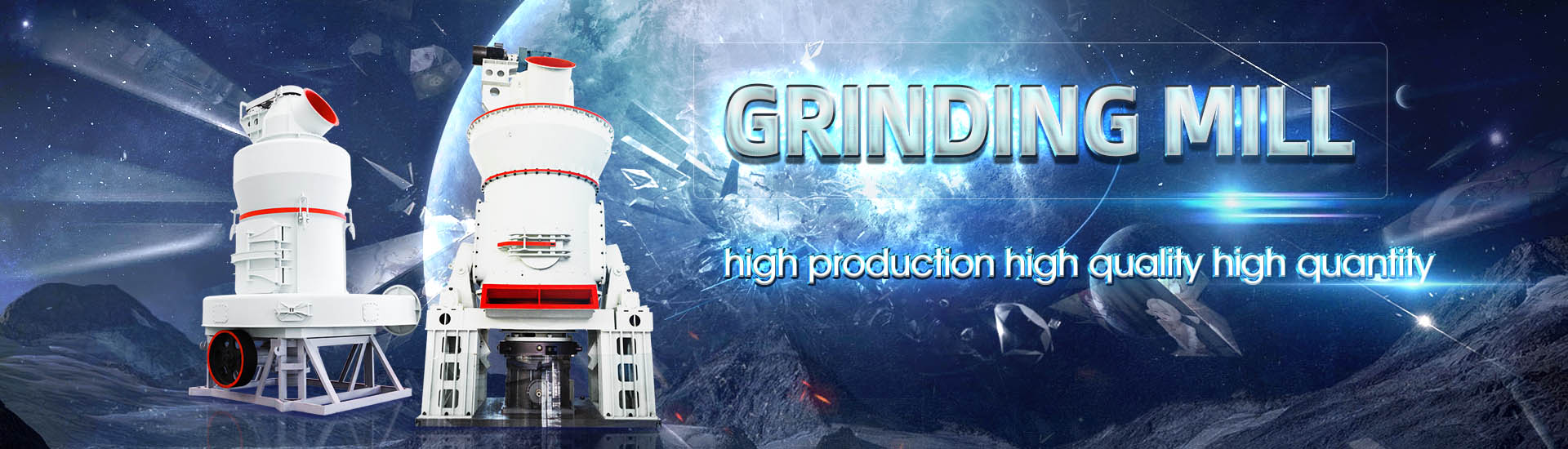
Ore crushing and grinding system with efficiency as the main factor
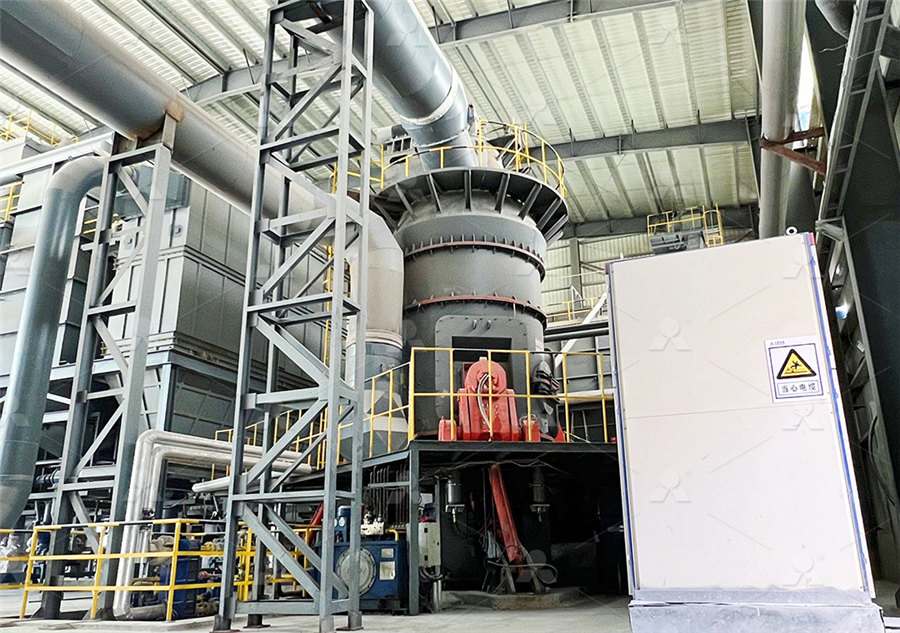
Modeling and Improving the Efficiency of Crushing
2023年6月30日 This article presents a systematic review of the task of improving the energy efficiency of crushing units This is achieved by studying modelling methods and results, the automation of crushing and grinding There are three main steps in designing a good crushing plant: process design, equipment selection, and layout The paper analyses all of these steps Gold mining is the process of Design of a crushing system that improves the crushing efficiency 2023年6月30日 On the grounds of the reviewed sources, the main methods of increasing the efficiency of crushing units are identified A mathematical model of the cone crusher was designed The simulationModeling and Improving the Efficiency of Crushing 2003年1月1日 Blasting has an important impact on mining and milling well beyond the necessary ability to dig and load the ore efficiently There is an increasing body of blasting research indicating(PDF) The Effects of Blasting on Crushing and Grinding
.jpg)
Research into the crushing and grinding processes of iron ore with
The effectiveness of simultaneous effect of mechanical load and electric field of ultrahigh frequency (UHF) in the process of iron ore crushing is substantiated in theoretical and 2023年7月20日 Moist grinding, a special grinding method, is used to prepare pellets for smelting According to the grinding medium features, ore grinding is mainly classified into ball grinding Ore Grinding SpringerLink2022年10月13日 The three parameters of grinding time (X 1), grinding concentration (X 2) and filling ratio (X 3), which have an important influence on grinding effect, are selected as the influencing factors, and the grinding Research on Grinding Law and Grinding Parameters 2022年10月4日 Optimum fragmentation is feasible for several reasons: (a) blasting induces microcracks within ore fragments and thereby weakening them; (b) a large disparity in energy Reduction of Fragment Size from Mining to Mineral Processing: A
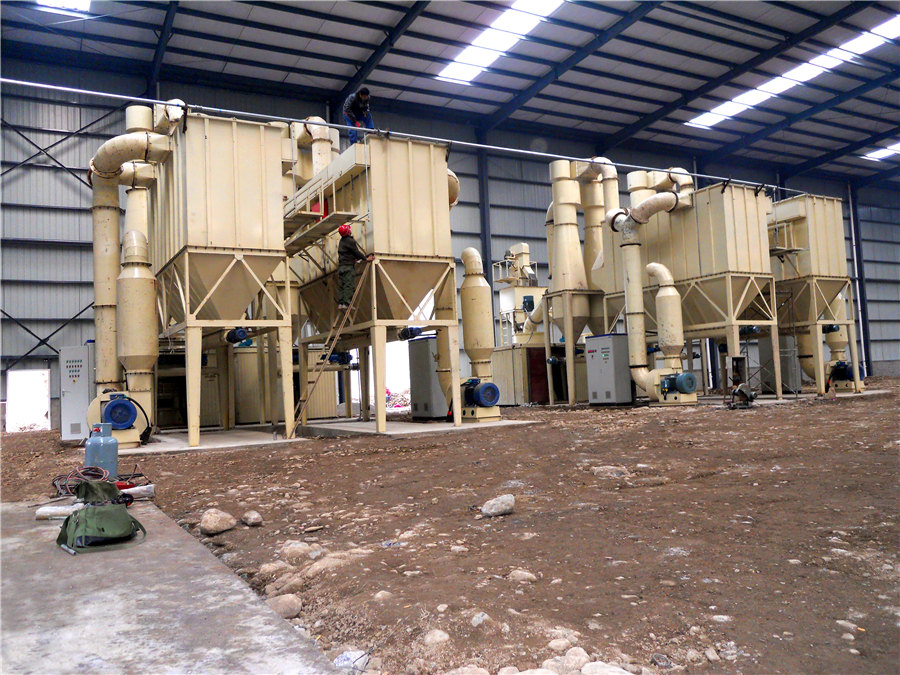
Ore Crushing SpringerLink
2023年7月22日 Development trend of ore crushing: (1) Research and develop highefficiency crushers to improve the energy conversion rate of fine crushers; (2) develop crushers with 2022年8月31日 The results show that the impactcrushing capacity of Tongkeng ore and Gaofeng ore are “medium” grade and “soft” grade, respectively The crushing resistance of Tongkeng ore increases with the decrease in particle Grinding Modeling and Energy Efficiency in Ore/Raw 2023年7月3日 1) Crushing and grinding of the ore 2) Concentration or benefaction of the ore 3) Extraction of crude metal from concentrated ore 4) Purification or refining of the metal (1) Crushing and Grinding of the Ore The Crushing, Grinding and Concentration of the Ore2024年1月1日 The ore crushing process includes four types: ore coarse crushing, ore medium crushing, ore fine crushing, and ore superfine crushing Ore coarse crushing is a process of crushing ore blocks with a feeding particle size of 500–1500 mm to 125–400 mm The maximum crushing ratio of coarse crushing is about three The main force in the coarse Ore Crushing SpringerLink
.jpg)
Introduction to Mineral Processing or Beneficiation
The general focus of this document will be on metaliferrous ores represented by runofmine material described in category 3 above An exception to the above discussion of mineral processing arises when the valuable component of the 2015年12月26日 In mineral processing or metallurgy, the first stage of comminution is crushing Depending of the type of rock (geometallurgy) to be crushed, there are 2 largely different techniques at your disposition for crushing rocks In principle, compression crushing is used on hard and abrasive rocks by placing them between a high wearresistant plate/surfaceCrushing in Mineral Processing 911Metallurgist2014年1月1日 This estimate is in agreement with an energy saving of 118% observed in an iron ore application where VSI’s were introduced as a crushing step preceding the grinding circuit View Show abstractFactors affecting the performance of crushing plant operations2016年3月11日 In the crushing section, the ore as it comes from the mine is broken down dry to a size suitable for the wet grinding machines ; these can, if necessary, be 911 Metallurgist is a trusted resource for practical insights, solutions, and support in mineral processing engineering, helping industry professionals succeed with proven expertise Crushing Plant Flowsheet Crushing Plant Flowsheet DesignLayout 911Metallurgist
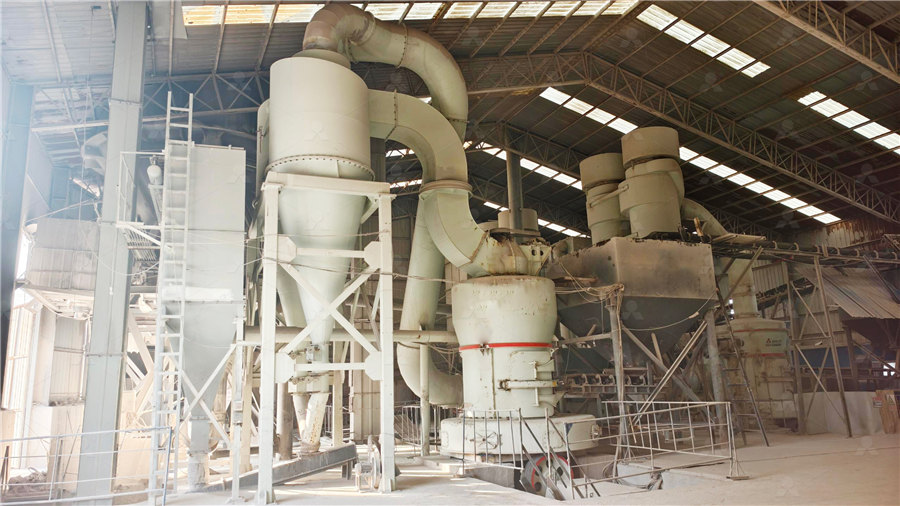
Comminution a Heart of Mineral Processing ResearchGate
2021年7月6日 PDF Comminution: The key to optimizing concentrate, grade and recovery Find, read and cite all the research you need on ResearchGate2017年8月24日 Haldar described mineral processing «as the valueadded processing of raw material (runofmine ore) to yield marketable intermediate products (eg copper concentrate) or finished products (eg silica sand) containing more than one valuable minerals and separation of gangue (tailing)»The runofmine components consist of the following:Mineral Processing SpringerLink2021年2月19日 The results of improving ore crushing in a highpressure rollerpress are presented Application of a rollerpress enables higher crushing efficiency due to both power saving and reduction of (PDF) Ore crushing in the highpressure rollerpress as a Chemical analysis of iron ore grinding products during mechanical destruction with and without application of UHF field has been carried out; statistical analysis of the obtained results has been performed as well Efficiency of using UHF electric field during mechanical crushing and grinding of iron ore under production conditions has been provenResearch into the crushing and grinding processes of iron ore
.jpg)
Gold Extraction Recovery Processes
2016年2月29日 The processing of gold ores has traditionally made use of conventional crushing and grinding circuits In each case where gold is formed either as coarse native particles or in coarse grained sulphides, it is recovered Secondary crushing 102 191 61 043 Grinding 191 0053 1935 135 Totals 2043 150 By far the greatest work input is in grinding Size is reduced by a factor of 360 In primary crushing, it is reduced by a factor of four and in secondary crushing by about five times Clearly,The Effects of Blasting on Crushing and Grinding Efficiency and 2016年5月10日 In the handling of wet, sticky ores such as encountered in tropical areas having distinct dry and rainy seasons, the crushing plant is a section of the mill which must be planned very carefully Unless this is done, crushing becomes a constant source of trouble resulting in lost production and high milling cost In some areas rainfall is high for prolonged periodsCrushing and Grinding Wet Sticky Ore 911Metallurgist2019年1月1日 Main properties of the processes of iron ore destruction in terms of its simultaneous effect by mechanical load and electric field of ultrahigh frequency have been studiedResearch into the crushing and grinding processes of iron ore
制粉-10.25公众号.jpg)
(PDF) Grinding Media in Ball MillsA Review ResearchGate
2023年4月23日 Comminution includes the blasting, crushing, and grinding of ore to liberate valuable mineral particles It consumes most of the energy used in mineral processing plants with grinding using up to Six steps to process iron ore 1 Screening We recommend that you begin by screening the iron ore to separate fine particles below the crusher’s CSS before the crushing stage A static screen is used to divert the fine particles for crushing This step prevents overloading the crusher and increases its efficiencyThe six main steps of iron ore processing Multotec2016年11月22日 Fundamentals of grinding mechanism As a material removal process, grinding process is similar to other cutting processes in many respects, such as materials are removed in forms of chips (Chen, Citation 2009; Rowe, Citation 2009)However, grinding has its distinctness from other machining processesEffect of different parameters on grinding efficiency and its This paper does not examine quantitatively other beneficial results of improved blasting However, these exist and they include: 1 Increased productivity in crushing and grinding 2 More undersize that bypasses stages of crushing 3 Reduced consumable wear The Effects of Blasting on Crushing and Grinding Efficiency and
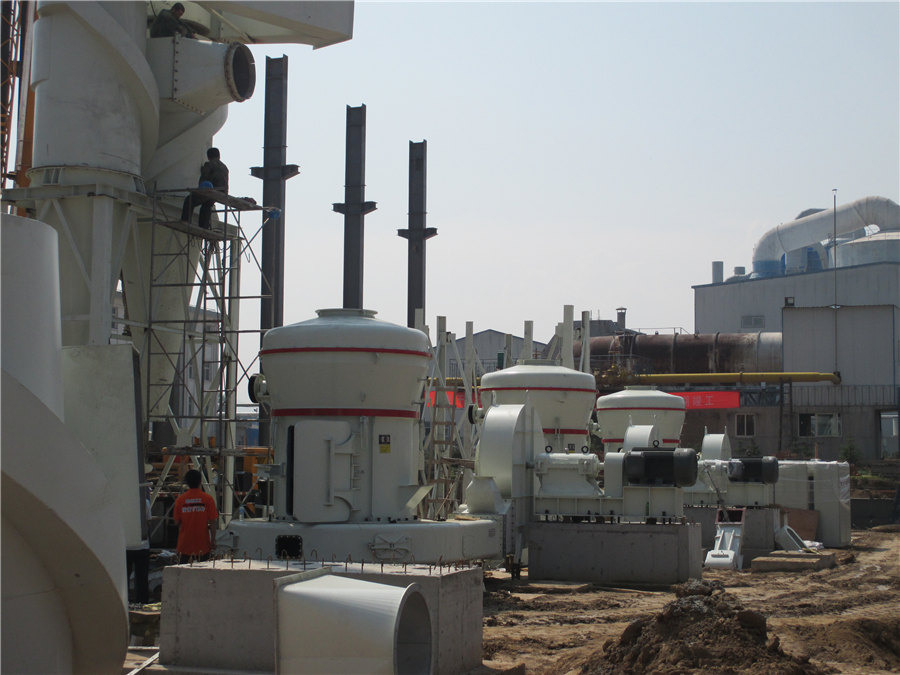
PRESENTATION OF CRUSHING AND GRINDING COMPLEX AS SYSTEM
2021年6月15日 The article proposes representation of crushing and grinding complex in form of a system with distributed parameters of the reducing function of the processed raw materials size in order to diameter before pure gold can be extracted from them The ore usually has to pass various crushing stages, each reducing the ore to a certain size Crushing plant layout is of vital importance Goldcontaining rocks are crushed for several reasons Crushing reduces the physical size of large rocks, exposing more surface area of rock, thus exposingDesign of a crushing system that improves the crushing efficiency (Horst 1985, p 3A5) Average grinding sizes for the ore can be brought down to 1015 microns at the very most, if using long grinding periods on a product which has already passed a 200 mesh sieve Some specific mills are reported to be available, which are capable of grinding the ore down to sizes of 5 microns or lessCHAPTER 5 GENERAL PRINCIPLES OF MINERAL PROCESSING 2022年12月30日 Purpose The purpose of this paper is to evaluate the efficiency of grinding operations in terms of how mechanical properties (eg, strength properties and ore texture) affect the Bond Work Index(PDF) Evaluation of gold ore properties and their impact on grinding
.jpg)
The Effects of Blasting on Crushing and Grinding Efficiency and
Table 2: Energy and cost calculations by unit operation with a higher powder factor "The Effects of Blasting on Crushing and Grinding Efficiency Blasting has an important impact on mining and milling well beyond the necessary ability to dig and load the ore fragmentation better suited to the crushing and grinding system is Eloranta, JW 1997, Efficiency of Blasting vs Crushing Grinding, Proceedings of the twentythird conference of Explosives and Blasting Technique, Las Vegas, Nevada, February 26, 1997 International Society of Explosives Engineers, Cleveland, Ohio ABSTRACT This paper compares energy requirements for blasting, crushing and grinding By THE EFFICIENCY OF BLASTING VERSES CRUSHING AND GRINDING diameter before pure gold can be extracted from them The ore usually has to pass various crushing stages, each reducing the ore to a certain size Crushing plant layout is of vital importance Goldcontaining rocks are crushed for several reasons Crushing reduces the physical size of large rocks, exposing more surface area of rock, thus exposingDesign of a crushing system that improves the crushing efficiency 2017年3月4日 Despite its significant contribution, this growth has implications for dust emissions, especially during the processes of crushing and grinding mineral ore Dust has the potential to degrade air SIZE REDUCTION BY CRUSHING METHODS ResearchGate
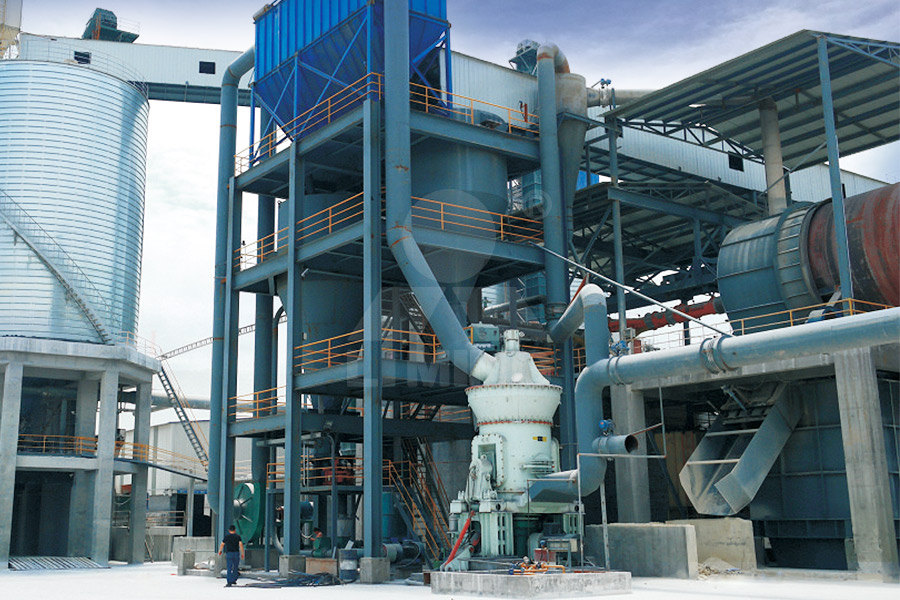
(PDF) Comminution in mineral processing ResearchGate
2018年11月19日 PDF The aim of mineral processing is to get the mineral from rock or Ore that has good economic value in the market Generally, the ability of Find, read and cite all the research you need 2022年1月23日 The crushing circuit is defined by a series of variables and how those variables come together to affect each other Those variables include the following: Feed Size maximum to the crusher Feed Size estimated distribution range Product Size required Feed rate to crushing circuit Delivery system to crushing circuit Haul trucks Railcars Physical Bauxite Processing: Crushing and Grinding of BauxiteCrushing, a form of comminution, one of the unit operations of mineral processing Mineral processing is the process of separating commercially valuable minerals from their ores in the field of extractive metallurgy [1] Depending on the processes used in each instance, it is often referred to as ore dressing or ore milling Beneficiation is any process that improves (benefits) the Mineral processing WikipediaProceedings of the 2015 International Conference on Operations Excellence and Service Engineering Orlando, Florida, USA, September 1011, 2015 Design of a crushing system that improves the crushing efficiency of gold ore at a local mine: case of Zimbabwe Tawanda Mushiri DEng Student; University of Johannesburg, Department of Mechanical Design of a crushing system that improves the crushing efficiency
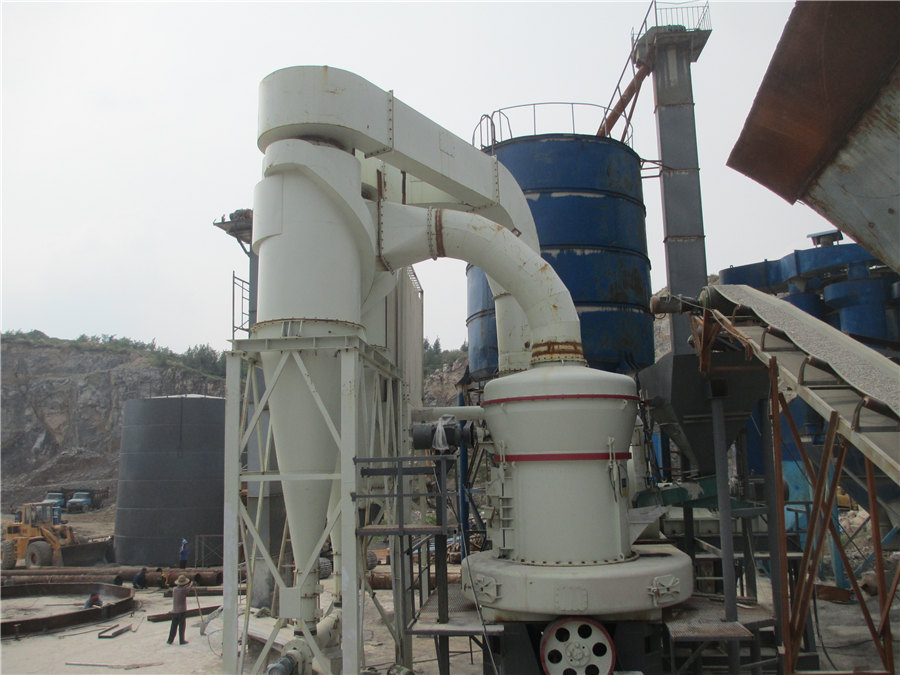
The Evolution of Crushing and Grinding: Changes in the Industry
2010年7月1日 Crushing and grinding processes have undergone significant changes over the last 20 years These adjustments have focused on lowering costs and increasing production and energy efficiency, mainly Table 1 Chemical composition of typical grinding media (% wt) Adapted from [24] 211 Cast Iron Cast iron can be grey cast iron or white cast iron, but white cast irons are commonly used in Grinding Media in Ball MillsA Review ResearchGateThe copper ore processing and production process mainly includes three processes: crushing, grinding and beneficiation In the crushing process, the threestage closedcircuit crushing is more modern and suitable for highhardness copper ore crushing, and can complete the work of ore crushing and partial dissociation, thereby improving the subsequent grinding efficiency;Copper ore crushing equipment and beneficiation process2017年5月21日 A second source of water to the grinding section is derived from fresh water to the crushing and ore storage dust collection systems when operating Flotation consists of one stage of rougher flotation of three cells, three stages of rougher scavenger flotation and one stage each of cleaner (3 cells), recleaner (2 cells) and cleaner scavenger flotation (3 cells)Copper Ore Crushing, Grinding Flotation 911Metallurgist
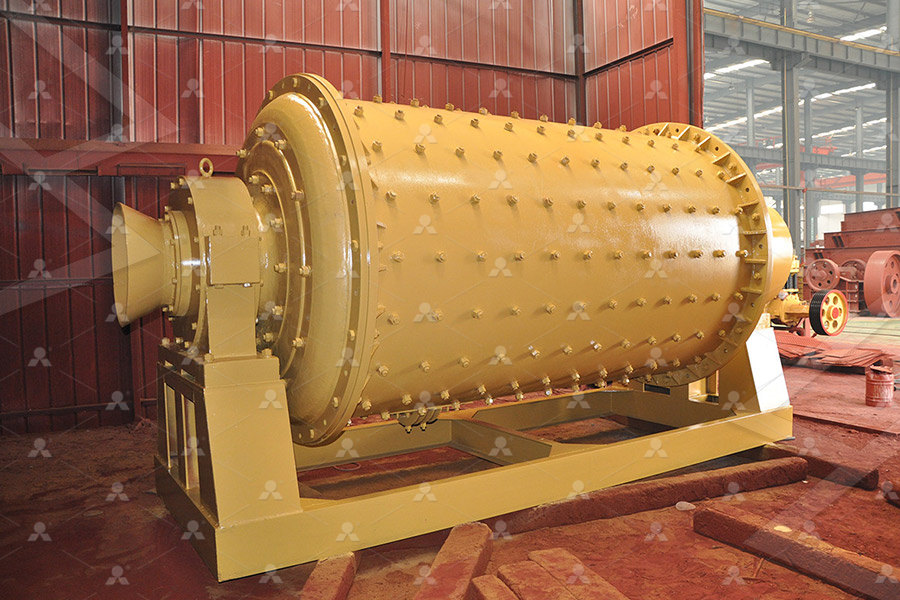
The Effects of Blasting on Crushing and Grinding Efficiency and
Blasting has an important impact on mining and milling well beyond the necessary ability to dig and load the ore efficiently There is an increasing body of blasting research indicating significant impacts in crushing and grinding These include increased production through higher output and fewer delays for bridging and jamming by oversize In addition, fragmentation better suited to 2023年6月3日 The main control contents of the crushing process control include crushing load control and crushing interlock control (1) The crushing load control is to improve the crushing load control as much as possible under the condition of ensuring that the crushed ore meets the particle size requirements of subsequent production by adjusting the feed quantity and the MeasurementControl for Crushing and Screening ProcessCrushing and grinding are mechanical processes used to reduce the size of materials, typically in the mining and mineral processing industries These processes help liberate valuable minerals from their host rock, enabling efficient extraction and processing The effectiveness of crushing and grinding plays a critical role in the overall efficiency of mineral processing, impacting the Crushing and grinding (Mineralogy) Fiveable2024年4月26日 By crushing the ore, it is broken down into smaller fragments, which facilitates subsequent processing steps such as grinding and beneficiation Screening ensures that the ore is classified into different size fractions, allowing for efficient downstream processing and ensuring that the ore meets the required specifications for further beneficiation or direct useIron Ore Processing: From Extraction to Manufacturing
.jpg)
Ore, Rock Aggregate Screening (Complete Guide)
2016年6月20日 Efficiency The amount of loading influences screening efficiency In practice it is impossible to reach 100% efficiency Maximum efficiency is about 95% In most of the cases 90% is achieved and the screen can be said to be under 100% loading Shape of the mesh hole A square hole is the usual shape2022年10月13日 Grinding plays an important role in mining, construction, metallurgy, chemical, coal and other basic industries In terms of beneficiation, grinding is the most energy consuming operation So, reasonable grinding conditions according to the properties of ores is the key to obtain good grinding results and reduce energy consumption and resource waste In this Research on Grinding Law and Grinding Parameters