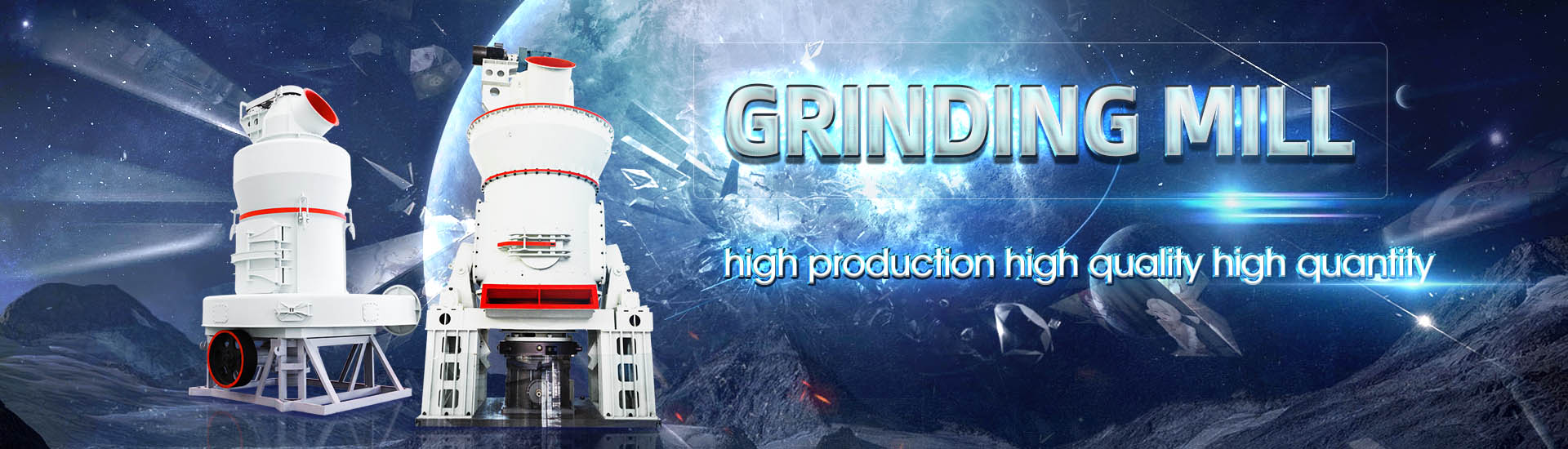
Ore crushing dust coefficient
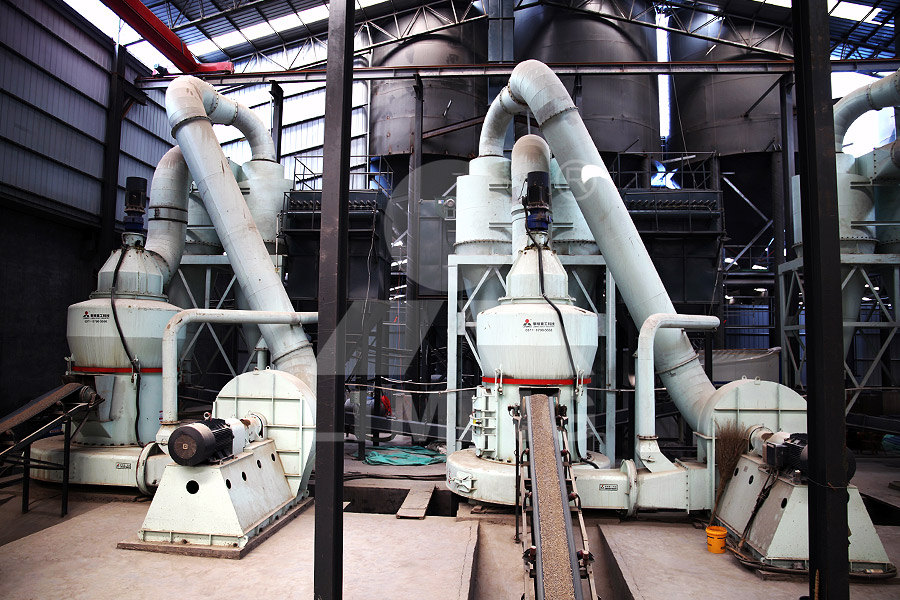
Classifying iron ore with water or dust adhesion combining
2024年10月1日 Hyperspectral imaging (HSI), a promising technique integrating imaging and spectroscopy, can help sort iron ores with different total iron (TFe) contents However, the Iron ore pellets degrade and generate dust during transportation and handling as well as during the iron making process This leads to material losses and effects the process efficiency in a Friction Forces and Mechanical Dust Generation in an Iron Ore 2024年7月15日 CCC enables the enrichment of coarser and cleaner graphite In this study the comminution methods of graphite bearing ore were compared by using five different crushing Continuously compressing crushing towards a dry processing 2019年1月1日 For the first time, the iron ore samples of cubic geometry were tested using a nonuniform volumetric compression unit Application of the ultrahigh frequency field resulted in ultimate strengthResearch into the crushing and grinding processes of
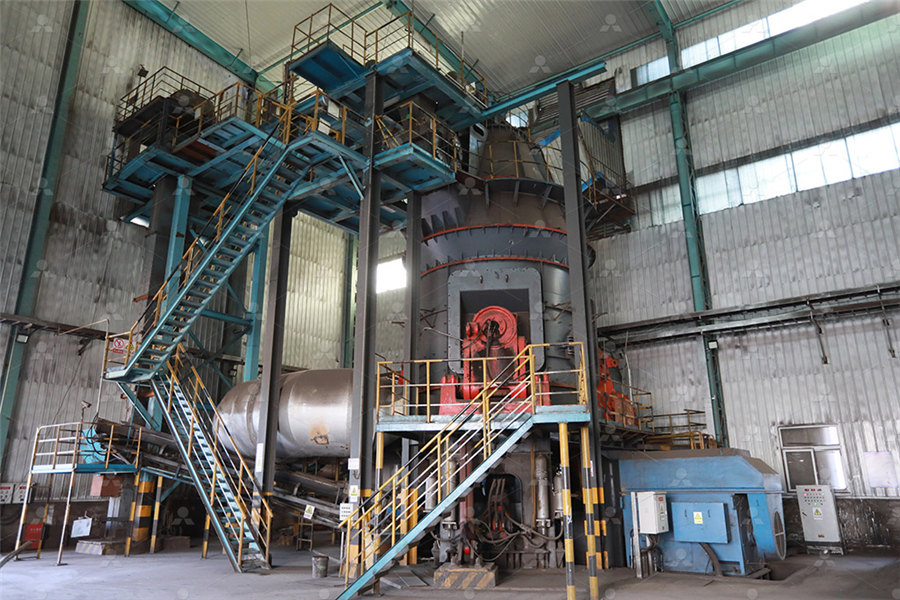
Impact Crushing Characteristics and Relationship
2023年5月15日 Based on the JK Drop Weight test and principle of selective crushing, a multicomponent complex ore with its component minerals, ie, pyrrhotite, sphalerite, and quartz, was used to explore the impact crushing 2018年11月1日 Investigations on rock crushability have become an important issue in mining operations and the manufacture of industrial crusher equipment The main objective of this research is to quantify the(PDF) New testing methodology for the quantification 2023年7月22日 Ore coarse crushing is a process of crushing ore blocks with a feeding particle size of 500–1500 mm to 125–400 mm The maximum crushing ratio of coarse crushing is Ore Crushing SpringerLink2023年6月3日 Ore feeding speed is measured by the frequency modulation regulators of feeding equipment such as vibrating feeder, disk feeder, and heavy plate feeder It is generally MeasurementControl for Crushing and Screening Process
.jpg)
Analysis on the impact crushing dust generation test method and
2021年4月27日 Experimental study was made on the breaking energy of two coal samples by the coal solidity coefficient tester,the test results showed that the breaking mechanism of coal 2015年8月3日 PDF The first process that most of the ores or minerals undergo after they leave any mine, is mineral processing or mineral/ ore dressing It is a Find, read and cite all the research you (PDF) Overview of Mineral Processing Methods2023年7月20日 Besides, mill utilization coefficient refers to the amount of raw ore processed by per cubic meter of mill effective volume per unit time (4) Xiao QF (2012) Crushing and grinding, 3rd edn Metallurgical Industry Press, Beijing Google Scholar Sun CY (2015) Handbook for mineral processing engineers, vol 1 Ore Grinding SpringerLink2023年12月1日 Due to the decreasing reserves of highgrade iron ore and secondary resources used for steelmaking, it has become an important research and development area to improve the grade of iron ore through crushing (Gul et al, 2014)The quality of iron ore crushing directly affects the performance of pellets and sinter, so as to influence the quality and performance of Crushing characteristics and performance evaluation of iron ore
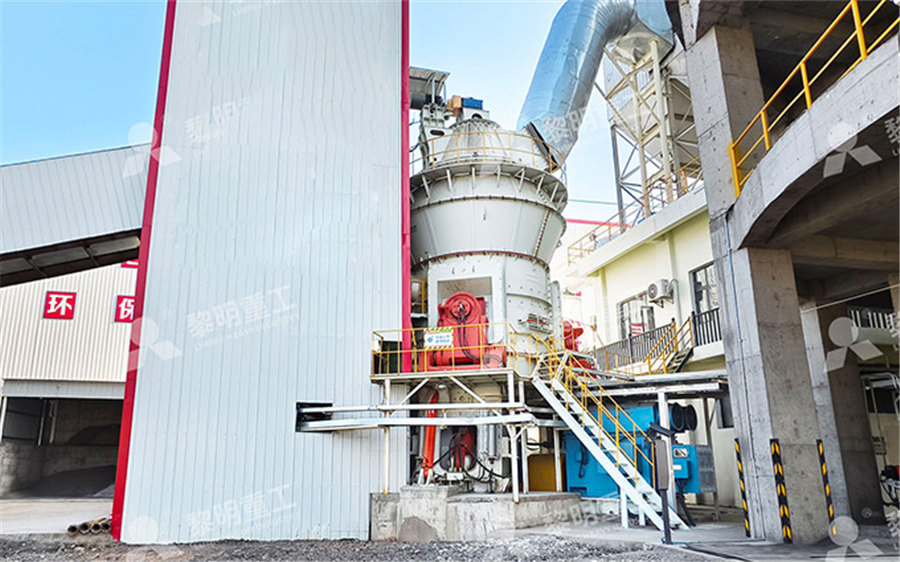
Ore Crushing SpringerLink
2023年7月22日 Ore crushing is the process of breaking, splitting, extrusion, There are two methods: (1) Fragility coefficient method The crushability factor is the ratio of the crusher’s ability to crush pending ore and the crusher’s crushing mediumhard ore under the same conditions2022年8月31日 The crushing resistance of Tongkeng ore increases with the decrease in particle size, and the crushing effect is more easily affected by particle size than that of Gaofeng ore For the same ore, the accuracy order of the three methods is: PSO–BP method > JK dropweight method > B III methodGrinding Modeling and Energy Efficiency in Ore/Raw Material 2023年3月31日 The fixed iron ore crushing station has a permanent concrete foundation, The cone crusher can still maintain high load capacity in high dust and high impact environments, The hydraulic adjustment device of the discharge opening has the advantages of low overload coefficient when passing through non crushing objects, The 4 Types Iron Ore Crushing Stations You Must Know2017年5月21日 A second source of water to the grinding section is derived from fresh water to the crushing and ore storage dust collection systems when operating Flotation consists of one stage of rougher flotation of three cells, three stages of rougher scavenger flotation and one stage each of cleaner (3 cells), recleaner (2 cells) and cleaner scavenger flotation (3 cells)Copper Ore Crushing, Grinding Flotation 911Metallurgist
.jpg)
Friction Forces and Mechanical Dust Generation in an Iron Ore
2017年3月7日 Iron ore pellets degrade and generate dust during transportation and handling as well as during the iron making process This leads to material losses and effects the process efficiency in a DoseDust = ConcDust x DCFDust x tWorker x VRateWorker where DoseDust dose due to the inhalation of radioactive dust, in mSva1 ConcDust ambient concentration of ore dust, in mBqm3 (this quantity is measured, for example using the MyRIAM) DCFDust dose conversion factor for inhalation of radionuclides, mSvmBq1 tWorker time period of worker ORE DUST DOSE CONVERSION FACTOR VO Consulting2020年11月21日 Abstract Dust suppression system plays a significant role in mining and allied industries It has become an integral part of the environmental management system Dust emission from mining and mineral processing industries poses environmental and health problems to workers and surrounding people Dust creates a reliability issue in machinery and Intelligent dry fog dust suppression system: an efficient 2015年12月27日 High powered microwave treatment of carbonate copper ore; Hydrometallurgical recovery of gold from arsenopyrite refractory concentrates; Impact crushing to the relationship of energy and particle size in comminution; Impact of metal prices on plant optimization Influence of additives on physicochemical properties of sodium aluminate solutionMineral Processing Articles 911Metallurgist
.jpg)
(PDF) The Effects of Blasting on Crushing and Grinding
2003年1月1日 Mining is typically conducted through a set of interdependent unitoperations, which commonly include drilling, blasting, digging and hauling, in order to deliver the required ore material into The process of reducing mined ore for processing is known as ‘comminution’, which is defined as ‘the action of reducing a material, especially a mineral ore, to minute particles or fragments’; this is normally achieved at mining operations Gyratory Crusher (Gyratory Crushers Explained)2021年6月30日 The object of research is traditional mining technologies and technical means in combination with underground block leaching (UBL) of metals from rock ores with their preliminary crushing with (PDF) EVALUATION OF EFFICIENCY AND ENVIRONMENTAL 2019年10月28日 In general, all kinds of concrete crushers would produce plenty of dust when it is crushing the ore materials The reason why it produces so much dust is that the material through the feeding port is crushed then being sent to the conveyor for the next process, during which a lot of dust with high Read MoreWhat Kinds of Concrete Crushers Reduce Air Dust What Kinds of Concrete Crushers Reduce Air Dust Pollution in a Crushing
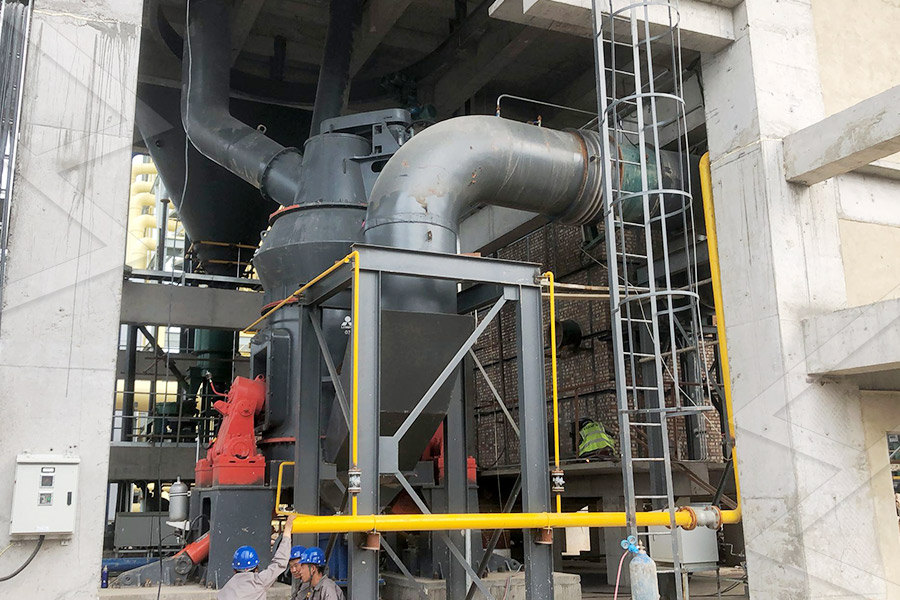
Crushing in Mineral Processing 911Metallurgist
2015年12月26日 In mineral processing or metallurgy, the first stage of comminution is crushing Depending of the type of rock (geometallurgy) to be crushed, there are 2 largely different techniques at your disposition for crushing rocks In principle, compression crushing is used on hard and abrasive rocks by placing them between a high wearresistant plate/surface2021年9月10日 High energy consumption in ore crushing brings great challenges to the mining industry Microwave irradiation provides a promising solution for rock breaking However, there is currently a lack of detailed understanding of the microwave parameters regarding magnetite ore The purpose of this study is to fully understand the potential value of microwave irradiation Study on Magnetite Ore Crushing Assisted by Microwave Irradiation 2015年7月1日 Iron ore pellets abrade during handling and produce dust This study was conducted to determine what factors affect pellet dustiness, and whether dustiness can be related to the abrasion indexIron Ore Pellet Dustiness Part I: Factors Affecting Dust Generation2023年6月3日 It mainly includes crushing process control, crushing appliance fault diagnosis, and automatic distributing control Crushing Process Control To ensure the continuous, stable, and safe operation of the ore crushing production process, it is necessary to monitor the running state and parameters of key equipment (such as crusher and belt conveyor) in real time for MeasurementControl for Crushing and Screening Process
.jpg)
AusIMM – Leading the way for people in resources
%PDF16 %âãÏÓ 4215 0 obj > endobj 4235 0 obj >/Encrypt 4216 0 R/Filter/FlateDecode/ID[87C03FABF6FB2246BC4F9AB649B4B217>]/Index[4215 26]/Info 4214 0 R/Length 101 2016年3月11日 In the crushing section, the ore as it comes from the mine is broken down dry to a size suitable for the wet grinding machines ; these can, if necessary, be as it comes from the mine in two steps to a maximum size of Crushing Plant Flowsheet DesignLayout2019年7月15日 Manganese ore smelting is reviewed in terms of processing parameters such as feed material particle sizes, energy input methods, heat transfer modes, smelting mechanisms, experimental findings on A Review of Ore Smelting in High Carbon 2023年12月1日 The processing of iron ore involves crushing (Jiang et al, 2023), which generates a considerable amount of dust that adheres to the surface of the ore (Zheng et al, 2021) Because this dust is stripped from the interior of the ore rather than from common airborne dust or sand (Sairanen and Rinne, 2019), its impact on the spectra may not be consistent with Crushing characteristics and performance evaluation of iron ore
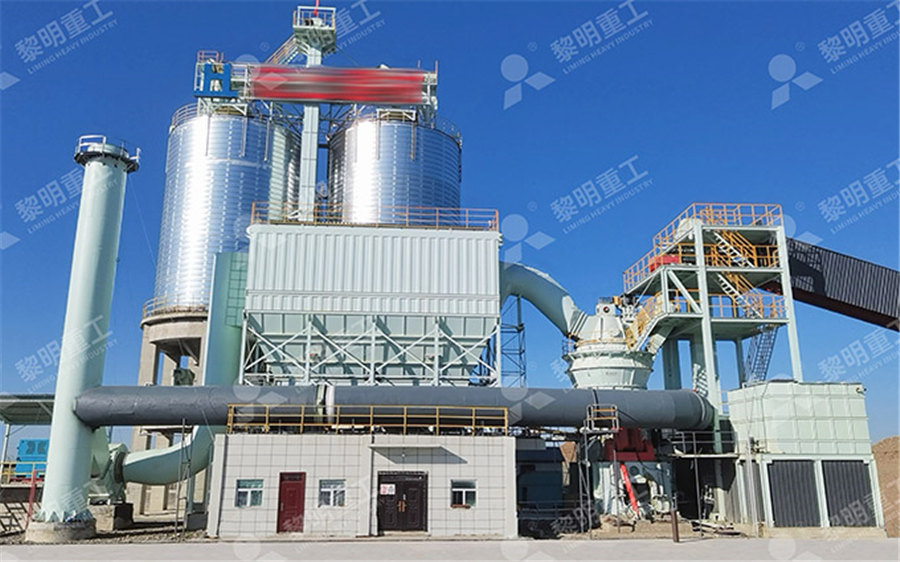
Friction Forces and Mechanical Dust Generation in an Iron Ore
where t is time 22 Evaluation of PSD of Dust Particles The outlet was connected to a particle analyzer, Dekati ELPI+ (Electrical Low Pressure Impactor), which can measure the particle concentration in the size range of an aerodynamic diameter (d a) ranging from 6 nm to 10 μmBefore starting the experimental measurements, the air in the container was analyzed to 2023年5月15日 Mechanical behavior and particle crushing of irregular granular material under high pressure using discrete element methodMechanical behavior and particle crushing of irregular granular 2009年12月8日 To examine how effective various reagents were in reducing respirable dust from iron ore, a novel dust tower was used A diagram of this unique apparatus is given in Fig 2This tower is unique in that it simulates material handling while allowing for direct PM 10 measurements Previous studies using this apparatus indicated that wetting agents such as Suppression of airborne particulates in iron ore ScienceDirectMedia Attributions; Metal deposits are mined in a variety of different ways depending on their depth, shape, size and grade Relatively large deposits that are quite close to surface and somewhat regular in shape are mined using openpit mine methods (Figure 815 in Section 81)Creating a giant hole in the ground is generally cheaper than making an underground 82: Mining and Ore Processing Geosciences LibreTexts
.jpg)
Dust emission reduction in iron ore concentrate production plant
2021年3月15日 Dust emission is one of the critical problems of the mining industry Dust emission can cause respiratory diseases among workers and adjacent residents of the factory and environmental pollution in the region This study aims to reduce dust emissions of an iron ore concentrate plant in Iran Applying dust control methods can affect the production process 2019年1月15日 In this study, high voltage pulse breakage was used to study the breakage process of copper ore The particle size, shape coefficient and preferential crushing index (Δαi) were determined using Preferential sequence crushing of copper ore based upon high 2020年2月11日 Gholami et al (24) reported an association (OR: 1155, CI: 11333) between respirable dust exposure among iron ore mine workers and increased occurrence of shortness of breath (23)Respiratory Symptoms and Diminished Lung Functions Associated 2020年1月30日 The explosion characteristic parameters of dust mainly include the maximum explosion pressure (P max), minimum explosible concentration (MEC), maximum explosion pressure rise rate ((dP/dt) max), and explosion Explosion Pressure and Minimum Explosible
.jpg)
Mineral Dust Emissions at Metalliferous Mine Sites
2016年10月19日 This review considers aspects of mineral dust related to the mining of metalliferous ores including: (a) sources of mineral dust at mine sites (ie land clearing, drilling and blasting, transport operations, crushing, milling , screening, stockpiles); (b) control measures to reduce dust generation; (c) monitoring techniques; (d) mineral dust characterization to DOI: 101016/JPOWTEC202104064 Corpus ID: ; Analysis on the impact crushing dust generation test method and its influencing factors @article{Zheng2021AnalysisOT, title={Analysis on the impact crushing dust generation test method and its influencing factors}, author={Lei Zheng and Dewen Li and Shengdong Xu}, journal={Powder Technology}, Analysis on the impact crushing dust generation test method and 2012年11月24日 A CFD model has been developed using the ANSYS CFX 100 software to simulate the dispersion of dust resulting from blasting operation in several limestone quarries in the presence of the physical (PDF) Fines and Dust generation and control in Rock2019年8月14日 When its own gravity is greater than the centrifugal force, it falls or rolls down from the inner wall of the cylinder, crushing the ore At the same time, in the process of mill rotation,the sliding motion of grinding medium also produces grinding effect on raw materials The ground material is discharged through the hollow shaft neckThe Ultimate Guide to Ball Mills Miningpedia
.jpg)
Characterization of haul road dust in an Indian opencast iron ore
1997年9月1日 Vehicular traffic on unpaved haul roads of the opencast mines has been identified as the most prolific source of fugitive dust An intensive study was carried out in Noamundi Iron ore mines of Tata Iron and Steel Co in January–February 1994 to characterize the airborne aerosol mainly contributed from unpaved haul road, traffic exhaust and reentrained dust from 2024年10月1日 Dust pollution, a highly concerned social issue, is among the most significant hazards in mining operations, contributing to occupational health issues, equipment degradation, and compromised visibility at workspace [[1], [2], [3]]Characterized by its substantial capacity and efficient conveying capabilities, the ore pass is pivotal in the ore transportation system [4, 5]Investigating the efficacy of foambased dust particle capture for dust PROCESSING AND COMPLEX USAGE OF MINERAL RAW MATERIALS EURASIAN MINING 2022 No 2 pp 54–57 55 kWh/t; M ia is the Morrell index for coarse ore treatment in tumbling mills to the size P 80 > 750 μm , kWh/t; Mic is the M orrell index for ore treatment in cone and jaw crushers, kWh/t; Mih is the Morrell index for ore treatment in HPGR circuits, kWh/t; Mib is the ORE HARDNESS PROPERTIES EVALUATION BASED ON Technological cycle of iron ore crushing and grinding under production conditions is possible only in terms of mechanical load being rather labourconsuming and energyintensive Application of physical impact methods on iron ore to intensify its crushing and grinding processes is still at the stage of research and development [9]Research into the crushing and grinding processes of iron ore
.jpg)
New insights into double roll crushing ScienceDirect
2023年11月1日 Double roll crushing is a comminution principle that has already been deployed for more than 100 years It is known for high throughputs of sometimes sticky materials such as overburden However, its applicability for ore and hard rock processing has been underestimated in recent decades