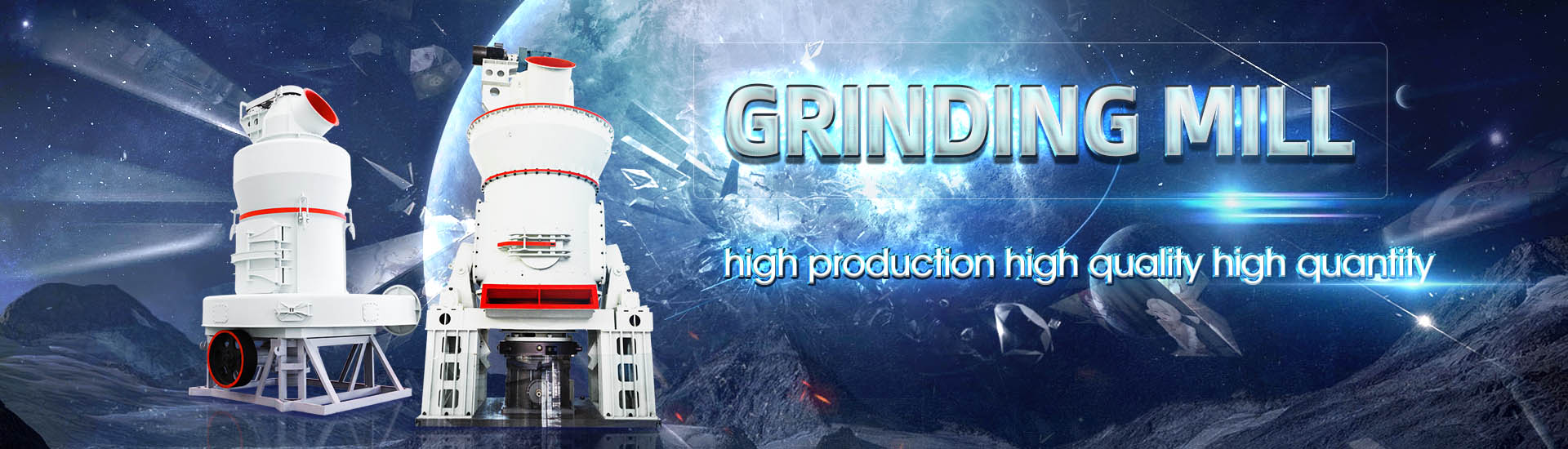
Production capacity 355th raw meal vertical mill

Grinding Process Optimization Featuring Case Studies and
Kiln capacities in the cement industry have now reached clinker production rates of up to 12,000 t/d This requires mills for the production of up to 1,000 t/h raw meal Lowest investmentvertical roller grinding mills for grinding: • Coal • Cement raw material • Clinker / granulated slag • Industrial minerals, and • Ores The core elements of these plants are the Loesche vertical PROCESS OPTIMISATION FOR LOESCHE GRINDING PLANTSBased on these investigations Loesche GmbH has developed a mill for producing raw meal that has an arrangement of six rollers on the grinding table This mill, designated the LM 606 has a Redundancy and interchangeability – large vertical roller mills for 2021年1月1日 Vertical roller mill has proved to be a popular choice for finished cement grinding over all other machineries due to advantages like low power consumption, higher capacity, Review on vertical roller mill in cement industry its performance

Operational parameters affecting the vertical roller mill
2017年4月1日 Vertical roller mills (VRM) have found applications mostly in cement grinding operations where they were used in raw meal and finish grinding stages and in power plants Vertical roller mills are adopted in 20 cement plants (44 mills) in Japan In the vertical roller mill which is widely used in the raw material grinding process, raw materials input grinding table Vertical roller mill for raw Application p rocess materials2010年11月1日 The trend in the cement industry is towards ever increasing kiln capacities that have now reached clinker outputs of up to 12000 t/d This requires mills that are capable of The new pfeiffer MVRR vertical roller mill for producing raw meal2015年4月1日 In this study, production capacity of a fully airswept dry grinding raw meal ball mill circuit was evaluated by modelling the mill using the perfect mixing modelling approach ( Optimization of a fully airswept dry grinding cement raw meal
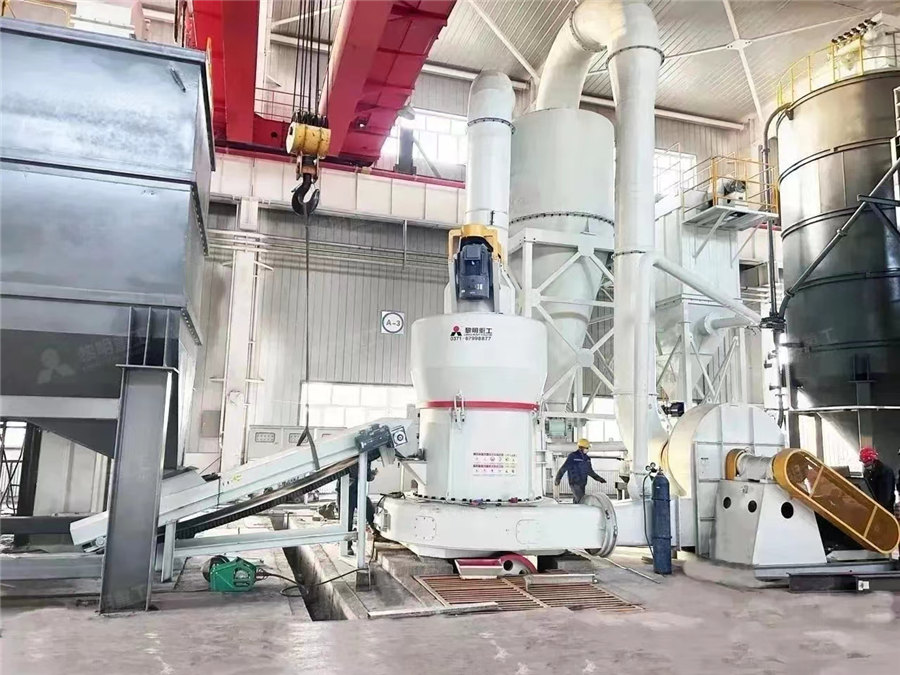
Analysis and Optimization of Grinding Performance of Vertical
2022年1月23日 There are usually four kinds of VRMs in the cement production line, including raw meal mill, coal mill, Clinker Mill and cement mill, and the vertical mill occupies a large FLENDER GEAR UNITS VERTICAL MILL GEAR UNITS PRECISION LANDING DIRECTLY IN THE RAW MEAL In the capacity range of up to 2,000 kW for pregrinding, our KMPS gear 7,000,000 KILOWATTS OF INSTALLED EXPERTISE FlenderThe OK™ Mill is offered in a complete size range, including 3, 4 and 6roller mills, and the largest vertical roller mill size available with installed power over 11 500 kilowatts This ensures the ability to meet all possible capacity OK™ Raw and Cement MillBuy vertical raw mill for raw materials grinding In the process of cement production in cement plant, cement raw meal needs to be ground by grinding equipment before calcination Capacity(t/h) Motor Power(kW) Rotate Vertical Raw Mill for Cement Raw Meal Grinding in
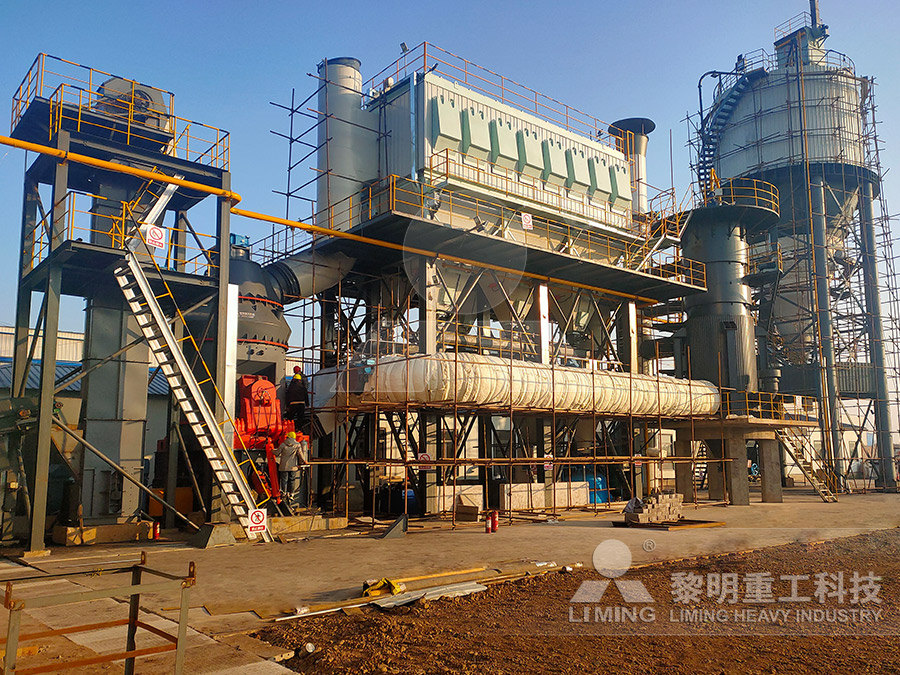
Optimization of A Fully AirSwept Dry Grinding Cement Raw Meal
Optimization of a Fully Airswept Dry Grinding Cement Raw Meal Ball Mill Closed Circuit Capacity With the Aid Free download as PDF File (pdf), Text File (txt) or read online for free This document discusses optimizing the production capacity of a fully airswept industrial scale twocompartment cement ball mill through simulation The mill has two compartments, with the first 2022年1月23日 This work concentrates on the energy consumption and grinding energy efficiency of a laboratory vertical roller mill (VRM) under various operating parameters For design of experiments (DOE), the response surface method (RSM) was employed with the VRM experiments to systematically investigate the influence of operating parameters on the energy Analysis and Optimization of Grinding Performance of Vertical 2021年1月1日 There are 210 large cement plants having total capacity of 410 MT cement production, With the grinding capacity of a vertical roller mill and the ability to dry, Optimization of a fully airswept dry grinding cement raw meal ball mill closed circuit capacity with the aid of simulationReview on vertical roller mill in cement industry its The mill is equipped with a water injection system The finish raw meal is separated by a cyclonesystem which removes more than 90 % of the dust raw meal The rest of the raw meal is separated in theGrinding Process Optimization Featuring Case Studies and
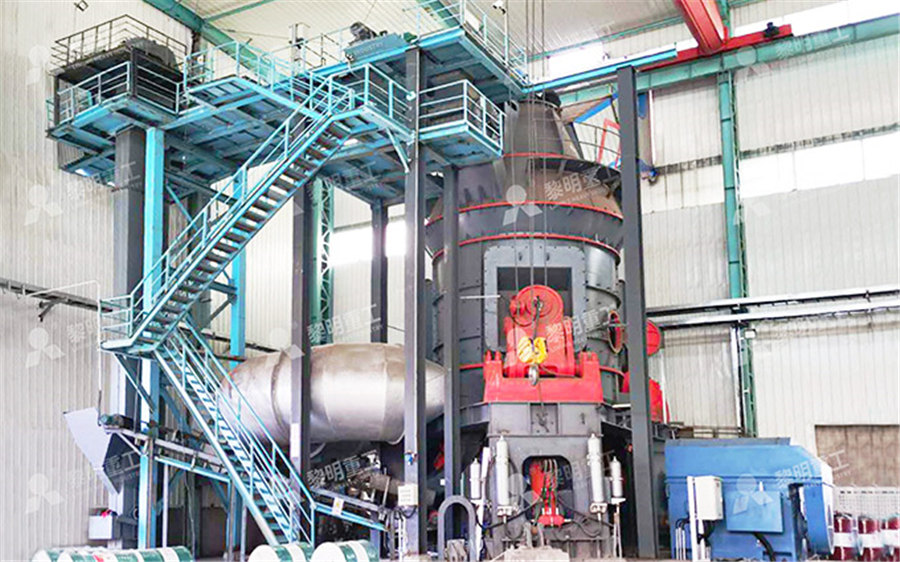
Energysaving and Efficient Vertical Roller Mill Fote Machinery
A vertical roller mill is an energysaving mill that meets market demand Raw materials: Slag, steel slag, blast furnace slag, metallurgical waste slag, ceramic waste, etc Slag moisture: ≤15% Finished product moisture: ≤1% c Production capacity: Production Capacity Zhongya Building Material Equipment is a rapidly growing company, 5 HRM Series for full Equipment and Parts: Raw Meal Vertical Mill, Mining Slag Micropower Vertical Mill, Cement Vertical Mill, Fine Roller Mill More Less Factory Address: 61 Fozhang Rd Vertical Mill Manufacturer, Raw Mill, Hrm Vertical Mill Supplier 2022年1月23日 There are usually four kinds of VRMs in the cement production line, including raw meal mill, coal mill, Roy, GR Increasing cement grinding capacity with vertical roller mill technologyAnalysis and Optimization of Grinding Performance of Vertical Mill production is determined by the grinding power available and feed grindability, but for high moisture feed, the system drying capacity may bethe limitingfactorTypically,thetarget moisturelevel exmill is below one per cent to assure good flowability of Raw milling and blending INFINITY FOR CEMENT EQUIPMENT
.jpg)
Optimization of a fully airswept dry grinding cement raw meal
2015年4月1日 In this study, production capacity of a fully airswept dry grinding raw meal ball mill circuit was evaluated by modelling the mill using the perfect mixing modelling approach (Whiten, 1972) Static separator in the circuit was modelled by efficiency curve model ( If the air volume of the system is too small, the thickness of the material layer, the pressure difference in the mill, and the current of the main motor will increase, and so will the vibration speed of the mill 6 The Hot Gas from the Kiln In the Vertical Roller Mill Operation in Cement Plant2022年10月3日 PDF Raw materials grinding process is a first step of cement production which is has an important role in the first grinding step Vertical Raw Mill Find, read and cite all the research you (PDF) ANALISA KINERJA ALAT VERTICAL RAW MILL PABRIK II PT Table 3 Power Consumption Of Roller Press Grinding System Overall, we can conclude the three tables: After the longterm operation, although unit raw material grinding power consumption of the cement roller press grinding system is still low, the indexes of the vertical roller mill grinding system are very close to it, among which the output power of the vertical mill and the roller Comparison Of Vertical Roller Mill And Roller Press Mill
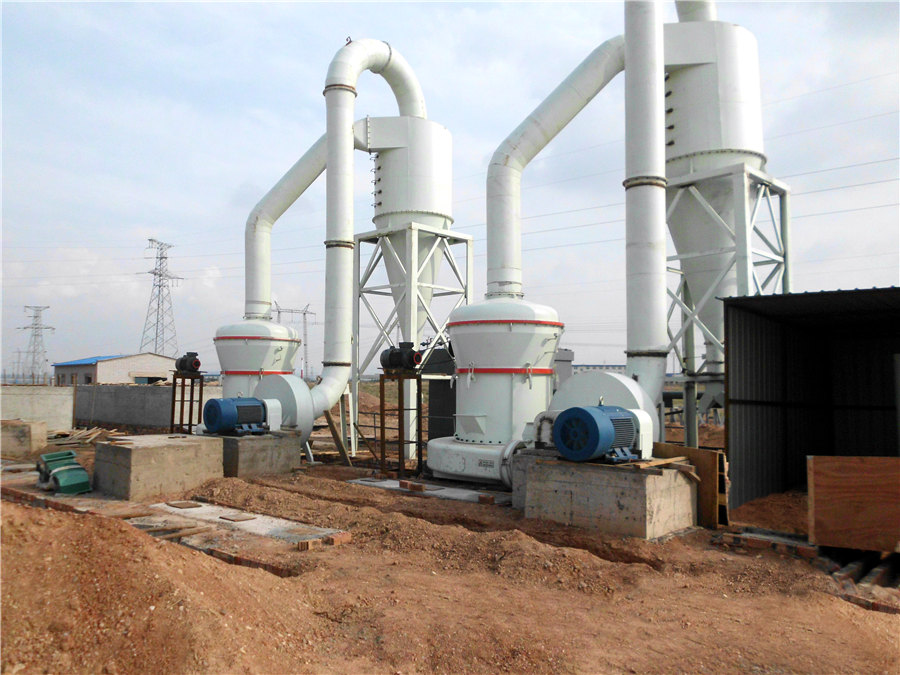
Vertical Roller Mill and Vertical Grinding Mill MadeinChina
2023年11月16日 Vertical Roller Mill, Production Capacity: 200: Payment Terms: L/C, T/T: Contact Now Product Description Company Info chemical and nonmetal mineral for the grinding of cement raw meal, clinker, mining slag, steel slag, coal, gypsum, calcite, pyrophyllite, quartz and limestone powder for sulfur treatment in power plant, etcAdaptive Dynamic Programming in Raw Meal Fineness Control of Vertical Mill Grinding Process Based on Extreme Learning Machine Xiaofeng Lin Guangxi University, Nanning , China; Against the problem, a production index prediction model of vertical mill raw meal grinding process was established using Extreme Learning Machine (ELM)Adaptive Dynamic Programming in Raw Meal Fineness Control of Vertical HLM vertical grinding mill and vertical roller mill is a highefficiency energysaving advanced pulverizing equipment integrating drying, pulverizing, grading and conveying, which has been researched and developed by Guilin Hongcheng Company for more than 20 years Hongcheng HLM vertical grinding mill has the advantages of high grinding efficiency, low power HLM Vertical Grinding Mill Vertical Roller MillA mediumsized dry process roller mill A raw mill is the equipment used to grind raw materials into "rawmix" during the manufacture of cement Rawmix is then fed to a cement kiln, which transforms it into clinker, which is then ground to make cement in the cement millThe raw milling stage of the process effectively defines the chemistry (and therefore physical properties) of the Rawmill Wikipedia
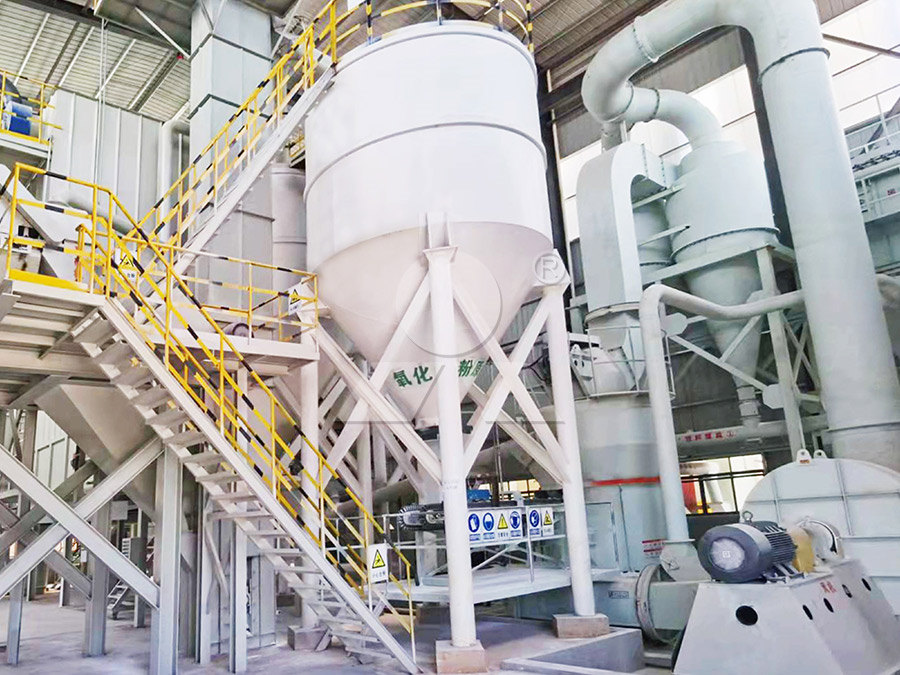
Trials on high quality cement with a Loesche vertical roller mill
2011年3月1日 Loesche GmbH from Düsseldorf supplied the grinding plants for producing raw meal and pulverized fuel as well as two LM 533+3 CS vertical roller mills for grinding the cement for the new cement this concept should ensure that 100 % raw meal capacity is available even when a mill is operating with only four rollers This treatment is also being applied to the grinding of cement clinker and granulated blastfurnace slag Even greater grinding capacities will come into operation in India and the United Arab Emirates in 2008 with LM 696 Redundancy and interchangeability – large vertical roller mills For drying the wet raw material it is necessary that prior to the mill start up the grinding plant isheated for some timeOtherwise the cold grinding plant would take away too much heat from the drying process and the finish product would PROCESS TRAINING for operators of Vertical RAW MillsAGICO vertical roller mills can be used as cement mills, raw mills, and slag mills AGICO also supplies vertical roller mill components and parts, we can customize machines according to customers’ needs Vertical roller mills (VRM) are a type Vertical Roller Mill for Sale AGICO Cement Plant
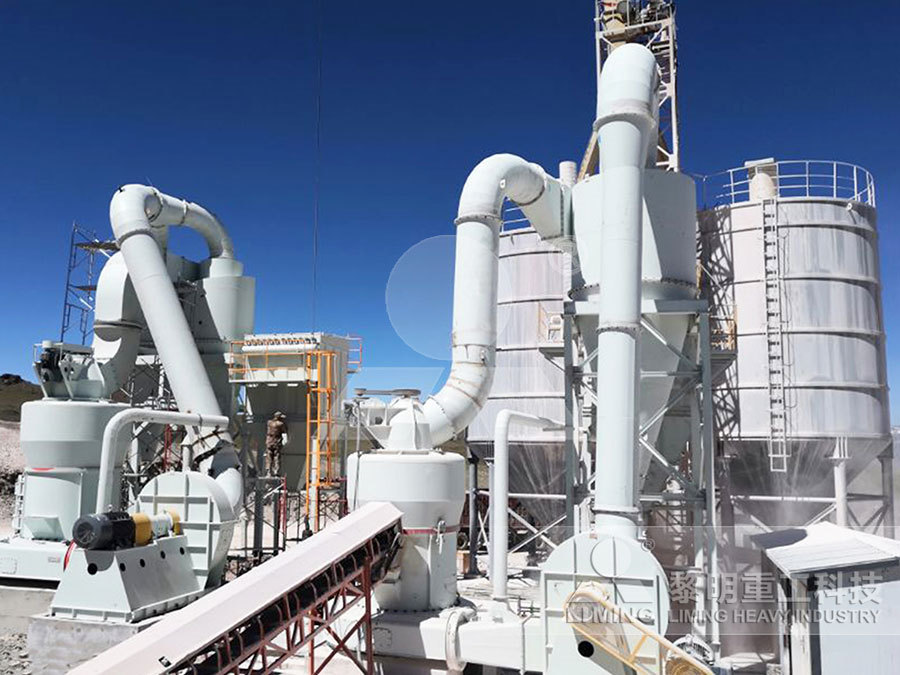
Application of Vertical Roller Mill in Cement Production
Raw Meal Grinding In the raw meal grinding process, VRMs are used to grind the raw materials used in cement production, such as limestone, clay, and silica After being crushed and processed in crushers,the raw materials are fed into the Cement Vertical roller mill (VRM) is mainly used to grind cement clinker into fine powder during cement production This vertical cement mill is widely used in the grinding of cement raw meal, cement clinker, slag, raw coal and other raw materialsVertical Cement Mill Great WallVertical Raw Mill is a main equipment that is used in grinding or refining raw materials at PT Semen Baturaja (Persero) Tbk using a tire roller that can produce raw meal with theANALISA KINERJA ALAT VERTICAL RAW MILL PABRIK II PTPart Three: Raw Mill Process of Raw Mill The proportioned raw material is feed first to a grinding mill In the mill, particles ground in to very fine sizes In the grinding unit, drying, grinding and mixing takes place simultaneously Hot gas from clinker burning unit is passed into the grinding unit to assist the drying and grinding processCement Manufacturing Process INFINITY FOR CEMENT EQUIPMENT
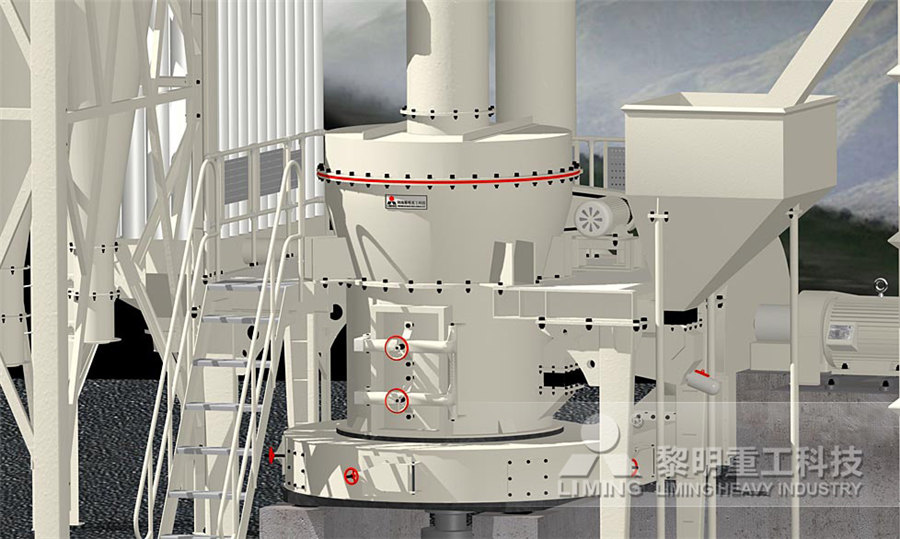
OPTIMASI INTERLOCKING MAIN MOTOR VERTICAL RAW MILL
In carrying out the production process continuously, various things will arise during the production process that can lead to downtime and result in production losses Vertical Raw Mill is equipment for producing raw meal (the basic product for making clinkers) with a production capacity of 420 tons / hour2014年9月3日 For cement raw meal grinding system, Xueyun et al (2013) achieved indirect measurement by establishing a soft sensor model of the material thickness based on the method of least squares support Modeling of vertical mill raw meal grinding process and optimal 2010年11月1日 The new MVR vertical roller mill for grinding cement raw material, cement and granulated blast furnace slag has a modular design, which enables operation to be continued even if one roller module The new pfeiffer MVRR vertical roller mill for producing raw meal The LM Vertical Grinding Mill, launched by SMMVIK Machinery, integrates five functions of crushing, PRODUCTION CAPACITY: Up to 128TPH(ore mill), up to 50TPH (coal mill) Meal to separate returns after a concentrated mill, fine powder was collected in LM Vertical Grinding Mill SMMVIK Machinery
.jpg)
Raw material mill Great Wall
Raw material ball mill, also called raw meal ball mill, is important grinding equipment in cement production process After being crushed, the raw meal enters the raw material mill The raw meal is grinded into fine powder by the Whether grinding raw coal, clinker, cement and/or slag, we have a VRM solution to suit your grinding needs What’s more, our online condition monitoring services enable you to adopt a proactive maintenance strategy for your OK™ and Vertical roller mills FLSmidth CementAbstract: Based on the analysis of the process of cement raw meal vertical milling system, this paper points out the key control output in the process, the mill vibration, and designs a controller to control it by iterative learning and modelfree adaptive control methods Firstly, the PPD state observer is designed for dynamic linearization, and the controller design is based on the MFAC ModelFree Adaptive Controller Design Based on Data IEEE 2020年12月29日 The details, raw meal production was not achieved, This target is set based on normal production capacity (Vertical Raw mill), Equipment 531WF04 (Clay Weigh Plant Maintenance Modelling Through Availability Analysis In Raw Mill
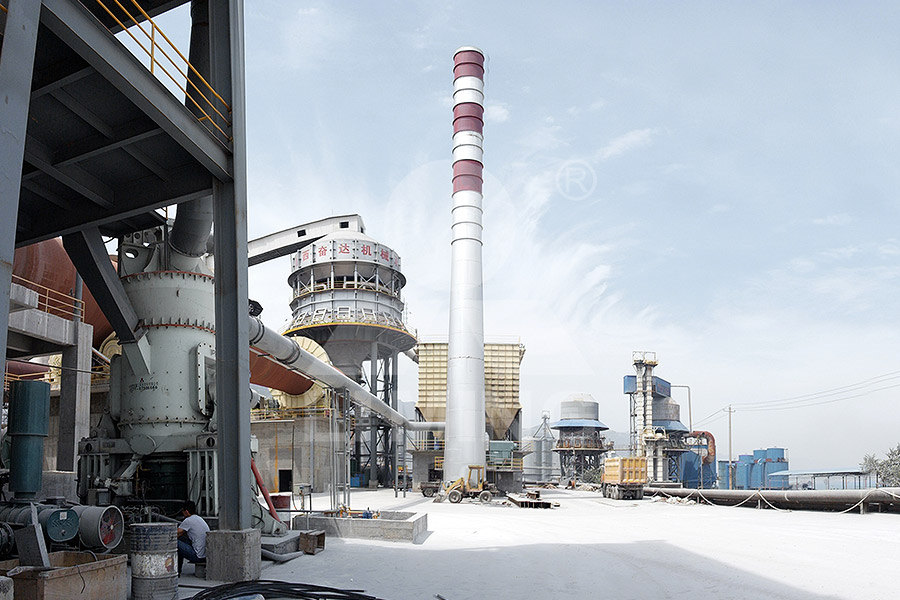
Evaluasi Kinerja alat Vertical Raw Mill Melalui Perhitungan Neraca
2021年7月27日 Raw materials grinding process is a first step of cement production which is has an important role in the first grinding step Vertical Raw Mill is a main equipment that is used in grinding or 2024年2月23日 The operation of the cement raw mill is a critical step in cement production By grinding the raw materials into a fine powder, these powders can be more easily mixed with other cement ingredients and burn more evenly during the cement clinker process Therefore, the efficient operation of the cement raw mill directly impacts the production efficiency and quality How Does a Raw Mill Work in a Cement IndustryThe present study is aiming to develop a simulator of the mixing process in production installations of raw meal comprising all the main characteristics of the process and raw materialsFlow chart of raw meal production Download Scientific Diagram(LOESCHE mill) e raw vertical roller mill has four rollers, 3000 KW main drive, 48 m table diameter, 216 m roller diameter with 330 t/h capacity (made by LOESCHE Company from Germany) e table Modeling of energy consumption factors for an industrial cement
.jpg)
EnergyEfficient Technologies in Cement Grinding IntechOpen
2015年10月23日 In this chapter an introduction of widely applied energyefficient grinding technologies in cement grinding and description of the operating principles of the related equipments and comparisons over each other in terms of grinding efficiency, specific energy consumption, production capacity and cement quality are given A case study performed on a 2023年3月1日 β [1 − α; p 2; n − p − 1 2] = (1–α) th quantile of β [p 2; n − p − 1 2] distribution For α = 005, the number of outliers is 44 among 280 data corresponding to an upper limit control U C L M a h a l a n o b i s = 455 as illustrated in Fig 3The results of these outliers have been carefully analyzed by a process expert from the cement plant Indeed, if an outlier carrying Efficient machine learning model to predict fineness, in a vertical raw