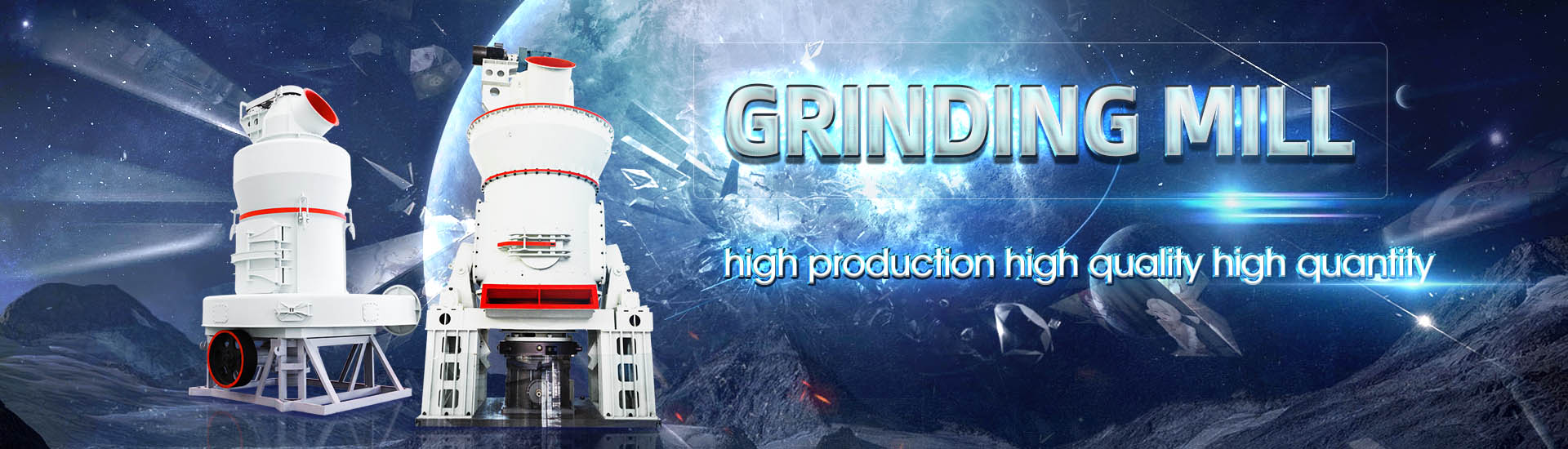
Coal powder furnace process
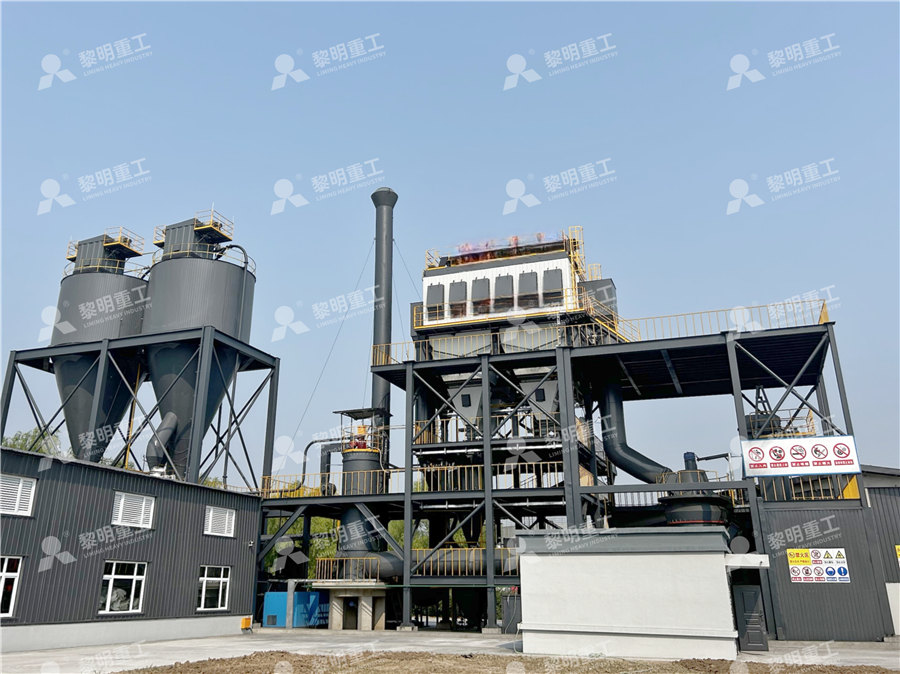
Pulverized Coal Boiler an overview ScienceDirect Topics
Steps in the process are (1) mining of the coal from nearsurface or deep mines, (2) transporting crushed coal several centimeters in size to the power station, (3) pulverizing the coal to a 2011年2月2日 Pulverized coal (pulverized fuelpf) has been fired in rotary cement kilns (see Kilns) and boiler furnaces (see Boilers) The latter are basically boxes lined with tubes in which water is evaporated and contain a PULVERIZED COAL FURNACESDuring combustion, coal particles undergo the following four welldefined steps (as illustrated in Figure 1): char oxidation The combustion process takes place not only in the burner, but also Fundamentals of pulverised coal combustion ICSC2023年3月27日 Using the model, pulverized coal combustion and the soot generation process were simulated in a 300 MW tangentially fired pulverized coal furnace Here, we proposed a soot evolution model which includes the Simulation of Pulverized Coal Combustion Process

CFD study of infurnace phenomena of pulverised coal injection in
2012年6月1日 A threedimensional mathematical model of the flow and combustion of coal powder in a coke packed bed has been developed to simulate the complicated infurnace In the present investigation, pulverized coals with high volatile contents are used as deoxidizer in aluminum silicon smelting process using “Submerged Arc Furnace” (SAF) method SAF Coal Pulverization System: Explosion Prevention and Process Control2021年11月2日 In the pulverized coal injection (PCI) process of a blast furnace (BF), intensifying the combustion of pulverized coal in the raceway and tuyere is the key to increasing the Combustion Characteristics of Coal for Pulverized Coal Injection 2023年1月13日 The analysis of literature shows that several future paths of development and scientific research related to the technology of pulverized coal combustion in boilers can be distinguished(PDF) Pulverized CoalFired Boilers: Future Directions of
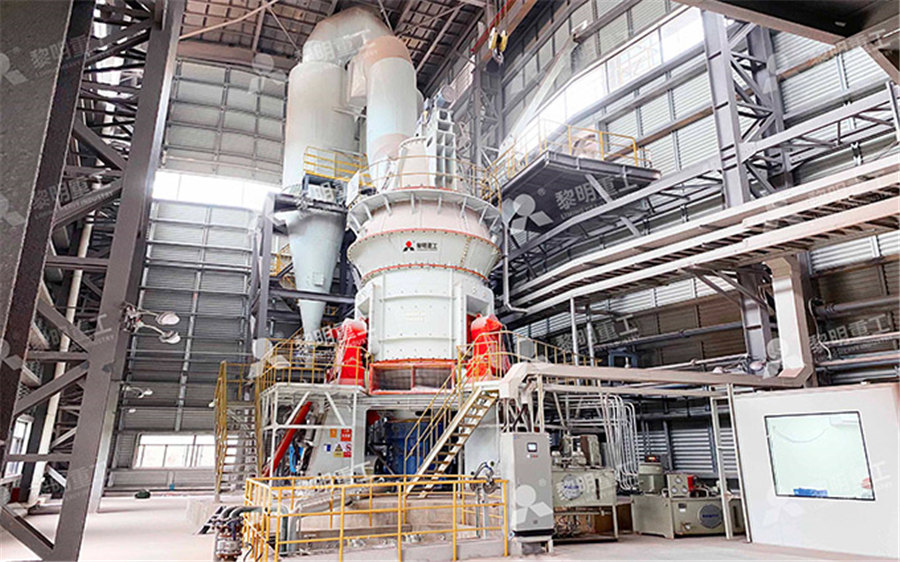
(PDF) Coal Gasification (chapter only) ResearchGate
2007年6月1日 PDF Coal gasification is presented in terms of the chemistry of coal conversion and the product gas characteristics, the historical development of Find, read and cite all the research you 2024年6月28日 In a nutshell, coalfired electricity generation is achieved through a complex process: Black or brown coal is pulverised into a powder that’s burned in a furnace; The heat generated from this turns water fed into the power CoalFired Power Stations In Australia Explained2022年8月10日 Coalconversion technologies, although used ubiquitously, are often discredited due to high pollutant emissions, thereby emphasizing a dire need to optimize the combustion process The cofiring of coal/biomass in a fluidized bed reactor has been an efficient way to optimize the pollutants emission Herein, a new model has been designed in Aspen Plus® to Flue gas analysis for biomass and coal cofiring in fluidized bed 2020年11月25日 Dried coal of BRXL lignite emits a smaller amt of NOx than that of BRXL lignite However, the dried degree of BRXL lignite is closely related to R90 fineness Dried coal with optimal moisture content yields least NOx emissions When deep or middle staged combustion was adopted, the application of multistaged combustion is conducive to NOx rednA Control Strategy of the Air Flow Rate of CoalFired Utility Boilers
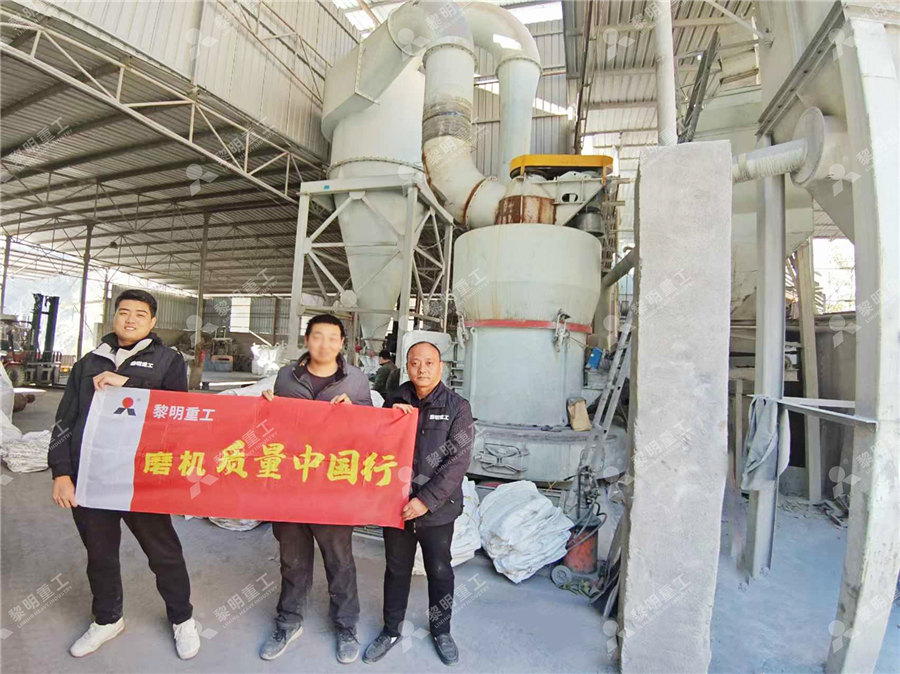
Simulation of Pulverized Coal Combustion Process Considering
2023年3月27日 The coal consumption in our country mainly lies in coalfired power stations and industrial boilers Since the temperature change in the furnace influences combustion, slagging In the pulverized coal combustion process, turbulence impacts the radiation transmission of the medium by changing the shape of the flame, and the heat release acts on the turbulence field 2024年6月15日 When employing a process of blowing pulverized coal in the BF, the temperature at the flame's center in the tuyere's raceway can rise substantially, reaching approximately 2373 K [73] Fig 11 presents the temperature variation in the raceway during the numerical simulation of scenarios where natural gas and pulverized coal (PC) are mixed, as Physical and chemical properties of metallurgical coke and its Fundamentally, due to the variation in the oxidant, and consequently in the infurnace gas environment (as compared to conventional airfired combustion), oxyfuel combustion affects the combustion process of pulverized coal as well as related processes such as heat transfer [22]Pulverised Coal Combustion an overview ScienceDirect TopicsEfficiently burning coal in a boiler or furnace is the key stage of power generation Our solutions include MWIRB640, NIRB, Lancom 4 and CDA Skip to content English Key measurements can support the efficiency of the combustion process, while helping to control emissionsCoal Boiler/Furnace Operation AMETEK Land
.jpg)
Optimization of combustion process in coalfired power plant
2017年8月1日 During last few years contactless temperature measurement technologies have become more popular in the industry There are two main technologies, which are used in coal fired boilers to measure temperature distribution – acoustic technology [2], [3], [4] and laser technology [5], [6]In [7] authors present advantages of acoustic system in evaluation of 2013年7月17日 After hand picking foreign material, coal is transported to the Crush house by conveyor belts where it is crushed to small pieces of about 20 mm diameter The crushed coal is then transported to the store yard Coal is transported to bowl mills by coal feeders 3 Bowl Mill The coal is pulverized in the bowl mill, where it is grounded to a Coal handling plant in a thermal power generating station EEP2021年4月21日 Japanese research suggests that pressed woody biomass can be used to prepare metallurgical coke after mixing with coal, achieving partial decarbonization 61 German research indicates that when using biomass coke powder to completely replace coal powder, the amount of carbon dioxide input in the blast furnace has been reduced by up to 45% 62 Lowcarbon production of iron and steel: Technology options, economic A schematic of oncethrough dry FGD processes involving drypowder injection and ductspray drying are shown in Fig 510 blast furnace process, and converter process a process used in coal power plants to bind sulfur oxides with the aim to minimise air pollutionFlueGas Desulphurization an overview ScienceDirect Topics
.jpg)
How a Coal Plant Works
Coalfired plants produce electricity by burning coal in a boiler to produce steam The steam produced, under tremendous pressure, flows into a turbine, which spins a generator to create electricity The steam is then cooled, condensed back into water and returned to the boiler to start the process over Here’s a reallife example: The 2015年2月1日 And the other plants went to Powder River Basin (PRB) coal, so they took a heat rate hit too So, someone just reckoned since we had to give up heat rate to meet emissions limits, there wasn’t Understanding Coal Power Plant Heat Rate and Efficiency4 The distribution of pulverized coal along the circumference: Utilizing a prototype, studies were made to understand the powder flow characteristics and to determine the distribution accuracy 1 Background and process overview˜ The injection of pulverized coal into blast furnaces in Japan3A2 Pulverized Coal Injection for Blast Furnaces (PCI)2017年8月1日 Optimization of combustion process in coalfired power plant with utilization of acoustic system for infurnace temperature measurement Author links open overlay panel Łukasz Śladewski a , Konrad Wojdan a , Konrad Świrski a , Tomasz Optimization of combustion process in coalfired power plant
.jpg)
Highfidelity modelling of unburnt coal flow in an industryscale
In the steelmaking industry, the ironmaking blast furnace (BF) plays a critical role in energy consumption and CO 2 emissions (Hu et al, 2019, Yu et al, 2021, Zhuo et al, 2021)To improve efficiency and reduce emissions, pulverized coal injection (PCI) technology is extensively employed in this process (Ishii, 2000, Shen et al, 2008) and biochar, a carbon–neutral solid 2021年4月20日 Cofiring coal and biomass in existing power plants facilitates influential advancement in the use of renewable energy resources and carbon emissions reduction Biomass is intended as a CO2zero net emission because, during its rise, it uses the same fraction of CO2 from the air as that released during its combustion In addition, the content of nitrogen and Experimental Study and Design of Biomass CoFiring in a FullScale Coal 2019年1月1日 However, for coalbased DR the reductant is generated from noncoking coal and rotary kilns, rotary hearth furnaces and multihearth furnaces are used (Ghosh and Chatterjee, 2017) It has been estimated that approximately 6575% of sponge iron production cost is attributed to the cost of raw materials (Indian Bureau of Mines, 2011)A review of ironmaking by direct reduction processes: Quality 2024年10月1日 Notably, the blast furnace process, which consumes large amounts of coke and pulverized coal (PC), is responsible for over 70% of the carbon emissions from steel production (Dutta Sah, 2016) Therefore, optimizing blast furnace operations is imperative, with one key area of research being the improvement of the PC injection process in blast furnaces ( Fig 1 )Numerical simulation of the effect of coaxial and crossaxis
.jpg)
Thermodynamic analysis of a coalfired power plant
2011年10月19日 India has huge coal reserves, about 71 per cent of the world’s total [] and thus the coalbased thermal power plants dominate the sourcewise mix with 541 per cent of the total installed capacity of about 174 GWe []Due 2000年8月18日 The Circofer process (Fig 8) is a coalbased process, which utilizes a combination of circulating and stationary fl uidized beds The fine ores are preheated in a twostageCOMPARISON OF DIFFERENT COAL BASED DIRECT 2023年7月15日 Most electricity generation and heat supply in China come from the combustion of fossil fuel at power plants and occupy over 50 % of Chinese coal consumption annually [1]Coalfired power plants play the dominant role with their capability of stable and reliable operation, short period of construction and low investment compared with other forms of power Combustion optimization of a coalfired power plant boiler using Coalfired power plant Kenneth Storm, in Industrial Process Plant Construction Estimating and ManHour Analysis, 2019 811 Equipment descriptions—Coalfired boiler pressure parts sheet 1 Coalfired power plants produce electricity by burning coal in a boiler to produce steam The steam produced, under pressure, flows into a turbine, which spins a generator to create CoalFired Boiler an overview ScienceDirect Topics
.jpg)
Life cycle carbon footprint of electric arc furnace steelmaking
2023年4月1日 To deal with the increasingly serious resource depletion and environmental problems [8, 9], the electric arc furnace (EAF) steelmaking process, in line with the highquality development concept and the two major themes of the green and intelligent innovation of the future ISI, served as an effective way to achieve the carbon neutral goal before 2060 during Advanced monitoring and process control technology for coalfired power plants Y Yan, in Advanced Power Plant Materials, Design and Technology, 2010 101 Introduction Coalfired power stations are burning an increasingly varied range of fuels and fuel blends, including subbituminous and lower volatile coals and biomass of varying composition and combustion CoalFired Power Station an overview ScienceDirect TopicsIEA Clean Coal Centre – Advanced sensors and smart controls for coalfired power plant 3 Preface This draft report has been produced by IEA Clean Coal Centre and is based on a survey and analysis of published literature, and on informationgathered in discussions with interested organisations and individualsAdvanced sensors and smart controls for coalfired power plant2023年2月15日 Combustion air is classified into primary air, secondary air, and overfire air (OFA), and is fed from a primary air fan and a forced draft fan, as indicated by (12) and (13), after being heated by a air preheater (8) before entering a furnace (3) in Figure 1 The operation data of the coalfired power plant consist of momentary values measured every hour, collected over Causal analysis of nitrogen oxides emissions process in coalfired
.jpg)
Lifecycle assessment of the coal gasificationshaft furnace
2020年11月1日 Request PDF Lifecycle assessment of the coal gasificationshaft furnaceelectric furnace steel production process China’s steel industry has been phenomenally developed However Fuel preparation for a pc boiler occurs in a mill, where coal is typically reduced to 70% through a 200mesh (74μm) screen Figure 2 shows a particlesize distribution from a bowlmill grinder typically used in power plants A typical utility specification for particle size distribution of the coal is that 70% of the mass should pass through a 200mesh screen, which is equivalent to 70% Pulverized Coal Boiler an overview ScienceDirect Topics2021年4月6日 The exergy assessment of the new hydrogenenriched steel production through coal gasificationshaft furnaceelectric furnace is studied in this work, which includes the material flow and exergy analysis of the overall CSE process and five subsystems (ie coal gasification gas purification, heating, pelletizing, shaft furnace, and EAF)Exergy analysis of hydrogenreduction based steel production with coal 2022年5月28日 The use of coal for power generation began in the United States in the 1880s, based on the same technology that was then used to create mechanical power from the steam engine Coal was burned to raise steam and the steam used to drive an engine, which in turn drove a dynamo or alternator, which produced electricityPower Generation from Coal, Oil, Gas, and Biofuels
]@S0{UDKK%G24F3JGHC.jpg)
Pulverized Coal Injection of Blast Furnace Ironmaking
2024年1月1日 The blast furnace injection process system is mainly composed of raw coal storage and transportation system, dry gas preparation system, pulverized coal preparation system, pulverized coal conveying system, pulverized coal injection system, and gas supply system (Fig 1)There is also a computer control center to control the entire pulverized coal 2017年8月10日 The top gas recycling oxygen blast furnace (TGROBF) is a new ironmaking process which can significantly reduce the coke ratio and emissions of carbon dioxide To better understand the coal combustion characteristics in the TGROBF, a three dimensional model was developed to simulate the lance–blowpipe–tuyere–raceway of a TGROBF The combustion Coal Combustion Behavior in New Ironmaking Process of Top 2004年4月1日 The blast furnace pulverized material injection simulator, showed in Figure 1, takes the variables of the process into consideration The two most important variables are the low particle New Developments for Powder Coal Injection into the Blast FurnacesThe effect of biomass cofiring on the furnace exit gas temperature and the gaseous emissions of CO 2, NO x and SO x is examined for a biomass cofiring based pulverized coal power generation system We consider four biomass fuels (rice husk, sawdust, chicken litter and refused derived fuel) and two coals (bituminous coal and lignite)Analysis of Emissions and Furnace Exit Gas Temperature for a
.jpg)
Modeling and Energy Efficiency Analysis of the Steelmaking Process
2022年9月16日 This paper presents a comprehensive model of an industrial electric arc furnace (EAF) that is based upon several rigorous firstprinciples submodels of the heat exchange in the EAF and practical experience from an industrial melt shop The model is suited for process simulation, optimization, and control applications It assumes that the energy demand of the 2023年6月4日 It is now agreed that climate change, is being caused by excess accumulation of GHG emissions in the earth’s atmosphere—majorly as CO2 from use of fossil fuels for meeting humanity’s needs over the last two centuries Steel production, a vital industry, needs transition to lower its carbon footprint Globally, almost 90% of CO2 emissions of ‘primary steelmaking’ The Blast Furnace: A Vital Tool in Climate Neutral OreBased Analysis of Coal Dust Oxyfuel Combustion Process of modelling of coal dust oxyfuel combustion in a cyclone furnace starts from supplying coal dust (500 µm) in the amount 1×103 kg/s to the upper part of the chamber PC2 through two inlets located at the opposite sides of the chamber The fuel was fed with the stream ofModelling of the Process of Coal Dust Combustion in a Cyclone FurnaceA fossil fuel power station is a thermal power station which burns a fossil fuel, such as coal, oil, or natural gas, to produce electricityFossil fuel power stations have machinery to convert the heat energy of combustion into mechanical energy, which then operates an electrical generatorThe prime mover may be a steam turbine, a gas turbine or, in small plants, a reciprocating gas Fossil fuel power station Wikipedia