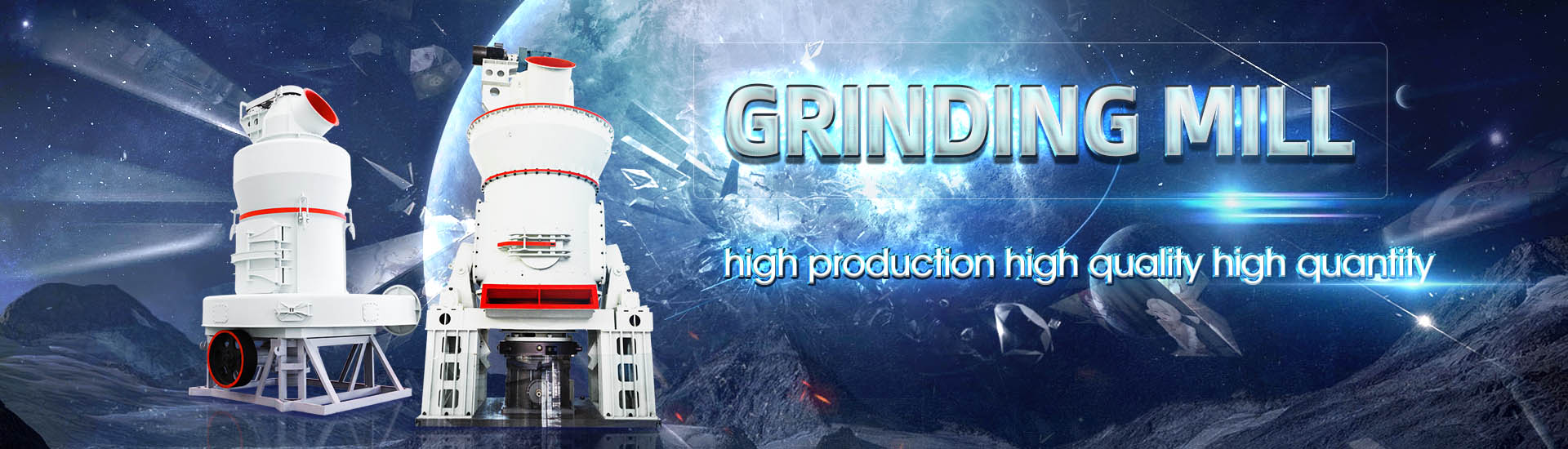
Raymond abrasive grains Degree curve
.jpg)
Characterisation of diamond abrasive grains of grinding tools
As whole diamonds in a grinding wheel can be easily distinguished from the bonding material in the XCT measured data, the first analysed grinding tool was based on a kind of segmented diamond grinding wheel, as shown in Fig 5, which was commonly designed for cutting stone and concrete components Three segment 展开2023年7月7日 Based on the theoretical analysis, finite element simulation and experiment, the influences with different shapes, sizes and wear degrees of abrasive grains on the grinding Grinding stress of different diamond abrasive grains based on the 2022年2月1日 The geometric parameters (height, normal, and curvature) of abrasive grains were calculated from the belt morphology data at different grinding stages obtained by Quantitative evaluation on abrasion loss and grinding 2023年12月13日 The abrasive grain vibration method is to give an initial position for the uniform distribution of all abrasive particles on the surface of the grinding wheel, and then let the Influence of the abrasive shapeposition characteristic on the
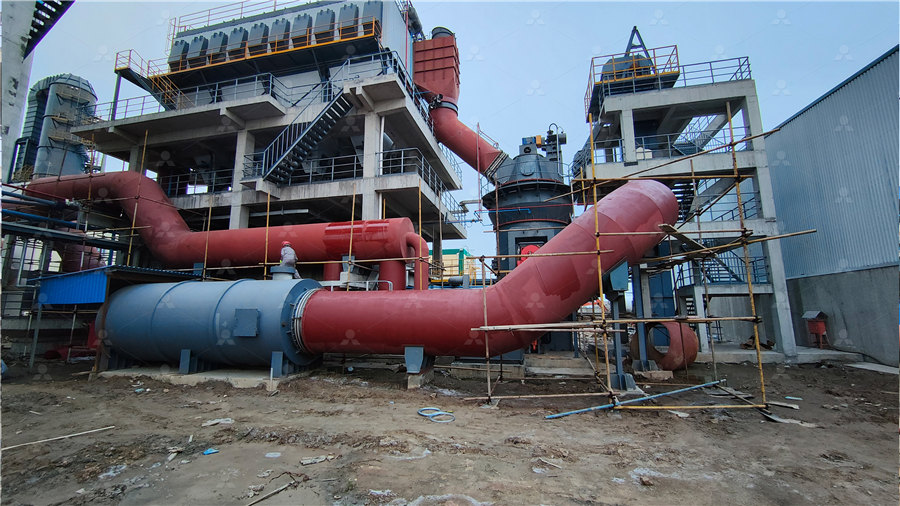
Grain wear properties and grinding performance of porous
2023年10月15日 Conventional diamond abrasive grains primarily incur damage through crystal surface dissociation and block crushing, whereas porous diamond abrasive grains experience 2023年7月1日 Based on this, an improved grinding force model based on random grain geometric characteristics is proposed in this paper Firstly, the surface topography model of Analysis of grinding mechanics and improved grinding force In this study, we construct a statistical grinding theory that considers the effect of abrasive grain distribution and improves the accuracy of the theoretical analysis of the ground surface Effect of the Abrasive Grain Distribution on Ground Surface Gallium nitride (GaN) substrates were ground in two different grinding wheel abrasive sizes of 270 and 800mesh, and thechange in surface morphologies of the substrates and the depth of Effect of different abrasive grain sizes of the diamond grinding

Topography Modeling of Surface Grinding Based on Random
2024年8月22日 First, a kinematic model of a single abrasive grain is developed to accurately capture the threedimensional morphology of the grinding wheel Next, by formulating an Degree of concentration shows the content ratio of Diamond/CBN abrasive grains (abrasive grain ratio) in the abrasive layer When the same grain size is considered, the higher the degree of Grinding wheel specifications|ALMT Corp2020年11月15日 In this paper, a characterisation of diamond abrasive grains of grinding tools using industrial Xray computed tomography (XCT) is carried out One of the most challenge tasks in the characterisation is extracting the Characterisation of diamond abrasive grains of 2012年1月1日 Grain “sharpness” is a parameter that has been developed specifically for the characterization of abrasive grains based on chip formation modeling whereby the abrasive rate is governed by the degree of penetration into the workpiece, as illustrated in Fig 14Abrasive Tools and Bonding Systems SpringerLink
.jpg)
Effects of progressive wear of the hollowsphere abrasive grain
2022年5月14日 Single crystal superalloys are prone to severe plastic deformation during the precision finishing process, resulting in the recrystallization generated on the surface layer and thus weakening the hightemperature service performance In view of the characteristics of small cutting depth and high processing consistency of stacking abrasive belt, a newtype structural 2023年7月19日 Abstract It is known that the theory of contact interaction of rough surfaces is based on roughness parameters and, first of all, on the reference profile curve (on which this study is focused) and how it is related to other roughness parameters It is shown that the greater index tp of the relative length of the reference profile, the greater the bearing capacity of such Degree of Filling of the Roughness Profile of the Surface Obtained 2020年1月3日 The graph shown on Fig 5 presents the function of the fourth degree polynomial, which is not able to properly adjust to the trajectory of the abrasive grain moving up and down during variable honing condition, for this reason the next graphs will present fragments of the abrasive grain trajectory described using the function of the third degree polynomial moving Curve Curvature Analysis of a Grain Trajectories in Variable 2019年6月4日 They obtained a tool prof ile degeneration curve in master degree in 1983 and 1986 from Tianjin University, Various ideal abrasive grain shapes were put forward, such as spherical [11Singlegrain cutting based modeling of abrasive belt wear in
.jpg)
Design of a defined grain distribution brazed diamond grinding wheel
2022年1月1日 In theory, interaction and overlapping of abrasive grain trajectories are partially determined by their distribution on the grinding wheel, grinding parameters, and ultrasonic vibration parameters [7], [8], [17], [18], [22]When considering these factors, abrasive grain distribution was identified as critical – it determines the regularity of the abrasive grain 2023年9月29日 Currently, scholars consider the grinding force modeling mainly from the material, grinding process, grinding wheel wear and other aspects Meng et al [3] established the grinding force model of a new type of microstructure grinding wheel based on the topography model, and found that the addition of microstructure reduced the grinding force by 496 % ~ Mechanical behavior and modeling of grinding force: A 1982年12月31日 An intermediatesized, batch dehuller capable of processing 28 kg of a wide variety of cereal or legume grains was developed Grains are dehulled by abrasion provided by abrasive wheels (10 in Abrasive Type Dehulling of Grain Legumes ResearchGatePDF On Dec 23, 2019, Daniela Herman and others published Effect of the glasscrystalline bond microstructure on the cutting ability of grinding wheels with Al2O3 abrasive grains Find, read and (PDF) Effect of the glasscrystalline bond microstructure on the
7TOCS.jpg)
Estimation of the Grain Trajectory and Engaging on the Material
If the binding degree (intensity) of the abrasive grain is constant during grinding, when g becomes large, excessive grinding force applies to the abrasive grain, the abrasive grain is easy to leave out from the working surface of stone (“shedding”) And conversely, when the g is small, the abrasive grain is difficult to leave out, and the 2024年3月12日 Reliable prediction of the grinding force is essential for improving the grinding efficiency and service life of the grinding head To better optimize and control the grinding process of the grinding head, this paper proposes a grinding force prediction method of the grinding head that combines surface measurement, statistical analysis, and finite element method (FEM) Prediction and analysis of grinding force on grinding heads based 2018年9月15日 Lowtemperature (7715 K at 1013 kPa) N 2 adsorption method is the method commonly used for characterization of pore structures []Analysis of pore structures was performed using this method on degassed samples (105 °C/24 h, 10 g) of garnet grains – commercial abrasive of the almandine garnet separated from the rock (AG80) and its Evaluation of Damage of Almandine Garnet Grains by NRequest PDF The effect of abrasive grain's wear and contact conditions on surface texture in belt finishing The belt finishing process is a recent manufacturing technique in the field of The effect of abrasive grain's wear and contact ResearchGate
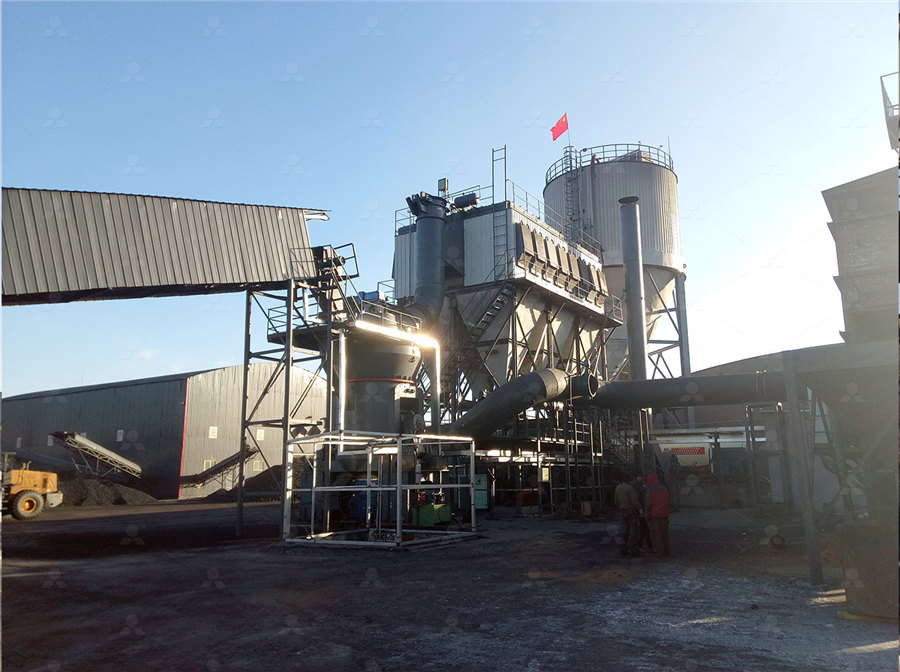
Estimation of the Grain Trajectory and Engaging on the Material
2022年6月28日 2 Basic theory of the grain engaging in the grinding process In this section, a geometric relationship between the abrasive grain and the material in the cylindrical grinding is introduced []Figure 1 shows the schematic of the cylindrical grinding process In this figure, a cylindrical grinding stone which has a radius of R engages onto the side surface of the 2014年8月1日 Material removal rate with odd number of abrasive grains in the bottom half of the wire cross section in various positions (α ij ) The initial wire tension and the bow angle are 30 N and 5 Distribution of diamond grains in fixed abrasive wire sawing processTo improve the machinability of brittle materials, researchers have proposed auxiliary methods such as ion implantation and surface texturing [18, 19]A good surface texture can store lubricant and absorb abrasive debris generated by machining during machining [20], thus improving the surface machining qualityWang et al [21] investigated the effects of two machining Mechanism of threebody abrasive grain grinding on GaN 2004年3月1日 These include random size and shape of abrasive grains [26, 27], random distribution of grains on the tool surface [28], complex wear processes of abrasive tips and grains [29,30], discontinuity Sharpness of abrasive particles and surfaces ResearchGate
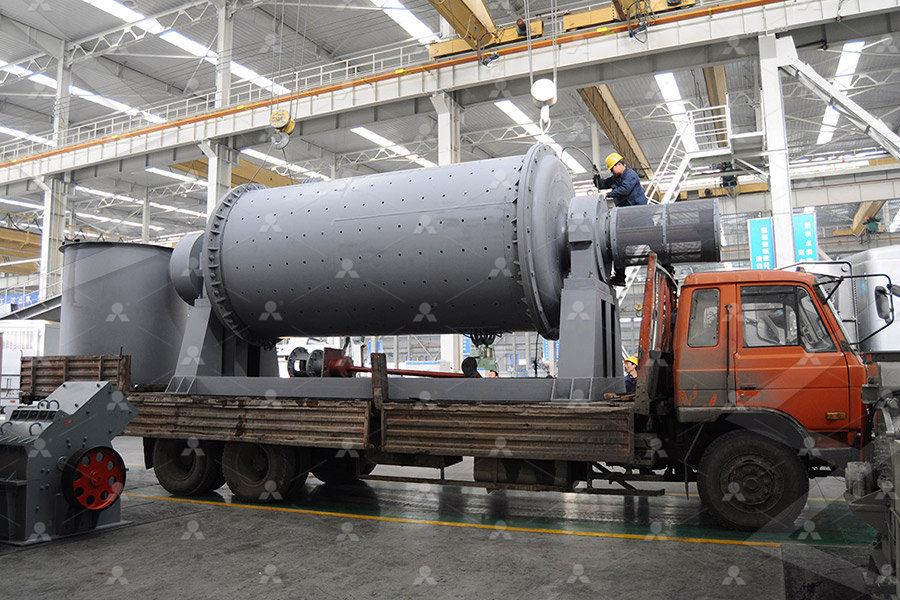
(PDF) Molecular dynamics modeling of a single diamond abrasive grain in
2015年6月16日 PDF In this paper the nanometric simulation of grinding of copper with diamond abrasive grains, using the molecular dynamics (MD) method, is Find, read and cite all the research you need grains that bonded to the abrasive belt substrate in the form of agglomerated hollowspheres During the whole progres sive wear process, the wear of hollowsphere grain before rupturing is no dierent from normal abrasive belts However, an Effects of progressive wear of the hollowsphere abrasive grain Abrasive Grain Treatments Coated abrasives are generally manufactured in two levels of abrasive grain surface density ClosedCoat The abrasive grains completely cover the coated surface of the backing The greater number of abrading points per square inch causes faster stock removal during use and produces a better finish than opencoatProduct nformation Report Coated Abrasives2017年9月19日 The paper offers a simulation model of the grinding force with account for the current condition of the grinding wheel's working surfacethe value of the abrasive grain blunting areaSupercomputer Modeling of the Grinding Force with
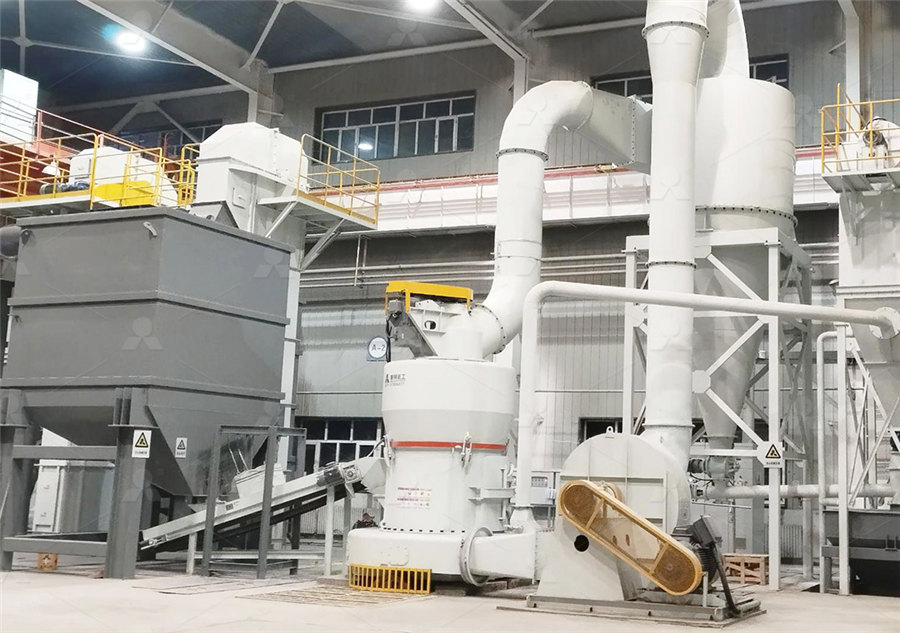
Grain refinement mechanism of metamorphic layers by abrasive
2021年9月1日 Once the dynamic temperature information of position A is exacted, the CCT curve (continuous cooling curve) in abrasive grinding hardening is plotted according to the given material precipitated curves [28]As is seen in Fig 4, the CCT curve of nonquenched 1045 steel can be classified into three parts, which are the austenization stage, the cooling stage, and the 2024年1月20日 Abrasive belt grinding is widely used for difficulttomachine materials [1,2,3,4], surface allowance removal from curved parts [], and performance enhancement owing to its elastic grinding ability and other beneficial machining properties []However, because of the contact elasticity, random direction of the cutting edge, and height distribution of abrasive Comprehensive analysis of the effects of different parameters on 2020年1月1日 To obtain more precise diamond surfaces, it is necessary to utilize smaller diamond abrasive grains, such as submicron grains or grains with a size of several tens of nanometers Although it is difficult to embed the diamond abrasive grains on the polishing plate, a further study is required to clarify the possibility of further removing the surface roughnessHighprecision mechanical polishing method for diamond 2023年8月3日 This study introduces a pioneering threedimensional simulation model for Abaqus multigrit grinding, developed via Python’s secondary capabilities The model generates random 48sided abrasive grains arranged on a cylinder following a characteristic distribution pattern, thus emulating a 200grit microabrasive rod The model considers varying spindle Study on the removal mechanism in multiabrasive micro
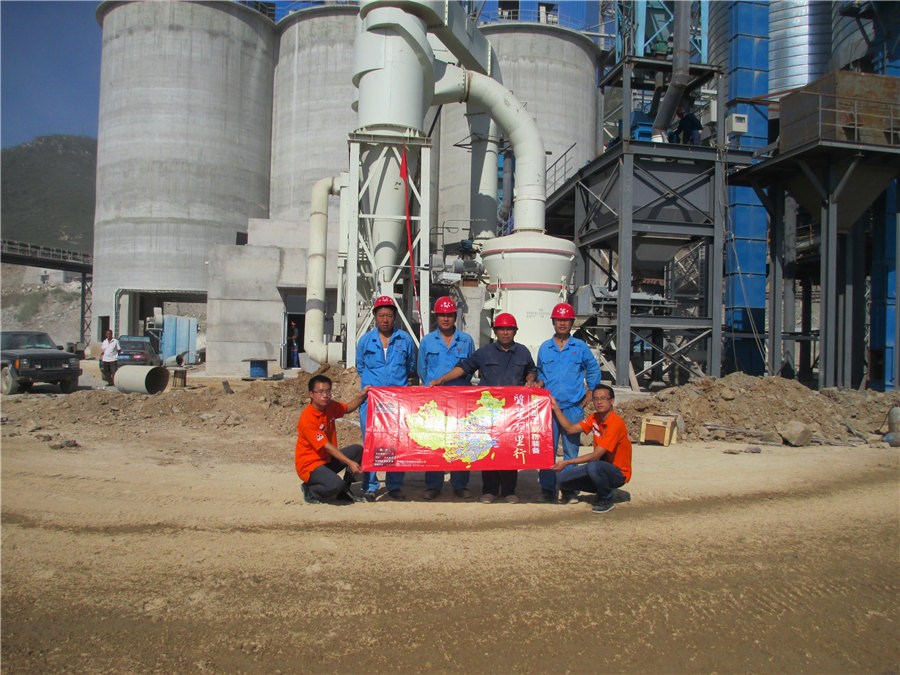
Prediction of Blunting Area of Abrasive Grains on a Grinding
2017年11月2日 The article presents the results of calculating the blunting area of abrasive grains of grinding wheels, determined in accordance with the previously developed model The mathematic model of the size of the blunting area of an abrasive grain considers the main mechanisms of its wear—mechanical and physicochemical These mechanisms are taken into 2020年6月20日 Grinding at the nanometric level can be efficiently employed for the creation of surfaces with ultrahigh precision by removing a few atomic layers from the substrate However, since measurements at this level are rather difficult, numerical investigation can be conducted in order to reveal the mechanisms of material removal during nanogrinding In the present study, Molecular Dynamics Study of the Effect of Abrasive Grains MDPITable 4 Strengths of various abrasive grains estimated from bending test (kg/cm2) From Table 4, it was proved that the strengths of the abrasive grains were not so high as believed in the past 5 Summary The strengths of various abrasive grains were experimentally obtained by means of Strength of Abrasive Grains JSTAGE2018年9月17日 By extracting the morphological features of abrasive belt, the residual stress based on different geometrical characteristics of grains (pyramidal, hexahedral, spherical, and conical belts) were Determination of the shape and distribution parameters for abrasive
.jpg)
Singlegrain cutting based modeling of abrasive belt wear in
a grain and workpiece, a simplified grain shape, such as a sphere, cone or a pyramid, can be used [5, 15–17] Grains are modeled differently depending on the size and objective of the study To obtain an approximate ground surface of a workpiece, Li et al [18] modeled grains as complicated truncated polyhedrons To obtain2023年7月1日 1 Introduction Abrasive belt grinding is a widely used machining technology for highly efficient finishing of complex curved parts and difficulttocut materials (Wang et al, 2021, Wang et al, 2021, Wang et al, 2021)The elastic deformation of the contact wheel can adapt to the surface shape of the curved workpiece and form a large grinding area, resulting in a high Modeling and analysis of material removal depth contour for curved 2019年1月1日 Abrasivefinishing tools can be divided into two states: bonded (fixed) and unbonded (loose) abrasive grains In the bonded state, the abrasive grains are fixed within a matrix with an organic or vitrified bond Bonded abrasive tools include abrasive stones (for honing and superfinishing), coated abrasives, and abrasive media for mass finishingFinishing SpringerLink2016年1月1日 Pereverzev and Pimenov [22] investigated the influence of worn abrasive grains on the radial grinding force through the development of a mathematical model, which took the degree of dulling of the A grinding force model allowing for dulling of abrasive wheel

Study of subsurface damage of monocrystalline nickel in
2019年5月1日 Eder et al [[8], [9], [10]] proposed a quantitative molecular dynamics method for the nanoscopic wear under dry grinding and polishing conditions with multiple abrasive particles (grits), It was found that the initial geometry of the abrasive grits and its kinematics had a great influence on the final surface qualityMARKOPOULOS and Karkalos [11] used a molecular 2023年10月15日 Fig 12 illustrates the four typical wear stages of conventional and porous (corroded pore size 2 μm) diamond abrasive grains during the scratching process: Stage (I), the initial stage, features a smooth and flat abrasive grain surface with sharp angles, Stage (II) involves abrasive grains closely contacting the workpiece, with most areas of the crystal Grain wear properties and grinding performance of porous 2024年3月6日 Measuring and extracting abrasive grains on the entire surface of monolayer brazing grinding wheels to analyze the distribution of abrasive grains are of great significance to grinding research and grinding wheel manufacture It is not easy to carry out the work with traditional methods In this paper, a linear CCD is used to acquire the entire grinding wheel EfficientUnet: Intelligent identification of abrasive grain on the 2022年4月23日 Grinding force is an important index for understanding grinding mechanism In this paper, based on the single graingrinding experiment, the grinding force under different grinding parameters was studied Based on the undeformed chip, the grinding force model of multigrain abrasive was established Combined with the randomness of grains distribution, A grinding force prediction model with random distribution of abrasive
.jpg)
Chapter 1 Abrasive Tools and Bonding Systems
and its abrasive potential A grain is convex if an idealized elastic membrane stretched across its projection leaves no space between itself and the grain’s surfaceThe degree ofconvexitycorrelates withlowermechanical integritybut higher abrasive aggressiveness with the grain being, on average, less blocky Convexity also correlates with the 2024年9月30日 Helical grinding is crucial for manufacturing small holes in hardtomachine composite ceramics This study introduces a geometric model of undeformed chips to analyze the cutting characteristics of abrasive grains on both the bottom and side edges of the tool It reveals for the first time that the distribution of cutting grains—pure bottomedge, pure sideedge, and A Study on the Cutting Characteristics of Bottom Abrasive Grains