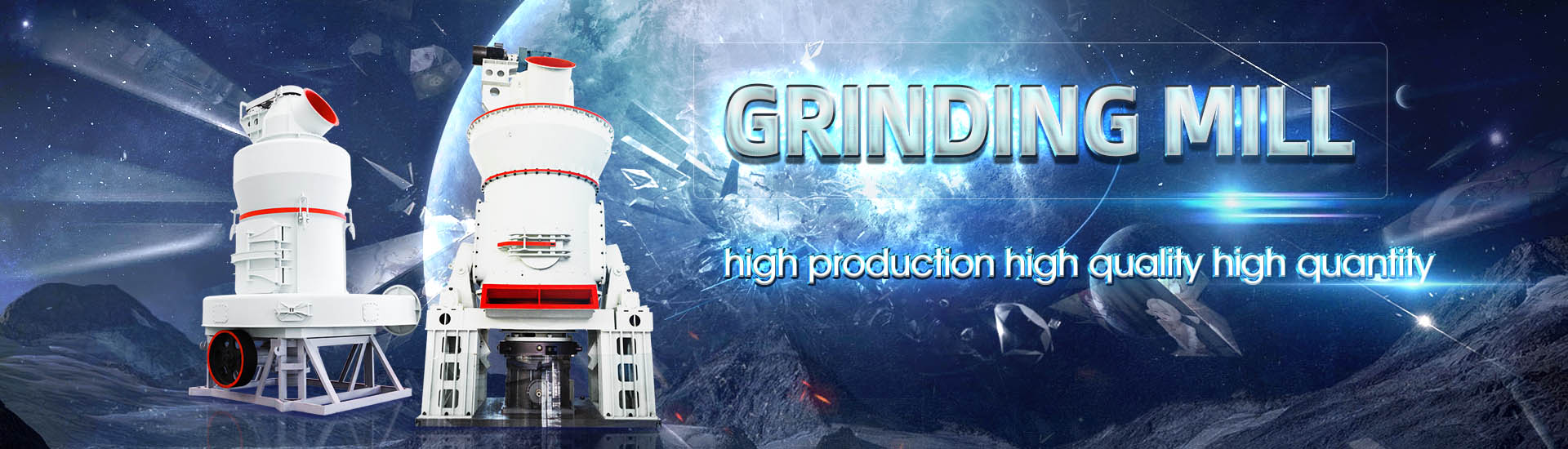
Electrolytic aluminum waste slag mill Where to buy ore mill
.jpg)
Aluminum Ash Processing Aluminum Ash Recovery Aluminum
Aluminum ash is the slag produced in the production process of electrolytic aluminum or cast aluminum, which is a hazardous solid waste Aluminum ash contains aluminum element, 2024年5月23日 Here, we review carbonrich solid wastes with focus on sources and hazards, detoxification, separation, recovery, recycling and disposal Treatment techniques include The recycling of carbonrich solid wastes from aluminum 2023年9月22日 What kind of mill is best for grinding electrolytic aluminum slag? In terms of equipment selection, both longitudinal pendulum mills and vertical mills can meet the What kind of mill is best for grinding electrolytic aluminum slag2024年2月21日 Grind the aluminum electrolysis waste residue through a Cryolite Raymond Roller Mill to below 75250 microns After removing the carbon and iron in the waste residue, Aluminum slag recycled cryolite powder production line
.jpg)
Research Progress of Electrolytic Aluminum Overhaul Slag Disposal
2023年4月25日 This article analyzes and summarizes the composition and hazards of the overhaul slag and the current development status of domestic and international electrolytic Companies that process aluminum have an opportunity to find out here about the professional processing of aluminum waste from sawing, turning or milling by means of shredding, Aluminum milling chips metal waste briquetting, disposal and Use the map below to find slag near you! 14 IMS DriveSlag Availability National Slag Association2021年7月30日 Salt slags generated from both primary and secondary aluminum production need to be recycled/treated as they are considered hazardous byproducts This review paper A Review of Secondary Aluminum Production and Its Byproducts
.jpg)
A solidstate electrolysis process for upcycling aluminium scrap
2022年4月13日 Here we propose a solidstate electrolysis (SSE) process using molten salts for upcycling aluminium scrap The SSE produces aluminium with a purity comparable to that of 2020年8月1日 Here, we discuss the influence of different processing parameters on electrolytic refining of aluminum alloy and investigate the mechanism of extracting Al from coarse AlSi Recovery of aluminum from waste aluminum alloy by low 2023年8月2日 The highvalue, green and harmless purification of aluminum electrolysis comprehensive solid waste can not only reduce its harm to the environment and soil but also separate and recover the highvalue rare elements This study aims to develop a process for recovering and treating waste aluminum electrolytes by sulfuric acid roasting The results of Sustainable Recovery of Fluorine from Waste Aluminum 2022年10月10日 The comprehensive recovery and utilization of electrolytic aluminum spent carbon anode slag (Hereinafter simplified as “carbon anode slag”) are therefore necessary Flotation is a physical separation method used to separate particles by using the difference in surface property of particles ( Chen et al, 2022 ; Ni et al, 2022 )Recovery of carbon and cryolite from spent carbon anode slag of
.jpg)
Recovery of RareEarth Elements from Molten Salt Electrolytic Slag
2022年2月19日 Recycling waste containing rare earth has always been a research hotspot The molten salt electrolysis process of rareearth metals and alloys generates a large amount of waste slag, which contains high rareearth content and, thus, has very considerable recovery value However, the high content of fluorine in rareearth molten salt slag brings challenges to the This study collected electrolytic aluminum waste cathodes, anodes, limestone and other materials After grinding the materials with an electric mill, 50 grams of electrolytic aluminum waste samples were sieved to 0075 mm The sample was then dried for 2 hours at a temperature of 110 °C in the dryer, then stored in aResearch on the Coprocessing of Mixed Electrolytic Aluminum Waste 2019年7月8日 The electrolytic aluminum waste, which would inevitably be produced from the electrolytic process in the aluminum industry, is harmful to environment and human bodyThermodynamic analysis of waste heat recovery of aluminum 2012年12月31日 During the treatment of spent cathode carbon from electrolytic aluminum, a large amount of fluoride containing wastewater is generated By adding different sodium source and aluminum source Study on Harmless and Resources Recovery Treatment Technology of Waste
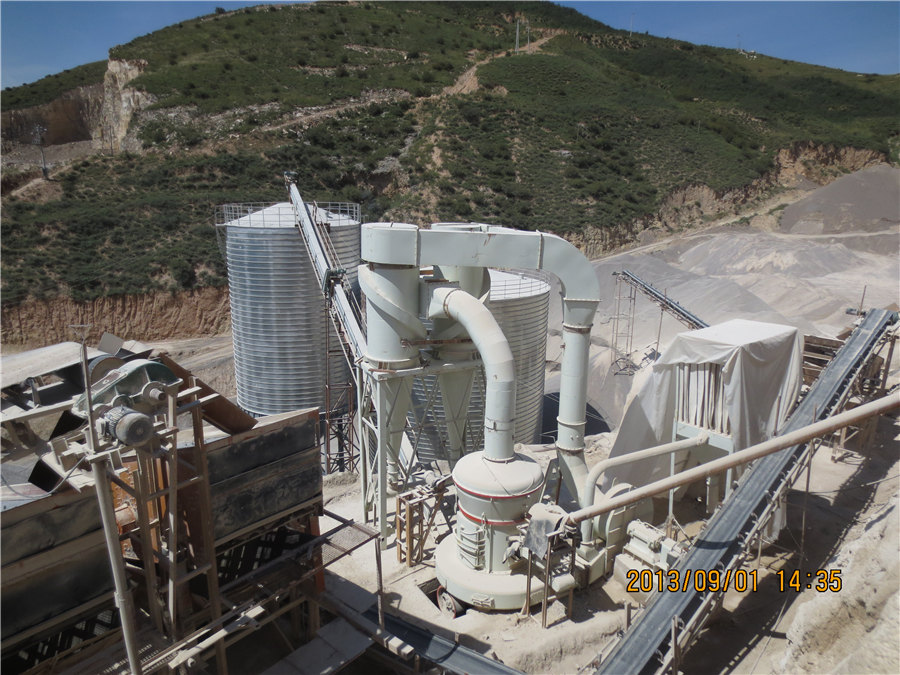
Comprehensive performance study of aluminum ash and calcium
2022年12月12日 Based on the research on bulk solid waste contact molding technology by our team [49], the comprehensive performance of pressed bricks with different ratios of aluminum ash and calcium carbide slag was investigated, the ratios of aluminum ash and calcium carbide slag are 9:1 ∼ 1:9 and pure aluminum ash and calcium carbide slag, the pressing pressure is 300 2024年2月1日 The electrolytic aluminum industry generates a large amount lithium (Li)containing electrolytic aluminum slag (EAS) annually, and this can result in severe environmental pollution and wasting of Li resources This paper proposes a method for recovering Li from the slag using AlCl 3 as the leaching agent The effects of the leaching temperature, AlCl 3 Efficient lithium recovery from electrolytic aluminum slag via an 2024年6月29日 Aluminum electrolyte is a necessity for aluminum reduction cells; however, its stock is rising every year due to several factors, resulting in the accumulation of solid waste Currently, it has become a favorable material for the resources of lithium, potassium, and fluoride In this study, the calcification roasting–twostage leaching process was introduced to extract Stepwise extraction of lithium and potassium and recovery of 2020年8月1日 Many researchers have studied the refining of aluminum by low temperature aluminium bath system Ali and Yassen (2018) used a different type of dissolvent to recover aluminum from industrial wastes This method was capable of obtaining aluminum of 99% purity by electrorefining of impure aluminum through the use of anhydrous AlCl 3 and NaCl as ionic Recovery of aluminum from waste aluminum alloy by low
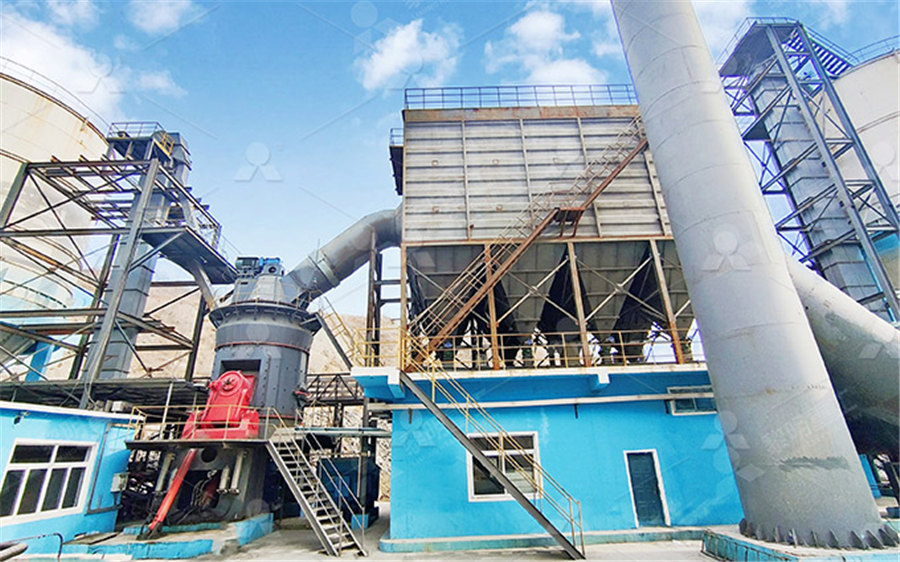
A comprehensive review of aluminium electrolysis and the waste
2023年4月13日 This paper proposes a technical viewpoint for the recovery of waste heat in aluminum electrolysis The idea of combining heatgenerating electrolysis process and the heatconsuming alumina tube 2024年4月17日 Aluminum dross is a wellknown industrial waste generated in the aluminium industry, and its recycling and reuse is still a worldwide issue Herein, aluminum dross waste (ADW) was recycled to Aluminum Dross: Aluminum metal Recovery and emerging 2021年12月1日 Abtract Aluminum slag waste generated from the smelting process of bauxite was used to prepare roof tiles samples Clay was substituted by slag waste in percentages reaching 40% in the basic mix The use of aluminum slag waste in the preparation of roof tiles2009年8月1日 Mill scale is an iron oxide waste generated during steelmaking, casting and rolling Total generation of mill scale at JSWSL is around 150 t/day and contains 60–70%FeO and 30–35%Fe2O3Recycling of steel plant mill scale via iron ore ResearchGate
.jpg)
(PDF) Recovery of Carbon and Cryolite from Spent Carbon Anode Slag
2023年3月12日 The aluminum electrolysis industry continually and unavoidably produces hazardous solid waste in the form of carbon anode slag Carbon anode slag poses a serious environmental pollution risk, and 2023年3月12日 The aluminum electrolysis industry continually and unavoidably produces hazardous solid waste in the form of carbon anode slag Carbon anode slag poses a serious environmental pollution risk, and it must be disposed of in a harmless manner On the other hand, it contains a few valuable resources, as well In order for the aluminum electrolysis industry to Recovery of Carbon and Cryolite from Spent Carbon Anode Slag2020年11月23日 Recycling aluminum ash and slag can not only reduce the waste of resources, but also produce considerable economic benefits The recycle process of aluminum ash and slag The aluminum ash and slag is ground by mill and then feed to separator to get the metal aluminum and aluminium oxideRecycling and utilization of the aluminum ash and slag Mineral HCM’s HC1700 vertical pendulum Raymond mill, HLM series manganese carbonate vertical mill and other equipment have a high reputation in manganese ore enterprises all over the world market share, the following two types of electrolytic manganese powder grinding mill equipment will be introduced to youNews How to choose the electrolytic manganese powder grinding mill
.jpg)
Sustainable Approaches for LD Slag Waste Management in Steel
2016年5月16日 Reduce, reuse, and recycle are important techniques for waste management These become significant for improving environmental and economic condition of industries Integrated steel industries are generating huge amounts of steel slag as waste through the blast furnace and Linz–Donawitz (LD) process Presently, these wastes are disposed by dumping in Aluminium ash and slag are produced from molten slag cooling in the electrolytic aluminium production process,the recycling and utilization of the electrolytic aluminium ash and slag is attracting more and more attention at home and abroad for their valuable components such as 10%30% aluminium and 30% Al2O3The recovery utilization and technology of advantages Recycling and Utilization of the Electrolytic Aluminium Ash and SlagUnderstanding Mine to Mill is presented in five parts Part A – Setting the Scene provides some definitions of Mine to Mill (M2M) and the historical background A chronology of Mine to Mill developments is followed by brief descriptions of the very wide range of Mine to Mill applications which have been implemented over the last 15 yearsUNDErsTaNDINg MINE TO MILL 911 Metallurgist2020年12月1日 The rapid development of the electrolytic aluminum industry in China and the increasing demand for aluminum products have led to the development of many lowgrade bauxite mines with an average Li 2 O content of at least 058% (Wang et al, 2013)Due to the use of this lowgrade bauxite in the electrolytic aluminum process, the content of lithium in the Novel process for the extraction of lithium carbonate from spent
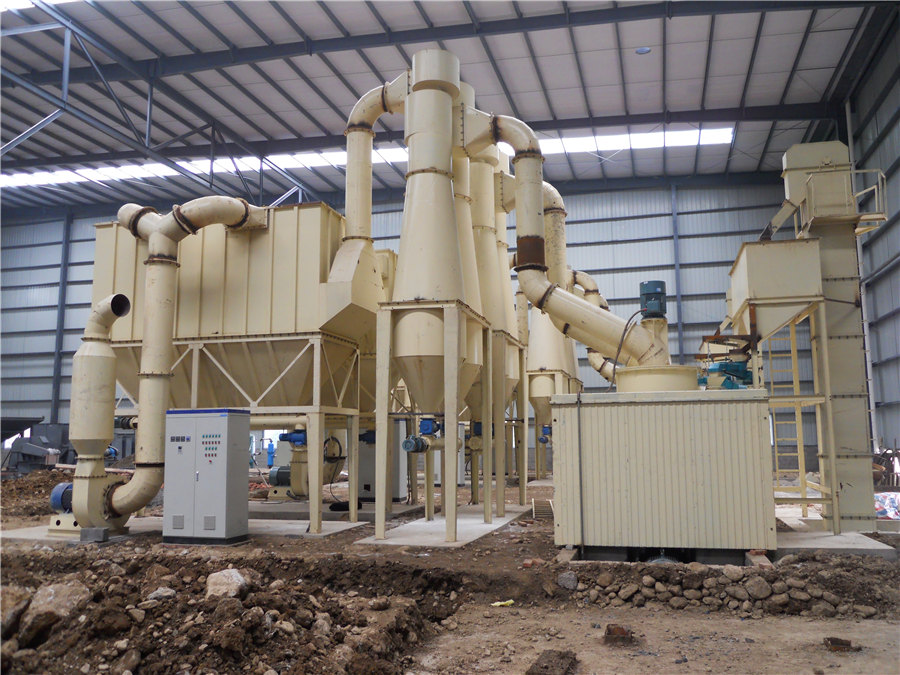
Mill Food Recycler
2024年6月29日 The aluminum bucket conducts heat for an ultrafast dry time Buy now Buy now As low as $1977/mo 90day trial Get started With no trash service we had to freeze our food waste then take to the waste station 2024年2月21日 The electrolytic slag is sent to the jaw crusher and broken into small pieces 2 Grinding The crushed small pieces are sent to the cryolite mill and ground into powder 3 Stir The powdery electrolytic slag is fed into the mixer and stirred evenly 4 FlotationAluminum slag recycled cryolite powder production line2018年2月5日 Piles of steel slag, a solid waste generated from the iron and steel industry, could be seen due to no utility found for the past century Steel slag has now gained much attention because of its new applications The properties of slag greatly influence its use and thus had got varied applications The chemical composition of steel slag varies as the mineral composition Review on the innovative uses of steel slag for waste minimization2020年8月14日 Paste backfilling is an incipient underground mine backfill technology in India It facilitates maximum use of mill tailings with enhanced stability of the underground workings and minimises rehandling of water, as well as provides bulk disposal of mining solid waste Binder type and dosage plays an important role in paste backfill performance This paper highlights Utilisation of lead–zinc mill tailings and slag as paste backfill
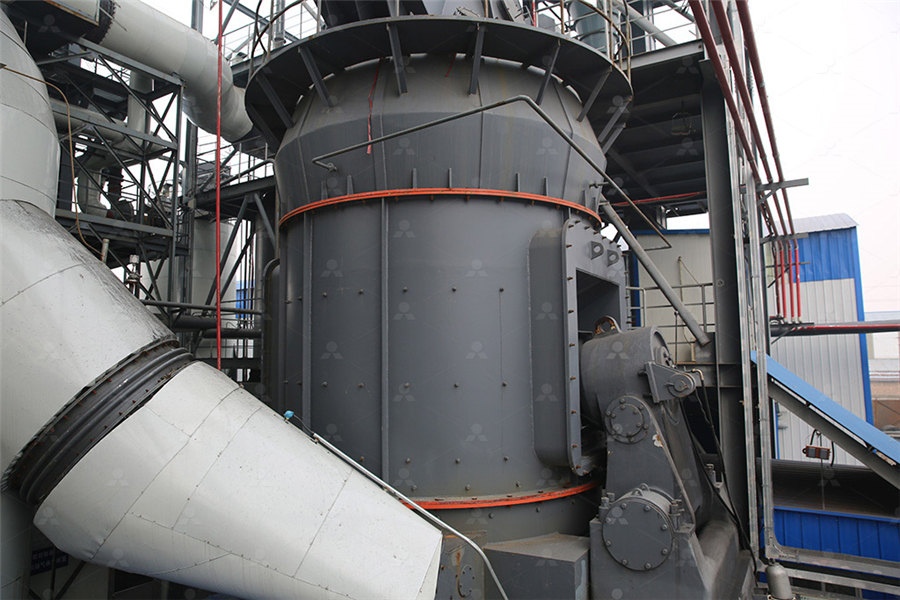
Efficient extraction and recovery of lithium from waste aluminum
2023年10月1日 Cryolitealumina (Na 3 AlF 6Al 2 O 3) molten salt electrolysis is the only modern method for the industrial production of metallic aluminum (Ishak et al, 2017)Under the influence of direct current, Al 2 O 3 dissolved in the molten salt is reduced to monolithic aluminum at the cathode (Haraldsson and Johansson, 2020)As the blood of the electrolytic cell, the electrolyte 2024年2月1日 Efficient lithium recovery from electrolytic aluminum slag via an environmentally friendly process: Leaching behavior and mechanismEfficient lithium recovery from electrolytic aluminum slag via an 2022年9月1日 To better solve the waste pollution problem generated by the electrolytic manganese industry, electrolytic manganese slag as the main raw material, chromium iron slag, and pure chemical reagents (PDF) A study of the solidification and stability mechanisms of 2021年7月30日 Aluminum is the second mostconsumed metal in the world, only outranked by steel Primary aluminum is produced through the HallHeroult process1 In this process, alumina dissolves in a sodium cryolite melt, and aluminum is reduced at the aluminum liquid cathode pool while the anode products are significant amounts of \({\mathrm{CO}}{2}\) and other A Review of Secondary Aluminum Production and Its Byproducts
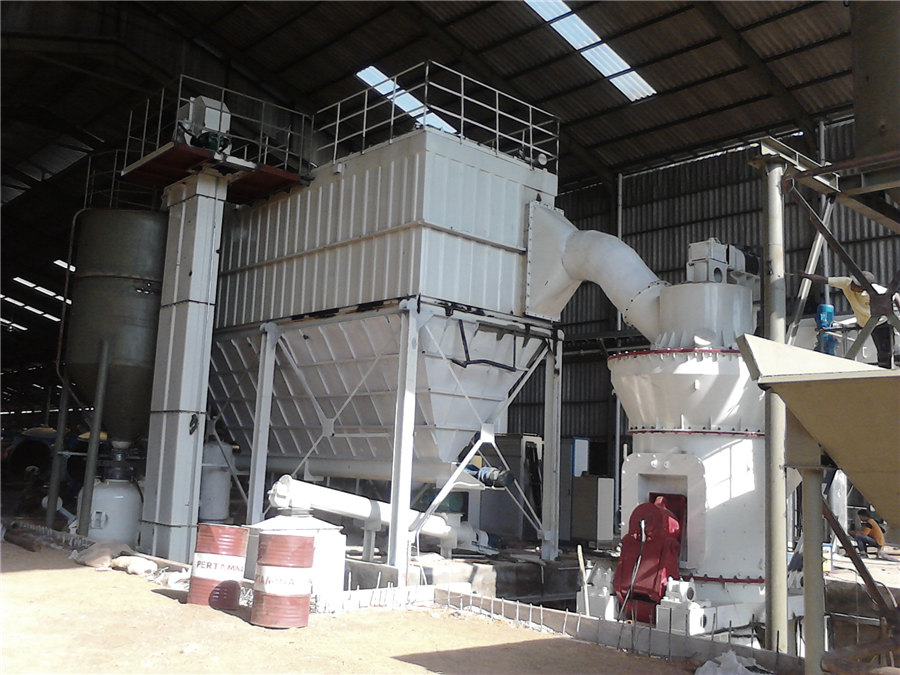
电解铝废渣提锂工艺研究【维普期刊官网】 中文
MORE The recycling technology and process of electrolytic aluminum byproduct,lithiumcontaining electrolytes by comprehensive utilization of electrolytic aluminum waste slag is relatively backward,failing to realize recycling of the expensive lithium resourcesThe structure and physical and chemical properties of the byproduct lithiumcontaining electrolytes are 2012年5月30日 Aluminium salt slag is toxic/hazardous waste (production: 200–500 kg/Al tonne) Chemical and mineralogical characteristics are presented Various processes for Al metal recovery and recycling of KCl/NaCl to smelting process are reported Preparation of value added products from the final NMR is discussedAluminium salt slag characterization and utilization – A reviewAs a byproduct of production, aluminum plant waste residue is also increasing The total loss of aluminum content in the waste residue of aluminum plant in the production process is 112% HCMilling (Gulin Hong Cheng) can provide you with the best quality aluminum plant slag grinding mill machine and serviceWhat’s The Use Of Aluminum Plant Waste? The Price Of Aluminum Waste 2016年2月1日 The conditions of declining gold grade in the ore, increasing depth of excavation, and decreasing unallocated stock of deposits make it necessary to develop efficient solutions for the mineto Monitoring ore loss and dilution for minetomill integration in
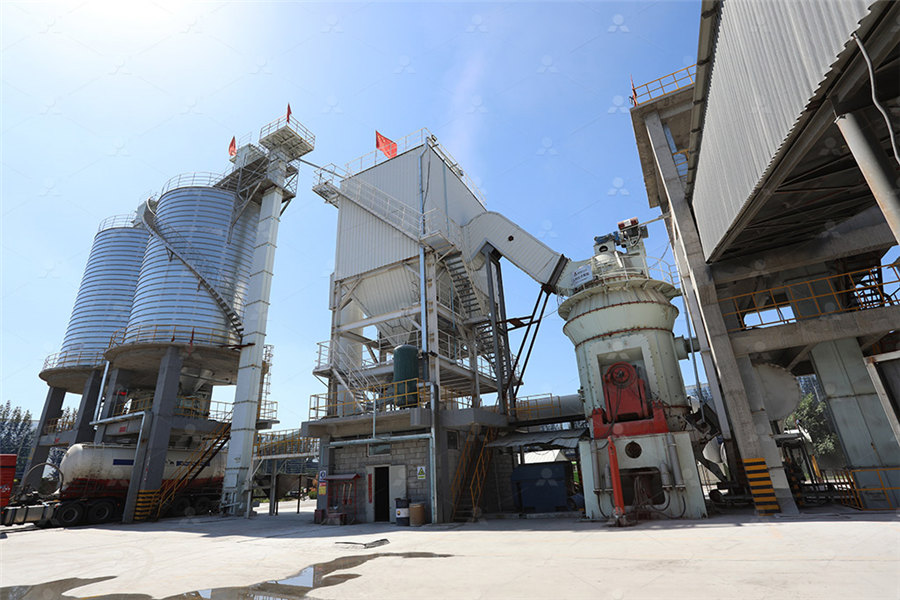
Preparation of electrolytic manganese residue–ground
2013年6月1日 Electrolytic manganese residue (EMR) is added into ground granulated blastfurnace slag (GGBS) as an activator to prepare EMR–GGBS cement The effects of chemical activation, mechanical 2017年3月5日 PDF Nowadays, iron and steel industries are moving toward environmental sustainability through careful control of greenhouse gas emissions and Find, read and cite all the research you need (PDF) Iron and Steel Slags ResearchGateas a waste4) Byproducts bearing high iron content such as, mill scale, LD sludge and BF dust are more attractive in comparison with low iron bearing materials like slags One such attractive material to explore is mill scale obtained from hot rolling mill operations Mill scale, generally obtained in the size range of 1–5Direct Reduction Recycling of Mill Scale Through Iron Powder During a longterm operation of the aluminum electrolysis cell, the molten salts continuously infiltrate and corrode the pot lining, resulting in a huge amount of hazardous waste after the overhaulElectrolytic cell spent lining Fig 2 Overhaul slags of the
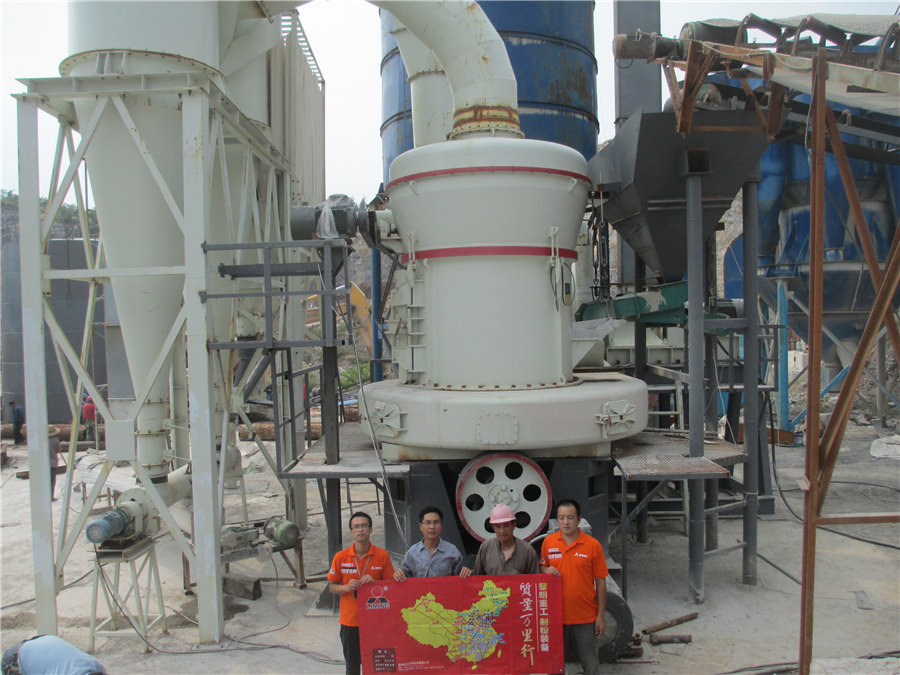
From waste to waste: iron blast furnace slag for heavy metal ions
2022年3月31日 Inordinate levels of heavy metals in water sources have long been a matter of concern, posing serious environmental and public health risks Adsorption, on the other hand, is a viable technique for removing heavy metals from water due to its high efficiency, low cost, and ease of operation Blast furnace slag (BFS) is considered a cheap sorbent for the get rid of Find your ore mill easily amongst the 42 products from the leading brands (Fritsch GmbH, Retsch, Eriez, ) on DirectIndustry, waste (7) glass coarse powder for powders (5) for metals (5) copper food (5) for solid fuels (4) for coal grinding for biomass for ceramics (3) for plastics (1) Submit Final grain sizeOre mill, Ore grinding mill All industrial manufacturers