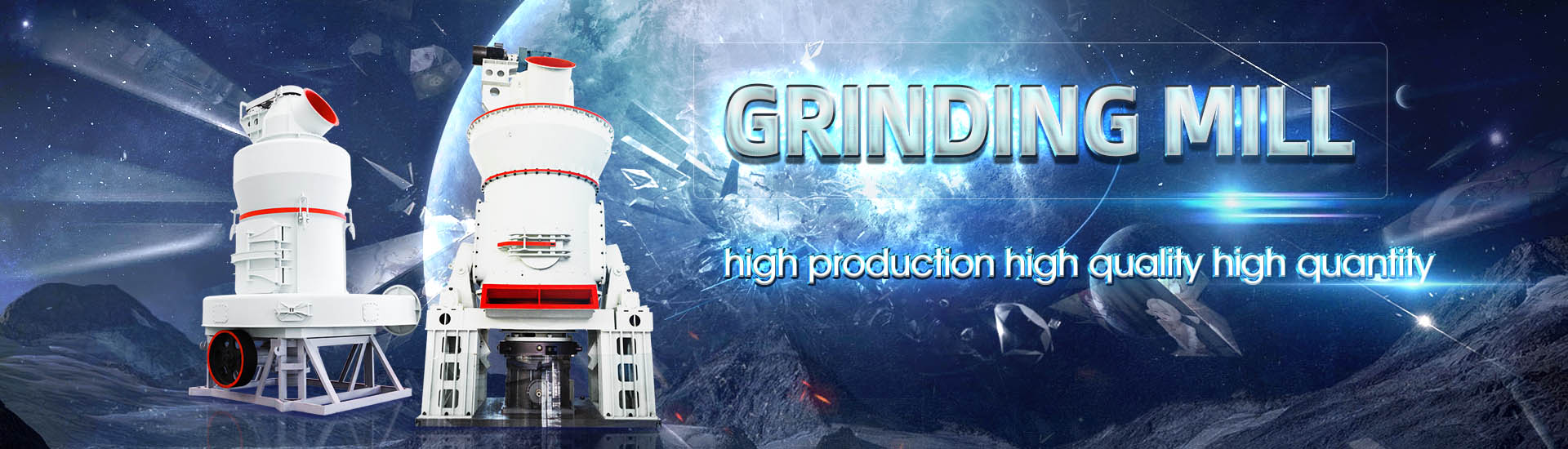
Vertical mill air leakage point
.jpg)
Brief analysis of air leakage in raw meal vertical mills
2024年11月26日 Air leakage in raw material vertical mills is a complex and critical issue Enterprises should address this from multiple angles, including design, installation, and maintenance By optimizing equipment design, enhancing maintenance, and improving sealing Vertical Roller Mills Air Flow Profile Check for False Air Leakage because: •False air after nozzle ring reduces grinding capacity • Any false air reduces drying capacity Influenced by: Optimization of VRM Operation RUCEMRU2024年1月15日 The performance of two new Vertical Roller Mills (VRM) has been analysed using Computational Fluid Dynamics (CFD) The results show notable air ingress from the Optimisation of the performance of a new vertical roller mill by 2020年8月12日 To understand the performance of a vertical roller coal mill, the real operational tests have been performed considering three different coal sources Obtained results indicate that grindingAn investigation of performance characteristics and
.jpg)
Brief analysis of air leakage in raw meal vertical mills
Solve air leakage issues in raw material vertical mills Improve efficiency and reduce energy costs in cement productionTreatment of air leakage in TRM534 raw meal vertical mill system: MA Jifeng, et alTreatment of air leakage in TRM534 raw meal vertical mill systemThe following paper presents and analyses methods of monitoring the key performance factors of a vertical spindle mill that is suited for implementation on older power stations, ie theASS FLOW AND PARTICLE SIZE MONITORING OF PULVERISED 2017年4月1日 In this study, pilot scale tests were performed with a mobile verticalrollermill grinding plant to investigate the relationships between operational parameters The Operational parameters affecting the vertical roller mill
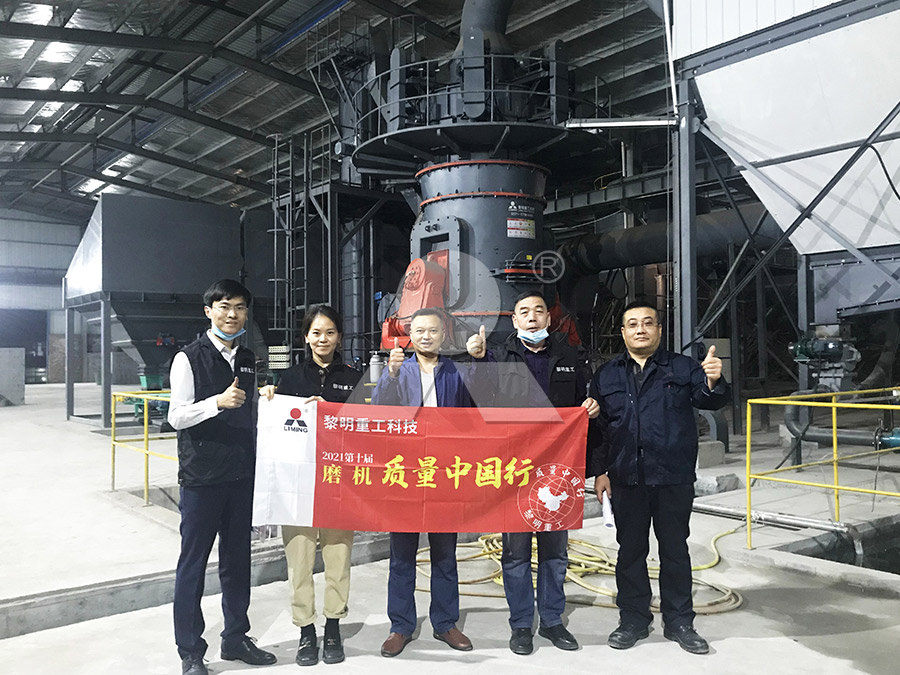
EFFECTS OF VENTILATION LEAKAGE IN DEEP, HOT ROOM Vuma
examples examined, the leakage was found to be up to 85% for ‘Poor’ category seals and up to 50% for ‘Good’ category seals The total air flow [and refrigeration] requirements grow In a cement plant, the air flow to a raw mill is monitored The objective of this monitoring is to achieve the highest possible efficiency of the raw mill Controlling the supply air to such a vertical mill can also lead to considerable energy Volume flow measurement for regulating the air Fora ball mill with a capacity of 2L, if the matching mill pot specification is 25ml or 50ml, you need to purchase a base holder separately Related Products Vibration Mill BKVBM01Vertical Planetary Ball Mill (Square Type) BIOBASEIn the vertical mill production line, in the pulse and air box type pulse dust collector, the dust adheres to the outer surface of the bag When the dustladen gas passes through the dust collector, the dust is trapped on the outer surface of the filter bag, and the clean gas passes through the filter material and enters the inside of the filter bagWays to improve dust removal efficiency of bag filter in vertical mill
.jpg)
Causes of Roller Oil Leakage and Bearing Damage of Vertical Grinding Mill
2020年10月22日 ② The sealing of the flange of the air pressure sealing pipe, and the joint points of the joint bearing on the sealing pipe inside the vertical grinding mill are poor and the air leakage leads to the reduction of the air pressure entering the roller chamber; ③ When the grinding mill is put into operation or shut down, the unreasonable air 2023年11月18日 In order to improve the detection accuracy of vertical barrier leakage, three contamination leakage working conditions, including point leakage only, point and vertical leakage, and horizontal leakage, were simulated by smallscale soil tank tests The dynamic evolution of soil resistivity over time was monitored by electrical resistivity tomography (ERT) Research on the detection of leakage points in vertical barrier 74 Mill discharge Valve is commissioned and kept opened fully 75 Mills should be in their normal operating mode for the Clean Air Flow Tests – and for this, the Mill Seal Air valve must be OPEN and Mill discharge seal air valve also to kept OPEN 76 The Coal Pipes isolation gate near the burner end (in all 4 corners) are kept opened fullyPROCEDURE FOR CLEAN AIR FLOW TEST OF COAL PIPESTherefore, it is critical for cement plant operations to increase the monitoring and control of a vertical raw mill energy process or air leakage because the process is in steady state b) As a result of the process, neither atmospheric nor pressure drop A set of operational parameters was selected with 1025 monthly data points, Assessment of the thermodynamics efficiency of a cement vertical
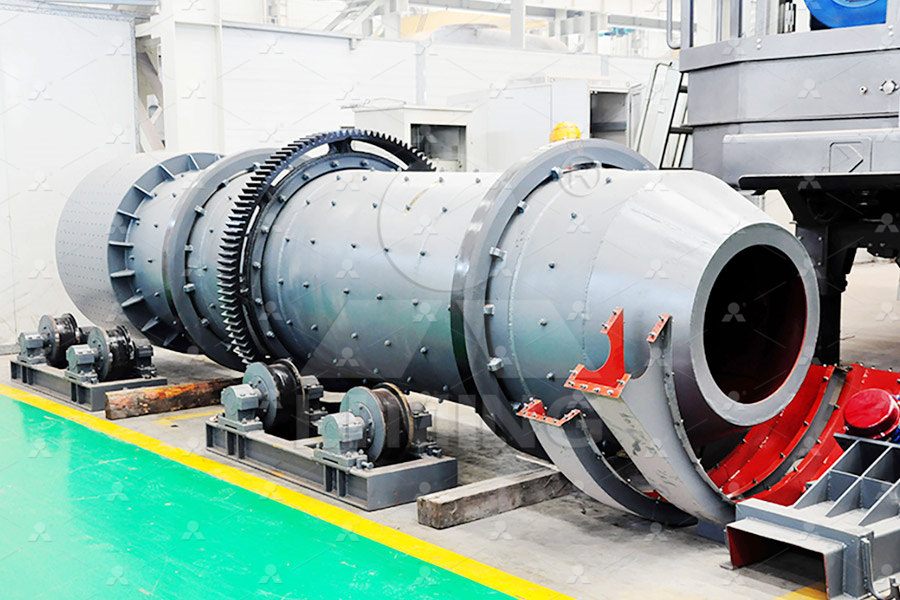
Industrial application of system integration updated technology
The third production line of YongDeng Qilianshan Cement Co, Ltd was updated and put into production in 2010, the raw material mill of which is the TRM534 vertical mill The vertical mill output is 500t/h and the product R 80μm is 12% The vertical mill system has defects such as a large mill pressure difference and a high system negative the entire suction track of the sinter machine, it is difficult to pin point which source of fresh air leakage is contributing maximum to the drop in suction Literature Study In early 70s, the air leakage of the sinter machine was more than 60% The air leakage is generally lower for the newly built sinter machines However, as reported by Maximising sinter machine productivity through identification and pulverized coal flow at desired set point value 1 INTRODUCTION Coal mill is an important component of the thermal power pla nt It is used to grind and dry the moisturized raw coal and transport the pulverized coal ± air mixture to the boiler Poor dynamic A simplified design schematic of a vertical spindle mill is shown in Modeling and Control of Coal Millmeasurements are also useful in determining the level of mill performance (mill air inleakage values—on suction mills), mill heat balance calculations, airflow balance, three points are needed on the RosinRammler Chart to plot the fineness results Four sieves of 50, 100, vertical runs of coal pipingPulverized Coal Pipe Testing and Balancing Storm Technologies, Inc
.jpg)
Vertical roller mill for raw Application p rocess materials
Fig1 Flow of Conventional Vertical Mill Grinding System Mill Kiln IDF (Kiln gas exhaust fan) Fig2 Flow of direct dust collection system Results Power consumption of fan(s) reduces about 3 to4 kWh/t Cost estimation When a mill with a production Vertical roller mill manufacturers Vertical roller mill or VRM is a largescale grinding equipment designed for pulverizing cement raw meal, cement clinker, slag, coal, fly ash, limestone, and other hard grinding materialIt integrates grinding, drying, separation, and conveying in one machine The equipment is widely used in many industries such as cement, electric power, metallurgy VRM In Cement Plant Maximize Energy Saving CNBMSINOMAOn the other hand, when the specimen was tested after removing the PE sheet (and sealing the box perimeter), air leakage increased substantially, and smoke started to leak as the pressure was raised to 5 Pa Smoke emission was (PDF) Air Leakage of Curtain Rachel BeckerInformation on the importance of false air in the kiln and raw mill process in cement plants False air calculation and measurement Comparison between different sealing solutions to reduce false air in kilns The importance of equipment maintenance to reduce false air Manuel Castro November 2019 Rev May 2022 1FALSE AIR IN THE CEMENT MANUFACTURING PROCESS
.jpg)
(PDF) Development law of air leakage fractures in ResearchGate
2018年11月22日 Continuous air leakage from ground mininginduced cracks is a significant cause of coal spontaneous combustion, low oxygen at the working face and other disasters in shallow coal seams2023年8月16日 The leakage rates are dif ferent at each airleakage points in the tunnel W hen the leakage point is closer to the 275 duct inlet, more air is lost throu gh the du ctNumerical Simulation of Tunnel Ventilation Considering Air Leakage The vertical mill allows the installation area to be decreased, leading to a reduction of construction cost 3 Easy operation Material feed, grinding force, air volume and separator feed can be adjusted through a remote control system, which makes the operation easier 4 UBE Vertical Mill UBE Machinery Corporation, LtdTroubleshooting HRM vertical mill hydraulic system of exclusion; No Common malfunctions: cause: Method of exclusion: 1: Air suction pump Inlet pipe bad seal leakage 7、Clear air leakage points 8、 Inspection, replacement of the thermocouple 6: Kiln temperature is too highTROUBLESHOOTING OF cement plant mechanical and electrical equipment
.jpg)
(PDF) Performance Evaluation of Vertical Roller Mill in
2017年9月11日 Many secondcompartment mill studies of particles sampled "through the mill" look at about 10100 plus data points longitudinally; we are looking at 300800 plus data points longitudinally page 05 2 vertical mills introduction page 07 3 principles of vertical grinding systems page 07 31 vertical mill components page 07 32 how does a vertical mill work? page 08 4 a new generation of grinding additives: maga/vm and mape/vm page 08 41 mill output increase page 09 42 quality and water demand optimisation page 09 5Technical Notebook CEMENT ADDITIVES FOR VERTICAL MILLSBecause the air mix is so critical, it is important to avoid air leaks (also known as ‘False air’), where additional unwanted air enters the process One way of finding false air in gas streams of less than 21 % oxygen is to measure the oxygen content at different points in the process Due to its impact on combustion efficiency, theMeasuring false air in cement production ABBThe closed system of vertical ball mill has less air leakage, which can reduce the specification, investment and power consumption of electrostatic precipitator for waste gas treatment Technical Data Model Volume of Barrel(L) Grinding Vertical Ball Mill
.jpg)
Operational parameters affecting the vertical roller mill
Request PDF On Sep 1, 2016, Deniz Altun and others published Operational parameters affecting the vertical roller mill performance Find, read and cite all the research you need on ResearchGateTherefore, when the vertical mill is operated, the control of the inlet and outlet dampers should be balanced by the kiln mill When the vertical mill inlet and outlet dampers are balanced, the system's wind will be balanced and will not affect the pressure at the kiln end Precautions for Starting and StoppingImportant Operation Tips For Cement Vertical MillOxygen percentage of more than 1214% is considered catalyst for fire/explosion risk Rotary feeders (gravel gate), double flap valve are used to stop/minimize cold air leakage into mill system Cold air leakage percentage can be determined by measuring oxygen percentage at inlet and outlet of the circuit element Coal Mill:Coal Grinding Cement Plant Optimization2022年1月10日 Vertical Cement Mill is the main tool used in the final process of making cement at PT Semen Baturaja (Persero) Tbk Vertical Cement Mill is used to mix and grind clinker and corrective materialsAnalisa Kinerja Alat Vertical Cement Mill di Pabrik II PT Semen
.jpg)
Key points for maintenance and care of vertical mills
The cleanliness of the vertical mill is often overlooked but is essential Dust and debris can accumulate and affect the performance and efficiency of the mill Regular cleaning of the mill, including the air intake and exhaust systems, helps maintain proper airflow and 2014年5月1日 vertical air flow separator and this is extensively examined by vertical roller mill pro ducers and users Finite volume as well as di screte element simulation meth ods are used for this task(PDF) Matrix Model Simulation of a Vertical Roller Mill with High The VR5 brings 2axis spindle head capabilities to our midsize VMC platform to create a compact 5axis machine for profiling and contouring midsize partsVR5 5Axis Mill 30Taper Vertical Mills – Haas CNC MachinesResearch on the detection of leakage points in vertical barrier walls using a combined method of ERT and tracer methods Haitao Yu 1 Zhibin Liu 1 Xinchen Cai 1,2 Min Song 3 Liangliang Lu 1Research on the detection of leakage points in vertical barrier
.jpg)
Air Leakage Enerma Certified Energy Advisor
2024年5月24日 Air Leakage Testing: In some cases, it may be beneficial to conduct a blower door test or thermal imaging to assess the extent of air leakage and identify specific problem areas Addressing air leakage not only helps Vertical Roller Mill The vertical roller mill (VRM) shown in Figure 4 is an air swept, mediumspeed, vertical pulverizer with integral classifier It pulverizes coal by applying hydraulicallyloaded grinding pressure through three grin ding rollers onto a rotating bed of coal Grinding pressure can be adjusted to account for variations in coalA Comparison of Three Types of Coal Pulverizers Babcock PowerFigure 51 Breakage function from grinding in a laboratory vertical stirred mill 85 Figure 52 Specific selection function from grinding in a laboratory vertical stirred mill 86 Figure 53 Measured (points) and predicted (dotted lines) product particle size distributionPREDICTING THE PRODUCT PARTICLE SIZE DISTRIBUTION FROM A VERTICAL 2020年11月4日 The 3D geometry model of the vertical roller mill 1: separator outlet; 2: separator; 3: shell; 4: return hopper; 5: grinding roller; 6: wind ring; 7: air inlet; 8 Effects of Blade Parameters on the Flow Field and Classification
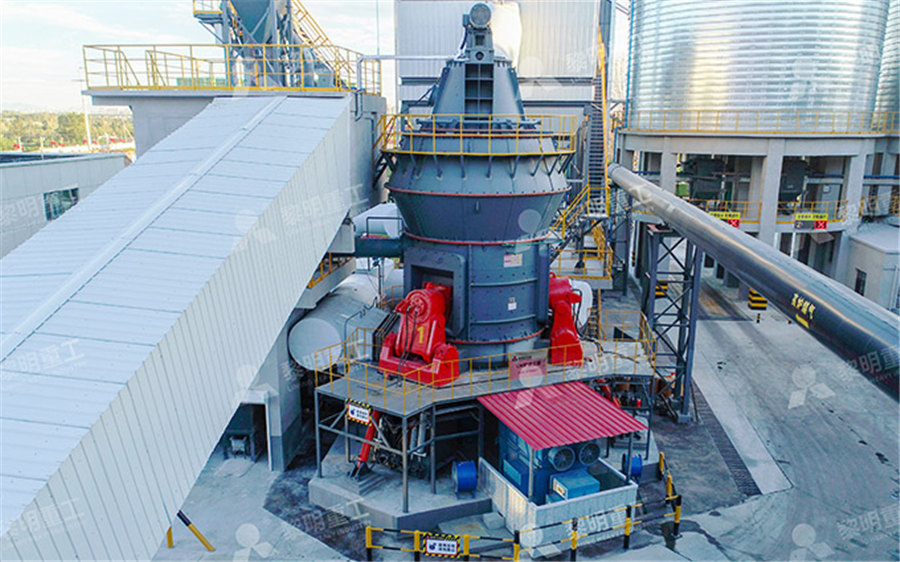
VF2SS 40Taper Mill Super Speed Vertical Mills – Haas CNC
The Haas highperformance SuperSpeed vertical machining centers provide the high spindle speeds, fast rapids, and quick tool changes necessary for highvolume production and reduced cycle times Each SS machine features a 12,000rpm, inline directdrive spindle, an ultrafast sidemount tool changer, and highspeed rapids on all axes The VF2SS is our most popular Super 2021年10月20日 A compressedair system analysis consists of a complete review of the compressedair system from the air intake to the end users, plus a compressedair leak detection and correction program To achieve success in your compressedair system analysis, follow these 12 steps: 1 Conduct a walkthrough of the entire plant or specific areas to be AirSystem Leak Assessment in 12 Steps Power Motion2023年6月1日 The points will lie on the 45°line if the model is good As shown in Fig 5, the 31 samples are largely distributed around the 45°line There are many parameters in the operation of a large vertical mill, such as feed rate, air intake rate, rotation speed, powder output, water consumption, powder particle size, Operation parameters multiobjective optimization method of Vertical roller mills are traditionally airswept mills In the grinding bed there are multiple contact points where pressure is applied on energyefficient size reduction compared to tumbling mills Figure 1: Vertical roller mill operating principle (left: standard configuration, right: Vertical Roller Mills used for the comminution of mineral ores
.jpg)
Coal Mill – Coal Mill In Cement Plant AGICO Cement Equipment
The coal mill grinding system is an important part of the dry process cement manufacturing In cement plants, we usually adopt the air swept coal mill system or vertical mill system as the pulverized coal preparation system, which is arranged at the cement kiln head or kiln tail to provide fuel for clinker calcination However, due to the flammable and explosive