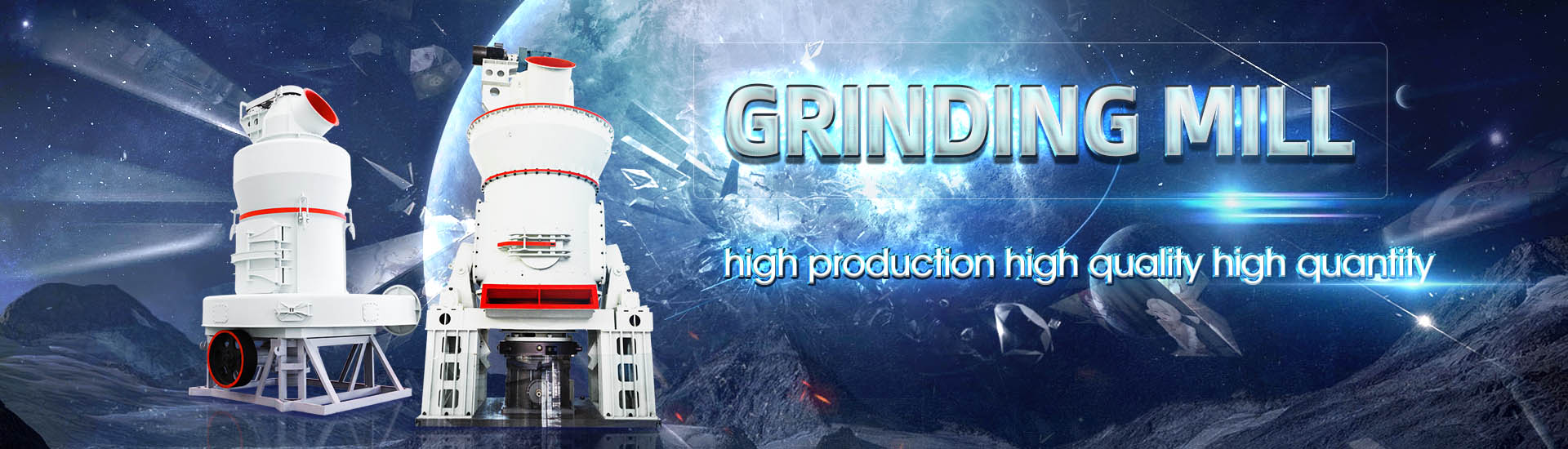
What is the crushing particle size of 600 type ore mill
.jpg)
AMIT 135: Lesson 5 Crushing – Mining Mill Operator Training
The selection of the right crushing equipment is influenced by many factors some of which are upstream of the crushing plant (eg blasting pattern and mining method) and others which are downstrea 展开2017年3月4日 Crushing is the first step of mineral processing where the ore/rocks from the mine site is fed into the mechanical equipment in order to reduce the size of masses for subsequent usage by SIZE REDUCTION BY CRUSHING METHODSTo achieve a uniform final particle size with minimal fines, the roller mill must have the right roll surface, roll speed ratio, and roll gap for your applicationRoller mills: Precisely reducing particle size with greater efficiencyThe comminution process reduces particle sizes by breaking, crushing, or grinding of ore, rock, coal, or other materials The process is most often used in the field of mining and / or mineral processing, where mineral ore is broken Comminution Multotec

Rock Crushing Rule of Thumb 911Metallurgist
2015年12月17日 For example, a 48 by 60 crusher will have a capacity in the order of 600 tph when crushing ore in a hard rock mine Source: Jack de la Vergne The capacity of a jaw 2014年1月1日 Crushing plants have been of great interest in reducing the particle size of ores milling operations need to consider sustainable development Since the crushing plants are operatedFactors affecting the performance of crushing plant 2017年3月4日 Size Reduction is mainly done through crushers and mills Crushing and grinding are the two primary comminution processes Crushing is normally carried out on the "runofm ine" oreSIZE REDUCTION BY GRINDING METHODS2016年1月1日 The crushers are normally fed with rocks, up to about 1 m in size, while the grinders are usually fed with rocks crushed down to a maximum size of about 50 mm Larger Size Reduction and Energy Requirement ScienceDirect
.jpg)
Ore Crushing SpringerLink
2023年7月22日 The ore crushing process includes four types: ore coarse crushing, ore medium crushing, ore fine crushing, and ore superfine crushing Ore coarse crushing is a process of Particle size differences can alter properties like particle shape, surface area, and porosity That can affect the end product in many ways — product performance, efficacy, processability, MILLING METHODS COMPARISON GUIDE Custom Processing 2015年4月9日 This type of mill is only suited for those kinds of ores which are of a fairly coarse nature but once they are broken, disintegrate readily into small size Typically this type of mill can deliver a product with a fineness of less Grinding Mills and Their Types – IspatGurutechnologies also require lab measurements to track changes in particle size including crushing, homogenization, emulsifi cation, micro fl uidization, and others Separation steps such as screening, fi ltering, cyclones, etc may be monitored by measuring particle size before and after the process Particle size growth may beA GUIDEBOOK TO PARTICLE SIZE ANALYSIS Horiba
.jpg)
Solids Choose the Right Grinding Mill Chemical
where T is the grinding time to reach a certain median particle size, K is a constant that depends upon the material being processed, the type of media and the particular mill being used, D is the diameter of the media, and N is the The different type of fracture mechanisms may be observed from the particle size distribution functions of a mill product Figure 112 provides the particle size distribution of a mixture of two plastic waste products After grinding, the particle size distribution changed to that shown in Figure 113 Clearly, the two different types of plastic11 Crushing and classification2016年2月26日 911 Metallurgist is a trusted resource for practical insights, solutions, and support in mineral processing engineering, helping industry professionals succeed with proven expertise Crushing Products Size and Shape What to ExpectCrushing Products Size and Shape What to ExpectEven though the ore is reduced below 3 mm with conical and some impact crushers, this process is called crushing The process of size reduction is defined by below conversion formula: The ore whose size will be reduced + Energy = Reducedsize ore + Sound + HeatWhat Is The Crushing Process MEKA
.jpg)
Roller mills: Precisely reducing particle size with greater efficiency
How the mill achieves uniform particle size To achieve a uniform final particle size with minimal fines, the roller mill must have the right roll surface, roll speed ratio, and roll gap for your application Roll surface Typically, the roll surface is corrugated rather than smooth to achieve efficient size reduction, as shown in Figure 32021年7月6日 Crushing reduces the ROM ores to a size of three types of iron ores with 30425 mm were oxide minerals compared to ball mill grinding at the particle size of the products close to Comminution a Heart of Mineral Processing ResearchGateLearn more below about a few different types of particle size reduction types Crushing Crushing is generally considered to reduce particles, like large rocks and stones, to gravelsized material This translates to roughly 0 to 5 mesh Williams Crushers has a variety of machines that can perform crushing size reduction like our Roll Crushers Particle Size Conversion Chart Williams Patent Crusher2018年2月1日 In another study to investigate ball size distribution on ball mill efficiency by Hlabangana et al [50] using the attainable region technique on a silica ore by dry milling, a threeball mix of Effect of ball and feed particle size distribution on the milling
.jpg)
Reduction of Fragment Size from Mining to Mineral Processing: A
2022年10月4日 A notable fact is that the energy efficiency of conventional milling is only about 1%, as mentioned in Sect 1 An earlier experimental study indicated that about 80–90% of the energy input of a ball mill was used in heating the material (Schellinger 1951, 1952), and a recent study showed that over 75% of the electrical energy was used to heat the slurry (Bouchard et 2015年6月19日 The basic parameters used in ball mill design (power calculations), rod mill or any tumbling mill sizing are; material to be ground, characteristics, Bond Work Index, bulk density, specific density, desired mill Ball Mill Design/Power Calculation 911Metallurgist2017年9月30日 The ore particle size distribution is an important basis for the evaluation of crushing effect The particle size parameters mainly include the particle area, [300, 600] ranges accounts for about 55 and 38% of the total number of ore particles, and the average diameter of the ore in the Research of Ore Particle Size Detection Based on Image Processing2016年2月26日 The hammer mill is the best known and by far the most widely used crushing device employing the impact principle of breaking and grinding stone Thus far we have described machines which do a portion of their work by impact, but the only machine described in which this action plays an important role was the sledging roll type and particularly the Edison roll crusher Hammer Mill Crusher Grinder 911Metallurgist
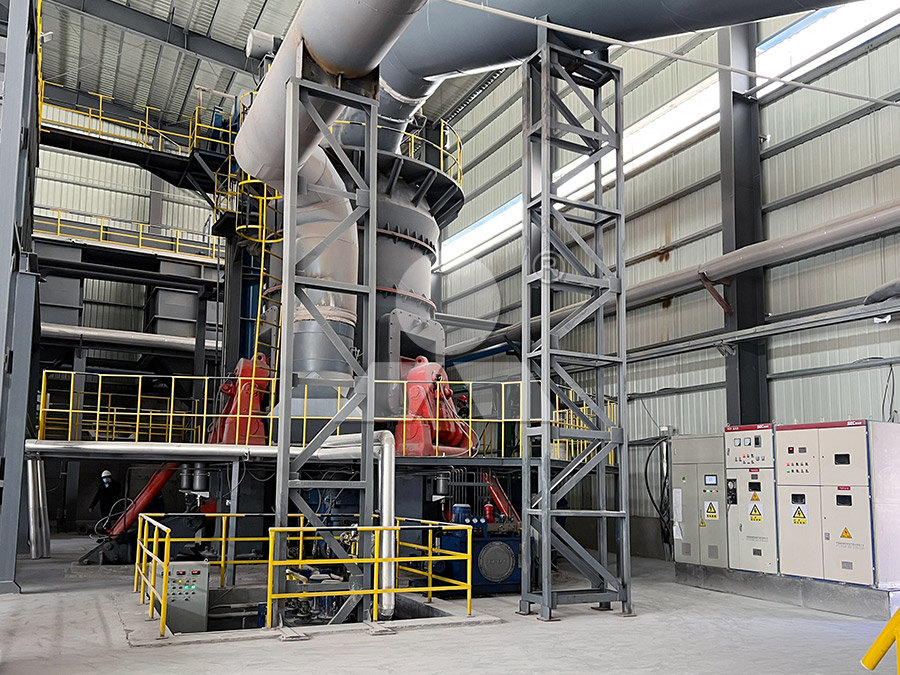
SIZE REDUCTION BY CRUSHING METHODS By ResearchGate
3 Size reduction of ores is normally done in order to liberate the value minerals from the host rock This means that we must reach the liberation size, normally in the interval 100 – 10 micron 2022年1月1日 The product size of an AG mill depends strongly on the nature of the ore being ground Tests must be carried out to determine the competency of the ore and its “natural” particle size distribution Results from pilotplant tests are used to calculate the required mill size and motor power for a particular production minution and classification technologies of iron ore2017年3月4日 Comminution is particle size reduction of m aterials is a type of mill machine that cru shes material by Crushing involves reducing the ore size from various sizes ranging from SIZE REDUCTION BY GRINDING METHODS ResearchGate2024年4月26日 The crushed ore obtained from the crushing stage is typically in larger size fractions and needs to be further processed through screening 2 Screening Screening is the process of separating the crushed ore into various size fractions It involves passing the crushed ore through a series of screens with differentsized openingsIron Ore Processing: From Extraction to Manufacturing

Fractal dimension of crushing products: effects of feed size
2021年8月9日 In all of three types of crushers, the fractal dimensions and crushing rate of the ore were increased with an increase in feeding feed size distribution and by increasing the amount of particles 2023年10月13日 Figure 3 Types of crushing and grinding machinery for laboratory use Different applications, quantity of throughput and size of final products often designate the method employed to grind materials from large scale crushers to finer impact mills Table 2 gives the relative reduction of particle size from original material and the equipment Principles of Sample Preparation by Grinding or Comminution2013年7月15日 For any circuit, whether a crushing circuit, a rod mill, or a closed ball mill circuit, the Work Index always means the equivalent amount of energy to reduce one ton of the ore from a very large size to 100 um The sample was Bond Work Index FormulaEquation 911Metallurgist2019年1月1日 A grain size reduction hammer mill for crushing corn (Zea mays L) was designed depending on variety characteristics and by using computer aided design “ANSYS” softwareDesign and Evaluation of Crushing Hammer mill
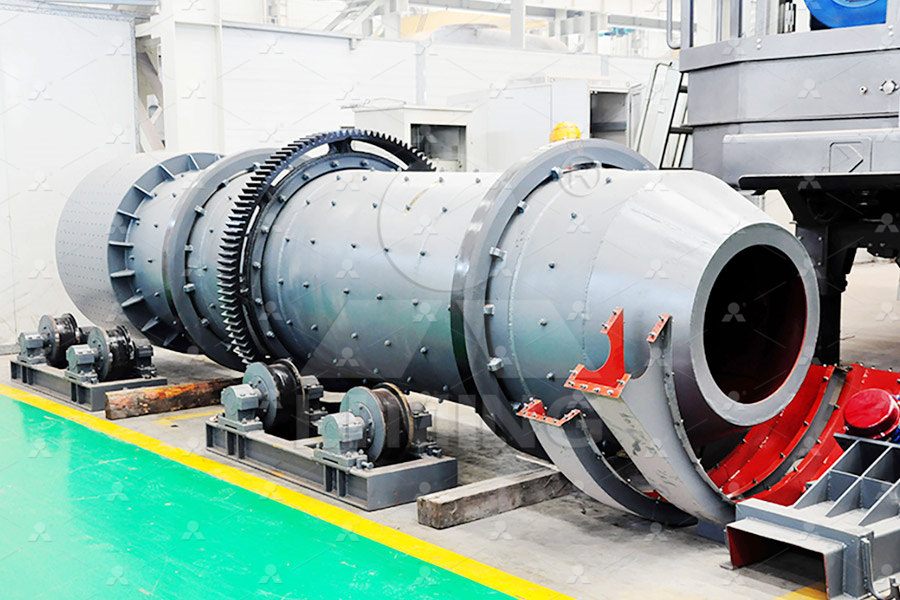
What Is The Process Of Barite? Eastman Rock Crusher
2023年6月27日 The size of the barite ore after crushing is uneven, and the beneficiation equipment generally has its own required input size and size range Therefore, the crushed barite ore after screening can optimize the following 2020年3月20日 Types of mill: Ball mill: Rod mill: SAG mill: Advantages : 1Strong production capacity 2Fine discharging size: 1Uniform particle size 2Simple configuration and low cost: Wide range of feeding size and large crushing ratio: Disadvantages: 1Higher cost 2Be prone to overcrushing: 1Rough output products 2Poor grinding efficiency: 1Large What’s the Difference Between Ball Mill, Rod Mill and SAG Mill?2023年3月16日 Samples used for this study include chalcopyrite and ilmenite ores Feed size was divided into two fractions of (+238 −4) and (+2 −238) millimeters, from which different feeds with different Fractal approach of particle size distribution description of ball While not as widely used as some other types of grinding equipment in copper ore mining, rod mills offer distinct advantages in certain applications due to their efficient operation and ability to produce a specific range of particle sizes Tower Mill The Tower Mill is another type of grinding mill used in the mining industryUnderstanding the SAG Mill in Copper Ore Mining Process
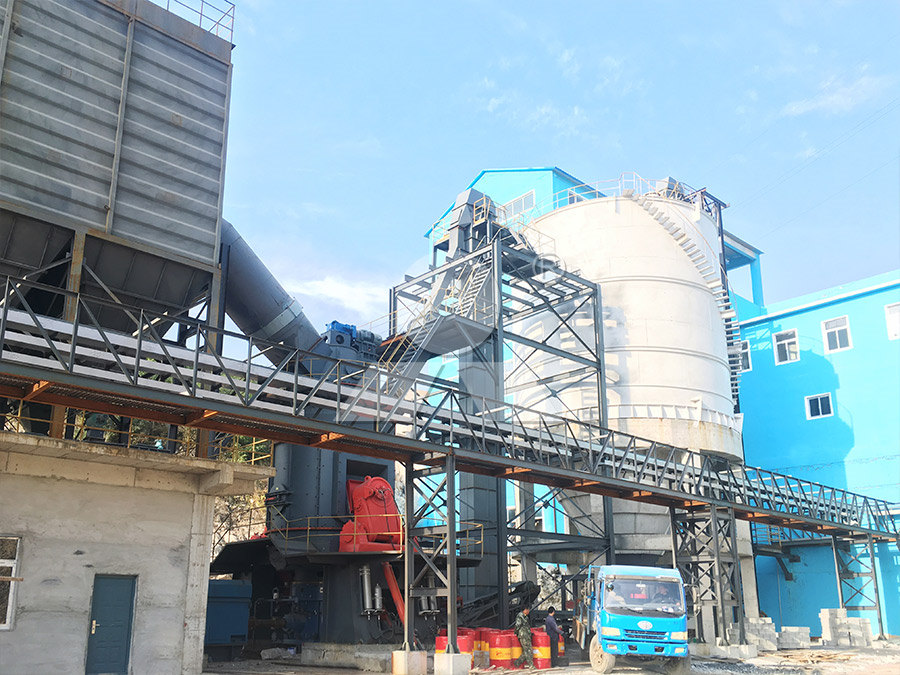
Rock Crushing Rule of Thumb 911Metallurgist
2015年12月17日 For example, a 48 by 60 crusher will have a capacity in the order of 600 tph when crushing ore in a hard the maximum particle size that is normally desired for skip hoisting is obtained when calculations define the efficiency of a fine stagecrush ball mill circuit as 10 to 12 depending on ball mill feed size, and 2023年7月22日 Ore fine crushing is a process of crushing ore blocks with a feeding particle size of 50–150 mm to 5–25 mm, and the maximum crushing ratio of fine crushing is about five The main equipment suitable for fine crushing operations includes a fine crushing jaw crusher, short head cone crusher, highpressure roller mill, etcOre Crushing SpringerLink2024年4月19日 The crushing process is commonly conducted in several stages Each stage of the crushing process implements a different type of crusher to gradually reduce the size of the material The first step is crushing the material by using larger crushers that can reduce the material into smaller sizes that will be used in the next stageTypes of Crushers Explained: Everything You Need to Know JXSCThe largest broken particle size is 1000 * 1200mm Skip to content Menu Aimix’s oretype crusher includes many kinds of ore crusher for sale According to the different crushing forces, the crusher Aimix’s experts will tell you what kind of ore crushing plant should you use in various crushing stages Using Jaw crusher in Ore Crusher PE Series Jaw Type Ore Crusher AIMIX GROUP
.jpg)
SAG Mill Grinding Circuit Design 911Metallurgist
2016年6月6日 For these ore types, a pebblecrushing circuit is tin imperative for efficient circuit operation Such a circuit can counteract the effects of harder ore coarser ore decrease the size of SAG mill required, or rectify poor Comminution Barry A Wills, James A Finch FRSC, FCIM, PEng, in Wills' Mineral Processing Technology (Eighth Edition), 2016 Bond Tests The most widely used parameter to measure ore hardness is the Bond work index WiCalculations involving Bond’s work index are generally divided into steps with a different Wi determination for each size class The low energy Bond Work Index an overview ScienceDirect Topics2018年6月1日 A number of researchers (Deniz, 2012; Bwalya et al, 2014; Petrakis et al, 2016) carried out studies about the effect of feed particle size and grinding media size on the grinding kinetics of different oresKhumalo et al, 2006 postulated that generally larger sized grinding media would break larger particles quicker but a finer product would be obtained by use of Effect of ball and feed particle size distribution on the milling 2018年8月17日 Extreme temperatures, impact velocity, mill load, grinding media, ore types, and applications are some of the factors to be considered while installing new linersGrinding Mills — Types, Working Principle Applications
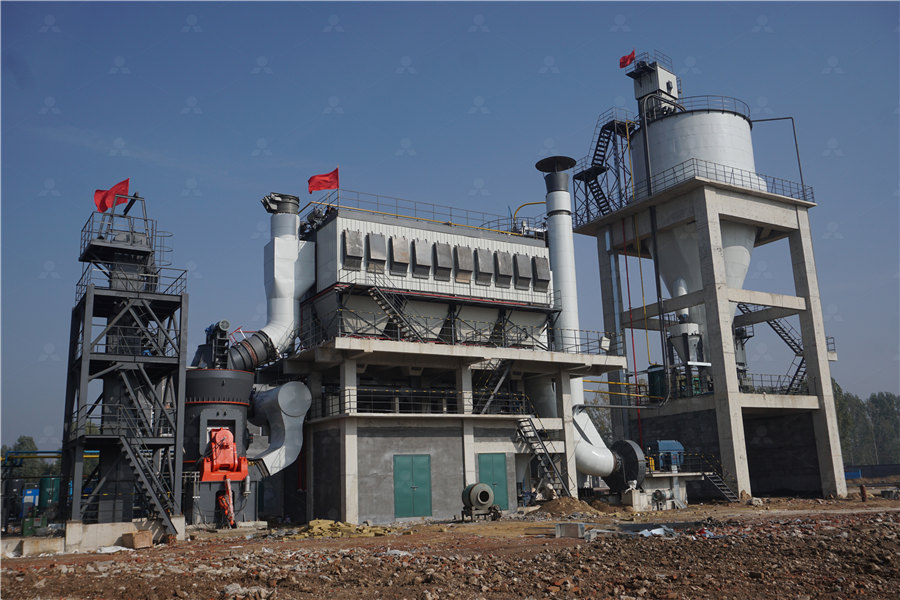
Investigation on Iron Ore Grinding based on Particle Size Distribution
2020年5月28日 where F 80 is 80% feed particle size passing (μm), P 80 is 80% product particle size passing (μm), P i is the size of the mesh selected for the test, and Gpb is the grindability of the undersized product produced per mill revolution (g/rev) After grinding the iron ore samples X, Y, and Z in the BBM, it was recorded that P 80, BWI, and RT varied for each iron ore sample 2024年10月24日 Since t 10 refers to the cumulative yield under the screen of the impact crushing product whose particle size is less than 1/10 of the initial particle size, in order to facilitate the acquisition of t 10 value from the crushed product, the horizontal coordinate in Figs 7–9 is represented by the relative size (x i /x 0), that is, the ratio of the child particle size to the Experimental Study of the Crushing Characteristics of Single Particle finished particle size is the screen Any material that enters the grinding chamber must be reduced to a size small enough to pass through the screen that covers the mill's discharge opening Because of this the screen size generally provides 70% or more of the control over the finished particle sizeIntro to Size Reduction Schutte HammermillCelculaled camel ty16 ' 25 7 I n 0 05 1 15 2 25 Actual capacl tylh' Q Present Eqn + Rose 8 Engllsh Eqn Fig 1 Comparison of calculated capacltles wlth the oata of Hersam (1 9231 for different machlne parameters thereby influencing the degree of compaction of the product The final equation for the capacity of jaw crushers canCapacities and performance characteristics of jaw crushers
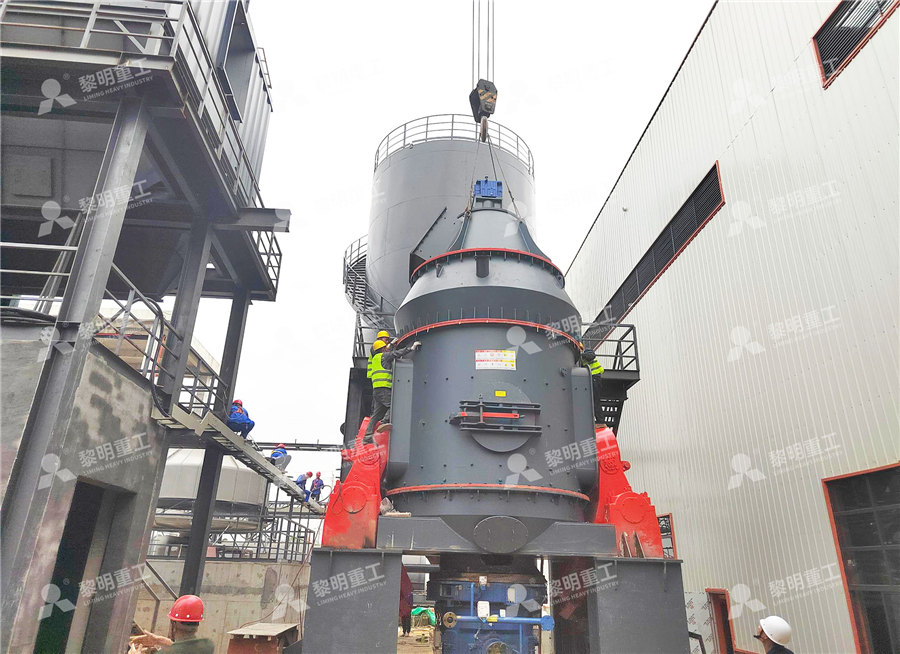
The Complete Guide to Primary Crushing, Secondary Crushing,
2023年2月28日 Learn everything you need to know about primary crushing, secondary crushing, and tertiary crushing in this comprehensive guide Discover the types of crushers used in each stage, their working principles, and the advantages and disadvantages of each process Get answers to frequently asked questions and improve your understanding of the comminution