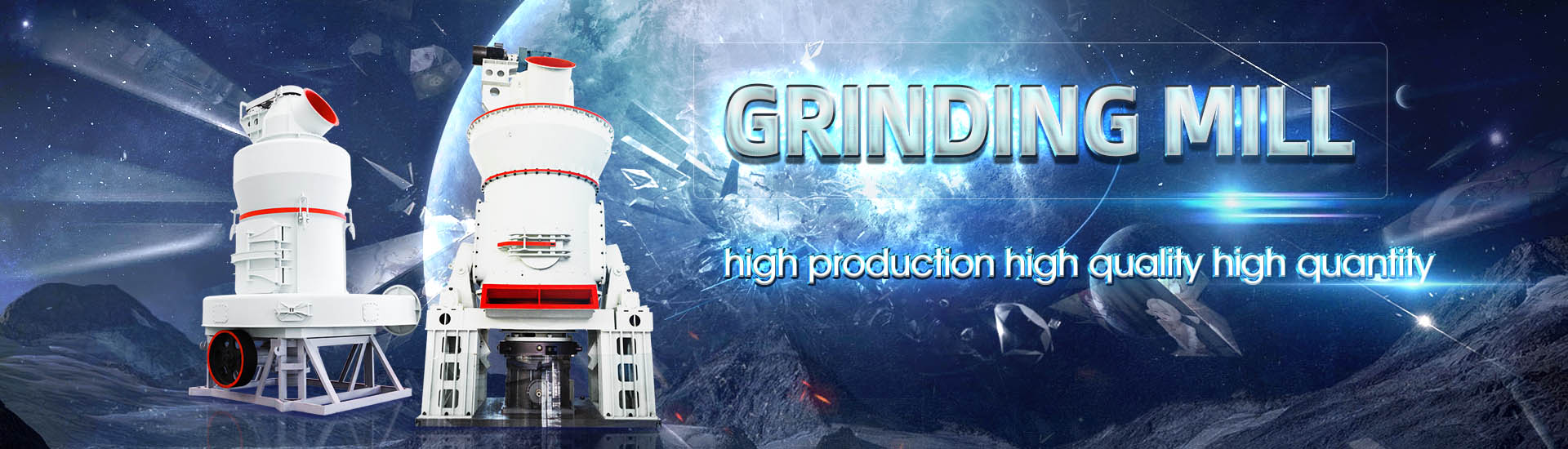
Which pulverized coal vertical mill is more expensive
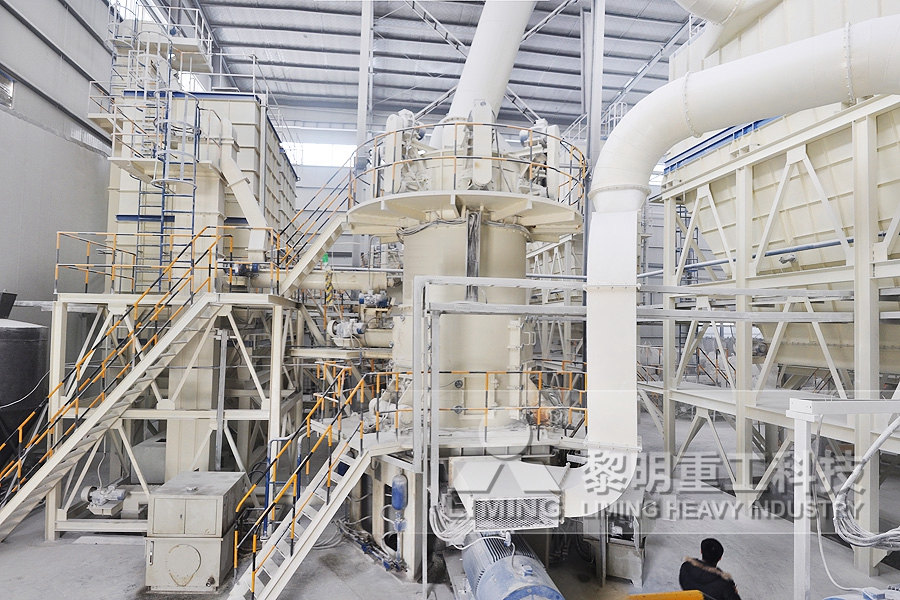
A Comparison of Three Types of Coal Pulverizers Babcock Power
The vertical roller mill (VRM) shown in Figure 4 is an air swept, mediumspeed, vertical pulverizer with integral classifier It pulverizes coal by applying hydraulicallyloaded grinding pressure through three grinalternative to ball tube mills and vertical spindle mills Since its introduction, Riley Power has furnished more than 1600 mills to over 500 installations throughout the world Riley Power also RILEY POWER’S ATRITA COAL PULVERIZERS RELIABLE COST Coal Pulverizer are designed to reduce the size of the incoming raw coal to a fineness that will result in good furnace performance The grinding surface in the pulverizer resembles a shallow dish or bowl Therefore the name “Bowl Mill” Bowl Mill Coal Pulverizer COAL HANDLING PLANTSFrom our original E/EL ballandrace type pulverizers for lower capacity applications, to the latest BW Roll Wheel™ pulverizer capable of grinding up to 230,000 pounds of coal per hour (104,300 kg/hr), we set the standard for high Reliable Coal Pulverizers and Mills » Babcock Wilcox
.jpg)
Coal Pulverizer – Power Plant Pall Corporation
Vertical Roller Mills This mill uses hydraulically loaded vertical rollers resembling large tires to pulverize raw coal fed down onto a rotating table As the table rotates, the raw coal is 2020年8月12日 Vertical Coal Mill (VCM) is equipment for grinding and pulverizing coal into micron size Rotary kilns then use the powders as fuel burners The VCM has a housing section equipped with aAn investigation of performance characteristics and We’re a world leader in coal pulverizing and boiler mill operations for horizontal and vertical boiler mills—committed to highefficiency performance, reduced maintenance costs, and longer time between outages Can GE service my Boiler Mill and Coal Pulverizer Performance GE Steam 2020年8月12日 This study shows the performance of a currently running vertical roller coal mill (VRM) in an existing coalfired power plant In a power plant, the coal mill is the critical An investigation of performance characteristics and energetic
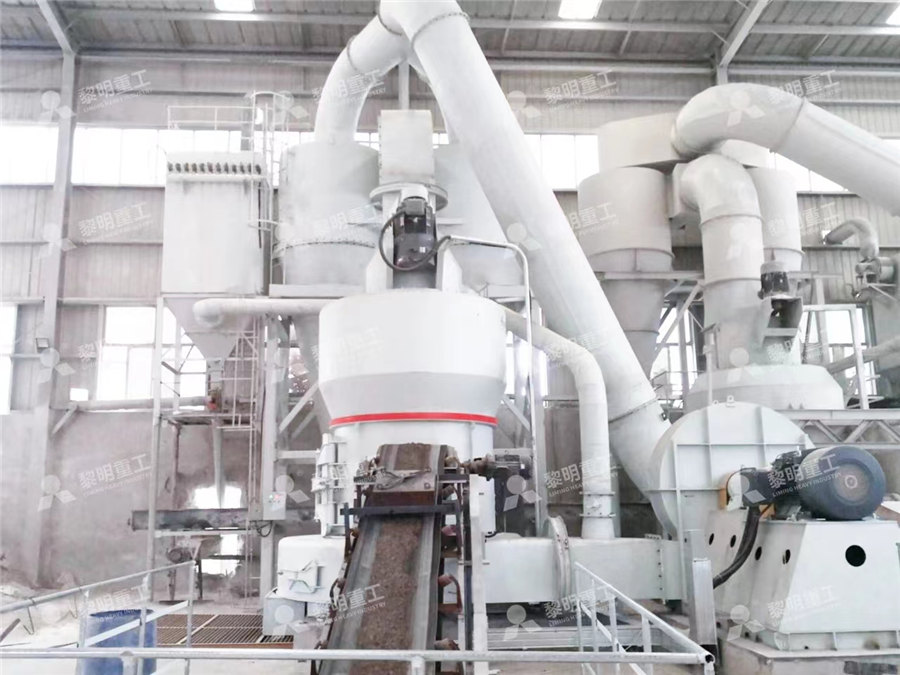
COAL VERTICAL MILL Xinxiang Great Wall Machinery Co, Ltd
Process introduction GRMC coal vertical mill produced by CHAENG adopts a special structure design and production technology, and the quality is up to the leading level in China It is the first choice equipment for grinding raw coal and bituminous coal 1 The raw coal is screened from the raw coal storage yard and then dropped onto the belt conveyor through the grid screen2024年1月11日 With a vertical roller mill (VRM) VRMs consist of a rotating table or bowl and rollers 1 To grind the coal, feed raw or initially crushed coal into the mill which is then ground between the rotating components; 2 Finally, hot air How to Process Coal into Pulverized Coal in 5 Steps?From the initial stages of coal crushing to the final step of coal powder creation, how coal is pulverized in a ball mill Skip to content Home; Product Center; Ball Mill More efficient combustion: Pulverizing coal into a fine powder enables better combustion by ensuring that all Vertical Coal Mill; Rod Mill; AG Mill and SAG Mill; Ball How Is Coal Pulverized in a Ball Mill?Mill connection: the circulating fan is connected to the explosionproof bag dust collector and the inert gas supplement pipe: the inert gas supplement pipe is connected to a heat source system that supplements the low oxygen content heat source gas to the pulverized coal vertical mill to control the low oxygen in the extracorporeal circulation system The limiting oxygen content What is the process flow of vertical mill to produce pulverized coal?
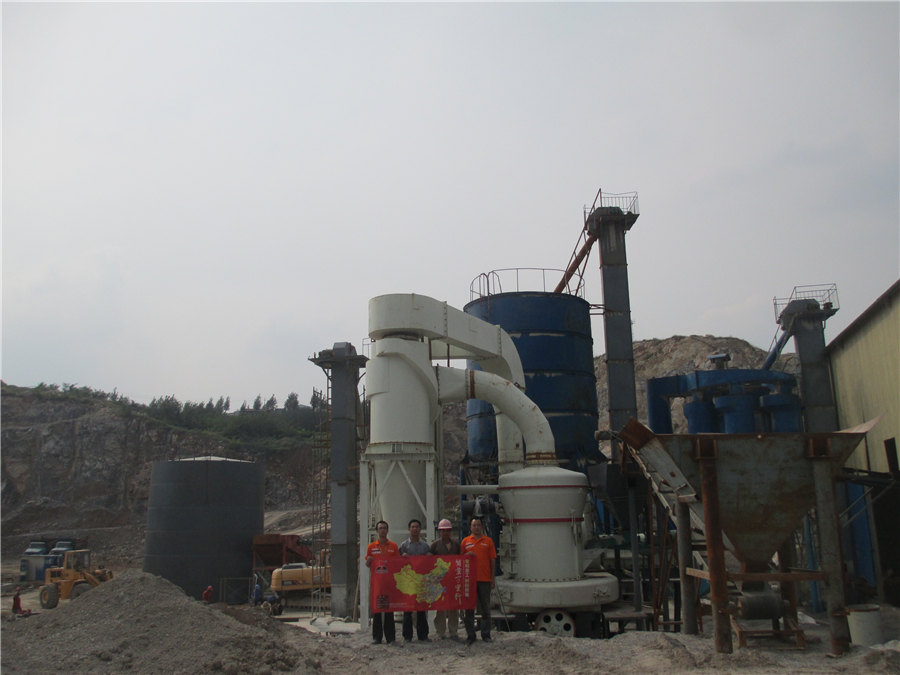
(PDF) Modeling and Control of Coal Mill Academia
Outlet pulverized coal flow is measured using sensors and that information has been used in modeling of coal mill (Blankenship, 2004) The drawback is that the equipment tends to be more expensive and requires frequent calibration2012年11月17日 20 131Fineness Fineness is an indicator of the quality of the pulverizer action Specifically, fineness is a measurement of the percentage of a coal sample that passes through a set of test sieves usually designated at 50, 100, and 200 mesh A 70% coal sample passing through a 200 mesh screen indicates optimum mill performance The mill wear and Coal mill pulverizer in thermal power plants PPT SlideSharePulverized coalfired boiler technology is a major con tributor to meeting worldwide electrical power generation requirements with approximately 970,000 MW e of capacDevelopments in Pulverized CoalFired Boiler TechnologyGas turbine combined cycle Shigehiro Shiozaki, Akira Yamada, in Advances in Power Boilers, 2021 637 Gasifier facilities 6371 Coal pulverizing and feeding system The purpose of the coal drying system is drying and grinding the raw coal for stable transportation of pulverized coal to gasifier and stable/highefficiency gasification at the gasifierCoal Pulverizers an overview ScienceDirect Topics
.jpg)
An investigation of performance characteristics and energetic
et al 2017) In a coalfired power plant, one of the main equipment is the coal mill, whose effectiveness influences mainly the whole power plant performance (Shah, Vuthaluru, andLearn more about GE's boiler mill services Our Boiler Mill and Coal Pulverizer Service Solutions help you make the most of your mill’s operational efficiency We’re a world leader in coal pulverizing and boiler mill operations for horizontal and vertical boiler mills—committed to highefficiency performance, Boiler Mill and Coal Pulverizer Performance GE Steam Powerand pulverized coal flow at desired set point value 1 INTRODUCTION Coal mill is an important component of the thermal power pla nt It is used to grind and dry the moisturized raw coal and transport the pulverized coal ± air mixture to the boiler Poor dynamic performance of coal mill will lead to decrease in theModeling and Control of Coal MillDrying Capability: Vertical coal mills can simultaneously dry and grind wet coal, which is essential for maintaining the quality and flowability of the pulverized coal 4 Low Wear and Maintenance: The design of vertical mills reduces wear on grinding parts, leading to lower maintenance requirements and longer equipment lifeVertical coal milling for blast furnace pulverized coal injection
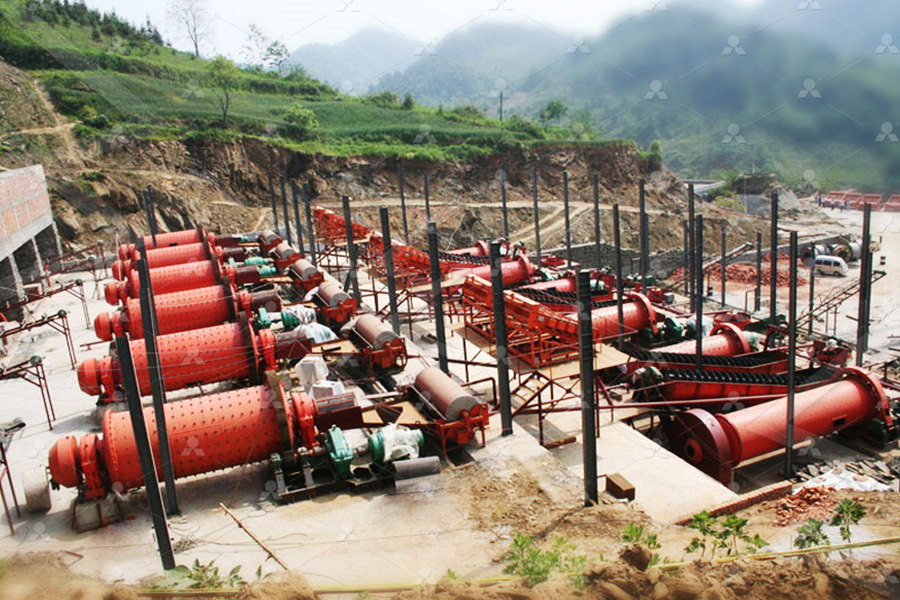
Coal Pulverising in Boilers
Niepce brothers of France were pioneers in pulverized coal firing This technology gained momentum after World War I in the power generating industry It was John Anderson, chief engineer of power plants at the Wisconsin Electric Power Company who introduced pulverized coal firing in power stations Pulverized coal is the most efficient way of 2023年5月19日 It is an important auxiliary equipment for pulverized coal furnace, rotary kiln and other kilns which need pulverized coal as fuel As its output can reach 570h/t, vertical coal mill is more suitable for medium and large pulverized coal projectsApplication of Vertical Coal Mill Great Wall1996年4月10日 New pulverized coalfired systems routinelyinstalled today generate power at net thermal cycle efficienciesranging from 34 to 37% (higher heating value) while removingup to 97% of the combined Developments in Pulverized CoalFired Boiler TechnologyProcess introduction Vertical coal mill, also known as vertical roller coal mill or vertical coal grinding mill, is a mechanical equipment for crushing and grinding coal into coal powerMainly used for grinding raw coal, bituminous coal, and other fuels into coal powder, which is supplied to rotary kiln and other kilns in the cement plant and thermal power plantcoal grinding machine CHAENG

Coal Mill an overview ScienceDirect Topics
A simple energy balance model of the coal mill is derived in (Odgaard and Mataji 2006), this model is based on a more detailed model found in (Rees and Fan 2003)In this model the coal mill is seen as one body with the mass m mThe following variables are defined: T(t) is the temperature in the coal dust flow in the mill, ṁ PA (t) is the primary air mass flow, T PA (t) is Pulverized coal storage is a critical aspect of various industrial processes that utilize coal as a primary fuel November 2023 Accept the probability that the fire and explosion safety of your coal grinding system is nothing more than a mirage Pulverized Coal Storage: Essential Practices and Considerations Coal 2020年5月11日 Optical measurement system for single pulverized coal particle ignition based on Hencken flat flame burner core, as shown in fig 1 The burner is mainly divided into three layers: a mixture of CO Ignition test for mechanically activated pulverized coal in a vertical 2014年10月1日 Request PDF Numerical and experimental analysis of pulverized coal mill classifier performance in the Soma B Power Plant Coal particle separation in a classifier after the pulverization Numerical and experimental analysis of pulverized coal mill
.jpg)
Pulverised Coal an overview ScienceDirect Topics
When coal is pulverized into a very fine powder, the combustion process is more efficient With a PCfired unit, the coal is first pulverized in a mill to the consistency of talcum powder, which means that at least 70% of the particles will pass through a 200mesh sievePRODUCT OVERVIEW LM series vertical mill is a new type of milling equipment with advanced technology, excellent performance and drying functionIt integrates the functions of drying, grinding and powder classifying,used in LM series vertical mill2009年9月20日 A control oriented model was then developed by Fan (1994) and Fan and Rees (1994) In 2009, coal flow and outlet temperature of mill were modelled using mass and heat balance equations for startup Modeling and Parameter Identification of Coal MillCoal Very highmoisture coal Very highmoisture coal Mill Total moisture in raw coal 55% 45, 50, 55% Inlet gas temperature 450°C up to 450°C Outlet gas temperature 75°C 67 to 75°C Outlet relative humidity 85% 47 to 94% Figure 3 shows the relationship between relative humidity and the drying ratio fraction of pulverized coalDevelopment of Millburner System for Lowrank Coal with Super
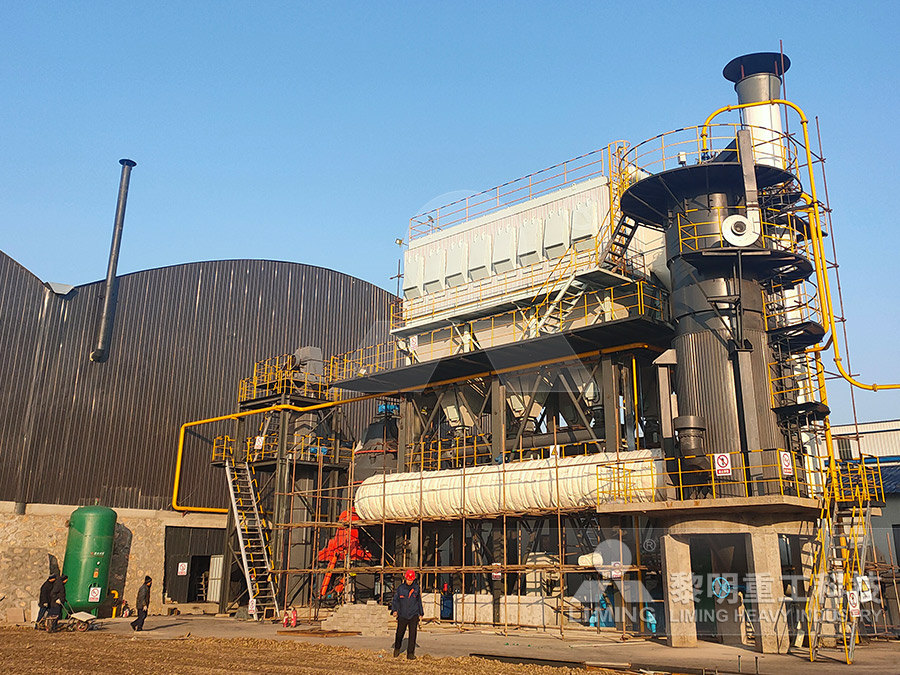
Pulverized Coal Injection Paul Wurth
• no pulverized coal buffer volume (Splitter type Distribution Device) Inward Transfer Hot blast backpressure as well as pressure drops in pneumatic conveying lines and flow rate control devices require a pressurizing of pulverized coal from atmosphere pressure level to overpressure level After pressurizing, pulverized coal is transferredSince the first application using an MPS mill to process pulverized coal in Germany in the mid 1960s, there have been over 2,000 different MPS mill installations operating in coalfired power plants worldwide As one of the most popular coal pulverizers in the utility industry, the MPS mill was first introduced into the US in the early 1970sCOAL PULVERIZER DESIGN UPGRADES TO MEET THE DEMANDS Vertical mill is widely used for pulverized coal preparation system in power plant, cement plant, metallurgy industry, chemical plant, etc It could be used to grind bituminite, meagre coal, and anthracite lignite with high moisture under some conditions Vertical mill adopts low speed, big roller diameter, high loading force designVertical mill for coal pulverizing in power plant Geckointech2014年1月1日 Two mill systems are employed for most coal grinding applications in the cement industry These are, on the one hand, vertical roller mills (VRM) that have achieved a share of almost 90% and, on (PDF) MPS mills for coal grinding ResearchGate
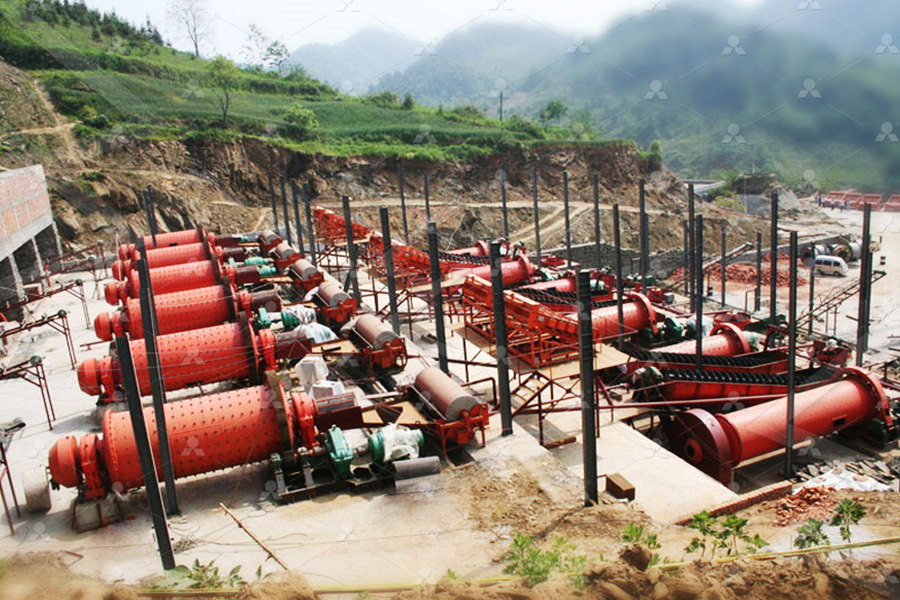
Understanding Pulverized Coal Injection in Blast Furnace
2018年10月21日 Fig 1 Pulverized coal combustion and gas composition in raceway The extent of combustion (combustion efficiency), and hence the amount of unburnt material transported out of the raceway, depends on several parameters which include (i) properties of the coal, such as the VM content, particle size and density, and (ii) operating conditions, for example, blast gas Collecting coal samples using an isokinetic probe provides the best data describing actual operating conditions inside the coal pipe Source: Storm Technologies Inc The isokinetic coal sampling method, although more difficult, is the best option for determining the true mill coal fineness produced and to calculate pulverizer performancePulverized Coal Pipe Testing and Balancing Storm Technologies, typically mill biomass and coal blends in a conventional vertical roller mill or mill each component separately in dedicated mills 11,12 It is possible to achieve a high biomass cofiring ratioMilling Characteristics of Coal and Torrefied Biomass Blends in a Raw coal used for making pulverized coal will inevitably encounter bituminous coal or lean coal with high ash content, low calorific value and impure composition At this time, if the grinding quality is not good, the efficiency of Coal Ball Mill Grinding for Different Kinds of
.jpg)
LM Vertical Roller Mill, Vertical Mill Manufacturer
Vertical roller mill is used to pulverize materials like limestone, coal, feldspar LM130M highefficiency pulverized coal production line has high efficiency and environmental protection, processes coal into highefficiency pulverized coal Vol 44 No 2 2011 1 Advanced Development of Pulverized Coal Firing Technologies TAMURA Masato : General Manager, Combustion Engineering Department, Power Plant Division, Energy Systems Operations WATANABE Shinji : Combustion Engineering Department, Power Plant Division, Energy Systems Operations OONO Emi : Manager, Combustion Engineering Advanced Development of Pulverized Coal Firing TechnologiesOperation of Vertical Coal Mills in Steel Plant Casting: The operation of a vertical coal mill in a steel plant casting process typically involves the following steps: 1 Feeding: Raw coal is fed into the mill from the top 2 Grinding: As the mill rotates, the coal is ground between the grinding roller and the grinding table 3 Drying: Hot Vertical coal mills in steel plant casting: Efficient pulverization for 2015年8月19日 Each of the two to eight mills feeds pulverized coal into two or more burner nozzles An online detection of the pulverizedcoal mass flow distribution among the burners is vital for the control The Characterization of PulverizedCoal Pneumatic Transport Using
.jpg)
Energysaving and Efficient Vertical Roller Mill Fote Machinery
A vertical roller mill, also known as a vertical grinding mill or vertical mill, is a comprehensive grinding equipment integrating crushing, drying, grinding, grading, and conveying Vertical grinding mills can be widely used in electric power, metallurgy, construction, chemical industry, and other industries to make powder, especially for materials such as cement clinker, coal Since the first application using an MPS mill to process pulverized coal in Germany in the mid 1960s, there have been over 2,000 different MPS mill installations operating in coalfired power plants worldwide As one of the most popular coal pulverizers in the utility industry, the MPS mill was first introduced into the US in the early 1970sCoal Pulverizer Design Upgrades to Meet the Demands of Low Coal is crushed to desired fineness between spheres or cylindrical rollers After that, air from the boiler is heated to around 330°C (650°F) The raw coal is then fed into the pulverizer where it is ground into fine coal particles What are the Advantages of Pulverized Coal? Pulverized coal produces a larger amount of heat than traditional coalCoal Crushers Coal Pulverizers Mills Williams Crusher2023年1月13日 The pulverized coal combustion process in power boilers is still being improved by the preliminary cleaning of coal and However, they can be more expensive to produce than metal oxide B Numerical study of the erosion process and transport of pulverized coal–air mixture in the millduct system Energies 2022, 15, 899 Pulverized CoalFired Boilers: Future Directions of Scientific