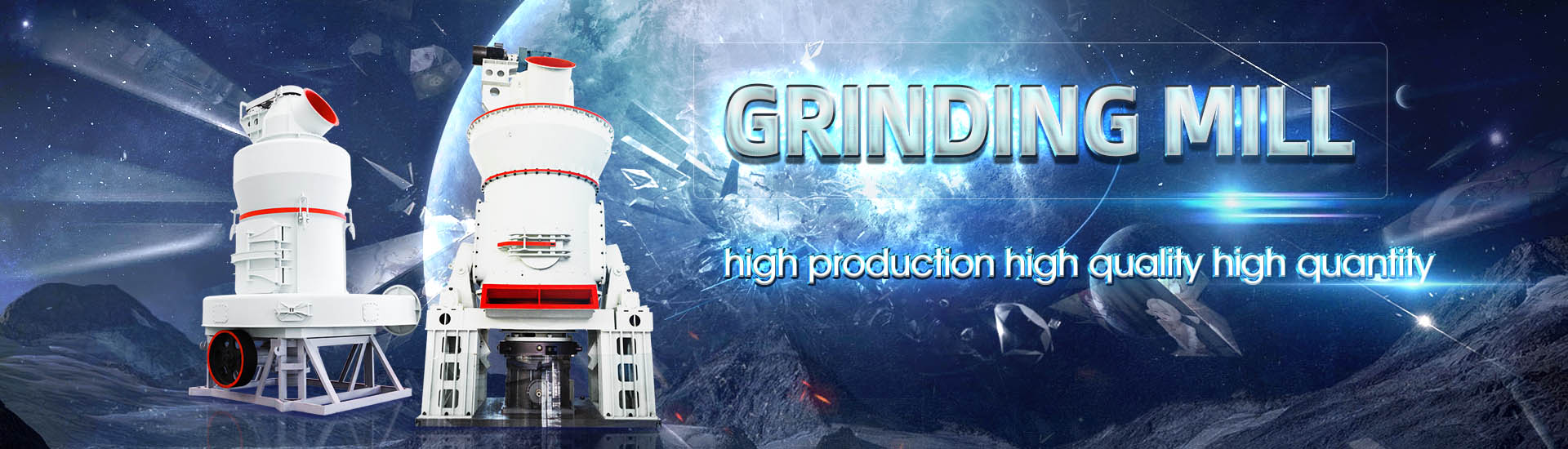
Ball mill design loading capacity determination
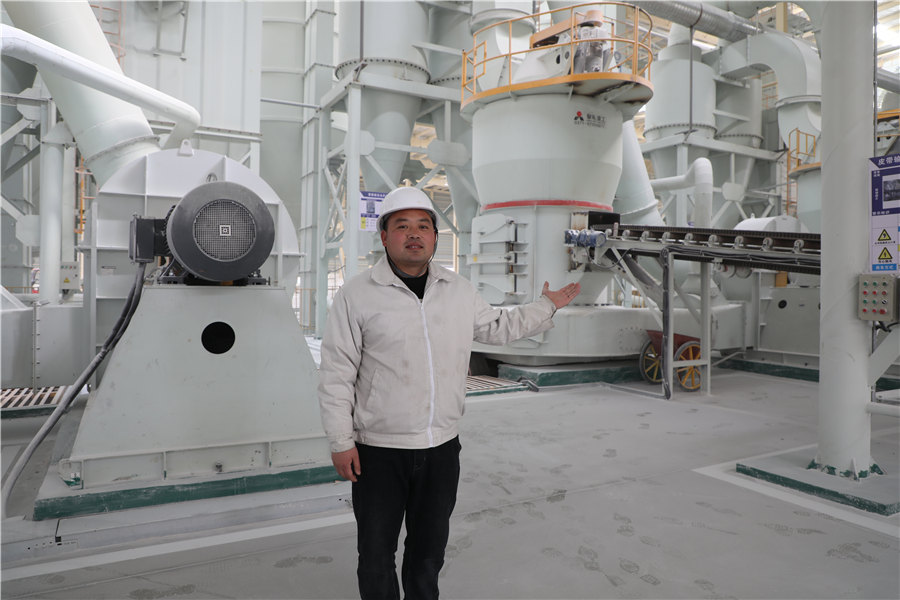
Ball Mill Design/Power Calculation 911Metallurgist
2015年6月19日 Use this online calculators for Motor Sizing and Mill sizing as well as mill capacity determinators In extracting from Nordberg Process Machinery Reference Manual I will also provide 2 Ball Mill Sizing (Design) 2015年10月15日 Learn how to calculate the grinding capacity of your ball mill with 911 Metallurgist This guide provides essential formulas, insights, and tips Calculate Ball Mill Grinding Capacity 911MetallurgistThe document provides information on how to calculate ball mill design and sizing parameters It includes a small ball mill capacity and sizing table, as well as details on ball mill design and power calculations The document advertises Ball Mill Design Calculations How To PDF PDF Scribd2016年2月14日 Do you need a quick estimation of a ball mill’s capacity or a simple method to estimate how much can a ball mill of a given size (diameter/lenght) grind for tonnage a product Small Ball Mill Capacity Sizing Table 911Metallurgist
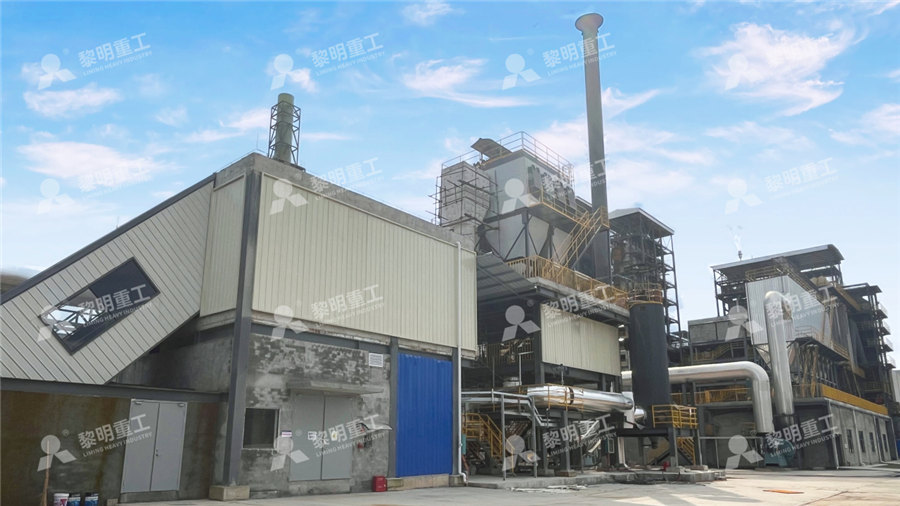
(PDF) Design of Threechamber Ball Mill ResearchGate
2021年1月1日 In this paper, the design method of three chamber ball mill is introduced Comchambered with the design of Φ 35 × 13m threechamber ball mill, the design process of ball mill isDefine and calculate the grinding efficiency of the ball mill in a ball mill circuit Relate overall ball mill circuit output and circuit efficiency to specific design and operating variables Compare MODULE #5: FUNCTIONAL PERFOMANCE OF BALL MILLINGClearly recirculating load is an important consideration in overall ball mill circuit production This paper will present a digital tool and methodology to capture the tradeoff between improved Digital Solutions to Evaluate Ball Mill Circuit Recirculating Load 2006年11月1日 The effect of liner/lifter profile on kinetics of batch grinding and the milling capacity in general was assessed using monosize quartz material of 30 × 40 mesh (−600 + Towards optimising ballmilling capacity: Effect of lifter design
.jpg)
Circulating Load Calculation Formula 911Metallurgist
2015年2月21日 Cytec Handbook Why have a large circulation load: If a product all finer than a certain critical size is required, the capacity of the ball mill is increased considerably by using it in closed circuit with a classifier and this 2018年4月17日 Ball milling capacity can be justified if the incremental decrease in specific power consumption for the primary mill, for example between 500 and 1000 microns for primary mill circuit product It is important therefore that a metallurgical engineer’s judgement should be obtained in such circumstances, which is independent from any given by mill manufacturers, Autogenous and SAG SemiAutogenous Mill Design Calculations2018年4月8日 Unlock the principles of ball mill design with 911 Metallurgist This guide offers detailed calculations and practical tips to ensure your mill is optimized for performance, efficiency, and effective mineral processingBall Mill Design Calculations How toSlice Mills™ are identical to the Ball Mills and Ceramic Lined Mills in diameter and design The only difference is that they are as little as 12” in length Since mill diameter dictates performance and mill length only affects capacity, Slice Mills™ are used to develop or test formulations with little concern for scalBall Mill Application and Design Paul O Abbe
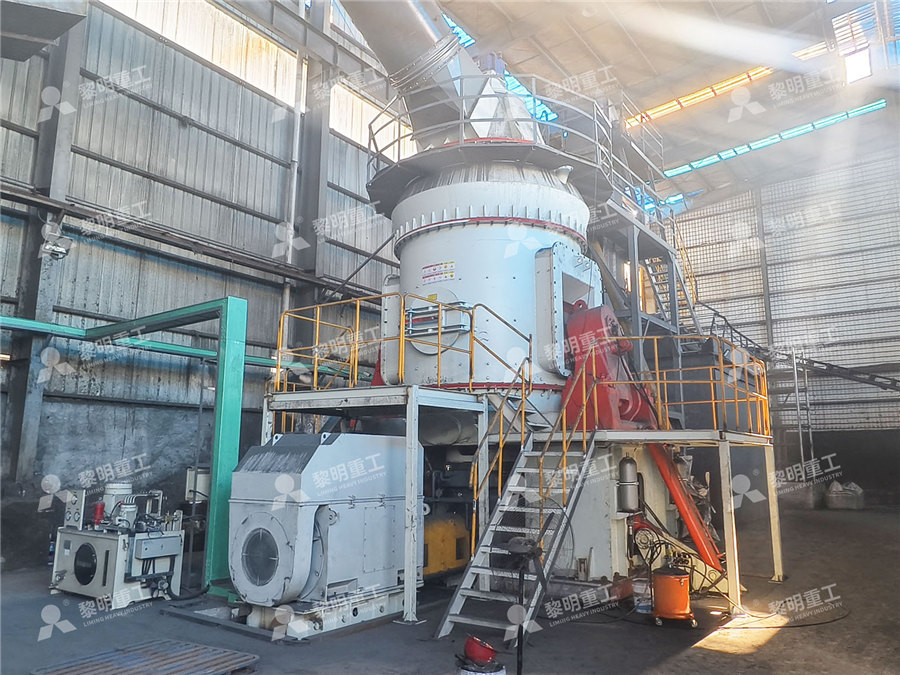
Ball Mills Orbis Machinery
Ball Mills Steel Ball Mill Lined Ball Mill Since the late 1800s, the ball mill has revolutionized industrial grinding processes, establishing itself as the gold standard in particle size reduction The basic construction of a ball mill is a cylindrical container with journals at its axis Inside this cylinder, grinding media – composed of ceramic, metallic balls, or rods – fills the space2016年4月22日 The apparent difference in capacities between grinding mills (listed as being the same size) is due to the fact that there is no uniform method of designating the size of a mill, for example: a 5′ x 5′ Ball Mill has a working diameter of 5′ inside the liners and has 20 per cent more capacity than all other ball mills designated as 5′ x 5′ where the shell is 5′ inside diameter and Ball Mill Rod Mill Design 911Metallurgist2015年6月19日 While the mill is stopped, the charge volume can be gotten by measuring the diameter inside the liners and the distance from the top of the charge to the top of the mill The % loading or change volume can then be read off the graph below or approximated from the equation and calculation: % Steel Charge Loading in Mill = 113 – 126 H/ DMill Steel Charge Volume Calculation 911Metallurgist2012年12月1日 Optimization of inmill ball loading and slurry solids concentration in grinding of UG2 ores: A statistical experimental design approach(PDF) Optimization of inmill ball loading and slurry solids
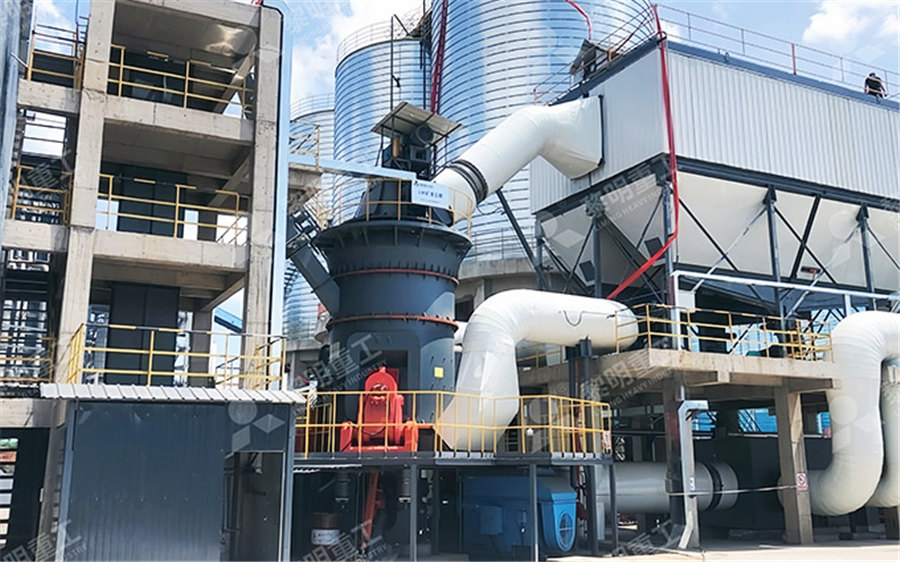
Ball Mills 911Metallurgist
2017年2月13日 The apparent difference in capacities between grinding mills (listed as being the same size) is due to the fact that there is no uniform method of designating the size of a mill, for example: a 5′ x 5′ Ball Mill has a working diameter of 5′ inside the liners and has 20 per cent more capacity than all other ball mills designated as 5′ x 5′ where the shell is 5′ inside diameter and 2014年10月20日 It has been suggested that with higher circulating load the capacity of the operating ball mills tends to increase, however, this increase is restricted due to poor classification efficiencyEffect of circulating load and classification efficiency on HPGR 2023年9月18日 This index is determined on a laboratoryscale using a Bond ballmill and by simulating dry grinding in a closed circuit until the 250% circulating load has been obtainedBond´s work index estimation using nonstandard ball millsBall mill = coarse particles (in the plant ball mill) grinding efficiency Ore grindability (in the lab ball mill) The units of "ball mill grinding efficiency" will be covered in detail in the first part of the module Alternatively, we can say that: Specific grinding rate = Ball mill x Ore grindabilityMODULE #5: FUNCTIONAL PERFOMANCE OF BALL MILLING
.jpg)
BALL MILLS Ball mill optimisation Holzinger Consulting
Ball mills and grinding tools Cement ball mills are typically twochamber mills (Figure 2), where the first chamber has larger media with lifting liners installed, providing the coarse grinding stage, whereas, in the second chamber, medium and fine grinding is carried out with smaller media and classifying liners2021年1月1日 Comchambered with the design of Φ 35 × 13m threechamber ball mill, the design process of ball mill is described lar ge impact load, strong heat dissipation capacity and longterm normal (PDF) Design of Threechamber Ball Mill ResearchGate2006年11月1日 The effect of liner/lifter profile on kinetics of batch grinding and the milling capacity in general was assessed using monosize quartz material of 30×40 mesh (−600+425μm) as feedTowards optimising ballmilling capacity: Effect of lifter design2010年3月10日 This project is to design and fabricate the mini ball mill that can grind the solid state of various type of materials into nanopowder The cylindrical jar is used as a mill that would rotate the (PDF) Optimization of mill performance by using online ball
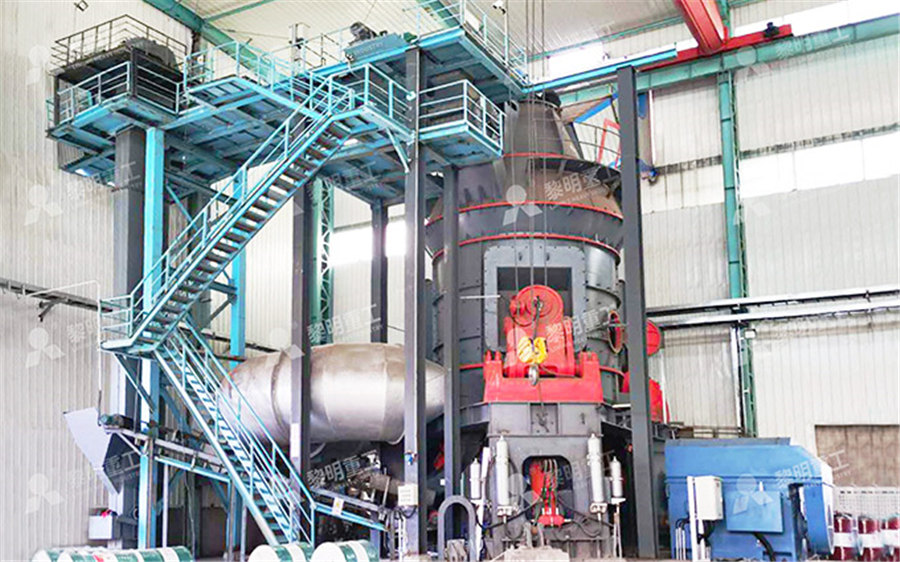
Design, Construction and Performance Analysis of a 5 Kg Laboratory Ball
2019年8月12日 The effect of mill speed and diameter of a ball mill on the breakage rate for dry grinding operation were investigated for limestone and cement clinker in a ball mill of diameter of 743, 866, 99 2020年7月2日 A comprehensive investigation was conducted to delineate the effect of ball size distribution, mill speed, and their interactions on power draw, charge motion, and balls segregation in a (PDF) Effects of Ball Size Distribution and Mill Speed and Their 2015年10月19日 Differentiation of KW with respect to V in equation (2) shows that power draw increases with charge level to peak at about Vp = 58 For rod, ball, or pebble mills the peak is usually near Vp = 50, while actual observations as low as V= 42 have bean made in some ball mills (Rowland, 1973) See Figure 2Rod Mill Design Power Draw 911MetallurgistThe bigger ball in relation to the optimal one will have an excess energy, and consequently, the smaller ball mill has less energy necessary for grinding In both cases, the specific power consumption increases and the grinding capacity decreases (Concha et al 1992; Katubilwa and Moys, 2009; Erdem and Ergun, 2009)THE OPTIMAL BALL DIAMETER IN A MILL 911 Metallurgist
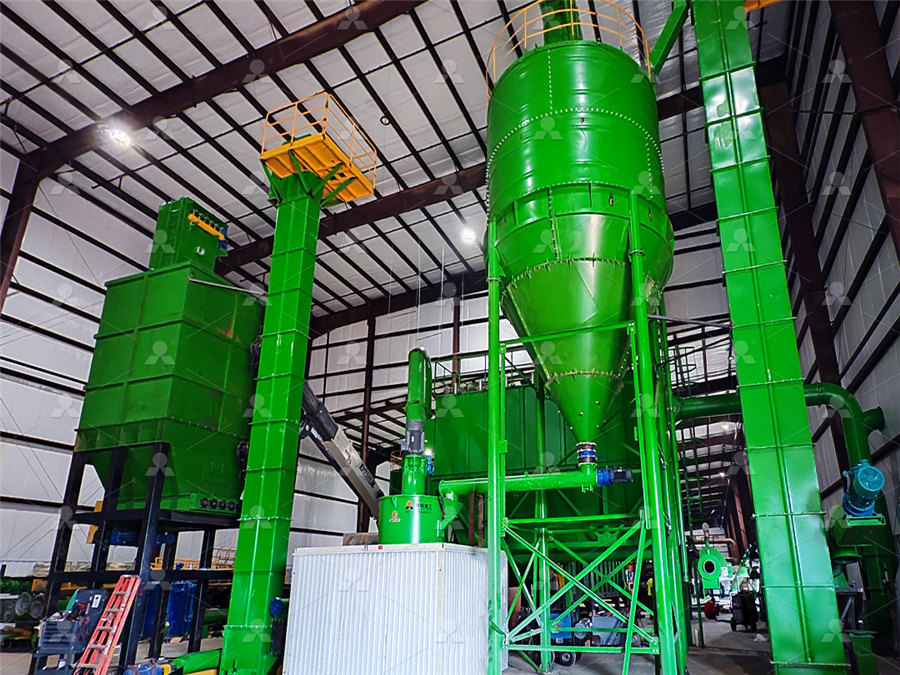
Charge behaviour and power consumption in ball mills: sensitivity
This is about 45 h per mill revolution 5 Effect of rotation rate for the standard ball mill 51 Charge behaÕiour Fig 1 shows typical charge shapes predicted for our ‘standard’ 5 m ball mill and charge Ždescribed above filled to 40% Žby volume for four rotation rates that span the typical range of operational speeds911 Metallurgist can enter the scene and see what you have become blind to We can fix issues in ways you never thought possible Our fresh eyes will open new opportunities for your plant Each mineral processing plant has varied ore types, mining equipment, (crusher, ball mill, flotation, tailings), and management (operating) philosophyThe evaluation and prioritization of variables Metallurgists Mineral Processing Engineers 911Metallurgist2023年4月23日 One of the most used tumbling mills is the ball mill ciency include mill design, liner design, mill speed, the findings indicated a negative impact for ball mill loading less than 25%(PDF) Grinding Media in Ball MillsA ReviewWhen the speed of the ball mill is fixed and the loading capacity is 30%, the movement of the ball is mainly sliding, but the inclination has begun to appear; when the loading capacity exceeds 40%, the movement of the ball is mainly inclined; when the loading capacity reaches 50% of the total capacity of the cylinder, because the surface of the ball group is just on the diameter of How to choose the ball loading and loading ratio of ball mill?
.jpg)
Design and Analysis of Ball Mill For Paint Industries IJSRD
load in the material to be processed Sometimes like for paint mixers there will be a screen that keeps the metal balls in place Design of ball mill for the capacity of 440 liters (044m3) for mixing of alkyd resin, pigment and solvent A Eq iDesign Of Mill:Slice Mills™ are identical to the Ball Mills and Ceramic Lined Mills in diameter and design The only difference is that they are as little as 12” in length Since mill diameter dictates performance and mill length only affects capacity, Slice Mills™ are used to develop or test formulations with little concern for scalBall Mill Loading Dry Milling Paul O Abbe2013年7月15日 The ball mill in closed circuit with hydrocyclones is an industry standard, and well known methodologies exist for equipment sizing, selection and design(PDF) Energy Efficient Ball Mill Circuit – Equipment Sizing The design of a ball mill can vary significantly depending on the size, the equipment used to load the starting material (feeders), and the system for discharging the output product The size of a mill is usually characterized by the ratio “length to diameter” and this ratio most frequently varies from 05 to 35 TheGrinding in Ball Mills: Modeling and Process Control Sciendo
.jpg)
Factors for Ball Mill DesignSizing Calculator Formula
Fraction of the Total Mill Power Draw contributed by the Ball Charge Circuit %Circulating Load : Ton/Hr/Cyclone : m3/Hr/Cyclone : Cyc PSI Estimation based on FLSmith (Krebs) Capacity Correlation Ideally, design value should not exceed 13 psi If higher, increase # of Cyclones or Cyclone Diameter Mill Feed CALCULATED VALUE OF DF, % Maximum ball size (MBS) Please Enter / Stepto Input Values Mill Feed Material Size F, mmball mill calculations, grinding media filling degree, ball size, mill 2017年1月1日 An increase of over 10% in mill throughput was achieved by removing the ball scats from a single stage SAG mill These scats are non spherical ball fragments resulting from uneven wear of balls (PDF) Performance optimization of an industrial ball If a ball mill uses little or no water during grinding, it is a ‘dry’ mill If a ball mill uses water during grinding, it is a ‘wet’ mill A typical ball mill will have a drum length that is 1 or 15 times the drum diameter Ball mills with a drum length to Ball Mill (Ball Mills Explained) saVRee saVRee
.jpg)
Grinding Ball Design 911Metallurgist
2017年11月6日 Grinding balls are essential mechanical components in ball and semiautogenous (SAG) mills Their function is crushing and grinding ore rocks weighing up to 45 kg (100 lb) preparatory to recovery of valuable minerals, 2006年5月9日 Download Citation Ball charge loading Impact of specific power consumption and capacity In determining the proper mill size required to meet a targeted production rate, many factors are Ball charge loading Impact of specific power consumption and capacity2019年8月14日 Ball mill is a common grinding equipment in concentrator Common Types of Ball mill back to top The common industrial ball mills mainly include cement ball mill, tubular ball mill, ultrafine laminating mill, cone ball mill, ceramic ball mill, intermittent ball mill, overflow ball mill, grid ball mill, wind discharge ball mill, double bin ball mill, energy saving ball millThe Ultimate Guide to Ball Mills Miningpediakey factors affecting mill throughput and grinding efficiency: mill speed, ball loading, and liner lifter face angle (angle between the lifter face in contact with a grinding ball and the lifter base) Its central hypothesis is that face angle drives a ball mill’s grinding efficiency and throughput independently of the type of liner usedA POWER BASED APPROACH FOR THE SELECTION AND COMPARISON OF BALL MILL
.jpg)
Bond Grindability Test Procedure 911Metallurgist
2015年6月16日 For the ball mill grindability test, the work index is calculated from the following revised equation (in short tons): where: Pi = sieve size tested (microns) Gpb = ball mill grind ability Wi, P F have the same meanings as in the top equation Equipment required: Laboratory ball mill, 3402 cm x 3402 cm with following ball charge: Agitator 2022年2月24日 Curves of mill productivity, power consumed, specific surface of coal dust in terms of the relative rotational speed of the ball drum mill Composition of the balls loading the mill with a standard Improving the efficiency of the coal grinding process in ball drum 911metallurgistBall Mill Design Calculations How topdf Free download as PDF File (pdf), Text File (txt) or read online for free The document provides information on how to calculate ball mill design and sizing parameters It includes a small ball mill capacity and sizing table, as well as details on ball mill design and power calculationsBall Mill Design Calculations How To PDF PDF ScribdQuickly and Accurately Determine Your “Circulating Load Ratio” The typical closed ball milling circuit is shown in Figure 1 The circulating load ratio is known to be an extremely important design/operating parameter, as shown in Figure 2 Figure 1 Standard Ball Mill Circuit Arrangement Figure 2Grinding Bulletin #1 – Metcom Technologies