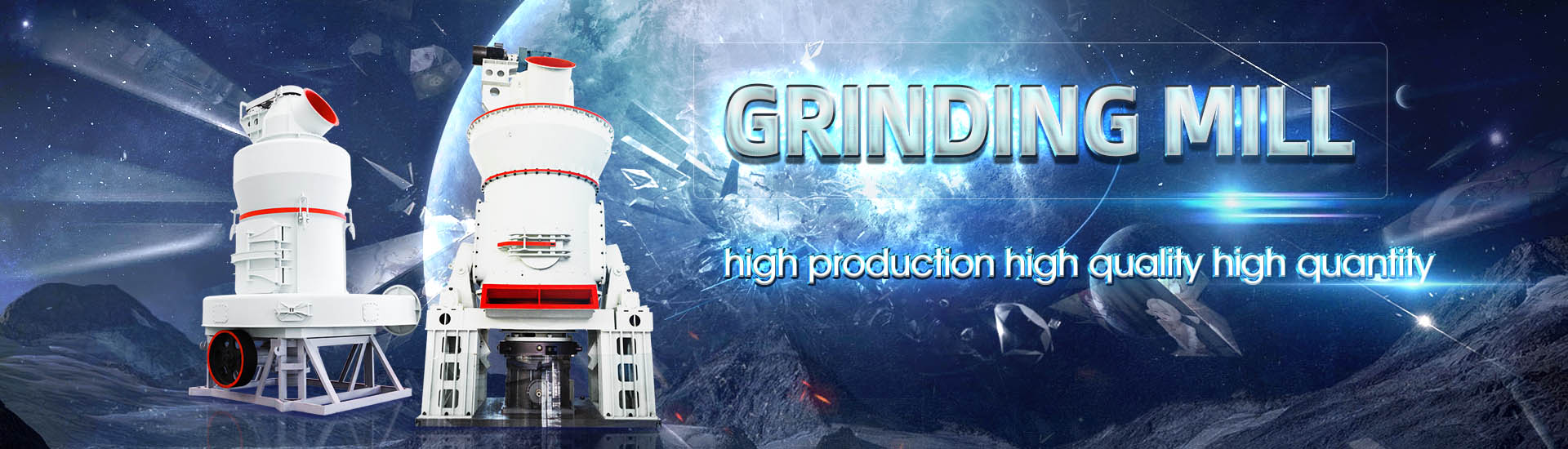
Power plant B coal mill repair danger point
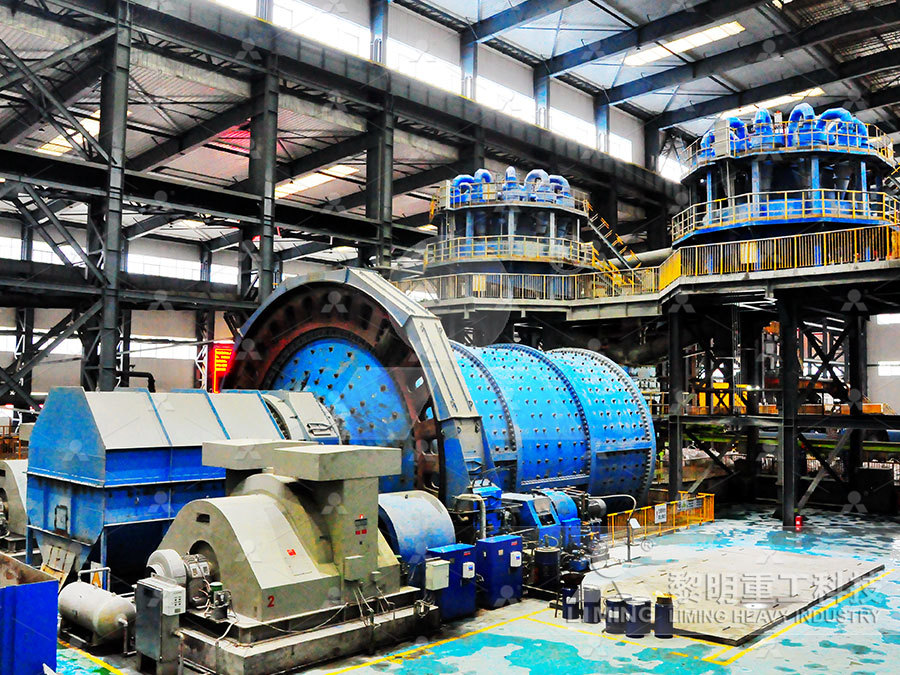
Coal Mill Safety: A Critical Aspect of Power Plant Operations Coal
Coal mills, also known as pulverizers, play a critical role in power plants by grinding coal into fine powder, which is then used in various pyroprocesses These mills pose significant safety risks Ensuring the safe operation of coal mills is crucial for preventing accidents, maintaining plant 2012年11月17日 The document discusses coal mill/pulverizers used in thermal power plants It describes how pulverized coal is dried, ground, circulated, and classified within the mill to produce a fine powder that is then transported to Coal mill pulverizer in thermal power plants PPT2015年8月1日 Power plant performance and reliability is highly influenced by coal mills that grind, dry, and transport coal to the furnace This paper presents a review of the current state Review of control and fault diagnosis methods applied to coal Coal mills or pulverizers play a very essential part in the coalfired power production system Coal mills grind the coal into fine powder, and the primary air entering the mill dries and drives the Coal Mill an overview ScienceDirect Topics
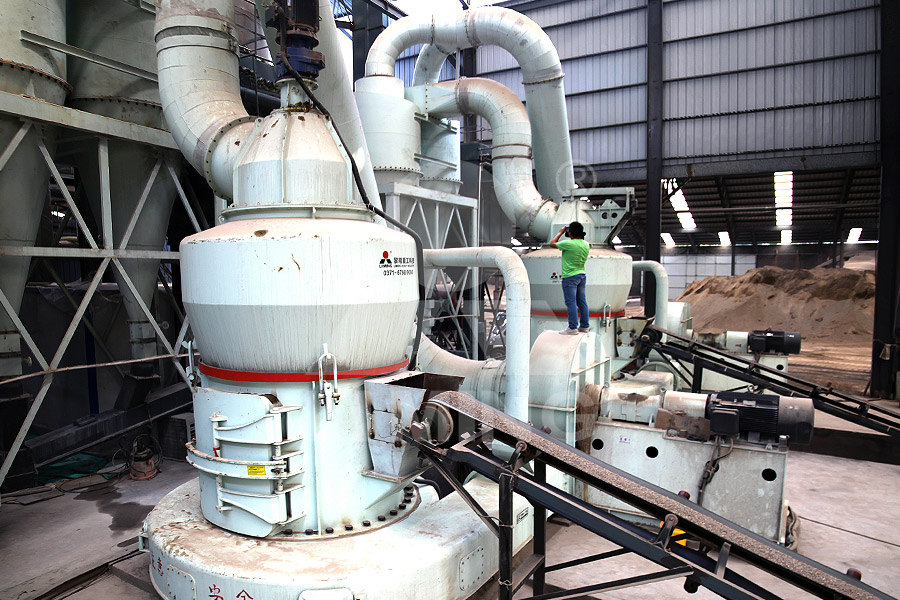
Risks assessment in thermal power plants using ISM methodology
2019年2月6日 Results reveal that insulation failure, barrier (B7), is the most influential hazard; hence, it must be addressed first for the effective implementation of OHS measures in coal 2018年3月15日 Specifically to plant workers, depending on the process and materials used, there are potential workplace hazards at different locations of the coal fired power plant These Criticalitybased maintenance of a coalfired power plantpotentially dangerous coal oxidation within a mill so that action can be taken to reduce the risk of a fire or explosion At the Hoosier Energy Merom power plant, 12 twinstream Millwatch COAL MILL Land Instruments InternationalRingRoll (BowlMill) and BallRace Mills comprise most coal pulverizers currently in service at pulverized coal power plants The grinding rolls are stationary in this design, while a worm Coal Pulverizer – Power Plant Pall Corporation
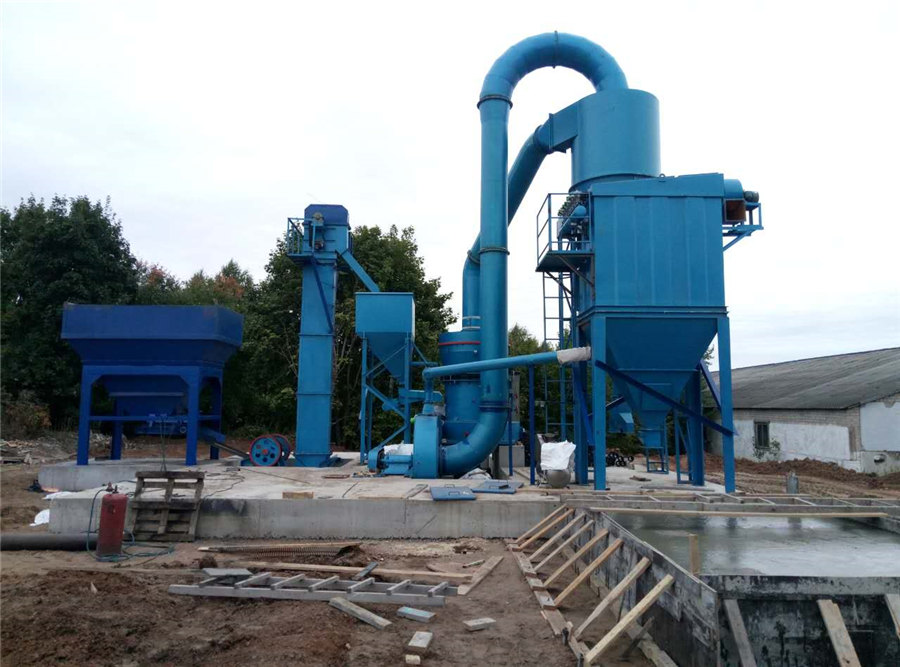
COAL HANDLING SAFETY Land Instruments International
Even in routine mill shutdowns, there is a danger that any residual coal left within the mill will oxidise, and may explode as the mill is restarted The Millwatch system is installed near the In this video you will get a live overview of ball and tube type coal mill used in thermal power plantLive Working of Ball and Tube Coal Mill in Thermal 2023年10月11日 Coal Dust Severity in a Power Plant: InSitu, Analytical, and Numerical Assessments(PDF) Coal Dust Severity in a Power Plant: InSitu, Profoundly influencing ability to generate power economically There are risks Firing high moisture highly reactive subbituminous coals exposes your plant to risks of: • Unsafe working conditions, possible threat to worker safety • Damage repair cost (Primary air inlet ducts, PA fans, mill internals, feeders, etc)Mill Inerting and Pulverizer/Mill Explosion Mitigation
.jpg)
OPTIMISATION OF THE INSTALLED BOILER AND TURBINE
2022年5月1日 Process model of the Coalfired Power Plant Source: (CoalFired Power Station, Diagram Stock Image C024/7686, nd) Can GE service my boiler mills? YES Our boiler mills and coal pulverizers span the globe and are built in a variety of sizes and capacitiesWe provide customized maintenance solutions, and offer a full spectrum of highquality solutions for each—in addition to our thousands of standard boiler mill parts and boiler service solutionsThis is the Power of YesBoiler Mill and Coal Pulverizer Performance GE Steam Power2020年4月2日 Milling system in coal power plant purposely to process the raw coal to become as pulverise fuel before enter to the Mill capacity with coal B typical 68 t/h 4 The usual set point is Analysis of the Coal Milling Operations to the Boiler Parameterscolumns The coal is fed into the terrace bin 1 by two overbin feed conveyors, T3AB while extracted by two underbin feeder belts, T4AB supplying coal through incline conveyor, T5AB before distributed by mill bunker filling conveyors, ECB into the five (5) mill bunkersCOAL HANDLING PLANT TERRACE BIN 1 REPAIR WORK eTenders
.jpg)
Hazards Identification and Risk Assessment in Thermal Power Plant
The coal fired thermal power plant susceptible to a wide range of hazards in its various operational areas Hazard identification and risk assessment is systematic approach to protect the health and minimize danger to life, property and environment This paper ball mill 3 3 1 B Training, proper supervision, PPE’sA control oriented model was then developed by Fan (1994) and Fan and Rees (1994) In 2009, coal flow and outlet temperature of mill were modelled using mass and heat balance equations for startup Sectional view of MBF coal mill Download Scientific Diagram2 Reliable and precise process monitoring Siemens has extensive and indepth experience of the power industry Our process instrumentation and analytics portfolio gives you the precision and integration into the automation system you need to ensure theProcess Instrumentation and Analytics for PowerIt is stable at temperatures required in the plant Equipment of a Steam Power Plant: A steam power plant must have the following equipment 1 A furnace for burning the fuel 2 A steam generator or boiler for steam generation 3 A power unit like a turbine to convert heat energy into mechanical energy 4UNIT – I COAL BASED THERMAL POWER PLANT
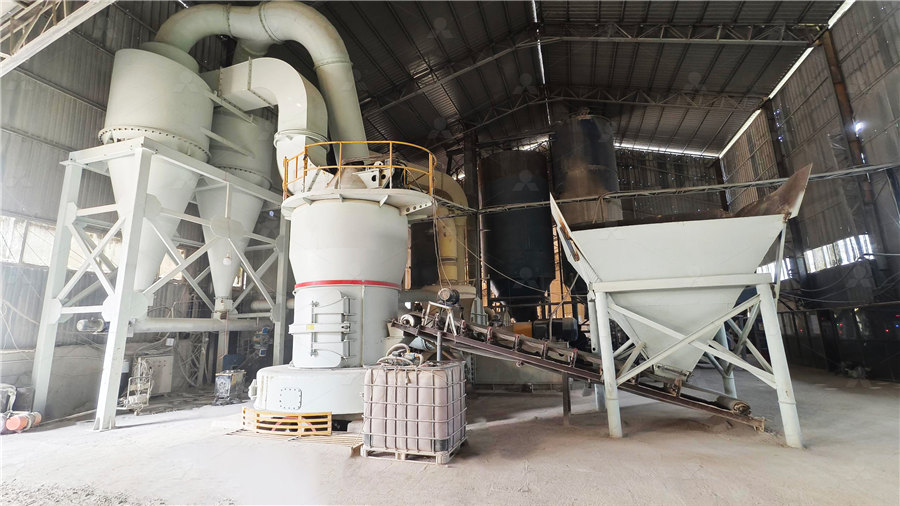
Pulveriser in Thermal Power Plant Bowl Mill Ball Mill
Introduction The main Function of the Pulveriser in thermal power plant is to crush/grinding the raw coal coming from coal handling system through coal feeder into a predetermined size in order to increase the surface area of the coal If 2019年5月21日 Maintenance Strategy Optimization of a CoalFired Power Plant Cooling Tower through Generalized Stochastic Petri Nets(PDF) Maintenance Strategy Optimization of a CoalFired Power Plant Lecturer Notes on EE2252 Power Plant Engineering II Year /IV Semester Eee Academic Year 20122013 PRATEEK JENA 2014 download Download free PDF View PDF chevronright Boilers and Thermic Fluid Heaters Arvind Yadav download Download free PDF View PDF chevronright Steam Generating System(PDF) Power Plant Engineering Ramesh PanthaganiThis document discusses coal pulverization in power plants It covers various topics related to coal pulverizers including: Types of coal and reasons for pulverizing coal like improved efficiency and combustion control Two types of pulverizer firing systems direct and indirect Different types of pulverizers classified by speed tube mills, bowl mills, and impact mills Key Coal Mills in Thermal Power Plant PDF Mill (Grinding) Scribd
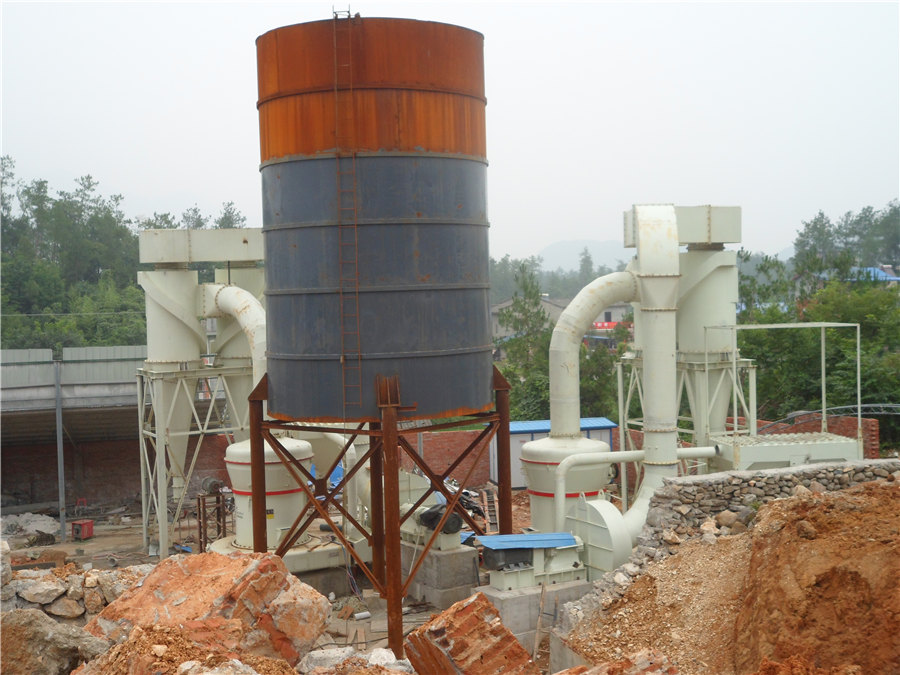
Coal Mill in Thermal Power Plant: Enhancing Efficiency and
Bellian Machinery leads the industry in providing highquality coal mills for thermal power plants With enhanced grinding efficiency, reliable and safe operation, precise control, low maintenance requirements, and commitment to environmental sustainability, Bellian Machinery's coal mills are revolutionizing coal milling in thermal power plants Understanding coalfired power plant cycles 5 1 Introduction Figure 1 shows the basic principle of combustionbased power generation using a steam turbine The optimum point lies at higher pressures as the turbine inlet temperature is increased As most gas turbines exit to atmosphere, ambient conditionsUnderstanding coalfired power plant cycles ICSC2011年12月31日 Defects such as fastener oxidation and corrosion and liner edge warping are recurrent in coal bunkers, requiring maintenance and repair in order to avoid inner wall damages, compromising the safe Operation and Maintenance of Coal Handling System in Thermal Power PlantCoalfired plants are the most widely used power plant today They involve the combustion of coal producing high pressure (typically 2400–3500 psig, ~165–240 bar) and high temperature (>500ºC) steam which is used to drive a turbine at synchronous speed (3000 rpm in countries such as the UK with a 50 Hz supply frequency, 3600 rpm in Instrumentation and control in coalfired power plant ICSC
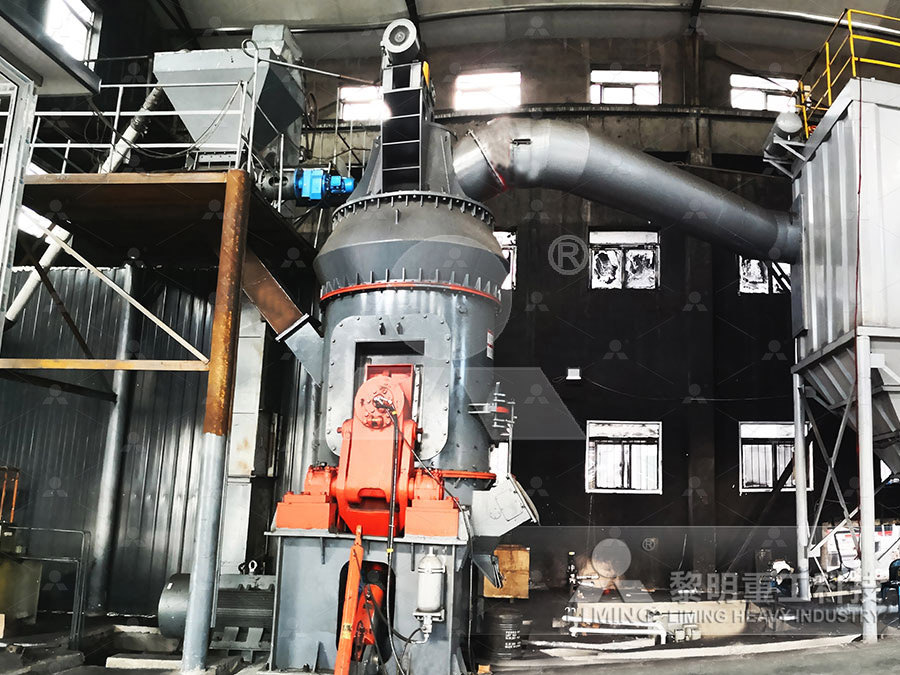
Pulverised Coal Flow measurement in Thermal Power Plant
In this paper, GA is applied to develop the coal mill model and to estimate the pulverised coal flow using real time onsite plant data 2 COAL MILL MODELLING In thermal power plant, pulverization of coal is carried out by coal mill Raw coal is moved from the storage to the mill by conveyor mechanism The type of coal mill envisaged for ourMerits (A dvantages) of a Thermal Power Plant: The unit capacity of a thermal power plant is more The cost of unit decreases with the increase in unit capacity Life of the plant is more (2 530 years) as compared to diesel plant (25 years) Repair and maintenance cost is low when compared with diesel plantUNIT – I COAL BASED THERMAL POWER PLANTThe design parameters of the 750MW pulverizedcoalfired power plant as discussed in Chapter 2 provide a net plant efficiency of 45% at rated output condi Skip to Main Content Close Journals ASME Journals At part load, the performance of the nozzlecontrolled turbine with 3 valve points at about 100%, 90%, PulverizedCoal—Fired Power Plant Performance and Operating 2011年8月1日 Now suppose this same pulverizer must grind sufficient coal flow to produce full load on the boiler with fuel that is 40 HGI, still 3/4inch maximum size with 7% moisture, but with an increased Pulverizers 101: Part I POWER Magazine
.jpg)
A Study on 500 MW Coal Fired Boiler Unit’s Bowl Mill
Section of coal bowl mill Table 1 Guaranteed coal conditions for mill performance evaluation Coal Moisture % 20 Coal HGI 55 Mill Outlet Temperarure °C 80 Mill Air Flow T/hr 102 Coal Fineness (% passing trough 200 mesh) 70% passing through 200 mesh and 90% passing through 50 mesh Differental Pressure 300 mmwc Coal Output from Mill 609 t/hrA coalfired power plant (Fig 2) operates by burning coal to generate heat, which is then used to produce steam in a boilerThe highpressure steam drives turbines connected to generators, converting the kinetic energy into electricity Coalfired power plants have long been prominent in electricity generation due to the abundant availability of coal reservesCoalFired Thermal Power Plant ScienceDirect TopicsCOAL MILL COAL MILL Derek Stuart, AMETEK Land, and Todd Collins PE, Hoosier Energy, US, discuss available techniques for detecting early signs of mill fires and explosions Hoosier Energy Merom power plant Reprinted from World Coal March 2014 March 2014 COAL MILL Land Instruments International2014年10月1日 Request PDF Numerical and experimental analysis of pulverized coal mill classifier performance in the Soma B Power Plant Coal particle separation in a classifier after the pulverization Numerical and experimental analysis of pulverized coal mill
}@~3SRDG`IA1KP_ICWAA.jpg)
Coal Mill Safety: A Critical Aspect of Power Plant Operations Coal
Safe operation of coal grinding systems: Raw coal silo protection against fire and explosions Safe operation of coal grinding systems: Raw coal yard management The purchasing process for coal grinding systems needs changes Talk at a virtual seminar, November 2023 Accept the probability that the fire and explosion safety of your coal grinding system is nothing more than a mirage1 Coal Mill Startup and Shutdown Free download as Word Doc (doc / docx), PDF File (pdf), Text File (txt) or read online for free This document provides a standard operating procedure for starting up and shutting down coal mills at a power plant It outlines the steps to take for normal coal mill start up including ensuring proper pressure and flow, opening gates and valves, Coal Mill Startup and Shutdown PDF Energy TechnologyAdvanced Review Steam power plant configuration, design, and control Xiao Wu,1 Jiong Shen,1 Yiguo Li1 and Kwang Y Lee2∗ This article provides an overview of fossilfuel power plant (FFPP) configuraSteam power plant configuration, design, and control Baylor 2013年6月24日 6 PARTS 1Coal Conveyor Coal conveyor is a belt type arrangement that are used to move coal efficiently 2Pulverizer Pulverizer increases the coal combustion efiiciency of coal 3Boiler (Furnace) A boiler is Coal power plant PPT Free Download SlideShare
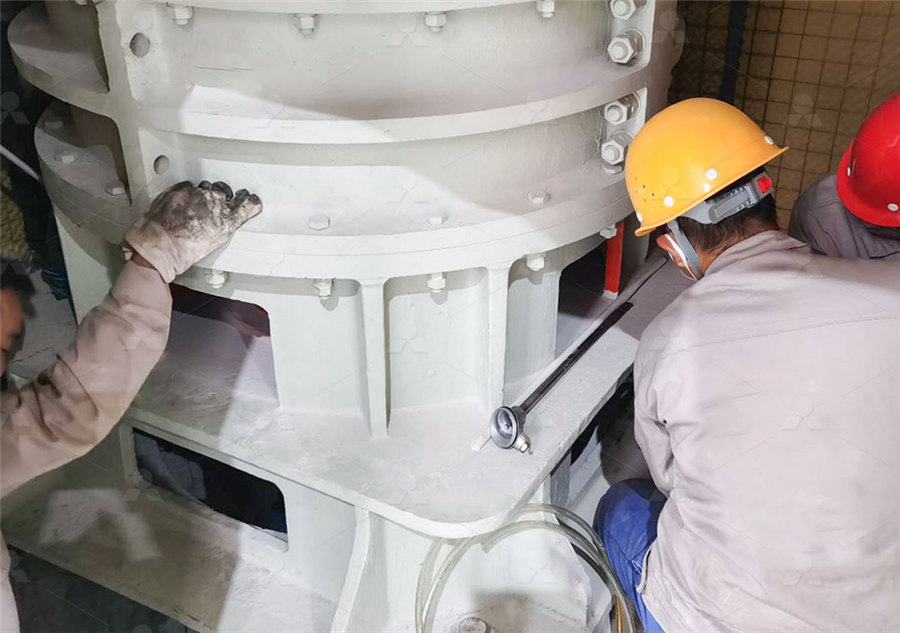
Modeling and Parameter Identification of Coal Mill
2009年9月20日 A control oriented model was then developed by Fan (1994) and Fan and Rees (1994) In 2009, coal flow and outlet temperature of mill were modelled using mass and heat balance equations for startup The mill design in the power plant is a vertical bowl The mill rotated on his axis at minimum speed 35rpm by a motorreducer train The grinding rolls are supported by three oscillating journals The rolls rotate freely crushing the coal on the bowl, the pressure for optimal crushing beingAnalysis of the Coal Milling Operations to the Boiler ParametersCOAL MILL COAL MILL Derek Stuart, AMETEK Land, and Todd Collins PE, Hoosier Energy, US, discuss available techniques for detecting early signs of mill fires and explosions Hoosier Energy Merom power plant Reprinted from World Coal March 2014 March 2014 COAL MILL Land Instruments International2022年3月1日 With the ever‐increasing danger of climate change, power plants are shifting from polluting fossil fuels to sustainable bioenergy fuels As Malaysia continues to pledge to decrease glasshouse An overview of palm oil biomass for power generation sector
.jpg)
Automatic explosion door of power plant coal mill
1, a kind of power plant coal automatic burstpreventing door comprises former coal pulverizer explosion proof door (C), it is characterized in that utilizing active section (8) to be hinged on the end of explosionproof vent (B) explosionproof door closure (A) being installed at former coal pulverizer explosion proof door (C) rear portion configuration explosionproof vent (B); Fixed 2015年12月5日 Coalfired power plants are of high importance for the secure electrical power generation in the next decades However, the massive growth of renewable energy in some countries changes the market conditions [1]In 2014, the installed capacity of wind and photovoltaic energy has reached an amount electrical capacity of 404 GW and 382 GW, Development and validation of a dynamic simulation model for 2013年1月1日 Zhao Lh (2011) Operation and maintenance of coal handling system in thermal power Plant[J] Coal Mine Mach 32(2):201–204 Google Scholar Zhao Lh et al (2001a) Application of SBS400 type comb vibrating screen in coal coveyoring system Coal Mine Mach 22(1):51–52 Google ScholarOperation and Maintenance of Coal Conveying System 2015年2月1日 Advanced coal plant emissions controls are the norm, and PRB coal is in use to some extent at most power plants in the US, and the Environmental Protection Agency (EPA) has proposed standards Understanding Coal Power Plant Heat Rate and Efficiency
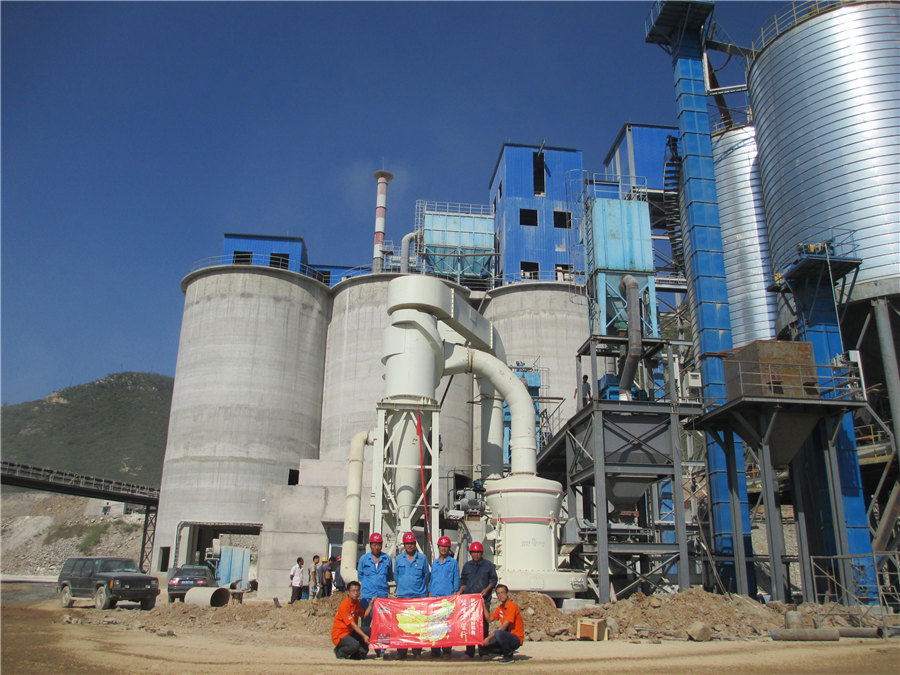
Decision Support System for Coal Mill Fault Diagnosis in Coal
The coal mill under study is a vertical roller type, such as the one available at the PLTU (coalfired steam power plant) Rembang unit, which has two boilers with a steam generator capacity of 513 t/h The schematic of a coal pulverizer mill is provided in Fig 1 Details of these coal mill parameters are presented in Table 1 Coal mill modeling