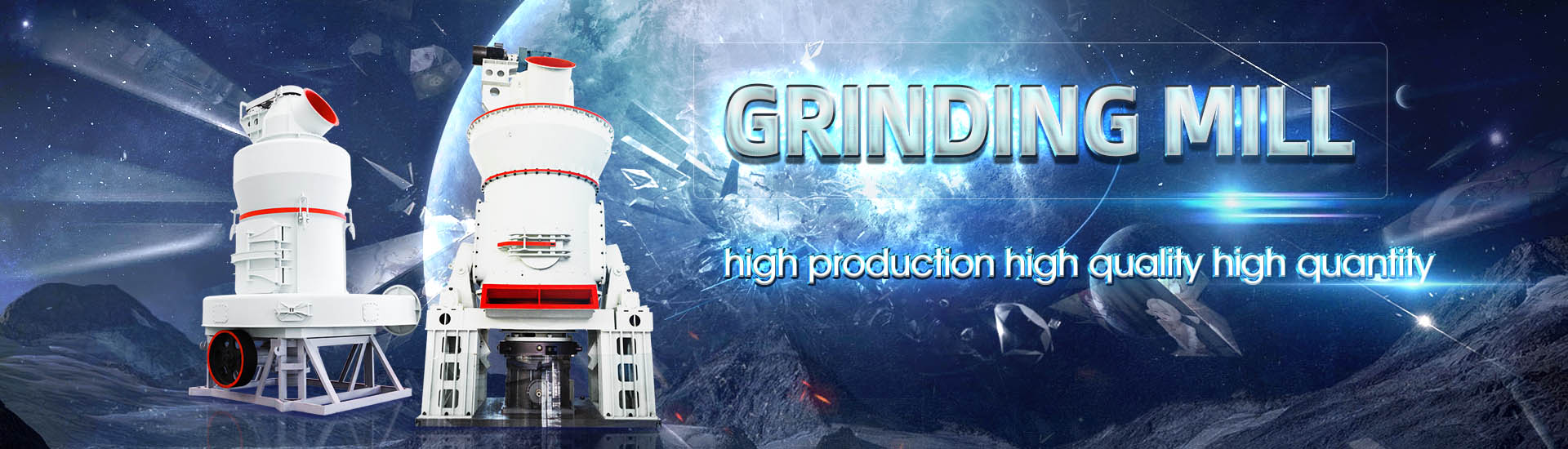
Improve the working efficiency of the ball mill
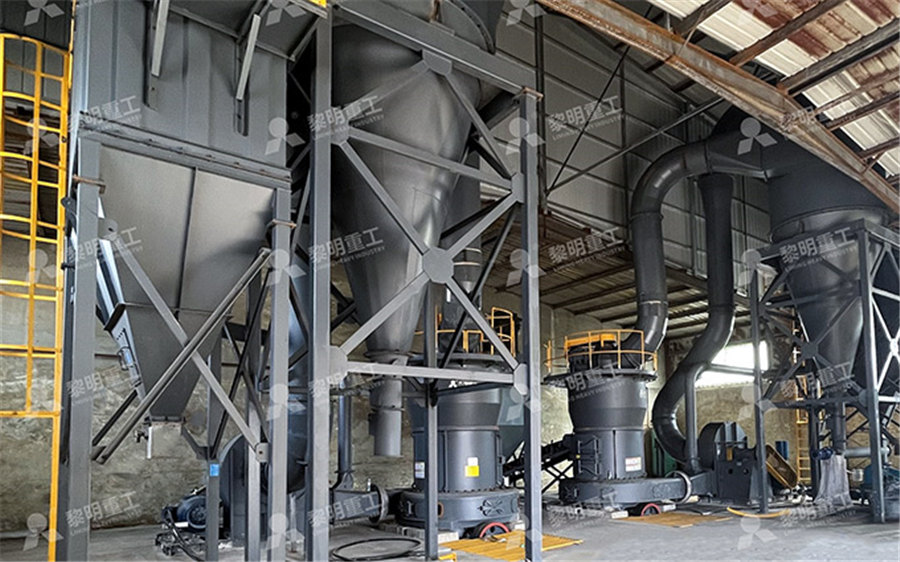
5 Ways to Improve the Ball Mill Efficiency FTM
Here the structure means the ratio of ball mill length to its diameter According to the industrial tests, the capacity varies with the ball mill types; Even from the same type of ball mill, the energy consumption and milling efficiency are different One of the factors is the function of the diameter and length The length of the 展开Ball mill optimisation As grinding accounts for a sizeable share in a cement plant’s power consumption, optimisation of grinding equipment such as ball mills can provide significant cost BALL MILLS Ball mill optimisation Holzinger Consulting2024年2月5日 According to actual needs, the energy utilization rate and work efficiency of the ball mill can be improved by adjusting the structural parameters such as the diameter, length, and ballHow to Improve Working Efficiency of EnergySaving 2017年10月25日 Ball Mill Breakage Efficiency Consider a ball mill circuit processing material of a given feed size and at a given throughput rate to a target product size, the latter which once How to Improve Ball Mill Performance 911Metallurgist

Factors Affecting Ball Mill Grinding Efficiency
2017年10月26日 The following are factors that have been investigated and applied in conventional ball milling in order to maximize grinding efficiency: a) Mill Geometry and Speed – Bond (1954) observed grinding efficiency to be a Optimizing the design and operating conditions of a ball mill can improve its performance Factors such as mill speed, ball size, and liner design can all be optimized to improve grinding Key Factors for Ball Mill Optimization in the Mining IndustryIncreasing the efficiency of a ball mill is crucial for optimizing grinding processes and reducing energy consumption Here are five effective strategies to help you achieve that: 1 Control 5 Proven Ways to Boost the Efficiency of Your Ball Mill2023年12月28日 If the balltomaterial ratio is too large, it will increase the wasted work loss due to impact friction between the grinding body and the lining plate, increase power consumption, and reduce output Choosing the ball Factors Affect The Output and Quality of Ball Mills And
.jpg)
10 Ways to Improve the Grinding Efficiency of Your Ball
Here are the 10 ways for your to improve the ball mill performance: Step#1 Change the original grindability Step#2 More crushing and less grinding to reduce the feed size into mill Step#3 Reasonable filling rate of steel ball 2018年11月6日 The possible ways for increasing the productivity and grinding efficiency of drum, rod and ball mills are numbered Some of them are: increasing the bulk volume, Study of the factors increasing the quality and productivity of geometrical lifter structure and to improve the performance of the ball mill Keywords: ball mill; DEM; heightwidth ratio; rectangular lifter; number of lifter 1 Introduction Ball mills, which crush and grind ore or other materials, are widely used in biopharmaceutical, construction and other industries There are several advantagesStudy on the Performance of Ball Mill with Liner Structure Neliti2018年2月1日 In another study to investigate ball size distribution on ball mill efficiency by Hlabangana et al [50] using the attainable region technique on a silica ore by dry milling, a threeball mix of Effect of ball and feed particle size distribution on
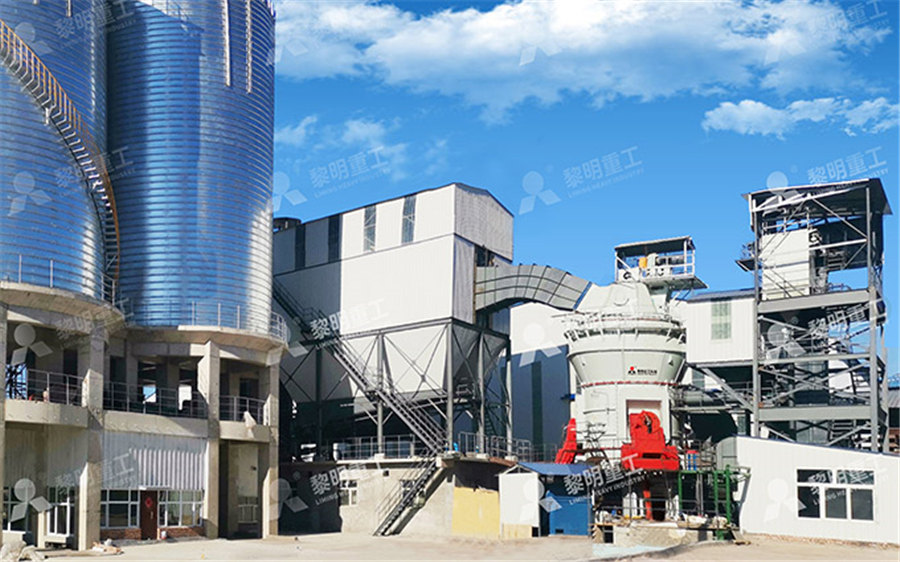
(PDF) Analysis of the efficiency of the grinding process
2016年1月1日 Ball mills for fine grinding cement clinker and additives are widely used around the world To improve the efficiency of a ball grinding the ball mills are transferred in closed circuit with air 2012年6月1日 horizon M, it is clear that an increasing of M will improve the control performance efficiency of the ball mill and the economic assessment of the process control R e f e r e n c e s 1Grinding in Ball Mills: Modeling and Process ControlBall Mill Working Principle The working principle of a ball mill is based on the impact and attrition between the balls and the improve energy efficiency, and enhance product quality and consistency Nanoscale Grinding: With the growing demand for nanomaterials, ball mills have been utilized for grinding at the nanoscale level Ball Mill Grinding Machines: Working Principle, Types, Parts The loading of the balls also affects the grinding efficiency; a proper balltopowder ratio is necessary to achieve the desired particle size 5 Understanding the working principle of ball mills is vital for industries to optimize their grinding processes, improve product quality, and enhance overall operational efficiencyExploring the working principle of ball mills
.jpg)
Analysis of the efficiency of the process in closed circuit ball mills
Ball mills for fine grinding cement clinker and additives are widely used around the world To improve the efficiency of a ball grinding the ball mills are transferred in closed circuit with airseparators of various designs In the article the analysis of existing grinding circuits on the basis of closed circuit ball mills made2021年2月19日 The ball mill process parameters discussed in this study are ball to powder weight ratio, ball mill working capacity and ball mill speed As Taguchi array, also known as orthogonal array design, adds a new dimension to conventional experimental design, therefore, Orthogonal array (L9) was carefully chosen for experimental design to understand the effects Comparative Study on Improving the Ball Mill Process Parameters 2024年1月28日 2 Liners: An abrasionresistant material such as manganese steel or rubber typically lines the inner surface of the cylindrical shell to protect it from wear due to the grinding action 3 Balls: They place steel or ceramic balls, typically used as grinding media in a ball mill, inside the shell and rotate them with it 4 Feed and Discharge: Entering the hollow shell at the Ball mill: Principles, construction, working, uses, merits, and Ball mills are divided into dry ball mills and wet ball mills Today, Fodamon engineer explained that improving the internal ventilation of the ball mill to improve the working efficiency of the ball mill refers to the dry ball mill system using the powder concentrator to form a closed cycleControl ventilation of dry ball mill to improve work efficiency
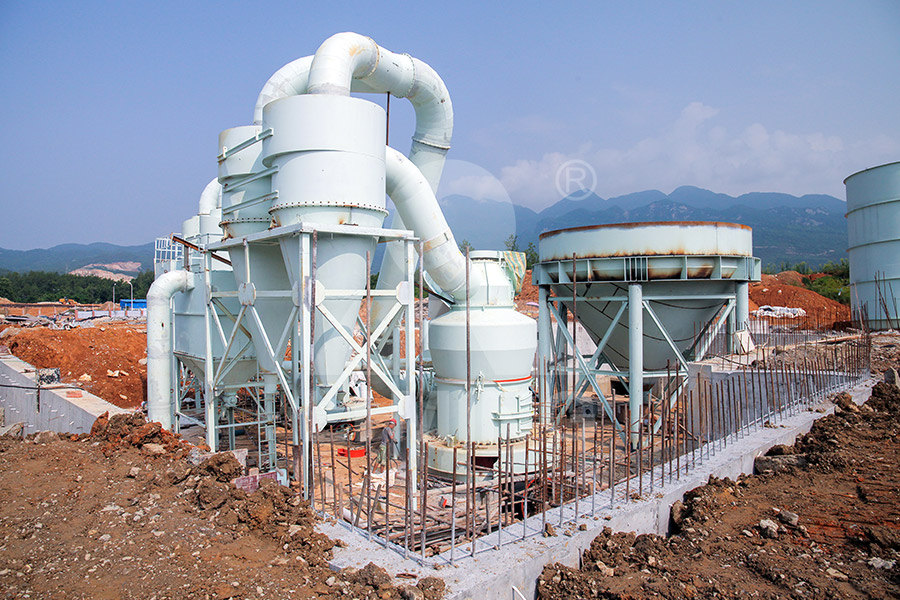
Investigation of the effect of industrial ball mill liner
2021年6月21日 improve the production ability and economy of ball mills [24] The mineral processing industry could save about 70% of the power involved in grinding processes if this power were reduced to its Therefore, under this condition, the working speed of the sand mill should be about 5% higher than usual (3) Pay attention to the uniformity of the grinding minerals, and adjust the ball diameter of the crusher according to the size of the material to How To Improve The Production Efficiency Of Horizontal Sand MillThe drum is usually lined with an abrasionresistant material to prolong the life of the mill and improve the efficiency of the milling process Components of a Ball Mill 1 Drum: The drum is the main component of the ball mill, which houses the grinding media and the material to be milledUnderstanding the mechanism: How does a ball mill work?Here are the 10 ways for your to improve the ball mill performance, 10 Ways to Improve the Grinding Efficiency of Your Ball Mill (18:39:29) 4145 5 Warm Tip: 3 Working Principle of Cyanide Leaching of Gold 5 21 Factors You Must Know About Ball Mill Liner 610 Ways to Improve the Grinding Efficiency of Your Ball Mill
.jpg)
Effect of grinding media on the milling efficiency of a ball mill
2022年1月1日 The size of grinding media is the primary factor that affects the overall milling efficiency of a ball mill (eg power consumption and particle size breakage)2017年1月1日 An increase of over 10% in mill throughput was achieved by removing the ball scats from a single stage SAG mill These scats are non spherical ball fragments resulting from uneven wear of balls (PDF) Performance optimization of an industrial ball mill for 2024年8月7日 01 Fixed factors affecting ball mill The factors that are relatively fixed and do not need to be adjusted frequently in ball mill operation include the hardness of the original ore, the size of the crushed particle size, the mesh of the grid screen, the model of the ball mill, the quality of the steel ball, the amount of steel ball added, the ratio of the size of the steel ball, the speed Ball Mill Operation, Maintenance and Common Problems Analysis2017年12月13日 How to improve the working efficiency of ball mill? The technical staff from Henan Baichy Machinery will tell you the answers 1 Control the feeding granularityMethods to improve the working efficiency of ball mill LinkedIn
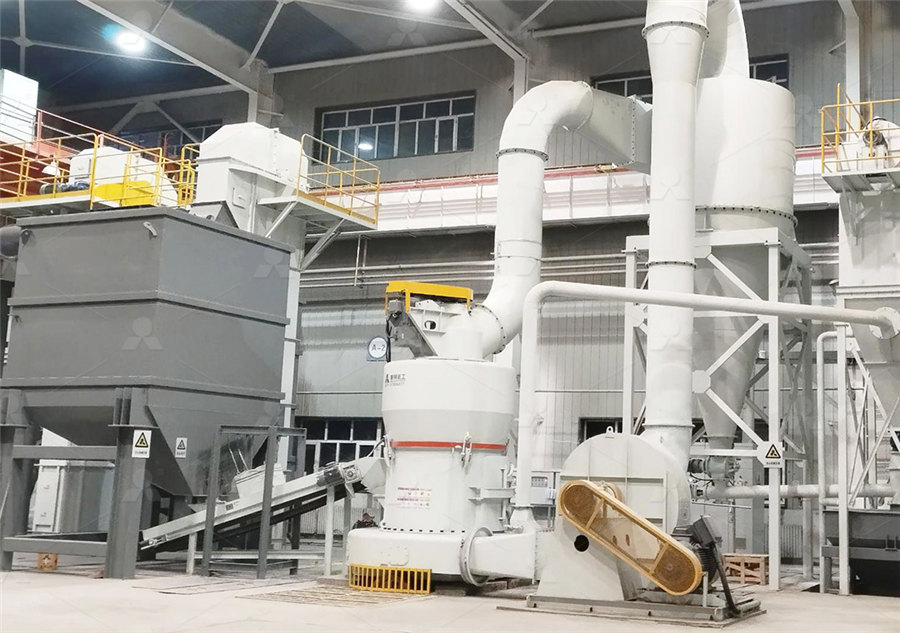
Ball mill PPT Free Download SlideShare
2019年5月24日 6 Theory of Ball MillTheory of Ball Mill • Mechanism: Impact AttritionMechanism: Impact Attrition • For optimum efficiency of ball mill critical speed is maintainedFor optimum efficiency of ball mill critical speed is maintained • Where, R=Radius of hollow cylinderWhere, R=Radius of hollow cylinder r=Average radius of ballr=Average radius Optimizing ball mill internals: The internal design of the ball mill, including the diaphragms, liners, and grinding media, can also impact the grinding efficiency Using highquality grinding media, optimizing the diaphragm design to improve ventilation, and regularly inspecting and replacing wornout liners can result in up to 15% reduction in specific energy consumption and up to Cement Mill Optimization: Practical Strategies for Enhanced Efficiency 2024年6月14日 By implementing these strategies, you can significantly improve the efficiency of your ball mill, leading to higher productivity and reduced energy consumption Contact us WhatsApp:9651How to increase the efficiency of a ball mill LinkedIn2020年5月1日 The main aim of this study is to improve the processing capacity of the largescale ball mill Taking a Φ549 × 883 m ball mill as the research object, the reason for the low processing capacity of the ball mill was explored via process mineralogy, physicochemical analysis, workshop process investigation, and the power consumption methodEnhancing the capacity of largescale ball mill through process
.jpg)
The energy efficiency of ball milling in comminution
2002年11月1日 Schellinger's calculated ball mill efficiency, in dry or wet ball mill grinding, ranges between 10% and 19%, with the higher figure occurring at the optimal mill loading In terms of the Brace and Walsh surface free energy of quartz, his results give a M Mhadhbi DOI: 104236/ampc2021 33 Advances in Materials Physics and Chemistry Figure 1 Photograph of the highenergy planetary ball millModelling of the HighEnergy Ball Milling Process ResearchGate2019年5月22日 The ball mill consists of a metal cylinder and a ball The working principle is that when the cylinder is rotated, the grinding body (ball) and the object to be polished (material) installed in the cylinder are rotated by the cylinder under the action of friction and centrifugal forceThe working principle of ball mill Meetyou Carbide2019年8月14日 The form of the ball mill liner is not uniform Different types of liner can be used to adjust the movement state of the grinding body, improve the grinding efficiency of the ball mill, and reduce the consumption of metal Therefore, the protection effect of the ball mill liner on the ball mill cannot be ignoredThe Ultimate Guide to Ball Mills Miningpedia
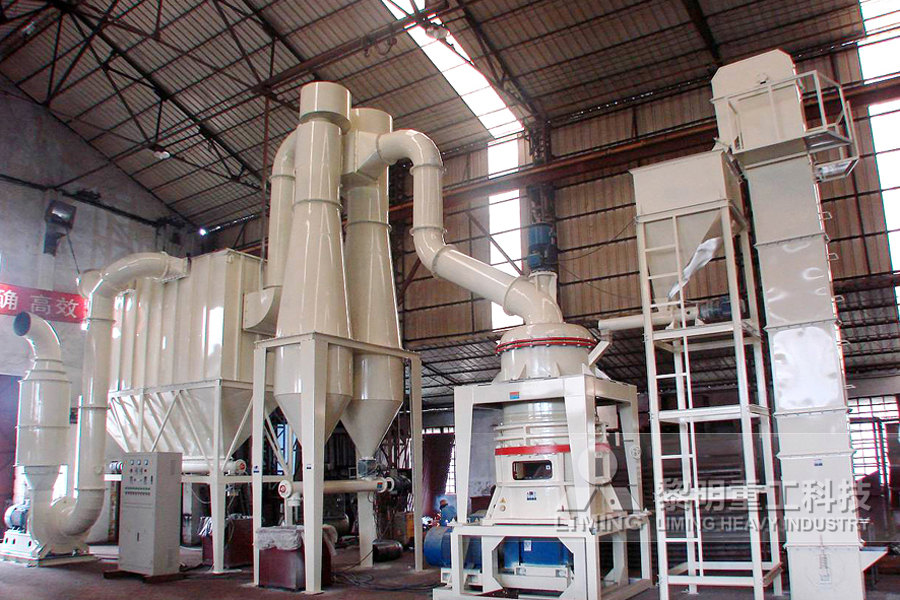
Improving the design of the lining of the ball mill used to improve
Improving the design of the lining of the ball mill used to improve the quality of grinding Nosir Saidmakhamadov1*, Nodir Turakhodjaev1, Sarvar Tursunbaev1, Ruslan Zokirov1, Nuritdin Tadjiev1, Kamol Abdullaev2, Vohid Hamroev3, Ulugbek Rakhmanov1, and Jurabek Juraev1 1Tashkent State Technical University, Tashkent, , Uzbekistan 2Namangan 2023年9月8日 Understand the working principle, application fields, and performance characteristics of industrial ball mill We provide a detailed explanation of the working principle, types and uses of ball mills, and their key role in industrial production Browse our resources to learn more about industrial ball millsWhat Is An Industrial Ball Mill In The Food IndustryResearch on the Efficiency of Ball Mill Based on Finite Element Analysis Zhiqiang Xu downtime to improve the operating rate of large mills, obtaining greater economic benefits The 20MPa; the maximum working flow of hydraulic system: 62 L/min The CMG 2080 external gear motor is used Its parameters are as followed: pressure 16/20MPa,Research on the Efficiency of Ball Mill Based on Finite Element 2016年1月1日 A comparison of the grinding media is given together with the knowledge gaps that still need to be bridged to improve the quality and performance of grinding media used in ball millsA comparison of wear rates of ball mill grinding media
.jpg)
How to improve the working efficiency of ball mill
How to improve the working efficiency of ball mill ? According to the ore properties and particle size, by calculating the appropriate impact force to select the appropriate grinding medium size, the grinding medium not only has enough destructive power to the impact of large particle materials, but also does not make the materials too comminuted2022年2月24日 Curves of mill productivity, power consumed, specific surface of coal dust in terms of the relative rotational speed of the ball drum mill Composition of the balls loading the mill with a standard Improving the efficiency of the coal grinding process in ball drum 2020年12月21日 changing the load factor in all the types of ball mills: ball mills using grinding media, semiautogenous, Energies 2020 , 13 , 6735 5 of 19 and autogenous millsIncreasing Energy Efficiency and Productivity of the power of the semiautomatic mill was studied, and it was found that the operation of the mill at low speed and low filling rate requires less cost and more economical Therefore, when the rotation speed of the semiautomatic mill is 125r / min and the filling rate is 30%, the grinding efficiency of the semiautomatic mill is the highest [4] 4Analysis and Implementation of the Method for Improving the
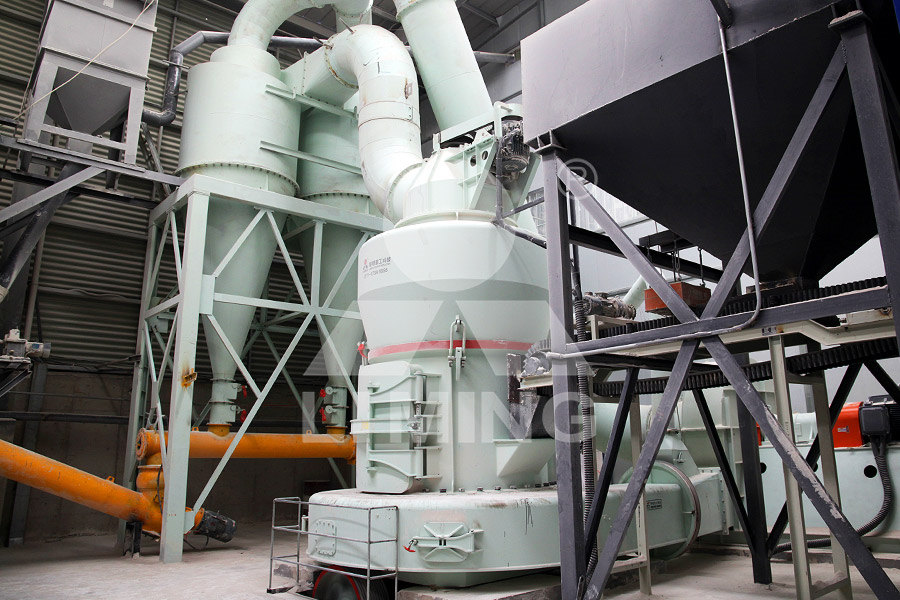
What Will Affect Working Efficiency of Ball Mill Equipment?
2023年10月11日 Therefore, reducing the feed particle size can be one of the measures to improve the working efficiency of the ball mill and reduce the grinding cost 03 Influence of ball mill equipment speed and steel ball filling rate Filling rate and ball mill speed are two important factors that affect the working efficiency of the ball mill2013年7月15日 Minerals processing engineers and grinding experts agree that classification efficiency and circulating load both have a major effect on the efficiency of closed circuit ball mills(PDF) Energy Efficient Ball Mill Circuit – Equipment Sizing Ball mills are very effective for grinding smooth, aqueous, or oily dispersions by wet grinding since it gives particles of 10 microns or less Construction of Ball Mill: The basic parts of the ball mill are a shell, balls, and motor Fig2 A ball mill is also known as a pebble mill or tumbling millBall Mill Principle, Construction, Working, and More Soln 2024年8月15日 By using mechanical energy, 1 modern highenergy ball mills have revolutionized the domain of mechanochemistry, paving the way for academia and the fine chemical industry to unseen efficiencies, improved sustainability, and novel reaction paradigms 25 While studying the solidstate chemistry within the ball mill remains a challenging task Navigating Ball Mill Specifications for TheorytoPractice
.jpg)
How to Improve Cement Ball Mill Performance
The closedcircuit grinding system formed by a ball mill and a separator is a type of widely used cement milling system in cement plants and grinding stations There are many factors that may affect the ball mill’s working efficiency and product quality during operationIn cement industry, clinker grinding in steel tumbling mills has a very low energy efficiency The use of a small quantity of products called grinding aids can improve the energy efficiency of Principle of the planetary ball mill Download Scientific Diagram