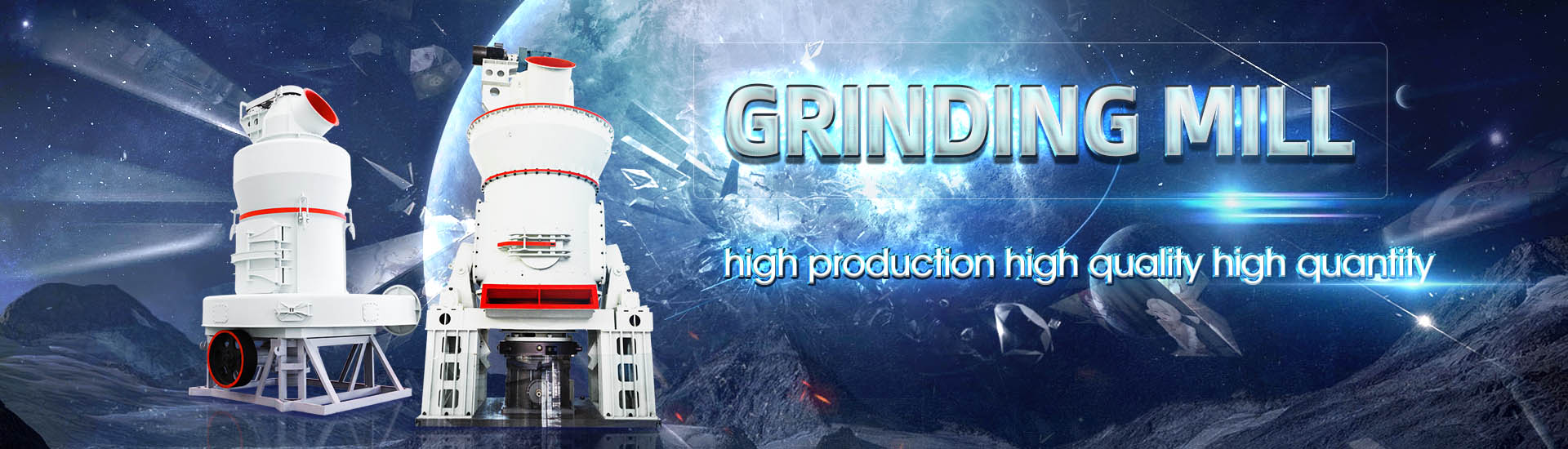
The fineness of rotary kiln coal powder
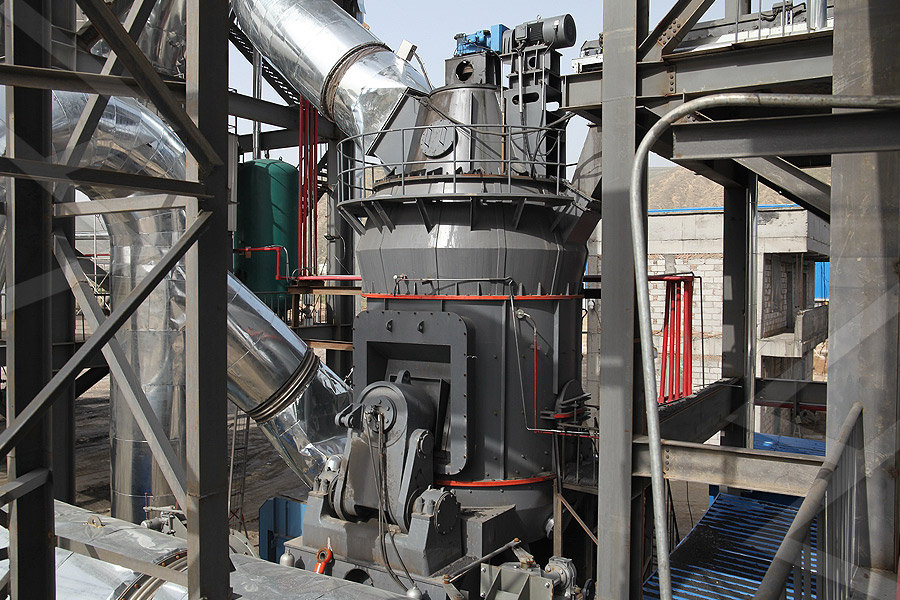
Modeling of Pulverized Coal Combustion in Cement Rotary Kiln
Combining the models of gassolid flow, heat and mass transfer, and pulverized coal combustion, a set of mathematical models for a fullscale cement rotary kiln were establishedThe predicted results indicated that the improved model accounts for the thermal enthalpy of the clinker formation process and can give more insight (such as fluid flow, temperature, etc,) from Modeling of Pulverized Coal Combustion in Cement Rotary KilnOptimizing coal powder combustion within rotary kilns and preheaters is a critical endeavor in the cement industry By understanding the intricacies of combustion stages, adjusting burner designs, and adopting innovative approaches for low How to Accelerate Coal Powder Combustion Inside 2021年8月17日 In order to implement measures to ensure the efficient production of pellets by coalfired rotary kilns, the mechanism and influencing factors on the deposit formation were reviewed The pellet powder and coal The Deposit Formation Mechanism in CoalFired
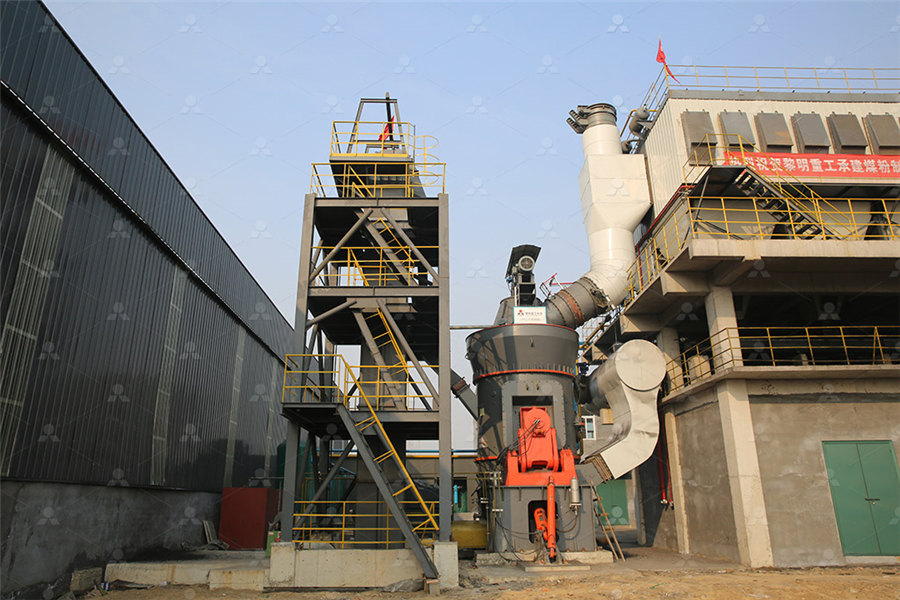
Rotary kiln process: An overview of physical mechanisms, models
Solid transport, heat transfer and thermochemical transformation are discussed in detail The heat and mass transfer modeling process in rotary kilns is summarized The commonly used 2023年2月25日 This article presents the key stages in the modeling of rotary kilns First, the parameters characterizing the transport of the solid load are presented in detail The second Rotary kiln process: An overview of physical mechanisms, models 2020年12月11日 This paper represents the medialization of alternative fuels cocombustion, in a cement rotary kiln, established on the commercial computational fluid dynamic (CFD) software ANSYS FLUENT The focus is placed on the Coal and Biomass CoCombustion: CFD Prediction of 2024年5月28日 The issue of ring formation in rotary kilns poses a significant obstacle to the efficient and costeffective production of oxide pellets This study focuses on sampling and Inhibiting the Accretion in the CoalFired Rotary Kiln of HighSilica
.jpg)
Characterization and comparison of deposits in a coalfired rotary
2022年5月1日 The formation deposit problem becomes more severe for iron ore fluxed pellet production by the graterotary kiln process, especially for high silica iron ore and when Correspondinly, Taeda calcium aluminate rotary kiln holds obvious energy saving effect Hot air from kiln head cover can be used to dry coal powder Coal powder fineness can be flexibly adjusted through dynamic powder selecting machine so that to provide convenience for full combustion of coal powderCalcium Aluminate Powder Rotary Kiln – Zonelion Taeda Rotary 2019年6月4日 KONA Powder and P article Journal, Vol 32, 2015, pp 115130 4 Minimum response time of a large coal fired rotary kiln (80 m in length) is approximately 34 hours View fulltext(PDF) Operation of CoalBased Sponge Iron Rotary 2024年5月30日 Solution II: Easily prevent kiln ring formation Ensuring normal rotary kiln flame is one challenge; another is material looping This occurs when furnace charge adheres in a ring shape to the inner wall of the hightemperature zone Minor adhesion is termed kiln skin, while thicker adhesion affecting furnace operation is called ring formationFacing Rotary Kiln Challenges? 4 Solutions to Help You!
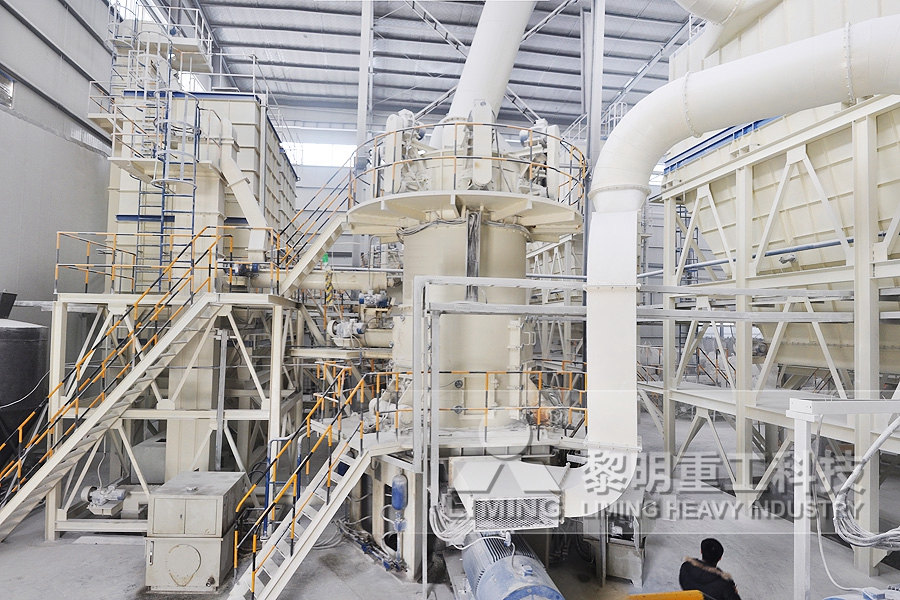
Everything you need to know about Kiln System Operations in
Recommended Coal Fineness Fuel Feed Rate In a rotary kiln system producing cement clinker, gas flows are countercurrent to material flows Gases enter the kiln as secondary air at about 600°C – 1100°C and rise abruptly to over 1750°C as heat from fuel combustion, Rotary kiln Electromagnetic Rotary Kiln; External Heating Electric Rotary Kiln; ensuring the desired fineness and quality of coal powder coalfired boilers for power generation and heating boilers in the metallurgical industry, coal powder preparation in shaft kiln, coal chemical industry Type specification: VRM800M: VRM1100M HighEfficiency Vertical Coal Mill Enhancing Coal Pulverization2023年5月15日 In the rotary kiln, the raw material particles gradually move towards the kiln head with the rotation of the rotary kiln, and are calcined into petroleum proppant ceramsite sand at a temperature of 1400°C~1600°C in the firing zone The ceramsite sand enters the single cylinder cooler for cooling, and the secondary air of the cooler enters the Bauxite Rotary Kiln Calcination Process and Refractory as well as heat economy of the kiln he type of heat transmitting element T would influence the amount of ash which absorbed by the material in process The dust absorbing elements installed and the extent to which the dust is recycled to the rotary kiln will also have its influence The coal ash would thus accountEFFECT OF COAL ASH CHARACTERISTICS ON KILN
.jpg)
Powder Fineness (Types of Powder) Pharmaguideline
2023年6月3日 Superfine powder A powder of which not less than 90 percent by the number of the particles are less than 10 micron size When the fineness of the powder is described by means of a number, it is intended that all the particles of the powder shall pass through a sieve of which the nominal mesh aperture, in /lill, is equal to that number2024年5月28日 The issue of ring formation in rotary kilns poses a significant obstacle to the efficient and costeffective production of oxide pellets This study focuses on sampling and analyzing deposit formation at various points along the longitudinal axis of a 40mlong, highsilica, pellet coalfired rotary kiln The primary factors influencing deposit formation in the kiln Inhibiting the Accretion in the CoalFired Rotary Kiln of High THE ROTARY KILN IN THE METALLURGICAL INDUSTRY About 1900, various metallurgists were experimenting with the rotary kiln for nodulizing fluedust, fine iron ores, etc Edison conducted experiments, for example, on the fine concentrates obtained from his magnetic separators Within a few years plants were established for this purpose(PDF) History of the rotary kiln Fathi Habashi AcademiaCPG has an experience of successfully executing numerous complete Rotary Kiln Cement Green Field Projects, Cement Rotary Kiln Plant and Rotary Kiln Turnkey Cement Plant To make our solution easily understandable, we have split it into three sections: Raw Material Crushing, Grinding And ,Blending; Pyro Processing; Cement ProductionTurnkey Rotary Kiln Cement Plant Manufacturers and
.jpg)
Rotary kiln process: An overview of physical mechanisms, models
2023年2月25日 The rotary kiln is used in many solid processes, including drying, incineration, heating, cooling, humidification, calcination and reduction This widespread application can be attributed to factors such as the ability to handle varied loads, with large variations in particle size [1]The rotary kiln is a slightly inclined steel cylinder that rests on supports (bearing rollers) 2018年2月12日 In order to clearly reveal coal combustion behaviors and quantitatively evaluate using coal in rotary kiln, combustion behaviors of four coals (C13, C23, C32 and C6 coals) and their blended coals Combustion Behavior of Coals in Rotary Kiln and TheirKEY WORDS: siderite; low rank coal; coalbased direct reduction; DRI; semicoke; rotary kiln obtained sponge iron powder with iron grade in range of 8485%–8850% and metallization degree above 90% after magnetic separation of coalbased reduction of siderite in a fixed bed reactor Wei7) crushed the siderite ore to −2 mmCoproduction of DRI Powder and Semicoke from Siderite Ore 2023年1月1日 The utilization of coal in the cement and concrete industries takes three basic forms: (1) as a fuel in the production of cement clinker; (2) ash produced by burning coal in power stations is used as a component in cement rotary kiln feeds; (3) ash produced by burning coal in power stations is used as a mineral additive in concrete mixesCoal utilization in the cement and concrete industries
.jpg)
Coal pyrolysis in a rotary kiln: Part II Overall model of the furnace
Coal Pyrolysis in a Rotary Kiln Part 2: Overall Model of the Furnace FABRICE PATISSON, ETIENNE LEBAS, FRANÇOIS HANROT, DENIS ABLITZER AND JEANLEON HOUZELOT Abstract — In order to simulate coal pyrolysis in a rotary kiln in the steady state regime, a mathematical model has been developed which calculates the temperatureMathematical Model of the Aluminum Oxide Rotary Kiln × Close Log In Log in with The activation of coal applying physical or thermal method is sulfate (BAAS), a white powder with a particle size ranging between 20 and 100 F A rather large part (205070) of the powder is carried away from the kiln by the gas stream and is recovered Mathematical Model of the Aluminum Oxide Rotary Kilnand coal and coal ash in the rotary kiln12–14 Previous studies have shown that the ring of rotary kiln during the production of pellets from hematite mainly comes from preheated pellet powder Research on the ring formation mechanism of magnesian flux2024年1月1日 Rotary kiln is the thermal equipment for hightemperature heat treatment of solid raw materials in a rotary cylindrical kiln, also called rotary furnace, which is a continuous furnace The rotary kiln (Fig 1 ) is mainly composed of kiln body, kiln lining, rolling ring, supporting device, transmission, discharge end hood, sealing device, dust collection chamber, combustion Rotary Kiln SpringerLink
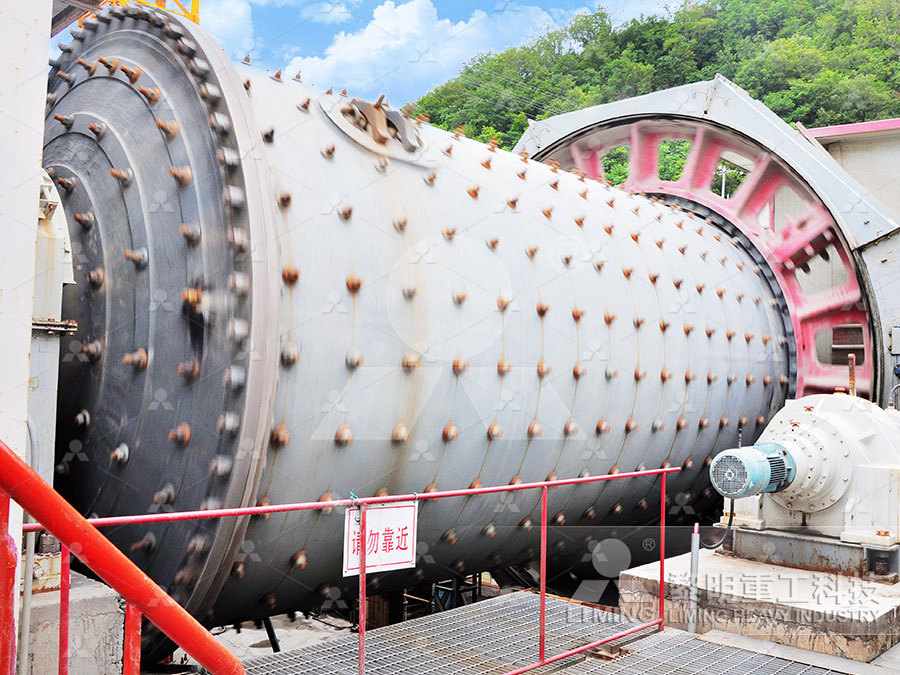
The Deposit Formation Mechanism in CoalFired Rotary Kiln for
22 The Distribution of Deposit in CoalFired Rotary Kiln The distribution of deposits in a grate and rotary kiln is mainly affected by pulverized coal injection and temperature field [21,22] As shown in Figure2, at the heads of the rotary kiln, pulverized coal is sprayed with highpressure air and burned to provide heat2020年4月14日 There are different traditional calcination processes of kaolin, eg, fixed bed process (such as tunnel kiln, down flame kiln, shuttle kiln, push plate kiln and heat preservation cylinder), moved bed process (such as shaft kiln, rotary kiln and multilayer open hearth furnace) [1,2,3,4]But, there are more or less intractable disadvantages in these modesResearch and Design of Suspension Calcining Technology and Process introduction Vertical coal mill, also known as vertical roller coal mill or vertical coal grinding mill, is a mechanical equipment for crushing and grinding coal into coal powerMainly used for grinding raw coal, bituminous coal, and other fuels into coal powder, which is supplied to rotary kiln and other kilns in the cement plant and thermal power plantcoal grinding machine CHAENG2021年8月17日 The depositforming problem is one of the main bottlenecks restricting the yield and production benefit of iron ore pellets produced by coalfired rotary kilns In order to implement measures to ensure the efficient The Deposit Formation Mechanism in CoalFired
.jpg)
(PDF) Coal pyrolysis in a rotary kiln: Part II Overall model of the
Fig 1—Trajectory of a grain in a rotary kiln 4 In the general case where the height of the bed H varies along the axis z (cf Figure 2), the angle θ varies The charge profile H(z) generally depends on the solid flowrate and on the heights of any diaphragms present at the entrance and exit of the rotary kiln2023年7月3日 Dephosphorization is essential for utilizing highphosphorus iron ore (HPIO), and this work prepared reduced iron powder via reductive roasting in a semiindustrial rotary kiln follower by Preparation of Reduced Iron Powder from High Phosphorus Iron 2012年5月1日 In order to simulate coal pyrolysis in a rotary kiln in the steadystate regime, a mathematical model has been developed which calculates the temperature profiles in the charge, the gas, and the (PDF) Coal pyrolysis in a rotary kiln: Part II Overall model of the 2017年10月1日 Ash melting characteristics of five coals up to 1873 K were characterized using Thermomechanical analysis (TMA) to predict their ash deposition tendency during coal combustion in a rotary kiln Effect of coal ash on ring behavior of ironore pellet powder in kiln
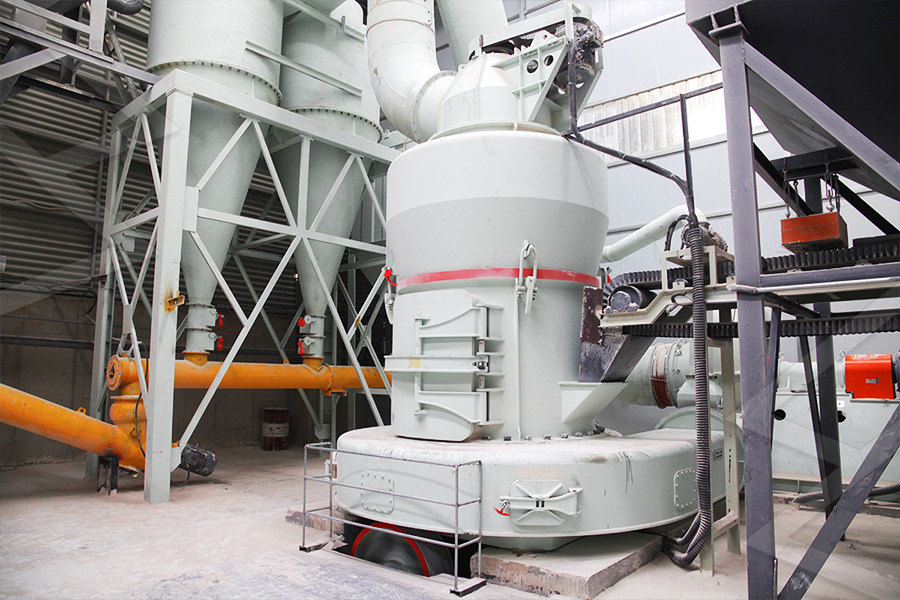
Particle motion simulation and pulverized coal injection
2022年3月16日 The production process of direct reduced iron from titanomagnetite by coal reduction in air in rotary kiln is a key step in the extraction of titanium and iron This process is conducive to alleviating the stocking problem of a large amount of Tibearing blast furnace slag The relationships between particle movement and pulverized coal injection combustion in 2022年4月19日 Powder Bulk Processing Using rotary kilns for hightemperature bulk solids processing April 19, 2022 The rotary kiln’s diverse capabilities have made it a cornerstone of modern industry, and as pressure to build a circular economy intensifies, the reach of this thermal processing device is evergrowingUsing rotary kilns for hightemperature bulk solids processingFig 1—Trajectory of a grain in a rotary kiln 4 In the general case where the height of the bed H varies along the axis z (cf Figure 2), the angle θ varies The charge profile H(z) generally depends on the solid flowrate and on the heights of any diaphragms present at the entrance and exit of the rotary kiln(PDF) Coal pyrolysis in a rotary kiln: Part II Overall model of the kiln Fig4 Rotary kiln: Clinkerisation Process The kiln composes the clinker in the form of mould like balls, which consists of silicates, aluminates, and ferrites of calcium Clinker along with blast furnace slag and coal fly ash is ground to a fine and matching powder, which is called cementDevelopment and Evaluation of Mathematical Model based
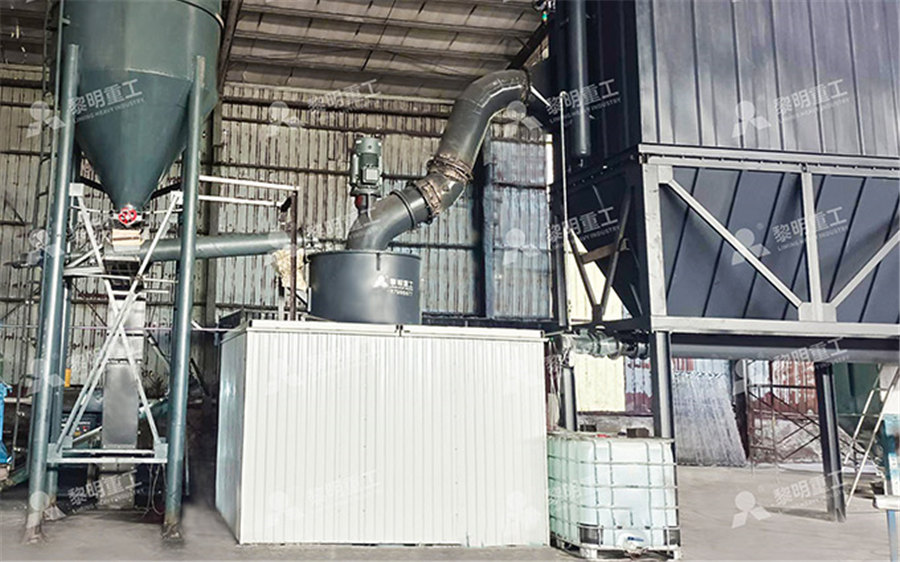
(PDF) Coal pyrolysis in a rotary kiln: Part II Overall model of the
Coal Pyrolysis in a Rotary Kiln: Part II Overall Model of the Furnace ´ FABRICE ´ PATISSON, ETIENNE LEBAS, FRANÇOIS HANROT, DENIS ABLITZER, and JEANLEON HOUZELOT In order to simulate coal pyrolysis in a rotary kiln in the steadystate regime, a mathematical model has been developed which calculates the temperature profiles in the charge, the gas, and the What’s more, the proportion of coal used in decomposition furnace at kiln tail and injected at kiln head should be controlled at 6:4 to increase the mixing degree of coal ash with raw materials in decomposition furnace and reduce the negative Calcining Technology Of Clinker Kiln Cement Rotary Poor Quality of Coal Powder: Subpar coal powder can result in incomplete combustion, affecting clinker quality Unstable Thermal System: Inconsistent kiln temperatures can lead to improper clinker formation Excessive Material Layer Thickness: A thick material layer can prevent proper burning, leading to high fCaO contentAnalysis of Cement Kiln Production Malfunctions and Their SolutionsROTARY KILN CONSTRUCTION While FEECO rotary kilns are custom designed around the material to be processed, in general, there are some standard components that serve as the basic design of a rotary kiln The diagram shown on page 8 illustrates some of the common standard components found on a basic directired kiln A diagram of anThe FEECO Rotary Kiln Handbook FEECO International Inc
.jpg)
The problems of rotary kiln of cement and their remedies
2019年2月1日 2coal fineness (maximum reside 50% The interior of a rotary kiln has been acquired The study of basic refractories corrosion by cement kiln materials was carried out with powder tests and In addition, too high temperature will bring about a risk of ring formation in rotary kiln and more energy consumption In consideration of that operation reduction temperature should be lower by 100–150°C than the softening temperature of coal ash in rotary kiln, therefore, the optimum reduction temperature is recommended at 1050°C 312Coproduction of DRI Powder and Semicoke from Siderite Ore clinker, coalfired, fourstage preheater kiln with planetary cooler • a mothballed f32 x 90m long, 320tpd clinker, petcokefired, wetprocess kiln with a short rotary cooler Case study 1 – converting a preheater kiln An existing kiln, which runs for only six months per year for clinker production, was studied The client approachedClay calcining technologies: the rotary kiln approach1 Saving Energy Air swept coal mill is an ideal coal processing equipment that can both grind and dry, with characteristics of high efficiency, energy saving, environmental protection, 8% and above of its grinding coal can pass through the 200 mesh screen, and the water content can be under 2%, it is an ideal grinding equipment for coal powders that are used in industrial Pulverized Coal Preparation Pulverized Coal Grinding Plant Coal
.jpg)
(PDF) Coproduction of DRI Powder and Semicoke from Siderite
2015年11月26日 Coproduction of DRI Powder and Semicoke from Siderite Ore and Low Rank Coal by Excessive Coalbased Direct Reduction in Rotary Kiln November 2015 ISIJ International 56(1)