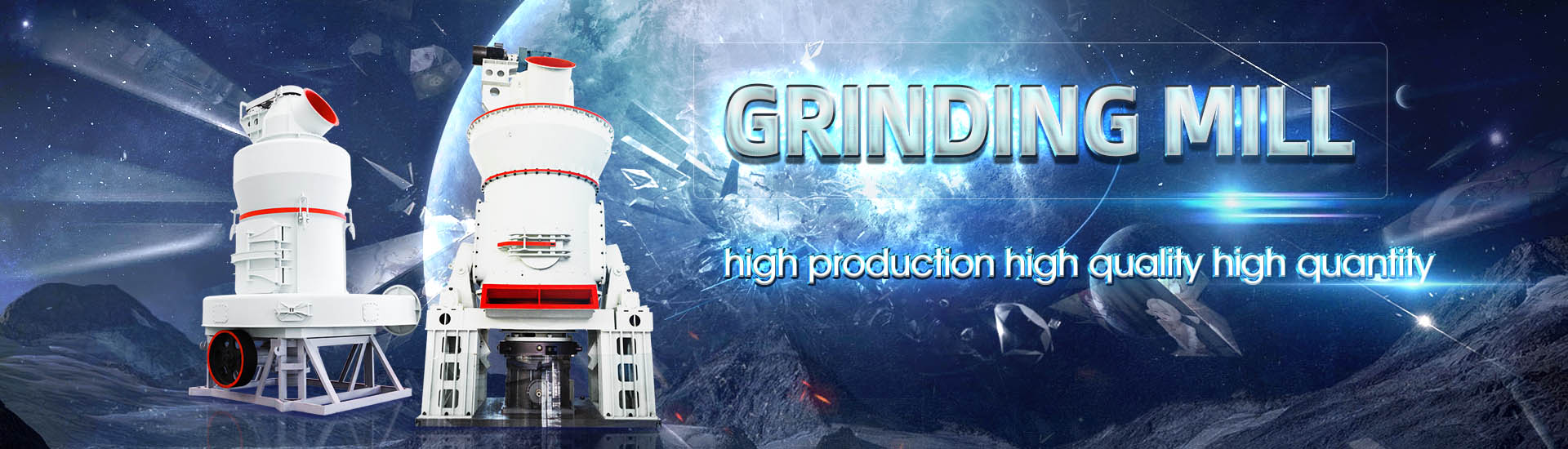
Tangshan water slag iron separation equipment
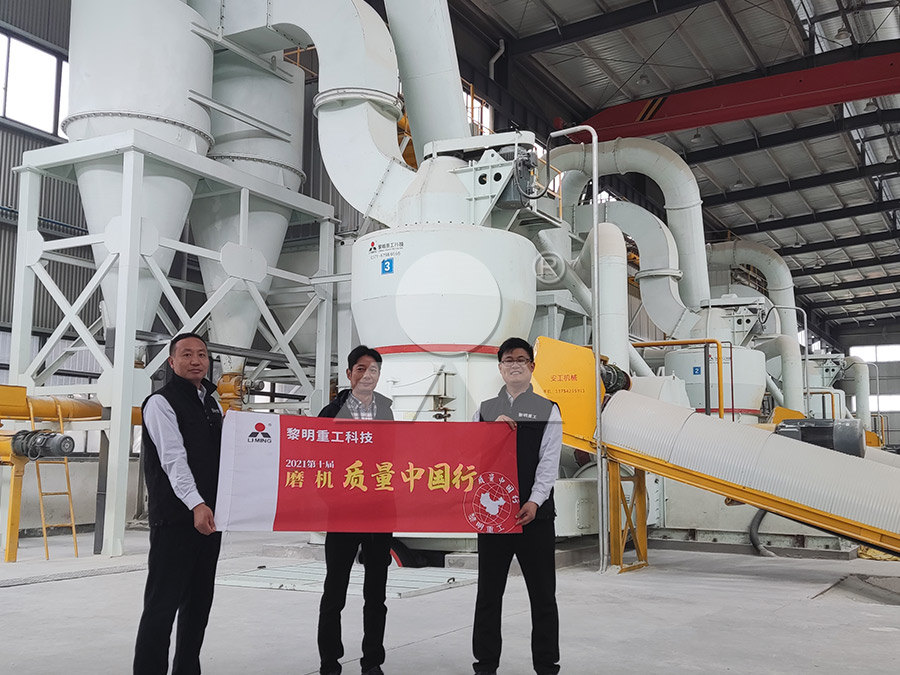
Tangshan Fengnan Iron Steel orders slag granulation kit from
Capital Engineering Research Incorporation (CERI), the general contractor, has signed two contracts with Paul Wurth for engineering and supply of four sets of Central Feed Bell Less 2023年3月1日 In this study, chemical analysis, Xray diffraction, and scanning electron microscopy were used to analyze the changes in phase composition and morphology during Efficient separation of iron elements from steel slag based on 2022年7月1日 This study used the processLCA method to evaluate the melting reduction technology for iron and steel waste residues in a steel plant of Tangshan The results reveal Life cycle assessment of melting reduction treatment for iron and 2018年8月1日 In China, after steelmaking, the steel slag is poured from the converter, transported to the slag stacking place, and treated by aging Then the steel slag is Steel slag in China: Treatment, recycling, and management
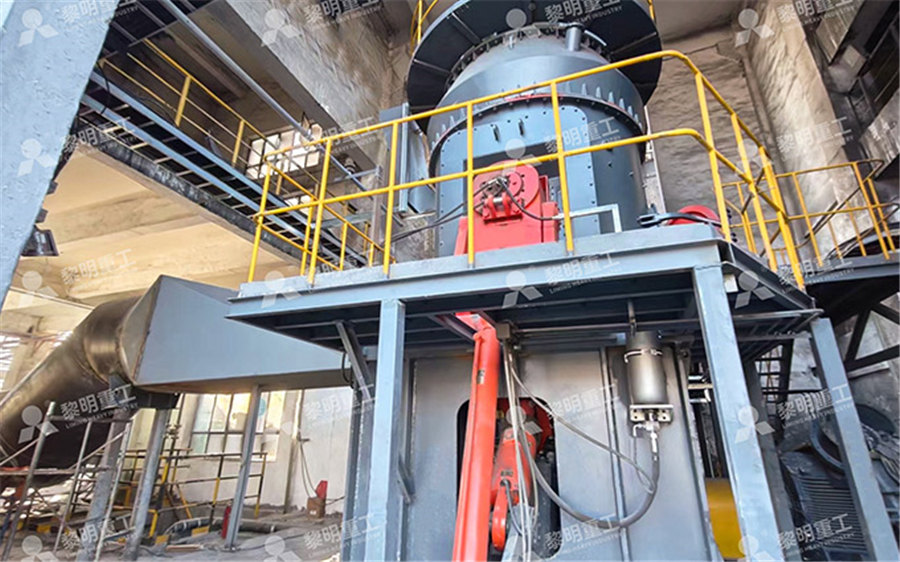
Current Development of Slag Valorisation in China
2014年2月19日 In this paper, the current state of iron and steelmaking slags valorisation in China is reviewed The main hot stage slag valorisation processes were introduced to deal 2024年3月1日 The utilization of this airfluidized magnetic separator for primary separation of steel slag powder can enhance its iron grade from 1493% to 2181%, while also reducing the iron grade in nonmagnetic productsAn airfluidized magnetic separator and its separation 2024年3月1日 Primary magnetic separation tests on a steel slag fine powder material demonstrate that the air fluidized dry magnetic separator effectively separates inert minerals (PDF) An airfluidized magnetic separator and its separation 2021年11月3日 Among the wastes of the metallurgical production of orereduction profile (blast furnace and electrocarbothermic production of pig iron and ferroalloys), slag melts generated A new technological approach to the granulation of slag melts of
.jpg)
Recycling of iron and steel slag for carbon reduction and low
2024年6月12日 BFS and SS discharged from ironmaking or steelmaking furnaces carry a significant amount of latent heat, especially the calcium oxide component in SS, which gives it 2021年11月3日 The technological factors required to improve the operational properties of granulated metallurgical slags demanded in the building industry have been analyzed In order to satisfy these factors, a new technology for hydrovacuum granulation of slag melts (HVG) has been developed It is shown that the main advantage of the proposed HVG process is the A new technological approach to the granulation of slag melts of 2018年8月1日 In China, after steelmaking, the steel slag is poured from the converter, transported to the slag stacking place, and treated by aging Then the steel slag is magnetically separated to recover the metal iron (Fe) After magnetic separation, the steel slag is irregularly piled on the open groundSteel slag in China: Treatment, recycling, and management2017年2月1日 Three types of slags, namely basic oxygen furnace slag, desulfurization slag, and iron ladle slag, were studied, and the results showed that the optimized recovery efficiencies were 93 20%, 92 Optimization of magnetic separation process for iron recovery
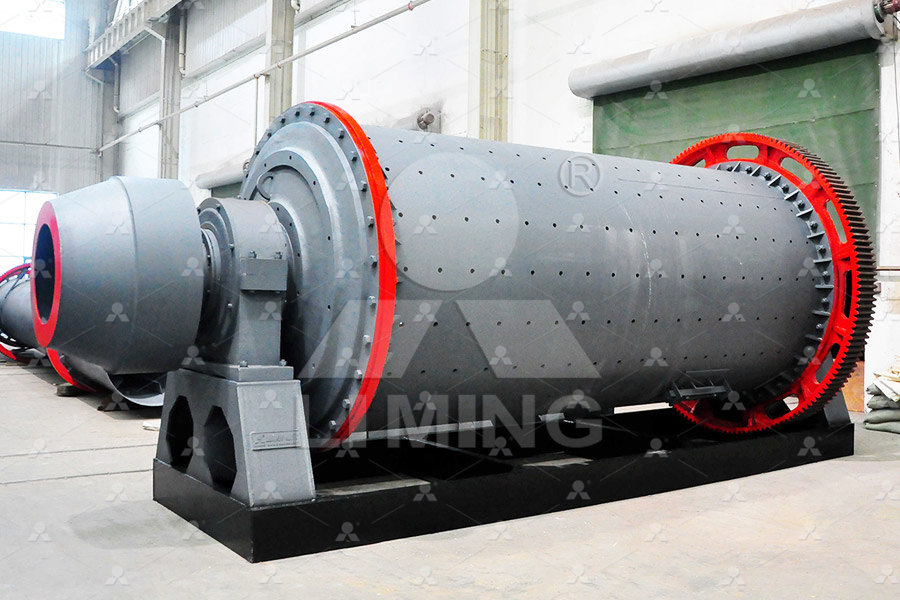
(PDF) Optimization of Iron Recovery from BOF Slag by
2022年4月27日 Compared with the initial steel slag, the iron grade increased by 822%, and the iron recovery increased by 4638% compared with direct magnetic separation without oxidation [13]2022年3月14日 During slag granulation, after metal separation in the blast furnace main runner, the contact between water and slag can lead to explosions due to the presence of metal in the slag This study aims to reduce the amount of molten metal passing through the slag port of a main runner in a Brazilian steel mill With this goal, multiphase numerical modeling simulations Improving the Slagmetal Separation of a Blast Furnace Trough 2005年2月1日 Steelmaking slag has been considered a potential P source due to its huge production and the increasing P content in slag with the utilization of lowgrade iron ores If the efficient separation (PDF) Industrial uses of slag The use and reuse of iron and 2023年12月27日 The purpose of the steel slag process is to recover useful ironcontaining components, including bulk iron, granular iron, and fine iron tetroxide Due to the strong magnetism of the above components, the process of steel slag beneficiation is magnetic beneficiation, and the required equipment is a magnetic separatorSteel Slag Processing Plant Equipment Selection
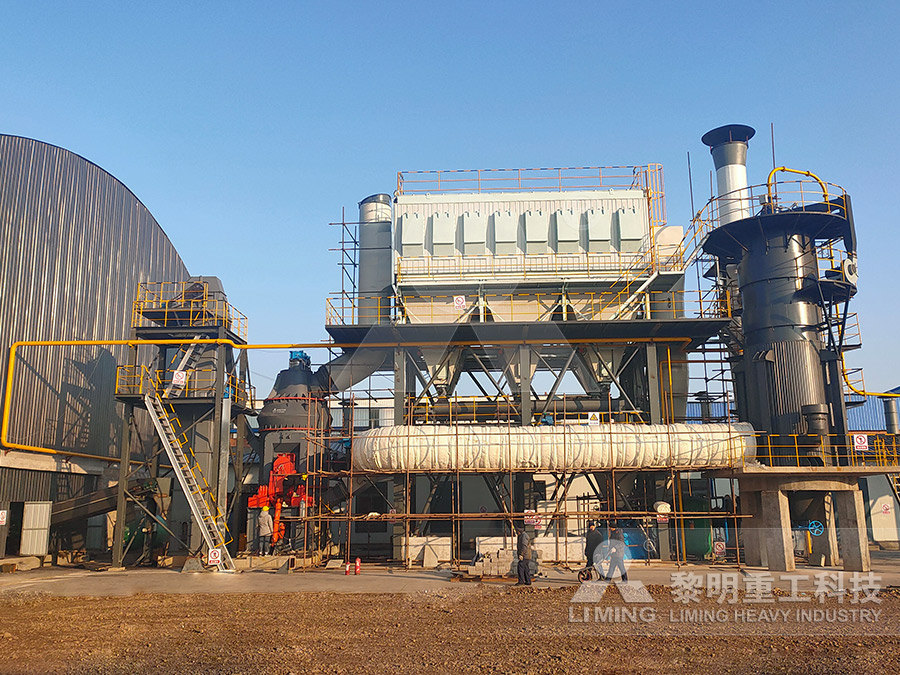
(PDF) Recovery of high grade iron compounds from LD slag by
2013年1月1日 It was shown that 3334% of the wastes can be recycled with 5490% iron recovery and 7443% sulphur removal after dry magnetic separation experiments while 1466% of the wastes can be recycled 2024年3月1日 The presence of magnetic inert minerals (RO phase, Fe 3 O 4, Fe) in steel slag powder 13 enables the separation of these minerals from the slag to enhance its gelling properties and facilitate iron resource recovery, thereby improving the activity of steel slag powder 14 However, during wet magnetic separation operations, hydrated active minerals, such as C 2 S, An airfluidized magnetic separator and its separation grade of the new separation technology reached up to 5278% and 6474%, in comparisson the with existing technology Thus, it wa demonstrated that the selfs developed separation technology has the potential to improve the iron recovery of the finegrained steel slag Keywords: Finegrained steel slag Dry magnetic separationDRY MAGNETIC SEPARATION TECHNOLOGY FOR THE RECOVERY OF IRON 2021年10月1日 Several studies have used carbothermic reduction for processing various feeds, such as EAF dust (Ferreira et al, 2018), iron concentrate (Liu et al, 2018), iron ore tailing (Bai et al, 2018), chromite iron oxide (Hu, 2016), high alumina iron ore (Chun et al, 2015), titaniumbearing BF slag (Zhen et al, 2016), bauxite residue and BOF slag (Xakalashe and Friedrich, Valorization of electric arc furnace slag via carbothermic reduction
.jpg)
Extraction and separation of iron technology and research progress
2024年4月14日 Its advantages over precipitation enable the wide application of the extraction method, which has been a research hotspot in the world in petrochemistry, hydrometallurgy, fine chemical industry, separation, and purification of biochemical substancesIron extraction has been studied extensively due to the damage caused by iron ions to water, soil, and organisms2024年11月10日 An efficient treatment of the slag was proposed using copper flotation, silica removal by smelting and subsequent magnetic separation The copper recovery rate after flotation increased from 186% to 3902% at a copper concentrate grade of 46% when the sample was ground from 75% to 95% passing 74 mm Silica removal was conducted for 30 min smelting at Mineralogical Study of Waterquenched Slag from Copper 2024年4月14日 Solvent extraction of iron plays an important role in hydrometallurgy [18], [19], [20], wastewater treatment [21], environmental monitoring [22], [23], and soil and plant nutrient detection [24]To improve the separation technology of iron, since the 1960s, people have studied the removal of iron via solvent extraction, and most of the research focused on sulfuric acid Extraction and separation of iron technology and research progressOptimization of magnetic separation process for iron recovery from steel slag Yuanpei Lan", Qing cai Liu':* , 1 Departme nt of Metallurgy Engineering, 1) 0001jlj , China 2 Chongqing Materials Research Institu te, ARTICLE INFO Ke y words : Steel slag Magnetic se para tion Iron recovery Recovcry efficicncy Ab rasion Fei Meng" , Deliang Niu Optimization of magnetic separation process for iron recovery
.jpg)
Iron recovery from lead smelting waterquenching slag by
2024年4月15日 This study explored the recovery of valuable metal elements in the lead smelting waterquenching slag using the method of “roasting–grinding–magnetic separation” at a roasting temperature of 1250 °C, coal dosage of 125%, roasting time of 90 min, and grinding time of 45 min An iron concentrate with a grade of 9361% and a recovery rate of 9071% were obtained2014年2月19日 Slags are byproducts of the metallurgical industry It is of importance to recycle materials and recover heat from metallurgical slags to reduce the energy consumption and environmental impact of steel industry China is the largest iron and steelmaking slag producer in the world, and intensive efforts have been made during last decades for slag valorisation, Current Development of Slag Valorisation in China2011年5月1日 By using DR followed by a magnetic separation process for iron recovery from copper slag, Yang [10] obtained iron powder of 9205% iron content with an iron recovery rate of 8101%, and Wang [11 Iron recovery from copperslag with lignitebased direct reduction 2017年3月5日 slag could be potentially reactive with water at room tem perature [40, 45] BFS (iron slag) is particularly suitable for highperformance concrete because the hardening (hydration) (PDF) Iron and Steel Slags ResearchGate
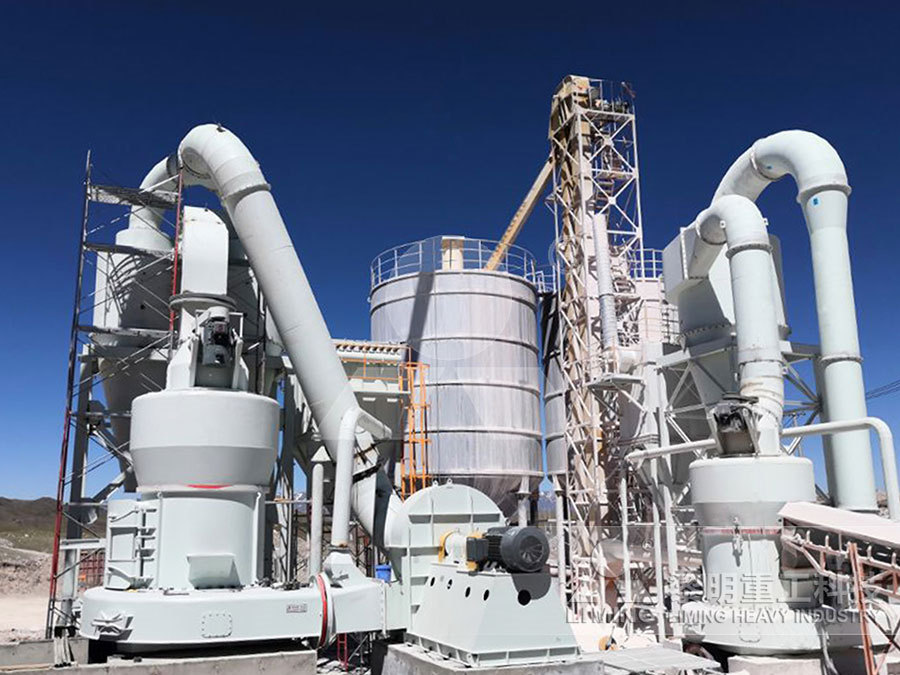
Characteristics of water quenched coppercontaining slag and separation
2012年2月1日 Download Citation Characteristics of water quenched coppercontaining slag and separation of iron and silicon from it A mineralogical study of water quenched coppercontaining slag was carried Under these conditions, the iron grade in the magnetic concentrate was greater than 90%, with an iron recovery ratio greater than 95% Keywords: copper tailings; iron; direct reduction; magnetic separation; recovery; process optimization 1 Introduction Approximately 30 Recovery of iron from copper tailings via lowtemperature direct 2023年1月1日 Matteslag separation behavior as a function of iron phase reduction in copper slag January 2023 Journal of Mining and Metallurgy Section B Metallurgy 59(00):33(PDF) Matteslag separation behavior as a function of 2017年8月22日 The iron resources in nickel slag were recycled by oxidation and magnetic separation The effects of holding time, temperature, air flow rate and basicity on the crystallization of magnetite were investigated systematically Crystallization and Beneficiation of Magnetite for
.jpg)
Slag Separation an overview ScienceDirect Topics
Slag processing George C Wang, in The Utilization of Slag in Civil Infrastructure Construction, 2016 54212 Selfdissolving In this method, hot steel slag is put into a sealed pressure tank, holding approximately 100 kg (220 lb) of steel slag (it can be a smaller or larger amount depending on the trial scale) (SRIM, 1982)Molten steel slag can produce large amounts of 2022年5月1日 Abstract Considering the BSSF steelmaking slag generated in a Brazilian steelwork, it would be worth to separate iron and calcium from it, with the objective of increasing its iron content, or Separation of Iron and Calcium from a BSSF Steelmaking Slag Hence, effective recycling of iron from steel slag, would not only alleviate environment pressures and improve economic efficiency, but would also reduce the industrial demand for iron ore [3] The technique used for efficient recycling of iron mainly include dry magnetic separation of bulk slag, wet stage grinding and magneticWET MAGNETIC SEPARATION OF IRON FROM FINEGRAINED 2015年12月31日 This chapter introduces the principle of how lowgrade iron ores are upgraded to highquality iron ore concentrates by magnetic separation Magnetite is the most magnetic of all the naturally Developments in the physical separation of iron ore: Magnetic
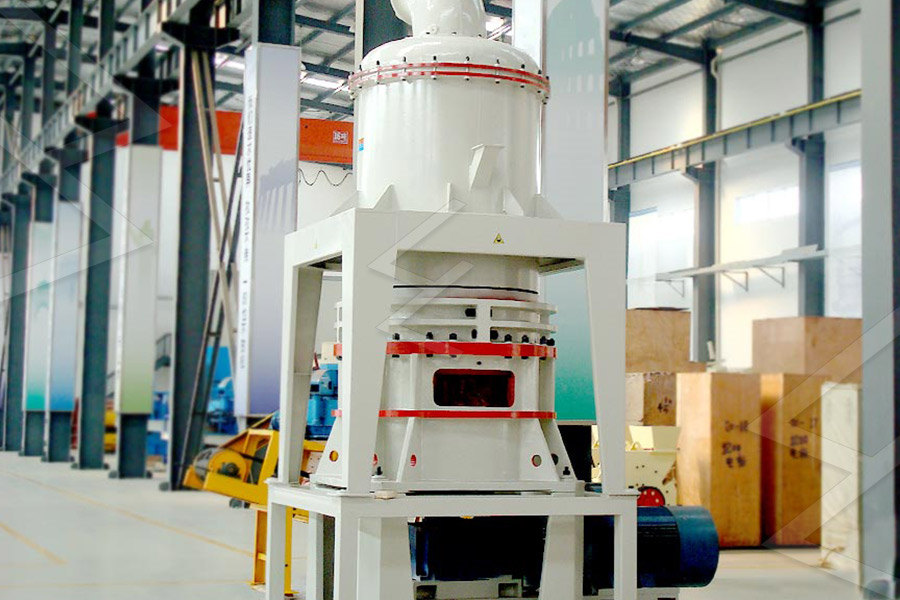
Chemical and Mineralogical Analysis of Reformed Slag during Iron
2021年7月28日 Copper slag is usually a mixture of iron oxide and silicon dioxide, which exist in the form of fayalite (2FeOSiO2), and contains ceramic components as SiO2, Al2O3 and CaO depending on the 2017年8月22日 The iron resources in nickel slag were recycled by oxidation and magnetic separation The effects of holding time, temperature, air flow rate and basicity on the crystallization of magnetite were Crystallization and Beneficiation of Magnetite for Iron 2018年2月5日 Blast furnace (BF) slag and steel slag make up the dominant portion of byproducts in an integrated steel mill Steel slag is a byproduct from either the conversion of iron to steel in a basic oxygen furnace (BOF) or melting of scrap to make steel in an electric arc furnace (EAF) []Iron slag is generated from Blast Furnace (BF slag) in the iron production, Valorization of Metallurgical Slag for the Treatment of Water 2017年9月1日 In order to recycle iron from copper slag with total iron content (TFe) of 3996%(mass fraction), a technique with lignitebased direct reduction followed by magnetic separation was presentedRecovery of iron from copper tailings via low

(PDF) A physicochemical separation process for upgrading iron
A physicochemical separation process for upgrading iron from waste copper slag × xxx–xxx Wast e Copper slag separation experiment, the sample was continuously fed into a magnetic field by the waste slag was granulated and cooled quickly by spraying with water The waste slag was verified to have a complex amorphous structure by 2024年7月29日 The mineral dry separation method is a technique for the comprehensive utilization of steel slag In this process, two products, ie, steel slag powder with high activity (reaches 75% of the cementitious activity of pure cement) and inert mineral material, are obtained by crushing and separating steel slag 12,13 If wet magnetic separation is adopted, the active Magnetic separation characteristics of steel slag powder in a 2018年10月31日 To recover iron from waterquenched nickel slags, CaO was added Thermodynamic analysis showed that CaO promotes the reaction between fayalite (Fe2SiO4) and O2 Phase diagrams of the FeOSiO2MgOCaO slag with various CaO contents in an air atmosphere drawn by FactSage 71 showed that the phase components can be significantly Effects of CaO Addition on the Iron Recycling from Nickel Slags by China Mining Separation Equipment wholesale Big Bowl Decanter Centrifuge Dewatering Equipment to Obtain Dry Slag Sustainable Mining US$ 55000 / Piece 1 Piece (MOQ) Gold Mining Equipment of Iron Drum Magnetic Separator for Iron Minerals Separation US$ 1800 / Piece 1 Piece (MOQ)Mining Separation Equipment MadeinChina
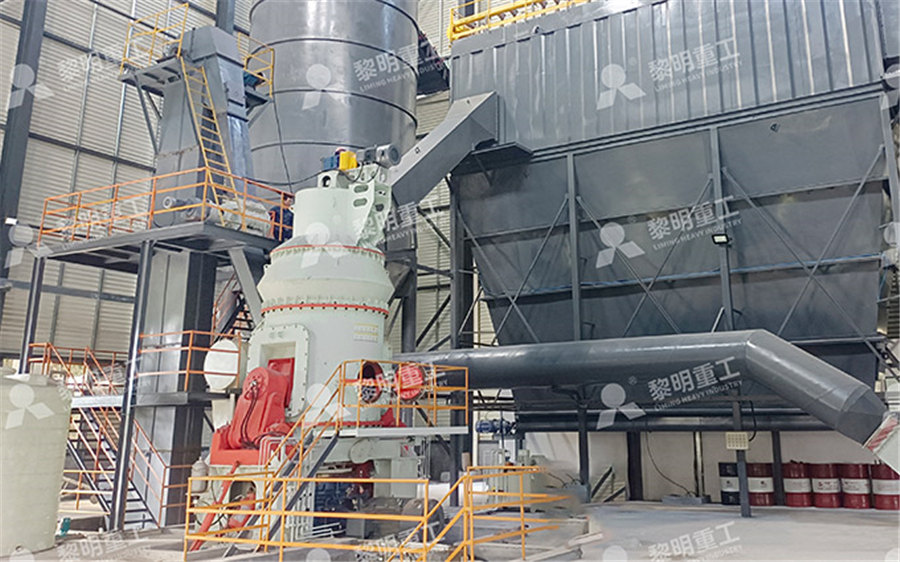
DRY MAGNETIC SEPARATION TECHNOLOGY FOR THE RECOVERY OF IRON
grade of the new separation technology reached up to 5278% and 6474%, in comparisson the with existing technology Thus, it wa demonstrated that the selfs developed separation technology has the potential to improve the iron recovery of the finegrained steel slag Keywords: Finegrained steel slag Dry magnetic separation2013年11月1日 A large amount of waste copper slag containing about 35–45 wt% iron is generated every year from pyrometallurgical processes for producing copper from copper concentrateUpgrading of Iron from Waste Copper Slag by A Physicochemical 2020年7月16日 Gasquenched steel slag abrasive was obtained by gas quenching with hightemperature liquid steel slag as raw material The phase composition, thermal properties, micromorphology, magnetic properties, and mechanical properties of the particles were characterized by using an Xray diffractometer, a differential thermal analyzer, a scanning Structure characterization and grinding performance of gas 2024年10月1日 Iron grain growth during deep reduction roasting is important for iron enrichment from copper slag (CS) through magnetic separation In this work, a novel method of additivefree activation roasting, including oxidation and subsequent reduction roasting, was proposed to increase the iron grain size, then the iron was extracted by magnetic separationIron extraction from copper slag by additivefree activation
.jpg)
Iron recovery from lead smelting waterquenching slag by
2024年4月15日 This study explored the recovery of valuable metal elements in the lead smelting waterquenching slag using the method of “roasting–grinding–magnetic separation” at a roasting temperature of 1250 °C, coal dosage of 125%, roasting