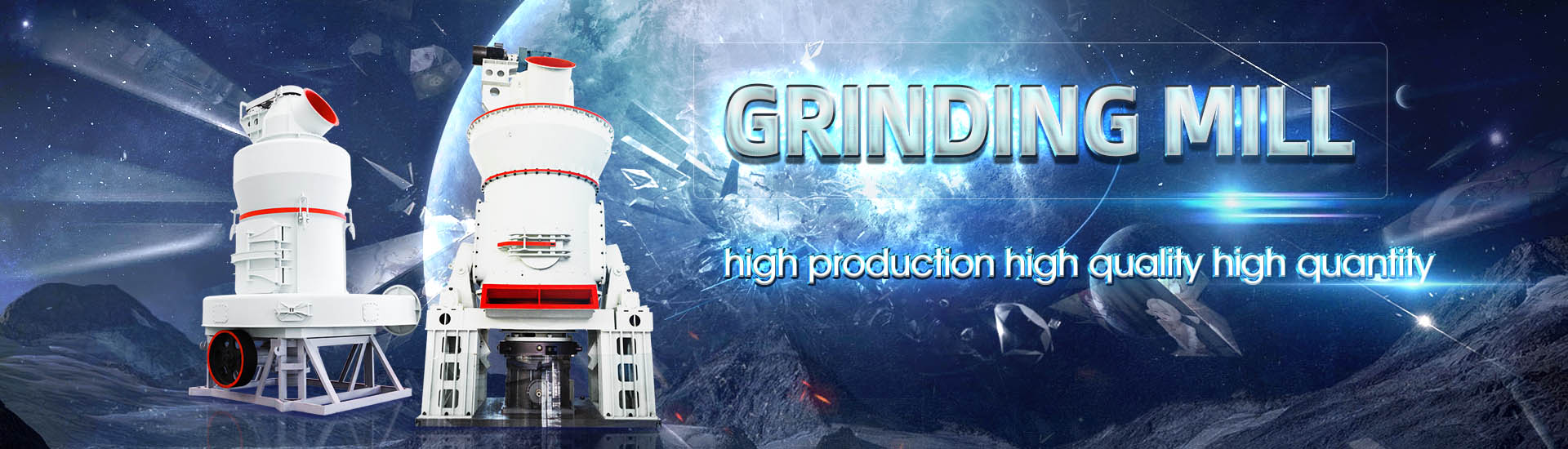
HOME→High energy ore mill demand Highenergy ore grinding machine demand Highenergy ore grinding machine demand
High energy ore mill demand Highenergy ore grinding machine demand Highenergy ore grinding machine demand
.jpg)
Quantification of HPGR energy efficiency effects on downstream
HPGRs (high pressure grinding rolls) have been developed within the last decades for energy efficient processing of a wide variety of ores Special interest has been raised by projects 2022年3月30日 HPGR circuits can reduce the hard rock mining industry’s CO 2 emissions by up to 435% compared to SAG/Ball mill circuits Analysis of published data has confirmed that Helping to reduce mining industry carbon emissions: A stepby 2023年12月1日 Mining energy use could rise by a factor in the range 2–8 by 2060 Material flows and associated energy use are lacking in key energyeconomy models Improving the Global energy consumption of the mineral mining industry: 2022年3月1日 High Pressure Grinding Rolls (HPGR) circuits have the potential to reduce the Mining Industry’s CO2 emissions by up to 345 megatonnes/year, or 435% when compared to Helping to reduce mining industry carbon emissions: A stepby
.jpg)
Outotec Higmill – EnergyEfficient HighIntensity Grinding
OUTOTEC HIGMILL – ENERGYEFFICIENT HIGHINTENSITY GRINDING With global ore grades declining and the demand for commodities continuing to increase, mining BENEFITS 2013年12月18日 In a laboratory study by Nesset et al, a GIS mill charged with 5mm steel shot, and with other operating conditions similarly optimized, achieved high energy efficiencies Energy Use of Fine Grinding in Mineral Processing2022年3月16日 HPGR has been found to be efficient size reduction equipment compared to conventional size reduction equipments due to its potential processing benefits in terms of Potential of HighPressure Grinding Roll (HPGR) for Size Reduction Datadriven machine learning approaches have emerged as effective solutions, enabling energy consumption prediction and optimization These methods offer valuable insights to improve the Predicting Grinding Mill Power Consumption in Mining: A
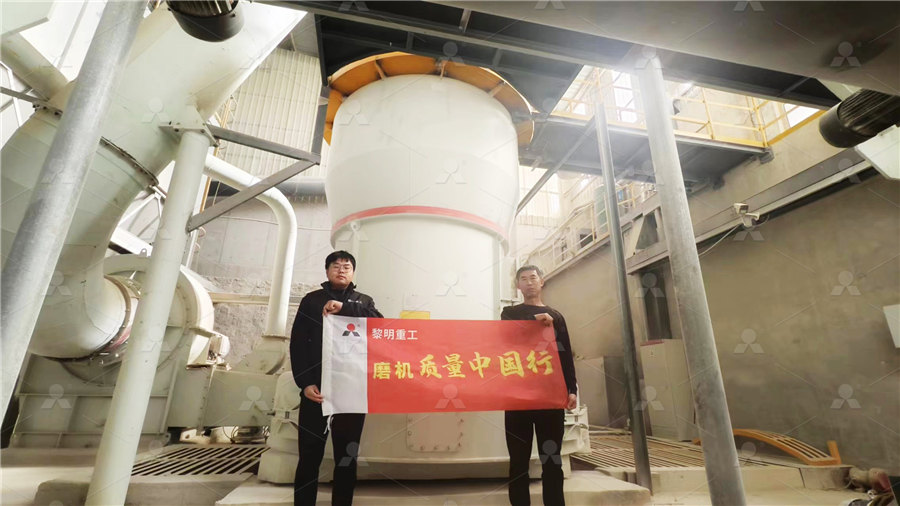
Ore Grinding SpringerLink
2023年7月20日 Moist grinding, a special grinding method, is used to prepare pellets for smelting According to the grinding medium features, ore grinding is mainly classified into ball grinding Abstract: Milling is among the most energyconsuming technological stages of copper ore processing It is performed in mills, which are machines of high rotational masses The start of Energy Efficiency Analysis of Copper Ore Ball Mill Drive SystemsFor highenergy milling, Emax is a completely new kind of ball mill Impact and high friction's unique combination leads to very fine particles within an extremely short processing time The optimized jar design and 2000 min1 of extreme High Energy Ball Mill Equipment and Its Application Explore our mining equipment to find the ideal wholesale high energy ball mill machine model and mills for any mining challenge Competitive price high energy Lead zinc rock gravel gold ore grinding ball mill machine $5,00000 Shipping per piece: $28053 Min The versatility of high energy ball mill machines is evident in their various High energy ball mill machine
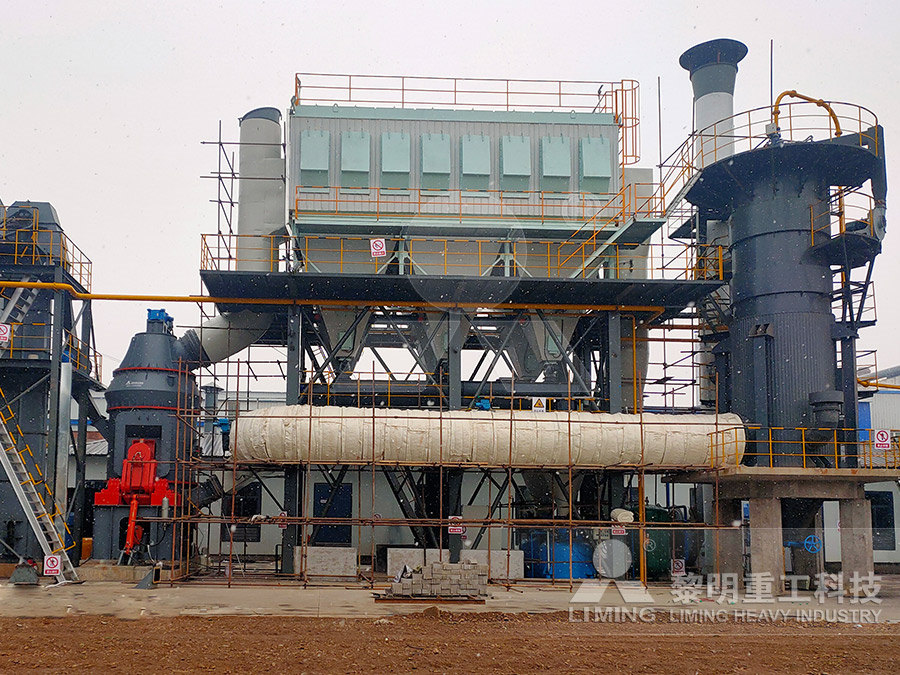
Research of iron ore grinding in a verticalrollermill
Request PDF On Mar 15, 2015, Mathis Reichert and others published Research of iron ore grinding in a verticalrollermill Find, read and cite all the research you need on ResearchGateThe Emax is an entirely new ball mill designed for high energy grinding The maximum speed of 2000 rpm, so far unrivaled in a ball mill, The High Energy Ball Mill Emax is used wherever highest demands are placed on speed, fineness, purity and fibers, chemical products, ores, gypsum, glass, semiprecious stones, wood, lime, catalysts THE REVOLUTION IN ULTRAFINE GRINDING RETSCH2023年7月20日 (2) Various working parameters of grinding mill, including fraction of critical speed for grinding mill, filling rate for grinding mill, grinding concentration, grinding cycle load, etc (3) And grinding material properties, including ore grindability, feeding particle size, etc Huge energy and steel consumption in ore grinding process greatly affect the subsequent separation Ore Grinding SpringerLinkThe Emax is an entirely new ball mill designed for high energy grinding The maximum speed of 2000 rpm, so far A sensor monitors the correct position of the jars before starting the machine Possible imbalances are The High Energy Ball Mill Emax is used wherever highest demands are placed on speed, fineness, purity and High Energy Ball Mill Emax – The Revolution in Ultrafine Grinding
.jpg)
Quantification of HPGR energy efficiency effects on downstream grinding
Figure 4 – Correlation of specific hydraulic pressure and specific energy demand from a test series with iron ore Moreover, the high pressure grinding regime leads to microfractures within the product as shown in Figure 5 Those microfractures reduce the strength of the ore fed to subsequent comminution machinesMain machines in ore grinding process are Iron ore mill equipment The most common Iron ore mills in mining are ball mill, raymond mill and high pressure suspension mill The selection of is according to customers’ requirements and the nature of the minerals Ore grinding can be divided into grinding with media and withoutSBM Iron ore grinding plant for ores milling process2015年10月23日 In this chapter an introduction of widely applied energyefficient grinding technologies in cement grinding and description of the operating principles of the related equipments and comparisons over each other in terms of grinding efficiency, specific energy consumption, production capacity and cement quality are given A case study performed on a EnergyEfficient Technologies in Cement Grinding IntechOpen2021年3月23日 Milling is among the most energyconsuming technological stages of copper ore processing It is performed in mills, which are machines of high rotational massesEnergy Efficiency Analysis of Copper Ore Ball Mill Drive Systems
.jpg)
Studying the integration of solar energy into the operation of a
2019年3月27日 Grinding is one of the most energydemanding processes of copper mines Declining ore grades and harder rocks will further intensify this demand2023年7月10日 The present literature review explores the energyefficient ultrafine grinding of particles using stirred mills The review provides an overview of the different techniques for size reduction and (PDF) EnergyEfficient Advanced Ultrafine Grinding of 5 Quality guarantee, safe operation, energysaving The ball grinding mill machine usually coordinates with other rock crusher machines, like jaw crushers, and cone crushers, to reduce the ore particle into fine and superfine sizes Industry Grinder for Mineral Processing JXSC MachineHigh Energy River Sand Limestone Mine Ball Grinding Mill Machine Price, Find Details and Price about Grinding Ball Mill Machine Iron Ore Ball Mill from High Energy River Sand Limestone Mine Ball Grinding Mill Normally the machines are taken apart before delivery and are packed by suitable packing ways, the packing ways are as below High Energy River Sand Limestone Mine Ball Grinding Mill Machine
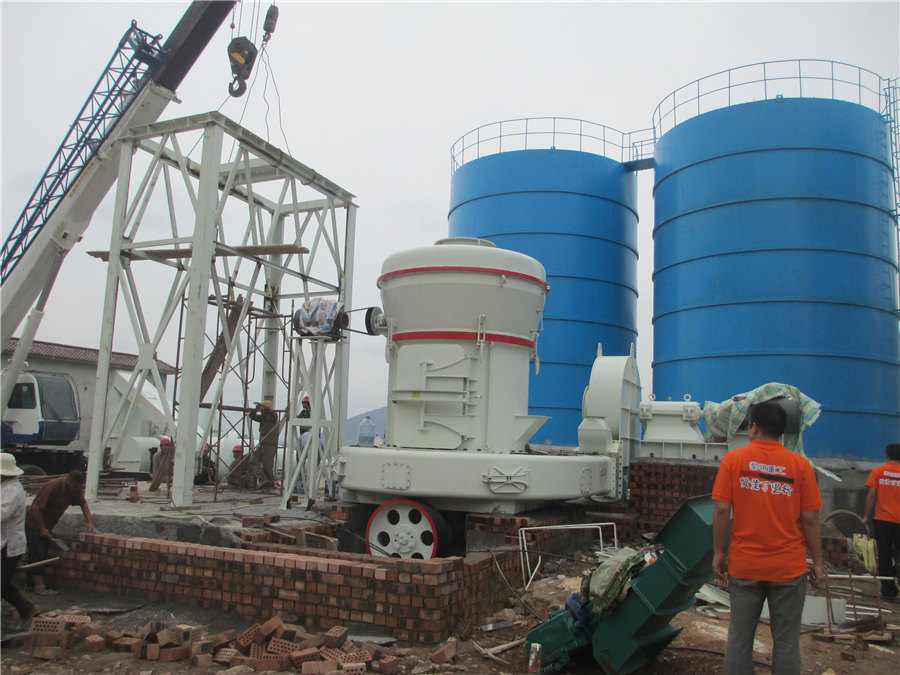
High Energy Ball Mill Emax Revolutionizing Ultrafine Grinding!
The E max is an entirely new type of ball mill for high energy milling The unique combination of high friction and impact results in extremely fine particles within the shortest amount of time The high energy input is a result of an unrivaled speed of 2000 min1 and the innovative jar designThanks to the revolutionary water cooling system, the high energy input is effectively High capacity ball mills are essential for enhancing iron ore grinding efficiency and meeting the production demands of the steel industry By optimizing mill design, selecting appropriate grinding media, and controlling operating conditions, iron ore processors can achieve a higher throughput, reduced energy consumption, and improved grind qualityEnhancing iron ore grinding efficiency with high capacity ball mills2019年10月31日 As described above, the grinding of talc using a highenergy ball mill results in di ff erences in crystallinity , particle size, specific surface area, and aggregation behavior Figure 10 Effects of Ball Size on the Grinding Behavior of Talc Using a High 2018年6月18日 Demand for energyefficient grinding pretreatment methods will grow in the future considering the depletion of highgrade resources and stringent environmental constraints related to reject disposalOre Pretreatment Methods for Grinding: Journey and Prospects
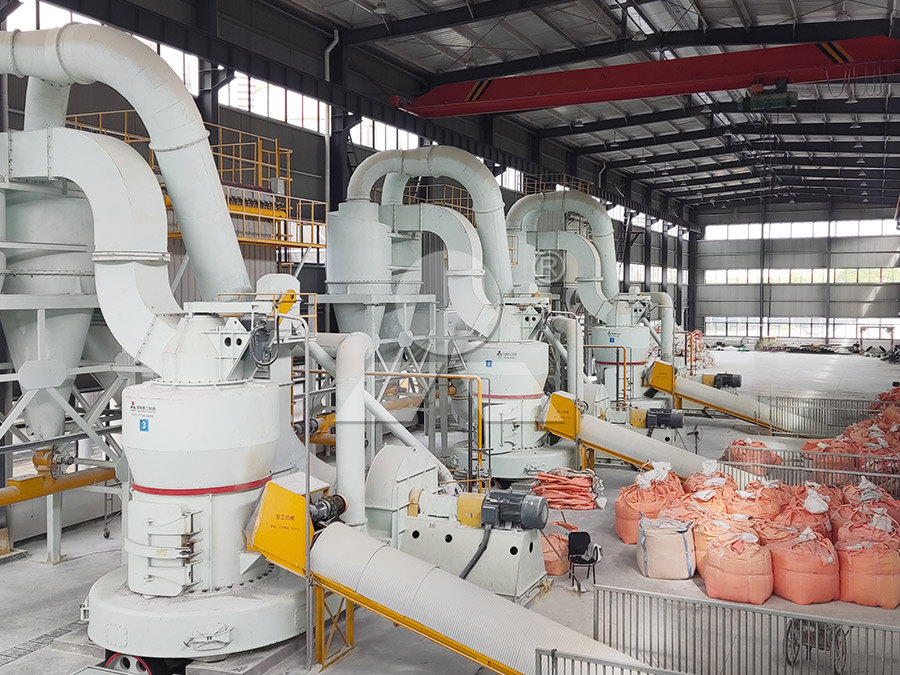
High Pressure Grinding Roll and Magnetic Separation for Energy
2024年5月31日 This paper presents an industrial verification test, adding a high pressure grinding roll and magnetic separation operation after the thirdstage fine crushing operation to reduce the particle size of ball mill feed and improve the processing capacity of grinding operation The optimal process parameters of high pressure grinding roll and magnetic separation were Grooved ring high manganese steel liners are used to increase the contact surface of ball and ore, strength the grinding, lift the ores, and reduce the energy consumption The steel frame can be used for the ball mills with diameter 27 meter or less in order to design and manufacture the modular plant, reduce the amount of civil construction and install the machine easilyGold Processing Plant Ball Mill Ore Grinding Machine2023年7月10日 The present literature review explores the energyefficient ultrafine grinding of particles using stirred mills The review provides an overview of the different techniques for size reduction and the impact of energy EnergyEfficient Advanced Ultrafine Grinding of 2019年6月21日 Nextgeneration grinding technologies in particular offer vast scope for improvement, and machines such as highpressure grinding rolls (HPGRs) and vertical stirred mills that were introduced 30 Grinding down energy consumption in
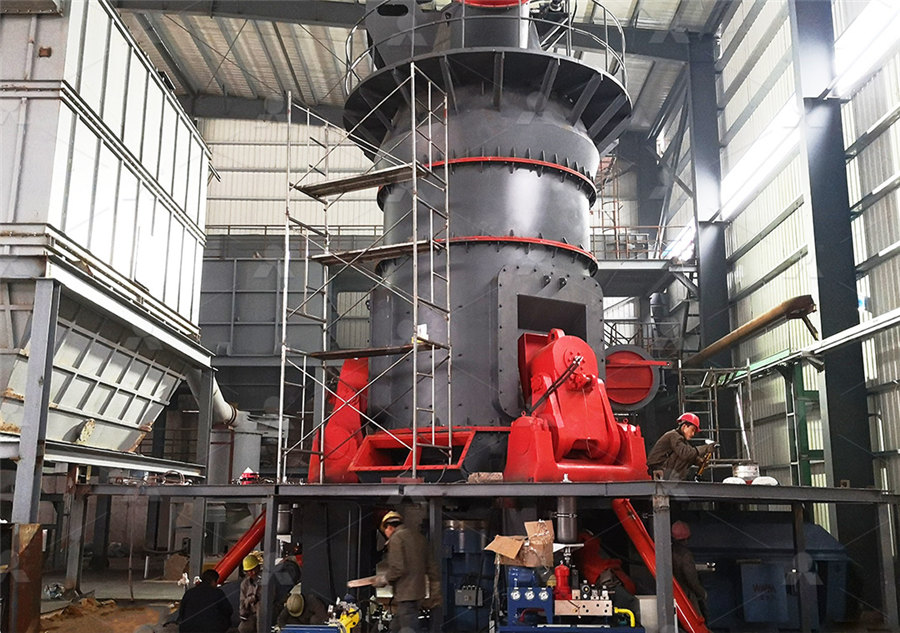
High Precision Lead Oxide Manganese Ore Ball Mill Grinding Machine
High Precision Lead Oxide Manganese Ore Ball Mill Grinding Machine Orice, Find Details and Price about Gold Rock Ball Mill Copper Rock Ball Mill from High Precision Lead Oxide Manganese Ore Ball Mill Grinding Machine Orice Energy saving mining ball mill is a key equipment in beneficiation plant2021年2月26日 Milling is among the most energyconsuming technological stages of copper ore processing It is performed in mills, which are machines of high rotational masses The start of a mill filled to capacity requires appropriate solutions that mitigate the overloading One method for increasing the energy efficiency of ball mills is to optimize their drive systems This article Energy Efficiency Analysis of Copper Ore Ball Mill Drive 2023年4月23日 It consumes most of the energy used in mineral processing plants with grinding using up to 50% of the provided energy Tumbling mills are an old technology that is still commonly used for grinding(PDF) Grinding Media in Ball MillsA Review ResearchGate2022年1月1日 Recently, to overcome the problems of high energy consumption, large medium consumption and iron pollution in traditional grinding operation [5–7], Northeastern University has innovatively developed a special ceramicmedium stirred mill (as shown in previously published article by Zhang et al [8]) with small pitch, high speed and low energy consumptionHighefficiency and energyconservation grinding technology using
.jpg)
Potential of HighPressure Grinding Roll (HPGR) for Size
But the grinding process is highly energy intensive and has very low energy efficiency [1] Therefore, it is highly essential to use in an efficient manner to increase their operational efficiency Since grinding constitutes a bulk of operating cost in mineral processing [2], it has become necessary to take recourse to efficient grinding 2023年9月1日 As shown in Table 3, the highest energy consumption is from Ball Mill 1, followed by Ball Mill 2 The reduction ratio may explain this since these units aim to reduce particle size by two orders of magnitude Interestingly, regrinding requires less energy than SAG mills, despite having a higher specific energyLimit of recovery: How future evolution of ore grades could Selective smart blast design uses data to target relatively high ore concentration sections with greater blast energy This significantly improves the grade of ore fed to the mill The net total energy consumed at the crushing and grinding stages is reducedMining energygovauOres output from HPGR are with high ratio of fine particle, and the internal of the ore will have a lot of micro cracks More fine particle and micro cracks will help to highly reduce the ore grinding cost Compare to the crushing system which is made of cone crusher, rod mill, ball mill, for an HPGR system is with lower energy consumption for (HPGR) high pressure grinding rolls/rollers for cement, ores
.jpg)
Energy conservation and consumption reduction in grinding
2023年11月1日 Grinding operation is the last preparation stage before beneficiation In this stage, the material undergoes the combined action of impact and grinding, so that the ore particle size is diminished and the qualified materials is provided for succeeding beneficiation operations [1, 2]Generally, the quality of the grinding product is also an important factor to determine the 2022年1月1日 However, with the depletion of highgrade deposits and strong demand for steel, a greater number of lowgrade deposits are being developed To operate viably and sustainably, there is a need to reduce costs and energy consumption, particularly of the energyintensive grinding required for lowgrade magnetite minution and classification technologies of iron oreTechnology and technics of ore preparation processes 13 High pressure grinding rolls were successfully introduced in the cement industry in the late 1980s and enabled appreciable reduction in energy consumption Promptly enough their potential was realized in mineral mining industry Strikingly efficient in diamond ore processing, HPGR immeHIGH PRESSURE GRINDING ROLLS—A PROMISING AND COST grinding energy efficiency using three stages of magnetic separation, traditional autogenous milling, HPGR and stirred milling technology In this conceptual flowsheet steel grindingReducing Grinding Energy and Cost Magnetite Iron Ore
.jpg)
Iron ore grinding mill Grinding plants for Iron Ore
1, Raymond Mill, HC series pendulum grinding mill: low investment costs, high capacity, low energy consumption, equipment stability, low noise; is the ideal equipment for wollastonite powder processing But the degree of largescale is relatively lower compared to vertical grinding mill 2, HLM vertical mill: largescale equipment, high capacity, to meet the largescale production from the ores The grinding of ore is a highly energyintensive process [1–4] In this process, the size of the particle obtained depends on the energy consumption of the ball mill The major challenge encountered in the process of iron ore grinding is to maintain the desired product particle size distribution (PSD) with sufficientEstimation of Grinding Time for Desired Particle Size Distribution2017年1月17日 Other process activities, such as spraying the ore with water for dust control or the fact that runofmine ore moisture is approximately 2%5% are not generally considered (Bleiwas, 2012a)Breaking down energy consumption in industrial grinding millsDOI: 101016/jpowtec202110056 Corpus ID: ; Highefficiency and energyconservation grinding technology using a special ceramicmedium stirred mill: A pilotscale studyHighefficiency and energyconservation grinding technology
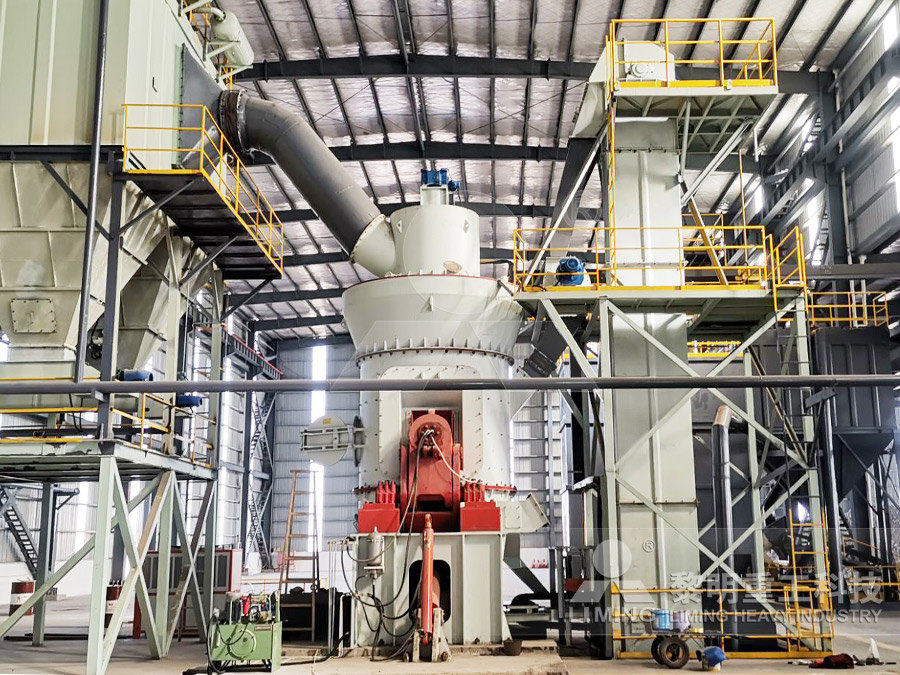
Design, Construction, and Operation of a High‐Energy Mill for
2019年2月7日 A highenergy mill was designed and built with the purpose of processing magnesium (Mg) powders The main characteristics of the mill are grinding capacity of 1 kg and demolition elements of 10 kg; it has a distributed form to the interior ten blades of similar geometry, six of which are of the same size and four of them were increased in length in order 2020年5月9日 The comminution of ores consumes a high portion of energy Therefore, different pretreatment methods of ores prior to their comminution are considered to reduce this energy However, the results of pretreatment methods and their technological development are scattered in literature Hence, this paper aims at collating the different ore pretreatment methods with Methods of Ore Pretreatment for Comminution Energy Reduction