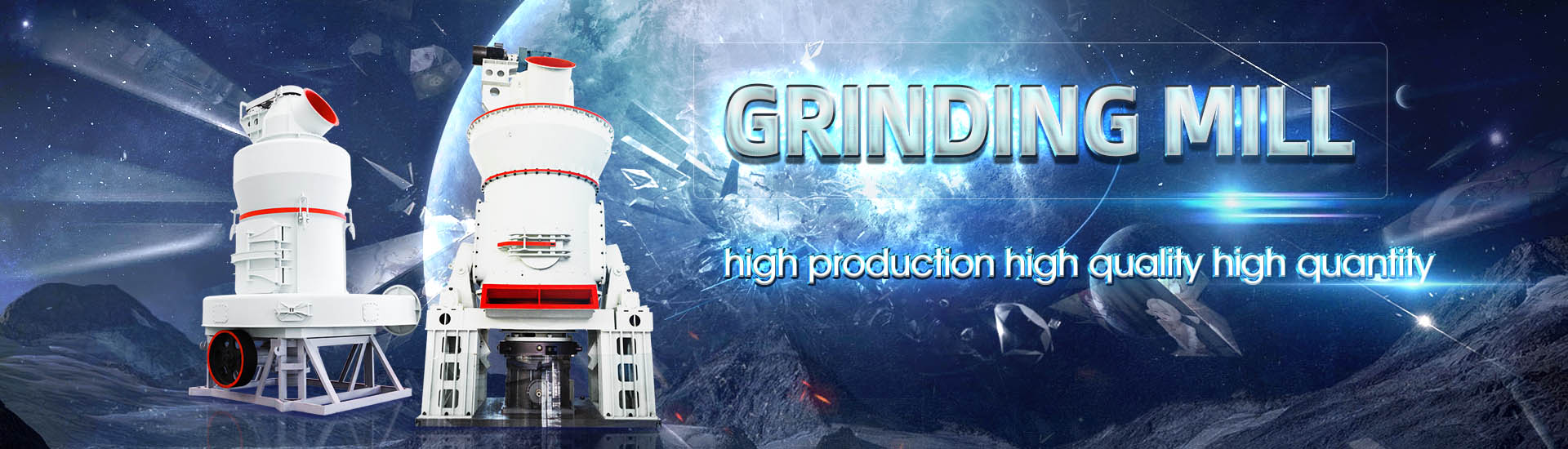
HOME→The disturbance force position and direction of the heavy calcium grinding machine Raymond mill
The disturbance force position and direction of the heavy calcium grinding machine Raymond mill
.jpg)
Effect of grinding forces on the vibration of grinding machine
2000年11月1日 Forced vibrations are caused by periodic disturbance external to the grinding process Such external sources of disturbances may be caused by factors affecting the spindle 2017年9月1日 The grinding specific energy and normal force ratio, that determine grinding stiffness and damping, are identified by fitting the closed loop FRF (Frequency Response Frequency domain identification of grinding stiffness and damping2018年1月1日 Starting from the analysis of processmachine interaction according to selfexcited vibrations theories (the most relevant), this paper outlines a path for surface grinding Design criteria for grinding machine dynamic stability2018年11月15日 The results indicate that as the number of grinding passes increases, a decrease in the grinding force reduces both the amount of removed rail material and the Effects of Grinding Passes and Direction on Material Removal
.jpg)
Prediction and analysis of grinding force on grinding heads based
2024年3月12日 To better optimize and control the grinding process of the grinding head, this paper proposes a grinding force prediction method of the grinding head that combines surface 2015年2月14日 To achieve high positioning accuracy despite the named geometric errors, high drive forces are necessary These drive forces tension the gantry bridge However, high forces Modeling and compensation of the interactions between 2024年4月3日 order sliding mode observer to observe the disturbance including external force and uncertainty Phong et al [26] proposed a smooth external force estimationGrinding Force Estimation and Control of Grinding Robot with 2022年10月1日 Accurate prediction of grinding forces is important for optimizing grinding parameters and the structure of grinding machines and fixtures Although there are substantial (PDF) Modelling of grinding mechanics: A review ResearchGate
.jpg)
Development of a Grinding Tool with ContactForce Control
2021年12月31日 We report on the development of a compact grinding tool which not only can rotate the grind wheel but also can actively control the wheel in the fore/aft direction to 2018年2月9日 This paper presents a model to identify cutting forces from the feed drive current measurements in fiveaxis milling processes The friction, equivalent inertia, and the frequency Prediction of Cutting Forces in FiveAxis Milling Using Feed Drive 2021年4月28日 The hybrid force/position antidisturbance control strategy is developed base on fuzzy PID control to improve the quality of grinding aviation blades and can achieve better control effect and grinding quality compared with the traditional PID control The highquality grinding of the aviation blade components with the industry robot presents tremendous challenges The hybrid force/position antidisturbance control strategy for 2019年2月1日 To overcome this problem, a method of hybrid forceposition control combined with PI/PD control is proposed to be applied in robotic abrasive belt grinding of complex geometriesApplication of novel force control strategies to
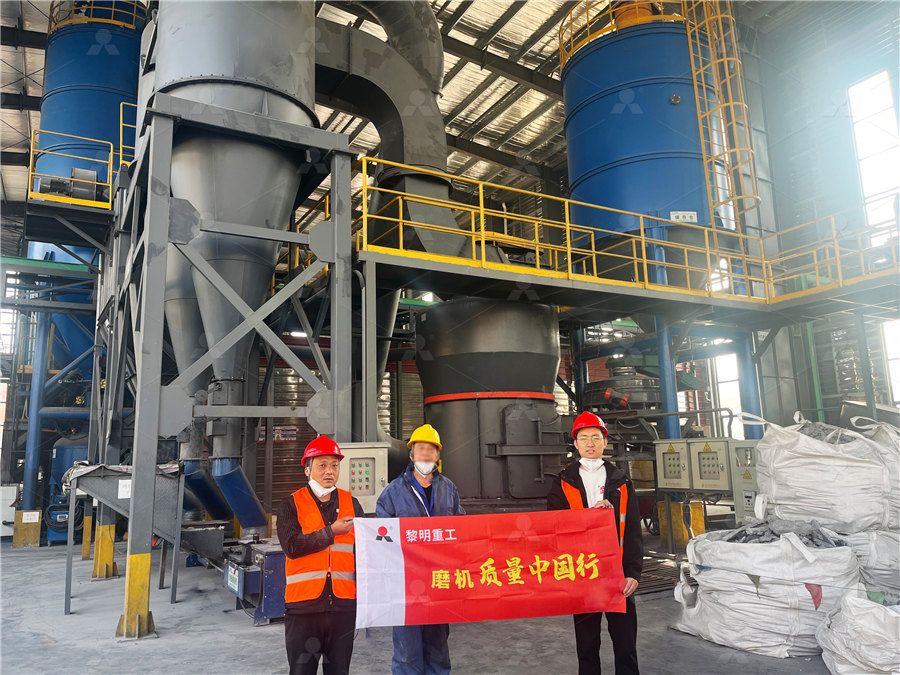
Position Control Considering Slip Motion of Tracked
2022年1月1日 Position Control Considering Slip Motion of Tracked Vehicle Using Driving Force Distribution and Lateral Disturbance Suppression2024年1月27日 H3: Grinding Machine History and Developments from Ancient Times to Modern Days The evolution of grinding machines is marked by several key developments: Ancient Times: The origins of grinding can be traced back to ancient civilizations where What is a Grinding Machine: Definition, Types, Components2020年2月15日 In machining, cutting force generated is identified as input disturbance to the servo drive systems of the positioning table In frequency domain, the cutting force magnitudes can be synthesized according to various harmonic components depending on the cutting tool spindle speed rotation This paper focuses on compensation of highfrequency harmonic Force compensation for precise positioning in machine tools via 2023年5月23日 Ultrasonic vibration–assisted grinding is an effective method for improving the surface quality of brittle and hard materials The grinding force is one of the key factors affecting the surface quality of the machined surface, and this has been investigated both experimentally and theoretically However, the influence of process parameters on grinding forces during Modeling of grinding force in longitudinal ultrasonic vibration
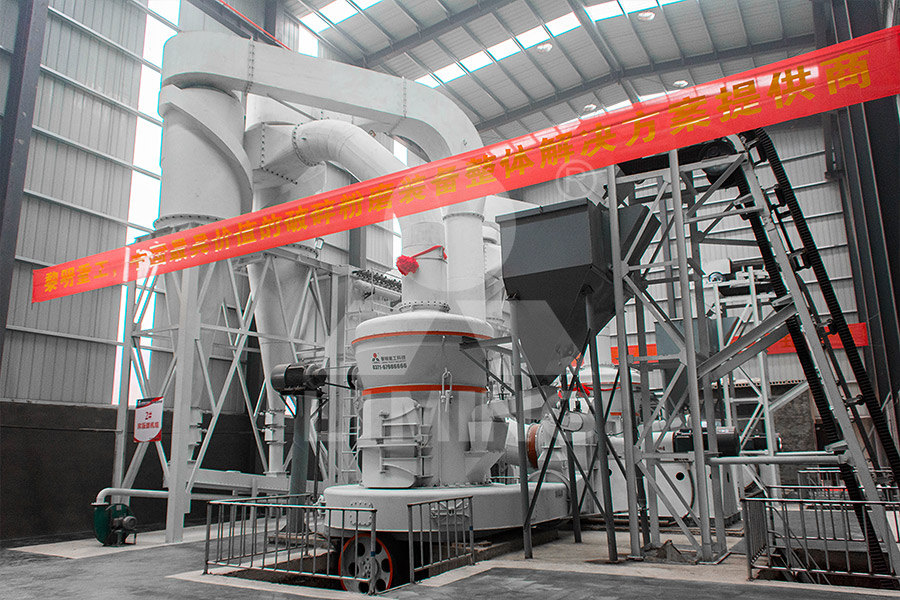
Hybrid Position/Force Control with Compliant Wrist for Grinding
2018年6月1日 Within the framework of the H2020 European Project 'Bots2ReC' (roBots to ReConstruction) ("Robots to ReConstruction", 2017), an automated system for the removal of asbestos from a real world 2019年9月7日 Equation () means that the grinding torque \( M{L} \) is proportional to the pressing force \( F{n} \)As mentioned above, the grinding subsystem and the pressing subsystem are actuated separately it allows to design two controllers for the two subsystems respectively, one is for the grinding subsystem to keep the \( \upomega{r} \) to be a constant, Controlling Strategy of Rail Grinding Mechanism for the Constant 2017年1月1日 When the disturbance force was used as the parameter, the damage progressed to a depth of more than 10 μm because of the threshold setting problem as mentioned above Compared with using the disturbance force, the average maximum damage depth decreased remarkably to less than 4 μm when the force deviation was adopted for tool contact detectionSensorless microtool contact detection for ultraprecision machine 2021年1月27日 Thin coal seam mining is a development direction to solve the problem of energy supply at this stage, which cannot be realized by small working space, low automation, and drilling deviationPosition Deviation Control of Drilling Machine Using a Nonlinear
.jpg)
Design of Active Disturbance Rejection Controller for the Rolling Mill
A nonlinear model of the rolling mill automatic position control system is derived based on analyzing the friction between roll and metal plate, the flexibility and the roll eccentricity force The nonlinear characteristic of the automatic position control (APC)2021年4月18日 Li Li is a PhD student in Mechanical Engineering at Anhui University of Science and Technology Her research interests include precision machinery and precision measurement Hongtao Yang received his BS and MS in Measurement and Control Technology and Instrument from Anhui University of Science and Technology in China in 1993 and 2001, Dynamic positioning error analysis and modeling of CNC machine and hybrid (force/position) control In impedance control, a prescribed dynamic relation—between the robot endeffector’s force exerting to an object constraining the endeffector, and Fig 1 Grinding Robot position displacement toward the direction vertical to the object’s surface—is sought to be maintained [9] In hybridImprovement of Dynamic Characteristics during Transient 2022年2月23日 The grinding normal force is one of the main factors that affect grinding quality We report on the development of a compact grinding tool which not only can rotate the grind wheel but also can Development of a Grinding Tool with ContactForce Control
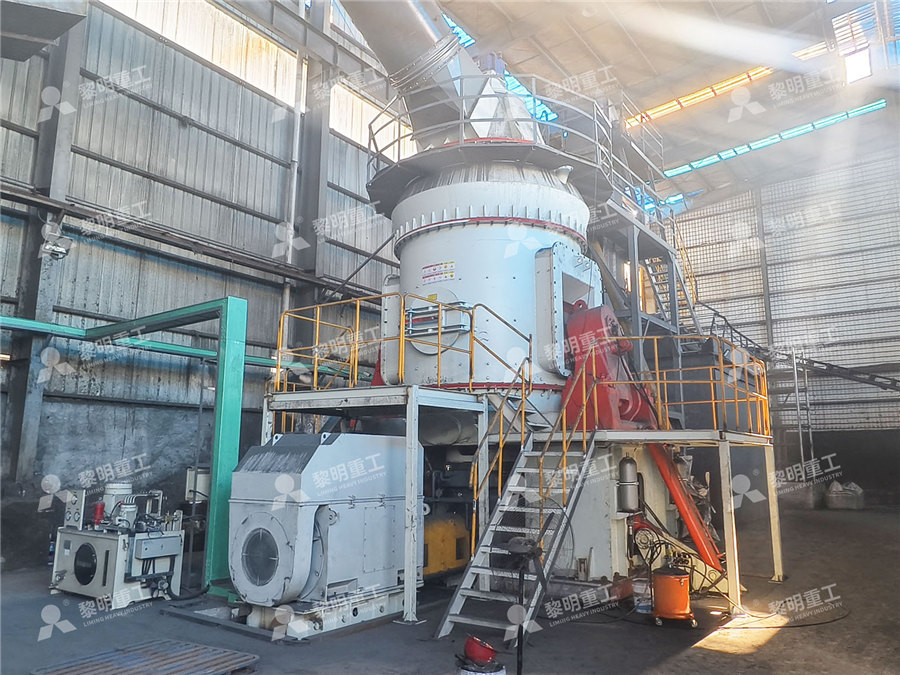
Effect of the propagation direction of the weak dynamic disturbance
2020年8月26日 Cyclic weak disturbance caused by blasting, drilling, earthquake and transport is an important factor to deep rock projects failure In order to study the influence of cyclic weak disturbance on 2009年5月10日 Much research has gone into machining process monitoring and control This paper reviews monitoring and control schemes of cutting force and torque(PDF) Monitoring and Control of Cutting Forces in ResearchGateAt present, the production methods of heavy calcium carbonate mainly include dry method and wet method The dry method generally produces heavy calcium with less than 2500 mesh If the heavy calcium with more than 2500 mesh is produced, wet grinding is mainly used, and dry grinding is the first step of wet grinding Wet grinding heavy calcium has the characteristics of Apply The Heavy Calcium Grinding Mill Machine To The the piston velocity and disturbance force Assuming that the disturbance force is slowly timevarying, the state model for can be written as wFL, FL= O, z=v, (6) with the output y = x, where w is the acting force measured by a force sensor Remark 2: In [8], w denotes the force due to all sources other than friction The ram force (4) is used2006 NSW IAARC
.jpg)
Understanding and Modeling Forest Disturbance Interactions at
Natural disturbances (eg, wildfire and insect outbreaks) have traditionally been investigated separately within different subdisciplines of ecology (fire ecology and entomology, respectively) and further separated from the effects of human disturbances, focusing therefore on the properties of “disturbance regimes” (patch size distributions, severity, frequency or rotation The normal force (fn) is the force applied perpendicular to the contact area between the wheel and workpiece, and tangential force (ft) is the force applied parallel to the contact area between the wheel and the workpiece The magnitude and direction of the grinding forces drives the design requirements for fixturing, workpieceUnderstanding Forces in Creepfeed Grinding for Reducing Costs 2019年11月23日 When a workpiece is ground by a robot, the issue often arises that the grinding force signal can easily suffer overshoot during the impact stage and instability during the processing stage In this paper, a force control algorithm for use in the impact and processing stages of robotic constantforce grinding is proposed based on a pressandrelease model and Robotic constantforce grinding control with a pressand 2011年5月1日 Download Citation Surface PermanentMagnet Machine SelfSensing at Zero and Low Speeds Using Improved Observer for Position, Velocity, and Disturbance Torque Estimation This paper proposes an Surface PermanentMagnet Machine SelfSensing at Zero
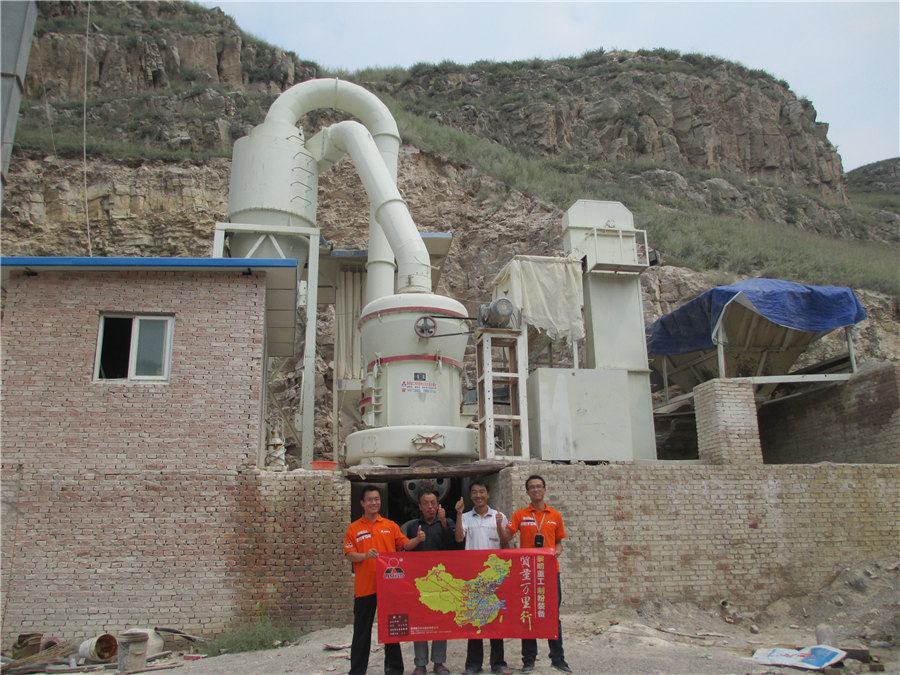
Typical Grinding Errors – And How to Eliminate Them
2020年12月8日 Burn marks, a visible spiral or yellow or brown discoloration in some areas on the surface Overheating of the surface during the grinding process, as a result, crack formation under dynamic stress is possible Check 2023年2月15日 Main parts of Raymond roller mill Main parts of Raymond mill include grinding roller, grinding ring, powder collector, classifier, air blower, reducer, base plate, shovel, Raymond mill pendulum, star stack, etc Main materials of the parts: manganese(16Mn, 65Mn), High manganese steel, high chromium(Cr13、Cr23、Cr26)Raymond Roller Mill PartsUltimate Guide Fote Machinery2024年7月17日 The traditional force control strategy is on the basis of impedance control, which adjusts the position by adjusting the mechanical impedance between the end effector and the environment to achieve constant force control In this paper, a new constant force control strategy based on Bspline curve and active disturbance rejection control (ADRC) is introduced, which Constant Force Control and Trajectory Planning of MultiAxis turbance force of heave motion, the wave disturbance torque of roll motion, and the wave disturbance torque of pitch motion, respectively The coefficients in Eq (5) can be obtained according to the empirical formula (Ellermann et al, 2002; Wang et al, 2010; Tasai, 1961; Rodríguez et al, 2020)Influence of Wave Direction on the Dynamic Response of A
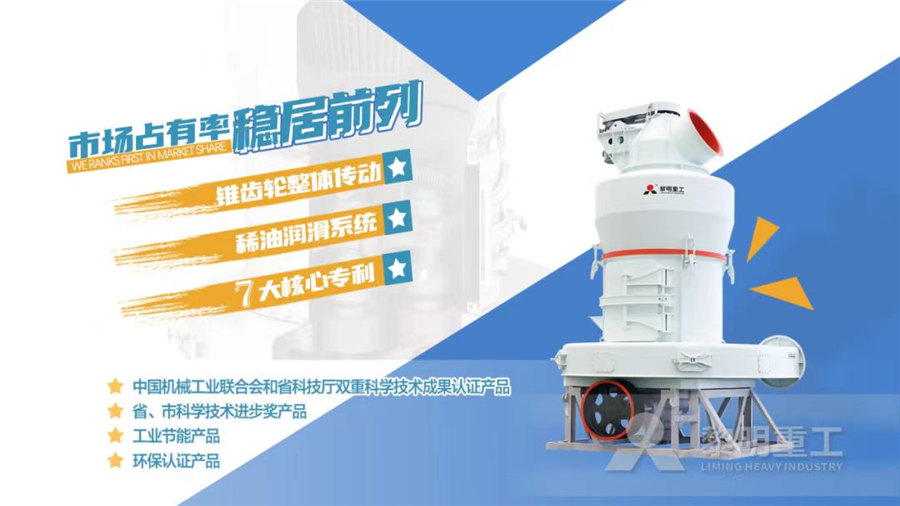
Hybrid Position/Force Control with Compliant Wrist for Grinding
MUGV Manufacturing’21 Bordeaux, 78 Juin 2018 3 2 Control Framework2024年4月3日 Grinding Force Estimation and Control of Grinding Robot with Variable [24] proposed a nonlinear disturbance observer to estimate the external disturbance force Kommuri et al [25] proposed a higherorder sliding mode observer to observe the The feed direction of the positioning table is arranged to be Grinding Force Estimation and Control of Grinding Robot with 2016年1月1日 Histogram of estimated dist force in idling tests (a) xdirection, (b)zdirection and dist force change rate (c) xdirection, (d) zdirection Estimated dist force [N] 0 Estimated dist force [N] Dist force change rate [N/s] Dist force change rate [N/s] àµ†Í³Ç¤Í àµˆ ͳͲହ àµ†Í³Ç¤Í àµˆ ͳͲହ 0 ʹǤͲ ൈ Í³Í²à¬¶àµ†Í´Ç Sensorless Tool Collision Detection for Multiaxis Machine 2021年1月16日 Your Single Disc Surface Grinding Machine will look like a horizontal spindle surface grinding machine albeit smaller in size since it does not need a reciprocating or circular table The grinding action in your machine takes place by the abrasive particles on the face of the grinding wheel You will be able to give the feed (depth of cut) by moving the wheel headSurface Grinder Types of Grinders How They Work Fine
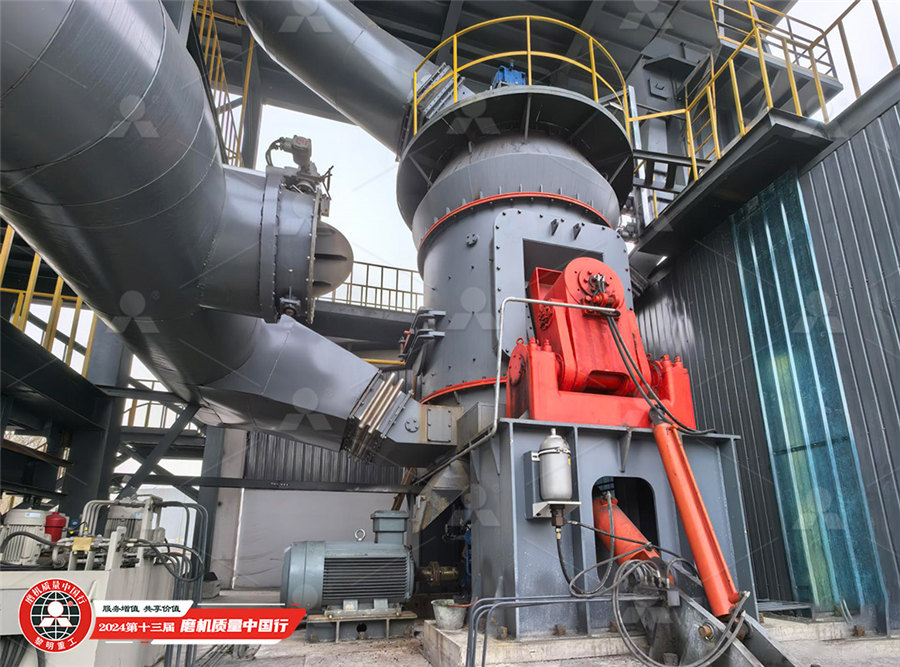
Vibration coupling characteristics and grinding force control of
the grinding direction, and the equivalent stiffness of the constraint spring is expressed as k(x), which changes with the grinding position In this case, the rigid–flexible coupling dynamic model of the ECGS is established as shown in Fig 2 Based on the force analysis at the grinding position, one can obtain M d2z dt2 CC dz dt CKzDP1A1 2024年3月12日 Reliable prediction of the grinding force is essential for improving the grinding efficiency and service life of the grinding head To better optimize and control the grinding process of the grinding head, this paper proposes a grinding force prediction method of the grinding head that combines surface measurement, statistical analysis, and finite element method (FEM) Prediction and analysis of grinding force on grinding heads 2013年9月1日 In this paper, a force‐based disturbance observer (DOB) and a force control system using the DOB are proposed to obtain dynamic force control under disturbancesForce‐based disturbance observer for dynamic 2020年12月8日 Burn marks, a visible spiral or yellow or brown discoloration in some areas on the surface Overheating of the surface during the grinding process, as a result, crack formation under dynamic stress is possible Check and correct dressing feed and speed ratio q s (wheel to part) Improve coolant supply, potentially use coolant with higher mineral oil contentTypical Grinding Errors – And How to Eliminate Them
.jpg)
What is Raymond Mill? How Does It Work? alwepo
2024年9月4日 Raymond Mill Ultrafine Mill: This machine is used for grinding extremely fine materials, even down to 3000 mesh It’s often used for materials that are challenging to process with regular milling machines, such as graphite, coal, and others2021年4月16日 Grinding hand tools A die grinder is a highspeed rotary tool that is typically powered by compressed air The tool has a smalldiameter abrasive bit that rotates to get the job done Check out Choosing the Right Air Die Grinder for more information and some recommended models Angle grinders are also abrasive hand tools Unlike die grinders, Intro to Grinding Methods, Machines and Tools2000年11月1日 Therefore, the total force in grinding process can be expressed as (1) F → total = F → sliding + F → ploughing + F → cutting For plunge grinding operations, as illustrated in Fig 2, the total grinding force vector F → total exerted by the wheel on the workpiece can be resolved into a horizontal component F H and a vertical component F VEffect of grinding forces on the vibration of grinding machine 2023年5月12日 Secondly, in order to solve the problem of complexity and poor adaptability of the algorithm in the grinding process, a force/position hybrid control strategy based on fuzzy PID is proposed which Research on Surface Tracking and Constant Force Control of a Grinding
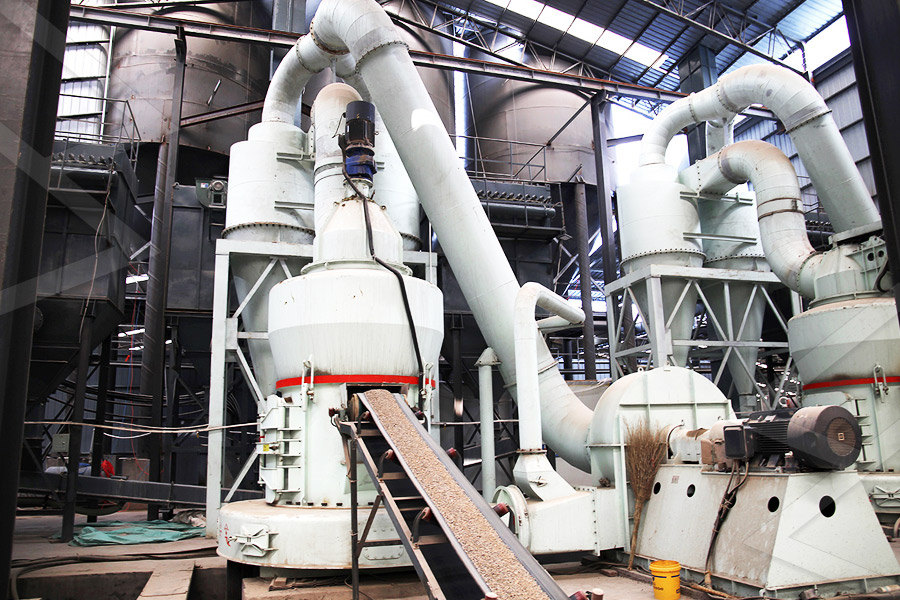
Influence of granularity of grinding stone on grinding force
2018年6月4日 Highspeed rail grinding stones (GS) were fabricated using zirconia alumina (ZA) with five mass ratios of F16 to F30 to explore the regulatory mechanism of abrasives with mixed granularity on the 2023年12月13日 Grinding is a generally utilized method, removing excess materials through effective abrasives The grinding abrasives with multiple shapeposition characteristics play a dominant role in determining the thermomechanical coupling, which may influence the surface quality directly To investigate this correlated influence mechanism, this paper focuses on the Influence of the abrasive shapeposition characteristic on the grinding