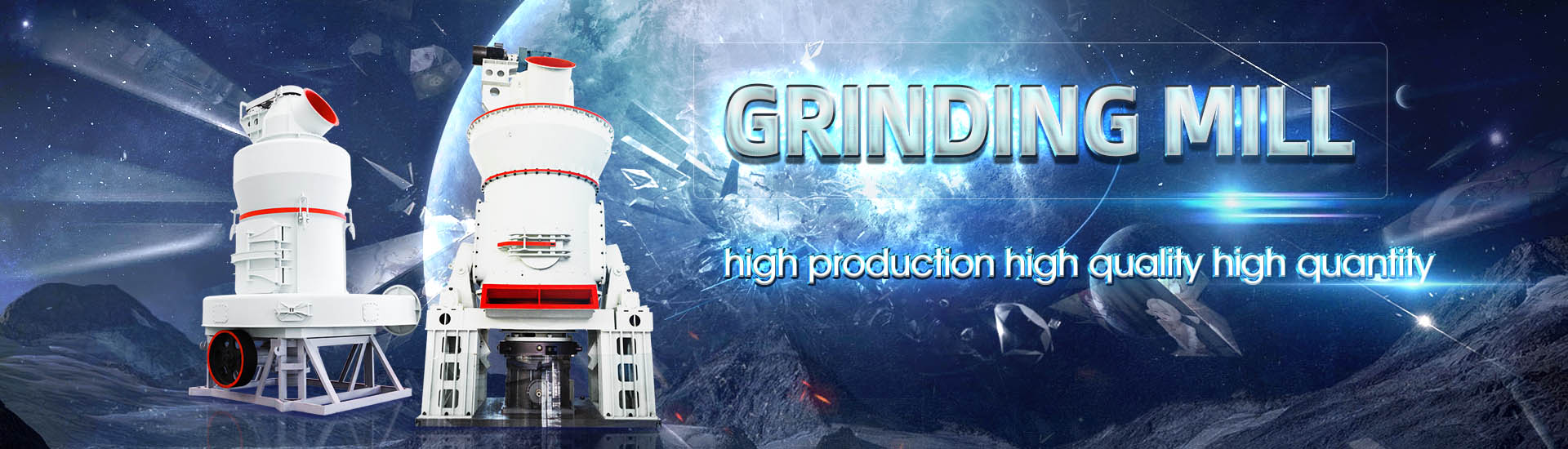
Use rotary kiln waste heat to increase the concentration of waste acid
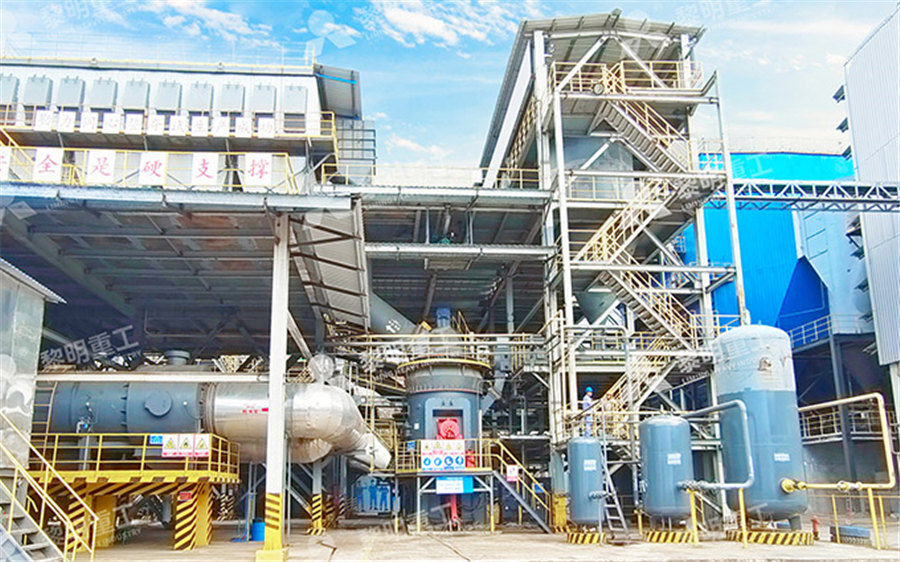
Design requirements and performance optimization of waste heat
2016年2月1日 In this paper, we propose a heat transfer model to analyze the required heat loss rate along rotary kilns Applying this model together with experimental measurements gives the required heat loss rates of nine regions in a rotary kiln, which are the required heat transfer “ Waste heat recovery and utilization of cement rotary kiln based on biomass energy,” BioResources 18 (2), 30563072 A rotary kiln is a central piece of equipment for the Waste heat recovery and utilization of cement rotary kiln based on 2024年2月15日 With the actual operation data of a hazardous waste rotary kiln incineration project over 77 weeks in the case company, the study analysed the incineration performance Improving longterm operation performance of hazardous waste 2021年1月1日 Depending on their applications, heat losses from the shells of rotary kilns account for 3 to 25% of the total heat input Over the hottest zone of the kiln shell, an annular duct with aImproving design and operating parameters of the
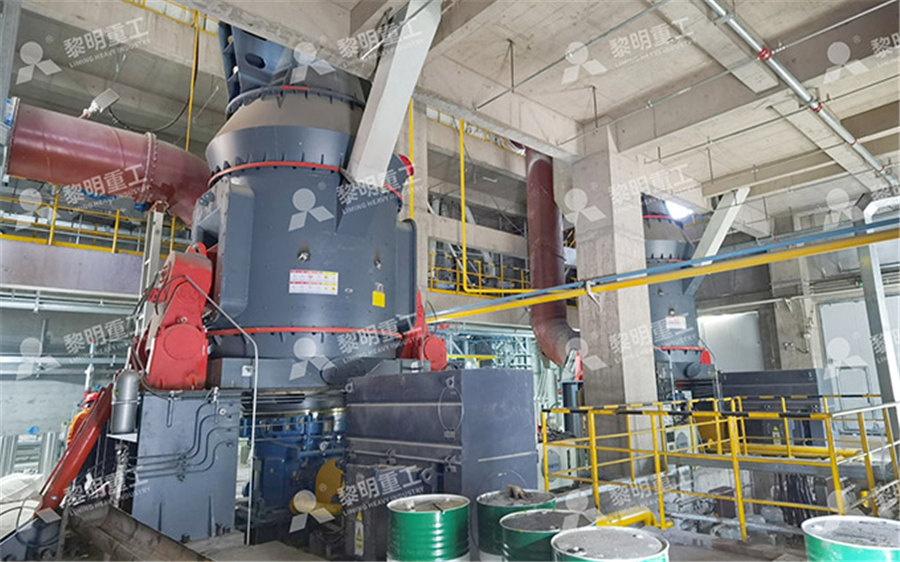
Enhancing the Performance of a Hazardous Waste Incineration
2024年2月3日 Rotary kilns used in the cement industry and metallurgy can also be fed with waste in the socalled form of alternative fuel A significant difference in the design of the kiln, 2019年4月18日 From a new perspective, further research should be focused on a comparative analysis of the rotary kiln and the cement kiln, full life cycle assessment of the impact factors Hazardous waste incineration in a rotary kiln: a reviewRotary kilns are pyroprocessing devices used to raise materials to a high temperature in a continuous process [1] The kilns are widely applied in various technological processes such asIMPROVING DESIGN AND OPERATING PARAMETERS OF THE 2022年8月17日 In this paper, a 40 t/d counterflow rotary kiln incineration system owned by a Jiangsu environmental protection company was researched The software Aspen Plus was Simulation research of a counterflow rotary kiln hazardous waste
.jpg)
Rotary kilns coprocessing hazardous wastes ScienceDirect
2022年1月1日 The increase of air leakage in the kiln head provides more sufficient oxygen in the rotary kiln, and thereby strengthens the combustion efficiency in the furnace, and advances 2018年6月1日 High temperature WHR consists of recovering waste heat at temperatures greater than 400 °C, the medium temperature range is 100–400 °C and the low temperature range is for temperatures less than 100 °C [2]Usually most of the waste heat in the high temperature range comes from direct combustion processes, in the medium range from the exhaust of Waste heat recovery technologies and applicationsThe main costs for modern rotary kiln incinerators are refractory brick maintenance Every 1–3 years, parts or the entire brick lining has to be renewed due to refractory wear and tearFigure 1: General sketch of the rotary kiln and the 2021年9月26日 The rotary kiln incinerator used in this experiment was developed from combustion furnace technology in Japan and was designed to achieve the highest possible efficiency for incineration systems used to dispose of infectious waste The several recent improvements to the incinerator system in this study are described below and shown in Figure1Treatment of Infectious Waste through the Application Rotary Kiln
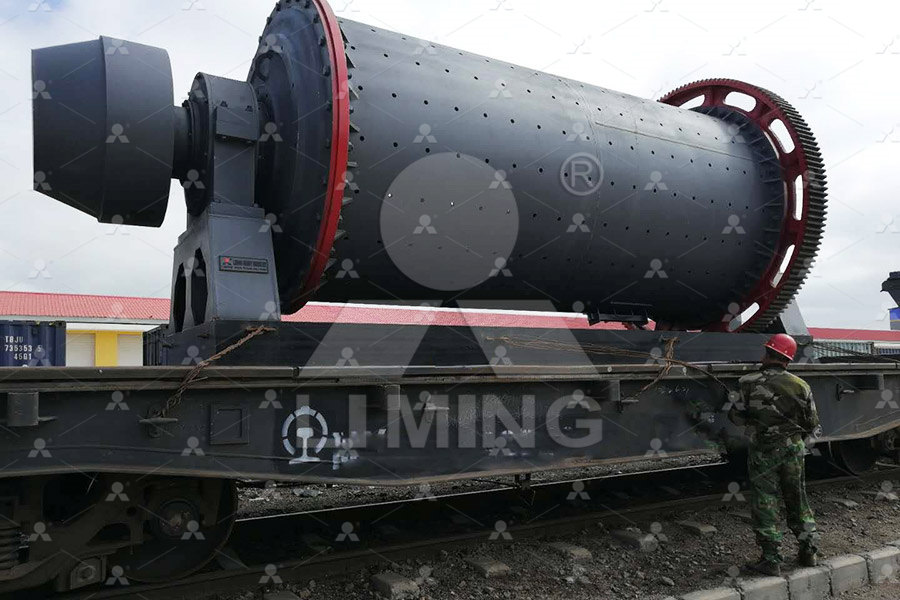
Waste heat recovery and utilization of cement rotary kiln based
Zhu (2001)’s study was on flue gas waste heat, waste heat from clinker, kiln body heat loss using, and processing recycling waste heat in the rotary kiln cement production line links, which are a variety of ways that waste heat is utilized The rotary kiln shell waste heat recovery that was proposed for the development of low energy 2020年12月1日 The VAM system used had a capacity of 70TR (tons of refrigeration), and total heat recovery was over 70 kW (1680 kWh/day) A study to evaluate the potential recover of waste heat from the kiln Utilization of cement rotary kiln waste heat for calcination of 2021年6月5日 The heat energy produced during combustion of solid waste can be used for clinkering and the CO 2 emitted from combustion can be employed as strength activator or pretreatment agent However, the cement manufactured with MSWI FA should address potential issues of chemical compatibility and longterm physical performanceTreatment of municipal solid waste incineration fly ash: Stateof Utilization of waste heat from rotary kiln for burning clinker in the cement plant Dust concentration , Surface temperature, Velocity were identified A detailed analysis of Grate cooler, Using the waste heat as a power generation source, increases the energy efficiency of the process and decreases the thermal energy lossesUtilization of waste heat from rotary kiln for burning clinker in
.jpg)
Utilization of waste heat from rotary kiln for burning clinker
2016年1月1日 Waste heat recovery is a prominent option to increase the energy efficiency of the rotary kiln furnace in the RKEF process This option reduces fuel consumption and contributes to mitigating the The rotary kiln is followed by a secondary combustion chamber with a separate burner that burns off any residual hazardous components remaining in the flue gas stream after the rotary kiln Waste with a high heating value can be used as a fuel source for the kiln itself, or for the secondary combustion chamber to further improve the Rotary Kiln Incinerators on the Rise in Waste Management2019年4月18日 Hazardous waste output in the world is increasing every year To achieve higher efficiency and lower pollution, the incineration technology for hazardous waste needs to be studied furtherHazardous waste incineration in a rotary kiln: a review2014年12月17日 The first objective of any waste policy should be to minimize the negative effects of the generation and management of waste on human health and the environment Reuse and recycling of waste, although of high priority in the waste hierarchy, is not necessarily always the best treatment method In the case of hazardous waste containing toxic Incineration of Hazardous Waste: A Sustainable Process?

Utilization of waste heat from rotary kiln for burning clinker
a corresponding author: sztekler@agh Utilization of waste heat from rotary kiln for burning clinker in the cement plant Karol Sztekler1,a, Maciej Komorowski2, Milena Tarnowska3 and Łukasz The alarming rate at which infectious waste is growing was an unsolved problem worldwide before the pandemic, and it has only gotten worse It is especially prominent in the medical services, owing to the improper use or the lack of Treatment of Infectious Waste through the Application 2 waste heat from the surface of rotary kilns While the former has attracted much of the attention of the industries and waste heat recovery plants for flue gases are installed by cement IMPROVED WASTE HEAT RECOVERY THROUGH SURFACE OF KILN the heat losses of the clinker burning process In the Fig 1 the sources of waste energy from the rotary kiln and possible ways of its use are shown Till now common in the cement industry process of waste heat use (particular enthalpy of flue gases and excess air) is to use it for raw materials, coal and slag dryingThe thermoelectric generators use for waste heat utilization from
.jpg)
Technoeconomic assessment of a rotary kiln shell radiation waste heat
2021年2月1日 In a study exploring the economic feasibility of a waste heat recovery system that captures radiation emitted from the surface of a rotary kiln [45], the authors determined that for markets with Thus, the current study proved significant waste heat recovery potential from kiln shell of a cement industry which can be further utilized for any onsite application Keywords: Waste heat recovery, Kiln, Heat Recovery System, Experimental Analysis, Cement industry 1An Experimental Analysis of Waste Heat Recovery Potential from A Rotary 2013年8月1日 A range of different reactors, such as fixedbed (batch), screw kiln, rotary kiln, vacuum and fluidisedbed have been used for pyrolysis of waste tyres Table 2 shows the range of pyrolysis reactors used to research the pyrolysis of waste tyres and the yields of oil, char and gas from the processPyrolysis of waste tyres: A review ScienceDirectThe 2 rotary kiln incinerators at the Indaver site in Antwerp, Belgium, each with a capacity of 60 kton/year, are used to thermally process hazardous waste that is notIncineration of Hazardous Waste: A Sustainable Process?
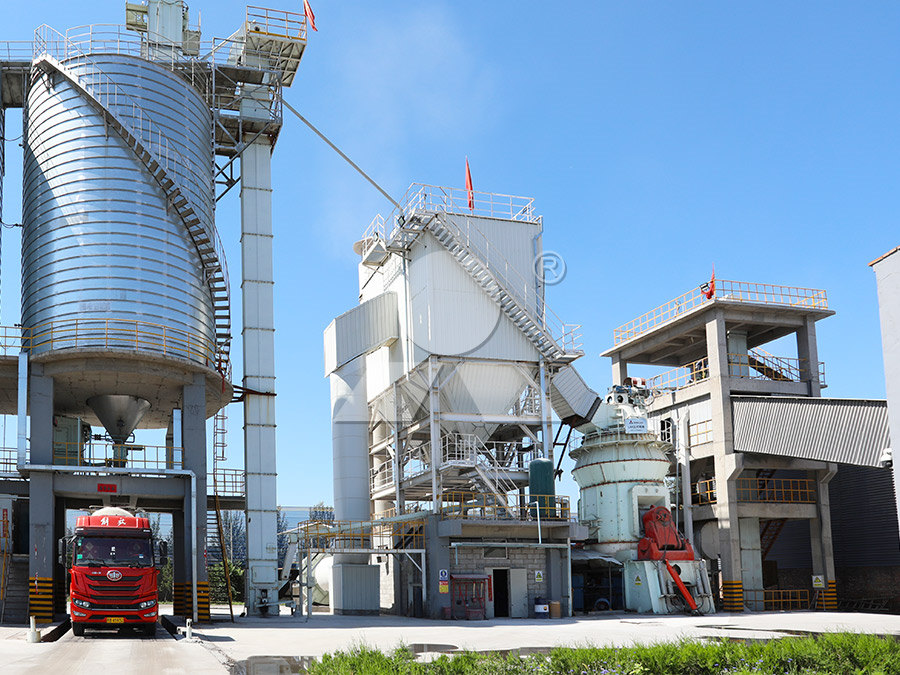
(PDF) History of the rotary kiln Fathi Habashi Academia
THE ROTARY KILN IN THE METALLURGICAL INDUSTRY About 1900, various metallurgists were experimenting with the rotary kiln for nodulizing fluedust, fine iron ores, etc Edison conducted experiments, for example, on the fine concentrates obtained from his magnetic separators Within a few years plants were established for this purpose2023年2月25日 The rotary kiln is used in many solid processes, including drying, incineration, heating, cooling, humidification, calcination and reduction This widespread application can be attributed to factors such as the ability to handle varied loads, with large variations in particle size [1]The rotary kiln is a slightly inclined steel cylinder that rests on supports (bearing rollers) Rotary kiln process: An overview of physical mechanisms, models Download scientific diagram Process scheme of the rotary kiln for hazardous waste incineration (including input and output flows measured, as well as the system boundary used for the Process scheme of the rotary kiln for hazardous waste process heat are a mix of fossil fuels (mainly petcoke, coal and oil), waste fuels and biomass While biomass usage has tripled since 2007, it currently only accounts for 16% of the total fuel mix in the EU (Figure 1) The coprocessing of fuels (use of alternative fuels, such as waste and biomass) currently represent nearlyDeep decarbonisation of industry: The cement sector Europa
.jpg)
Modeling of the Thermochemical Conversion of Biomass in Cement Rotary Kiln
2020年3月28日 Abstract Because of the depletion of fossil fuels and because of its increasing cost, waste has been used as alternative fuels in cement rotary kilns for several years In order to fulfil the requirements of environmental protection and quality of the final product, it is necessary to understand and quantify the different processes occurring in the kiln The aim of our work is increase the distance between the kiln and the recuperator, and (ii) promote heat transfer to the air in 4 the outer annulus, which does not have the problem of eccentricity and can be narrowed IMPROVING DESIGN AND OPERATING PARAMETERS OF THE RECUPERATOR FOR WASTE 2021年9月26日 Therefore, using the proposed rotary kiln incineration method modified with addon ozone is suitable for use in the elimination of infectious waste in that it drastically reduces air pollution and Treatment of Infectious Waste through the Application Rotary Kiln a corresponding author: sztekler@agh Utilization of waste heat from rotary kiln for burning clinker in the cement plant Karol Sztekler1,a, Maciej Komorowski2, Milena Tarnowska3 and Łukasz Posak4 1,a AGH University, Faculty of Energy and Fuels, Mickiewicza Av 30, 30059 Krakow, Poland 2 AGH University, Faculty of Energy and Fuels, Mickiewicza Av 30, 30059 Utilization of waste heat from rotary kiln for burning clinker
.jpg)
Thermal cotreatment of combustible hazardous waste and waste
2016年9月1日 Process scheme of the rotary kiln for hazardous waste incineration (including input and output flows measured, as well as the system boundary used for the investigations)2020年8月30日 Abstract The recovery and reuse of waste heat offers a significant opportunity for any country to reduce its overall primary energy usage Reuse of waste heat improves the ambient air quality by reducing both industrial pollution and greenhouse gas emissions from industries This paper presents an estimation of thermal waste heat potential in five energy Estimation of waste heat and its recovery potential from energy 2006年9月21日 Reuse of the fly ash from the municipal solid waste incinerator (MSWI) is a policy of Taiwan EPA However, the fly ash is often classified as a hazardous waste and cannot be reused directly because the concentrations of heavy metals exceed the TCLP regulations The main objective of this study is to investigate the continuous sintering behavior of fly ash with a Thermal treatment of the fly ash from municipal solid waste incinerator 2022年2月1日 Nevertheless, to keep away from cross contamination, plate heat exchanger and heat pipe systems are used to transfer heat from one source with different temperature ranges, while heat pumps appears good for lowtemperature waste heat recovery, as it gives the capability to upgrade waste heat to a higher temperature and quality (Khordehgah et al, 2018)A recent review on waste heat recovery methodologies and
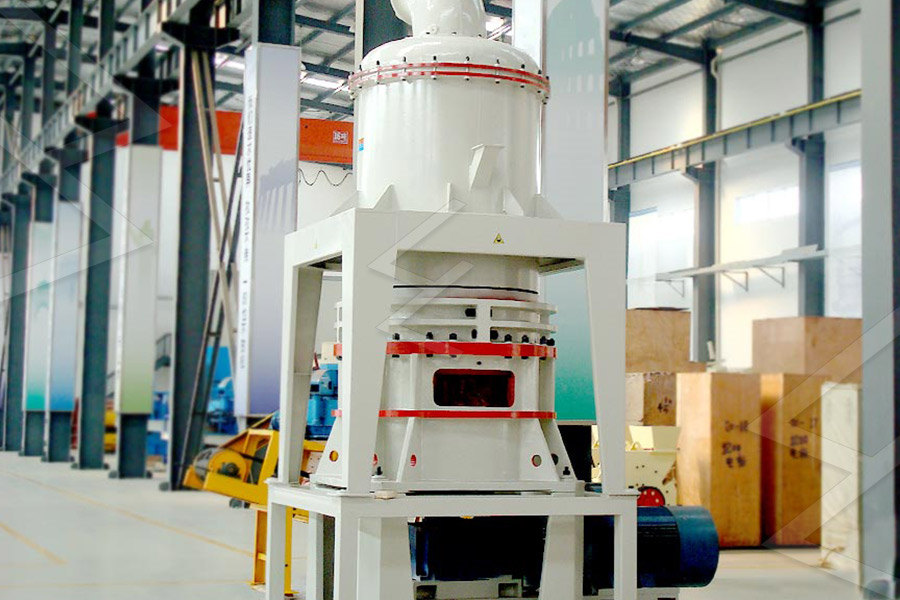
(PDF) Evaluation of waste heat recovery technologies
2020年8月1日 In this work, the waste heat obtained from the cooling of a hightemperature gas effluent from the rotary kiln in a Colombian cement plant is analysed for its potential use either to dry wet raw 2020年12月30日 The aim of this study was to review the significant of waste heat recovery technologies as means of achieving sustainable energy development Most developing nations of the World are faced with (PDF) WASTE HEAT RECOVERY TECHNOLOGIES: PATHWAY TO2021年2月1日 The Lniano municipality In Kujawy and Pomerania Province (Poland) It was developed to serve as a source of thermal energy in the form of steam for technological use in an animal waste treatment plant The system consists of the rotary pyrolyzing reactor, the fluidized bed chamber and the waste heat recovery boilerThermal utilization of meatandbone meal using the rotary kiln 2016年5月1日 Compared with the kiln without the thermoelectric recovery system, the kiln with the system can recover more than 3285% of the energy that used to be lost as waste heat through the kiln surface ViewHeat Recovery Analysis of a Rotary Kiln in Cement Industry
.jpg)
(PDF) Parameter design of rotary kiln incinerator and application
2020年7月3日 In this paper, according to the type and scale of hazardous waste incineration, process selection, design of rotary kiln incinerator, and the engineering principle and performance characteristics 2023年3月6日 The waste heat power generation project can recover 37% of the total input exergy of the rotary kiln system and meanwhile improve the objective exergy efficiencies of the raw material preparation Waste Heat Recovery and Utilization of Cement Rotary Kiln Download scientific diagram Concept of the waste heat recovery in metal steel industry from publication: ETEKINA: Analysis of the potential for waste heat recovery in three sectors: Aluminium Concept of the waste heat recovery in metal steel industry2022年10月1日 The desired operating temperature of 1100–1300 °C of the kiln has been achieved even with decreased fuel intake of 002 g/s by considering the increased waste heat recovery from the kiln flue Numerical investigation on the heat transfer of plastic waste
.jpg)
(PDF) Improved waste heat recovery through surface of kiln using
2018年1月1日 The results show that the waste heat recovery rate is increased by 3% to 8% (EMs) using fatty acids including lauric acid (LA The energy balance of a rotary kiln used for calcination