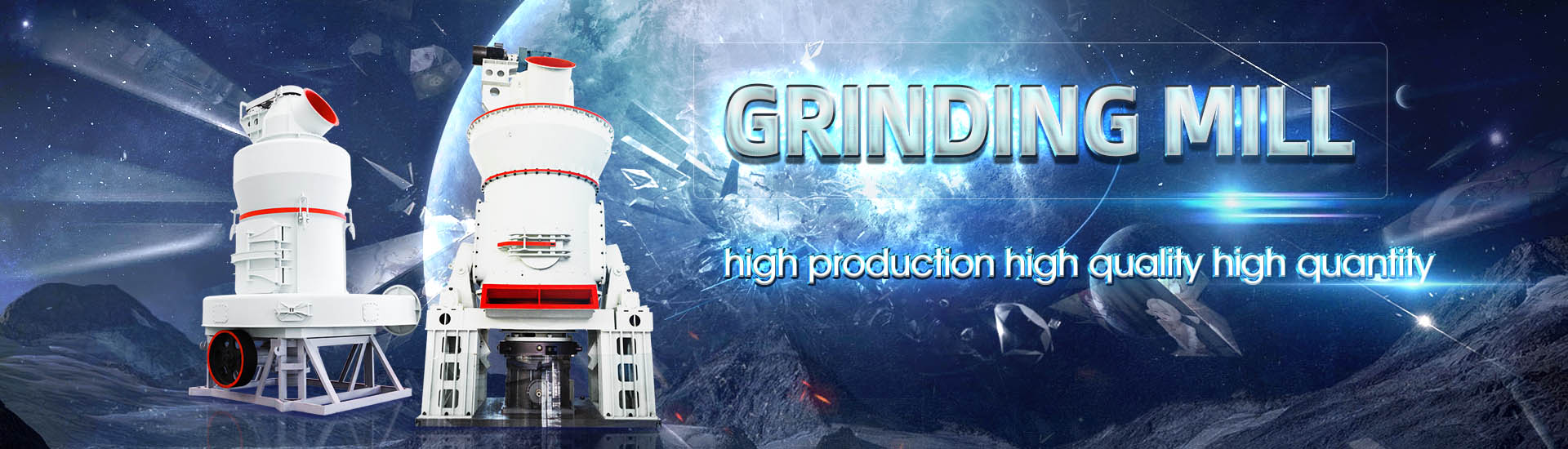
710TPH ore grinding mill 2 preparation processing
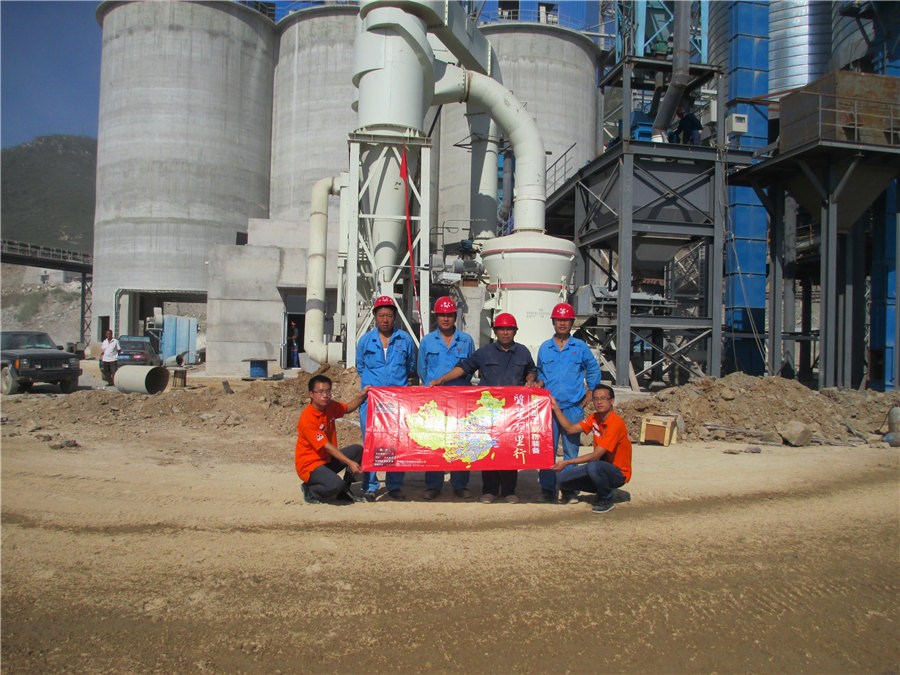
Ore Grinding SpringerLink
2023年7月20日 Moist grinding, a special grinding method, is used to prepare pellets for smelting According to the grinding medium features, ore grinding is mainly classified into ball grinding Wet semiselfgrinding mills of WSGM type (Fig 2) are used, mainly, in the first stage of grinding in a twostage mode The use of large mills allows to exclude the stages of medium and fine Reengineering of the ore preparation production process in the operation (1) Structure parameters of grinding mill, including its specifications, model, aspect ratio, ore discharging method, and liner form (2) Various working parameters of grinding mill, Ore Grinding Methods and Process of Ore Grinding2019年4月12日 Based on the current research results and industrial data, this paper compares the process flow of highpressure roller mill in metal mine and pellet pretreatment industry, as 高压辊磨机在金属矿选矿与球团预处理领域的工艺和
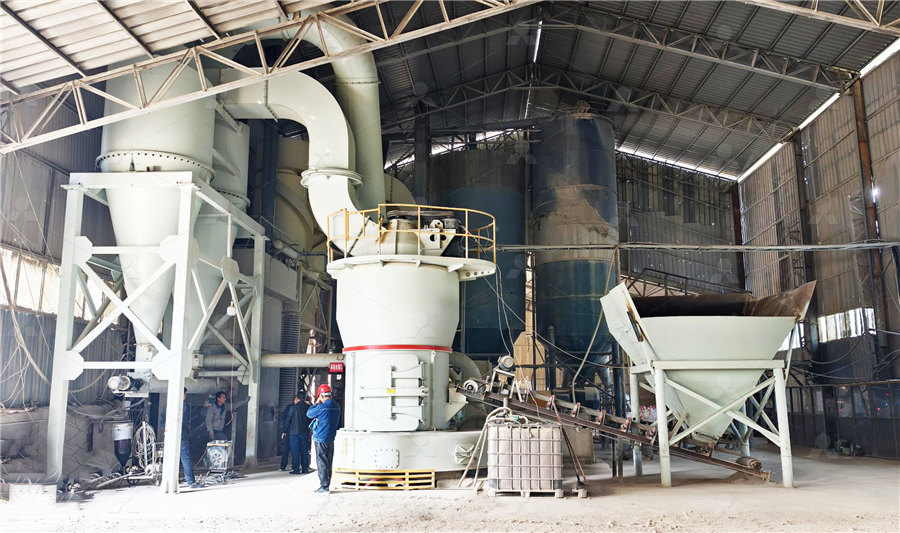
Modern Systems of Automatic Control of Processes of Grinding
2013年1月1日 Automatic process control grinding uses the principle of maintaining a rational level of loading of the drum mill ore and balls While the system is operating, energy and 2017年9月1日 The objective of this work is to assess the influence of fine grinding in ball mills and stirred mills on valuable mineral liberation and particle shape characteristics of UG2 ore, a Fine grinding: How mill type affects particle shape characteristics ore before feeding to milling cycle is a promising area of activity, which sometimes enables enhanced ore pretreatment efficiency at operating processing plants Owing to reduced grain ORE PRETREATMENT REENGINEERING AT OPERATING This paper details the operation of the ultra fine grinding process at KCGM as a non oxidative treatment for the extraction of gold from a refractory ores The refractory nature of gold ores is Ultra Fine Grinding A Practical Alternative to Oxidative Treatment
.jpg)
Development of ore sorting and its impact on mineral processing
2014年10月15日 Runofmine molybdenum ore was sorted using a dual energy Xray transmission array Sorting thresholds permit optimization of Mo recovery and waste rejection 2013年12月18日 Fine grinding, to P80 sizes as low as 7 μ m, is becoming increasingly important as mines treat ores with smaller liberation sizes This grinding is typically done using stirred Energy Use of Fine Grinding in Mineral ProcessingMedia Attributions; Metal deposits are mined in a variety of different ways depending on their depth, shape, size and grade Relatively large deposits that are quite close to surface and somewhat regular in shape are mined using 82: Mining and Ore Processing Geosciences LibreTextsoperation (1) Structure parameters of grinding mill, including its specifications, model, aspect ratio, ore discharging method, and liner form (2) Various working parameters of grinding mill, including fraction of critical speed for grinding mill, filling rate for grinding mill, grinding concentration,grindingcycleload,etc(3)AndgrindOre Grinding Methods and Process of Ore Grinding
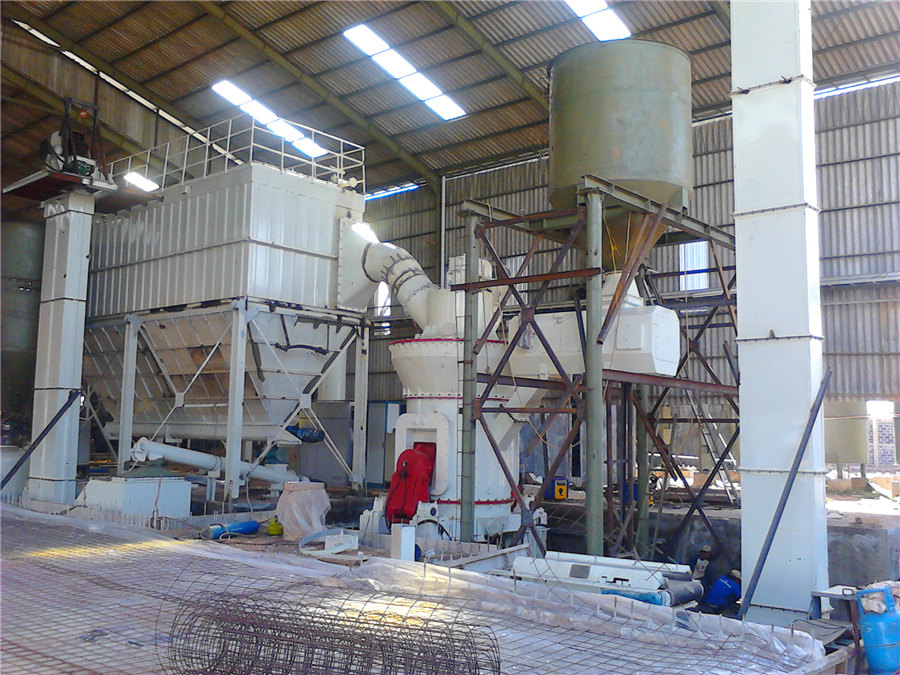
A Review of the Grinding Media in Ball Mills for
2023年10月27日 The ball mill is a rotating cylindrical vessel with grinding media inside, which is responsible for breaking the ore particles Grinding media play an important role in the comminution of mineral When iron ore is extracted from a mine, it must undergo several processing stages Six steps to process iron ore 1 Screening We recommend that you begin by screening the iron ore to separate fine particles below the crusher’s CSS before the crushing stageThe six main steps of iron ore processing MultotecYGM Industrial Raymond Mill Discharge fineness: 80600 mesh Feed size: 35 mm Output: 0435 t/h Materials: Calcite, limestone, wollastonite, gypsum, potassium feldspar, kaolin, bentonite, barite, phosphate rock, manganese ore, quartz stone, marble and other materials with Mohs hardness below 7YGM Industrial Raymond Mill2015年8月3日 It is a process of ore preparation, The objective of this lesson is to provide the details of size reduction methods involved in mineral processing using grinding methods and equipmentOverview of Mineral Processing Methods ResearchGate
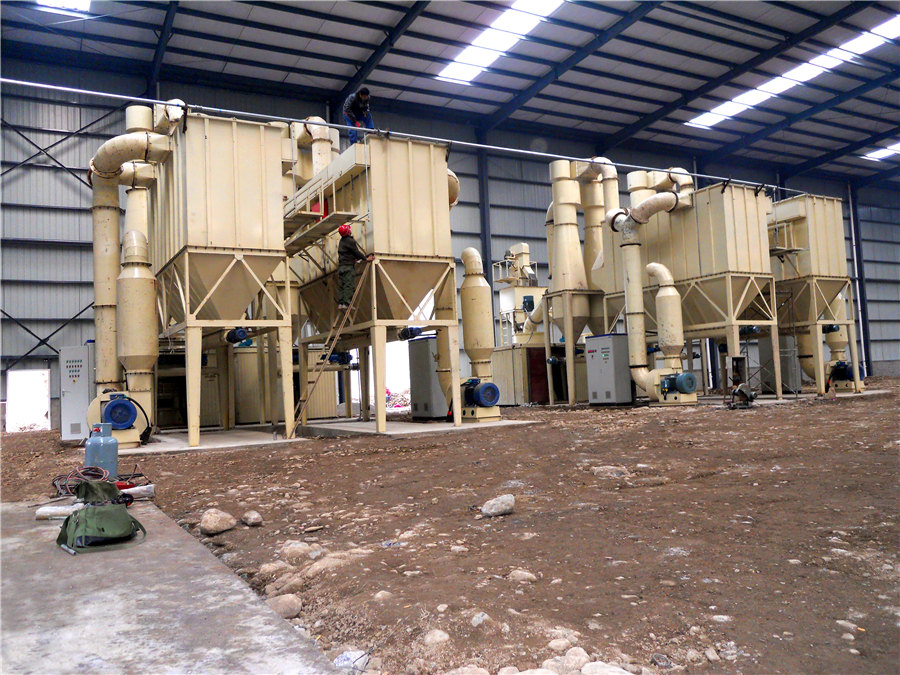
The effects of iron ore concentrate grinding methods (HPGR and
2020年10月18日 An iron ore concentrate sample was ground separately in a pilotscale HPGR mill in multiple passes and a dry opencircuit ball mill to increase the specific surface area of particles2012年6月1日 u 2 − fresh ore feed rate, u 3 − mill critical speed fraction, u 4 − sump dilution water flow rate and u 5 − sump discharge flow rate The va lues of these variables can beGrinding in Ball Mills: Modeling and Process Control2023年4月23日 grinding media in a grinding mill with about 2630 wt% chrome by Chen et al [37] using a phosphate ore in a modified ball laboratory ball mill whose electrochemical potential could be controlled(PDF) Grinding Media in Ball MillsA Review ResearchGate2009年1月1日 Site preparation and improvements 2 098 103 2 083 of rod and ball mill grinding during the multiple steps of ore processing or recycling 25 Classical separation technologies Processing of Magnetite Iron Ores–Comparing Grinding Options
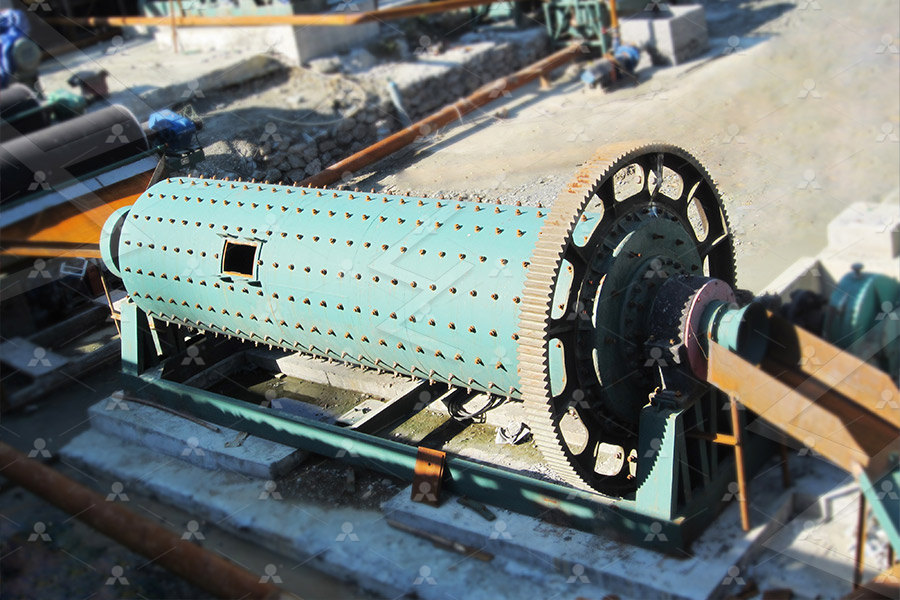
Gold processing 101 Mining Magazine
2017年9月7日 Metallurgical processing of metalliferous ores in general and gold ores in particular, consists essentially of three stages, often colloquially referred to as: Bashing (crushing); Mashing (grinding); and; Hashing (extraction/recovery) 1 Population balance model approach to ball mill optimization in iron ore grinding Patricia M C Faria1,2, Luís Marcelo Tavares2 and Raj K Rajamani3 1 Vale SA, Brazil 2 Department of Population balance model approach to ball mill optimization in iron ore The performance of grinding mills depends on many operating factors among which are the time of grinding, mill speed, grinding media–toore ratio, 00 7 00 PROCESSING OF MAGNETITE IRON ORES process plant 200 913 722 208 392 675 188 588 092 186 240 895 Site preparation and improvements 2 098 103 2 083 927 1 885 881 1 862 409 Processing of Magnetite Iron Ores–Comparing Grinding Options2018年8月8日 One of the most effective methods of grinding Portland cement is the use of an electromagnetic mill, which has proven its advantage in creating clinkerless binders [2], regulating the kinetics of (PDF) Grinding Kinetics Adjustment of Copper Ore Grinding in

Energy Use of Fine Grinding in Mineral Processing
2013年3月1日 Request PDF Energy Use of Fine Grinding in Mineral Processing Fine grinding, to P80 sizes as low as 7 μm, is becoming increasingly important as mines treat ores with smaller liberation sizesOur Wet Pan Mill Roller Material: 6% manganese alloy steel, which can last at least 3 years Ring Material: Optional casting steel, casting iron, and manganese steel Thickness: Standard 85mm Steel Steel stand: A2 standard steel frame Basin: 5mm thickness steel plate Gearbox: Specially designed for wet pan mill, 1year quality guarantee Motor: Simens or China 1st level standard Wet Pan Mill JXSC Mineral• 2 x 60”x89” Svedala 750 kW Primary Gyratory Crushers • A 61 km Overland Conveyor discharging ore to a 360,000 tonnes Mill Coarse Ore Stockpile • 2 x 36’ x 19’ ABB Svedala Gearless Motor Drive 134MW SAG Mills • 4 x 20’ x 335’ Svedala 7,400 kW Ball Mills • 4 x MP1000 750 kW Pebble CrushersBATU HIJAU MILL THROUGHPUT OPTIMIZATION: MILLING CIRCUIT CONFIGURATION 910 A Abazarpoor, M Halali Materials and methods Sample preparation The iron ore concentrate was obtained from GolEGohar line 5 plant, South East of Iran The concentrate was taken from the Investigation on the particle size and shape of iron ore pellet feed
.jpg)
Case Study of Dry HPGR Grinding and Classification in Ore Processing
2019年2月5日 Comparative grinding tests of twostage closed HPGR with 7 mm and 1 mm screens and a final mill grind, and twostage closed HPGR with a 7 mm screen and an air classifier cutting for final product JXSC design 10TPH Rock Coltan Ore Processing Plant for valued Mozambique customer, and provide the complete mineral processing machine Find here more mining cases and solutions Gold Mining Equipment Chat on WhatsApp; 10TPH Rock Coltan Ore Processing Plant in PDF On Nov 1, 2018, Frank Peter van der Meer and others published Aspects of HPGR in Iron Ore Pellet Feed Preparation Find, read and cite all the research you need on ResearchGateAspects of HPGR in Iron Ore Pellet Feed Preparation2018年12月24日 EVALUATION OF THE ALTERNATIVES FOR GOLD ORE GRINDING CIRCUITS BY USING OF 2112 Sample preparation and optimal operating conditions of a ball mill in a copper processing EVALUATION OF THE ALTERNATIVES FOR GOLD ORE
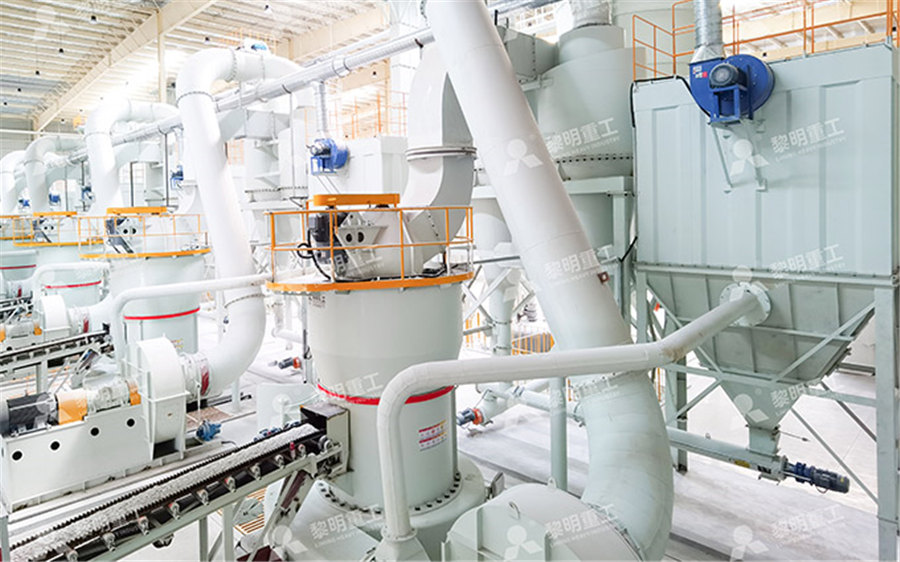
Iron Ore Processing, General SpringerLink
2022年10月20日 Iron ore handling, which may account for 20–50% of the total delivered cost of raw materials, covers the processes of transportation, storage, feeding, and washing of the ore en route to or during its various stages of treatment in the mill Since the physical state of iron ores in situ may range from friable, or even sandy materials, to monolithic deposits with hardness of Impactors are often primaryreduction machines for rock and ore, processing up to 600 ton/h They give particles that are more nearly equidimensional admitted through nozzles at a pressure of 7 atm In the mill the grinding chamber is an oval loop of pipe 25 to 200 mm in diameter and 12 to 24 m highSize Reduction1: Grinding – Unit Operations in Food Processing2018年6月18日 Ore pretreatment methods for grinding: journey and prospects, Mineral Processing and Extractive Metallurgy Review, DOI: 101080/2018 To link to this article: https://doior g/10 Ore Pretreatment Methods for Grinding: Journey and ProspectsCLUM series of ultrafine gypsum powder vertical grinding mills are a new type of ultrafine industrial ore grinding equipment that integrates grinding, grading, powder collection and conveying +17CLUM Ultrafine Vertical Grinding Mill
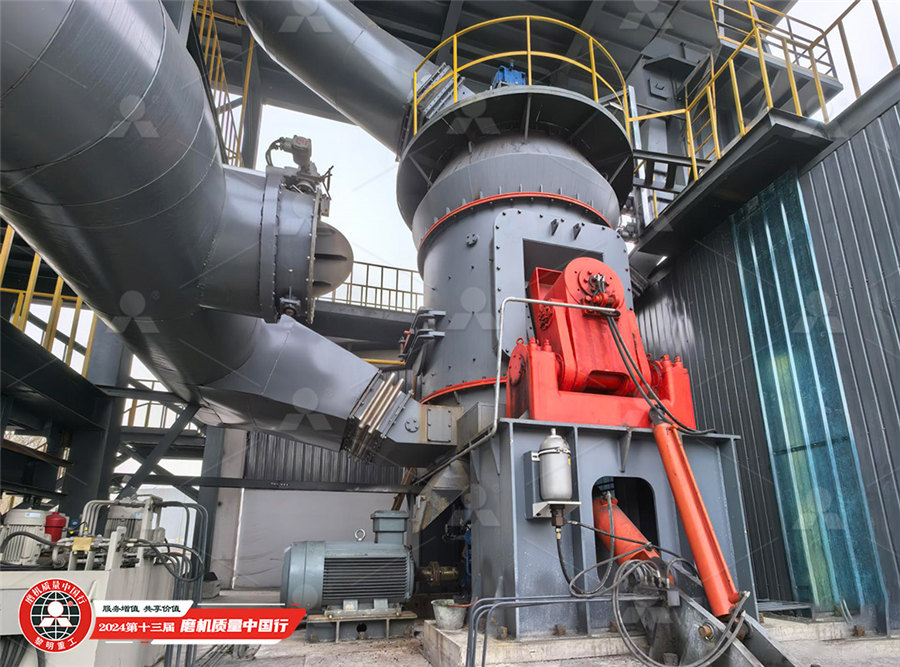
Grinding Mills 911Metallurgist
Grinding Mills: Ball Mill Rod Mill Design PartsCommon types of grinding mills include Ball Mills and Rod Mills This includes all rotating mills with heavy grinding media loads This article focuses on ball and rod mills excluding SAG and AG mills Although their concepts are very similar, they are not discussed herePhotographs of a glass ended laboratory ball mill show 2017年1月1日 In this investigation, we optimize the grinding circuit of a typical chromite beneficiation plant in India The runofmine ore is reduced to a particle size of less than 1 mm in the comminution Performance optimization of an industrial ball mill for chromite processing2024年6月7日 Some of the best grinding mills for achieving fine particle sizes in ore processing include: Ball Mills: Ball mills are commonly used in ore processing for grinding materials into very fine powdersOptimal Grinding Mills for Fine Ore ProcessingThe screen oversize recirculates to the mill and the undersize feeds to secondary grinding in a ball mill The Nabralek mill in Queensland fed runofmine (ROM) ore directly to a grinding circuit consisting of a wet semiautogenous mill followed by a conventional ball mill 44 PART II PROCESSING TECHNOLOGY 4243 Dry semiautogenous grindingCRUSHING AND GRINDING 1 Introduction ORE PREPARATION
.jpg)
Gold Ore Beneficiation 10tph Cil Gold Extraction
Type: 380V or Customized Motor Type: AC Motor Motor Power: 15kw Application: Mine Materials: Limestone Outlet Size: 1848mmmineral processing, art of treating crude ores and mineral products in order to separate the valuable minerals from the waste rock, or gangue It is the first process that most ores undergo after mining in order to provide a more Mineral processing Metallurgy, Crushing Grinding 2017年3月20日 Physicochemical Problems of Mineral Processing Investigation on the particle size and shape of iron ore pellet feed using ball mill and HPGR grinding methods March 2017 DOI: 105277/ppmpPhysicochemical Problems of Mineral Processing Investigation In the 1950s, many iron ore and nonferrous metal mineral processing plants were built, eg, the iron ore and nonferrous metal mineral processing plants in Anshan and Benxi, Liaoning, the tin mineral processing plant in Gejiu, Yunnan, the copper mineral processing plant in Baiyin, Gansu, and the tungsten ore mineral processing plants in Jiangxi represented by the mines at Daji Mineral Processing SpringerLink
.jpg)
Grind Optimization of Konkola Blended Copper Ore
2020年8月1日 4mm sieved sample ores crushed and weighed (1000g) 24 Grinding The laboratory pebble mill with a diameter of 180mm and depth of 240mm was charged with fifteen 8mm steel balls, 1000grams ore, 1 litre water, closed and operated at 210 rpm as recommended by the senior metallurgist2019年8月16日 Mining, mineral processing and metal extraction are undergoing a profound transformation as a result of two revolutions in the making—one, advances in digital technologies and the other, availability of electricity from renewable energy sources at affordable prices The demand for new metals and materials has also arisen concurrently This necessitates Future of Mining, Mineral Processing and Metal Extraction Industry2022年8月31日 Dear Colleagues, The grinding process, as a primary stage of ore/raw material processing, is a necessary operation in beneficiation plants It not only provides the appropriate particle size for subsequent separation operations but also enables the liberation of valuable minerals from the gangueGrinding Modeling and Energy Efficiency in Ore/Raw Material The following is the working process of the dolomite mill 1 Crushing: The primary dolomite ore is crushed into smaller particles by crushing equipment such as jaw crushers or hammer crushers This step is to reduce the particle size of the ore in preparation for Dolomite Micro Powder Grinding Mill
.jpg)
(PDF) Optimization of inmill ball loading and slurry solids
2012年12月1日 Optimization of inmill ball loading and slurry solids concentration in grinding of UG2 ores: A statistical experimental design approach December 2012 Minerals Engineering 39:149155