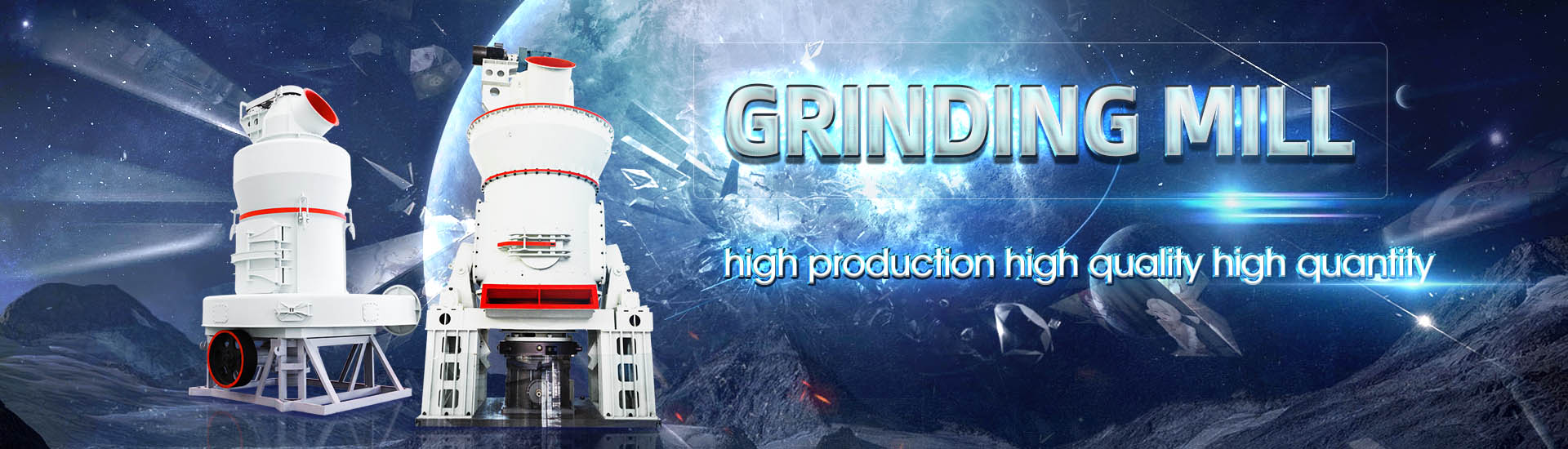
Coal mill energy efficiency index
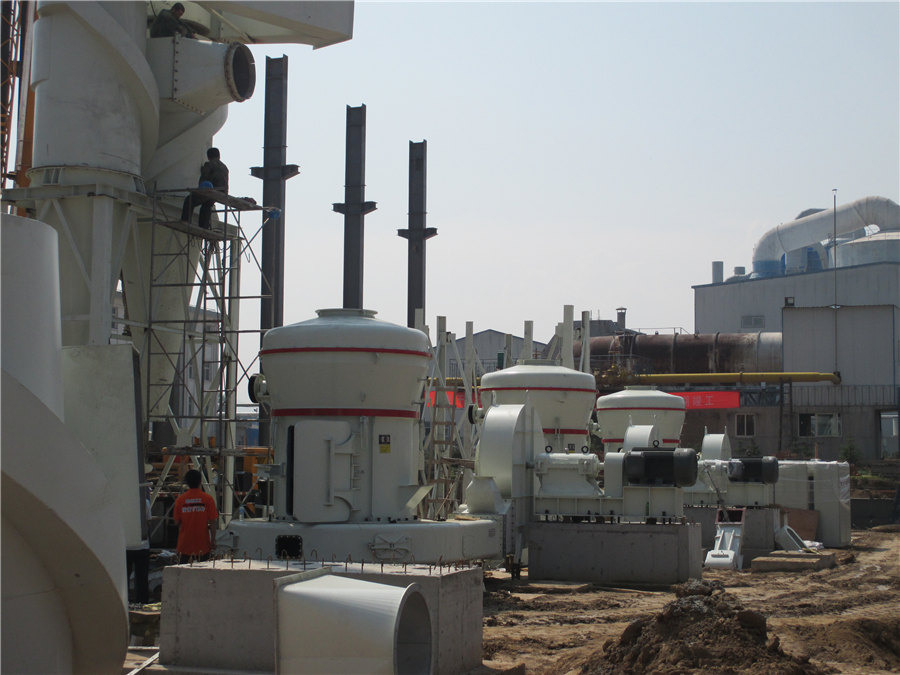
An investigation of performance characteristics and energetic
2020年8月12日 This study shows the performance of a currently running vertical roller coal mill (VRM) in an existing coalfired power plant In a power plant, the coal mill is the critical 2020年1月1日 The operational optimisation of coalfired power units is important for saving energy and reducing losses in the electric power industry One of the key issues is how to Benchmark value determination of energy efficiency indexes for The effect of low calorific value coal was observed on mill’s response to match the boiler energy requirements Evaluation of the current operating pulveriser data enabled the determination of Performance optimisation of vertical spindle coal pulverisers2018年11月1日 This study redesigns energy efficiency evaluation indicators for underground coal production It uses eight indicators, divided into two categories (composite evaluation Developing a more comprehensive energy efficiency index for coal
.jpg)
Efficiency assessment of coal energy and noncoal energy under
2021年1月6日 The average eastern coal index efficiency was 098, the average central coal index efficiency was 094, and the average western coal index efficiency was 091 From 2011 2022年9月1日 Considering China's low energy efficiency as a dominant barrier in achieving sustainable development goals and environmental pollution control, the presented study is Evaluating the factors of coal consumption inefficiency in energy Aiming to achieve 50% cofiring on a thermal basis, IHI has been working to verify and demonstrate the effectiveness of a comprehensive system — including the supply chain for Meeting the Challenge of Realizing a High Ratio CoFiring System 2020年1月1日 The operational optimisation of coalfired power units is important for saving energy and reducing losses in the electric power industry One of the key issues is how to Benchmark value determination of energy efficiency indexes for
.jpg)
Technology Roadmap HighEfficiency, LowEmissions CoalFired
Combined with CCS, HELE technologies can cut CO2 emissions from coalfired power generation plants by as much as 90%, to less than 100 grams per kilowatthour HELE technologies will Performance optimisation of vertical spindle coal pulverisers SR Chateya Dissertation submitted in fulfilment of the requirements for the degreePerformance optimisation of vertical spindle coal pulverisers2016年10月18日 The paper industry is heavily using energy during all the phases of the manufacturing process This is especially the case in Nordic mills where pressure ground wood is the source of fiber The purpose of this case study is to show how energy consumption behaves on a monthly basis in a Finnish paper mill that has several paper machine lines The research Energy efficiency at the paper mill—dilemma of improvement2021年1月6日 The demand for energy has continued to increase because of global economic development, which has led to rising fuel prices and continued pollution problems China is currently the largest coal consumer and is also the largest emitter of coalfired CO2 emissions However, past efficiency studies have been mostly limited to static analyses and have not Efficiency assessment of coal energy and noncoal energy under
.jpg)
Effect of moisture on energysize reduction of lignite coal in
2020年6月15日 The classical JKFBC energysize reduction model would be applied to describe the effect of moisture content on the energy efficiency for Shengli lignite in the Hardgrove mill [38]: (4) t 10 = A × 1eb ∙ E cs where t 10 is the cumulative passing of ground particles less than 1/10th of the initial granule geometric mean size (%), which is approximately 009 mm in this 2015年11月1日 As presented by Andersen et al (2009) and Odgaard, Stoustrup, and Mataji (2007), coal moisture imposes limit on the maximum load at which a coal mill can be operated and the load gradient (how fast the mill may change its operating point), if it is desired that the pulverized coal entering the furnace has moisture content less than or equal to a certain value A unified thermomechanical model for coal mill operation2023年4月10日 If the coal was PRB, (8,4008,900 Btu/lb) coal I would suspect that there could be issues with the heat rate or the coal flow measurement as the calculated Btu/lb is too high for PRB coals Method 3 Heat Rate Models If the unit is equipped with a heat rate model, these can be useful as both a valid value and another method for comparisonCoal Plant Efficiency Heat Rate Calculation Methods Energy angle on the classification efficiency in CoalFired power plants The gas flow inside the coal mill was solved by the realizable k ε turbulence model (RKE) with a detailed 3D classifier geometry meanwhile the discrete phase model was used to solve the coal particles flow The steepest classifier blade angle of 40 o achievedINVESTIGATION ON CLASSIFICATION EFFICIENCY FOR COAL
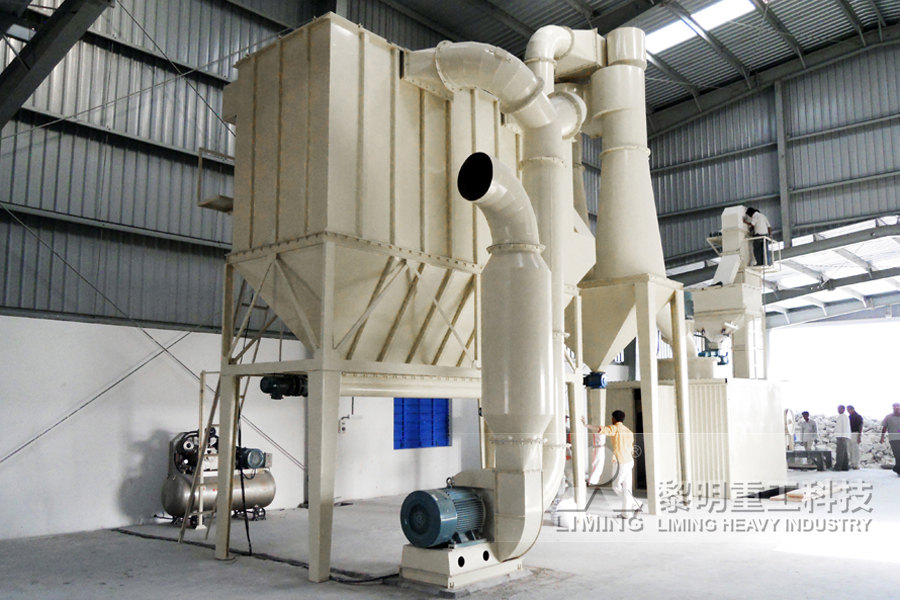
Coal explained Mining and transportation of coal US Energy
Coal miners use large machines to remove coal from the earth Many US coal deposits, called coal beds or seams, are near the earth's surface, but others are deep underground Modern mining methods allow US coal miners to easily reach most of the nation's coal reserves and to produce about three times more coal in one hour than in 1978The primary energy demand in India has grown from about 450 million tons of oil equivalent (toe) in 2000 to about 770 million toe in 2012 This is expected to increase to about 1250 (estimated by International Energy Agency) to 1500 (estimated in the Energy Efficiency Government of India Ministry of Power1998年11月1日 Share this article Anyone you share the following link with will be able to read this content: Get shareable linkUsing the Bond work index to measure operating comminution efficiency 4 Methodology for Baseline and Energy Performance Index (EPI) 2 41 General rule for establishing Baseline 3 42 Methodology for Baseline and Energy Performance Index (EPI) 3 43 In built Normalization in EPI Calculation 3 431 Product Mix 3 432 Energy Mix 4 433 InputOutput for a typical Cement plant 4 434 Normalisation Factor considered 5Cement Sector Bureau of Energy Efficiency

Ball Mill Energy Efficiency Optimization Techniques: A Review
Ball mills are essential machinery in the mining industry, thermal powerproducing companies, and cement manufacturing companies, for grinding different ores, grinding coal into pulverized coal, and processing cement clinkers into fine powder cement or pulp Their design operational and energy inefficiencies are because of drivetrain inefficiencies, output load rerun, lifter face 1989年1月1日 This balance indicates that the total energy input into the initial section of the coal mill is equal to the total energy output from the terminal section of the coal mill This method considers all the energy involved in the coal mill; however, no coal mill model has been established based on the heat balance of coal mills [9–11]Calculation of energy required for grinding in a ball mill2024年10月25日 This is the official website of Coal Ministry, Government of India You can find information related Tenders, Energy Efficiency Measures; Guidelines Report; Videos; Nominated Authority About NA; Auction/Allotment; National Coal Index Base year 20172018 (provisional) for the month of September 2024364 MB Ministry of Coal, Government of India2015年4月1日 González et al [18] proposed an energy efficiency index, EEI B for buildings, which relates the energy consumption within a building to that of a reference building The objective of this index is to develop a quantitative energy efficiency metric, based on actual measurement as well as accurate prediction of energy consumptionEnergy efficiency index as an indicator for measuring building energy
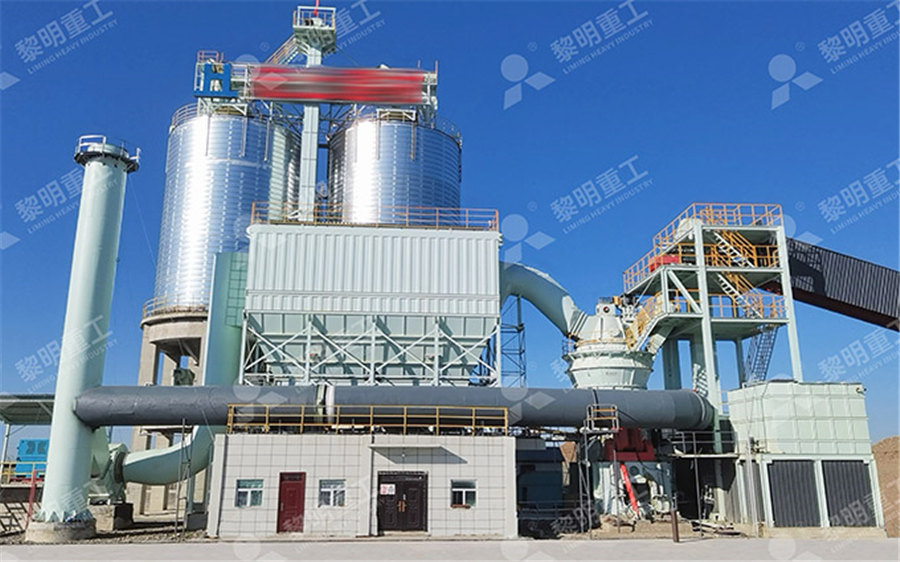
Boiler Mill and Coal Pulverizer Performance GE Steam Power
Our Boiler Mill and Coal Pulverizer Service Solutions help you make the most of your mill’s operational efficiency Learn more about GE's boiler mill servicesThe average energy efficiency of Australian coalfired power plants is one of the lowest among the OECD countries which is 33% In a typical coalfired plant, there are pulverisers to mill the coal to a fine powder for burning in a combustion chamber of the boilerExergy Analysis and Efficiency Improvement of a Coal Fired 2020年3月15日 Xie and He also adopt the similar concept and applied to the mixture grinding of minerals, and coals of various narrow size fractions in a Hardgrove mill [13], [14] Based on the energy split factor, energies split by components are determined and interaction between components is evaluated by the change of grinding energy efficiency [15]Energysize reduction of mixtures of anthracite and coking coal 2014年1月1日 Common primary energy sources are coal, oil, natural gas, and biomass For the sugar mill, energy usage and GHG emissions for 1 ton of sugar production were 761667 MJ and 46536 kgCO 2eq, respectively Bureau of Energy Efficiency (2011) Carbon Footprint and Energy Estimation of the Sugar Industry: An
.jpg)
Mill Optimisation Process Efficiency hrl: expertise in action
Mill maintenance costs are one of the highest maintenance costs in a coal fired power station; Testing allows a change to 'condition based' maintenance (from set mill operating hours) which in HRL's experience can increase time between minor / major mill overhauls by up to 10%;2019年7月19日 Besides the aspects of the coal selection, the efficiency of the process is mainly determined by the operating parameters compacting time and compacting energy for coal cake making At the beginning of the densification process, the particulate material yields under the stress applied by the compacting equipment, thereby filling the interstitial voids of the particle Coke Making: Most Efficient Technologies for Greenhouse Emissions consumption ~2145 Crores No of Electrified Households (under SAUBHAGYA scheme) Per Capita Electricity Consumption State (As on Mar’23) Highest: Goa 3,360 kWh Lowest: Bihar 348 kWh Maharashtra Top Electricity Consuming India Climate Energy Dashboard2014年3月1日 The influence of the coal blending and minerals in coal on the grinding efficiency was studied and the optimization scheme was put forward [8], [9] The pulverizing efficiency of the coal was optimized and improved by the establishment of mathematical model in order to reduce energy consumption and pollution emissionBreakage and separation mechanism of ZGM coal mill based on
.jpg)
Breakthrough in Clinker Grinding Massachusetts Institute of
2012年11月8日 energy of the material was equivalent to the loss of the material’s strain energy According to Griffith’s energy balance, a crack will grow, when the energy release rate equals the crack’s resistance force The propagation of a crack in an elastic solid must encompass three separate energies: external energyestablish test methods for evaluation of energy efficiency characteristics of the gear oils [15] A novel product has been developed and credentials established in the coal mill gearbox of thermal power plant Experimental: This paper describes the details of new energy efficient industrial gear oil developed in the author’sExtended Abstract (Control ID ) Society of Tribologists 2012年1月1日 Hardgrove grindability index (HGI) is an important indicator of coal grindability, and is one of the most important parameters to determine the capacity of coal pulverizer in power station However, HGI is an empirical grindability index without linkages to any known physical parameters To investigate the effect of energy input on the grinding in Hardgrove mill, a Relationship between coal size reduction and energy input in Hardgrove mill2024年7月30日 With the rapid economic growth, the energy demand is increasing in China Coal accounts for the largest proportion of China's energy consumption, and low coal use efficiency will generate more undesirable output like CO2 and soot, which inevitably lead to environmental problems and human diseases This paper aims to measure the impact of coalfired, soot on The Impact of CoalFired, Soot on China's Industrial Springer
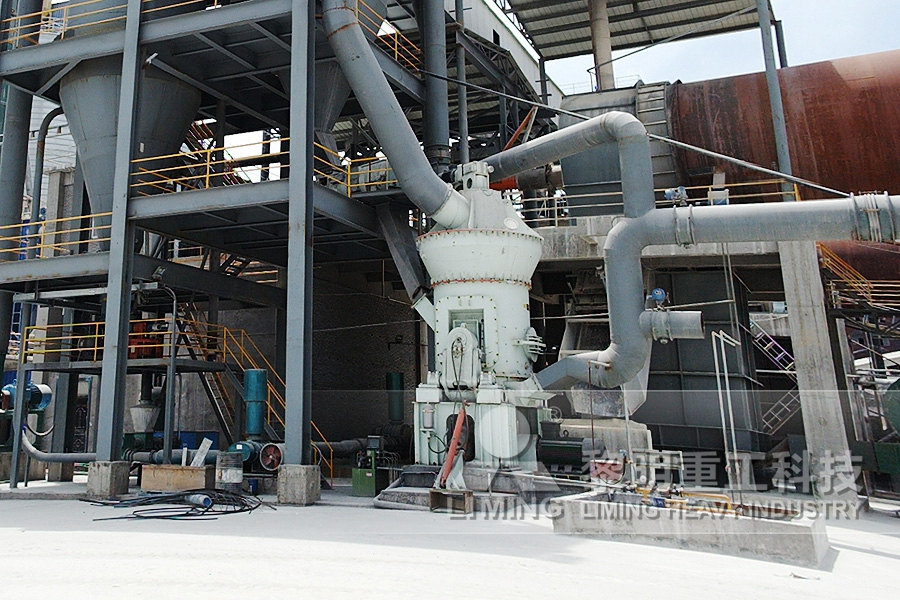
Breakage and separation mechanism of ZGM coal mill based
2014年3月1日 The influence of the coal blending and minerals in coal on the grinding efficiency was studied and the optimization scheme was put forward [8], [9] The pulverizing efficiency of the coal was optimized and improved by the establishment of mathematical model in order to reduce energy consumption and pollution emission2022年1月1日 The energy efficiency index method is less applicable for analyzing primary energy use There are typically problems with data quality and for example, millspecific energy conversion factors are unknown Moreover, the used method considers only the input energy, and therefore mills with excess energy have a lower primary energy efficiency indexPulp and paper industry in energy transition: Towards energyefficient 2020年3月15日 Energy split factors of coking coal is smaller than one, and decreases with product t 10, especially for the 3:1 mixture Above conclusions mean that the more anthracite coal added in mixture, the less energy efficiency of coking coal in multicomponent grinding Download : Download highres image (169KB) Download : Download fullsize image Energysize reduction of mixtures of anthracite and coking coal 2023年10月1日 The Bond ball mill work index test is a standard procedure to determine the ore grindability in function of specific energy (kWh/ton) This index is extensively used in the mineral processing industry and needs an available skilled staff and specially prepared feed samples ( Aksani and Sönmez, 2000 )Estimation methodology for Bond ball mill work index
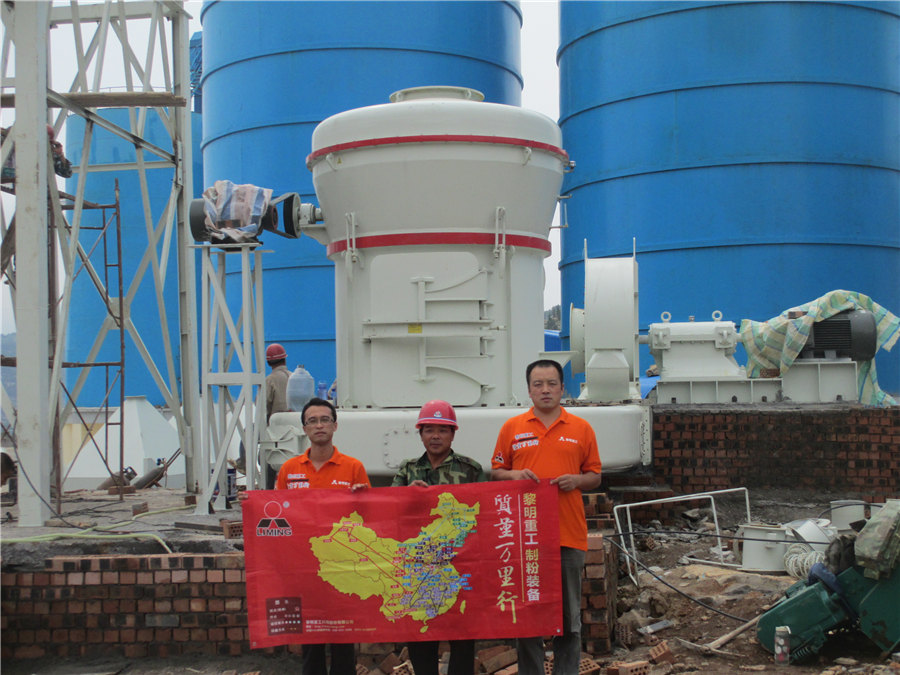
Coal mill model considering heat transfer effect on mass
2021年8月1日 Yukio et al [7] proposed a model consisting of blending, grinding and classifying processes for pulverizer control Agarawal et al [8] differentiated coal powder into ten size groups, divided the bowl mill into four zones, and developed a unified model Palizban et al [9] derived nonlinear differential mass equations of raw coal, recirculation coal and suspension coal in 2023年1月15日 Several studies have investigated the particle breakage in the stirred media mills [6, 7]In addition, the optimization of the size reduction process in stirred mills as a function of the operation parameters is a subject of several research works [8, 9]The stress model was widely used to optimize the particle breakage in the stirred media mills [10] Although stirred mills are Novel methodology for mill efficiency determination based on 2012年1月1日 4 Conclusions (1) The experiments indicated that Shi–Kojovic model fits the coal breakage process in Hardgrove mill well, with a mean R 2 of 0967 (2) The form of Shi–Kojovic model can be used to simulate the relationship between t −75 and k(E cs − E min) in the case of identical feed size, with a mean R 2 of 0952 Under the same k(E cs − E min), the content of Relationship between coal size reduction and energy input in Hardgrove mill2023年2月22日 Chinese coal enterprises are facing severe challenges due to lowcarbon economy requirements and capacity reductions This paper adopts a dynamic SBM model to compare the mining efficiency of each mining area of a coal company in China We use total excavation footage, number of working platforms, and machine quantities as input indicators, Dynamic slackbased measure model efficiency evaluation of
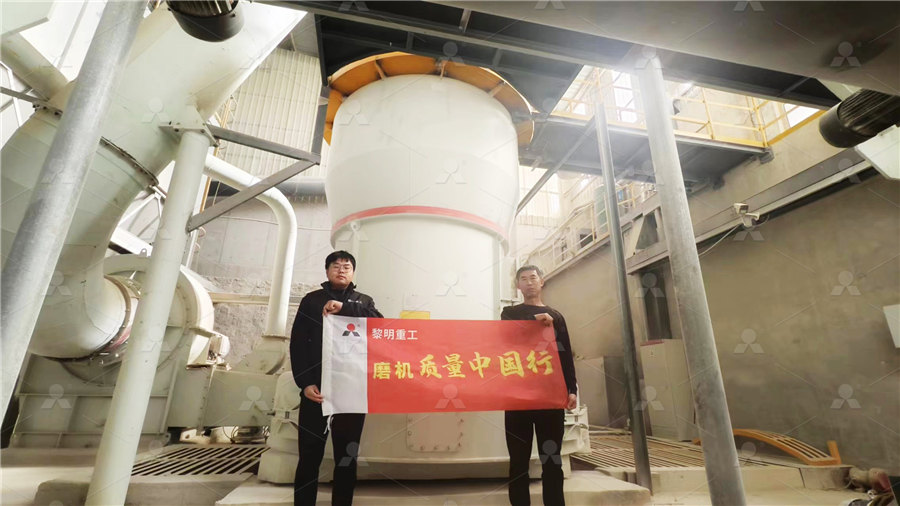
Achieving carbon neutrality in energy transition economies:
2024年7月24日 This study inspects the environmental impact of resource efficiency, natural gas efficiency, and coal efficiency in the top energy transition economies while incorporating economic growth and globalization, social globalization, political globalization, and economic globalization as control variables We utilized the method of moments quantile regression to analyze a dataset 2013年1月1日 Grindability – Hardgrove Grindability Index (HGI) is the most commonly used parameter for characterising the grindability of higher rank coals However, this measure is somewhat meaningless if lignite is being considered The vast majority of coal mill designs are based upon a 50 to 55 HGI design pointCoal utilisation in the cement and concrete industries2023年12月16日 The presence of rejected coal in a thermal power plant's coal mill significantly impacts its performance Rejected coal, consisting of noncombustible impurities, harms the mill in several ways: Reduced Efficiency: Impurities in rejected coal damage grinding elements, lowering grinding efficiency The mill works harder, increasing energy Utilization of Rejected Coal Through Blending Techniques in 2024年3月13日 Guo P, Qi X, Zhou X, et al Totalfactor energy efficiency of coal consumption: an empirical analysis of China's energy intensive Li Z, et al Logarithmic Mean Divisia Index (LMDI) decomposition of coal consumption in China based on the energy allocation diagram of coal flows Energy 2015; 85: 366–378 Crossref Web of ScienceUnleashing China's coal conservation potentials by analyzing efficiency