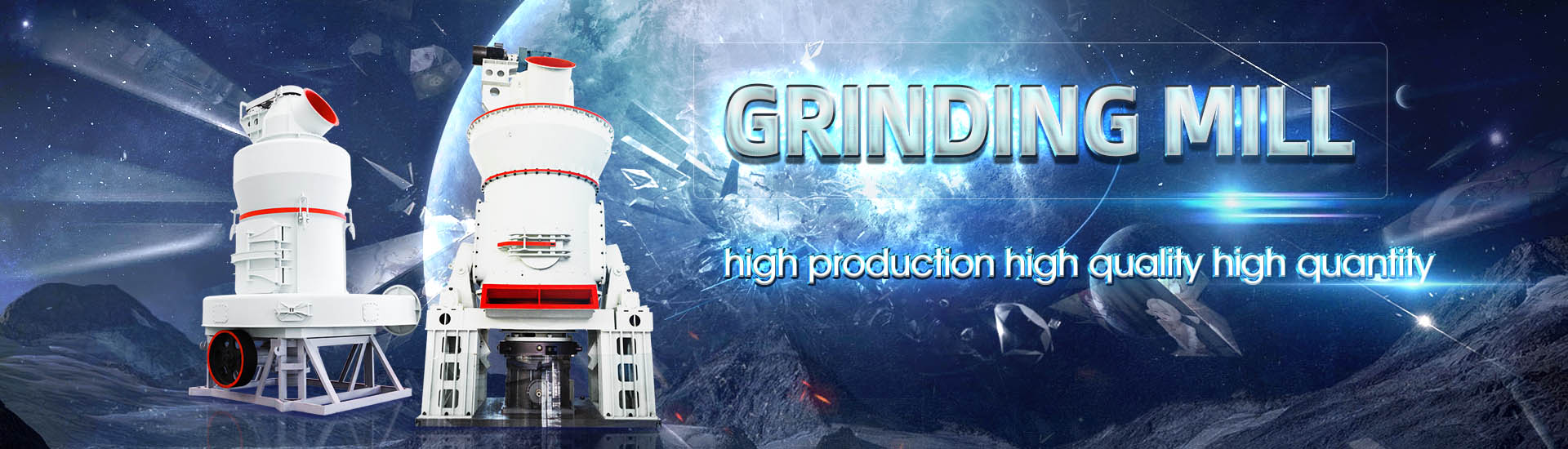
Ore mill working method
.jpg)
Iron Ore Processing: From Extraction to Manufacturing
2024年4月26日 Learn about the key stages in iron ore processing, including crushing, screening, and beneficiation techniques for optimal resource utilization2023年7月20日 With a certain amount of grinding medium in the cylinder, when the cylinder rotates, the grinding medium is fluctuated to produce impact and grinding effects According to Ore Grinding SpringerLink2015年8月3日 It is a process of ore preparation, milling, and ore dressing or ore beneficiation Ore dressing is a process of mechanically separating the grains of ore minerals from the gangue(PDF) Overview of Mineral Processing Methods2023年10月27日 Grinding media play an important role in the comminution of mineral ores in these mills This work reviews the application of balls in mineral processing as a function of the A Review of the Grinding Media in Ball Mills for Mineral Processing
.jpg)
Ore Grinding Methods and Process of Ore Grinding
Ore grinding is a process to further reduce and disperse the ore particle size In the mineral processing industry, ore grinding is the particle size preparation before the separation of the When iron ore is extracted from a mine, it must undergo several processing stages Six steps to process iron ore 1 Screening We recommend that you begin by screening the iron ore to separate fine particles below the crusher’s CSS The six main steps of iron ore processing Multotec2014年10月15日 The goal of ore sorting is to reduce the total amount of material sent to the high energy milling circuit, while not significantly impacting total metal recovery In general, ore Development of ore sorting and its impact on mineral processing 2022年10月20日 Making iron and steel from iron ore requires a long process of mining, crushing, separating, concentrating, mixing, agglomeration (sintering and pelletizing), and Iron Ore Processing, General SpringerLink
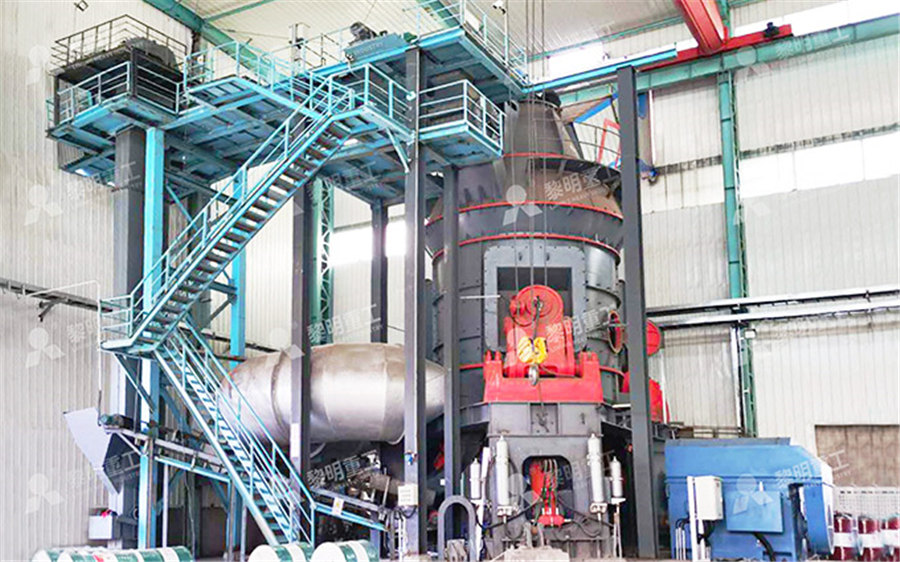
82: Mining and Ore Processing Geosciences LibreTexts
When ore is first processed (typically close to the mine) it is crushed to gravelsized chunks and then ground to a fine powder and the ore minerals are physically separated from the rest of the rock to make a concentrate At a 2017年6月15日 To understand the friction and wear of working mediums in iron ore ball mills, experiments were conducted using the ball cratering method under dry and wet milling conditions, which mimic the Friction and wear of liner and grinding ball in iron ore ball millAccording to different working conditions, the rod mill performs different grinding tasks Generally speaking, For hard ores, the more economical method is to use a shorthead cone crusher to form a closed circuit with the screen The choice of ball mill or rod mill in the design must be determined according to the specific situationThe Working Principle and Advantages of the Rod MillMinetomill integration, MCF, fragmentation, ore loss, and dilution may have different connotations for people working in various mining disciplines, in particular those that are not working in mineral resource management (MRM) Monitoring ore loss and dilution for minetomill
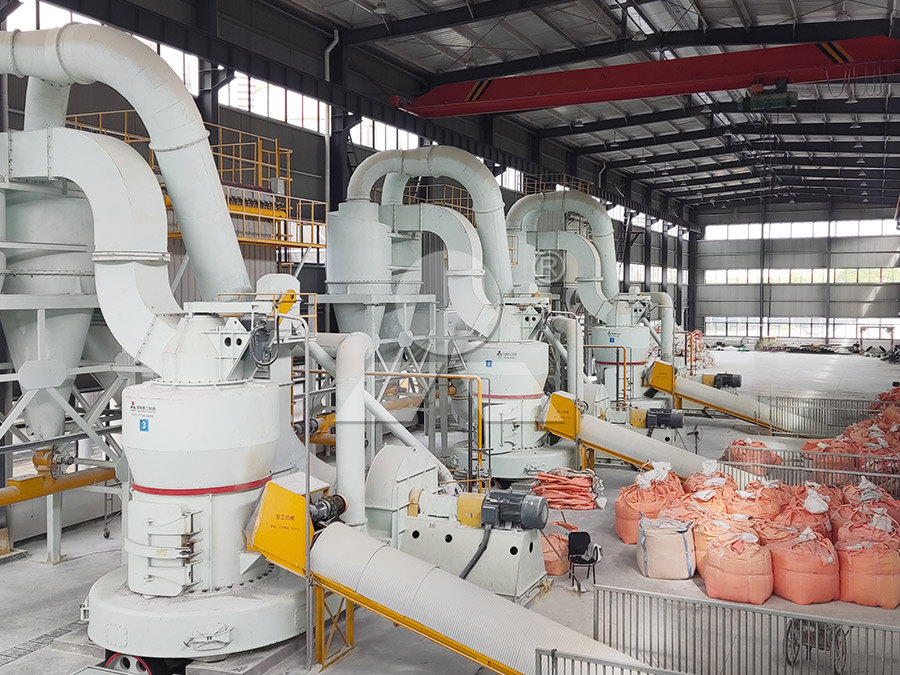
Ball Mill Grinding Machines: Working Principle, Types, Parts
Ball Mill Working Principle The working principle of a ball mill is based on the impact and attrition between the balls and the grinding media As the mill rotates, Mining and Ore Processing: Ball mills are used for grinding ores and minerals, enabling the extraction of valuable metals2021年5月31日 A Method of Ore Blending Based on the Quality of According to the working order, the ore blending JM Kinetics of DryBatch Grinding in a LaboratoryScale Ball Mill of Sn (PDF) A Method of Ore Blending Based on the Quality of 2017年11月1日 To understand the friction and wear of working mediums in iron ore ball mills, experiments were conducted using the ball cratering method under dry and wet milling conditions, which mimic the operating conditions in ball mills The liner sample is made of Mn16 steel, the ball had a diameter of 25 mm and was made of GCr15 steel, and the iron ore powder was Friction and wear of liner and grinding ball in iron ore ball mill 2024年1月10日 If the raw materials are brittle materials such as tungsten tin ore, rare metal ores, and coal, choose a rod mill; if the materials are aluminum ash, lime, slag, molybdenum ore, etc, use a ball mill It is relatively better to deal with it According to the particle size effect of the finished product The product particle size is 1~3mmBall Mill VS Rod Mill: Difference Selection JXSC Machine
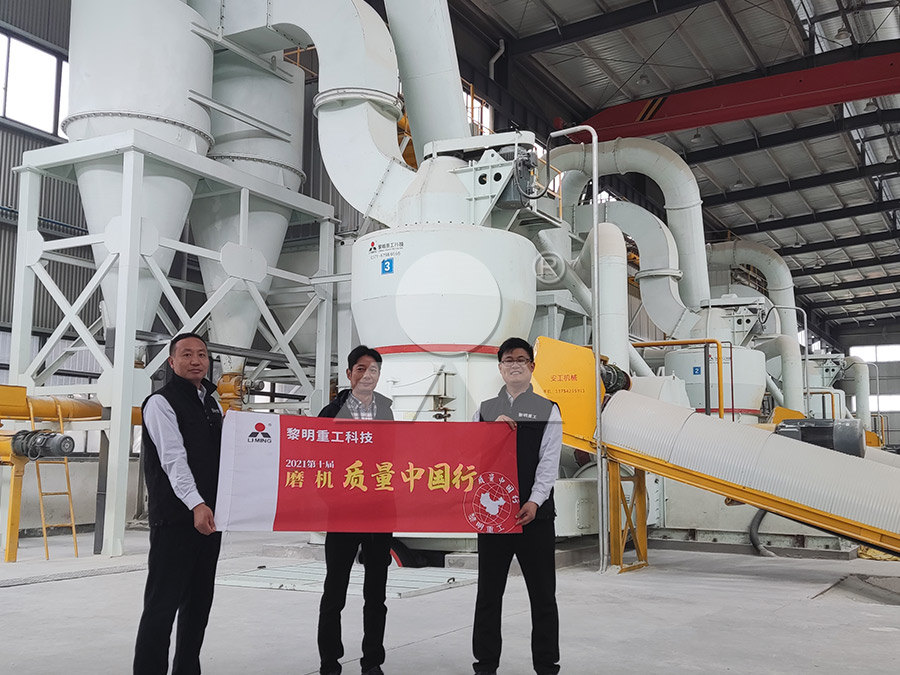
Ball Mill Working Principle Ball Mill Types MC
1 Ball Mill: The grinding medium of the ball mill is mainly steel balls or steel sections, and it is widely used 2 Rod Mill: The grinding medium is mainly steel rod, the diameter of steel rod is mostly between 50100mm, and the grinding time is longer 3 Gravel Mill: also known as a pebble mill, is a device used for grinding pebblesUsually used for processing stone or ore to Vertical Roller Mill Working Principle Train the startup process, teardown method, common problems, and maintenance service Illite ore industrial grinding mill machine can grind illite into powder up to 3000 mesh, including ultrafine mill, vertical mill, Vertical Roller Mill SBM Ultrafine Powder Technology2018年8月8日 The article presents research on the comminution of copper ore in a selfconstructed mill using highpressure water jet energy to investigate the usefulness of such a method for comminuting copper (PDF) Grinding Kinetics Adjustment of Copper Ore Grinding in 2016年2月1日 The purpose of this study is to understand how ore loss and dilution affect the mine call factor, with the aim of subsequently improving the quality of ore mined and fed to the millMonitoring ore loss and dilution for minetomill
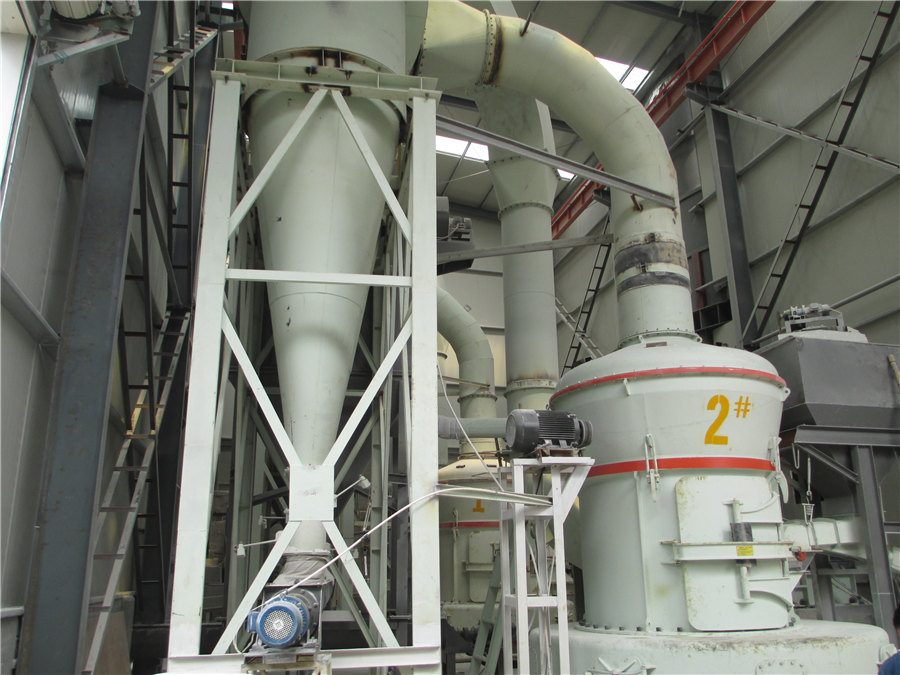
Ball Mills 911Metallurgist
2017年2月13日 In all ore dressing and milling Operations, including flotation, cyanidation, gravity concentration, and amalgamation, the Working Principle is to crush and grind, often with rod mill or ball mill, the ore in order to liberate the Energies 2021, 14, 1786 2 of 14 size [11] The cost of the energy used in comminution represents 50 ÷ 60% of the entire ore processing costs [12]Energy Efficiency Analysis of Copper Ore Ball Mill Drive Systems2017年2月16日 The methods employed in dressing the tin ore up to the required percentage of purity depend mainly on the type of ore crushed These may be briefly divided 911 Metallurgist is a trusted resource for practical insights, solutions, and support in mineral processing engineering, helping industry professionals succeed with proven expertise Tin Ore ProcessingTin Ore Processing 911Metallurgistdrive system to be overloaded when the mill filled with copper ore is started For this reason, the mill is stopped only in the case of a failure or planned maintenance work The aim is to minimize the potential number of startups, as the mill at a standstill must be later started under full load In the case of a prolonged downtime, the moist Energy Efficiency Analysis of Copper Ore Ball Mill Drive Systems
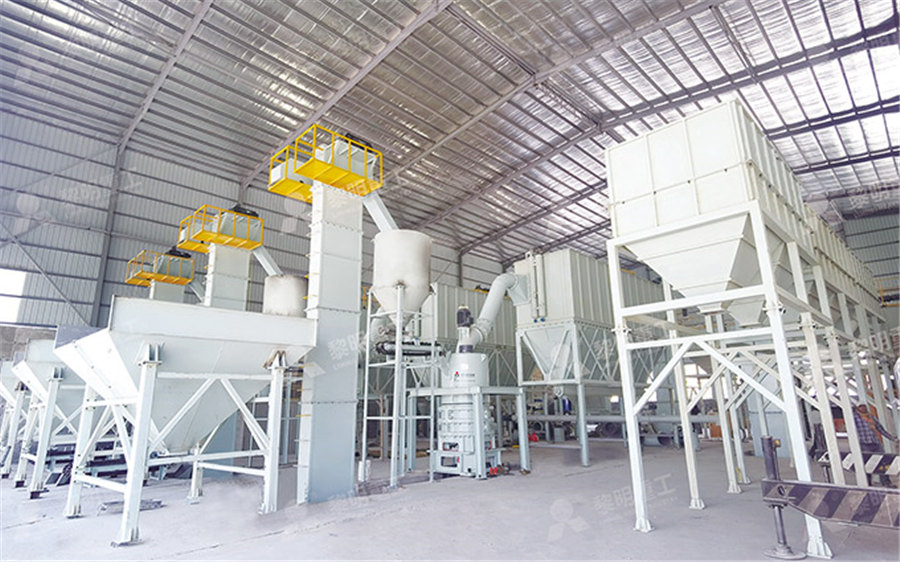
Operation Analysis of a SAG Mill under Different Conditions Based on
2020年10月9日 Based on ore characterisation studies and combined with Discrete Element Method (DEM) simulations, it is possible to evaluate samplers’ dimensions as proposed by the theory of sampling and GM comes into the office asking why the grade is not appearing at the mill! Interestingly, in the authors’ experience , the term ‘ore loss’ is used far less frequently or not mentioned at all This is a little perplexing , as the potential economic impact of ore loss is far greater than dilutionDilution and ore loss – A short practical guide Cube ConsultingHighstress abrasive wear is a major material consumption process in mining and ore beneficiation industries The common laboratory highstress abrasion apparatuses suffer from lack of capability of closely simulating the service conditions of grinding media and mill liners, being the main consumables in these sectors The ball mill abrasion test (BMAT) is a versatile Ball mill abrasion test (BMAT): Method development and 2024年7月12日 Unlock ball mill technology Let’s dive into the world of mills and explore their components, working principles, rod mills are better for preparing feed for gravimetric ore dressing methods and certain flotation processes We’ll What Is a Ball Mill and How Does It Work? Certified MTP Blog
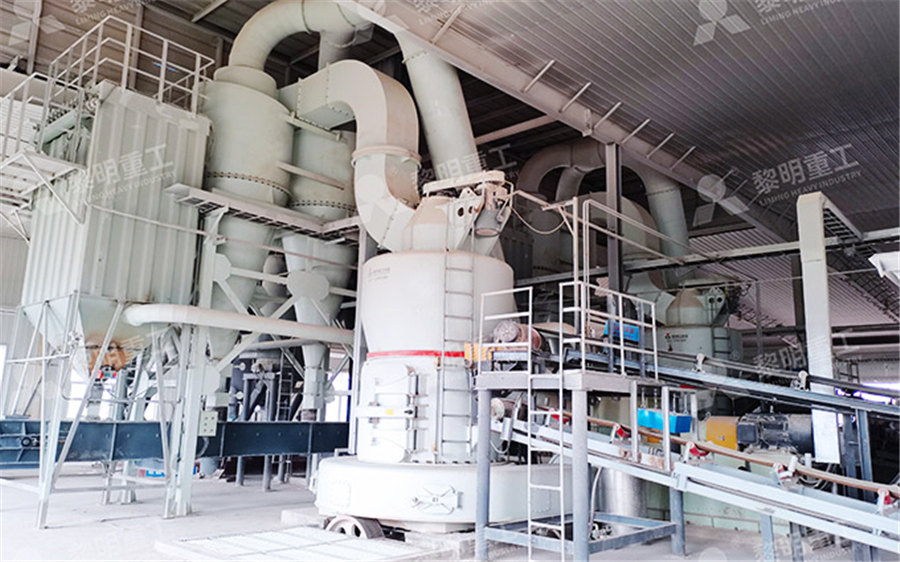
Friction and wear of liner and grinding ball in iron ore ball mill
2017年11月1日 In this study, the ball cratering method is used to analyze the friction behavior and the wear mechanism of the liner in the iron ore ball mill under different working conditions And as stated in the literature [30] , it is very important to choose the appropriate contact parameters in simulations using the discrete element method (DEM)SemiAutomatic Mill Parameter Optimization Method and Simulation Modeling Process 35 Actual Best Speed of SemiAutomatic Mill The working conditions of the semiautomatic grinding machine in actual operation are more which is the basis for ensuring the grinding efficiency of the semiautomatic mill The bulk oreAnalysis and Implementation of the Method for Improving the 2018年6月18日 Ore pretreatment methods for grinding: journey and prospects, Mineral Processing and Extractive Metallurgy Review, DOI: 101080/2018 To link to this article: https://doior g/10 Ore Pretreatment Methods for Grinding: Journey and Prospects2022年4月21日 In actual industrial production, labeled sample data of a ball mill is difficult to obtain under variable working conditions Aiming to realize the soft measurement of ball mill load under variable working conditions, a joint discriminative highorder moment alignment network (JDMAN) is proposed, based on the deep transfer learning in this paperSoft measurement of ball mill load under variable working
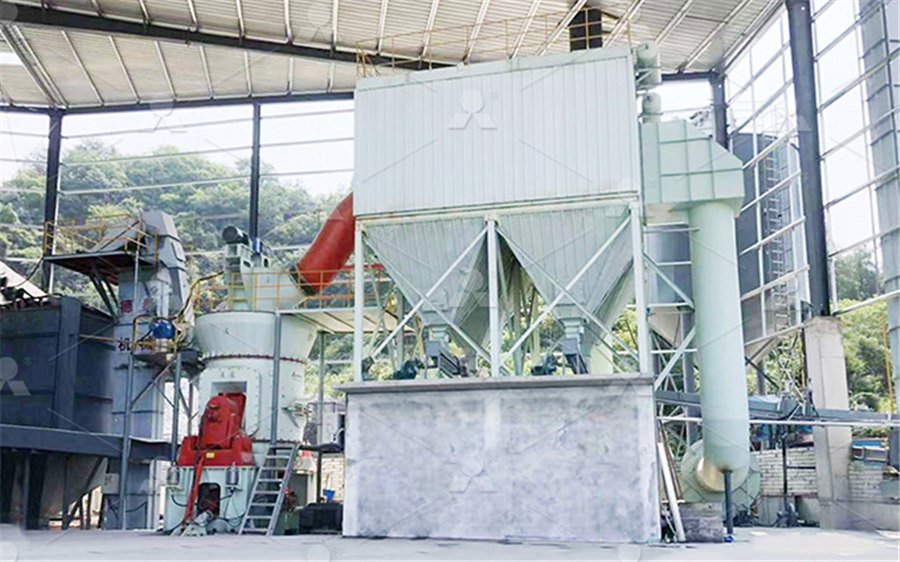
Research of iron ore grinding in a verticalrollermill
2015年3月15日 For the grinding tests, a Loesche mill LM45 (table diameter 045 m) is used (Fig 2a) This pilot scale mill is a special development for ore grinding, which is reflected by several features The mill has four rollers, which are able to stress the particle bed with grinding pressures of up to 5000 kN/m 22024年10月8日 Research on optimization of mining methods for broken ore bodies based on intervalvalued pythagorean fuzzy sets and TOPSISGRAResearch on optimization of mining methods for broken ore2017年4月5日 The stoping method may affect the percentage of ore minerals recovered in the oredressing plant, especially where certain sulfide ores are concentrated by flotation Thus, a stoping method that permits immediate removal of the ore after it is broken so as to preclude its partial oxidation before it goes to the mill may be desirable or necessaryOre Dilution Recovery in Mining 911MetallurgistCrushing, a form of comminution, one of the unit operations of mineral processing Mineral processing is the process of separating commercially valuable minerals from their ores in the field of extractive metallurgy [1] Depending on the processes used in each instance, it is often referred to as ore dressing or ore milling Beneficiation is any process that improves (benefits) the Mineral processing Wikipedia
.jpg)
Research of iron ore grinding in a verticalrollermill
Request PDF On Mar 15, 2015, Mathis Reichert and others published Research of iron ore grinding in a verticalrollermill Find, read and cite all the research you need on ResearchGateSize, hardness and density of ore particles according to M M Protodiakonov scale It is a system that can measure ore content on 4 inputs and includes realtime measurement of pulp density The rate at which fresh ore from the belt conveyor enters the mill From the electromagnetic measurement of the consumption water coming to the millControl of ball mill operation depending on ball load and ore The rod mill is another type of grinding mill used in the copper ore mining process This machine uses steel rods as the grinding media instead of balls, which are commonly used in ball mills The rods grind the ore by tumbling within the mill, similar to the action of a rotating drumUnderstanding the SAG Mill in Copper Ore Mining ProcessMill linings, Weir Rubber Engineering, Salt Lake City, UT 84126, United States of America ABSTRACT Dramatic shortcomings of mill liner designs, especially of large SAG mills, such as rapid failure and even mill shell damage arising from The Selection and Design of Mill Liners 911 Metallurgist
.jpg)
Methods to Estimate AG/SAG Mill Power Requirements
2015年10月20日 (3) Using Don Burgess’ method (11th Mill Operators Conference 2012) They seem to give very different predictions for guiding the selection of SAG mill sizes I tend to favor the updated Barratt method in terms of the rationale behind the approach, but I don’t have access to a database to really check it outA mill is a device, often a structure, machine or kitchen appliance, that breaks solid materials into smaller pieces by grinding, crushing, or cutting Such comminution is an important unit operation in many processesThere are Mill (grinding) WikipediaDOI: 101016/JTRIBOINT201706017 Corpus ID: ; Friction and wear of liner and grinding ball in iron ore ball mill @article{Peng2017FrictionAW, title={Friction and wear of liner and grinding ball in iron ore ball mill}, author={Yuxing Peng and Xu Ni and Zhencai Zhu and Zhangfa Yu and Zixin Yin and Tongqing Li and Liu Songyong and Lala Zhao and Jie Xu}, Friction and wear of liner and grinding ball in iron ore ball mill2019年10月17日 Working Principle of Rod Mill Rod mill is a common equipment for grinding operation in mineral concentrator, 4 Siderite Ore Extraction Method (12:03:04) 8 Types of Iron Ore Magnetic Separator (04:03:13) Research on Vat Leaching Test of A Small Gold MineThe Working Principle and Structure of Rod Mill
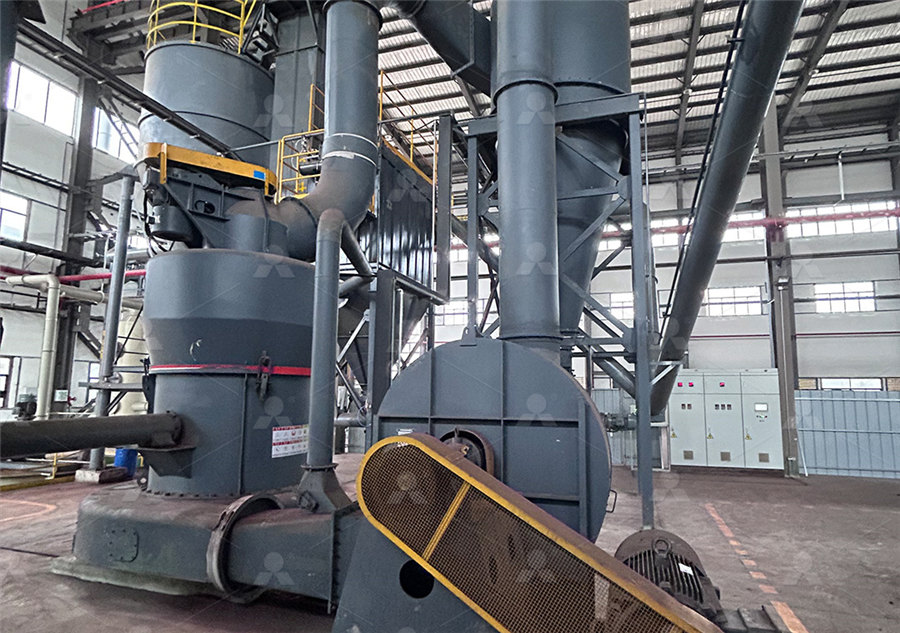
CLUM Ultrafine Vertical Grinding Mill
Raymond mill: 2um content is about 6% or more, the highest fineness is 45um, lowend finished powder Production of coarse powder and general fine powder above 45um, stable operation, high cost performance and high noise Ring roller mill: 2um content is about 20% or more, the highest fineness is 810um, middle and highend finished powderSteel is primarily produced using one of two methods: Blast Furnace or Electric Arc Furnace The blast furnace is the first step in producing steel from iron oxides The blast furnace uses coke, iron ore and limestone to produce pig iron Coal traditionally has been a key part of the cokemaking processSteel Production American Iron and Steel Institute2015年8月3日 PDF The first process that most of the ores or minerals undergo after they leave any mine, is mineral processing or mineral/ ore dressing It is a Find, read and cite all the research you Overview of Mineral Processing Methods ResearchGateA section cutthrough of ball mills A ball mill is a type of grinder filled with grinding balls, used to grind or blend materials for use in mineral dressing processes, paints, pyrotechnics, ceramics, and selective laser sinteringIt works on the principle of impact and attrition: size reduction is done by impact as the balls drop from near the top of the shellBall mill Wikipedia
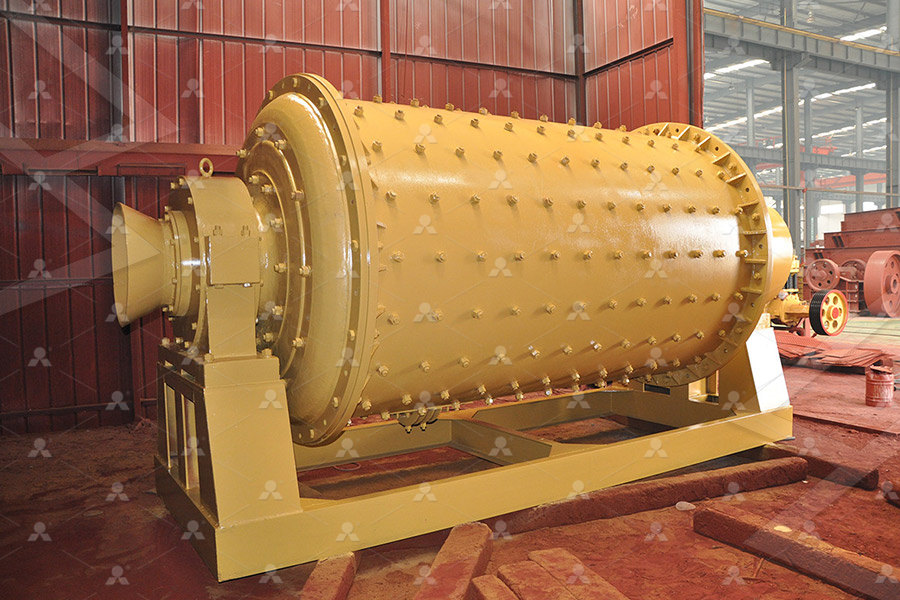
Ore Grinding Methods and Process of Ore Grinding
mill, including its specifications, model, aspect ratio, ore discharging method, and liner form (2) Various working parameters of grinding mill, including fraction of critical speed for grinding mill, filling rate for grinding mill, grinding concentration,grindingcycleload,etc(3)Andgrindingmaterial properties,includingore grindability,