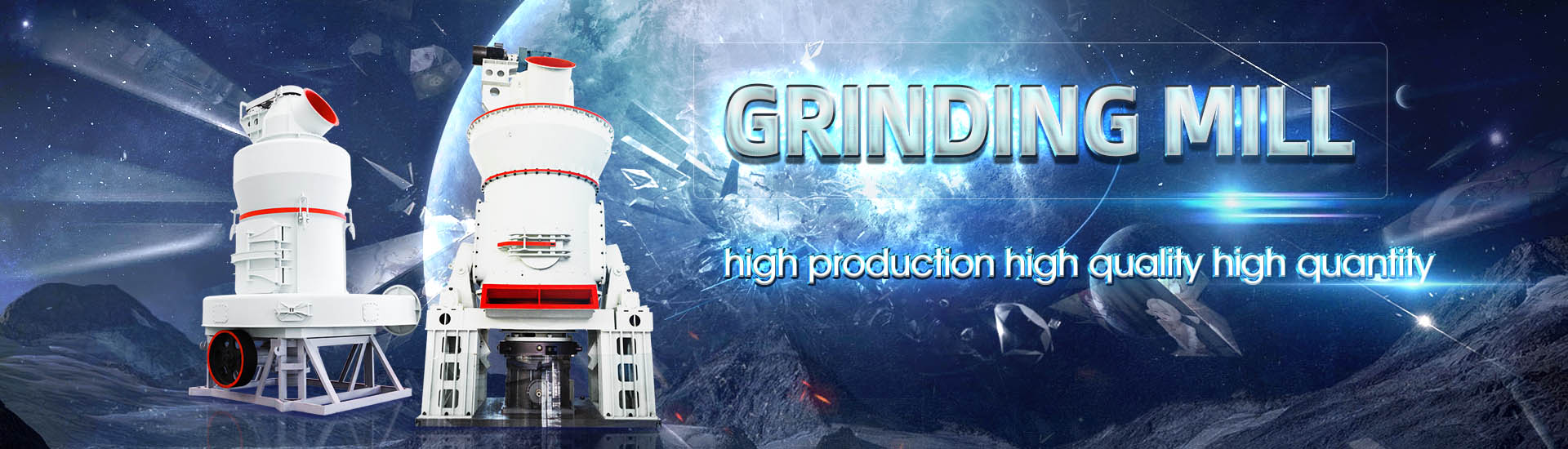
How many OEMs are there for drilling tip grinding in Kunshan
.jpg)
(PDF) Gundrilling knowhow ResearchGate
Understanding the entire gundrilling system helps resolve tooling problems Drill failure as a result of excessive misalignment between the starting bushing and machine spindle A shank thatUnderstanding the entire gundrilling system helps resolve tooling problems Drill 登录Machining centers can accommodate two types of gundrills The onepiece design is typically found in smalldiameter applications of less than 10 mm and is made from a solid carbide Gundrilling On A Machining Center Modern Machine Shop2020年1月1日 Holes are manufactured by using conventional and CNC milling machines This review shows how investigational and hypothetical contributions have lead to the theory of a Drilling operation: A review ScienceDirect
.jpg)
A review of modern advancements in micro drilling techniques
2017年10月1日 In line with the trend of miniaturisation, micro drilling is now being extensively used in areas such as precision engineering, microelectro mechanical systems (MEMS), 2022年6月24日 Grinding is a manufacturing process which significantly contributes in producing high precision and durable components required in numerous applications such as aerospace, (PDF) A comprehensive review on the grinding process: 2014年7月1日 Modern processing solutions set higher requirements for the accuracy and efficiency of carbide drill manufacturing This paper presents a detailed study of mathematical Practical and reliable carbide drill grinding methods based on a The most prominent processes are grinding, honing, lapping, and jetbased applications Nonconventional machining (chipless) processes In chipless machining material, particles are Machining Processes SpringerLink

Burr formation and its treatments—a review The International
2020年3月17日 This study investigates mechanisms, effects and variations on burr formation in most common machining processes such as drilling, milling, turning and grinding based on the The cutting edges of a drill are formed by adding a relief to the tip of the flute The following table explains the variety of designs and their applications Also, because the regrinding of the drill TECHNICAL GUIDE DRILLING USCTI2022年10月4日 Drilling uses rotating drill bits to produce the cylindrical holes in the workpiece The drill bit’s design allows the waste metal—ie, chips—to fall away from the workpiece 9 Types of Machining Processes XometryThis gives the tip of your drill bit a place to ride in as you begin to drill 4 Lubricated Bits Last Longer For drilling holes in steel that’s 1/8 in or thicker, use cutting fluid or a multipurpose oil like 3INONE Lubricating the bit reduces friction and heat buildup, which makes drilling easier, and your bits last longerWhat is Drilling? Definition, Process, and Tips The Engineering
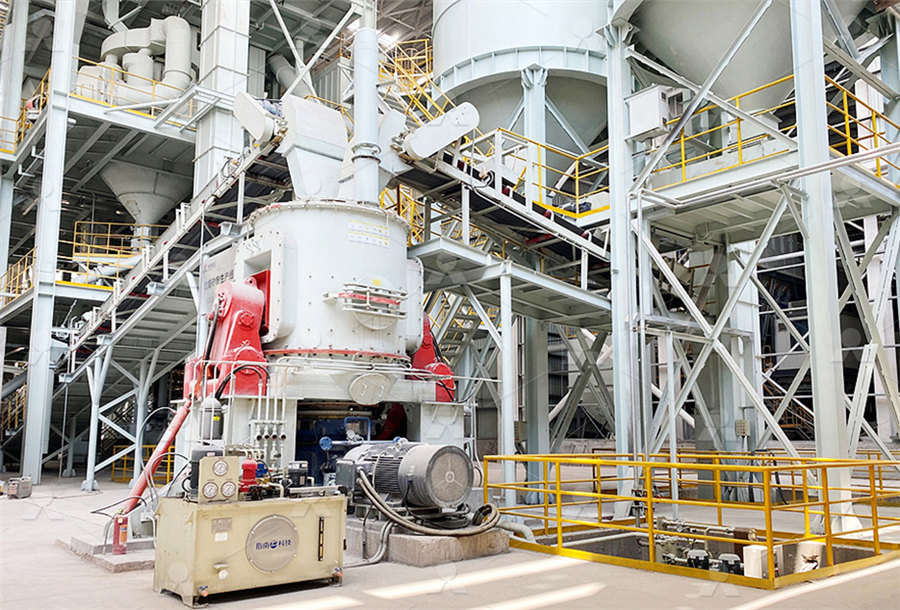
9 Types of Machining Processes Xometry
2022年10月4日 Ground surfaces of 200500 min rms are usually considered acceptable for many applications and are a starting point for further finishing operations, including lapping, honing, and superfinishing Double disc grinding 2020年6月14日 Infeed precision centerless grinding (or “plunge grinding”) is used to accurately grind parts with more complex shapes, such as minimally invasive guide wires that can transition over a length of 2 meters from a Precision Metal Grinding Metal Cutting Corporation2018年8月3日 With recent advances in MR/VR and the development of XRCoreShack, reexamination of core runs can be performed remotely, holographically, or virtually(PDF) Best practice and new technology in core drilling, logging How many methods of drilling are there? As the mining industry advances and more excavating opportunities present themselves, the number of drilling methods increases Whether it is for exploration, production, landclearing or geotechnical purposes, there are drilling methods that serve every mining purposeTypes of Drilling in Mining CR Mining
.jpg)
Precision Grinding: All Need To Know in Grinding Machining
2022年10月21日 More specifically, high precision grinding allows the machining of workpieces with complete accuracy, achieving very close tolerances as intricate as +/ 13 microns to +/ 13 microns for diameter and +/ 25 to 025 microns for roundness2022年11月28日 In internal grinding, the grinding speed is usually less than 30 m/s due to the small diameter of the grinding wheel 3) Surface grinding It is mainly used for grinding planes and grooves on the surface grinder There are two kinds of surface grinding: peripheral grinding refers to grinding with the cylindrical surface of the grinding wheelWhat is Grinding Process How It Works Different Types of GrindingProcess of bone drilling and temperature measurement without coolant 2 During this process temperature rises which can result in bone necrosis ie irreversible death of the bone cells when the temperature increases above a threshold 3–5 The compressive force acting on the fixation usually demands for high degree of stability of the fixating screwsDrilling of bone: A comprehensive review PMC PubMed Precision medicalgrinding expertise With a combined 200 years of experience, our medical grinding specialists design, manufacture, and implement solutions that answer the medical industry's call for cutting instruments with unique, complex geometries ARCH Medical Grinding provides this expertise at multiple locationsGround cutting tools, drills, reamers, and taps for medical OEMs
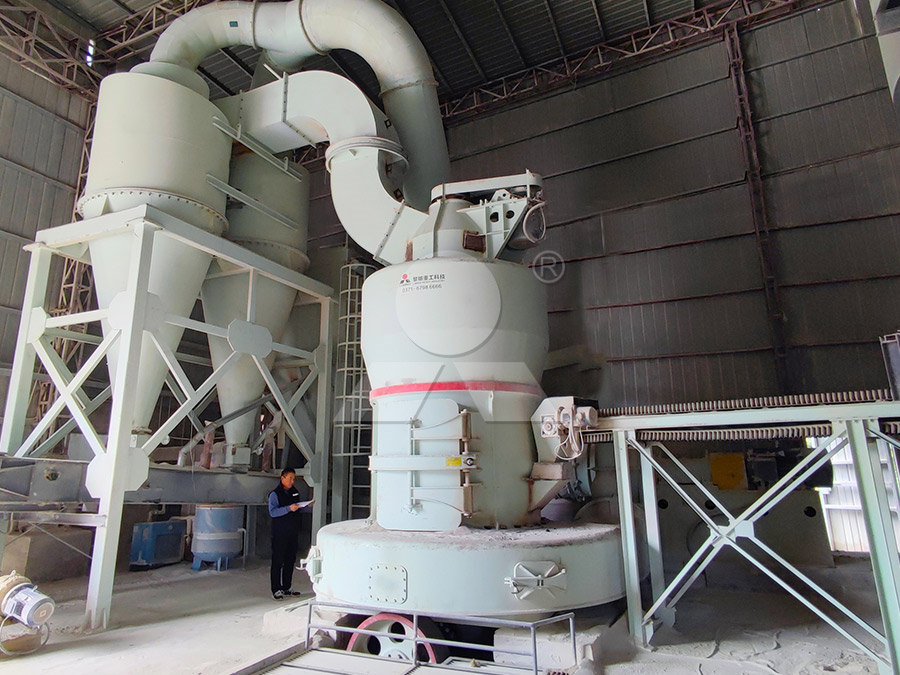
Machining Processes SpringerLink
Drilling is a metalcutting process with a rotary cutting motion (primary motion) The tool, i e, the drill, performs the feed motion in the direction of the rotational axis Figure 1215 shows common drilling processes With drilling into solid metal either Understanding Continuous Generating Grinding Many types of geargrinding processes exist with varying levels of part quality and productivity Knowing the terminology related to continuous generating gear grinding is helpful, and described as follows: • When profile grinding, the gear tooth profile is formed from aTechnology Advances for Continuous Generating Gear Grinding 2020年6月29日 Grinding wheel structure The structure of a grinding wheel refers to the relative spacing of the abrasive grains; it is the wheel's density There are fewer abrasive grains in an openstructure wheel than in a closed Chapter 16: Grinding Wheels and Operations2023年3月10日 The act of drilling involves using a drill bit to create or expand a hole in a material The main reason for drilling a hole in a workpiece is usually to enable the attachment of mechanical fasteners, such as bolts, and screws Machining Operations Explained – Engineering Cheat

Introduction to Turning Tools and Their Application
Tip: The most commonly used insert/holder combination for OD rough turning and facing is the C type 80 diamond insert with a 35 negative lead tool holder It is often selected because it is the best compromise between strength of insert and endangle clearance2022年12月1日 Figure 2: Diamond grinding cup for an electric grinder 2 Understand the Hardness of the Material Surfaces Depending on the toughness of the surface, the diamond cup wheel generally exists in two phases Phase 1 consists of coarse grinding In this phase, there is a high propensity for the diamond to become blunt during this phase7 Tips for Choosing the Right Diamond Cup Wheel NCCuttingToolsAn annular cutter is a specialized bit for drilling through metal Like a hole saw for wood, an annular cutter only cuts the outside edge of a hole It produces accurate burrfree holes to close tolerances without predrilling or step drilling It can drill a much larger hole and requires less force and time than a standard twist drill bitBASIC GUIDE TO MAGNETIC DRILLS ANNULAR CUTTERSGoogle 提供的服務無須支付費用,可讓您即時翻譯英文和超過 100 種其他語言的文字、詞組和網頁。Google 翻譯
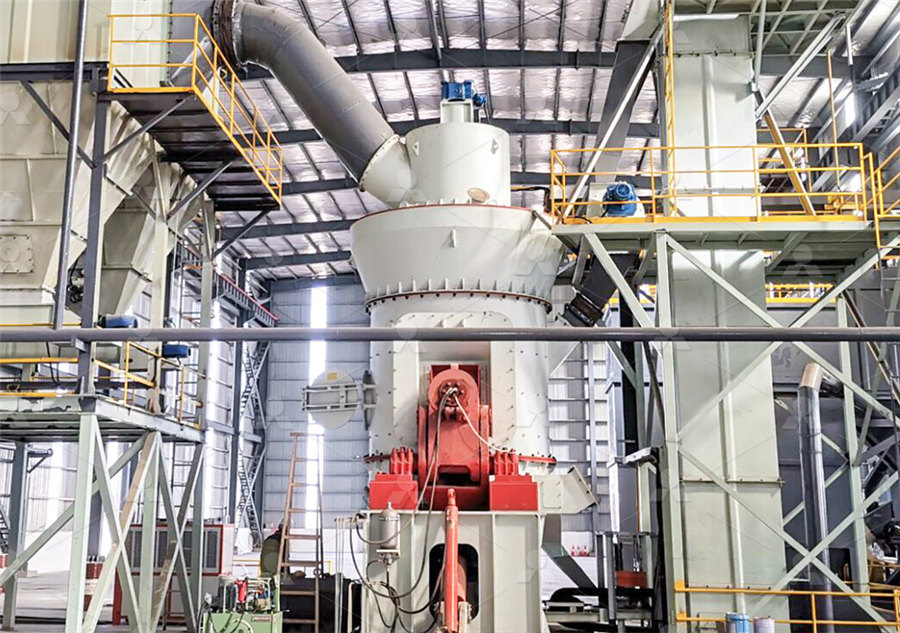
Analysis of the Performance of Drilling Operations for Improving
2021年3月9日 Drilling is a vital machining process for many industries Automotive and aerospace industries are among those industries which produce millions of holes where productivity, quality, and 2022年8月25日 I dont feel this is correct A drill tip magnified, you cant get a cutting edge So if the tip touches first, for a split second it smears I have spotted many 90 deg holes and never experienced “shock loading” Thats why center drills are 60 deg Lets the cutting edge of drill engage before the drill tipSpot Drilling: The First Step to Precision DrillingProvided by OSG Drilling Technical Guide 3 Drilling Technical Guide Proper Application and Usage of Drilling Tools Part 1: Drill Basics 11 Types of Drills A drill is a holemaking tool that has cutting edges at the tip, and a groove to evacuate chips to the outside of hole This “groove” is commonly referred to as the drill “flute”TECHNICAL GUIDE DRILLING USCTI2021年4月16日 Grinding hand tools A die grinder is a highspeed rotary tool that is typically powered by compressed air The tool has a smalldiameter abrasive bit that rotates to get the job done Check out Choosing the Right Air Intro to Grinding Methods, Machines and Tools
.jpg)
CNC Machine Types Guide: Types, Definitions, Uses
CNC grinders are available in various types, including cylindrical grinders, surface grinders, and roll grinders, among others There is also a wide range of abrasive materials used for grinding, such as aluminum oxide, plated or vitrified CBN, June 2022; ARCHIVE Proceedings of the Institution of Mechanical Engineers Part C Journal of Mechanical Engineering Science 19891996 (vols 203210) 236(2):1107(PDF) A comprehensive review on the grinding process: Grinding – Ex 11 • You are grinding a steel, which has a specific grinding energy (u) of 35 Ws/mm3 • The grinding wheel rotates at 3600 rpm, has a diameter (D) of 150 mm, thickness (b) of 25 mm, and (c) 5 grains per mm2 The motor has a power of 2 kW • The work piece moves (v) at 15 m/min The chip thickness ratio (r) is 10Grinding and Finishing IIT Bombay2008年5月10日 In many applications, Is there today a new dawn, a new moment for American manufacturing? Top Shops Benchmarking See All 23 Sep 2024 Top Shops During drilling, the tool tip will not be visible, and the normal visual cues that alert operators to trouble will be absentGundrilling On A Machining Center Modern Machine Shop
.jpg)
10 Turning Operations You Need To Know Turntech Precision
2020年8月29日 Turning is the most common lathe machining operation During the turning process, a cutting tool removes material from the outer diameter of a rotating workpiece The main objective of turning is to reduce the workpiece diameter to the desired dimension There are two types of turning operations, rough and finish2023年10月11日 There are many hazards involved in working with abrasive wheels for grinding These range from immediate physical hazards, such as abrasions from wheel contact or dangerous projectiles from wheel breakage, to lifethreatening health hazards, including handarm vibration syndrome (HAVS) from vibrations and pulmonary diseases from grinding dustGrinding Safety Precautions Hazards Control Measures2020年6月29日 Belt grinding has become an important production process, in some cases replacing conventional grinding operations such as the grinding of camshafts Belt speeds are usually in the range of 2,500 to 6,000 ft/min Machines for abrasivebelt operations require proper belt support and rigid construction to minimize vibrationChapter 17: Grinding Methods and Machines American Machinist2019年12月25日 If it can, it’s worth looking into ECG The process can replace many conventional grinding applications, including conventional form grinding “ECG can remove a lot more metal a lot faster than conventional grinding, in New Applications for Electrochemical Grinding
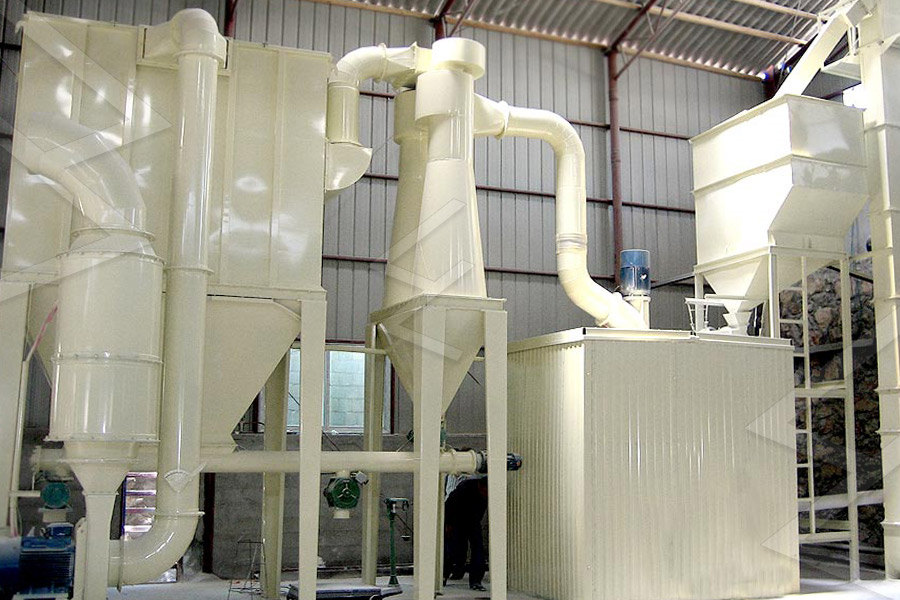
8 Vital Tips to Improve Chip Control When Drilling
Consider a Tooling Upgrade Don’t be afraid to try new tools, either If you’re stuck in Jobbersland, it might be time for an upgrade, and one of the best alternatives to an HSS drill is one with a replaceable carbide tipDavid Vetrecin, product manager for Iscar Tools, advises using replaceable drilling tips that are less solid carbide drills but offer equal or greater performanceThere are many different types of drill bits available which we’ll look at in this section In the drill bit guide below, we’ve split them into three categories: type of drilling application or material being drilled, the best types of drill bits, and then Guide to Types of Drill Bits ScrewfixThe right spindle can make a huge difference in your machine’s performance Whether you’re looking for speed, versatility, or just trying to save a few bucks, there’s a spindle design out there for you And if you’re ever in doubt, experts A Comprehensive Guide to Machine Tool Spindle Design2015年12月31日 Although there are already simulationbased studies in the literature aiming to understand, improve and design [21] continuous generating grinding processes of gears [22][23][24][25] [26] [27][28 Approach for the Calculation of Cutting Forces in
.jpg)
Technologies in deep and ultradeep well drilling: Present status
2017年11月1日 During the following 13th FiveYear Plan period (2016â 2020), there are still many challenges to the drilling of deep and ultradeep wells, such as high temperatures, high pressures, narrow 2020年9月1日 Fig 1 shows an abridged timeline of milestones in the development of UVAM, starting with rotary ultrasonic machining devices [[31], [32], [33]] and vibrationassisted turning devices [34, 35] in the 1960s, and extending to other vibration modalities in the 1980s and 1990s, with improved concepts, materials and methods [1, 36, 37]The 2000s saw the emergence of Review of ultrasonic vibrationassisted machining in advanced 2001年12月1日 PDF Understanding the entire gundrilling system helps resolve tooling problems Find, read and cite all the research you need on ResearchGate(PDF) Gundrilling knowhow ResearchGateDrilling into solid material is performed with a twist drill A cylindrical hollow body is generated by machining the material For drilling in a diameter range up to 20 mm and a hole depth up to 100 mm, the twist drill is the most frequently used toolDrill geometry basics CERATIZIT WNT KOMET
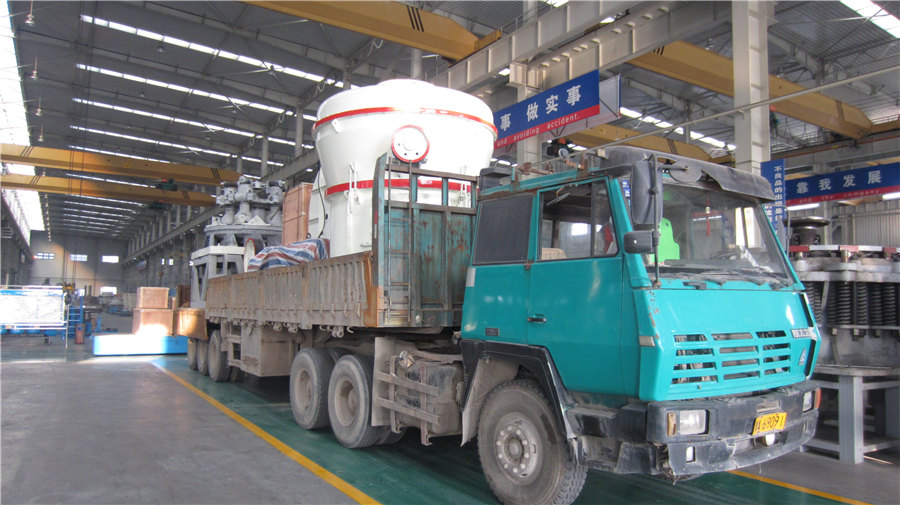
Kansas Oil Gas Activity MineralAnswers
Current Kansas oil gas activity includes production data, producing companies, new drilling permits, mineral values, and more MineralAnswers is the ultimate resource for mineral royalty owners searching for information on assets in KansasThere are several different types of grinding, including surface grinding, cylindrical grinding, and centerless grinding Spot facing: It is a machining operation that is used to create a flat, circular surface on a workpiece While drilling machines offer many advantages, they also have some limitations and disadvantages10 Different Types of Drilling Machines Runsom Precision2024年1月9日 In order to achieve automatic rounding for blade tip, the study was conducted on small radius rounding based on elastic grinding, and a method of robot automatic grinding for small radius fillets of blade tip was proposed An elastic grinding wheel with polyester ammonia fiber as substrate material utilized the characteristics of elastic envelope deformation contact Study on robot automatic rounding for blade tip based on elastic grinding