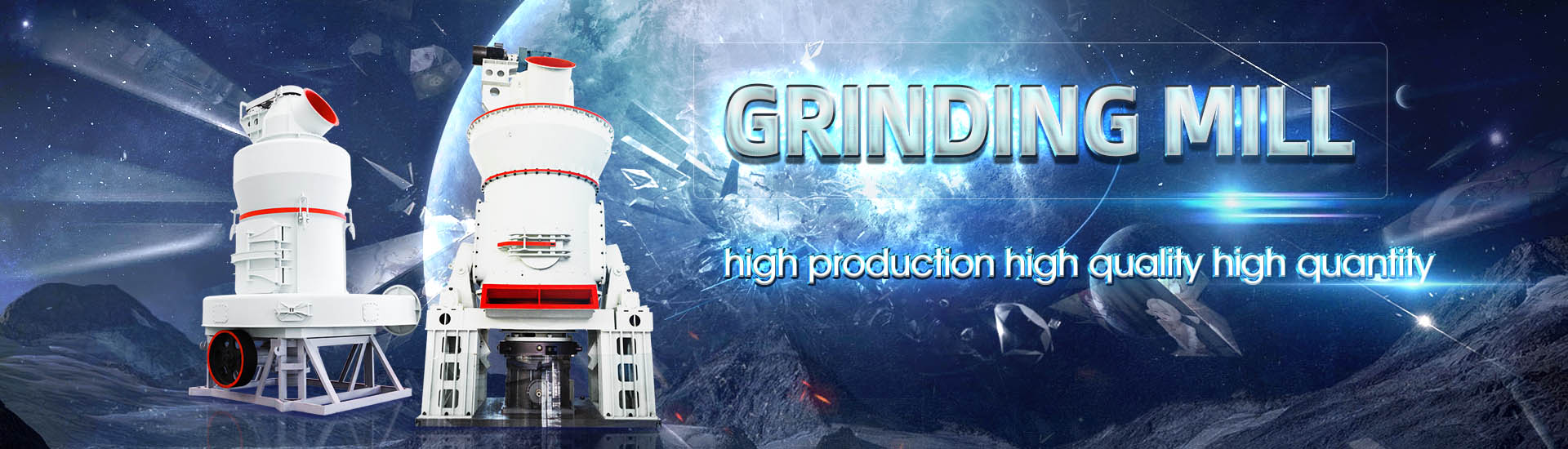
Raw material grinding system instrument
.jpg)
Vertical roller mill for raw Application p rocess materials
Grinding raw materials needs lots of energy Tube mills had been used for grinding, but the energy efficiency level was lower Therefore, the introduction of highly efficient grinding equipment was anticipated The vertical roller mill has high energy efficiency and the installation space is The LMmaster is a system designed by Loesche to optimize grinding plants from the start of the material feed onwards The LMmaster is a software based application which can either be PROCESS OPTIMISATION FOR LOESCHE GRINDING PLANTSStable quality by optimal raw material preparation and raw material grinding at maximum effi ciency for energysaving operation of facilities Monitoring and control of burning and cooling Monitoring Control Systems for Cement Plants Fuji Electric GlobalWith the Smart Grinding product, CemtecDigital offers operators of dry grinding and classifying circuits a remedy by enabling them to operate their grinding circuit in an energyoptimized and Smart Grinding CEMTEC DIGITAL
.jpg)
Grinding Systems Penta Engineering Corporation
We can assist you in evaluating and optimizing your current operation, modifying and/or upgrading your existing grinding system to achieve a maximum sustainable production rate Drying of moisture in raw materials is required for effective grinding and subsequent handling of raw meal This is achieved normally by ducting part of the kiln exhaust gas through the mill Raw Material DryingGrinding Cement Plant Optimizationcommon solution to grind raw materials and cement Roller presses are used mainly in combination with a ball mill for cement grinding applications and as finished product grinding BALL MILLS Ball mill optimisation Holzinger ConsultingGrinding of cement clinker and granulated blast furnace slag in roller grinding mills (vertical airswept grinding mills) is a technology introduced by Loesche The first use of a Loesche mill, 2 µm 5 µm Loesche
.jpg)
quadropol® thyssenkrupp Polysius Grinding Technologies
For raw material grinding four QMR² 48/24 are contracted, while for cement grinding four polycom® high pressure grinding rolls as a combi grinding system are considered due to ange of different systems in raw material, coal, and cement grinding While new plants mainly focus on highly energy‐eficient systems, using roller comminution systems like vertical roller Thomas Holzinger, Holzinger Consulting, grinding system final raw material grinding system based on technology of TRP roller press and separator with flow sheet shown below Feed material will be fed to Vseparator by belt conveyor Material at roller press outlet will be sent to Vseparator by bucket elevatorTRP ROLLER PRESS FOR FINAL RAW MATERIAL GRINDING SYSTEM product grinding units, as well as raw ingredient grinding equipment in mineral applications This paper will focus on the ball mill grinding process, its tools and optimisation possibilities (see Figure 1) The ball mill comminution process has a high electrical energy consumption, especially when those systems are in combination withBALL MILLS Ball mill optimisation Holzinger Consulting
.jpg)
Thomas Holzinger, Holzinger Consulting, grinding system
grinding system optimisation Introduction The cement industry uses a wide range of different systems in raw material, coal, and cement grinding While new plants mainly focus on highly energy‑efficient systems, using roller comminution systems like vertical roller mills (VRMs) and high pressure grinding units (roller presses), less efficientThis specialist edition features key innovations in the science and engineering of new grinding processes, abrasives, tools, machines, and systems for a range of important industrial applications Topics written by invited, internationally recognized authors review the advances and present results of research over a range of wellknown grinding processes A significant Modern Grinding Technology and Systems MDPI Books2021年1月1日 Stacking Reclaiming of Raw material: Swing type stacker Reclaimer: Limestone other raw material are stored in open area into a longitudinal storage unit called stockpile through Stacker These are then extracted transversely from the stockpile through reclaimer: 3: Raw Meal Grinding Homogenization: Grinding Mill Vertical Roller Mill Review on vertical roller mill in cement industry its performance Figure 2 Typical blending systems The prepared raw materials are stored in silos for the next technological step, which is the raw material grinding and blending system 22 Raw Material Blending At the next technological unit, the prepared raw materials are mixed during a grinding operation by dry process or together with water in wet processAUTOMATION AND CONTROL IN CEMENT INDUSTRIES
.jpg)
RAW MATERIAL GRINDING ITadipatri’s big sixer Loesche
raw material and cement grinding Here identical components such as grinding rollers, rocker arms for transmission of the spring force onto the rollers, roller bearings and main components of the hydropneumatic suspension spring systems such as cylinders and accumulators were used in the mills RAW MATERIAL GRINDING 0% 25% 50% 75% 100% 50 2022年8月31日 Dear Colleagues, The grinding process, as a primary stage of ore/raw material processing, is a necessary operation in beneficiation plants It not only provides the appropriate particle size for subsequent separation operations but also enables the liberation of valuable minerals from the gangueGrinding Modeling and Energy Efficiency in Ore/Raw Material Download scientific diagram Process and instrument diagram for the twostage grinding process from publication: Modeling and Simulation of Whole Ball Mill Grinding Plant for Integrated Control Process and instrument diagram for the twostage grinding 2022年2月15日 However, different from ordinary multivariate time series prediction problems [12], cement raw materials grinding is a dynamic process with nonlinear, strong coupling among input variablesIn the grinding process, the fluctuation of one variable will lead to the fluctuation of other related variables [13]Therefore, it is difficult to extract the dynamic characteristics SALSTMs: A new advance prediction method of energy
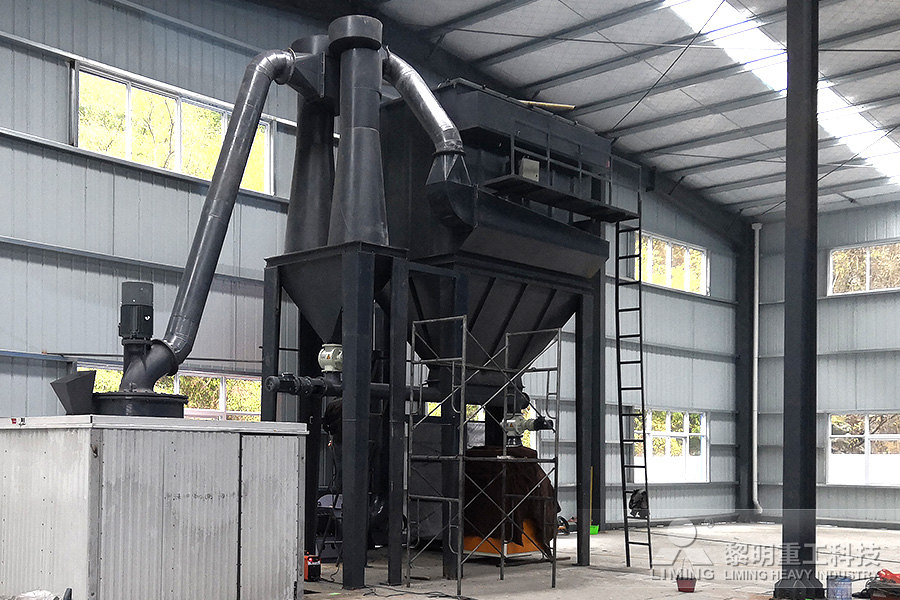
Grinding system energy consumption and fine management
Grinding system energy consumption and fine management Tel:+86513 Email:pf@ Cement, the requirement of the clinker should not be as low free calcium as better Choice of grindability raw materials Grinding way of energy saving and consumption reduction Instrument information collection:Make control as the final 4 The process chain at a glance xCrushing: crushers break up the raw material delivered from the quarry and provide the raw mill with the feed size range it requires Crushers xRaw material analysis:the POLAB® CNA online analyser provides the first data regarding the chemical contents and/or homogeneity of the raw materialRaw material preparation From the quarry to raw meal2010年7月1日 The paper presents a case study on the practical implementation of a hybrid expert system for a raw materials blending process (RMBP) Based on blending mechanism and expert knowledge, a hybrid Modeling of Raw Materials Blending in Raw Meal Grinding Systemsclosed mechanical grinding system The raw material was fed with the cooling air at various temperatures Operating conditions were adjusted for an air temperature of 50 degree C at the mill outlet Figure 8 shows the effect of the temperature of the cooling airTHE IMPROVEMENT OF GRINDING AND USING CLOSED CIRCUIT SYSTEM
.jpg)
The Cement Plant Operations Handbook International Cement
2 Raw materials management system – 22 Concrete problems 16 1 Raw materials – 2 Raw mix – 3 Reserves – 4 Crushing – 5 Drying – 6 Preblending – 7 Storage and handling 3 Raw milling and blending 3 Computerised Maintenance Management Systems 30 1 Raw milling – 2 Blending – 3 Kiln feed 4 Flames and fuels 38 12013年1月1日 There are additions in most chapters including abrasives, dressing, cooling, highspeed grinding, centreless grinding, materials, wear, temperatures and heat transfer There are numerous worked Principles of Modern Grinding Technology ResearchGate2010年7月22日 A reliable model of the dynamics between the chemical modules in the outlet of raw meal grinding systems and the proportion of the raw materials is built to achieve a robust controller able to attenuate the disturbances affecting the raw meal quality The objective of the present study is to build a reliable model of the dynamics between the chemical modules in the Modeling of raw materials blending in raw meal grinding systemsRAW MATERIALS INSPECTION SYSTEM In the polymer industry, OCS offers customized raw material testing and measurement solutions that can be used in the lab, during RD, or during (Distributor of Materials Testing Analysis Instruments, and Laboratory Equipment Raw Materials Inspection System LMS Technologies Singapore
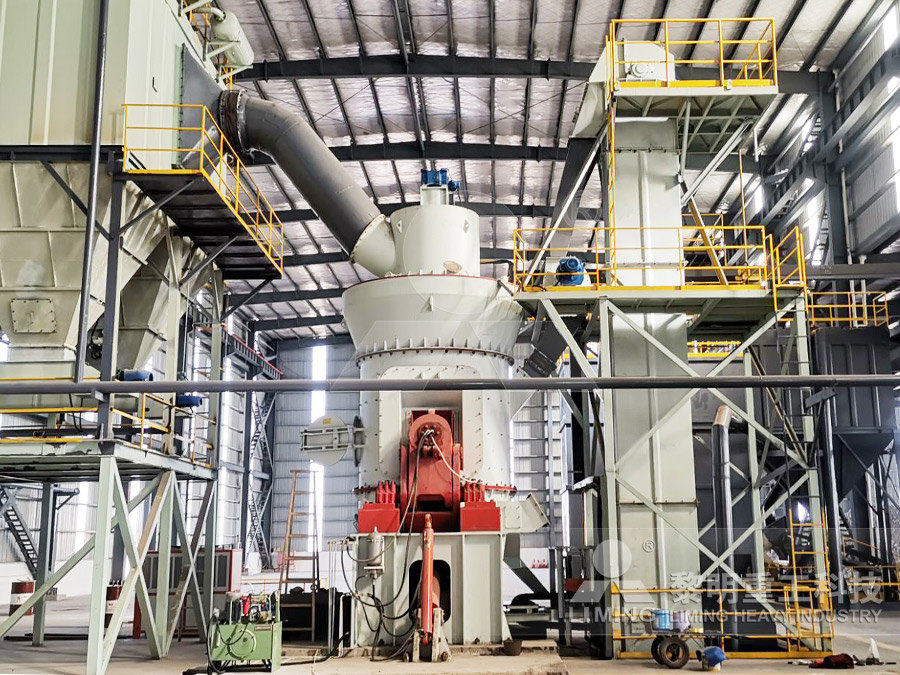
Automated Grinding Systems for Seed Processing Operations
All switches must be in the A for the grinding system to operate automatically The operator will use the HMI to select one of five previously stored sets of parameters to run Each set of stored parameters contains the following data points: Raw Material #1 Speed Setpoint (%) Raw Material #1 Agitator Speed Setpoint (%)Yamama Cement ordered two 10,000 tons per day kiln lines For raw material grinding four QMR² 48/24 are contracted, while for cement grinding four polycom® high pressure grinding rolls as a combi grinding system are quadropol® thyssenkrupp Polysius Grinding Coprocessing of Grinding Sludge as Alternative Raw Material in Portland Cement Clinker Production (XRD) is the scientific instrument to identify the crystalline compound in cement phases The effect of foreign ions on the Coprocessing of Grinding Sludge as Alternative Raw Download scientific diagram The cement raw material blending process and its control system from publication: Modeling and Optimization of Cement Raw Materials Blending Process This paper The cement raw material blending process and its control system
.jpg)
Design and Realization Of Roller Mill Control System ResearchGate
control, raw material hoist control, the bag dust collecting raw library control and the control of raw material library cutter 42 Cement standing roller grinding raw ingredients15 24th May 2024 Success of grinding systems VW thyssenkrupp Industries India High Pressure Grinding Roll : Raw Grinding Finish Mode Location JSW Shiva Cement, Sundargarh (tkII) HPGR operating in vicinity to JSW Shiva No of Circuits 1 1 Raw material grindability @ VRM shaft @ 15% R on 90 µ ~55 kWh/t (as per test report) 5 55 kWh/tSuccess of Raw Material Grinding Systems: Case Studies with Such measure might also be taken in case the available gases have a relatively low temperature, for example when they come from a heat recovery system Almost any plant for the grinding of cement raw material is a combination of machines specially adapted to the particular physical properties of the material to be groundRaw mills for all requirements Gebr Pfeiffergrinding with a raw coal rate of approx 12 t/h 1934 Loesche mills are increasingly also used worldwide for limestone and cement raw material 1937 400 Loesche mills have already been sold for coal, phosphate and cement raw material 1939 The largest Loesche mill at this time is an LM 16 with two steel springloaded rollers, a grinding trackFOR CEMENT RAW MATERIAL
.jpg)
Measurement of Raw Materials BYK Instruments
Plastic raw materials such as PP which is often used for colored enduse applications must be controlled for degree of yellowness If the resin is not “white”, the final color will be off specification The degree of yellowness is influenced by contamination or impurities of the raw materials as well as process variations2015年10月23日 The system is applied widely for clinker grinding and has also been used on raw material grinding In operation, material is fed through the inlet chute onto the grinding table centre, spread out to the grinding path by the centrifugal force arising from the table rotation, before being compressed and ground by the rollersEnergyEfficient Technologies in Cement Grinding IntechOpenUSING THE COTTON MANAGEMENT SYSTEM™ TO MINIMIZE RAW MATERIAL COSTS AND MAXIMIZE QUALITY • Michael Watson – Fiber Competition DivisionUSING THE COTTON MANAGEMENT SYSTEM™ TO MINIMIZE RAW MATERIAL 2010年10月1日 The objective of the present study is to build a reliable model of the dynamics among the chemical modules in the outlet of raw meal grinding systems and the proportion of the raw materials(PDF) Modeling of Raw Material Mixing Process in
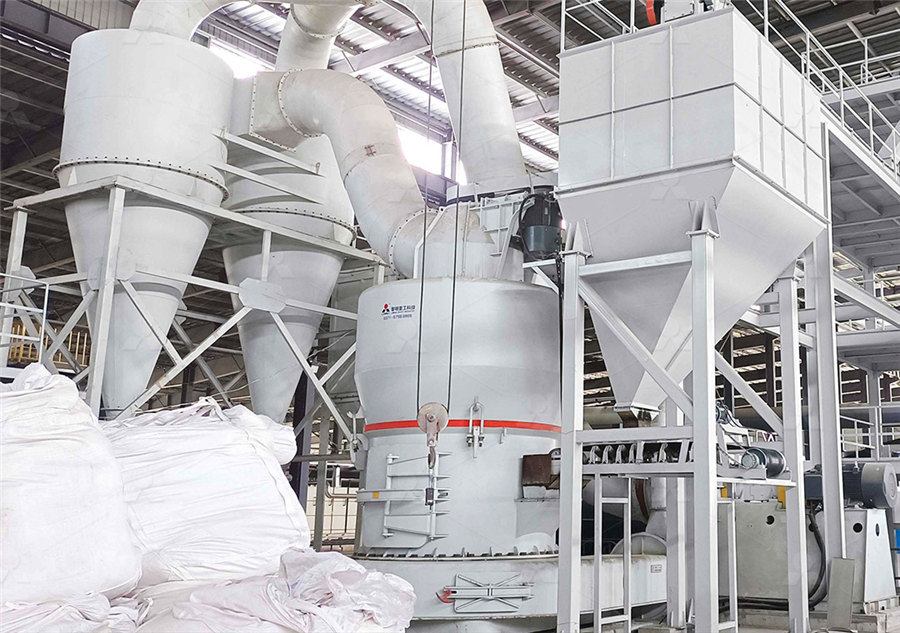
[PDF] Modeling of raw material mixing process in raw meal grinding
2010年10月1日 The objective of the present study is to build a reliable model of the dynamics among the chemical modules in the outlet of raw meal grinding systems and the proportion of the raw materials The process model is constituted from three transfer functions, each one containing five independent parameters The computations are performed using a full year industrial data 2020年11月9日 623 Length Uniformity Length uniformity is an indicator of fiber length distribution for a given sample of cotton It’s the ratio between the average fiber length (mean length) and the upperhalf mean length of the fibers, expressed in term of percentage (refer, Fig 62)For an ideal cotton fiber, where all of the fibers in the bale have the same length, say the Cotton Fiber Testing SpringerLinkOuting raw material of ball mill Automatic sampler Finished raw material Raw material homogenizer Xray analyzer Blending controller and blending control system Into cement kiln Artificial sample preparation Ball mill Feeding stuff Back stuff Sand stone Figure 1: The cement raw material blending process and its control Modeling and Optimization of Cement Raw Materials Blending During the grinding process from raw material to raw meal as well as during fine grinding of burnt clinker with additional primary components or additives, Robust instrument design and professional system maintenance by our qualified service employees ensure a lasting, Cement Particle Size Analysis Sympatec
.jpg)
MULTIPLE MATERIALS, ONE SOLUTION ROLLER PRESS
17th NCB International Conference on Cement, Concrete and Building Materials 2 20 KHD roller press Proven equipment is necessary for a reliable system KHD Humboldt Wedag is the pioneer in roller 2021年11月2日 Enhancing the extraction rate is one of the key objectives in optimization of extraction of substances from biogenic raw materials Ultrafine grinding of plant raw materials (to achieve particle size less than 300 µm) is a very appealing method for increasing the extraction rate using relatively simple equipment However, this approach often fails to yield the desired Effect of UltraFine Grinding on the Structure of Plant Raw Materials Grinder unit consisting of grinding machine, housing, handle cover with flange and counter nut, two handles and grinding diamond bit PF1101 Grinding support plate with green felt PF1102 Grinding bench plate with screws and nuts PF1103 Attachment ring and two bolts PF1104 Allen key, 4 mm CC25 2 adjustable clamping pliers C1023 Concrete sampling chloride measurements Profile Grinder2015年8月1日 The results show that approximately 248t, 469t, and 341t of materials are required to produce a ton of the product in raw material preparation, clinker production, and cement grinding stages (PDF) Analysis of material flow and consumption in
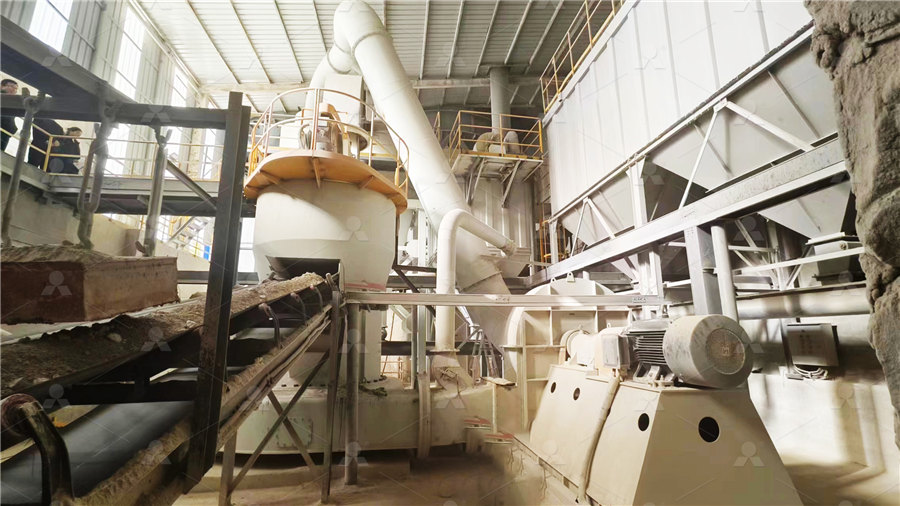
Treating Waste Gases World Cement
2012年2月9日 The design and application of raw material grinding and waste gas treatment systems for dry process cement plants The waste gas from the grate cooler, after passing through a cyclone dust collector, is sent to the cooler or raw material grinding system by the end fan on the kiln via a horizontal pipeline