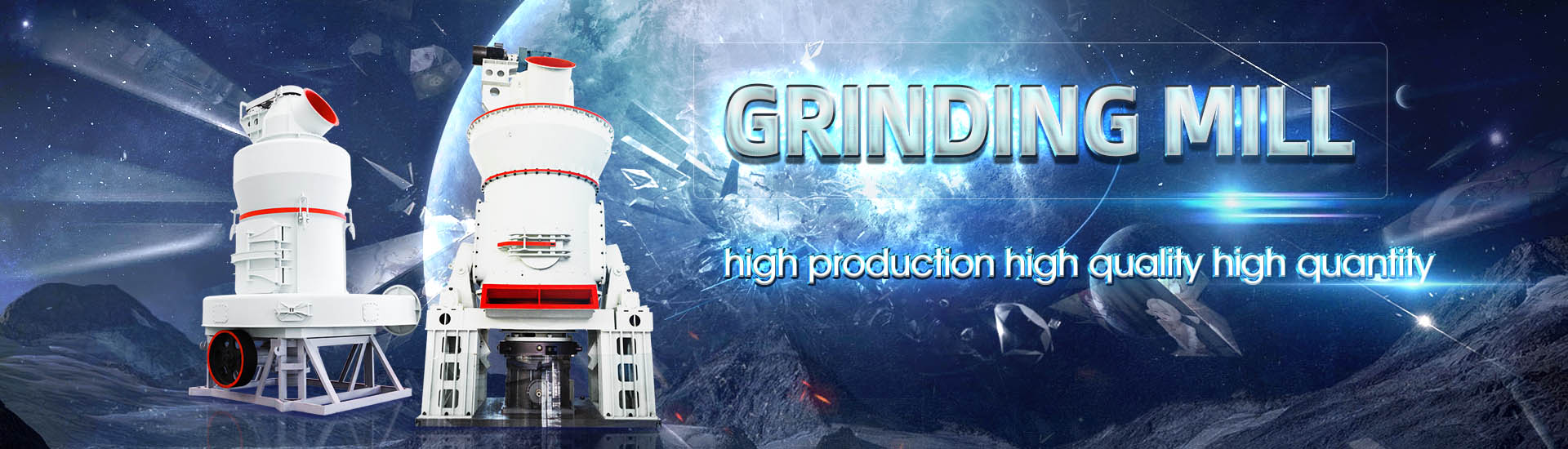
Uses of iron oxide grinding mill
.jpg)
An investigation on optimum grinding system and conditions for
2020年10月1日 This study aims to characterize and then determine the method which allows for a high efficiency and quality for grinding the αFe 2 O 3 red powder into red iron oxide pigment 2023年4月3日 In modern cold rolling mills in the steel industry, iron oxide powder is produced as a byproduct when used pickling agents are recycled Further processing of these iron oxide powders could enable the production of Manufacturing and Properties of Spherical Iron 2024年6月3日 In recent years, the use of ball milling to synthesize biochariron based materials has become an emerging and promising method due to its low cost, environmental Research progress on synthesis mechanism and performance5 天之前 Advantages of Using HGM80 for Iron Oxide Grinding 1 High Precision: Achieves ultrafine powder with consistent particle size, meeting industry requirements 2 Energy Iron Oxide Grinding Production Line With HGM80 Ultrafine Mill
.jpg)
Structure and Magnetic Properties of Iron Oxide Springer
2024年7月8日 Iron oxide nanoparticles have been fabricated using the electric wire explosion (EWE) technique The structure and magnetic properties of the nanoparticles have been 2022年1月21日 Mechanical milling is a simple reaction that utilizes milling iron powders such as hematite (Fe 2 O 3) alongside other metal oxides to produce IONPs Welding, fracturing, Approaches on Ferrofluid Synthesis and Applications: Current 2022年3月1日 In this work, we report the characterization of iron oxide waste scales obtained by rolling mill steel industry The sample was obtained during the mechanical cleaning of the Characterization of iron oxide waste scales obtained by rolling mill 2011年1月1日 Grinding mills typically used in the process include the attrition jet, planetary, oscillating and vibration mills, all of which are classified as highenergy mills Among these Preparation of iron oxide nanoparticles by mechanical milling
.jpg)
A Review of the Grinding Media in Ball Mills for Mineral Processing
2023年10月27日 Grinding media play an important role in the comminution of mineral ores in these mills This work reviews the application of balls in mineral processing as a function of the Iron ore is an important industrial source, a kind of iron oxide ore, an economically available mineral aggregate containing iron element or iron compound, and there are many kinds of iron ore Among them, ironmaking products mainly include magnetite, siderite, hematite and so onuses of iron oreiron ore grinding milliron ore Raymond mill Manufacturing Uses of Iron Oxide Iron Oxide: There is a natural Iron Oxide and Synthetic Iron Oxide from the steel mill When they produce the cold steel rolling plate in steel mill, they wash the plate by hydrochloric acid to remove the Manufacturing Uses of Iron Oxide EGTechGrinding Mills: Ball Mill Rod Mill Design PartsCommon types of grinding mills include Ball Mills and Rod Mills This includes all rotating mills with heavy grinding media loads This article focuses on ball and rod mills excluding SAG and AG Grinding Mills 911Metallurgist
.jpg)
The six main steps of iron ore processing Multotec
When iron ore is extracted from a mine, it must undergo several processing stages Six steps to process iron ore 1 Screening We recommend that you begin by screening the iron ore to separate fine particles below the crusher’s CSS before the crushing stage A static screen is used to divert the fine particles for crushing2014年9月23日 It is one of the wastes generated in steel plants and represents around 2 % of the produced steel It is a hard brittle coating of several distinct layers of iron oxides formed during the processing of steel and composed mainly of iron oxides and may contain varying amounts of other oxides and spinels, elements and trace compoundsGeneration Transport and Uses of Mill Scale – IspatGuru2011年1月31日 Request PDF Preparation of iron oxide nanoparticles by mechanical milling Hematite powder (Fe2O3) was ground in a planetary mill and the milling time and mill rotational speed were varied at Preparation of iron oxide nanoparticles by mechanical milling2010年7月1日 According to [2], cast iron with major composition of 95% elemental iron is used to manufacture local cornmill plates The paramount drawback of this material, however, is its susceptibility to Corrosion of Cast Iron Mill Plates in Wet Grinding ResearchGate
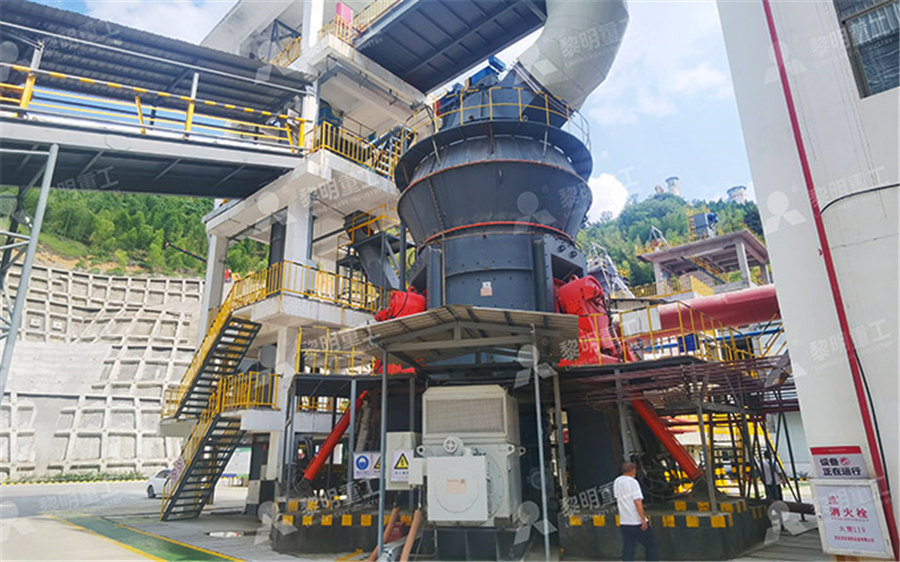
An investigation on optimum grinding system and conditions
2020年10月1日 After some other processes, αFe 2 O 3 red powder particles byproduct of regeneration of spent pickling liquor in ARP in iron and steel industry should be ground up to pigment grade to convert it to a value added product, red iron oxide pigment In this study, grinding tests on αFe 2 O 3 red powder were performed using four different types of 2015年4月9日 The drum diameter is limited to 06 or 07 times the length of the mill Rod mills are used for grinding hard minerals This type of mill is normally used as the first stage of a milling process to provide a reduced size feedstock for a further milling processGrinding Mills and Their Types – IspatGuru2000年12月15日 The first consideration is the material to be ground This determines the kind of abrasive you will need in the wheel For example, aluminum oxide or zirconia alumina should be used for grinding steels and steel alloys For grinding cast iron, nonferrous metals and non=metallic materials, select a silicon carbide abrasiveChoosing The Right Grinding Wheel Modern Machine ShopKeywords: micaceous iron oxide (MIO), magnetic separation, belt type high gradient magnetic separator, high gradient magnetic separator, pulsating high gradient magnetic separator 1 Introduction Natural iron oxides occur widely, and are exploited from a variety of deposit types World iron oxide pigment mine production in 2014 is given in Table 1Micaceous iron oxide production by application of magnetic
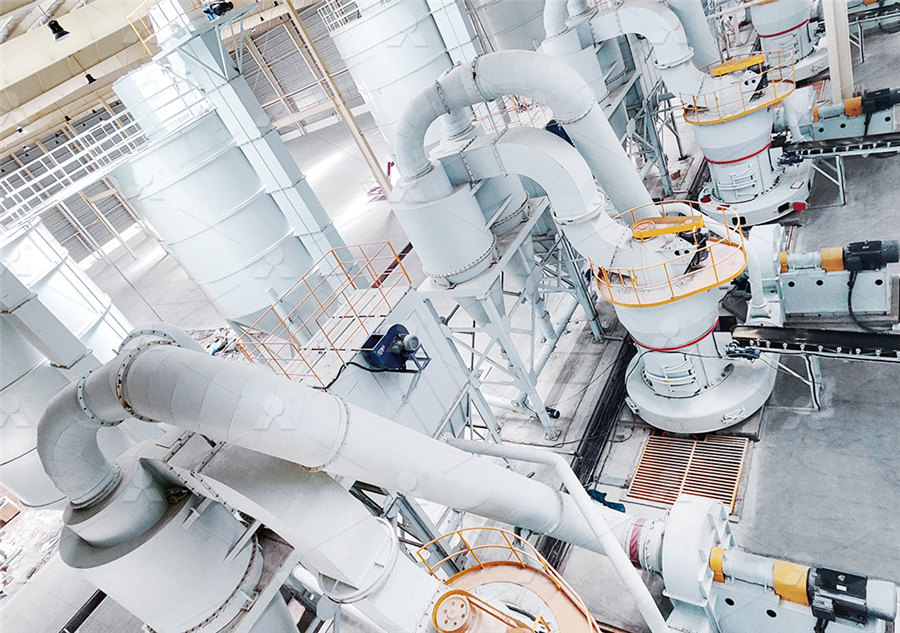
Iron Oxide Pigments 911Metallurgist
2021年1月4日 Until the late 19th century iron oxide pigments were obtained wholly from natural materials, generally with little alteration other than physical purification In some cases roasting or calcination was also carried out However, beginning in the first part of the 20th century, chemical methods were developed for synthetic production of commercial iron oxides2021年5月17日 The mill scale is a waste from the iron and steel industry Due to the high content of iron in the form of oxides, it is an attractive material for the recovery of metallic iron by reductionRecovery of Iron from Mill Scale by Reduction with Carbon 2019年8月5日 By enriching iron oxides from dust and sludge, as well as lowgrade iron ore fines; they can be produced iron oxidecoal composite pellets which are used subsequently for cast iron and steel An Overview: Utilization of Iron Ore Fines and Steel Plant Wastes2023年11月24日 Cast iron grinding media are one of the ancient media, In order to increase the efficiency of the grinding mill, Stoimenov et al Kitamura, SY; Privat, K; Sahajwalla, V Behaviour of Sulphide and NonaluminaBased Oxide Inclusions in CaTreated HighCarbon Steel Metall Mater Trans B Process Metall Mater ProcessGrinding Media in Ball Mills for Mineral Processing
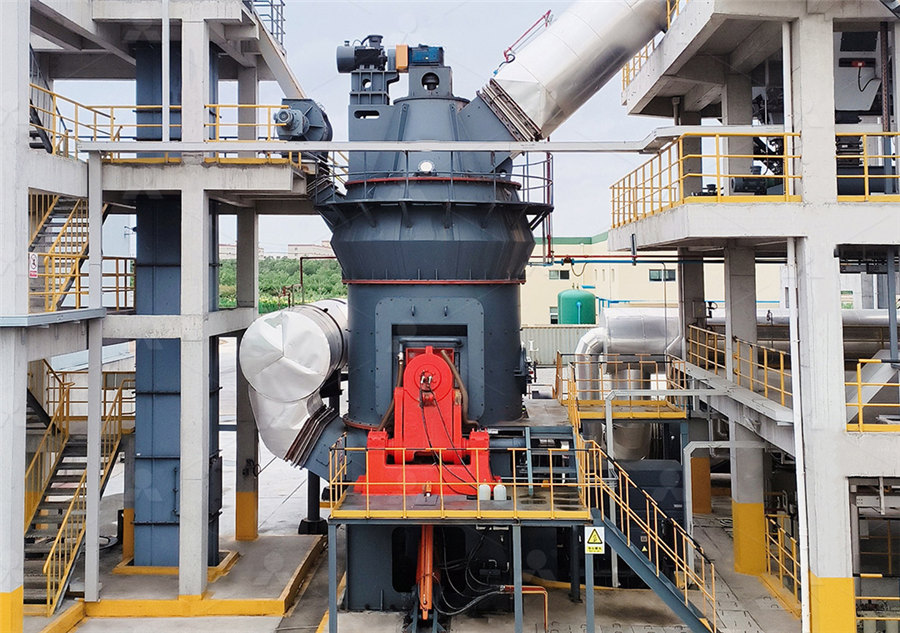
Grinding of Australian and Brazilian Iron Ore Fines for Low
2024年2月26日 Oxidised pellets have become an indispensable highquality charge for blast furnaces Nevertheless, highquality pellet feeds are becoming scarcer and scarcer To broaden the range of sources of pellet feeds and reduce the production cost of pellets, more steel mills are predicted to use coarse iron ore fines with a relatively low iron grade and low impurities for the 2023年12月29日 Mill scale, also known as iron oxide scale, Step 2: Grinding The screened mill scale is sent to a FTM Ball Mill for further grinding The discharge particle size can be controlled at or below 100 mesh according to actual needs The longer the grinding time, How to Turn Waste Mill Scale into Valuable Briquettes?2010年1月1日 Mill scale was recycled as iron oxide powder and used to reinforce 3Dprinted acrylonitrile–butadiene–styrene (ABS) matrix composite filaments Prepared mill scale powder was added to ABS Elaboration of iron powder from mill scale ResearchGateIn order to make better use of sinter return ore and iron oxide scale to achieve effective predephosphorization of molten iron, the effects of final slag morphology, mineral phase structure and Analysis of iron contained in mill scale Download Table
.jpg)
Oxide Strengthening of Iron Oxidized with Air
2020年10月28日 As a result of surface oxide dissolution during ball mill grinding of oxidized iron powder, spark plasma sintering (at temperature of 1000 °C and a pressure of 80 MPa), cold rolling with 88% reduction and recrystallization annealing at 1100 °C (05 h), bulk iron samples, containing strengthening FexO oxides of 32 nm in size, were obtained It is demonstrated that Similarly, the mill's grinding media filling level should be maintained at a constant level If the grinding balls fall below a certain diameter due to wear, CeraBeads are ceriumstabilized zirconium oxide grinding media of a high density and Grinding Media, Grinding Balls NETZSCH Grinding 2022年3月1日 Moreover, the characteristics of pigments obtained from recycled iron oxides are greatly affected by the grinding, milling and heat treatment processes and also by hematite content In addition, oxide scales obtained during rolling have different magnetic properties after magnetic separation [ 6 ]Characterization of iron oxide waste scales obtained by rolling mill of mill scale were used for tests, in the original state and after grinding to develop the surface Keywords: metallurgical waste; mill scale; iron reduction; pyrophoricity; TG/DTA thermal analysis 1Recovery of Iron from Mill Scale by Reduction with Carbon
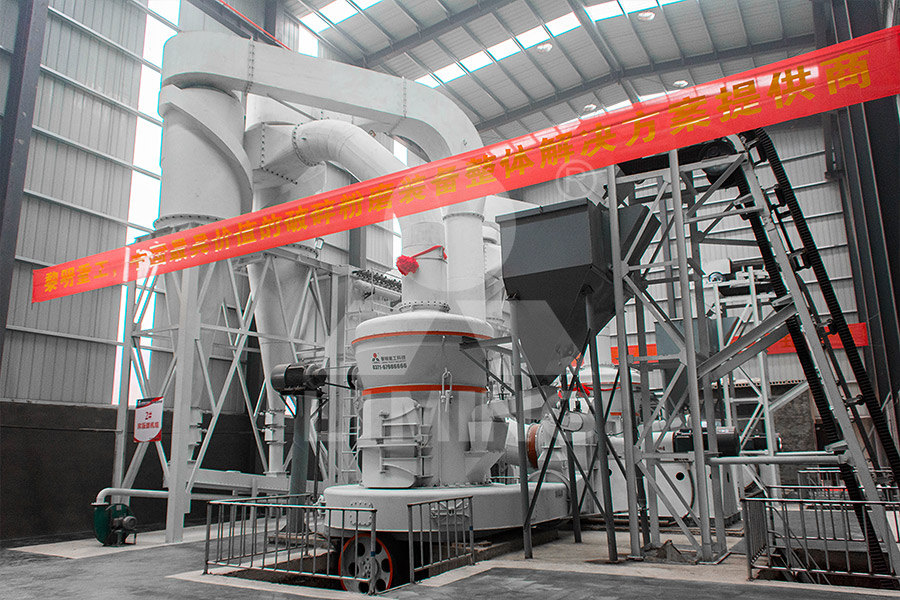
Examination of Oxide Scales of Hot Rolled Steel Products JSTAGE
preparing purely oxidized samples, water was used as the grinding lubricant However, when grinding sulfidized samples, it was found necessary to use kerosene as a lubricant to avoid reaction between the sulfidation products and water Further grinding on finer abrasive papers (1000 grit, or 1200 grit) was found unnecessary If the grinding Aluminum oxide occurs in two different forms, the crystalline polymorphic phase αAl 2 O 3 as well as the metastable cubic γAl 2 O 3 γAluminum oxide is turned into αAl 2 O 3 when heated Crystalline αaluminum oxide is often used for ceramic insulators or as abrasives and has a Mohs hardness of 9 to 95Aluminum Oxide Grinding on Bauermeister Universal or Gap Mill2017年8月11日 2 Types of the grinding media Most of the industries are using the grinding media, and the grinding media ball is available in different kinds such alumina oxide balls, flint pebbles, cylpebs, highdensity media, and others The grinding ball is expensive, and it is helical rolling of the round billet Highdensity media The highdensity media is specially developed for Different types of grinding media and its uses PDF SlideShare2020年6月29日 Wheel speeds are measured in surface feet per minute (SFPM) Vitrified bonds are commonly used to 6,500 SFPM or in selected operations up to 12,000 SFPM Resinoidbonded wheels may be used for speeds up to 16,500 SFPM Grinding pressure Grinding pressure is the rate of infeed used during a grinding operation; it affects the grade of wheelChapter 16: Grinding Wheels and Operations American Machinist
CFB石灰石脱硫剂制备96.jpg)
Process Mineralogical Assessment of the Grinding Products of the
2022年1月13日 For finegrained iron oxide minerals, the iron oxide minerals distribution of 80–100% composition class differed by 22% at −75 + 53 μm size fraction with the two grinding methods, and its The Raymond mill, also called Raymond roller mill, combines grinding, classifying, and if necessary, drying, in one machine to produce precisely sized powders to meet exact production specificationsIt is an efficient fine grinding machine for largescale powder production Applied materials: various nonflammable and explosive minerals such as gypsum, talc, calcite, Raymond Mill2009年1月1日 Also, equipment like ball mill is used at the final stages of grinding Among the comminution and grinding equipment, HPGR is increasingly utilized as tertiary crusher or primary mill because of Processing of Magnetite Iron Ores–Comparing Grinding Options2023年6月12日 1 Grind bulk silverrich gold ore to a finer size by using a ball mill 2 Leach the flotation tailings 3 Use cyanidation to extract gold and silver 3 Iron oxide copper gold ore Properties of iron oxide copper gold ore Iron oxide 8 Types of Gold Ore Properties and Ways to Process
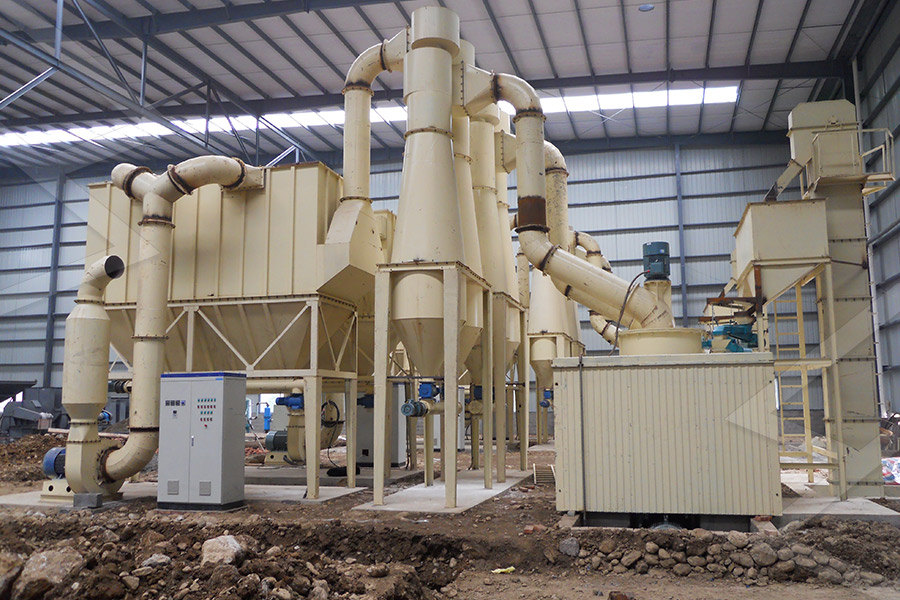
RecoDust—An Efficient Way of Processing Steel
2019年4月5日 RecoDust is believed to be an efficient way of processing steel mill dusts to produce reusable secondary raw material resources The rising costs of the steel production process and the increasing public attention towards 2021年5月17日 The mill scale is a waste from the iron and steel industry Due to the high content of iron in the form of oxides, it is an attractive material for the recovery of metallic iron by reduction The product of mill scale reduction is an Recovery of Iron from Mill Scale by Reduction with 2024年8月2日 The beneficiation of lowgrade iron ores is a key research and development topic in the mineral processing industry The gradual exhaustion of highgrade iron ore reserves, and rising consumer iron and steel demand globally necessitate efficient lowquality iron ore beneficiation to meet steelmaking quality requirements This comprehensive review explores Exploring LowGrade Iron Ore Beneficiation Techniques: A MDPI2021年10月12日 Mechanochemistry is driven by mechanical energy input, which often alleviates the need for solvents or heating to achieve desired products Here, the author reviews mechanochemical syntheses of Mechanochemical synthesis of metal oxide nanoparticles
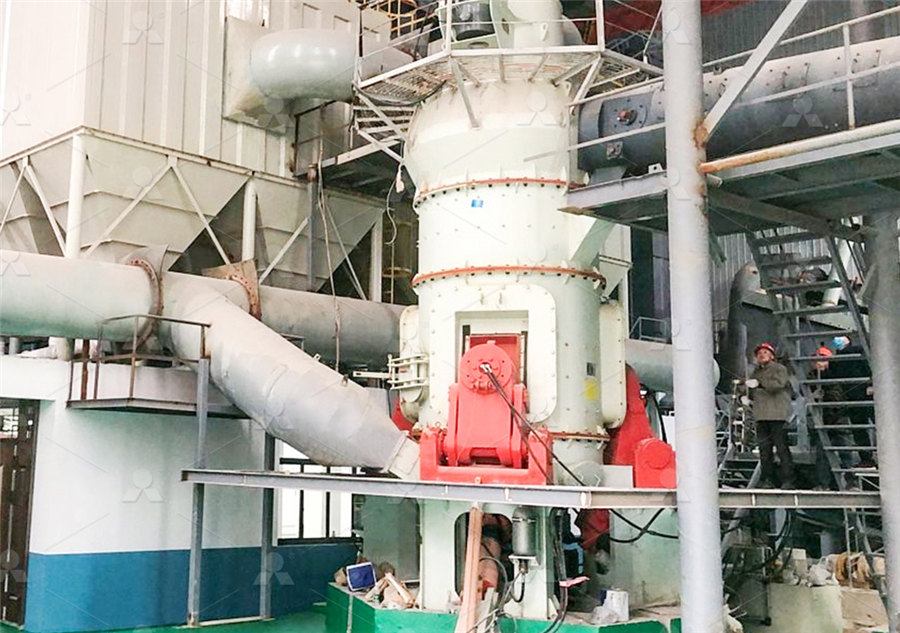
Iron Oxide Structure, Properties, Preparation and Uses Vedantu
Iron oxide, which is also called ferric oxide, is an inorganic compound having the chemical formula Fe 2 O 3It is one of the 3 major oxides of iron, and the remaining two being iron(II) oxide (FeO), which is the rare iron (II, and III) oxide (Fe 3 O 4), and also naturally takes place as the mineral magnetiteSince the mineral is referred to as hematite, Fe 2 O 3 is iron’s primary source for 2009年8月1日 Mill scale is an iron oxide waste generated during steelmaking, casting and rolling Total generation of mill scale at JSWSL is around 150 t/day and contains 60–70%FeO and 30–35%Fe2O3Recycling of steel plant mill scale via iron ore ResearchGate2018年11月21日 Harder than standard aluminium oxide with a very sharp abrasive grain It is a versatile material, recommended for grinding relatively soft metals such as aluminium or cast iron but can also be used on extremely hard materials such as cemented carbide Zirconia Alumina For use in rough grinding applications where high stock removal is requiredWhich Grinding Wheel Should I Choose? Norton Abrasives UK2 Due to the grinding method of the magnesium oxide grinding mill, there is basically no iron consumption and the product is pollutionfree 3 The working principle of magnesium oxide grinding mill machine is that it does not need to drive heavy grinding bodies, with high power utilization rate and 50% energy accumulation compared to ball Preparation Of Refractory Material From Fused Magnesia Grinding
.jpg)
Iron and Steel Slags SpringerLink
2017年3月5日 The principal raw materials for an integrated mill are coal (or coke), iron ore, and limestone, which are charged in batches into a blast furnace In the blast furnace thereby requiring a greater grinding work than clinker Moreover, since iron is Furthermore, because of its high iron oxide content, fresh BOFS may not be a