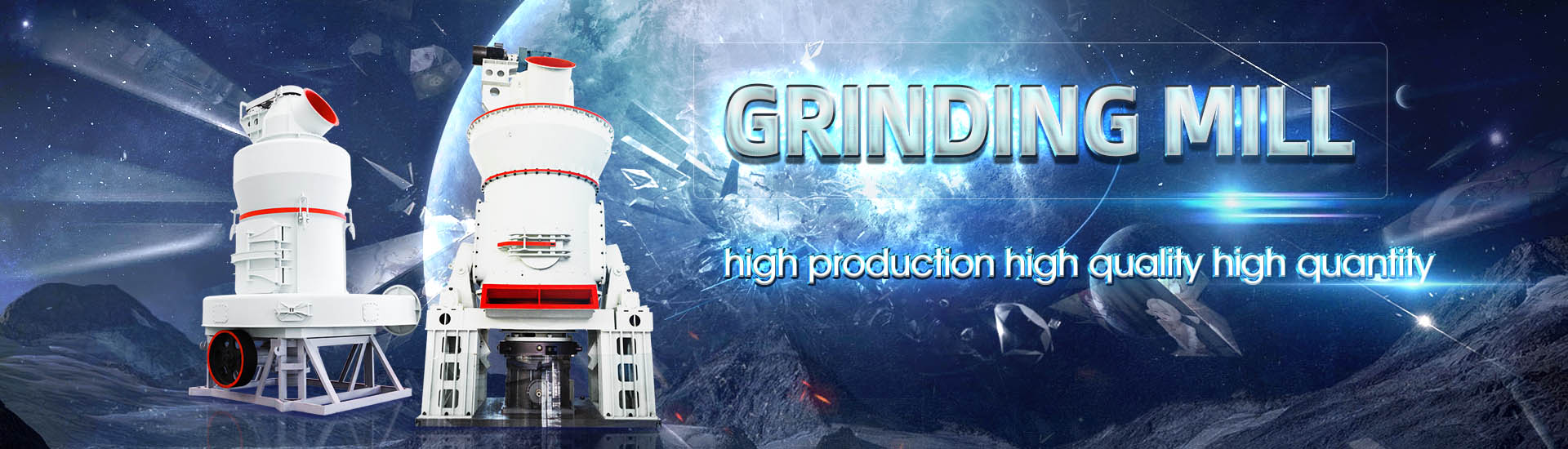
Ore mill vibration range
.jpg)
Monitoring the fill level of a ball mill using vibration sensing and
2019年10月19日 The fill level inside a ball mill is a crucial parameter which needs to be monitored regularly for optimal operation of the ball mill In this paper, a vibration monitoring 2019年7月1日 The most important conclusion is that the frequency range of the shell vibration of the laboratory wet mill can be divided into three parts, namely natural frequency band, main impactVibration characteristics of an operating ball mill2023年1月5日 In this paper, a foundation dynamic model of the ball mill is established based on the finite element software, and the influence of shock force, concrete grade and shock angle Study on shock vibration analysis and foundation reinforcement of In industrial practice, only three of these factors are usually controlled: the throughput, the density (more precisely the orewater ratio) and the rotational speed of mill The density and the Vibration measurements for copper ore milling and classification
.jpg)
Interpretation of mill vibration signal via wireless sensing
2011年2月1日 We interpret the vibration signature of a one meter diameter mill in response to changes in mill speed, rock/particle size, quantity of balls, and slurry viscosity A ±500 g tri 2021年9月1日 Specifically, the grinding behaviour of two different mill feeds (model quartz and iron ore) together with solid loadings (50, 57, and 67 wt% solids) were correlated against Predicting mill feed grind characteristics through acoustic 5 天之前 Das et al detected alterations in mill shell vibration signals with changes in fill volume, mill speed, and slurry viscosity in a laboratoryscale SAG mill They used variations in the Challenges and Opportunities in Vibrometry‑Based Online Nowadays, conducting grindability tests requiring only a few kilos of material on several samples, is a more typical approach to grinding mill design This paper summarises the requirements SAG Mill Testing Test Procedures to Characterize Ore Grindability
.jpg)
WholeBody Vibration in the Mining Industry: a Systematic Review
2022年12月21日 Exposure to wholebody vibration has been recognised as an occupational hazard in the mining industry, especially in the operations of earthmoving equipment 2015年1月1日 Parameters of Industrial Ball Mill Parameters Value Feed type Copper ore Feed rate 110130 MT/Hr Feed size 6 mm Discharge particle size 75 Micron Diameter of mill 116 Ft (35 m) Length of the mill 18 Ft (549 m) RPM 1747 Power rating of motor 10 MW Power required for grinding 700800 KW Temperature Ambient Ball diameter 65 mm Pulp density Vibration Feature Extraction and Analysis of Industrial Ball Mill Vibration milling is a type of mechanical milling that utilizes vibrations to generate an impact force that breaks down particles into smaller sizes This process is commonly used in various industries for material processing and synthesis Vibration milling is a milling process that uses the principles of mechanical vibration and impact to reduce the particle size of various materialsPrinciple of Vibration Milling and Its Industrial ApplicationsHowever, ore below the pay limit adds variation to the mill grade as increased mill throughput will be required to make up for the loss of gold, and that impacts on the recovery in the plant It is against these perspectives and findings of this Monitoring ore loss and dilution for minetomill
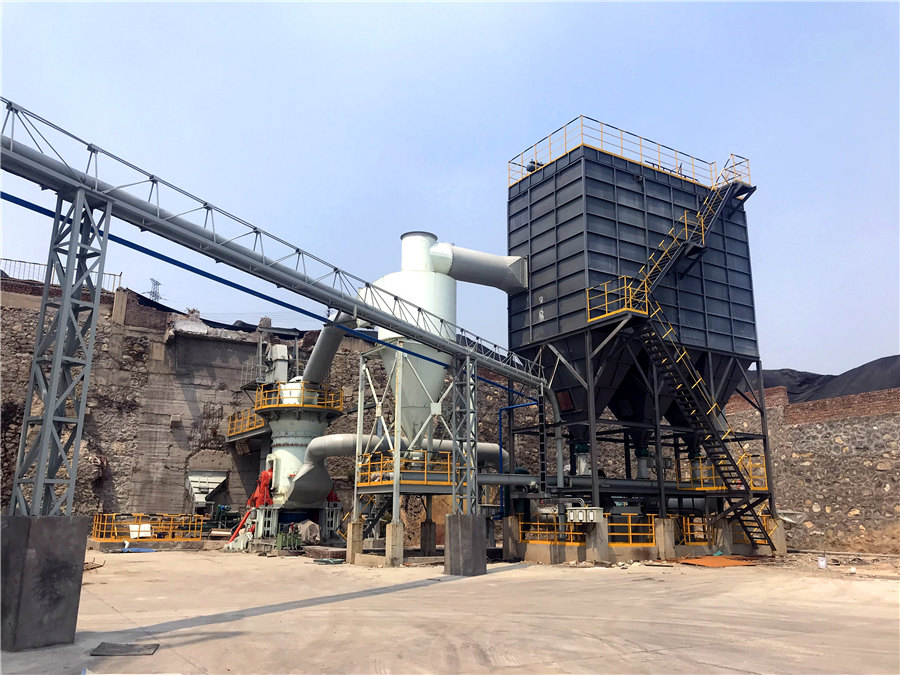
Experimental investigation of load behaviour of an industrial scale
2009年12月1日 Request PDF Experimental investigation of load behaviour of an industrial scale tumbling mill using noise and vibration signature techniques Mill load (ie the load level of coal powder Find your ore mill easily amongst the 42 products from the leading brands (Fritsch GmbH, Retsch, Eriez, ) on DirectIndustry, laboratory work The Planetary Micro Mill PULVERISETTE 7 premium line with 2 grinding stations is designed for a broad range of Compare this product Remove from comparison toolOre mill, Ore grinding mill All industrial manufacturersat the ball mill index range Table 2 compares the typical range of size reduction observed in grindability tests to those of the most common industrial devices BWI ratios indicate competent ores with low ball mill hardness, while low ratios represent friable or coarsegrained ores Fine and ultrafine grinding, also moreSAG Mill Testing Test Procedures to Characterize Ore By incorporating advanced sensors that can capture a wide range of vibration signals the aim of this research is to improve the accuracy and sensitivity of device the mill was filled up to 30% of the mill volume with iron ore as feed material Here, keeping the overall filling at 30%, the ball load 250 SP Das et al / Minerals Interpretation of mill vibration signal via wireless sensing
.jpg)
Monitoring the fill level of a ball mill using vibration sensing and
2020年3月1日 In this paper, a vibration monitoringbased method is proposed and tested for estimating the fill level inside a laboratoryscale ball mill A vibration signal is captured from the base of a laboratoryscale ball mill by using a ± 5 g accelerometer2010年8月1日 Request PDF Experimental analysis of wet mill load based on vibration signals of laboratoryscale ball mill shell Realtime measurement of the mill load is the key to improve the production Experimental analysis of wet mill load based on vibration 2017年2月1日 This work focuses on the characterization of heat generation during dry fracture by direct impact of a tantalum ore Moreover, an attempt was made to quantify the heat energy loss to the Heat generation model in the ballmilling process of a tantalum ore2024年1月1日 Mill load measurement is the measurement of the instantaneously total loading capacity inside the mill during the ore grinding process The the harsh working environment inside the mill Therefore, the vibration, the mill power greatly The power variation range is small when the mill is under noload and Mill Load Measurement SpringerLink
.jpg)
Disc Mills: Important Tools for Efficient Sample
2024年3月28日 Torontech’s range of Disc Mills, including the Soil Mill DP50, Disc Mill DP100, and Vibratory Disc Mill VM3, provide reliable performance and versatility Our Disc Mills excels in grinding soil, building materials, ores, 2023年5月28日 Mill load measurement is the measurement of the instantaneously total loading capacity inside the mill during the ore grinding process The the harsh working environment inside the mill Therefore, the vibration, the mill power greatly The power variation range is small when the mill is under noload and Mill Load Measurement SpringerLink2020年5月25日 This mill, which was charged with 332 lb of balls (3 pct 1 in by 7/8 in, 60 pct 7/8 by ¾ in, 37 pct ¾ by 5/8 in), required 560 ± 005 kw for operation at a frequency of 1260 rpm and a vibration radius of 9/32 in The procedure used in the experimentation was to pass about 1000 lb of ore through the mill at 1200 lb per hrRetention Time in Continuous Vibratory Ball Milling2019年6月18日 Important advances have been made in the last 60 years or so in the modeling of ball mills using mathematical formulas and models One approach that has gained popularity is the population balance model, in particular, when coupled to the specific breakage rate function The paper demonstrates the application of this methodology to optimize solids concentration in Optimization of Solids Concentration in Iron Ore Ball Milling
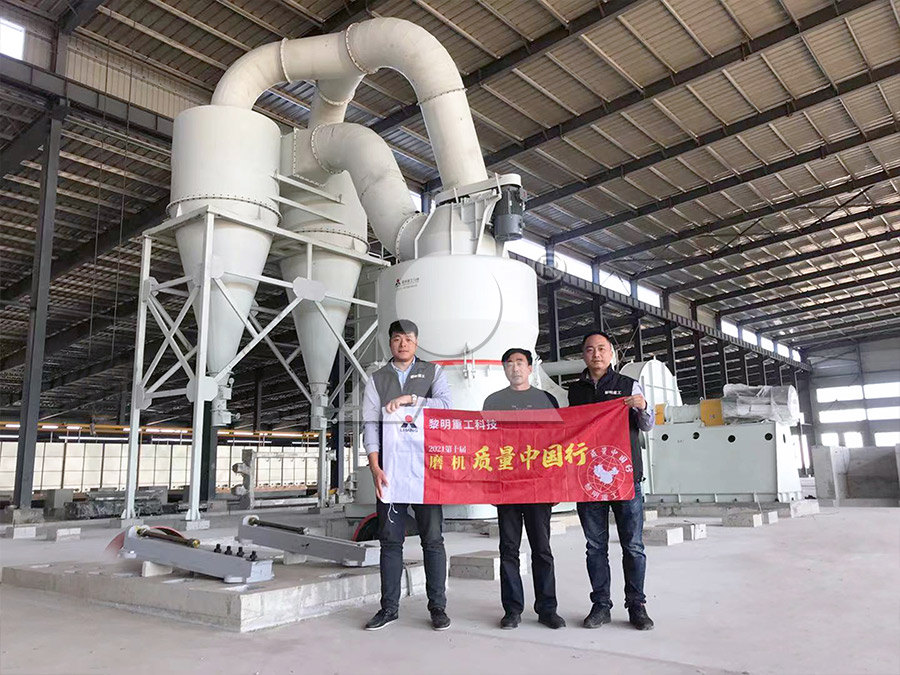
(PDF) Effect of Slurry Density on Load Dynamic and ResearchGate
2012年4月17日 Effect of Slurry Density on Load Dynamic and Milling Performances in an Iron Ore Ball Mill Online Estimation methods of free vibration A wide range of ball and pulp loads were tested SAG MILL MONITORING USING SURFACE VIBRATIONS Jonathan Campbell1, Steven Spencer1, David Sutherland1, Thressa Rowlands1, Keith Weller1, Paul Cleary2 and Adrian Hinde3 1CSIRO Minerals, PO Box 883 INTRODUCTION SAG MILL MONITORING USING SURFACE Ball mills are extensively used in the size reduction process of different ores and minerals The fill level inside a ball mill is a crucial parameter which needs to be monitored regularly for Experimental setup of a ball mill with control panel, accelerometer 2015年12月1日 Download Citation An experimental study on the ultrafine grinding of gypsum ore in a dry ball mill Gypsum is a crystalline form of hydrated calcium sulfate (CaSO42H20) generally used in An experimental study on the ultrafine grinding of gypsum ore in
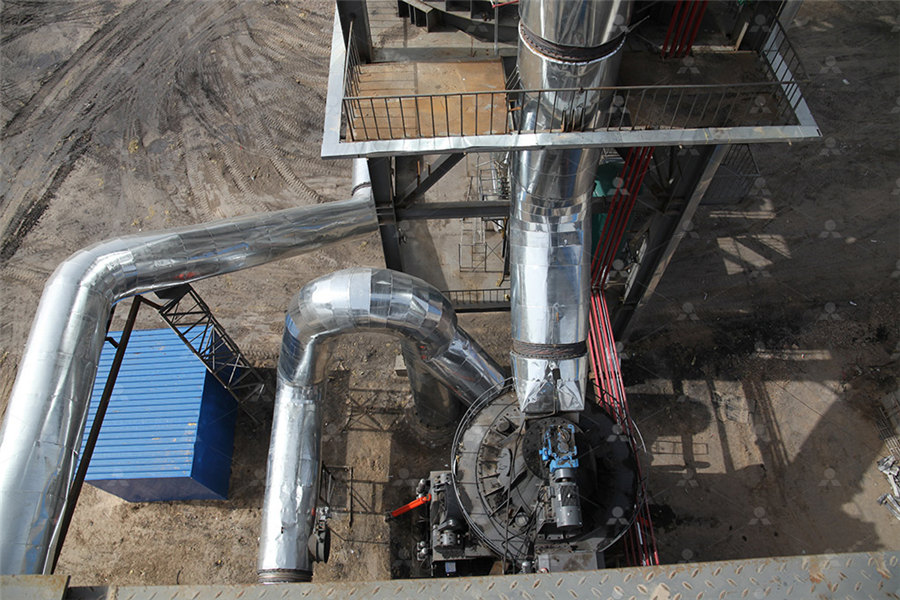
Combining Segmentation and Edge Detection for
2019年4月15日 This paper presents a machine vision method for detection and classification of copper ore grains We proposed a new method that combines both seeded regions growing segmentation and edge detection, where region DOVE Electromagnetic Vibrating Feeders are supplied in 11 models, capacity range of (5 – 1400 Tons/Hour), with various technical specifications, to be integrated in various feeding stages of the Hard Rock Processing plants, or Electromagnetic Vibrating Feeder Vibrating FeederPDF On Nov 5, 2012, G Brent and others published Ultrahigh intensity blasting for improved ore comminution Find, read and cite all the research you need on ResearchGateUltrahigh intensity blasting for improved ore China Vibration Mill wholesale Select 2024 high quality Vibration Mill products in best price from certified Chinese Oil Mill manufacturers, Coal Test Ore Grinding Vibration Grinding Sample Sealed Sample Making Mill US$ 13001500 / Piece 1 Piece (MOQ) Shicheng Oasis Mineral Equipment Manufacturing Co, LtdVibration Mill MadeinChina
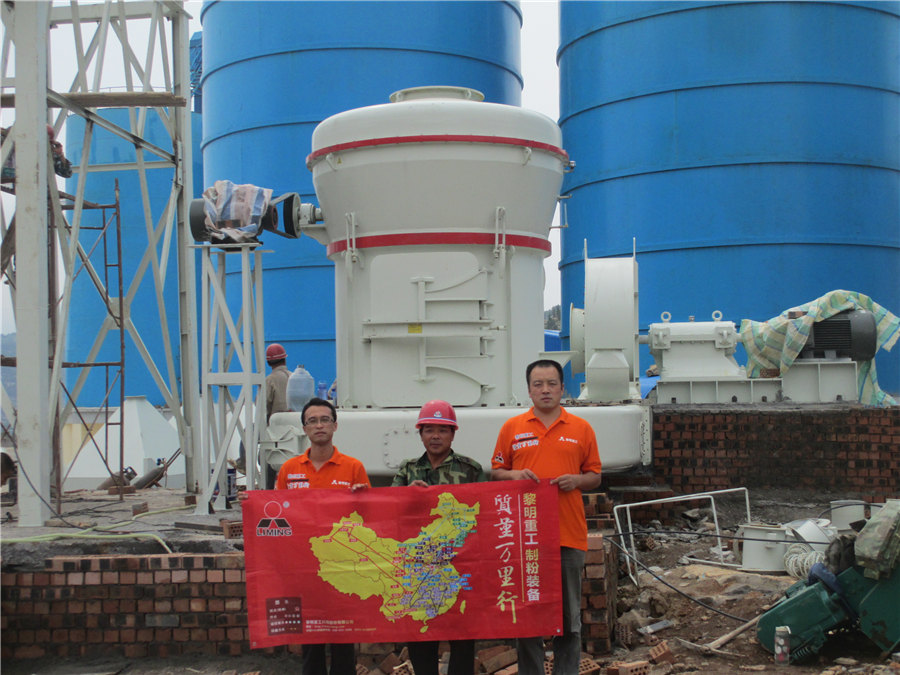
Wet Overflow Type Ball Mill and Applications
2024年1月12日 How Overflow Type Ball Mill Works Material Feed: The raw material is fed into the mill at one end and travels through the mill by rotation The feed enters the mill at a specific rate, ensuring a controlled grinding process; Grinding Process: As the mill rotates, the grinding media crushes and grinds the material into a fine powder The wet conditions enhance the 2019年2月25日 Due to the differences in beneficiation methods and mineral properties between cassiterite ore and polymetallic sulfide ore, there is an inherent contradiction between cassiterite overgrinding and sulfide ore undergrinding A method to optimize and characterize the grinding performance is presented in this paper In this method, the grinding characteristics are defined Grinding Optimization of CassiteritePolymetallic Sulfide OreMill Granulators are used in process plants for reducing raw coal or rock ore into fine power for burning or further processing They come in many designs but usually are rotary mills with rings Coal crushers of all types, such as ring granulators can often cause significant and unacceptable vibrations in their supporting structuresThe source of the vibration from a mill granulator is Vibration Monitoring System for Mill Granulator IRD MechDownload scientific diagram Ball mill (A) and rod mill (B) vibration signals presented on polar plots from publication: Increasing Energy Efficiency and Productivity of the Comminution Process Ball mill (A) and rod mill (B) vibration signals presented on polar

How to Improve Grinding Efficiency of Vertical Roller Mill
It gathers materials for grinding, conveying, powder selection, drying and separation of metal blocks and medium ore Under normal conditions, the roller mill can run Vibration of Verticle Roller Mill When vertical roller mill The speed of the separator is such that the fineness is controlled within the range of R 008≤14~16% Crushing2011年2月1日 Request PDF Understanding fine ore breakage in a laboratory scale ball mill using DEM DEM models of fine grinding in ball and stirred mills have to date almost entirely focused on the motion Understanding fine ore breakage in a laboratory scale ball mill using Download scientific diagram Location of the vibration sensors on the mill's shell (A) and time series of the ball mill vibration measurements (black, blue, and red representing separate full Location of the vibration sensors on the mill's shell (A) Download scientific diagram Total Vibration Power vs Mill Load for the MINTEK pilotscale mill from publication: The collection and analysis of single sensor surface vibration data to estimate Total Vibration Power vs Mill Load for the MINTEK
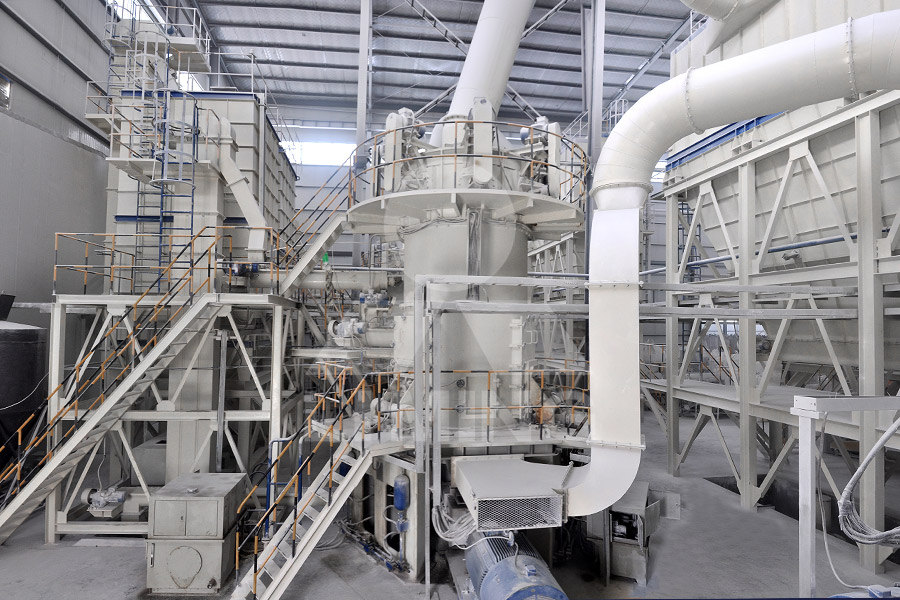
(PDF) Sensor‐Based Ore Sorting Technology in
2019年8月29日 Sensor‐Based Ore Sorting Technology in offers applicable size range It is applicable successful this route is for optimi zing the mill power draw and thro ughput of a gold ore millBall mills are extensively used in the size reduction process of different ores and minerals The fill level inside a ball mill is a crucial parameter which needs to be monitored regularly for Proposed method to monitor the fill level of a ball mill2019年4月16日 Conference: Applying a Successful Technology from the Cement Industry: Advantages of Grinding Ore in a VerticalRollerMill; At: Antalya, Türkey(PDF) LEARNING FROM OTHER INDUSTRIES; WHY THE VRMIn the mill, the mixture of medium, ore, and water, known as the mill charge, is intimately mixed, the medium comminuting the particles by any of the above methods Apart from laboratory testing, grinding in mineral processing is a continuous process, material being fed at a controlled rate into one end of the mill and discharging at the other end after a suitable dwell (residence) timeGrinding Mill an overview ScienceDirect Topics
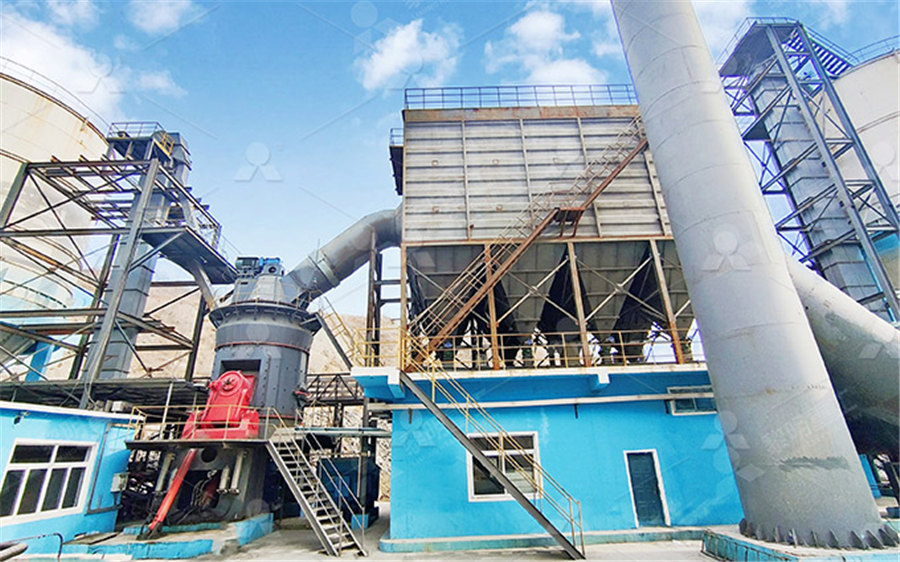
Ore, Rock Aggregate Screening (Complete Guide)
2016年6月20日 911 Metallurgist is a trusted resource for practical insights, solutions, and support in mineral processing engineering, helping industry professionals succeed with proven expertise Ore, Rock Aggregate Screening (Complete Guide)2024年10月8日 Model adaptability: As grinding conditions change over time (eg, different ore types), the model may need frequent retraining or finetuning 55 Operational constraints Varying operational conditions: Changes in mill speed, load, or grinding media can alter vibration patterns, potentially leading to false positives or negativesInnovative predictive maintenance for mining grinding mills: from 2023年1月22日 Vibration issues of a fivestand tandem cold rolling mill were found in the steel production practice, and the experimental observation and numerical analysis indicated that the vibrations were related to the backup roll bearing The results were validated by replacing the backup roll bearing with the new bearing resulting in 30% decline in vibration amplitude Vibrations of tandem cold rolling mill: coupled excitation of rolling Changes to the ore hardness, feed size or ore specific gravity require an alert operator to adjust the variables while keeping up with all the other demands in the plant With the operator’s attention frequently drawn away from the SAG mill, the actual mill load would vary around the target, resulting in large corrections to the manipulated variables to bring the SAG back in controlTake a look at Advanced Process Control Systems Ausenco