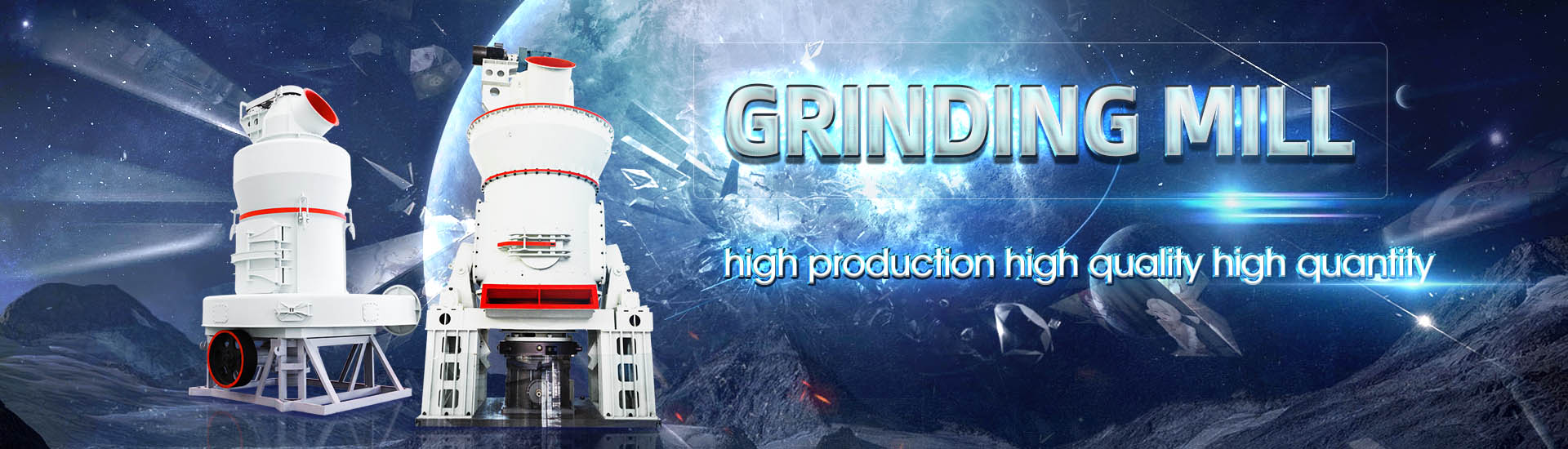
Cement mill grinding system energy efficiency test
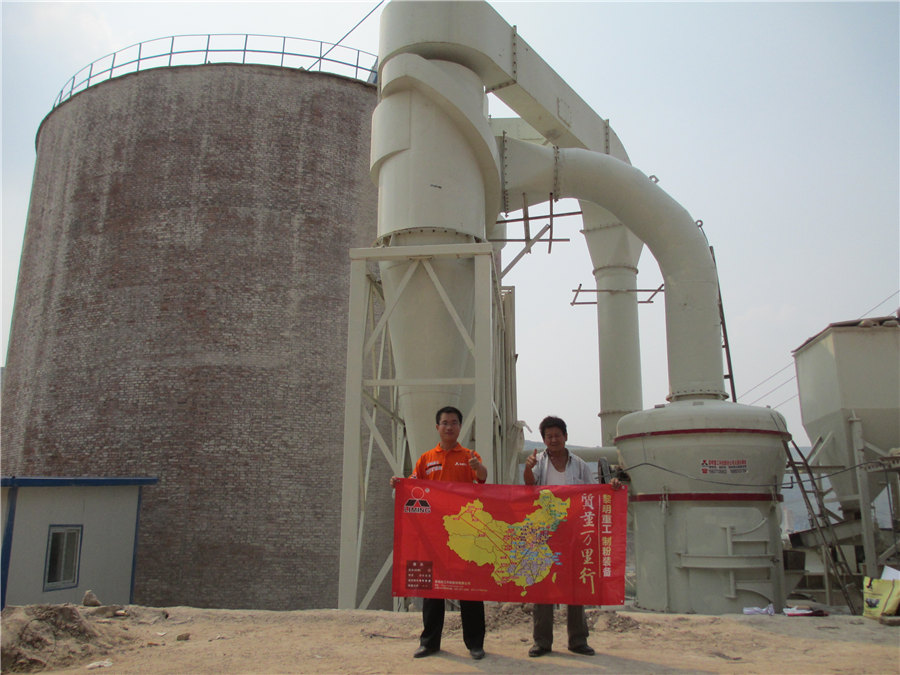
Energy and cement quality optimization of a cement grinding circuit
2018年7月1日 This study aimed at optimizing both the energy efficiency and the quality of the end product by modifying the existing flowsheet of the cement grinding circuit As a general 2012年5月1日 The three industrial grinding systems tested in this study were 1) the combined grinding system (Comflex®) using a HPRM circuit upstream of the ball mill circuit to produce a An industrial comparative study of cement clinker grinding 2004年11月1日 The electrical energy consumed in cement production is approximately 110 kWh/tonne, and around 40% of this energy is consumed for clinker grinding There is potential Cement grinding optimisation ScienceDirect2022年5月9日 By initiating a CL for an industrial cement vertical roller mill (VRM), this study conducted a novel strategy to explore relationships between VRM monitored operational Modeling of energy consumption factors for an industrial cement
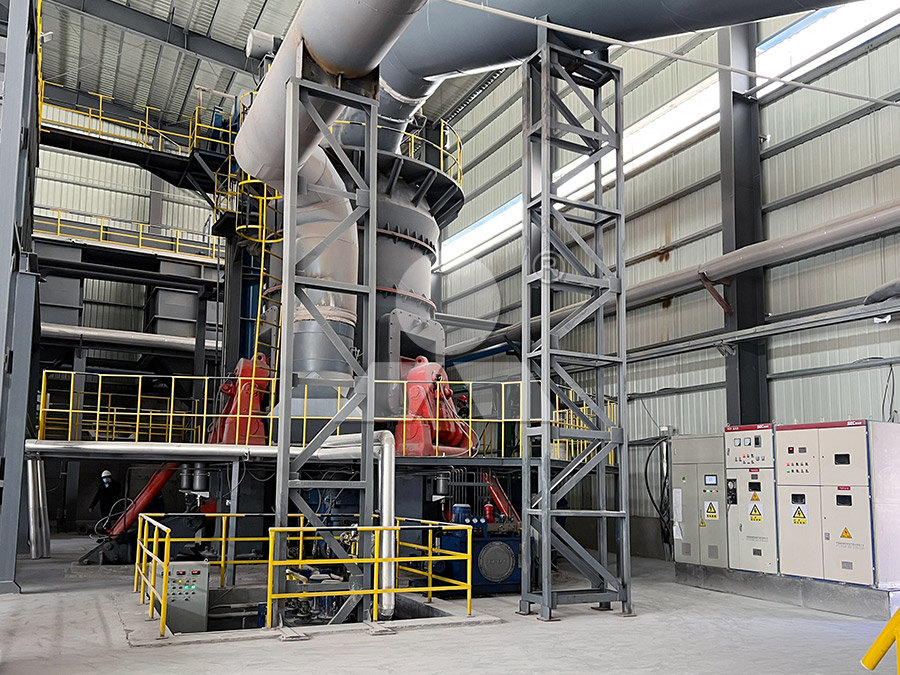
Energy Efficiency Improvement Opportunities for the Cement
The analysis of cement kiln energyefficiency opportunities is divided into technologies and measures that are applicable to the different stages of production and various kiln types used 2023年5月3日 In this paper, the specific energy consumption (SEC) and related emissions of a real scale cement factory currently running in Türkiye have been decreased by investigating A comprehensive investigation of a grinding unit to reduce energy 2020年5月1日 In this work, the energy and exergy analyses of a cement ball mill (CBM) were performed and some measurements were carried out in an existing CBM in a cement plant to Energy and exergy analyses for a cement ball mill of a new 2012年6月1日 In this study, the first and second law analysis of a raw mill is performed and certain measures are implemented in an existing raw mill in a cement factory in order to Reducing energy consumption of a raw mill in cement industry

Advanced Process Control (APC) and analytics for
APC can optimise the grinding circuit to increase throughput and secure consistent output quality, while also lowering energy consumption Material blending Stable and correctly proportioned raw meal is essential for energy 2004年11月1日 Due to limitation of the mill’s rotational speed, the smallest ball size is usually restricted to about 15 mm Cement grinding using stirred mills (Pilevneli and Azizli, 1999) indicates that using smaller media (5–8 mm range) improves grinding energy efficiency up to 50% using stirred millsCement grinding optimisation ScienceDirectTable 4 EnergyEfficiency Opportunities Applicable to Rotary Kilns 10 Table 5 EnergyEfficiency Opportunities Applicable to Vertical Shaft Kilns 17 Table 6 Energy Efficiency Measures for Final Grinding of Products in Cement Plants 19 Table 7Energy Efficiency Improvement Opportunities for the Cement energy efficient and sustainable cement Therefore, versatile systems with continuous development for energy efficiency and sustainability are required For grinding of raw materials, solid fuels and cements, the vertical roller mill (VRM) is one of the most energy efficient grinding systems available TheCEMENT CEMENT INTERN
.jpg)
An industrial comparative study of cement clinker grinding systems
2012年5月1日 The three industrial grinding systems tested in this study were 1) the combined grinding system (Comflex®) using a HPRM circuit upstream of the ball mill circuit to produce a combined final cement product, 2) HPRMonly system in which the cement was produced only with the HPRM circuit of the combined grinding system, and 3) the horizontal roller mill duction of Portlandcements [18853N] This twostage grinding process uses energetically highly efficient highpressure comminution systems for pregrinding of the main cement components (1st grinding step (GS)) Only a small portion of these preground intermediateImprovement of energy efficiency for the grinding of composite cements the Efficiency of Cement Grinding Ball Mill Motors* 1E Normanyo and 1R A Ofosu 1University of Mines and Technology, Tarkwa, Ghana Normanyo, E and Ofosu, R A (2021), “The Effects of Temperature, Vibration and Dosage on the Efficiency of Cement Grinding Ball Mill Motors”, Ghana Journal of Technology, Vol 6, No 1, pp 917 AbstractThe Effects of Temperature, Vibration and Dosage on the Efficiency 2021年1月1日 Cement Grinding: Grinding Mill Grinding systems in the cement industry play a crucial role in particle size distribution and particle shape Bureau of Energy Efficiency: beeindiagov Google Scholar [17] Loesche GmbH : Review on vertical roller mill in cement industry its performance
.jpg)
An industrial comparative study of cement clinker grinding systems
2012年5月1日 This paper is concerned with a comparative analysis of modern cement grinding systems, namely, combined grinding (Comflex®), highpressure roll mill (HPRM) grinding, and horizontal roller mill (Horomill®) grinding Cement production trials were run with these grinding systems in the same cement plant by using the same clinker/gypsum feed to produce cements and ground in a laboratory ball mill with steel balls as grinding media Clinker and gypsum were crushed into small particle less than 67 mm diameters prior to grinding procedure, and the total feed weight was 5 kg per mill and the grinding time was kept the same as 30 min for each ground cement 223 Grinding efficiency test The fineness of Effects of Polycarboxylatebased Grinding Aid on the 2016年11月22日 The grinding zone temperature elevation is dependent on the grinding efficiency and the proportion of grinding energy that enters the workpiece Experimental results (Rowe, Morgan, Black, Mills, Citation 1996 ) show that the energy transfer proportions between the workpiece and grinding wheel remain relatively constant; albeit the energy distribution is Effect of different parameters on grinding efficiency and its 2022年5月9日 Cement production is one of the most energyintensive manufacturing industries, and the milling circuit of cement plants consumes around 4% of a year's global electrical energy production It is well understood that modeling and digitalizing industrialscale processes would help control production circuits better, improve efficiency, enhance personal training systems, Modeling of energy consumption factors for an industrial cement
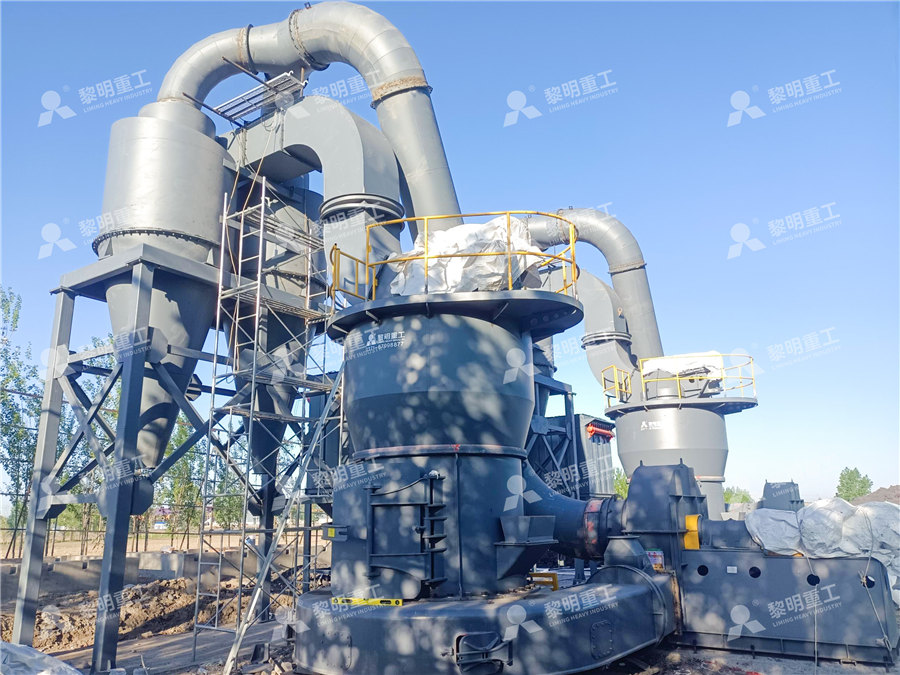
Grinding SpringerLink
2022年2月28日 This is closely dependent on the grinding system and the Abouzeid, AZ: The energy efficiency of ball milling in comminution Int J Miner Process 67 Toroglu, I, Çuhadaroglu, D, Yigit, E: Open and closed circuit dry grinding of cement mill rejects in a pilot scale vertical stirred mill Powder Technol 139 EUR 24592 EN 2010 Energy Efficiency and CO2 Emissions: Prospective Scenarios for the Cement Industry JA Moya, N Pardo, A MercierReqNo JRC59826 jrc2010energy efficiency and co2 emissions2018年7月1日 Energy optimization of a circuit has been subject of many of the studies Jankovic et al [12] considered the optimization alternatives of cement grinding circuits Benzer [13] studied on optimizing the fully airswept raw mill grinding circuit, Dundar et al [14] reported the optimization opportunities of a cement grinding circuitEnergy and cement quality optimization of a cement grinding circuit PROCESS AUDIT AT A GRINDING PLANT (CEMENT MILL) AT A CEMENT FACTORY A CASE STUDY IN ROMANIA CristianBogdan CIOBANU1, Gheorghe VOICU2, IrinaAura ISTRATE2, Paula TUDOR2, BiancaStefania ZABAVA2 1CEPROCIM SA Bucharest, 6 Preciziei Blvd, District 6, Bucharest, Romania 2University Politehnica of Bucharest, Department of PROCESS AUDIT AT A GRINDING PLANT (CEMENT MILL) AT A CEMENT
.jpg)
The Cement Plant Operations Handbook International Cement
Emergency power – 12 Plant control systems 6 Cement milling process summary data – 8 Typical equipment downtime 110 1 Storage of clinker and other components – 2 Cement milling – 3 Separators (classifiers) – 4 Ball mill circuit control – 5 Cement storage – 6 Cement dispatch – 7 Distribution – 8cement and raw material grinding Whereas the MPS mills for cement grinding and raw material grinding have been equipped with a power range between 500 up to 5 400 kW resp 6 400 kW, the MVR mill covers a range with installed power between 60 up to 11 500 kW Equipped with the socalled MultiDrive® there is a lot of available scope to go upReprint Sonderdruck aus Cement International 62021 Gebr2012年6月1日 Cement production in the world is currently about 16 billion ton per year About 2% of the electricity produced in the whole world is used during the grinding process of raw materials [1]While total electrical energy consumption for cement production is about 100 kWh/ton of cement, roughly two thirds are used for particle size reduction [2]Reducing energy consumption of a raw mill in cement industry1987年7月1日 Grinding in the cement industry is a uery energyexacting process, therefore it is essential that these systems should operate with the highest possible efficiency The CEMEXPERT grinding expert system assists the operator CEMENT MILLSEPARATOR SYSTEM FrL~NAMEl TC1MA21DAT 21VJ51985 12:30 1'1ASS FLOW Ct/h) Cemexpert: An Expert System for the Cement Grinding Process
.jpg)
Cement Manufacturing Process: Know Extraction, Processing
2024年9月10日 Steps of Cement Manufacturing The steps involved in cement manufacturing are as follows: Quarrying: Raw materials such as limestone and clay are extracted from quarries or mines; Crushing and Grinding: The extracted raw materials are crushed and ground into a fine powder; Blending: The crushed and ground raw materials are blended in specific proportions Table 5 EnergyEfficiency Opportunities Applicable to Vertical Shaft Kilns 17 Table 6 Energy Efficiency Measures for Final Grinding of Products in Cement Plants 19 Table 7 Energy Efficiency Measures for Plant Wide Measures in Cement Plants 21 Table 8Energy Efficiency Improvement Opportunities for the Cement 2022年2月15日 Electricity consumption is a major energy efficiency indicator in cement raw materials grinding system Advance prediction of electricity consumption provides the basis for cement production scheduling and achieves the energy saving However, due to the influence of strong coupling, delay, intrinsic nonlinearity and uncertainty, it is difficult to model the raw SALSTMs: A new advance prediction method of energy consumption 2022年1月1日 A pilotscale grinding technology of ceramic medium stirred mill was proposed in this study Based on the specific productivity and grinding efficiency, the appropriate grinding parameters were ascertained as follows: material ball ratio of 07, ceramic ball medium size ratio (10 mm: 15 mm: 20 mm = 3:2:5), stirring speed of 110 rpm, grinding concentration of 50%, Highefficiency and energyconservation grinding technology using
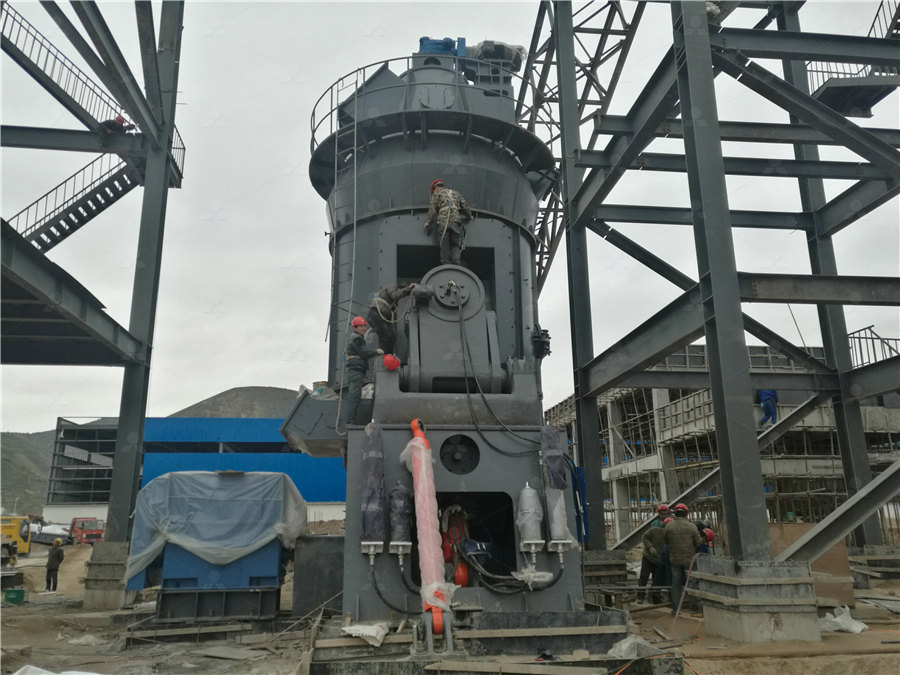
SikaGrind® for vertical roller mills
The grinding of the finished cement consumes approximately one third of the total electrical energy of a cement plant Vertical Roller Mills (VRM) have a clearly higher energy efficiency than ball mills, even if the ball mill is combined with a combined with pragmatical tests on a pilot mill of Loesche GmbH in Germany, proved some Raw material and cement grinding are the first and the last major process steps during cement production The energy demand of these two processes amounts to up to ~70% of the electrical energy used in a cement plant For you as participant, this training will help to obtain a better understanding of the comminution processes as well as the equipment used for grinding The Grinding Technology in Cement Production2020年7月1日 The term chemical additives or grinding aids (GAs) refers to any substance which results in increased grinding efficiency and reduction in power consumption when added to the mill charge (amounts not exceeding 025 wt% of the feed) during grinding [1], [2], [3]The use of grinding aids to increase mill throughput is quite common in the cement industry [2], [4], [5]A critical review on the mechanisms of chemical additives used in 2014年10月15日 Energy and exergy analyses for a cement ball mill of a new generation cement plant and optimizing grinding process: A case study Advanced Powder Technology, Volume 31, Issue 5, 2020, pp 17961810 Vahab Ghalandari , Ahad IranmaneshThe influences and selection of grinding chemicals in cement grinding
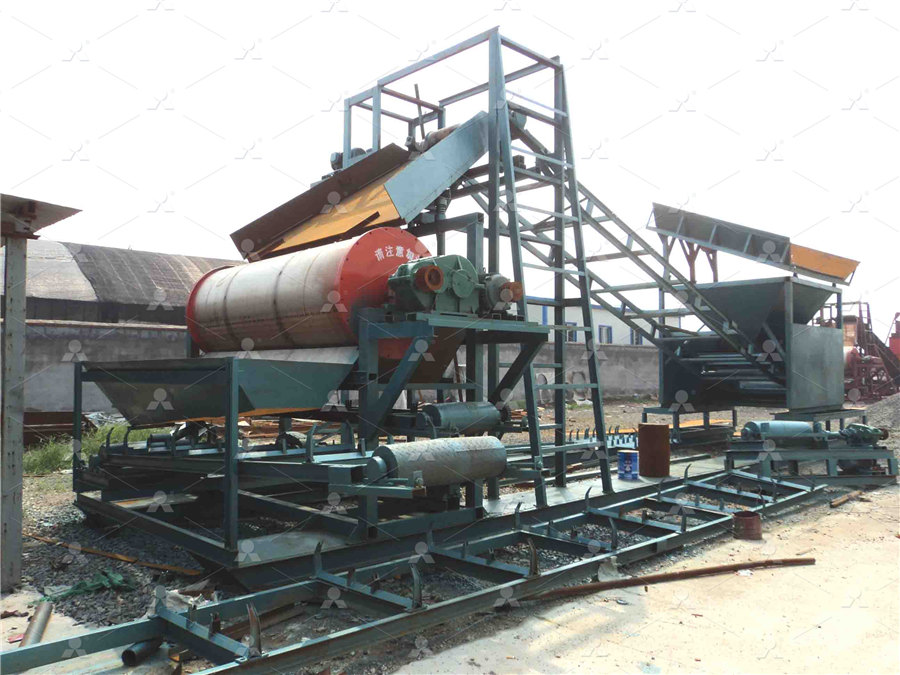
Modeling Based on the Extreme Learning Machine for Raw Cement Mill
2015年1月1日 Vertical grinding mill is the main grinding equipment for the newtype dry cement raw meal production, raw material grinding process in cement industries accounts for approximately 50#8211;60#160;% of the total energy consumption The dynamic characteristics of theImproving Thermal and Electric Energy Efficiency at Cement Plants: International Best Practice iii LIST OF FIGURES Figure 1: Cement Production Process Flow Schematic and Typical Energy Efficiency Measures 2 Figure 2: Rotary Cement Kiln (Dry Process with Cyclonic Preheaters) 4 Figure 3: Schematic Depiction of Control Points and Parameters in a Kiln System Control IMPROVING THERMAL AND ELECTRIC ENERGY EFFICIENCY AT CEMENT flowable powder before entering the kiln There are four main types of grinding systems in use: Tube Mill (or Ball Mill) – materials are crushed inside a rotating tube – up to 6 m in diameter and 20 m long – containing metal balls that tumble against the materials Tube mills are the most energy intensive of the four mill systems3Carbon emissions reductions for a specific new cement plant: ENERGY Pfeiffer's compact mill solution is perfectly suited for annual production rates of up to 550,000 tons of cement, energyefficient grinding system; different plant sizes available; compact modular design; The above flow sheet shows the Modular grinding plant Mill system ready2grind
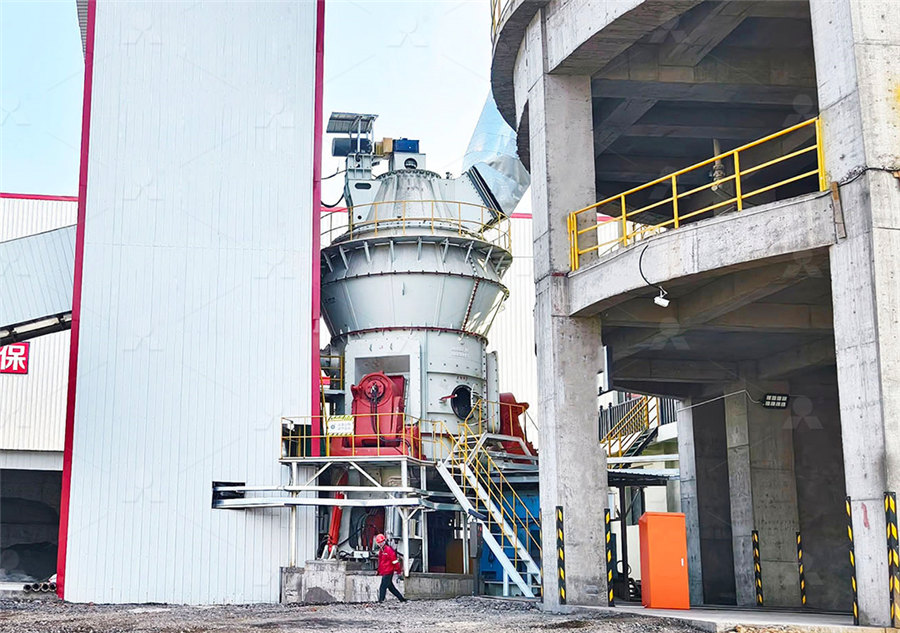
Energy conservation and consumption reduction in grinding
2023年11月1日 The ball mill on site, has problems such as uneven product particle size, low grinding efficiency, insufficient dissociation degree of useful mineral monomers, and high grinding energy consumption[[20], [21], [22], [33], [34]]The existing technological process of the first beneficiation workshop of Gongchangling Concentrator is as follows: twostage crushing, Olsen, Daniel, Sasank Goli, David Faulkner, Aimee McKane 2010 Opportunities for Energy Efficiency and Demand Response in the California Cement Industry PIER Industrial/Agricultural/Water End‑Use Energy Efficiency ProgramOpportunities for Energy Efficiency and Demand Response in the 2023年11月6日 The mode of action of GAs in improving the properties of cement is not fully understood []However, the proposed mechanisms are mostly pinned on two principles: first, the impact on particle distribution and material flow qualities; and second the chemical–physical influence on individual particles, for instance, surface energy reduction [21, 22]Review of the Effect of Grinding Aids and Admixtures on the Improving Thermal and Electric Energy Efficiency at Cement Plants: International Best Practice iii LIST OF FIGURES Figure 1: Cement Production Process Flow Schematic and Typical Energy Efficiency Measures 2 Figure 2: Rotary Cement Kiln (Dry Process with Cyclonic Preheaters) 4 Figure 3: Schematic Depiction of Control Points and Parameters in a Kiln System Control IMPROVING THERMAL AND ELECTRIC ENERGY EFFICIENCY AT CEMENT
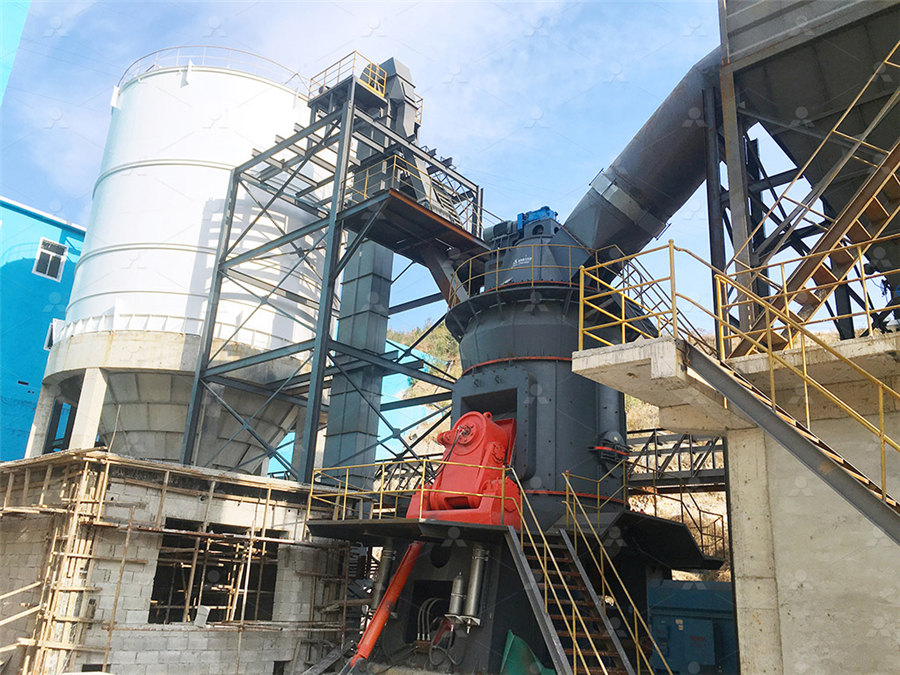
Energy Efficiency and CO2 Emissions: Prospective Scenarios for
decarbonising the energy system by 80 % by 2050 will require reinvention of the European energy system between now and 2050 and have a profound effect on its technology mix The EU Strategic Energy Technology Plan (SETPlan) is the technology pillar of the EU’s energy and climate policy It was adopted in 2008 by(DOI: 101016/JAPT202002013) Nowadays, ball mills are used widely in cement plants to grind clinker and gypsum to produce cement In this work, the energy and exergy analyses of a cement ball mill (CBM) were performed and some measurements were carried out in an existing CBM in a cement plant to improve the efficiency of the grinding process The first and second laws Energy and exergy analyses for a cement ball mill of a new kiln and raw mill, alkali bypass, clinker cooler, cement and coal mill, in terms of exit gas quantity, temperature, dew point, dust content and particle size It is seen that all these characteristics have a wide range of variance The ESP system must effectively deal with these variations The ESP system must effectively deal with these Energy Optimized Modern Air Pollution Control System for Cement 2020年5月1日 In this study, the CBM unit of Kerman Momtazan Cement Company (KMCC), which is a Portland cement factory, and it is located in the southeast of Iran, was considered as a case study for the exergy and energy analyses The KMCC cement grinding system consists of a closed circuit ball mill, and it was supplied in 2006 by KHD Humboldt Wedag Energy and exergy analyses for a cement ball mill of a new