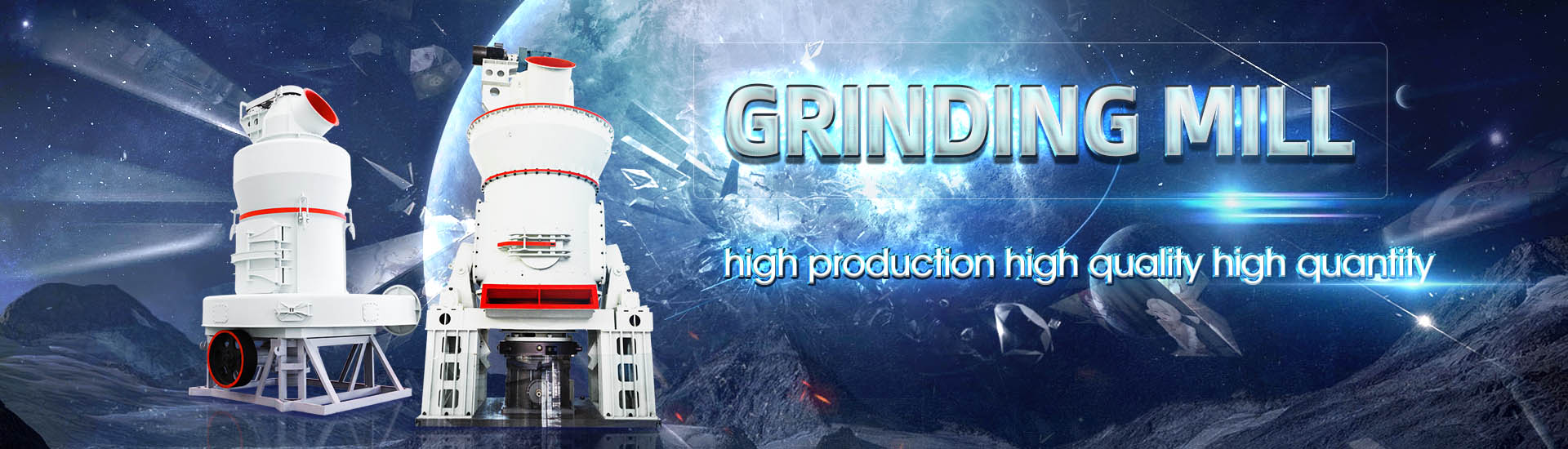
Direct drive manipulator wrist design
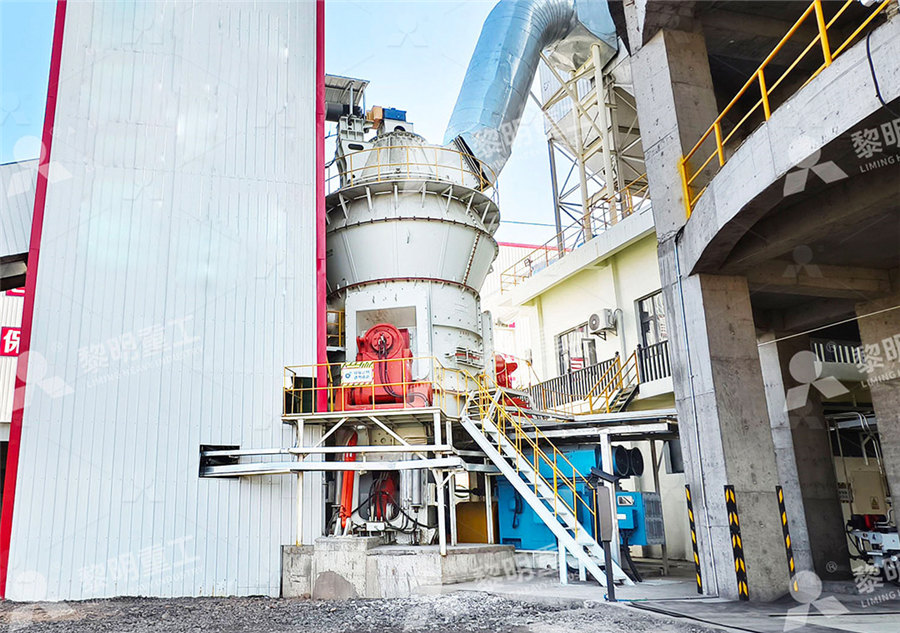
Design of DirectDrive Mechanical Arms Haruhiko Asada
directdrive manipulator is that the motors to drive wrist joints are themselves loads for the motors at elbow joints and they are also loads for the motors at shoulder joints In other2022年8月4日 The effectiveness of the proposed method for pointtopoint positioning and disturbance rejection as well as the controllable stiffness have been experimentally Energy Gradient Descent Method for Actuation of a DirectDrive The design and extensive experimental evaluation of a versatile, lightweight, and lowcost instrumented compliant wrist mechanism which can be mounted on any rigid robotic Position sensing wrists for industrial manipulators Semantic Scholar1989年1月1日 A threedimen sional force sensor (Kistler, type 9251 A) is mounted at the wrist of the manipulator to measure the forces at the wrist coordinate The end effector has a hemi Design and analysis of the statically balanced directdrive robot
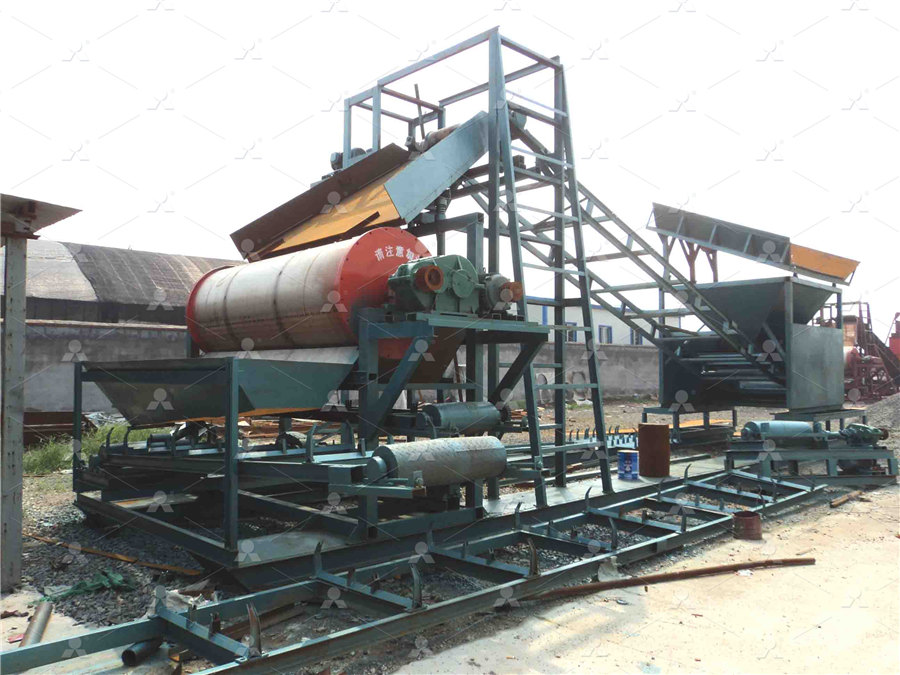
Design of a compact statically balanced directdrive manipulator
This paper addresses the conceptual design of directdrive manipulators which have good promise for high speed, high precision manipulation In the design methodology presented, the Directdrive manipulators are highly sensitive to the linear and nonlinear inertial interactive forces when the actuators are mounted between adjacent links This paper presents effective design Dynamic decoupling and control of a directdrive manipulatorWe introduce the concept of a remote directdrive (RDD) manipulator, in which every motor is located in the base, connected to remote joints via a lowfriction hydrostatic transmission We A FloatingPiston Hydrostatic Linear Actuator and RemoteDirect In this paper, the static and dynamic design of the 5barlinkage manipulator is analysed A technique is proposed whereby the motor torque requirements may be reduced to a fraction of On the design of a direct drive 5barlinkage manipulator
.jpg)
Prosthetic and robotic wrists comparing with the
The wrist prosthesis system developed by Abd Razak et al [Reference Razak, Osman, Gholizadeh and Ali 49], directly driven by two servo motors, can notably generate torques that are comparable to that of a healthy adult wrist, though The directdrive manipulator shows a superior performance over conventional systems as a result of fast actuator dynamics, low friction and no mechanical backlash The experiments are conducted to investigate the force speed of response and steady state behavior, impact control and surface following performanceForce control of directdrive manipulators for surface followingBecause of elimination of the transmission systems, and consequently backlash, the control and performance analysis of direct drive arms is more straightforward than the nondirect drive arms (not necessarily "easier") SUMMARY A practical architecture, using a fourbarlinkage, is considered for the University of Minnesota direct drive rotot This staticallybalanced direct Statically balanced direct drive manipulator Semantic Scholar1990年10月1日 A novel 3 DOF (RRR) directdrive manipulator is proposed and analyzed, which has an advantage over many currently known direct drive manipulators for achieving two desirable mechanical features, namely: static balancing and compactness (smaller driven inertias) SUMMARY This paper addresses the conceptual design of directdrive manipulators Design of a compact statically balanced directdrive manipulator
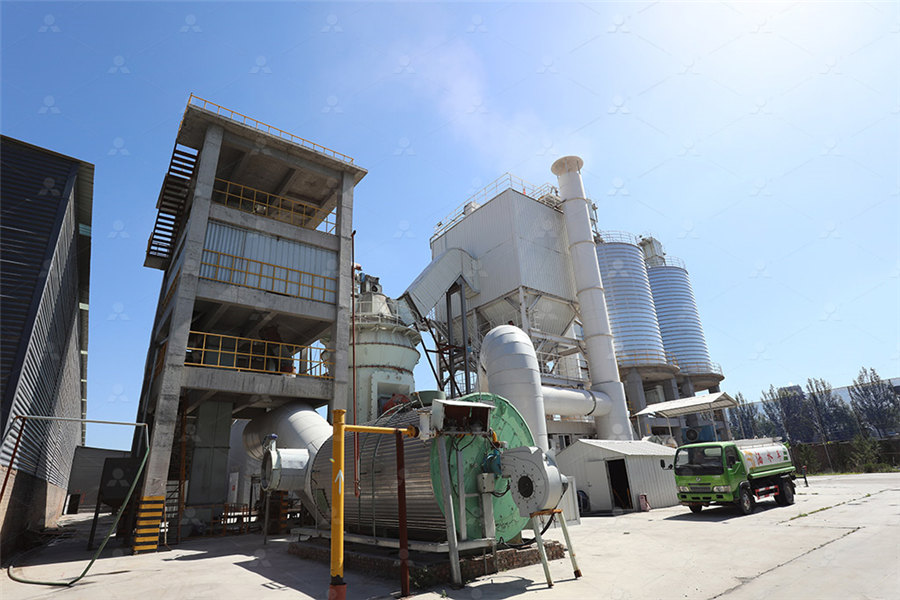
(PDF) Design of DirectDrive Mechanical Arms ResearchGate
2003年2月17日 A directdrive robotic manipulator (CMU DD Arm) is being developed at CarnegieMellon University This paper describes the design concept and theory of this new mechanical arm based on the direct A new approach to manipulator link mechanism design is presented, where a closedloop fivebarlink mechanism is applied to the directdrive arm, and the link dimensions arc optimized in order to acheive appropriate force and speed ranges at the arm tip without using reducers ExpandKinematic and static characterization of wrist joints and their 2019年5月20日 Fig 1: The DDHand executing the smack and snatch behavior The manipulator is uncertain of the object pose and the table directdrive actuation in endeffector design were subsequently explored [26, 12, 38, 23, 10] but failed to pick up momentum due to lacking torque density in motorsDirect Drive Hands: ForceMotion Transparency in Gripper DesignDirectdrive manipulators are highly sensitive to the linear and nonlinear inertial interactive forces when the actuators are mounted between adjacent links This paper presents effective design methods for articulated directdrive arms A new approach is developed for arm linkage design The goal is to simplify the controller design by reducing the effects of complicated manipulator Dynamic decoupling and control of a directdrive manipulator
.jpg)
On the design of a direct drive 5barlinkage manipulator
2009年3月9日 The design also lends itself to the use of direct drive motors However, these motors must be capable of providing a high continuous torque to counter gravitational loading in the conventional manipulator design In this paper, the static and dynamic design of the 5barlinkage manipulator is analysed2019年4月7日 Unconstrained automation using QuasiDirect Drive actuation The Blue manipulator is a 7 DegreeofFreedom robotic arm that is humansized, compliant, has a 2kg payload, and can cost less than QuasiDirect Drive for LowCost Compliant Robotic ManipulationWe introduce the concept of a remote directdrive (RDD) manipulator, in which every motor is located in the base, connected to remote joints via a lowfriction hydrostatic degrees of freedom and wrist mechanisms The result of the design and manufacturing efforts reported here is a compact, lowfriction, lowimpedence, hybrid hyA FloatingPiston Hydrostatic Linear Actuator and RemoteDirectDrive A Statically Balanced Direct Drive Manipulator H Kazerooni S Kim The productivity Center and the Mechanical Engineering Department University of Minnesota Minneapolis, MN 55455 H, Kanade, T, "Design of Direct Drive Mechanical arms", ASME Journal of Vibration, Acoustics, Stress, and Reliability in Design, vol 105, July 1983, pp 312 A Statically Balanced Direct Drive Manipulator
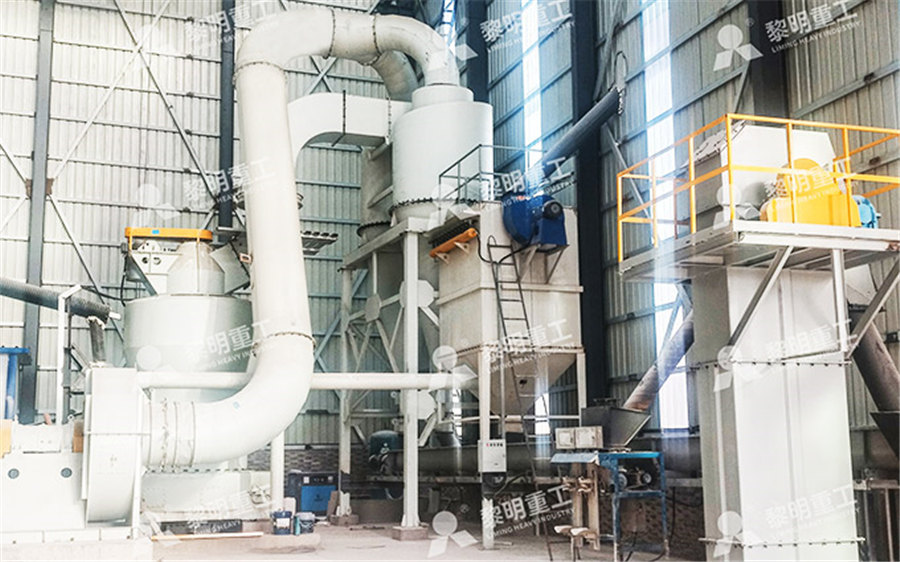
Design of a Spherical Wrist with Parallel Architecture: Application
Chablat D et Wenger P, “Design of a Spherical Wrist with Parallel Architecture: Application to Vertebrae of an Eel Robot”, Proc IEEE Int Conf Rob and Automation, Barcelone, 2326 Avril 2005 Design of a Spherical Wrist with Parallel Architecture: Application to Vertebrae of an Eel Robot Damien Chablat and Philippe Wenger2006年1月1日 D S Seltzer, "Compliant robot wrist sensing for precision assembly", Robotics: Theory and Application, P161–168, 1986 Google Scholar H Kazerooni, and J Guo, "Directdrive, active compliant endeffector" Proceedings of the IEEE International Conference on Robotics and Automation, P758–766, 1987Hybrid position force control of robot manipulator with anIn the design methodology presented, the procedure begins by considering the kinematic aspects and ends by configuring manipulator structures with promising kinematic and dynamic characteristics Based on the conceptual design considerations, a novel 3 DOF (RRR) directdrive manipulator is proposed and analyzedDesign of a compact statically balanced directdrive manipulatorThis book describes the design concept and discusses the control issues related to the performance of a directdrive robot, specifically, a directdrive mechanical arm capable of carrying up to 10 kilograms, at 10 meters per second, accelerating at 5 G (a unit of acceleration equal to the acceleration of gravity)DirectDrive RobotsTheory and Practice Books Gateway MIT
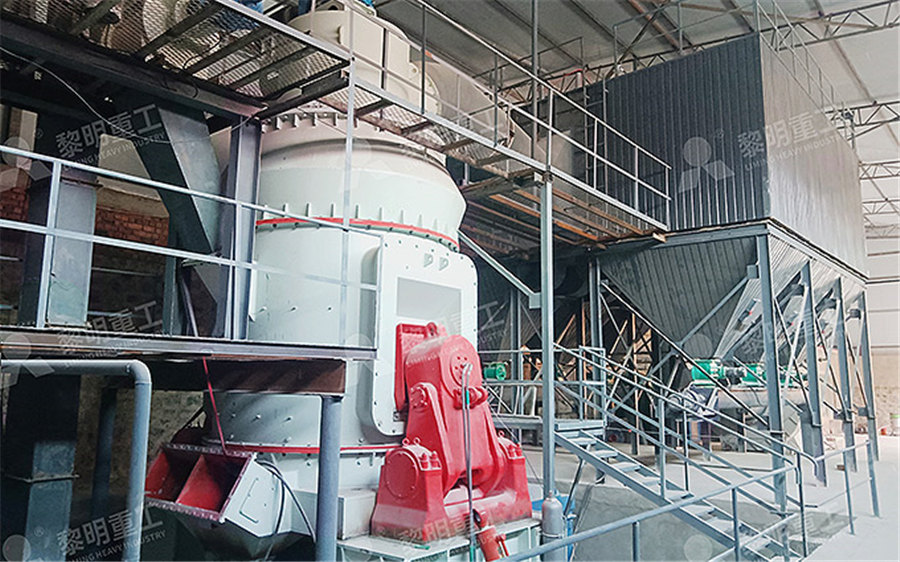
A novel spherical parallel manipulator: forward position problem
2008年9月8日 A novel spherical parallel manipulator: forward position problem, singularity analysis, and isotropy design Volume 27 Issue 5 Skip to main content Accessibility help We use cookies to distinguish you from other users and to provide for a directdrive robot manipulator is proposed, and an adequate learning control method for the directdrive robot manipulator is discussed THE MECHANISM OF DIRECTDRIVE ROBOT MANIPULATOR Fig1 shows a typical construction of a serial drive mechanism with three 127 degrees of freedom The weight of motor3DYNAMICS OF THE FIVEBARLINK PARALLEL DIRECT DRIVE ROBOT MANIPULATOR1989年1月1日 A threedimen sional force sensor (Kistler, type 9251 A) is mounted at the wrist of the manipulator to measure the forces at the wrist coordinate The end effector has a hemi spherical shape Kanade, T: Design of direct drive mechani cal arms ASME J Vibration, Acoustics, Stress, Reliabi lit)', Design 105: 312316, July Design and analysis of the statically balanced directdrive robot 2020年3月3日 In order to ensure good dynamic characteristics, servo valve is usually adopted as the drive part of Stewart manipulator which causes huge power consumption, while direct drive electrohydraulic servo system has the advantages of energy saving, simple structure, convenient installation, and low failure rate But its dynamic characteristics are so poor that it can only be PD Plus Dynamic Pressure Feedback Control for a Direct Drive
2FD{P}PC]854]XQ.jpg)
Analysis, design and control of directdrive manipulators
In this paper, a design and optimization approach for a 2dof manipulator based on parallelogram mechanism for high dynamic application is proposed and it shows that the optimized mechanism has an approximate decoupled dynamics structure, and each active joint could be regarded as a linear SISO systemAbstract: Dexterous, serialchain motordriven robotic arms have high moving mass, since most of the actuators must be located in the arm itself This necessitates high gear ratios, sacrificing passive compliance, backdrivability, and the capacity for delicate motion We introduce the concept of a remote directdrive (RDD) manipulator, in which every motor is located in the A FloatingPiston Hydrostatic Linear Actuator and RemoteDirectDrive 2022年5月1日 A robot called Universal Haptic Drive (UHD) was developed for the rehabilitation of the arm, forearm, and wrist by Oblak et al [4] Masia et al [5] designed a threeDoF exoskeleton robot that covers movements of the wrist and forearm This design was improved and developed by Squeri et al [6] byA portable lowcost 3Dprinted wrist rehabilitation robot: Design Request PDF On May 1, 2019, David V Gealy and others published QuasiDirect Drive for LowCost Compliant Robotic Manipulation Find, read and cite all the research you need on ResearchGateQuasiDirect Drive for LowCost Compliant Robotic Manipulation
.jpg)
Manipulatormechanism design Seoul National University
Section 82 Basing the design on task requirements 231 The breadth of engineering disciplines encompassed forces us to restrict our attention only to the design of the manipulator itself In developing a manipulator design, we will start by examining the factors likely to have the greatest overall effect on the design and then consider more3 in the wrist) as shown in Figure 1, can better mimic Unconstrained automation using QuasiDirect Drive actuation The Blue manipulator is a 7 DegreeofFreedom robotic arm that is humansized, compliant, B Defining a Useful Robotic Manipulator We define a design paradigm that enables usefula,QuasiDirect Drive for LowCost Compliant Robotic Manipulation2024年10月8日 The design leverages the high stiffness provided by the geared motors and the high forcesensing capability of the direct drives When the geared motors move synchronously with their directdrive counterparts, the manipulator mimics a Delta robot's spatial translation, while the direct drives double as highperformance force sensorsA SixAxis Asymmetric Parallel Manipulator CoDriven by DirectDrive 2009年3月9日 Takase, K, Hasegawa, T and Suehiro, T, “Design and Control of a Direct Drive Manipulator” Proceedings of the International Symposium on Design and Synthesis, Tokyo, Japan, 333 – 338 (07 1984)Google ScholarStatically balanced direct drive manipulator Cambridge Core
.jpg)
Mechanical Design for WholeArm Manipulation Springer
well have begun to design for good backdrivability For example, in order to simplify the dynamic equations for calculating the actuator torques in the trajectory control of a directdrive arm, Asada [Asada 84) redesigned a manipulator so that the inertia properties at its end tip would be nearly isotropic over a large portion of its workspaceA directdrive arm is a mechanical arm in which the shafts of articulated joints are directly coupled to the rotors of motors with high torque Since the arm does not contain transmission mechanisms between the motors and their loads, the drive system has no backlash, small friction, and high mechanical stiffness, all of which are desirable for fast, accurate, and versatile robots First, the [PDF] Control of a DirectDrive Arm Semantic Scholar2004年12月21日 This paper proposes design and implementation of a digital control system to drive a twolink robotic manipulator Our process adopting a completely digital control system design, to avoid using Digital control of direct drive robot manipulators ResearchGate2012年12月1日 The automatic updown material manipulator wrist requirements compact structure, rational layout The typical wrist structure has a variety of, this design wrist structure for step motor drives a turbine worm movement of the structure, main function is to drive the PAWS, make its can accurately to grab parts and placed parts Operation mode for step motor drive The Automatic UpDown Material Manipulator Wrist 3d Design
.jpg)
A Novel 3DOF Spherical Hybrid Mechanism for Wrist Movement: Design
2023年10月21日 It is the prerequisite work to design a mechanism that can drive wrist motion of obtaining wrist stiffness information through perturbation method Human wrist has three DOFs, i e, flexion and extension (FE), radial and ulnar deviation (RUD), pronation and supination (PS) (see Fig 1 ) and the range of max and activities of daily living (ADLs) wrist motion is listed in basic configuration of directdrive manipulators is shown Second, we present a design theory for direct drive manipulators by using a simple kinematic model We then find an arm structure most suitable for direct drive Finally, we describe a directdrive manipulator developed at CarnegieMellon University, and verify the theoretical result 2DESIGN CONCEPT OF DIRECTDRIVE MANIPULATORS USING 1991年12月1日 A technique is proposed whereby the motor torque requirements may be reduced to a fraction of those required in the conventional design, while simultaneously retaining the advantage of a decoupled inertia matrix SUMMARY The 5barlinkage manipulator configuration is well suited to many industrial robotic applications Aside from kinematic On the design of a direct drive 5barlinkage manipulator2021年1月7日 This article presents the design and validation of a regression model for the identification of dynamic parameters in manipulator robots The model exhibits implementation advantages as it is based on the acquisition of position, speed and voltage data from the actuator in each joint rather than on the calculation of acceleration and torque Actuators can be direct Design and validation of a dynamic parameter identification
.jpg)
Synthesis and dynamics of statically balanced directdrive
1991年1月1日 The resultant manipulators arc called directdrive manipulators The basic design concept of a directdrive manipulator was first established in 1981 [I, 2] Since then several directdrive manipulators have been built Ref [3] presents a survey of directdrive manipulator developments and discusses their design and control issues2016年8月1日 As a preliminary design and study, an overall design of the proposed flexible manipulator is suggested and identification of the direct drive is performed Index Terms – Direct drive, flexible Preliminary Design and Study of a Bioinspired Wire2022年8月1日 This paper presents an energy gradient descent method for actuating a spherical robotic wrist which is capable of providing threeDOF rotations in one jointEnergy Gradient Descent Method for Actuation of a DirectDrive 2022年3月15日 Thirdly, when the underwater multiDoF hydraulic manipulator moves in viscous fluid, the drag and lift force generated by the fluid will interact with the hydraulic manipulator directly which leads to stronger external disturbance (McMillan et al, 1995)In order to suppress strong external disturbance factors and modeling errors, Yao and Wang (2012) proposed a Adaptive robust control design for underwater multiDoF
.jpg)
Energy Gradient Descent Method for Actuation of a DirectDrive
of a DirectDrive Spherical Robotic Wrist Mengke Li, Yaqing Deng, and Kun Bai(B) Huazhong University of Science and Technology, Wuhan , China Abstract This paper presents an energy gradient descent method for actuating a spherical robotic wrist which is capable of providing threeDOF rotations in one joint