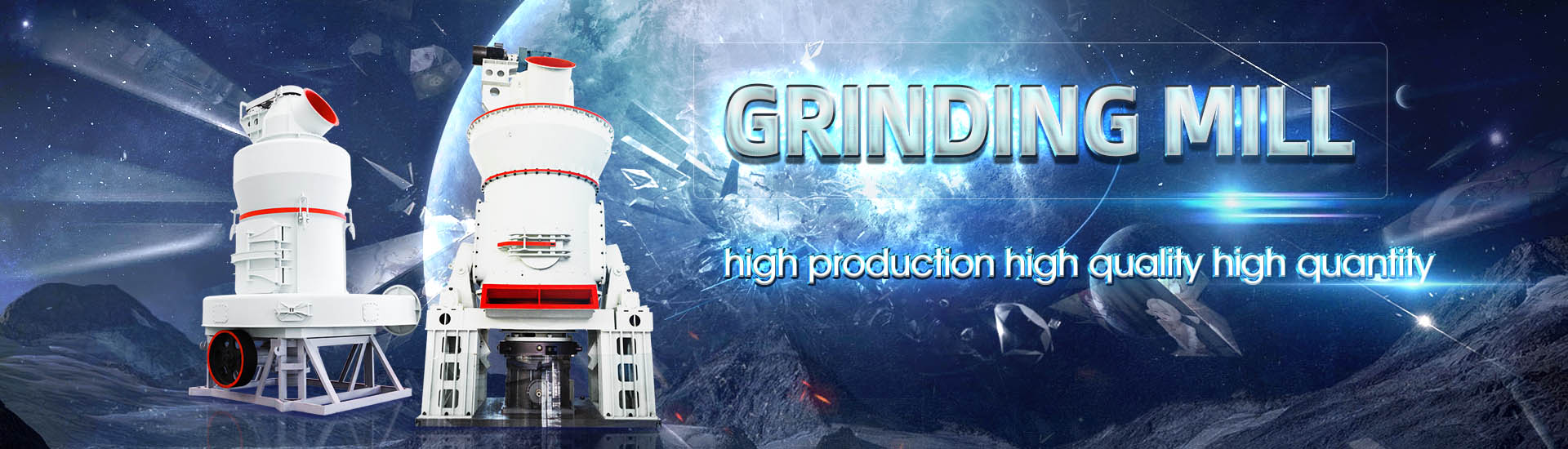
HOME→Working principle of matte iron powder making process Working principle of matte iron powder making process Working principle of matte iron powder making process
Working principle of matte iron powder making process Working principle of matte iron powder making process Working principle of matte iron powder making process
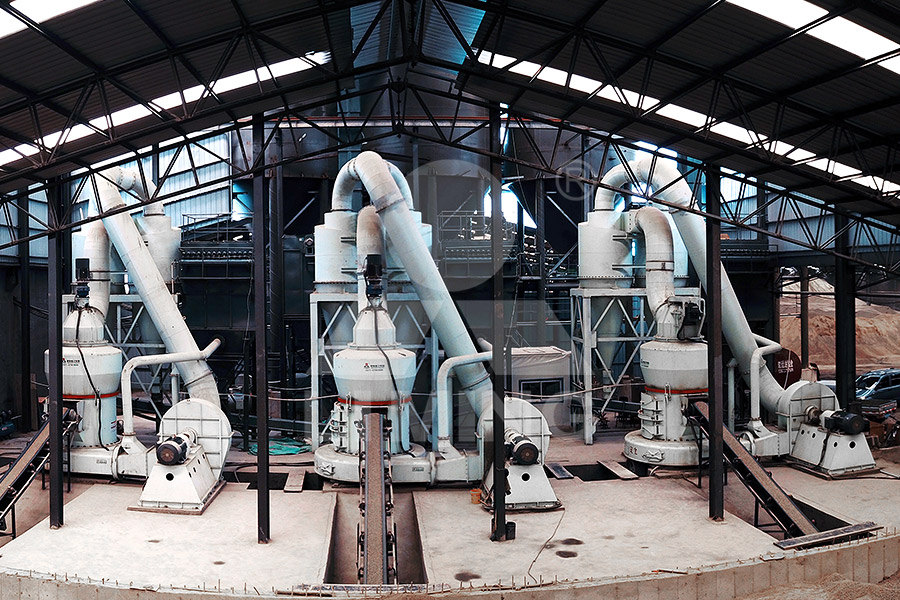
Making Metal Powder MPIF
In this process, molten metal is separated into small droplets and frozen rapidly before the drops come into contact with each other or with a solid surface Typically, a thin stream of molten 展开Powder metallurgy (PM) is a metal processing technology in which parts are produced from metallic powders In the usual PM production sequence, the powders are compressed into the MCE 313: Manufacturing Process I Powder Metallurgy 71 Powder • Iron powder => anode is low carbon steel; cathode is stainless steel The iron powder deposits are subsequently pulverized by milling in hammer mill The milled powders are annealed in Powder metallurgy – basics applications IIT GuwahatiPowder metallurgy is the process of blending fine powdered materials, compacting the same into a desired shape or form inside a mould followed by heating of the compacted powder in a Introduction To Powder Metallurgy Principles of Powder
.jpg)
Powder Metallurgy: Definition, Process, Advantages, Applications
2023年8月21日 Powder Metallurgy is a manufacturing process that produces intricate metal parts through powder compaction and sintering Fine metal powders are pressed into desired 2020年10月26日 This research includes a review of powder metallurgy processes, advantages and disadvantages, applications, and production methods of metal powder Powder metallurgy Powder Metallurgy Processes and Making Metal PowderKey steps include the shaping or compaction of the powder and the subsequent thermal bonding of the particles by sintering The process effectively uses automated operations with low Principles of Powder Metallurgy Total Materia1998年10月30日 Powder metallurgy (P/M) consists of making solid parts out of metal powders The powder is mixed with a lubricant, pressed into a die to form the desired shape, and then Metallurgy Powder, Process, Components Britannica
.jpg)
Powder Metallurgy PDF
Why Powder Metallurgy is Important •PM parts can be mass produced to net shape or near net shape, eliminating or reducing the need for subsequent machining •PM process wastes very It is the purpose of this chapter to deal with the various methods which are used to manufacture iron powders, the properties of the material resulting from the various methods, and the Iron Powder: Production—Characteristics—Fabrication2020年6月10日 Today’s modern steelmaking practice had been initiated about 200 years ago, when Henry Bessemer patented his process in 1856, and the process was introduced as Bessemer process of steel making The Bessemer process follows bulk steel production in large quantities and made it suitable for various applicationsIron and SteelMaking Process SpringerLinkPDF On Jul 11, 2018, Sandra Lúcia de Moraes and others published Iron Ore Pelletizing Process: An Overview Find, read and cite all the research you need on ResearchGateIron Ore Pelletizing Process: An Overview
.jpg)
Casting Process: Definition, Working Process, Types
2021年4月1日 Casting Process Working Principle in Detail: In this part, we will learn the detailed working process and Basic terminologies of Casting Mold Making; Pouring Process and; Solidification Process; Pattern Forming: The The key principle is removal of impurities from the iron by oxidation with air blown through the molten iron The oxidation also raises the temperature of the iron mass and keeps it molten Second Industrial Revolution : A phase of rapid industrialization in the final third of the 19th century and the beginning of the 20th, also known as the Technological RevolutionIron Making Boundless World History Lumen Learning1 Steel: Steel structures are one of the most popular substrates for powder coating It's durable, strong, and versatile, making it a prime choice for various industries Powdercoated steel is commonly seen in automotive parts, appliances, outdoor furniture, and industrial equipmentIts ability to withstand harsh environmental conditions, such as exposure to UV rays and Powder Coating Process Explained – A Detailed Breakdown2020年7月6日 The principle of the fire dilution method is that a large amount of Fe 3 O 4 in copper slag leads to an increase in slag viscosity and the loss of copper (Zhang et al, 2005)Equilibria of Iron Silicate Slags for Continuous Converting
.jpg)
Powder Metallurgy: Definition, Process, Advantages, Applications
2023年8月21日 Fig 5: Conventional Powder metallurgy process In conventional powder metallurgy, the process closely follows the basic steps of powder metallurgy, involving powder mixing, compaction, and sintering, with the incorporation of modern technology Injection Moulding Injection moulding offers the advantage of producing complex shapes in large 2018年8月7日 Powder bed fusion (PBF) is an umbrella term for three separate threedimensional (3D) printing technologies; selective laser sintering (SLS), direct metal laser sintering (DMLS) and selective laser melting (SLM) These processes share the same printing procedurePowder Bed Fusion: The Working Process, Current Applications Quality requirements of iron ore for iron production L Lu, D Zhu, in Iron Ore, 2015 164 Summary The BF ironmaking process is currently the dominant process for providing steelmaking raw materials worldwide However, the BF process relies heavily on metallurgical coke and involves cokemaking and sintering operations, which often attract serious environmental Ironmaking Process an overview ScienceDirect Topics2022年5月21日 Lapping Process, one of the most demanding manufacturing process of any industryEverything in this entire world is incomplete without finishing In our daily life also, if we didn’t finish our day well then everything seems to be in troubleLapping Process: Definition, Working Principle, Types, Material
.jpg)
(PDF) Development and Problems of Fluidized Bed
2023年10月9日 This paper introduces the working principle and several typical working states of fluidized bed (FB) technology to clarify the key to fluidized bed process operation2018年8月7日 Powder bed fusion (PBF) is an umbrella term for three separate threedimensional (3D) printing technologies; selective laser sintering (SLS), direct metal laser sintering (DMLS) and selective Powder Bed Fusion: The Working Process, Current Applications and high potential of the costefficient powder with comparable properties to that of the carbonyl iron powder Keywords: spherical iron powder, metal injection moulding, hydrogen reduction, iron oxide, metal powder production, powder processing, iron oxide 1 Introduction In recent years, major efforts have been undertaken to optimize the New Processing Route for Production of Fine Spherical Iron Powder2024年2月5日 Every part/component you see in the image above plays an integral role in the overall working principle of hammer mills However, the milling process mainly takes place in the crushing chamber (part 3) The working principle of a hammer mill is The Working Principle of Hammer Mills (Stepbystep Guide)
.jpg)
What Is Powder Coating? Types, Process Benefits
2021年9月3日 Each powder coating category has specific strengths and weaknesses Thus the requirements of each application will determine the one best suited to that situation Powder Coating Process The powder coating process requires three basic steps, regardless of the type of powder used: preparation, or pretreatment, application, and curingPowder Bed Fusion: The Working Process, Current Applications and Opportunities Fabrizio Fina, Simon Gaisford, and Abdul W Basit Abstract Powder bed fusion (PBF) is an umbrella term for three separate three dimensional (3D) printing technologies; selective Powder Bed Fusion: The Working Process,Roller presses are used to process bulk solids (powder, granules) in order to perform a dry granulation by compaction They can typically produce a compacted sheet of material that is later milled, even if some models have specific rollers whose shape allows to produce some briquettes This page is focusing on the design of roller presses, the mechanisms behind the Roller compactors : basic principles and technology overview2020年1月1日 This book presents the fundamentals of iron and steel making, including the physical chemistry, thermodynamics and key concepts, while also discussing associated problems and solutionsBasic Concepts of Iron and Steel Making ResearchGate
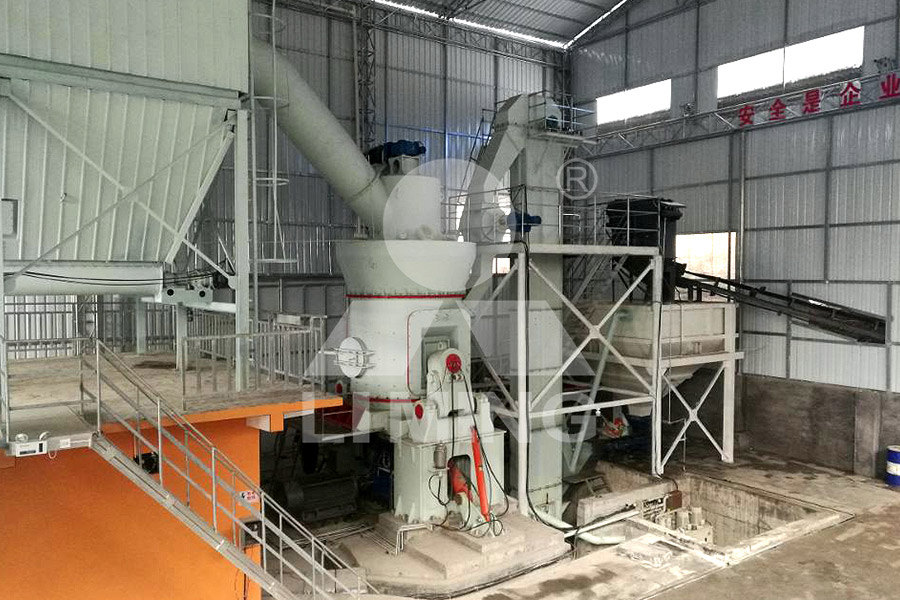
Powder metallurgy – basics applications IIT Guwahati
1 A hard brittle layer of pure metal which is subsequently milled to obtain powder (eg iron powder) 2 A soft, spongy substance which is loosely adherent and easily removed by scrubbing 3 A direct powder deposit from the electrolyte that collects at the bottom of the cell Factors promoting powder deposits are, high current density, low metal2014年2月1日 Request PDF Analysis on development of ironmaking process based on the principle of energysaving and emission reduction Through the basic research on current situation of ironmaking Analysis on development of ironmaking process based on the principle 2013年3月16日 The gas based process uses a shaft furnace for the reduction reaction The coal based process uses any one of the four types of reactors for the reduction reaction These reactors are (i) rotary kiln, (ii) shaft furnace, (iii) Direct Reduced Iron and its Production Processes – 2020年10月26日 This research includes a review of powder metallurgy processes, advantages and disadvantages, applications, and production methods of metal powder Powder metallurgy process steps consist of Powder Metallurgy Processes and Making Metal
.jpg)
Principles Of Powder Metallurgy and the Powder
Powder Metallurgy, applications of powder metallurgy and description of the process of powder metallurgy are the main features of this article The powder metallurgy technique is relatively new but it has become very popular among As we discussed thermite welding is a liquid state chemical welding process, in which joint formation takes place in molten state Practically, it is combination of welding and casting process in which, the molten iron poured at the welding plates and allow solidifying to make a permanent strong joint The molten state of iron creates without application of external heat or Thermite Welding: Principle, Working, Equipment's, Application 2022年8月17日 Eliminates possible waste and guarantees a high production rate In powder manufacturing, the three main methods are mechanical, chemical, and physical powder manufacturing methods However, the powder metallurgy process comprises of four necessary steps: powder manufacturing, powder mixing, compression, and sinteringOverview of powder metallurgy process and its advantages2014年1月1日 The powderforming process contains four basic steps: 1 Powder preparation 2 Powder mixing, blending, and/or slurry preparation (a powder–liquid suspension is known as a slurry) 3 Forming 4 Sintering The origins of powder forming date back to at least 20,000 years, as shown from the archaeological evidence of the first clay crockeryPowder Processing of Bulk Components in Manufacturing
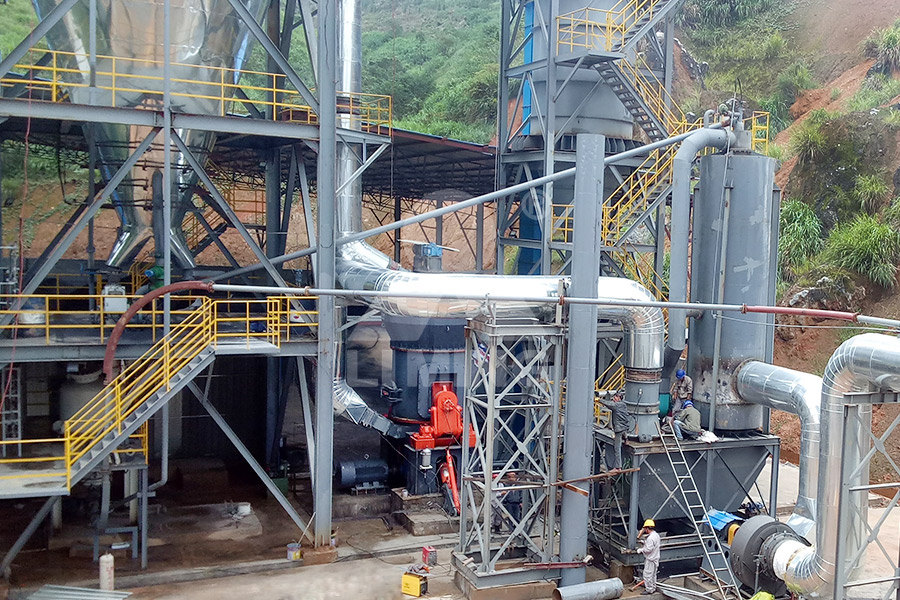
Principle of powder mixed EDM Download Scientific Diagram
Download scientific diagram Principle of powder mixed EDM from publication: Effect of Powder Mixed Electrical Discharge Machining (PMEDM) on Difficulttomachine Materials – a Systematic 1998年10月30日 Metallurgy Powder, Process, Components: Powder metallurgy (P/M) consists of making solid parts out of metal powders The powder is mixed with a lubricant, pressed into a die to form the desired shape, and then sintered, or heated to a temperature below the melting point of the alloy where solidstate bonding of the particles takes place In the absence of any Metallurgy Powder, Process, Components BritannicaIron processing Smelting, Refining, Alloying: The primary objective of iron making is to release iron from chemical combination with oxygen, and, since the blast furnace is much the most efficient process, it receives the most attention here Alternative methods known as direct reduction are used in over a score of countries, but less than 5 percent of iron is made this Iron processing Smelting, Refining, Alloying Britannica2016年6月5日 Definition of Rolling Process Rolling is the most important metal forming process More than 95% of ferrous and nonferrous metals and alloys are processed to their usable shapes by rolling Usable shapes of rolled metals are plate, sheet, strip, foil, different sections like rail, beam, channel, angle, bar, Introduction to Rolling Process (Chapter 1) Principles and
.jpg)
Iron Ore Pelletizing Process: An Overview IntechOpen
The iron ore production has significantly expanded in recent years, owing to increasing steel demands in developing countries However, the content of iron in ore deposits has deteriorated and lowgrade iron ore has been processed 2023年2月22日 Powder Metallurgy Process: Not Without Limitations PM is economical and widely used, but it has its limitations The powder metallurgy process cannot produce parts beyond 220 kilograms due to the fluidity of Powder Metallurgy Process: Steps, ApplicationsIndeed, products like instant milk or instant coffee are produced thanks to this process The possibility to avoid degradation during drying makes it also a process of choice for pharma Examples of applications for spray drying are Spray drying process : overview, fundamentals of 2024年2月5日 The powder fills the cavity and the plunger compacts it within the dosator This locks the powder in the dosator cavity Stage 3; The dosator retracts from the powder bed carrying with it the powder in the cavity Stage 4; At this point, the tip of the filled dosator should be free from excess powder A process referred to as “doctoring”Working Principle of Dosator Type Capsule Filling Machine to
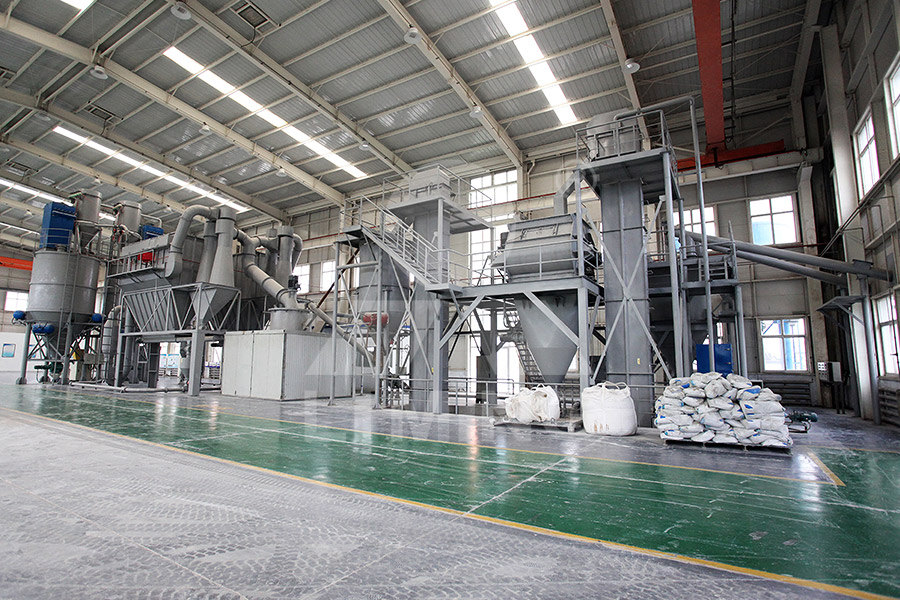
Powder Mixer Machine: Types,Production Steps,Working Principle
2024年9月18日 Powder Mixing machines: features, working principle, production steps, and types of mixers, everything you need to know These mixers are gentle on fragile powders, making them a perfect choice for materials that could be damaged Understanding the working process of powder mixer machines can optimize production efficiency and 2023年6月9日 Working Principle of Extrusion Process In the extrusion process, a substance is subjected to plastic deformation by the application of a force that causes it to flow through a die or orifice If the material has the right properties, it will assume the die's crosssectional profile, and the final extrudate will maintain that shapeExtrusion Process: Know Principle, Working, Advantages in detail2022年4月9日 working principle of the SLM process illustrated in Fig 3 initiates by applying a thin powder layer into the building platform, then the applied powder wholly melted on the thermal energy induced (PDF) Stateoftheart of selective laser melting process: A 2 An introduction to modern iron making, R H Tupkary, Khanna Publishers (2004) Course Outcomes After completing this course, the student should be able to: 1 Describe the physical and chemical processes that take place during iron making 2 Analyse the effect of change in process parameters in iron making 3LECTURE NOTES ON IRON MAKING SUBJECT CODE: PCMT 4307
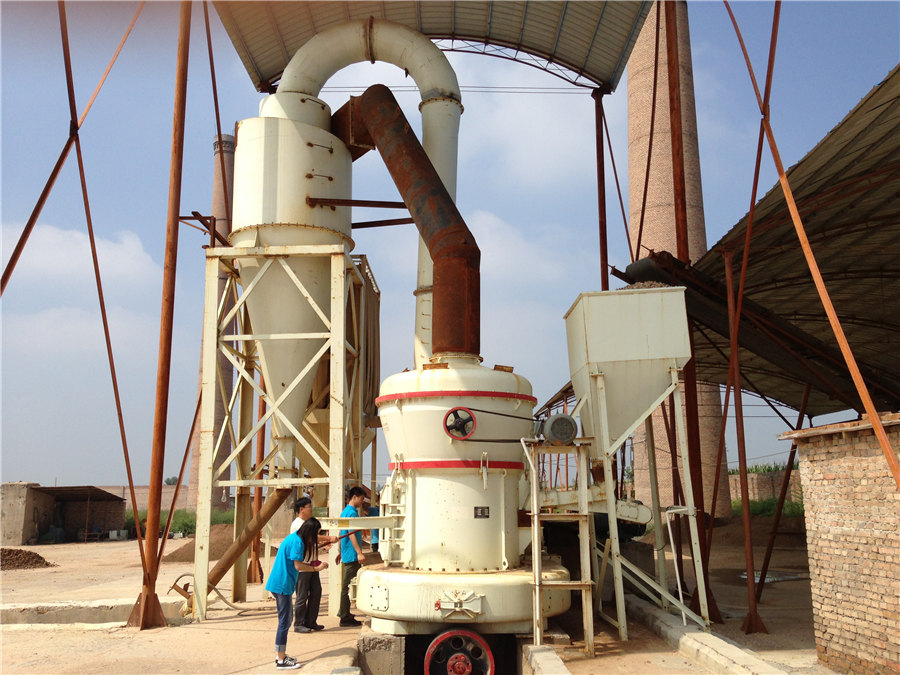
Powder Metallurgy: A Comprehensive Guide for Beginners
2023年9月5日 It is the most challenging and significant factor in injection molding and constitutes the longest step in the process 26 The Origin of Powder Injection Molding Powder injection molding is a new process that combines powder metallurgy technology with plastic injection molding2024年3月20日 Introduction to the Steel Making Process The steel making process is a fascinating journey that transforms raw materials into the world's most versatile building material Steel is central to our modern world, from towering skyscrapers to intricate machinery But the path from raw earth to refined steel is complex and involves multiple steps, each critical to Understanding the Steel Making Process: A Flow Diagram