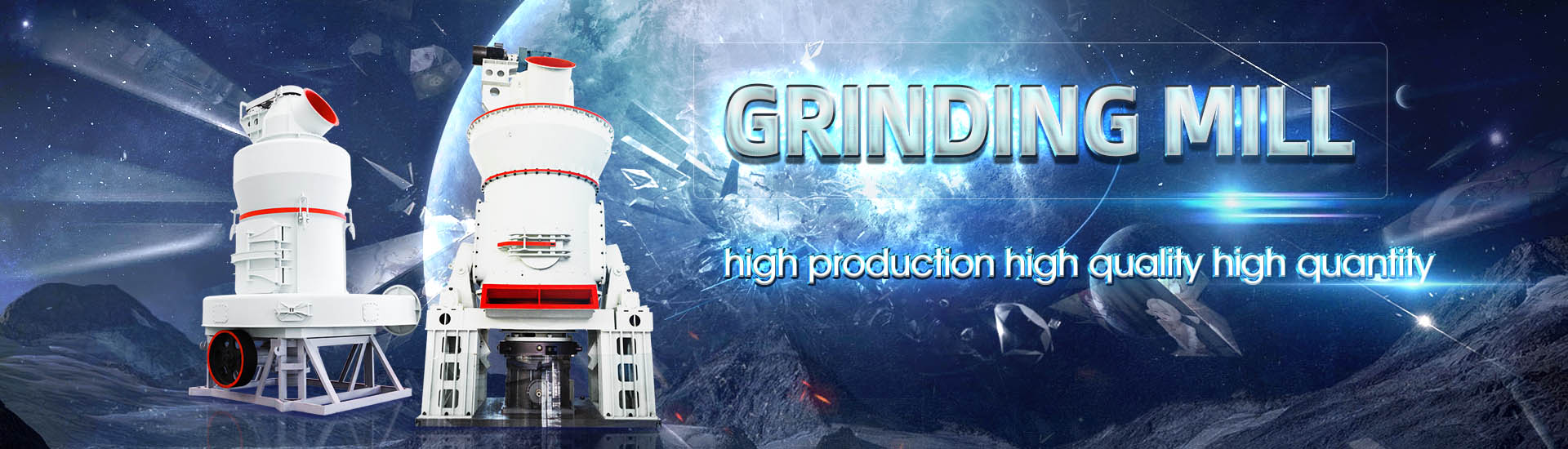
Ore mill production system

Monitoring ore loss and dilution for minetomill
This study was aimed at increasing mine output and profit margin by controlling fragment size distribution, managing grade variability, and ensuring that broken ore reaches the mill plant timeously Movement of rock, ore loss, and dilution 2018年3月25日 Ore resource and reserve block models are intended to forecast tonnage, grade, and contained metal within a mineral deposit Many models may be produced along the mine Implementing an Ore Reconciliation System Supported by 2022年1月1日 The BrainWave controller is able to maintain the mill weight on target with the least variability and avoid overloads without making excessive reductions to the ore feed rate Advanced process control for mineral processing operationsFrom the model, an alternative production plan is presented with a positive impact of USD 256M over the current net present value of the mining/mill system Keywords: sustainable RedalycMine/Mill production planning based on a
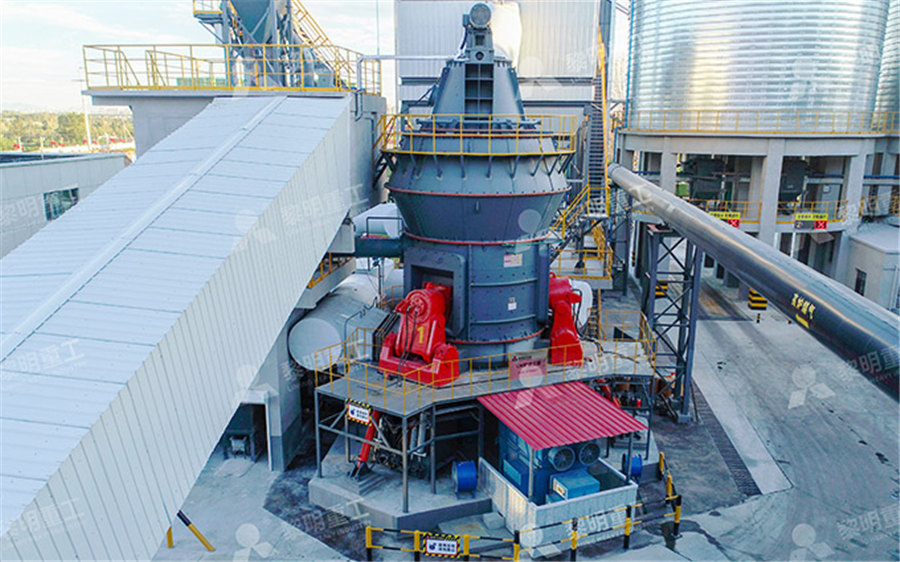
Characterizing a mining production system for decisionmaking
A mining production system (MPS) is a result of an iterative process of design, planning, and optimization of mining input variables and decisionmaking variables (DMVs) The MPS exists 2016年2月1日 The purpose of this study is to understand how ore loss and dilution affect the mine call factor, with the aim of subsequently improving the quality of ore mined and fed to the mill It wasMonitoring ore loss and dilution for minetomill 2017年11月2日 Mineral processing is one of the most energyintensive stages of the overall mining beneficiation chain, with an increasing share of the industry footprint This chapter Plant Automation for EnergyEfficient Mineral Processing2016年6月1日 Mine to mill optimization will lead to a systematic reduction of production costs in an open mine In this paper, mine to mill optimization has been designed and implemented in theComplete Optimisation from MinetoMill to Maximise
.jpg)
Development of ore sorting and its impact on mineral processing
2014年10月15日 The goal of ore sorting is to reduce the total amount of material sent to the high energy milling circuit, while not significantly impacting total metal recovery In general, ore 2023年10月17日 Choosing a suitable ore powder grinding mill is crucial to improving production efficiency and product quality Type of Ore powder grinding mil 1 Raymond mill Raymond mill feed particle size ≤30mm, production How to choose a suitable ore powder grinding mill?2017年7月26日 We will consider an ore with a ball mill work index varying between 16 and 13, feeding into a single stage ball mill operation with one million kilowatts per day consumed power For the particular mill configuration, a performance graph, Fig (21), has been constructed according to Bond’s methodsHow Ball Mill Ore Feed Size Affects Tonnage Capacity2019年8月29日 Sensor‐based ore sorting applies at various points in the process flow diagram and is suitable for waste elimination, for material diversion into different process lines, for the production of (PDF) Sensor‐Based Ore Sorting Technology in
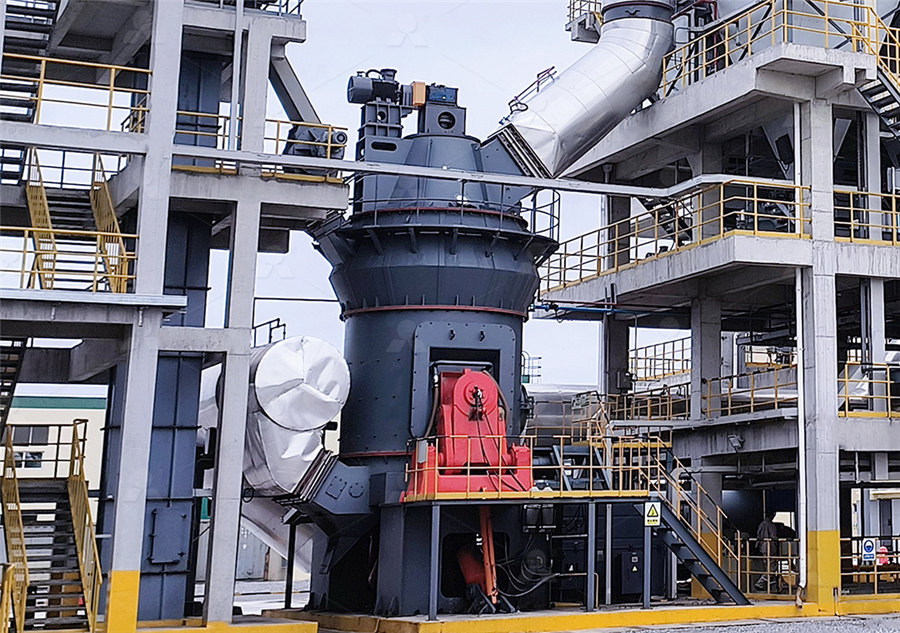
Mine/Mill production planning based on a Geometallurgical Model
2016年6月1日 From the model, an alternative production plan is presented with a positive impact of USD 256M over the current net present value of the mining/mill system Pau Branco mine geological modelSAG AND BALL MILL EFFECTS FROM ORE SORTING SYSTEM IMPLEMENTATION *J Starkey1,2, B Hilscher1, S Reeves1, and J Hedderson1 1SacréDavey Engineering 212 151 Randall Street In order to accurately forecast production, new measurements of hardness need to be performed on theSAG AND BALL MILL EFFECTS FROM ORE SORTING SYSTEM MinetoMill We can correlate ore characteristics with important operating parameters in the mine and processing plant, such as ore dilution, ore losses, fragmentation, throughput and energy consumption This provides an understanding of how different ores affect mine and plant operation and the final productSmartTag ore tracking MetsoRod Mill The rod mill is loaded with steel bars as grinding media and comprises five parts: cylinder shell, feeding system, discharge system, main bearing, and transmission system It is suitable for both dry and wet grinding to meet customer needs Materials with a Moh's Hardness of 5512 can all be handled by our millOre Grinding Mill
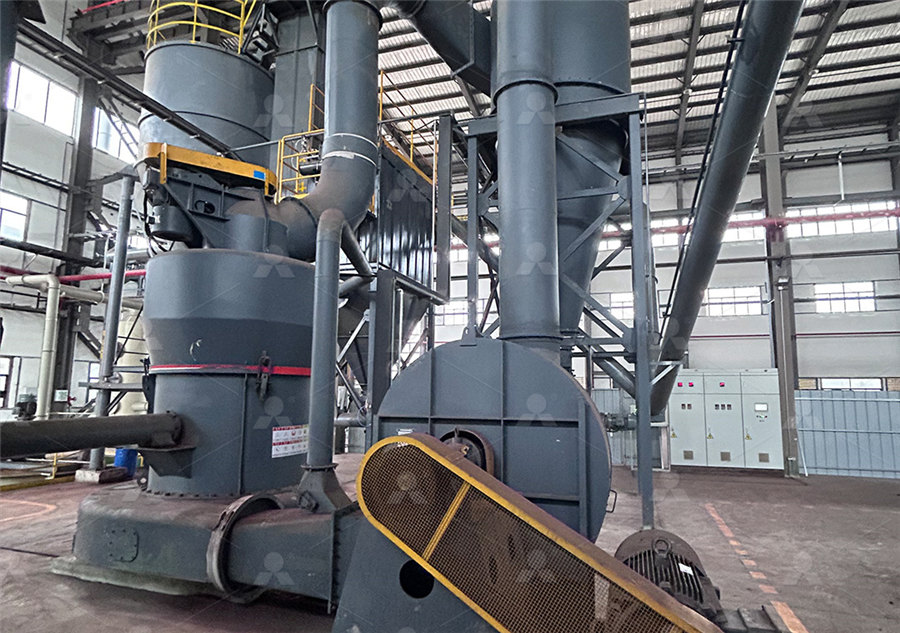
Understanding the SAG Mill in Copper Ore Mining Process
The rod mill is another type of grinding mill used in the copper ore mining process This machine uses steel rods as the grinding media instead of balls, which are commonly used in ball mills The rods grind the ore by tumbling within the mill, similar to the action of a rotating drum2020年10月19日 This study aimed to develop and assess the feasibility of different machine learning algorithms for predicting ore production in openpit mines based on a truckhaulage system with the support of the Internet of Things (IoT) Six machine learning algorithms, namely the random forest (RF), support vector machine (SVM), multilayer perceptron neural networks Estimating Ore Production in Openpit Mines Using Various SBM ultrafine powder technology co,ltd Is China's excellent ore mill supplier Our main products include ultrafine vertical roller mill, ultrafine grinding mill, stone powder production equipment, Welcome to consult and perfect service system The main products include: ore stone crushers (jaw crushers, cone crushers, hammer crushers SBM Ultrafine Powder Technology Industrial Grinding Mill, 2018年3月25日 Western United States This ore reconciliation system has been developed to capture variance between forecasted values and actual production data at multiple stages along the mine value chain Some basic ideas on statistical process control will be discussed and key recommendations for implementing an ore reconciliation system will be highlightedImplementing an Ore Reconciliation System Supported by
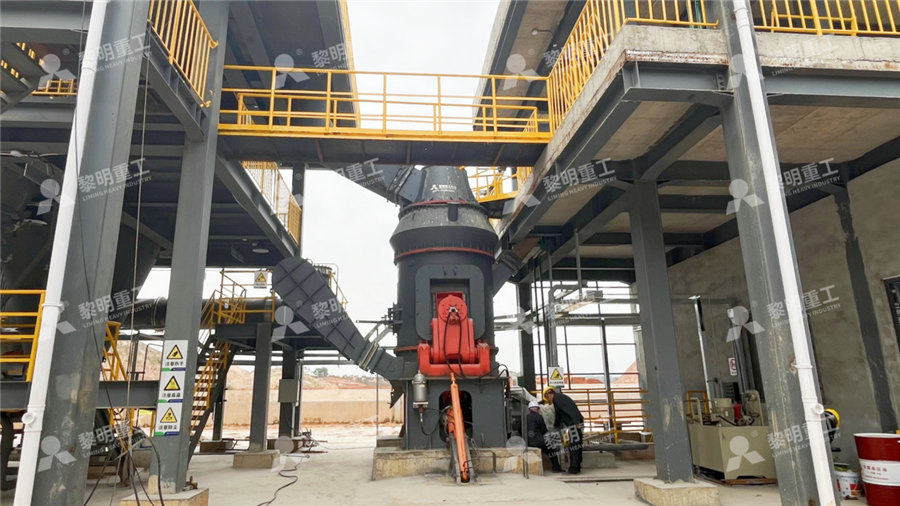
(PDF) Empirical Model of Discretized Copper Ore Flow Within the
2019年5月26日 A model of the transport system in a copper ore mine was prepared using FlexSim software and the simulations were performed for five days Empirical parameters were applied to each item of the 2024年4月26日 The final stage in iron ore processing is ironmaking, where the iron ore is transformed into molten iron through a process called reduction The most common method of ironmaking is the blast furnace route In a blast Iron Ore Processing: From Extraction to Manufacturing2017年7月30日 Simple Mass Balance Model (I = P + W) Notes: I = input, P = product, W = waste 32 Complex Mass Balance Model A complex mass balance model is detailing of simple model by making compartments A Closed Model of Production System for Energy SelfSufficiency Rice MillWhen iron ore is extracted from a mine, it must undergo several processing stages Six steps to process iron ore 1 Screening We recommend that you begin by screening the iron ore to separate fine particles below the crusher’s CSS before the crushing stageThe six main steps of iron ore processing Multotec
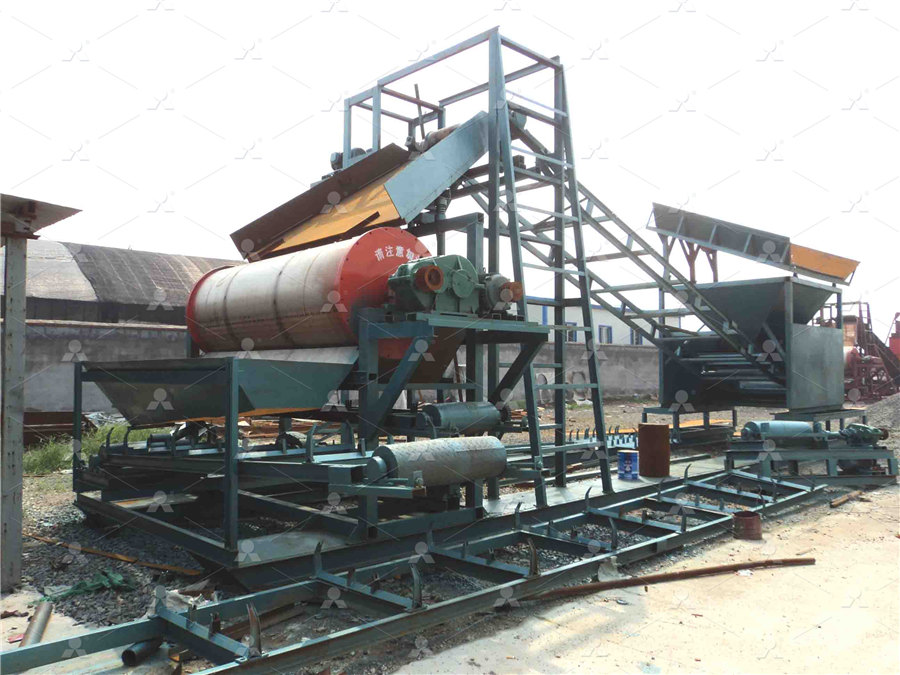
(PDF) THE TRANSITIONAL CHANGE ON THE IMPLEMENTATION
There are ive phases in the system thinking mentioned above that afect the transitional change from ISO 14001:2004 into ISO 14001:2015 in the environmental management system at copper ore mill: • Phase A – Output: Phase that deines clearly the objectives to the ore and the volume of the ready product The granularity of the ore is continuously reduced due to energy transfer by the grinding condition, which reduces their bond strength Ore size reduction is the result of the following three main fragmentation mechanisms 1 Abrasion 2 Cleavage 3 Fracture Figure 1 Grinding of ores inside a ball millControl of ball mill operation depending on ball load and ore 2015年1月1日 Current ore production from this mine property is about 200,000 tonnes per day (tpd) of which about 150 ktpd from the open pit and the rest is mined from DOZ (Deep Ore Zone) block cave mine (PDF) Deep Mill Level Zone (DMLZ) of East Ertsberg Skarn System (EESS 2023年12月1日 SBMmill can provide every customer with a complete set of gold ore crushing and processing production equipment and comprehensive technical support with an equiaxed crystal system and a cubic facecentered lattice Natural good crystal forms are extremely rare Clum ultrafine vertical mill Fineness: 1503000mesh Yield: 120t/hHow to crush gold ore?Gold ore crushing production line
.jpg)
Mill Village and Factory: Introduction: How Textile Mills Worked
2017年6月1日 How Textile Mills Worked Integrated cotton mills were "designed to move cotton through a precise series of production processes that separated, straightened, and twisted cotton fibers, combined them into yarn, then wove the yarn into cloth Manufacturing began in the opening room, where workers removed the ties and bagging from bales of raw cotton 2023年5月6日 The production process of copper ore processing mainly includes crushing, ore The copper ore processed into granules is screened by a vibrating sieve and sent to a ball mill for grinding and crushing Here also need Copper Ore Production Process JXSC Mineral2019年1月1日 The system of mining operations does not enable longlasting mining of singletype ores that causes instability of mineral materials intended for concentration(PDF) Adaptive control of ore mill charge ResearchGate2021年5月31日 The ore blending system was developed and operated stably on the production site The industrial test and actual production results have proved the effectiveness and reliability of this method (PDF) A Method of Ore Blending Based on the Quality
.jpg)
TracerBased MineMill Ore Tracking Via Process Holdups at
attempts at quality minemill metal accounting, reconciliation and optimisation are: 1 the need to reliably track ore from source to product, and 2 the need to accurately account for variable 42 Impact on mine/mill system Iron ore lump quality affects pig iron production operational cost Diluting the Fe content decreases the productivity of the blast furnaces; consequently, more charcoal is required to produce the same quantity of pig ironSciELO Brasil Mine/Mill production planning based on a Energies 2021, 14, 1786 4 of 14 (a) (b) Figure 2 Ball mill drive system with low‐speed SAS motor without intermediate gearbox: (a) prior to modernization, (b) after modernization on the right [34]Energy Efficiency Analysis of Copper Ore Ball Mill Drive Systems2024年4月3日 Purpose of the article Olive mill wastewater raises environmental concerns due to the presence of pollutants and phytotoxic compounds This study aims to evaluate the environmental performance of an integrated process that recycles olive mill wastewater while concurrently producing Arthrospira platensis for food applications Methods The quantification Environmental and economic analysis of an olive mill wastewater
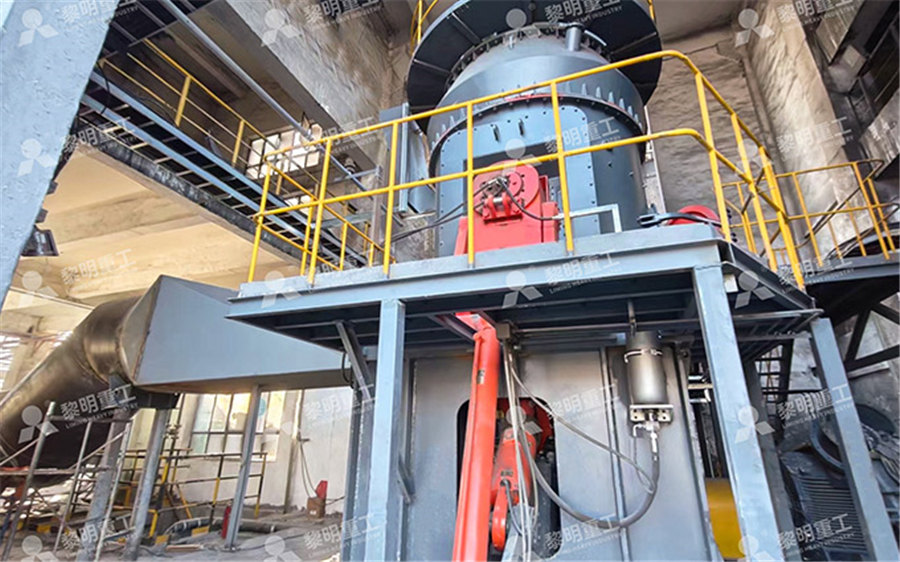
Pythonbased Fuzzy Control of Ore Feeding System ResearchGate
2021年4月13日 In this paper, an adaptive fuzzy control scheme is addressed for switched nonlinear systems with uncertain deadzone, unknown nonlinearities and immeasurable statesproduct system, where the classifier coarse is extracted as a product rather than returning to the mill This enables a twoproduct system with the fines extracted via the classifier overflow and the bulk of the product via the underflow using the so called grits extractor The achievable product size from a VRM isVertical Roller Mills used for the comminution of mineral ores2023年12月12日 In addition, the ore properties are one of the important parameters for the optimal utilizing of the ball mill Ore can have various properties, such as hardness, density, moisture content, etc (PDF) Control of ball mill operation depending on ball load and ore the economic value of the mine/mill system This model allows adjustment of the mineral process, better control of mine and plant operation, decreases the variability of feed quality, and supports an economic study to define the impact of production plans on the NPV of the mine/mill system 21 Geological model The first step was to define tyRedalycMine/Mill production planning based on a
.jpg)
Guidelines for Ore Tracking System in the Complex Underground
2019年3月1日 Tracking of a mined ore is now considered as one of the key issues for the needs of improvement of the whole value chain of metal production Ore beneficiation processes (grinding, milling 2019年8月14日 • Central discharge ball mill: the inlet of medium unloading ball mill is at both ends, and the outlet is in the middle of the ball mill 4 According to the ore discharge of ball mill: • Overflow ball mill: Discharge the ore through hollow shaft • Grid ball mill: Discharge the ore through the plaid plateThe Ultimate Guide to Ball Mills Miningpedia2024年3月17日 Steel making is a sophisticated process that turns iron ore into steel, involving methods like the Blast Furnace and Electric Arc Furnace to produce various grades of steel The industry emphasizes sustainability by using additives and recycled materials while ensuring quality through rigorous testing for diverse applicationsA Visual Guide: Steel Making Process Chart Cabaro GroupGearless mill drives GMDs offer ore producers multivariable interacting system Dynamically changing ore conditions and wear parameters pose 40 ft, 28 MW SAG mill and two 28 ft, 22 MW ball mills to the project in order to meet the challenge of highercapacity production coupled with low ore grades Learn more GMD system Making remote mines and low ore grades economical and shifting
.jpg)
Towards waterless operations from mine to mill ScienceDirect
2022年9月1日 The purpose of ore blending is simply to provide uniform mill feed which aids in improving production efficiency and reducing production cost Metso Minerals (2022) introduced an integrated approach, which is similar to the mine to mill approach ( Ouchterlony, 2003 , McKee, 2013 ), in quarries2018年9月24日 In this paper, the sand casting process was evaluated using ProCAST simulating software and practical experience for manufacturing of the high chromium stainless steel outlet diaphragms used in iron ore ball mill In the simulation practice, the effects of feeding and gating designs on the liquid flow, heat transfer and solidification phenomenon were Simulation of casting process: case study on the gating and PanAust Ore production rate is 45Mt pa with direct tipping to a SAB mill with a carbon in leach process plant Approximately 100,000 oz of gold is produced per annum The operation is located in mountainous terrain with minimal ROM stockpiling are which results is limited capacity for blending from stockpile with thePredicting Mill Ore Feed Variability Using Integrated Geotechnical operations in the iron ore pelletizing process The mill product, due to its physical properties, determines the efficiency of subsequent stages of classification, filtration and pelletizing, thus impacting the quality of iron ore pellets The work demonstrates the application of the population balance model in the optimization of a fullscale ballPOPULATION BALANCE MODEL APPROACH TO BALL MILL OPTIMIZATION IN IRON ORE

The transitional change on the implementation of iso 14001:
2017年9月1日 PDF The transition process of implementation standard for environmental management system (EMS) ISO 14001 :2015 lasts for three years, requiring every Find, read and cite all the research