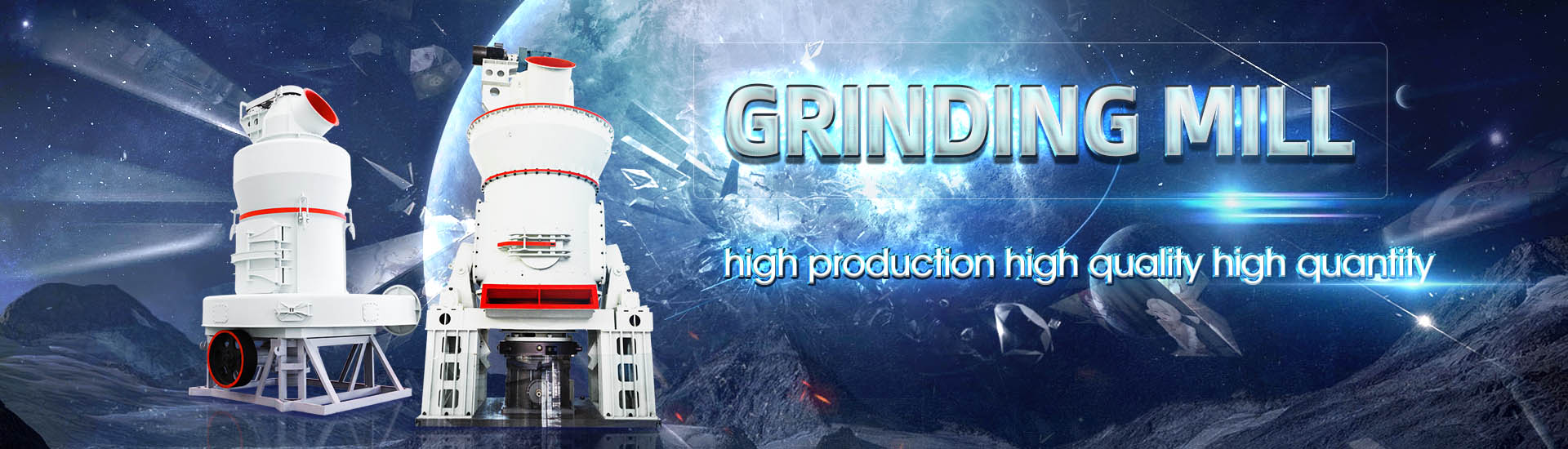
Powder mill performance introduction
.jpg)
Powder Milling an overview ScienceDirect Topics
2010年4月1日 The principle of mechanical milling is based on the ballpowderball collision in the case of shaker mills, frictional and impact forces in the case of planetary ball mills (Prasad Yadav et al, 2012), and very high shear and impact forces in the case of Attrition mills (Rajput, 2023年6月29日 1 Introduction Usually, it is common to apply a vertical stirred mill (VSM) in process industries handling various kinds of powders, especially at ultrafine scale The main Analysis and Optimization of the Milling Performance of an size distribution and type of balls on the performance (energy) of the high energy ball milling has been investigated for the first time Furthermore, different scenarios that lead to an increase Powder TechnologyThe performance test on the fabricated ball mill for the aluminum in powder form and blended with alumina shown proper distribution through scanning electron microscope images for different (PDF) IJERTDesign and Performance of Ball Milling for Powder
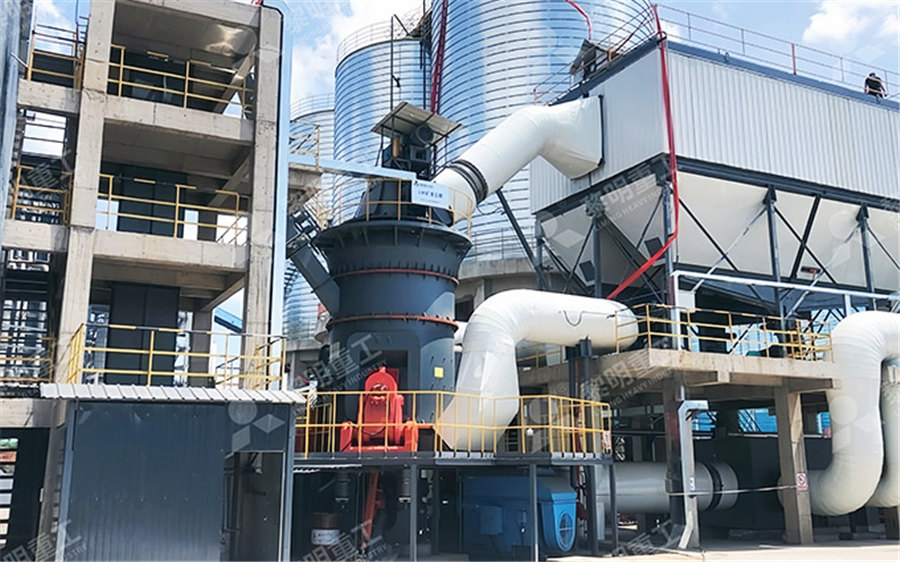
Optimization of the high energy ballmilling: Modeling and
2016年4月1日 The results showed that the powder weight loss can greatly enhance the performance of milling, while the increase of the number of balls at high BPR ratio, has a quite 2024年1月15日 This study is concerned with evaluating the performance of a novel roller mill, in which the crushing platen is a vertical wall over which cylindrical rollers rotate, thereby Optimisation of the performance of a new vertical roller mill by 2019年5月28日 Mechanical alloying is a nonequilibrium processing technique in which different elemental powders are milled in an inert atmosphere to create one mixed powder with the same(PDF) Design and Performance of Ball Milling for Powder The effect of grinding media geometries and density on the mill performance was also reviewed to determine what the research has recommended as the most suitable grinding media for Powder metallurgy – basics applications Academia
.jpg)
Application of Powder Simulation to Powder Metallurgy
Powder simulations provide a macroscopic interpretation of powder behavior by calculating the motion of individual particles that constitute the powder In this paper, the powder simulation is The present paper is the report of a study and development of suitable milling tools to be used in the well known Simoloyermill or in other high kinetic systems The goal is to be able to use PROCEEDING OF CERAMIC POWDER USING2024年8月8日 Introduction In the intricate dance of ball milling, where raw materials are transformed into finely milled particles, the choice of grinding media emerges as a pivotal performance lever This seemingly minor selection can Ball Mill Success: A StepbyStep Guide to Choosing 2021年9月29日 It is a highly efficient industrial powder mill +17 [ protected It also has good adsorption performance, rheological performance, and catalytic performance It has more than 130 uses, making it Sepiolite Superfine Powder Grinding Mill SBM
.jpg)
PROCEEDING OF CERAMIC POWDER USING
PROCESSING OF CERAMIC POWDER USING HIGH ENERGY MILLING H Zoz, H Ren Zoz GmbH, Maltoz Strasse, D57482 Wenden, Germany Keywords: high energy milling, milling process, ceramic powder, fine powder, ball mill, grinding system, Simoloyer 1 Introduction High Energy Milling (HEM) is a well known and commercially used technique [13] Today theIn conclusion, dietary supplementation with a moderate concentration of fennel affects carcass performance, and intestinal morphology, and promotes the growth and development of broilers Keywords: Fennel seed powder, Growth performance, Apparent metabolic rate, Carcass traits, Intestinal morphology IntroductionEffects of dietary fennel (Foeniculum vulgare Mill) seed powder Brief Introduction of Ultrafine Vertical Mill It has excellent performance and can be used for papermaking, coatings, plastics, rubber, PVC, printing ink, and other industries to provide highquality fillers and additives Ink Ultrafine vertical roller mill stone powder production lineUltrafine Vertical Mill SBM Ultrafine Powder TechnologySilica powder is made of natural quartz (SiO2) or fused quartz (amorphous SiO2 after natural quartz is melted and cooled at high temperature) through crushing, grinding, flotation, acid washing purification, highpurity water treatment and other processes So what is the performance and production process of silicon powder? The following describes the performance of silicon News Introduction To The Performance Of Silicon Powder And
.jpg)
Analysis of vertical roller mill performance with changes in
2022年5月31日 Mineral crushing is the main source of energy consumption in mineral processing According to statistics, this consumption accounts for about 35–50% of the total cost of the mine (Curry et al, 2014), or even higherIt may also account for 18% of the global electrical energy consumption (NapierMunn, 2015)More efficient crushing equipment needs to be PDF On May 28, 2019, Girisha Lakhman Naik and others published Design and Performance of Ball Milling for Powder Metallurgy Composites Find, read and cite all the research you need on ResearchGate(PDF) Design and Performance of Ball Milling for Powder Table I Machinery Combinations Machinery Combination Treatment No T\ M\ T2 M2 T3 M,M, T4 M2M2 Ts M,M2 T6 M2M, T7 M2M2M2 T8 M,M,M, T9 M,M2M2 TIO M\M,M2 TII M2M,M, T'2 M2M2M, in order to ensure that Performance Evaluation ofDifferent TypesofSpice Grinding 2021年11月27日 Powder Grinding Mill Introduction The powder grinding mill is the equipment used to grind and process materials such as ore The important parts are made of highquality steel, and the wear parts are made of highperformance wearresistant materials, What is Powder Grinding Mill? JXSC Machine
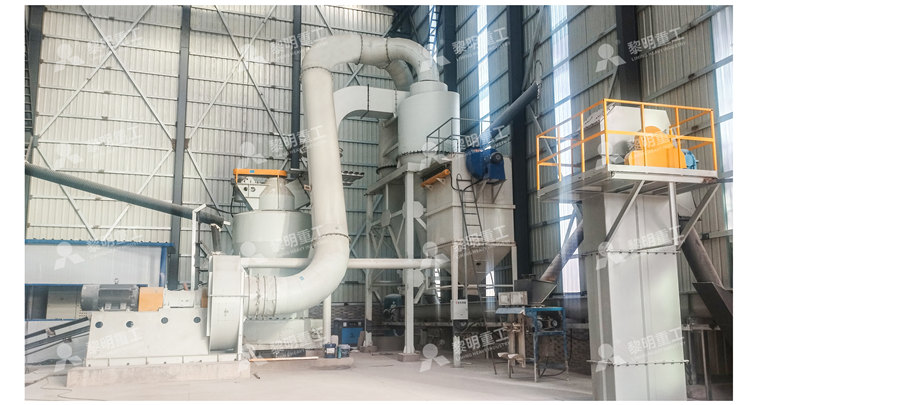
Optimisation of the performance of a new vertical roller mill by
2024年1月15日 The results show notable air ingress from the bottom of the mill, due to moving components in the mill This is detrimental to mill performance as the milled powder gets recirculated back into the milling region and reduces the overall milling efficiency Optimisation of the mill design has been carried out based on CFD modelling resultsBackground With the increasing demands in livestock and poultry breeding and the growing number of foodborne diseases, it is necessary to practice food safety and develop strategies to produce healthy livestock Fennel (Foeniculum Effects of dietary fennel (Foeniculum vulgare Mill) HGM100A professional ultra fine powder grinder is the new type mining equipment for making micro powders, fine powders, which is widely applied in the industries of metallurgy, mining, chemistry, cement, construction, refractory ultra fine powder grinding mill Shanghai Clirik Semantic Scholar extracted view of "The effect of ball size on mill performance" by L G Austin et al Skip to search form Skip to main content Skip to account menu Powder Technology; View via Publisher Save to Library Save Create Alert Alert Cite Introduction to the mathematical description of grinding as a rate process L G The effect of ball size on mill performance Semantic Scholar
.jpg)
Carbon Black Ultrafine Powder Mill
2021年8月31日 Introduction to equipment configuration of carbon black powder production line: SBM carbon black ultrafine powder mill has superior performance and good quality Directly produced and sold by the factory, the production efficiency is Introduction of Fine Impact Mill This SeFluid’s superfine powder mill series is composed of crushing host, cyclone separator, or pins to achieve optimal grinding performance Advantages of Fine Impact Mill Fine impact mills have a wide range of applications in Fine Impact Mill for powder making with 7 super features SeFluid2021年12月23日 The advantages of the ball mill are: 1 Stable operation and reliable work; 2 The use of materials and processing techniques with excellent performance extends the service life of main components; 3 Use threedimensional design and simulation to optimize the design to make the equipment more costeffective; 4Introduction advantages of ball mill ALPA Powder EquipmentHC Grinding Mill HC Series Grinding Mill widely applied in mineral grinding processing of metallurgy, construction material, chemical industry and mine fields, and is widely used to grind minerals with Mohs hardness below 7 and moisture below 6%, such as limestone, calcite, active carbon, talc, dolomite, titanium dioxide, quartz stone, bauxite, marble, feldspar, barite, fluorite, HC Grinding Mill, Raymond Mill, Pendulum Powder Mill, Non
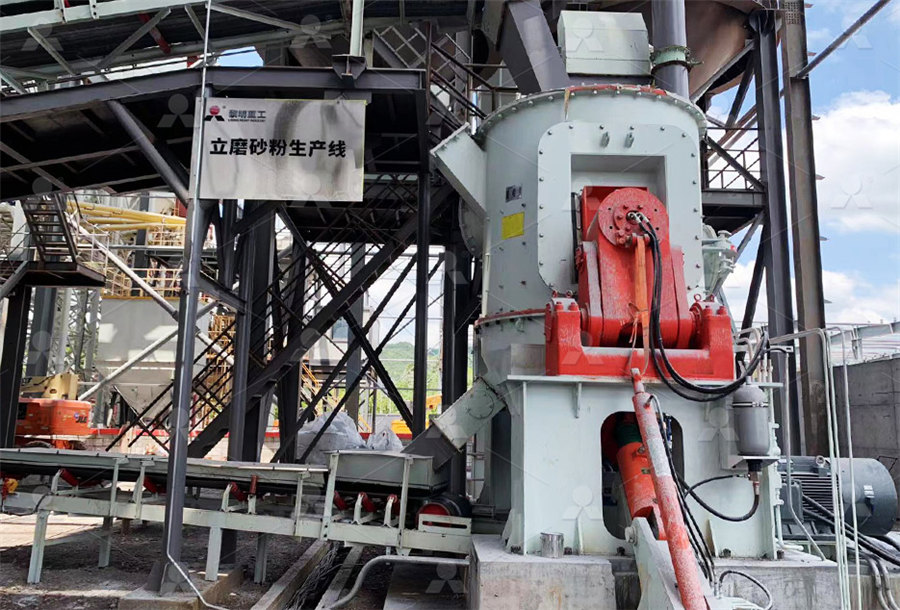
SCALEUP OF TOWER MILL PERFORMANCE USING MODELLING
Fine Particle Breakage Characterisation Single particle breakage tests are often used to study breakage properties of materials (Schönert, 1979; Whiten, 1987)2019 The performance of a hammer mill fabricated in Uganda was evaluated and the optimal performance conditions were determined The evaluation was done with screen hole diameters (S) of 15, 20, and 30 mm, hammer tip speeds (H) of 6812, 8181, 10217 m s and hammer thicknesses (T) of 40, 50, and 60 mm for determination of energy consumption and Design, Fabrication, and Performance Evaluation of a Hammer Mill 2020年8月12日 This study shows the performance of a currently running vertical roller coal mill (VRM) in an existing coalfired power plant In a power plant, the coal mill is the critical equipment, whose An investigation of performance characteristics and 2014年3月1日 With a view to developing a sound basis for the design and scaleup of ball mills, a large amount of data available in the literature were analyzed for variation of the two key mill performance (PDF) Analysis of ball mill grinding operation using mill power
.jpg)
Design and Performance of Ball Milling for Powder Metallurgy Composites
Keywords—Composite,MMC,Powder metallurgy,SEM I INTRODUCTION The composite material is the combination of two or more The performance test on the fabricated ball mill for the aluminum in powder form and blended with alumina 2010年4月1日 Introduction M Sherif ElEskandarany, in Mechanical Alloying, 2001 11 BACKGROUND Fundamentally, the term milling may be referred to as the breaking down of relatively coarse materials to the ultimate fineness Apart from the milling of ores, milling is also used for preparing materials for some industrial applications, such as milling of quartz to fine Powder Milling an overview ScienceDirect Topics2019年5月28日 The performance test on the fabricated ball mill for the aluminum in powder form and blended with alumina shown proper distribution through scanning electron microscope images for different weight percentages of alumina The ball mill is used for different speed, time conditions and conditions with the capacity of 250gms can be operated REFERENCESDesign and Performance of Ball Milling for Powder Metallurgy Compositesof calcite in a laboratory scale conventional ball mill Within the context, the influence of operating parameters such as mill speed, ball filling ratio, ball size distribution, powder filling ratio, grinding aid dosage and grinding time were studied The results of grinding tests were evaluated based on the product particle size (d 50, d 80Influences of operating parameters on dry ball mill performance
.jpg)
Performance optimisation of vertical spindle coal pulverisers
spindle coal pulverising mill’s performance to facilitate optimal plant performance Plant design and mill’s acceptance test data was analysed to understand the design and subsequent changes over the years of the mill’s operation The mill outputs, pulverised coal fineness and2022年5月31日 Introduction; Section snippets; Minerals Engineering Volume 182, 31 May 2022, Analysis of vertical roller mill performance with changes in material properties and operating conditions The vertical roller mill (VRM), including powder separation and crushing subsystems, is used extensively for intermediate crushing of Analysis of vertical roller mill performance with changes in 2021年10月26日 Product features: higher capacity, better powder quality, better overall performance Input size: 010mm Capacity: 518TPH Highpressure Powder Mill Vertical structure, so it has a small footprint, as well as the introduction of chemically active fluids, which change the existing solid rock In the process of metamorphism, Graphite Grinding Machine Powder Mill EquipmentThe Mikro® UMP Universal Milling System utilizes the same design and operating principles perfected in the original Mikro Pulverizer® Hammer and Screen Mill It was developed to meet the increased demand for highperformance machines for multiple applicationsHosokawa Mikro UMP – Introduction – Hosokawa Micron Powder Systems
CFB石灰石脱硫剂制备——磨机公众号12.8 推送案例(8)51.jpg)
Powder Coating Process Explained – A Detailed
Introduction to Powder Coating – Categories, Substrates, Manufacturing Before we go into the specifics of the process on how powder coating is applied, let’s take a moment to cover powder coating as a whole Powder coating of calcite in a laboratory scale conventional ball mill Within the context, the influence of operating parameters such as mill speed, ball filling ratio, ball size distribution, powder filling ratio, grinding aid dosage and grinding time were studied The results of grinding tests were evaluated based on the product particle size (d 50, d 80Influences of operating parameters on dry ball mill performanceAdvanced process control systems, such as mill optimization software, can analyze various operational data and provide recommendations for optimizing mill performance For instance, using mill optimization software can lead to up to Cement Mill Optimization: Practical Strategies for 2020年1月1日 Introduction; Section snippets; References (66) Cited by (50) Grinding kinetics by breakage function helps in evaluating the breakage mechanism and the performance of the grinding mill [35] However, The wet grinding of iron Wet and dry grinding of coal in a laboratoryscale ball mill: Particle
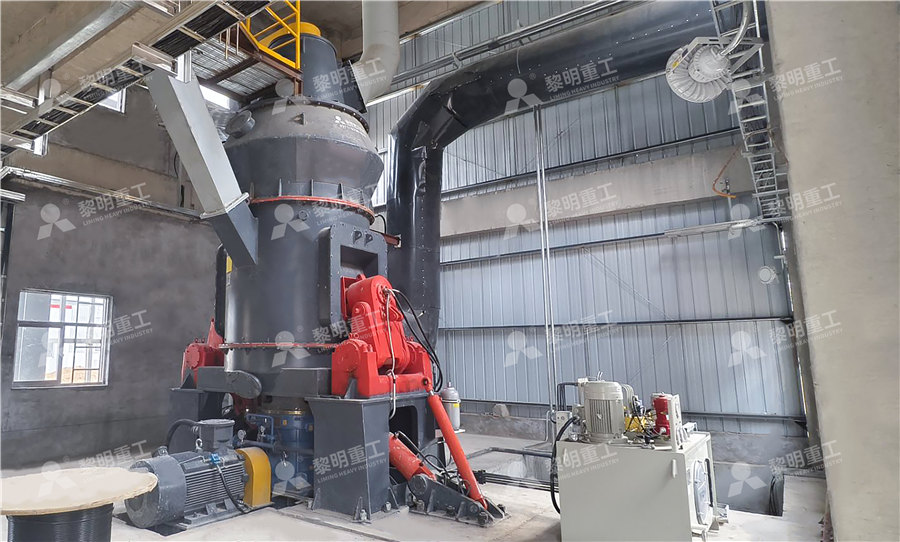
Research on performance of a laboratoryscale SAG mill based
2022年7月1日 The performance of the SAG mill is greatly affected by its structural and operating parameters and the characteristics of the rock material in the drum Cleary et al [7] systematically studied the influence of changes in mill operating parameters and particle characteristics on the charge characteristics and mill power based on DEM2023年8月1日 Introduction With the developing technology, fc = Mass of powder / powder density Mill volume Influences of operating parameters on dry ball mill performance Physicochem Probl Miner Process, 54 (2018), pp 751762 View in Scopus Google Scholar [26] D Ocepek, E EberlEffective role of grinding aids in the dry grinding performance of 2023年4月24日 Introduction According to data Kanda, Y Experimental study on the grinding rate constant of solid materials in a ball mill Powder Technol 2002, 122, 101–108 [Google Scholar] Tavares, LM; de Carvalho, RM Modeling breakage “Optimization of mill performance by using online ball and pulp measurements,” J South Afr Grinding Media in Ball MillsA Review [v1] Preprintslaboratory preparation of powder coatings Types of Mills used to match a production ACM mill The most common pieces of equipment used in the laboratory preparation of powder coatings including the following: coffee grinder, Vitamix, Brinkman, Bantam, and a bench top ACM mill This equipment ranges in price from $25 for a coffee grinder up to The Strand Mill Laboratory Preparation of Powder Coatings Introduction
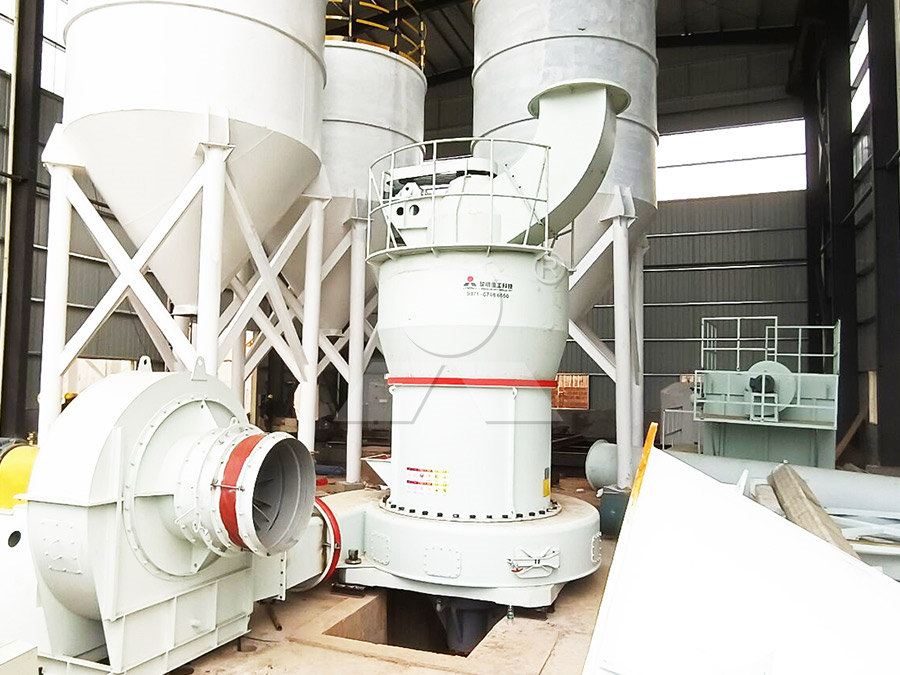
Narrowing particle size distributions to enhance powder coating
2024年2月15日 However, present powder coatings produced by ACM usually have wide PSDs, marked by undesirable ultrafine particles ( 80 μ m), presenting an enduring challenge in the powder coating industryIn the ACM operation, a highspeed rotor with grinding pins pulverizes chips into particles, while the classifier Abstract Flake silver powder with controllable particle size and specific surface area was prepared using planetary ball mill by varying milling parameters including milling time, revolution speed, and the weight ratio of balls to powder (BRP) Asprepared flake silver powder was characterized by laser particle analyzer, scanning electronPreparation of microsize flake silver powder by planetary ball mill