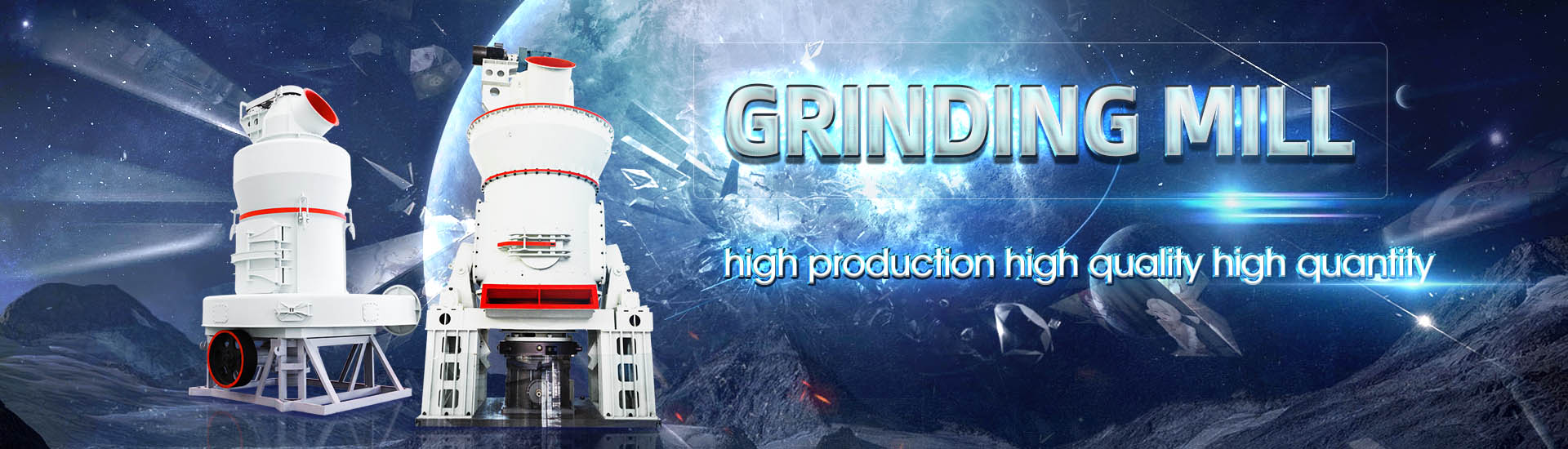
Hua Electricity and energy Mudanjiang Power Plant COSCO Group cement clinker
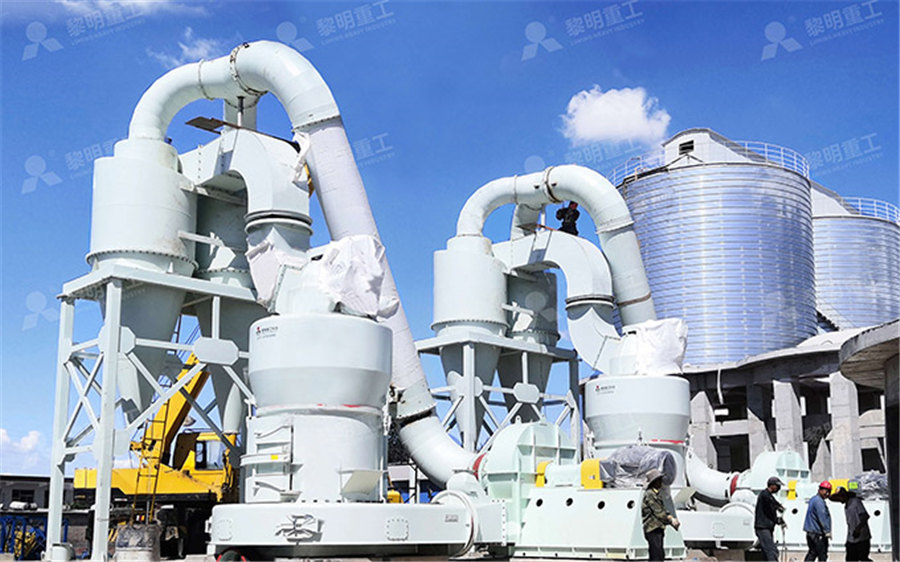
Power plant profile: Mudanjiang 2nd Thermal Power Plant, China
Mudanjiang 2nd Thermal Power Plant is a 600MW coal fired power project It is located in Heilongjiang, China According to GlobalData, who tracks and profiles over 170,000 power 2022年4月12日 To provide highquality data to estimate China’s processrelated emissions from cement production, this study developed a panel dataset for the cement industries of China’s China’s provincial process CO2 emissions from cement production 2023年9月15日 In China, the clinker to cement ratio experienced a downward trend for 25 years and reached 566 % in 2015 However, afterward, it rebounded to 660 % in 2020 owing to the Historical trend and decarbonization pathway of China's cement 2019年12月1日 The required electrical energy input for calcination in a kiln system producing 1 Mt of clinker per year, is about 85 MW An earlyphase cost estimate was conducted resulting Combined calcination and CO2 capture in cement clinker
.jpg)
The cement plant of tomorrow ScienceDirect
2023年11月1日 Cement plants of tomorrow will have to implement all CO 2 abatement and saving measures to the best extent possible Reducing the clinker factor, optimising the 2020年10月1日 In this article, future demand for concrete and cement has been quantified By studying different energy transition scenarios, the cement manufacturing process and the The impact of future power generation on cement demand: An 2019年3月8日 Improving Thermal and Electric Energy E ciency at Cement Plants: International Best Practice 1 Cement production is a resourceintensive practice involving large amounts ofIMPROVING THERMAL AND ELECTRIC ENERGY EFFICIENCY AT Clinker, and clinker substitutes, are the active components that confer cement its binding properties Producing traditional cement clinker is an extremely energy and CO2 intensive Deep decarbonisation of industry: The cement sector Europa
.jpg)
Peak cementrelated CO Wiley Online Library
2019年2月8日 Branger and Quirion investigated the changes of CO 2 emissions in the European cement industry from 1990 to 2012 and found that most of the emission change (activity, 2023年12月11日 The mitigation effects of waste fuels and SCMs on existing cement plants are explored based on the countrylevel energy structure and clinkertocement ratio dataProjecting future carbon emissions from cement production in 2018年12月31日 Energy recovery and exergy recovery in a clinker cooler was a major factor in optimizing clinker production and cement grinding process, the running clinker cooler has an energy recovery was 4831 Energy and Exergy Analysis of Clinker Cooler in the 2020年6月24日 The method of the cement production and the thermal energy losses across the preheater tower, kiln and clinker cooler etc has been studied for the reference cement plant (Emami cement) The total thermal energy losses were found as 45% through radiation and convection, whereas 41% from the surface of the kiln, 35% from the preheater, 15% from the Thermal energy consumption and its conservation for a cement
.jpg)
Benchmarking of Energy Consumption and CO2 Emissions in Cement
2024年2月2日 Gholipour Khajeh M, Iranmanesh M, Keynia F (2014) Energy auditing in cement industry: a case study Energy Equip Syst 2(2):171–184 Google Scholar Madlool NA, Saidur R, Hossain MS, Rahim NA (2011) A critical review on energy use and savings in the cement industries Renew Sustain Energy Rev 15(4):2042–2060 [online]Specific Heat Consumption in Kcal/kgclinker; Specific Power Consumption in kwh/tonclinker Specific Cooling Air in kgair/kgclinker Specific brick Consumption in grams/tonclinker The overall process of conversion from raw meal to clinker being endothermic demands a theoretical heat of about 380420 kcal/kgclinkerClinkerization Cement Plant Optimization(eg 50 years or longer) There were 110 operating cement plants in the US in 2010, spread across 37 states and Puerto Rico Portland and blended cement was produced at 110 plants in 2010, while masonry cement was produced at 71 plants Clinker was produced at 100 plants (102 including Puerto Rico) in the US in 2010Energy Efficiency Improvement and Cost Saving Opportunities for Cement Clinker cooler: the clinker cooler is heat exchange equipment, clinker cooler use air as medium, pass through the hightemperature clinker and cool the cement clinker, at the same time, recovery the waste heat, promote the thermal efficiencyOur cement cooler has advantages of high thermal efficiency, high clinker quality, fast cooling, high operation rateClinker Plant Cement Plant Cement Equipment For Clinker
.jpg)
Energy Savings Measures for Clinker Production in Cement Industry
2012年1月1日 The specific thermal energy consumption was reduced from 3900 kJ/kg clinker in 1990 to 3400 kJ/kg clinker in 1995, and the specific electrical power consumption was reduced from over 100 kwh/t 2019年11月18日 Cement is one of the most widely used materials in construction This study presents a processwise evaluation of energy use and CO2 emissions for clinker, Ordinary Portland Cement (OPC) and Study of Energy Use and CO2 Emissions in the Manufacturing of Clinker 2012年3月11日 Because countrylevel and unitlevel fuel consumption for the cement industry is not available, the historical technologybased energy consumption intensities (ie GJ/tonclinker) are first International comparisons of energy efficiency in power, steel, 2022年9月21日 This article is a continuation of the previous article on the indirect mechanosynthesis clinkerization process, which combines mechanical activation (highenergy milling) and thermal treatment at Cement and Clinker Production by Indirect Mechanosynthesis
.jpg)
Optimizing Electrical Energy Consumption In Cement Process Plants
In cement industry Electrical energy is used for many operations like Crushing,Grinding,Rolling etc, The present paper deals with the methods and technologies that can be adopted in cement process plants to optimize Electrical energy consumption to conserve energy Index Terms Cement industry, Energy conservation, Electrical Energy Clinker, and clinker substitutes, are the active components that confer cement its binding properties Producing traditional cement clinker is an extremely energy and CO 2 intensive process In the EU, 90% of clinker is now made via the more energy efficient dry clinkermaking process (2) Older, less efficient wetDeep decarbonisation of industry: The cement sector EuropaThe paper addresses the potential heattopower application of supercritical CO2 (sCO2) plants to the cement industry, thereby reducing their electricity demand and improving energy efficiencySpecific fuel and electricity consumption per ton of 2020年7月3日 As the cement production industry grows and adapts to new technologies and innovations, qualified methods of using alternative fuels will play an important role in ensuring the profitable (PDF) SELECTION AND USE OF ALTERNATIVE FUELS IN THE CEMENT
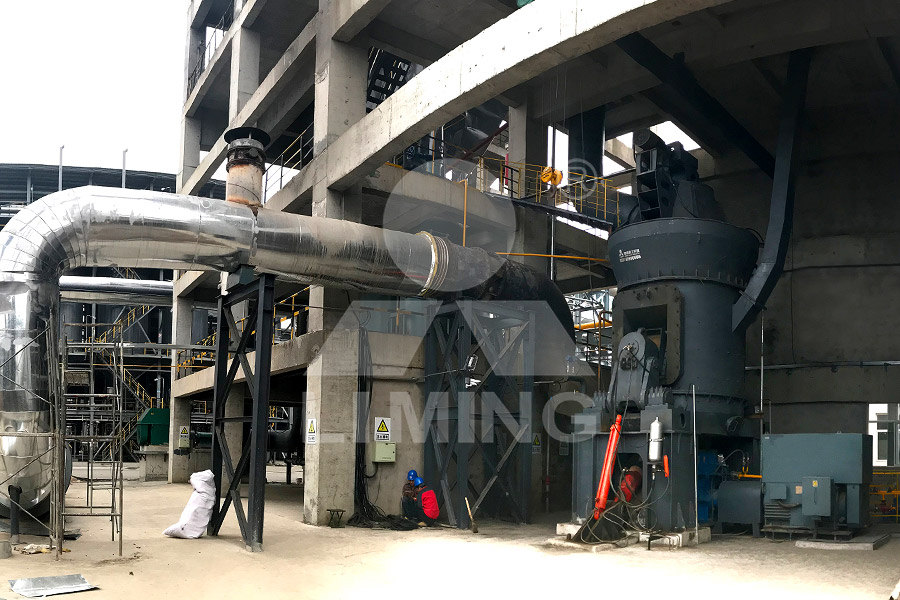
Cement costs and energy economics? Thunder Said Energy
CO2 intensity is estimated at 09 tons/ton in our base case, but there are interesting opportunities for decarbonization Half of the CO2 from a cement plant is 2030% concentrated CO2 from the thermal decomposition of limestone (CaCO3>CaO + CO2) which could be amenable to CCS Switching out solid fuels for gas would save 01 tons/tonAround 100kWh/ton of electricity use 2020年9月14日 Step #4 The burning of the raw meal at approx 1,450°C is carried out in Lepol or preheater kilns that work by varying methods, the main difference being in the preparation and preheating of the kiln feed By chemical conversion, a process known as sintering, a new product is formed: clinker Step #5The essentials of electrical systems in cement plants EEPDownload Table Energy consumption in cement making processes and process types a from publication: Carbon Dioxide Emission from the Global Cement Industry The cement industry contributes about Energy consumption in cement making processes and process 2013年1月1日 Studies on cement production optimisation have been carried out on clinker simulation using AspenTech [36], cement raw materials blending using a general nonlinear timevarying model [37], cement Modelling the cement process and cement clinker quality
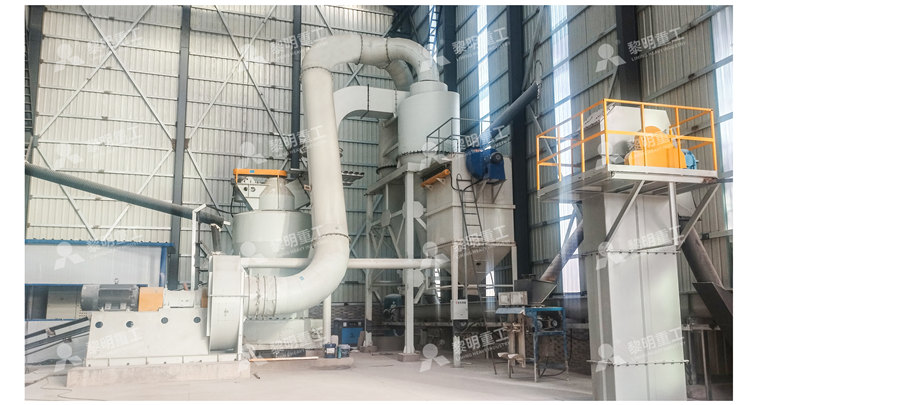
(PDF) Waste Heat Recovery Power Generation Systems for Cement
2015年1月1日 Cement production process is highly energy intensive with approximately 34GJ energy consumption per ton of cement produced Moreover, energy costs are responsible for 25% of total production 2016年3月1日 The second and third, owned by Guohua Electric Power Corp and Beijing Energy Investment Holding Co, were closed in March 2015 The last of its large coalfired power plants, China Huaneng Group Corp’s 845MW plant, is due for closure in 2016 The plants will be replaced by four gasfired stations with 26 times more production capacityCoal for cement: Present and future trends2021年10月1日 Cement is one of the highly energyintensive industries Producing one ton of cement consumes 34GJ which represent about 40% of the variable costs of cement productionPower generation in white cement plants from waste PDF On Aug 1, 2013, Ernst Worrell and others published Energy Efficiency Improvement and Cost Saving Opportunities for Cement Making An ENERGY STAR® Guide for Energy and Plant Managers Find Energy Efficiency Improvement and Cost Saving
.jpg)
(PDF) Waste Heat Recovery Power Generation
2013年4月1日 Since the 1980s, Japanese cement production companies pioneered the introduction of WHRS [22] WHRS is a proven technology that uses Rankinecycle steambased power cycle, Organic Rankine Cycle 2019年10月16日 The production of 1 tonne of Portland cement emits about ranges from 082 and 1 tonnes of CO 2 (Fayomi et al, 2019; Thwe et al, 2021); this quantity is being reduced continuously using energy Perspectives on environmental CO2 emission and energy factor in Cement A cement manufacturing plant requires significant amounts of energy, mainly in the form of heat, to produce clinker Significant amounts of electricity are then required during the milling (grinding) of clinker and other constituents to produce cement – the main binder in concrete For integrated cement plants, energy in the form of heat is Energy Use Cement2013年1月1日 The study evaluates the energy consumption of both wet and dry processes cement manufacturing plant in Nigeria Energy consumption data collected for the period 2003 to 2011 were used to estimate Energy and Cost Analysis of Cement Production Using the Wet
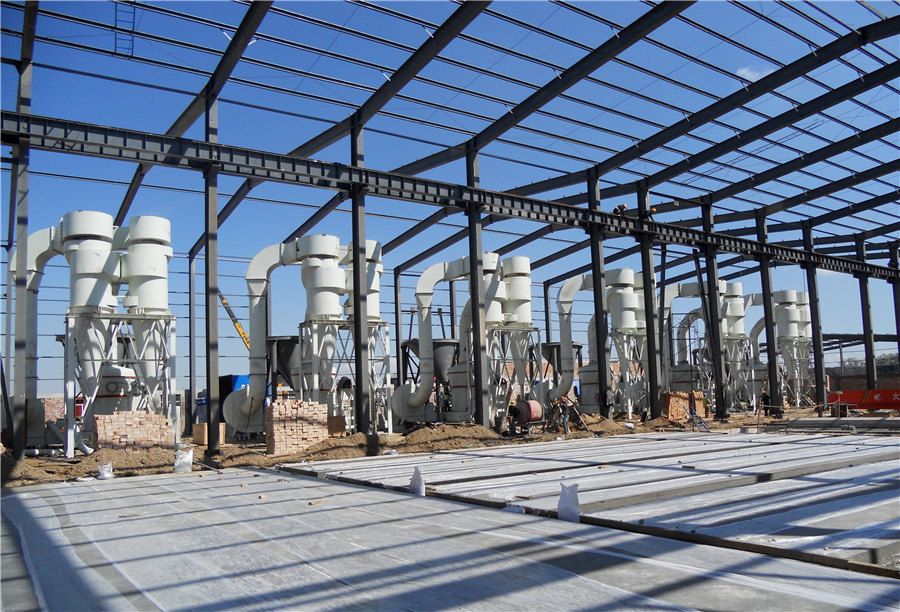
IMPROVING THERMAL AND ELECTRIC ENERGY EFFICIENCY AT CEMENT PLANTS
Improving Thermal and Electric Energy Efficiency at Cement Plants: International Best Practice iii LIST OF FIGURES Figure 1: Cement Production Process Flow Schematic and Typical Energy Efficiency Measures 2 Figure 2: Rotary Cement Kiln (Dry Process with Cyclonic Preheaters) 4 Figure 3: Schematic Depiction of Control Points and Parameters in a Kiln System Control 2015年6月1日 In this paper, implementation of proper energy saving actions in an Iranian cement production plant was studied and several useful methods were suggested to improve energy consumption, since cement industry is considered to be one of the most energy intensive industries [7], [8]Establishment of proper saving actions is necessary to facilitate energy Energy consumption assessment in a cement production plantPDF On Jun 13, 2020, Javed Akhter and others published CEMENT INDUSTRY PREFERENCES FOR CAPTIVE POWER PLANTS IN PERSPECTIVE OF CURRENT ENERGY CRISES OF PAKISTAN Find, read and cite all the (PDF) CEMENT INDUSTRY PREFERENCES FOR CAPTIVE POWER PLANTS 29th March 2019 – Bangkok Constant Energy is pleased to announce that it has executed a Memorandum of Understanding with SCG Cement to deploy 50 MW of solar PV plants under Corporate Power Purchase Agreements for numerous factories of the Group in Thailand, as well as several companies that SCG will introduce to Constant Energy Siam []Siam Cement Group and Constant Energy set to deploy 50 MW
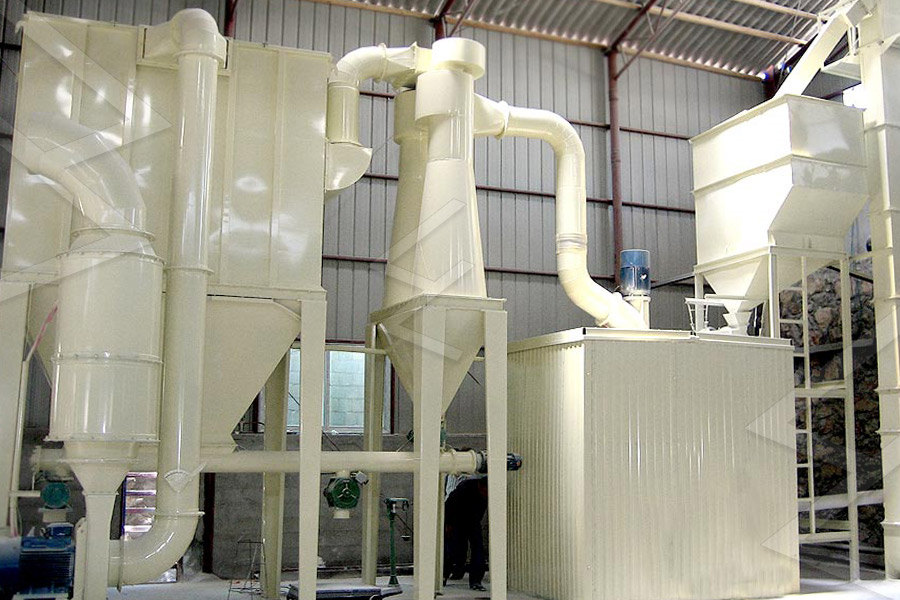
Electric Cement Production: The Technologies
2024年6月17日 Cambridge Electric Cement is a novel approach to the electrification of cement that integrates cement production with the production of steel in an electric arc furnace (EAF) The process is premised on the fact that , the corporate entity that owns and operates the 866 MW Matuno River Hydroelectric Power Plant in Bambang, Nueva Vizcaya COSCO acquired 100% of Matunos outstanding shares but did not reveal the pershare price, as it is not under an obligation to reveal the price since the cost of the transaction does not exceed the minimum for price disclosure The company said that Cosco Capital buys 87MW hydroelectric power plantOctober 2023; Journal of the Southern African Institute of Mining and Metallurgy 123(9):471478(PDF) A study of different grinding aids for lowenergy 2022年2月2日 The clinker was used to produce cement and was then further processed to produce concrete In the next phase of their joint research and development project, CEMEX and Synhelion aim to produce solar clinker in larger quantities as they work towards an industrial scale pilot at a cement plantCEMEX and Synhelion achieve breakthrough in cement
.jpg)
Solar energy—A look into power generation, challenges, and a
2018年11月1日 Three ways of converting solar energy into other forms of energy: (a) producing chemical fuel via artificial photosynthesis, (b) generating electricity by exciting electrons in a solar cell, and 2020年10月15日 This research focused the role to study the effects and ways to control the chemical composition of clinker for better cement production Cement is a substance produced by grinding a mixture of a Effects and Control of Chemical Composition of Clinker for Cement 2007年5月1日 null THE ENVIRONMENTAL IMPERATIVE Given the energyintensive nature of the cementmanufacturing process, it is perhaps not surprising that a twentieth of the world’s manmade CO 2 emissions can be traced to a single industry: cement About half of these emissions are a necessary byproduct of the chemical reaction essential in transforming the raw material Concrete energy savings – onsite power for the world’s cement 2020年5月14日 There are significant opportunities in most cement plants to improve their energy efficiency, as the gap between the best performing plant and other plants is still large (a difference of 1012 kWh per mt cement and 50 to 80 kCal per kg clinker)Improving Energy Efficiency: Cement industry steps up its efforts
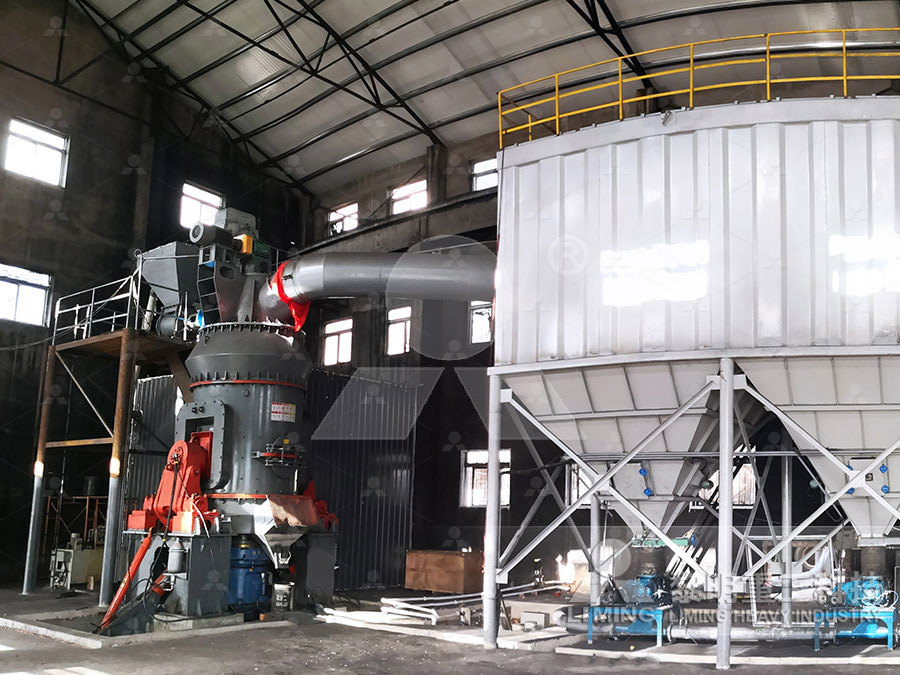
International Comparisons of Energy Efficiency (Sectors of Electricity
In Japan, coal fired electric power plants have accomplished high efficiency While, as for natural gas, we can say the United Kingdom has improved the efficiency of power generation since 1990 through replacing aged coal fired power plants with latest combined cycle gas turbines The averaged efficiency of fossil fuel power plants is2020年2月1日 Nowadays, ball mills are used widely in cement plants to grind clinker and gypsum to produce cement In this work, the energy and exergy analyses of a cement ball mill (CBM) were performed and Energy and exergy analyses for a cement ball mill of a new