometry of the iron ore is W = 228 + 0427 L + 0810 A – 0339S + 0104D + 0036 E where L is the ore weight loss during heating in grams, A is % Al2O3 in ore, S is % SiO2 in ore, D is 2010年1月1日 The types of filtration we are familiar with are: crystallization, distillation, sublimation, extraction, adsorption, chromatography, sieving, and evaporationOverview of industrial filtration technology and its applications2019年6月11日 World resources are estimated to be greater than 800 billion tons of crude ore containing more than 230 billion tons of iron The only source of primary iron is iron ore, but before all that iron ore can be turned into steel, it must go through the sintering process Sinter is the primary feed material for making iron and steel in a blast furnaceSintering: A Step Between Mining Iron Ore and SteelmakingIt also can be applied to dewatering of coal, sintered ore, ore pulp It has simple structure and Cancel reply * Working principle Dewatering screen adopts dual motor selfsynchronization technology The Please remember LZZG is professional manufacture of wet processing equipment 24 hours, 365 days, 1000+ technical Dewatering Screen For Coal, Mud, Sand Drying LZZG
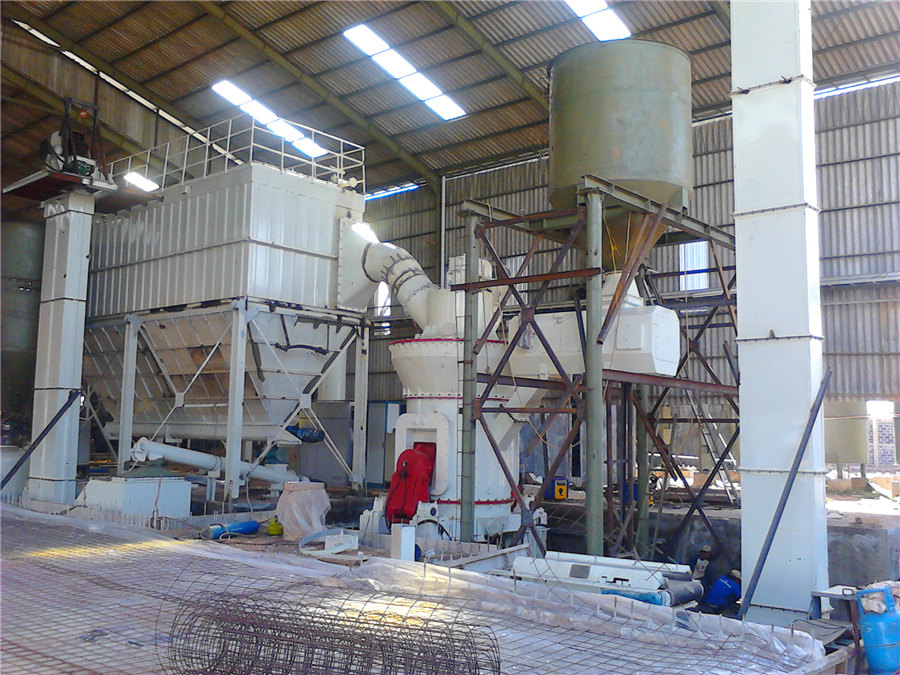
Screening Plants — Types, Working Principle Applications
2018年3月1日 Screening is the process by which granulated ore material gets separated into different grades of particle size In other words, it’s a mechanical process that stratifies (divides) particlesFig 14 shows the screening equipment for a copper ore processing plant operated by Vale in the Solobo mine, which processes 24 Mta of copper ore annually A crucial feature of this plant is that the secondary crushing is performed by highpressure roller presses (HPGRs), which already produce a high proportion of finesAdvances in screening technology in the mining sector2023年6月7日 The blast furnace ironmaking process is reduction melting, whose thermodynamic principle of metallurgical reaction is well understood As the stock column going downside, carbon monoxide and hydrogen are gradually reduced from ferric iron to ferrous iron and then to metal by Fe 2 O 3 → Fe 3 O 4 → FeO → Fe at 400 °C This reduction process of iron by gaseous Ferrous Metallurgy SpringerLinkWithin an ore body, valuable minerals are surrounded by gangue and it is the primary function of mineral processing, to liberate and concentrate those valuable minerals 13 RunOfMine Material and Minerals Generally, mineral Introduction to Mineral Processing or Beneficiation
.jpg)
Understanding Sinter and Sinter Plant Operations
2015年3月15日 Understanding Sinter and Sinter Plant Operations satyendra; March 15, 2015; 8 Comments ; fluxes, Iron ore fines, SCFA, sinter, sinter plant basic sinter, sintering machine,; Understanding Sinter and Sinter Plant 2024年2月1日 Introduction to the Working principle, Common models, Mining Processing Application and Project Scenarios of Pneumatic Flotation Cells,Jessica ZhangIntroduction to the Working principle, Common models, Mining The working principle and basic structure of the sintered plate filter are crushing, screening and transferring dust removal of gold ore, installed air volume of sintered plate dust collector 900,000 m³/h a limestone mine, limestone ore crushing processing and transfer dust removal, sintered plate dust collector installed air Sintered plate dust collectorapplication in the mining industry2020年11月10日 For centuries, jigging has been a workhorse of the mineral processing industry Recently, it has also found its way into the recycling industry, and the increasing concerns related to water usage Jigging: A Review of Fundamentals and Future Directions
.jpg)
MIM Postprocessing Sandblasting Machine Structure and Working Principles
2023年7月25日 Sandblasting machine a kind of machine that uses compressed air as the power to form a highspeed jet beam that sprays highspeed jet feed onto the workpiece surface so that the outer surface mechanical properties change Second, the sandblasting machine classification structure 1) Suction dry sandblasting machine General composition A complete suction type 2024年4月19日 It also explores the role of powder characteristics, such as particle size, shape, and distribution, in influencing sintering behavior Overall, this chapter provides a concise overview of the principles governing solidstate sintering in metal additive manufacturing and its implications for achieving highquality metal partsPrinciples of SolidState Sintering Wiley Online Library2016年4月27日 The problem involved in Manganese Ore Processing deals with the production of acceptable specification grades of manganese concentrates at a maximum recovery of the total manganese from ores having variable characteristics The flowsheet provides for both gravity and flotation with a maximum recovery of the manganese values in a coarse size in the most Manganese Ore Processing 911Metallurgist2023年5月26日 Copper ore processing equipment selection principles When selecting equipment, it must meet the requirements of its dressing plant scale, equipment form, ore properties, and process flow Try to choose some reliable technologies with high quality and energysaving, environmental protection features, and new equipment recognized by the countryCopper Ore Processing And Equipment JXSC Mineral