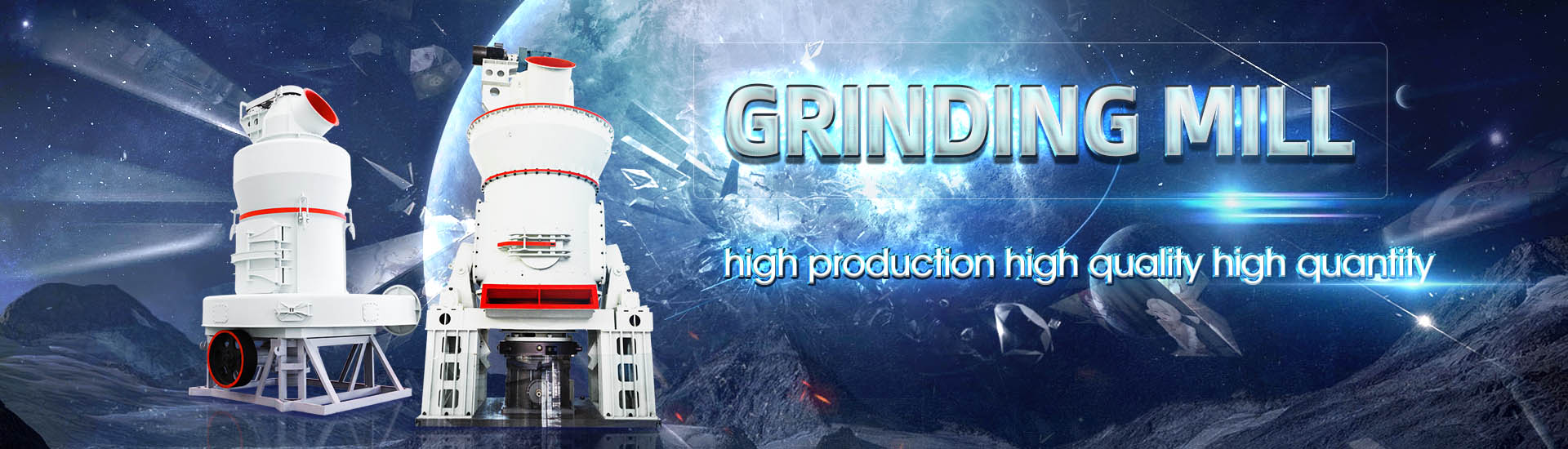
Rotary kiln cement powder making process
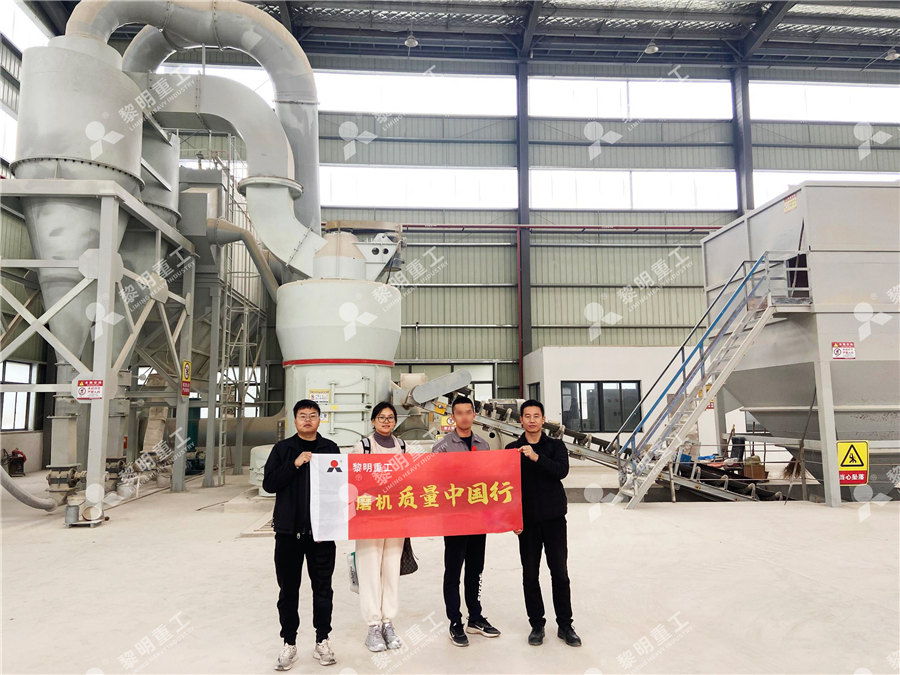
Rotary kiln process: An overview of physical mechanisms, models
The heat and mass transfer modeling process in rotary kilns is summarized The commonly used correlations involving rotary kilns are categorized by application The solidwall heat exchange The burning process is carried out in the rotary kiln while the raw materials are rotated at 12rpm at its longitudinal axis The rotary kiln is made up of steel tubes having the diameter of 2530 meter and the length differs from 90120meter Manufacture of Cement Materials and Manufacturing 2024年11月23日 The shaft kiln in a modernized form is still used in some countries, but the dominant means of burning is the rotary kiln These kilns—up to 200 metres (660 feet) long and six metres in diameter in wet process plants Cement Extraction, Processing, ManufacturingCement kilns are an essential component of the cement manufacturing process, playing a crucial role in producing the clinker that is ground into cement These massive, rotating cylindrical vessels are designed to withstand extreme Comprehensive Guide to Cement Kilns: Processes,
.jpg)
Rotary kiln process: An overview of physical mechanisms, models
2022年11月1日 Beginning with the research conducted on directly heated rotary kilns for cement applications, this review extends the scope of application to other fields, including waste, 1971年8月17日 In the wet process and long dry process, all of the pyroprocessing activity occurs in the rotary kiln Depending on the process type, kilns have lengthtodiameter ratios in the 116 Portland Cement Manufacturing US EPA2019年4月1日 In the present study, the optimization procedure for the rotary kiln by CFD modelling is done in parallel with the optimization of the full cement plant Even though not Study of a full scale oxyfuel cement rotary kiln ScienceDirectBottom right: rotary kiln with tertiary air duct above The Ushaped duct leading from the kiln inlet is an "alkali bleed" A typical process of manufacture consists of three stages: grinding the resulting clinker to make cement (see Cement mill)Cement kiln Wikipedia
.jpg)
The Cement Manufacturing Process
2017年8月15日 The materials reach temperatures of 2500°F to well above 3000°F in the kiln Rotary kilns are divided into two groups, dryprocess and wetprocess, depending on how the raw materials are prepared In wetprocess kilns, raw materials are fed into the kiln as a slurry with a moisture content of 30 to 40 percent5 天之前 The manufacture of Portland cement is a complex process and done in the following steps: grinding the raw materials, mixing them in certain proportions depending upon their purity and composition, and burning them to sintering in Manufacturing of Portland Cement – Process and He heated a mixture of limestone and clay powder in his kitchen, and grind the mixture into powder creating cement, that hardens when mixed with water The burning process is carried out in the rotary kiln while the raw materials are Manufacture of Cement Materials and Manufacturing 2023年2月25日 The originality of this review is to explore the various works that have led to a better understanding of rotary kiln process modeling Advanced Powder Technology, Volume 31, Issue 2, 2020, pp 678694 Hybrid model of a cement rotary kiln using an improved attentionbased recurrent neural network ISA Transactions, Volume Rotary kiln process: An overview of physical mechanisms, models
.jpg)
Rotary kiln process: An overview of physical mechanisms, models
Rotary kiln process: An overview of physical mechanisms, models and applications BabyJean Robert Mungyeko Bisulandu, Florian Huchet To cite this version: BabyJean Robert Mungyeko Bisulandu, Florian Huchet Rotary kiln process: An overview of physical mechanisms, models and applications Applied Thermal Engineering, 2023, 221, ppGypsum powdermaking process According to the process requirements, the construction gypsum production line is usually divided into five parts, including crushing system, storage conveying system, grinding system, calcining system, and electric control system STEP1 crushing system The size and specifications of gypsum ores are different after mining, and Gypsum Powder Manufacturing Gypsum Powder Making Machine Cement shaft kiln: machinery shaft kiln and ordinary shaft kiln; cement rotary kiln: wet process rotary kiln and dry process rotary kiln; By cement meal preparation technology: wet process cement kiln: the cement raw material is grinded with water powder into raw slurry (3340% water) and then fed into the wet process rotary kiln and burn into cement Cement Kiln, Cement Plant Kiln, Kiln In Cement Plant Shaft Kiln Rotary kilns (sometimes called calciners or rotary furnaces) are used for thermal treatment processes such as calcination, sintering, pyrolysis and firing, as well as for oxidation and reductionThese treatments can be applied to powders, granulates, suspensions and green bodiesA rotary kiln consists of a cylindrical, rotating body mounted between stationary The Rotary Kiln Experts for Trials and Production IBUtec

How Is Cement Produced in Cement Plants Cement Making Process
The cyclone preheating system Phase IV: Calcination The calcination is the core phase of the cement making dry process The calcination of the preheated raw meal takes place in the rotary kiln of the cement plant The rotary kiln is a huge rotating furnace in which the raw meal is heated up to 1450 ⁰C and turned to clinkerConsider some of the basics of the calcination zone from the standpoint of the energy requirement in the process of making portland cement clinker The calcination reaction is an endothermic reaction Peray, K E, The Rotary Cement Kiln, 2nd Ed Everything you need to know about Kiln System Operations in Cement As the term indicates, in this process the kiln feed enters the kiln in dry powder form Dryprocess kiln dimensions are similar to wet kilns in that they are long and typically show a lengthtodiameter ratio of approxi mately 30:1 to 35:1Types of Rotary Kilns INFINITY FOR CEMENT 2024年9月10日 Steps of Cement Manufacturing The steps involved in cement manufacturing are as follows: Quarrying: Raw materials such as limestone and clay are extracted from quarries or mines; Crushing and Grinding: The Cement Manufacturing Process: Know Extraction,

Rotary Kiln SpringerLink
2024年1月1日 Divided into dryprocess and wetprocess kiln, the cement kiln is mainly used for calcining cement clinkers The metallurgical chemical kiln is primarily applied to oxidizing roasting or reduction of iron ore pellets in metallurgical industry, direct reduction of chromite and josephinite, roasting of alumina minerals and clay minerals, roasting volatilization, separation, 2020年9月26日 Cement Manufacturing Process: ement is a material which is used to bind other materials together Binding means it has an effect of gluing the substances The rotary kiln is divided in to three parts; the upper part, the central part and the lower part The processes ongoing in each of the parts are:Cement Manufacturing Process Chemical Engineering World2020年8月4日 The cement rotary kiln has many classifications, in general, there are dry process and wet process according to the raw meal manufacturing process, so the related rotary kiln needed in the cement production can be divided into dry process rotary kiln and wet process rotary kiln Cement rotary kiln can also be classified by different heat Kiln For Cement Cement Kiln Rotary Kiln, Shaft Kiln AGICO CEMENTAlternative fuels like petcoke, rubber tyres, wood chips, etc have been introduced to economize cement making process PrecalcinerKiln Important Operational parameters with brief physical significance: Raw meal, Hot meal and Clinker Parameters: in a reactor like rotary kiln, therefore there will always be some unreacted lime Clinkerization Cement Plant Optimization
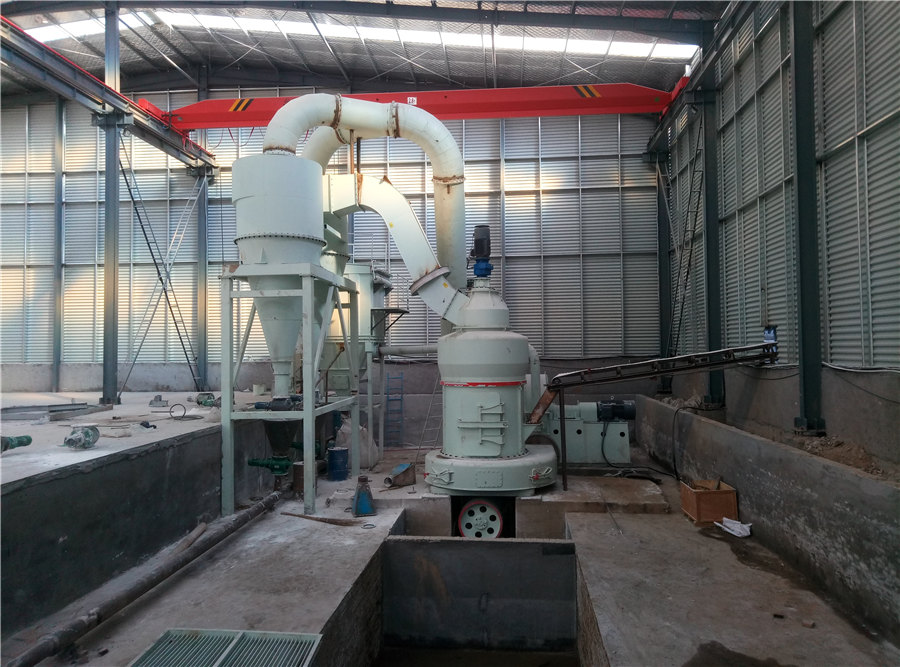
Cement Euipment Overview Cement Making Machines Cement
2019年9月27日 AGICO offers cement making machines including cement mill, rotary kiln, cement crusher, cyclone preheater, cement dryer, clinker cooler etc any need? Skip to content +86 Rotary kiln process: An overview of physical mechanisms, models and applications BabyJean Robert Mungyeko Bisulandu, Florian Huchet To cite this version: BabyJean Robert Mungyeko Bisulandu, Florian Huchet Rotary kiln process: An overview of physical mechanisms, models and applications Applied Thermal Engineering, 2023, 221, ppRotary kiln process: An overview of physical mechanisms, models With the arrival of rotary kilns in Britain in 1900, cement manufacturing processes became sharply defined according to the form in which the raw materials are fed to the kiln Raw materials were either ground with addition of water, to form a slurry containing typically 3045% water, or they were ground dry, to form a powder or "raw meal"Cement Kilns: Rotary kilnsWhat Is Cement Rotary Kiln Cement rotary kiln, also called cement kiln, is a pyroprocessing device used for calcining cement clinker in cement production linesIt is the main engine in the cement manufacturing process, commonly known as the “heart” of the cement plantIn the production process, an equipped kiln burner produces heat by burning fuel, and the heat is Cement Rotary Kiln Rotary Kiln Rotary Kiln Manufacturers
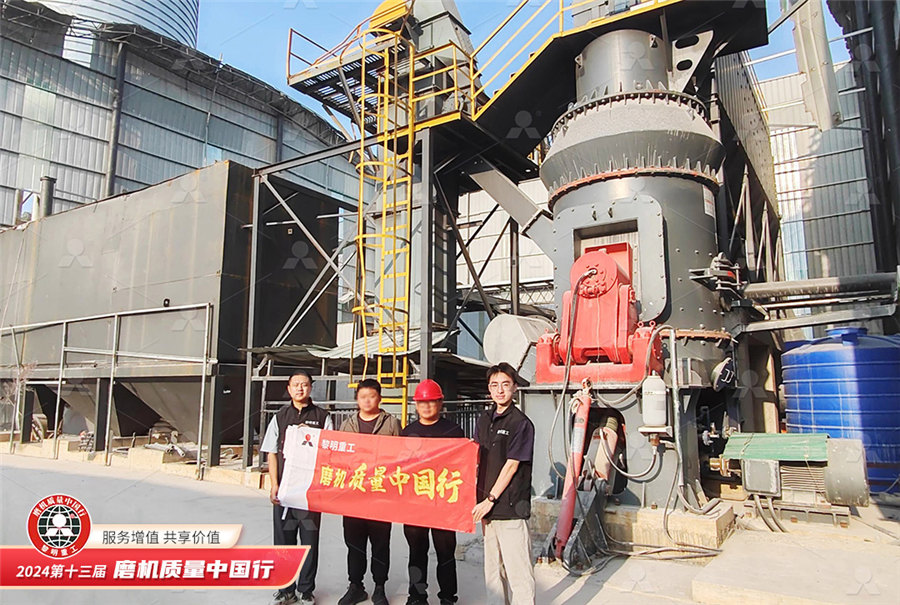
What is a Cement Kiln? How does it Work? – PanyamCements
To make cement, the raw materials are crushed and ground into a fine powder They are then fed into a rotary kiln and heated as they move through it Cement kilns are a key part of the cement making process and are often used in a variety of industrial processes beyond their uses in making cementKiln phase Since clinker is a complex mixture of ingredients, it requires a multistaged heat treatment, which is done in the kiln The main part of the manufacturing process of clinker takes place in the kiln The stages in the kiln phase are as follows:Cement Clinker Manufacturing Process with ReactionsCement manufacturing equipment needs to withstand the heat and the abrasive material from which cement is made Making cement involves combining raw materials including limestone, clay, and shale, which are milled into a very fine Cement Making Process: Equipment Manufacturing1971年8月17日 116 Portland Cement Manufacturing 1161 Process Description17 Portland cement is a fine powder, gray or white in color, that consists of a mixture of hydraulic cement materials comprising primarily calcium silicates, aluminates and aluminoferrites More than 30 raw materials are known to be used in the manufacture of portland cement, and these116 Portland Cement Manufacturing US EPA
.jpg)
Everything you need to know about Kiln Burning Systems
The first rotary kiln was introduced to the cement industry by Frederik Ransome (1885) when he took out a patent in England titled “Improvements in Manufacture of Cement” The first of these rotary kilns were up to 20 m in diameter and 25 m long, with an “enormous” production of 2019年11月6日 According to the raw material production process, the rotary kiln can be divided into the dryprocess rotary kiln and wetprocess rotary kiln Wetprocess rotary kiln The wet process refers that make raw materials into cement slurry contain 32%40% water The finished cement slurry is diffluent, so the raw materials have a good mixture, the Why Choose Rotary Kiln In Cement Manufacturing Plant?Picture: ©NERC: British Geological Survey Cat No P Front end of Ribblesdale Kiln 2 (constructed 1937): shell constructed mainly from staggered semicircular sections, with all joints riveted Picture: ©Rugby Archive: Cat No RC368 Back end of Southam Kiln 7 (constructed 1961): shell entirely welded The shell still consists of staggered halfcylindrical sectionsCement Kilns: Design features of rotary kilnsWith this crude method, Joseph Aspdin of Leeds laid the foundation for an industry that annually processes literally mountains of limestone, clay, cement rock, and other materials into a powder so fine, it will pass through a sieve Portland cement is the basic ingredient of concreteHow Cement is Made Portland Cement Association
.jpg)
Rotary Kiln, Cement Rotary Kiln, Lime Rotary Kiln, Cement
Brief Introduction to Wet Rotary Kiln Process The kiln body of wet rotary kiln is usually relatively long (the aspect ratio is 3040) In order to increase the heat transfer area of the kiln, the chains are often hung at the kiln tail to accelerate water evaporation2023年3月3日 Girth gear and pinion are two of the most crucial components in cement making machinery such as rotary kiln and cement ball mill They play a pivotal role in ensuring the smooth operation of the machinery and directly impact the quality and efficiency of Girth Gear and Pinion in Cement Industry Rotary Kiln Cement 2024年1月17日 Finally, the cement clinker cooler cools the hightemperature clinker discharged from the rotary kiln to a temperature that the downstream transportation, storage and cement machinery can withstand At the same What Do You Know About Wet Process Of Cement The blackash cylinder was a batch process, otherwise similar It is interesting to note that the Navarros, who first successfully used a continuous rotary kiln for portland cement, had in 1886 operated a batchprocess rotary furnace for burning “natural” cement It was 24’ × 12’, “similar to a large peanut roaster”Cement Kilns: Early rotary kilns
.jpg)
Slag Cement Production Line Blast Furnace Slag
Slag Cement Manufacturing Process Slag cement is also called blast furnace cement, pbfc cement and slag powder will be sent into the cement plant for making slag cement, and the raw material is converted into clinker at Although having vastly intensified heat exchange in the lowtemperature zones, no preheater can address another shortcoming of the rotary kiln process The kiln operator is rather limited in controlling the kiln temperature profile beyond the firing (sintering) zone As early as 1896, de Navarro patented and later built the rotary kiln with an Everything you need to know about Preheaters and Precalciners2023年1月16日 Dr SB Hegde, Professor, Jain University, Bangalore, talks about pyroprocessing and the role of preheater, rotary kiln and clinker cooler in the cement manufacturing process In the concluding part of the twopart series, we will learn more about the various factors aiding pyroprocessing False Air in Pyro ProcessingIndia is the second largest cement producer in []Pyroprocessing and Kiln Operation Indian Cement Review2019年12月26日 Rotary kiln process The rotary kiln carries out several functions simultaneously It is a device for conveying, mixing, heat transfer, and reaction These functions are needed to be in harmony The charge in the kiln moves both radially and axiallyRotary Kiln IspatGuru
.jpg)
Rotary Kiln Dryer Cement Plant
Advantages of rotary kiln dryer High temperature resistance, use hightemperature and hot air to dry materials fast; Strong expandability of AGICO dryer, the design of dryer fully consider the allowance of production, even if a little more production incensement, there is no need of equipment replacement; Reasonable design of structure, stable performance, high heat Bottom right: rotary kiln with tertiary air duct above The Ushaped duct leading from the kiln inlet is an "alkali bleed" A typical process of manufacture consists of three stages: grinding a mixture of limestone and clay or shale to make a fine "rawmix" (see Rawmill); heating the rawmix to sintering temperature (up to 1450 °C) in a cement kiln;Cement kiln WikiwandBefore you send inquiry Please provide us with project information as much as possible: For a complete project: the material availability, the required output capacity, the process technology, your budgetary and financing status, the estimated starting time, etc For singular machinery: the model, the capacity, your budgetary information, other requirements, etcRotary Kiln For Activated Carbon Production Cement Plant