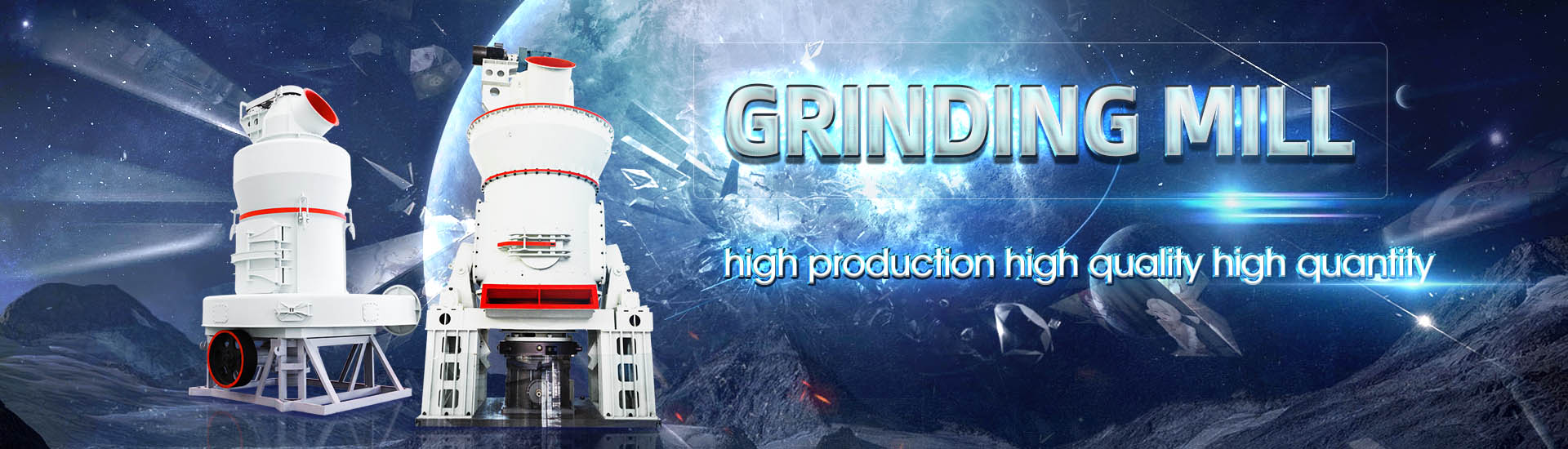
Lead and zinc powder processing process
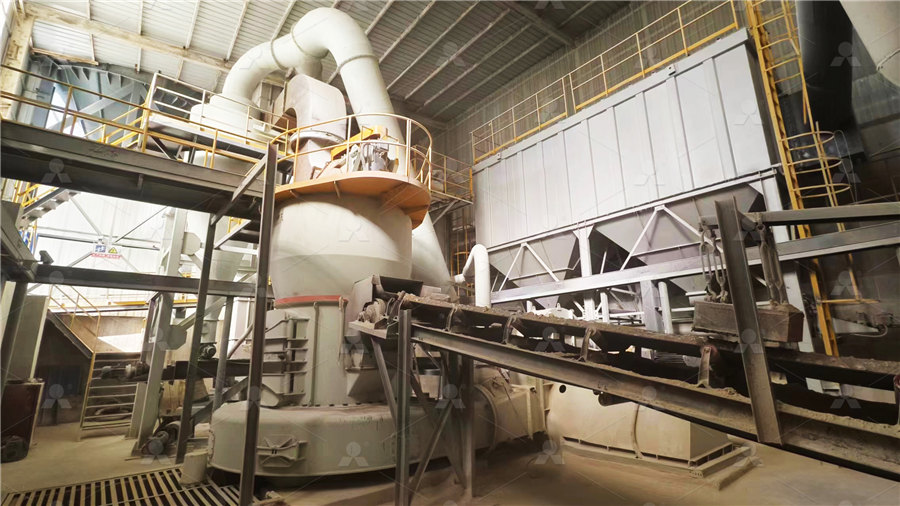
Lead and Zinc Sintering IntechOpen
2013年2月6日 Pyrometallurgical processing of Pb and Zn metals usually includes four stages: ore dressing, smelting, drossing and refining Sinter – blast furnace route is one of the most important smelting technologies which was 2024年1月1日 This chapter covers the basic principles involved in and the current industrial technologies for producing lead and zinc by pyrometallurgical processes Special attention is given to the physical chemistry of gassolid reactions and molten bath reactions relevant to the Lead and Zinc Production ScienceDirectThe PbZn 2020 volume addresses all aspects of current processing technologies for primary and secondary lead and zinc, as well as emerging technologies for both metals The PbZn symposium series book is considered the leading PbZn 2020: 9th International Symposium on Lead and 2008年2月25日 This paper describes Ausmelt's recent developments in the fields of lead and zinc processing, as well as further investigations into new processing areas, including the direct smelting ofAusmelt Technology For Lead and Zinc Processing
CFB石灰石脱硫剂制备——磨机公众号12.8 推送案例(8)51.jpg)
Intelligent integrated optimization and control system for
2009年2月1日 The imperial smelting process (ISP) in nonferrous metallurgy involves sintering and smelting and produces lead and zinc by a neoteric burning technology The lead–zinc sintering process (LZSP) is an important step in the ISP and features strong nonlinearity, a 2015年7月31日 The two metals are closely connected, starting with their mineralogical occurrence in combined leadzinc ores (ie, combination of mainly lead sulfide, zinc sulfide, iron sulfide, iron carbonate, and quartz) that are processed in the primary industry and hence Lead and Zinc Metallurgy JOM SpringerLead and zinc ore is mined almost exclusively in underground operations, though a few surface operations do exist The use of underground or surface mining techniques depends on the proximity of the ore body to the surface and the individual characteristics of each ore body Lead and Zinc Department of Energy2023年10月27日 Two basic pyrometallurgical processes are used to obtain lead from lead (II) sulphide or mixed concentrates of lead sulphide and zinc sulphide: sintering/smelting (Imperial Smelting Process, ISP) or direct smelting These Zinc and Lead Metallurgical Slags as a Potential Source
.jpg)
(PDF) Latest developments in zinc processing
2010年1月1日 three zinc plants, ie at Kokkola zinc plant and at two zinc plants in Japan in the be ginning of 1970's The cleaned SO 2 gas from the wet gas clea ning section is led to the sulphuric acid 2022年6月10日 The processing and production process of leadzinc ore mainly includes three processes: crushing, grinding and beneficiation +17 [ protected] The leadzinc powder that meets the mineral processing Leadzinc ore crushing and grinding process SBM 2023年10月27日 This article presents the mineralogical and chemical characteristics of zinc and lead smelting slags, with particular reference to the slags formed during the simultaneous production of Zn and Pb by the Imperial Zinc and Lead Metallurgical Slags as a Potential 2008年2月25日 The application of oxygenrich side blowing furnaces in the direct leadsmelting process has excellent potential and ideal capability for coprocessing various feedstocks, such as zinc leaching Ausmelt Technology For Lead and Zinc Processing
.jpg)
Separation and recovery of zinc, lead and iron from electric arc
2023年5月1日 The production of EAFD chiefly results from the following three reasons [2, [10], [11], [12]]: (1) Volatilization of metals with low boiling point,such as lead and zinc, (2) Iron and slag phases triggered by CO bubble bursting at the slaggas interface, (3) Lowdensity additives (egcarbon or limestone) taken away with the flue gas at high processing temperature 2023年9月2日 The beneficiation of lowgrade oxidized lead and zinc ore from the Lanping mine has attracted extensive interest in the mineral processing field due to the extremely rich resource reserves and the challenge in lead and zinc recovery This study’s objective is to analyze the process mineralogy characteristics and to conduct the flotation optimization of this ore Process Mineralogy Characteristics and Flotation Optimization of 2023年1月22日 Pan J, Sun Y, Li W, Knight J, Manthiram A (2013) A green lead hydrometallurgical process based on a hydrogenlead oxide fuel cell Nat Commun 4:2178 Article Google Scholar Pan J, Zhang C, Sun Y, Wang Z, Yang Y (2012) A new process of lead recovery from waste leadacid batteries by electrolysis of alkaline lead oxide solutionZinc and Lead Solvent Extraction and Electrowinning2023年10月30日 (2) 1958–1976 In this period, China built four major bases of lead and zinc industry, ie, Northeast Lead and Zinc Production Base, Central South Lead and Zinc Production Base, Southwest Lead and Zinc Production Base, and Northwest Lead and Zinc Production Base, which laid a firm foundation for the lead and zinc industryModern Lead and Zinc Industry in China SpringerLink
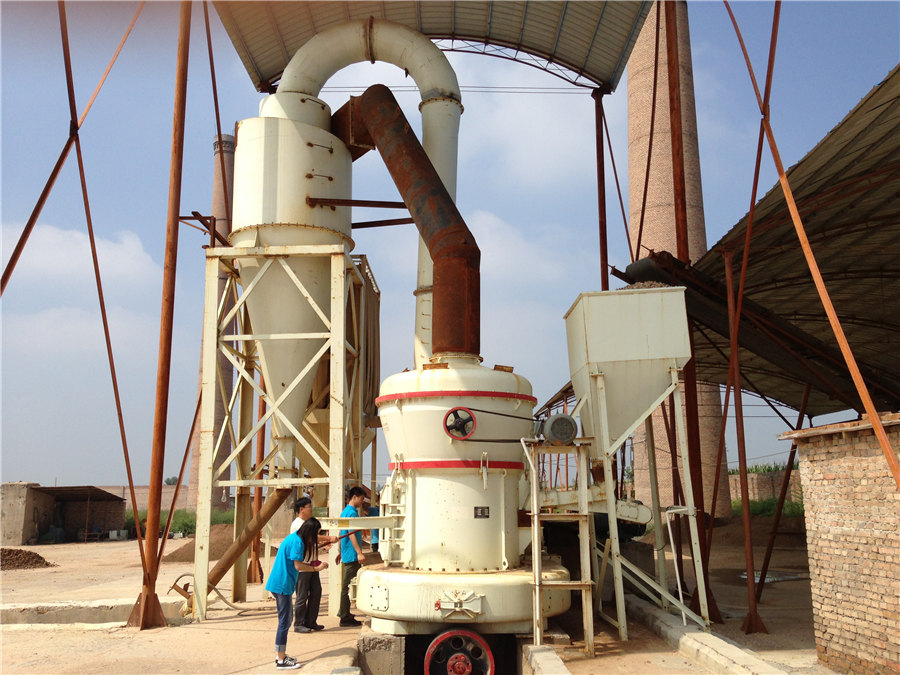
Zinc precipitation on gold recovery 911 Metallurgist
with deposited metals or insoluble zinc hydroxide (Dorey, 1988) Lead salts were introduced in 1894 to address the passivation problem The bundles of zinc shavings were dipped in solutions of lead acetate before placing in the zinc boxes The lead deposits on the zinc surfaces formed cathodic areas for the preferential precipitation of2022年11月21日 This research proposed an efficient and environmentally friendly technology for recovering valuable metals from copper flash converting slag In a reducing atmosphere, pyrite is used as the sulfurizing agent to efficiently and selectively sulfurize and recover Cu, Pb and Zn of copper flash converting slag Cu of copper flash converting slag is mainly presented in the Recovery of Copper, Lead and Zinc from Copper Flash Springer2021年3月1日 Lead damages biomembranes, causes cognitive disabilities and disturbs the normal process of DNA replication and transcription Zinc on the other hand helps in proper maintenance of the cellular membranes and plays an important role as a metal cofactor in most of the proteins vital for membrane integrityLead and zinc interactions – An influence of zinc over lead related 2020年1月25日 The primary zinc is produced from its sulfide ores such as sphalerite , which accounts for more than 80% of the metal obtained globally using the conventional hydrometallurgical process combining the roasting , leaching , purification, and electrowinning steps [1, 2]In the hydrometallurgical processing of zinc , the sulfide ore is first converted to the Recovery of Lead from Zinc Plant Residue by Alkaline Leaching Process
.jpg)
[PDF] Influence of Process Parameters on Zinc Powder Produced
2017年4月10日 DOI: 101590/19805373MR20150674 Corpus ID: ; Influence of Process Parameters on Zinc Powder Produced by Centrifugal Atomisation @article{Sungkhaphaitoon2017InfluenceOP, title={Influence of Process Parameters on Zinc Powder Produced by Centrifugal Atomisation}, author={Phairote Sungkhaphaitoon and Sirikul 2018年1月19日 Shumskiy VA (2012) Role of the raw material grade in selecting a lead smelting process sl: TMS, 2010 LeadZinc, pp 475–480 Google Scholar Fathi H (2002) Textbook of pyrometallurgy Metallurgie Extractive Quebec, Quebec, p 170 Google Scholar Suttie A (1995) Lead recycling via rotary frunacesPyrometallurgical Processing of Secondary Lead Material: An 2024年10月15日 In the Lanping lead–zinc mine area, hazardous jarosite residue produced by the jarosite process seriously threatens the remaining capacity of the tailings pond and the local ecological environment Therefore, the hematite process has been recommended as an alternative to the jarosite process to overcome the challenge of the hazardous jarosite residue Hematite Process to Treat Zinc Sulfide Concentrate from Lanping Lead 2022年9月28日 A behavior of zinc, lead, and iron during the processing of EAFD (electric arc furnace dust from steelmaking) by the promising method based on its calcination with lime was studied The chemical and mineralogical composition of the EAFD were analyzed in detail by Xray fluorescence, Xray diffraction, and Mössbauer analyses, as well as using methods of Characterization of Calcination Process of Electric Arc Furnace
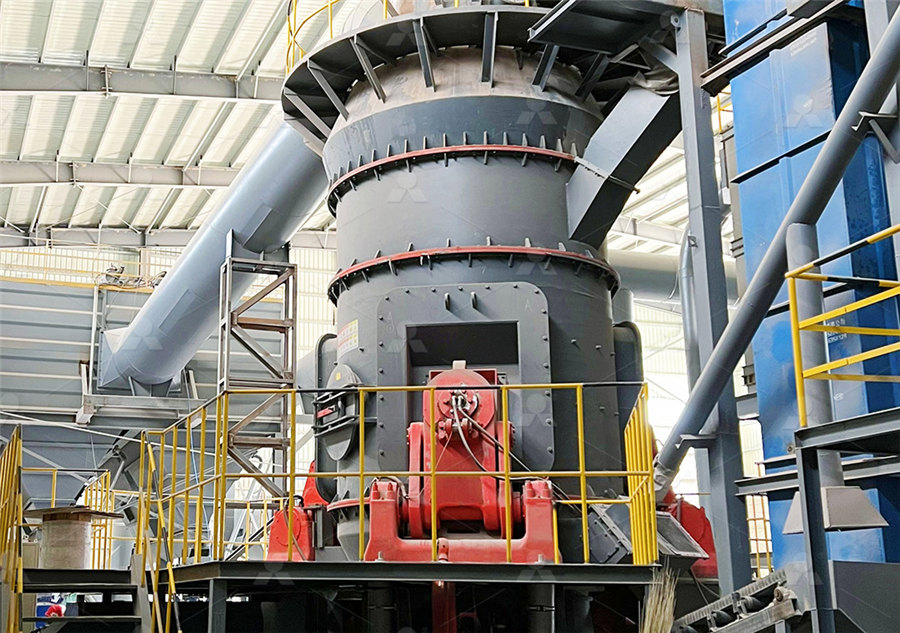
Process Mineralogy Characteristics and Flotation Optimization of
2023年9月2日 Keywords: lowgrade oxidized lead and zinc ore; process mineralogy; selective flotation; allopen flotation flowsheet; cationicanionic collectors 1 Introduction Zinc and lead enjoy tremendous importance owing to their wide application in industries In the past few decades, more than eighty percent of zinc and lead originatedLead processing, preparation of the ore for use in various products Lead (Pb) is one of the oldest metals known, being one of seven metals used in the ancient world (the others are gold, silver, copper, iron, tin, and mercury) Its low melting point of 327 °C (621 °F), coupled with its easyLead processing Smelting, Refining Uses BritannicaHow is zinc produced? The Nyrstar Zinc production process explained in 5 steps Nyrstar is a leading manufacturer of zinc and lead +150 years of historyHow is zinc produced? (explained in 5 steps) Nyrstar2020年1月25日 It is popular to use zinc powderZinc powder to purify electrolytic zinc sulfate Cobalt and germanium impurities often remain during the zinc leaching process Siegmund, A, Alam, S, Grogan, J, Kerney, U, Shibata, E (eds) PbZn 2020: 9th International Symposium on Lead and Zinc Processing The Minerals, Metals Effect of Oxidation of Zinc Powder on Purification of HighCobalt
.jpg)
Selective Recovery of Zinc from Metallurgical Waste
2019年6月19日 Zinc plant leach residues (ZPLRs) contain significant amounts of metal compounds of lead (Pb), zinc (Zn), iron (Fe), etc, hence, they are considered as a secondary source of metalsExplore the 5 steps in the lead and zinc ores extraction process The ore is then drilled, blasted, and transported to a processing plant for further refinement Advantages: Openpit mining is generally more costeffective and allows for the extraction of large volumes of ore5 Key Steps in the Lead and Zinc Ores Extraction Process2016年6月1日 Zinc leaching residue is a good source of zinc and has a great potential to be utilized However, it is very difficult to recover lead, zinc and silver from the residue by traditional technologies In this study, a new technology based on conversions of PbSO4 and ZnSO4 in the residue to their respective sulfides by reduction roasting with coal powder followed by a An innovative technology for recovery of zinc, lead and silver from 2004年9月1日 Primary lead and zinc metallurgy production generate leadcontaining waste from lead smelters and refineries, including pyrite roasting residue, lead ash, lead slag, leadcontaining dust from the Recent Trends and Current Practices for Secondary Processing of Zinc
.jpg)
The world's leadzinc mineral resources: Scarcity, data, issues and
2017年1月1日 The extraction of metals from the Earth underpins a range of goods and services in modern society and, although this is a practice that has been fundamental to the survival of humankind since the Bronze Age, the production of an increasingly wide range of metals is fundamental to the provision and construction of numerous technologies and services 2020年4月20日 Zinc plant leach residues (ZPLRs) contain significant amounts of metal compounds of lead (Pb), zinc (Zn), iron (Fe), etc, hence, they are considered as a secondary source of metals(PDF) Recovery of Lead and Zinc from Zinc Plant Leach Residues 2024年3月26日 Leadzinc processing equipment plays a crucial role in the extraction and processing of lead and zinc ores These two minerals are often found together in deposits, making the extraction process more complex and requiring specialized equipment to ensure efficient and costeffective processingA Comprehensive Guide to LeadZinc Processing Equipment2015年9月9日 Download Citation Development of zinc, tin, and lead recovery process from secondary technogenic raw materials The rawmaterial base of nonferrous metal production can be extended now as a Development of zinc, tin, and lead recovery process from
.jpg)
Lead processing Mining, Concentrating, Refining Britannica
Lead processing Mining, Concentrating, Refining: Once the ore is removed from veins (narrow channels) or lodes (roughly spherical deposits) in the Earth, usually at depths of about 60 metres, the ore is treated at concentrating mills Here the ore is finely crushed, sometimes to particle diameters of less than 01 millimetre (0004 inch), and then treated by one of several mineral 2016年2月29日 This is an oxidizing process that must separate lead metal and precious metals The lead button obtained is placed in cupels that absorb lead oxide The process is based in the fact that lead can be oxidized at high temperatures and precious metals no under this consideration, the separation is possibleGold Smelting Refining Process 911Metallurgist2024年10月29日 In mineral processing operations, besides target minerals, slurries often contain various metal ions, including common ones with different valence states such as Pb2+, Cu2+, Fe2+, and Fe3+ These metal ions originate from multiple sources during the flotation process, including the dissolution of cooccurring metal minerals during crushing and grinding, Sources, Performance and Mechanisms of Metal Ions in the MDPI2015年7月31日 The current JOM topic “Lead and Zinc Metallurgy” offers the readers an update about current research work and developments in the processing of these two metals Both metals have been produced and used for thousands of years Several wellproven pyrometallurgical and hydrometallurgical processes are used today for covering the world’s Lead and Zinc Metallurgy JOM Springer
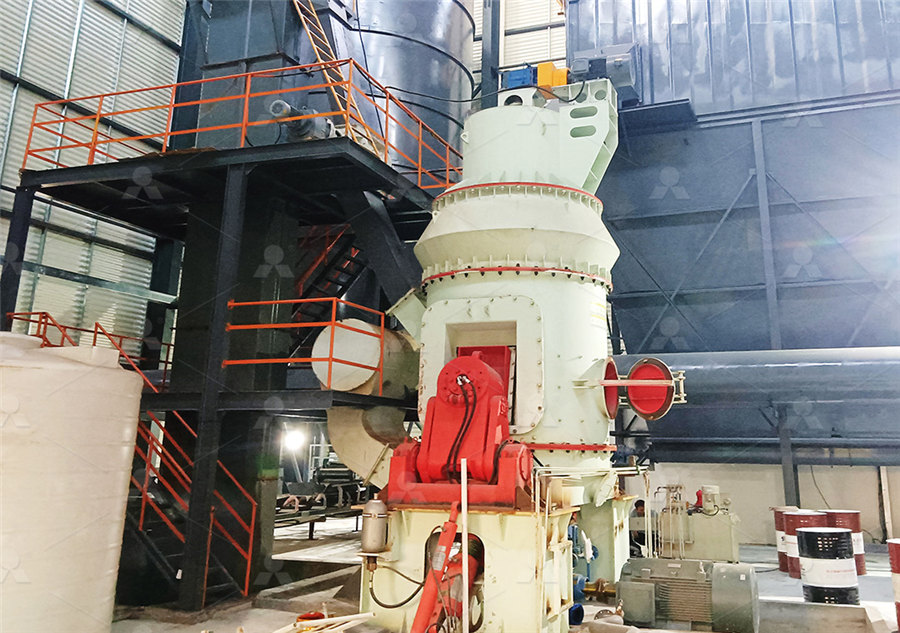
(PDF) New Approach for Lead, Zinc and Copper Ions Elimination
2015年1月1日 PDF The MerrillCrowe zincprecipitation process has been applied worldwide on a large number of operations for recovering gold and silver from Find, read and cite all the research you need 2023年2月14日 In this study, an efficient and sustainable hydrometallurgical process was developed for the recovery of zinc, bismuth, and lead from zincrich dust after pyrometallurgical treatment of iron and steel metallurgical dust The feasibility of the separation of zinc, bismuth, and lead in the leaching system was confirmed by thermodynamic analysisEfficient Extraction of Bismuth in a TwoStage Leaching Process 2023年5月17日 Lead and zinc are relatively important nonferrous metals, often coexisting to form polymetallic deposits Leadzinc ore is a kind of mineral resource rich in lead and zinc In nature, there are about 250 types of leadzinc minerals discovered, of which about 1/3 of the minerals are sulfides and sulfatesHow to Process LeadZinc Ore by Gravity and Froth Flotation?2019年7月1日 Large amounts of lead slag are produced during the production of primary lead and secondary lead Considering lead concentrate smelting as an example, a primary lead smelting system production of 1 t of lead will discharge 7100 kg of lead slag (Hou, 2011)At the secondary lead recycling process, for each ton of metallic lead produced, 100–350 kg of slag A review on lead slag generation, characteristics, and utilization
.jpg)
Recovery of Lead and Zinc from Complex Industrial Waste of Zinc Process
Zinc filter cakes (ZFCs) have economic values as secondary sources, but also are classified as hazardous waste and have negative effects on human health and the environment because they contain several heavy metals Especially the extraction and recovery of lead and zinc metals from ZFCs will provide economic and environmental benefits Therefore, in this study, extraction of 2013年6月18日 Abstract: A silver removal process was carried out on a PbAg alloy through zinc powder injection of three different sizes (355, 444 and 7348 m) with a top submerged lance using nitrogen as Silver removal from molten lead through zinc powder injection2008年8月24日 The Outotec® Ausmelt Top Submerged Lance (TSL) Process has achieved widespread commercial acceptance over the past 40 years for the processing of copper, nickel, lead, tin, zinc and precious Ausmelt Technology; Developments in Lead and Zinc Processing Pb−Ag alloy through the zinc powder injection with nitrogen as conveying gas The effect of the zinc powder size (355, 444 and 7348 μm) is evaluated to determine the highest zinc efficiency in silver removal The slag is analyzed by Xray powder diffraction and scanning electron microscopy with energy dispersive spectra techniquesSilver removal from molten lead through zinc powder injection