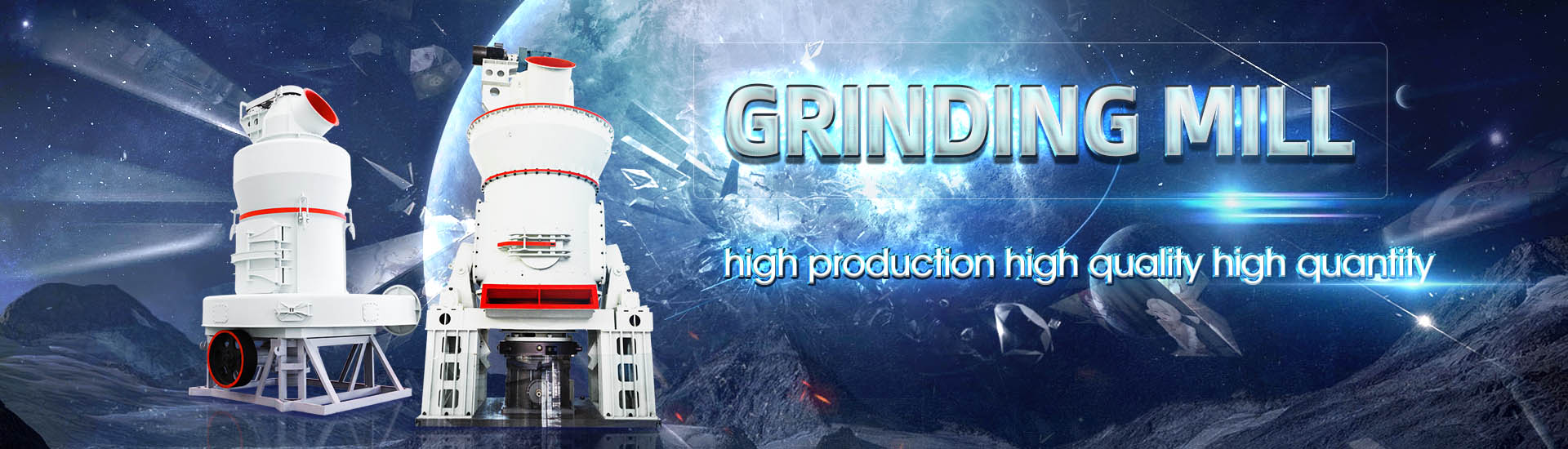
Magnesite D1308 silica ore grinding mill
.jpg)
Research on new beneficiation process of lowgrade magnesite
2020年4月14日 The results show that the optimum process parameters for the vertical roller mill are as follows: a grinding fineness of 816wt% of particles less than 0074 mm, a dodecyl amine (DDA) dosage in magnesite reverse flotation of 100 gt1, and dosages of Na 2 CO 3, (NaPO magnesite can be effectively separated by flotation from silicate gangue minerals but not from carbonates The flotation scheme to be used depends on the nature of the minerals involved In case the ore has increased percentage in silicates, reverse flotation can be used in the MAGNESITE BENEFIATION METHODS: A REVIEW SEPRMThe results show that the optimum process parameters for the vertical roller mill are as follows: a grinding fineness of 816wt% of particles less than 0074 mm, a dodecyl amine (DDA) dosage in magnesite reverse flotation of 100 gt−1, and dosages of Na2CO3, (NaPO3)6, and NaOL in Research on new beneficiation process of lowgrade magnesite 2009年2月1日 The process consists of three steps: (1) dissolution of olivine; (2) precipitation of magnesite and (3) precipitation of silica Separation and precipitation of the reaction products do not require chemical additives, such as acids or bases, and there will thus be few A continuous process for manufacture of magnesite and silica
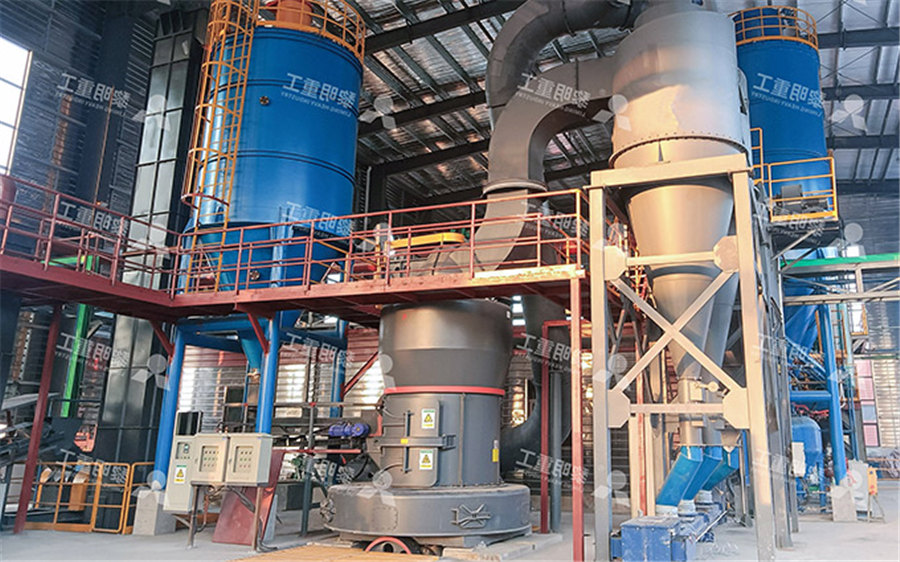
Study on regulators of purifying magnesite ore by
2021年8月20日 To improve the separation efficiency of magnesite and quartz in reverse flotation, Wang Jinliang 10 and others developed a new regulator KD1 and studied its effect in the flotation test of pure2021年6月1日 The disruption of the silicarich layer around partially reacted grains as a result of concurrent grinding on the degree of carbonation (magnesite yield) was investigated in this work Three types of naturallyoccurring magnesium silicate feedstocks, dunite, olivine and lizardite, Application of concurrent grinding in direct aqueous carbonation Although the majority of current steel production is supported by iron ore sourced from highgrade haematite deposits, the longterm growing demand for steel has led to higher raw material prices and opened the way for many new magnetite deposits to also be developedx000D There is a rich and long history of magnetite ore processing in Western countries, including large Processing of Magnetite Iron Ores Comparing Grinding Options 2021年10月29日 Magnesite grinding equipment includes ultrafine mills, vertical mills, highpressure mills, etc It can grind ores into a fine powder of up to 3000 mesh +17 Highpressure mill: can produce 50325mesh Magnesite Grinding Equipment Production Line
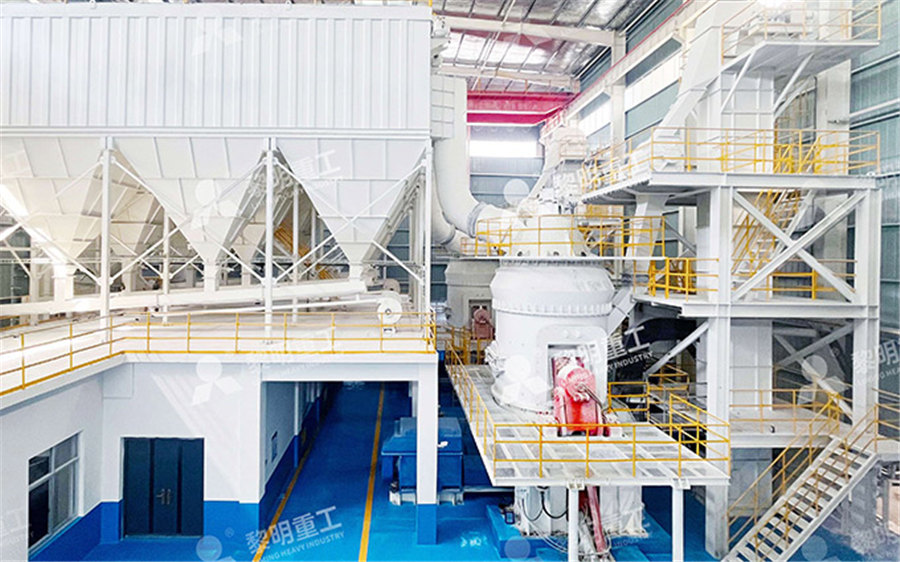
How to choose a suitable ore powder grinding mill?
2023年10月17日 3 Ultrafine Powder Grinding Mill Ultrafine powder mill (threering / fourring mediumspeed micropowder mill) feed particle size ≤25 mm, production capacity 0545 t/h, production fineness 1503500 mesh,it is a high Chemical composition of magnesite ore, and single mineral magnesite, dolomite, and quartz (wt%) Sample MgO CaO SiO 2 Al 2 O 3 Fe 2 O 3 LOI MgO (IL = 0) Magnesite ore 4601 075 238 013 023 50 Study on regulators of purifying magnesite ore by cationic 2021年11月8日 Illite ore industrial grinding mill machine can grind illite into powder up to 3000 mesh, including ultrafine mill, vertical mill, Raymond mill, wet mill, etc and activated silica fume In addition, because of its small particle size, large Illite Ore Industrial Grinding Mill Machine SBM Ultrafine lowgrade magnesite ores, which has resulted in the serious waste of magnesite resources [4] To address the shortage of highgrade magnesite resources and avoid wasting low grade magnesite grinding experiments, the ballmill grinding experiments were conducted using magnesite samples with particles smaller than 12 mm First Research on new beneficiation process of lowgrade magnesite
.jpg)
Ore mill, Ore grinding mill All industrial manufacturers
This mill accepts grinding set weights of up to 30 kg, the largest grinding jar has a volume of 2,000 ml chemical industry, etc, it has two ore grinding Compare this product Remove from comparison tool ball grinding mill horizontal for ore ball grinding mill Final grain size: 74 µm 2015年7月13日 Although the majority of current steel production is supported by iron ore sourced from high0grade haemetite deposits, the longterm growing demand for steel has led to higher raw material prices Effect of Mineral Density for Milling Magnetite Oreslowgrade magnesite ores, which has resulted in the serious waste of magnesite resources [4] To address the shortage of highgrade magnesite resources and avoid wasting low grade magnesite grinding experiments, the ballmill grinding experiments were conducted using magnesite samples with particles smaller than 12 mm First Research on new beneficiation process of lowgrade magnesite 911 Metallurgist can enter the scene and see what you have become blind to We can fix issues in ways you never thought possible Our fresh eyes will open new opportunities for your plant Each mineral processing plant has varied ore types, mining equipment, (crusher, ball mill, flotation, tailings), and management (operating) philosophyThe evaluation and prioritization of variables Metallurgists Mineral Processing Engineers 911Metallurgist
.jpg)
Grinding Mill Liners 911Metallurgist
2015年8月6日 Rubber liners absorb the impact of the larger grinding media and thus protecting – the mill structure and prolonging it’s life Weight: Rubber weighs about 15% of an equivalent volume of steel This means that a rubber liner 2014年10月1日 In a test performed in the Loesche test center in Germany, copper slag grinding saved 229% energy in an airswept model and 344% energy in an overflow model [13,14]Copper Ore Grinding in a Mobile Vertical Roller Mill Pilot Plant2021年9月23日 The barite industrial ultrafine grinding mill is a lowenergy, highefficiency nonmetallic ore milling equipment It can process ultrafine powder of 1503000 mesh It is often used for grinding more than 100 kinds of non Barite Industrial Ultrafine Grinding Mill SBM 2019年4月25日 Much work has been devoted to the technical aspects of grinding, the “how” of grinding But, in the writers’ opinion, the economically important subject of optimizing grinding capacity in mill design has not received the attention it deserves, at least not in published literature Optimizing Primary Grinding CapacityOptimizing Grinding and Regrinding Capacity in Mill Design
.jpg)
Micro Powder Grinding Mill
SBM micro powder grinding mill is a highly efficient industrial grinding mill, its finished products: 3253000 mesh; it's capacity: 0245t/h2021年3月24日 Mineral and Technological Features of Magnetite–Hematite Ores and Their Influence on the Choice of Processing TechnologyMineral and Technological Features of Magnetite–Hematite Ores 2019年12月15日 429 VertiMills Vertical mills were first designed in the 1950s for applications in fine and ultrafine grinding in Japan Lately, the vertical mill is making progress toward primary grind application and shown promise in energy reduction relative to ball mills, typical to what is normally seen in regrinding applications (Mazzinghy et al 2014)Beneficiation of Gold and Silver Ores SpringerLinkReducing Grinding Energy and Cost Magnetite Iron Ore Design Case Study A Jankovic and W Valery Metso Process Technology Innovation, PO Box 1028, Eagle Farm Qld, 4009, AustraliaReducing Grinding Energy and Cost Magnetite Iron Ore
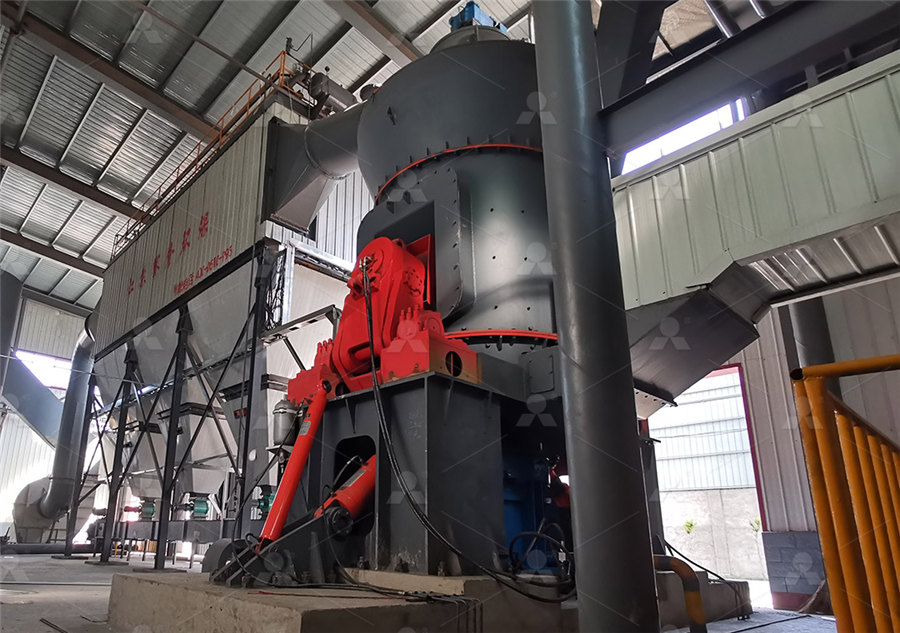
Equipment Sizing: Crusher or Grinding Mill 911Metallurgist
2016年7月8日 The Work Index values listed in Table I and II apply directly to a wet grinding overflow type rod mill 75 feet in diameter in open circuit; and to a wet grinding overflow type ball mill 75 feet in diameter in closed circuit with a rake classifier at 250% circulating load, and with 80% or more of the feed passing 4 meshDolomite micro powder grinding mill is a new type mining equipment for make and Mohs hardness ≤9 Such as calcite, dolomite, chalk, limestone, carbon black, kaolin, bentonite, talc, mica, magnesite, barite, gypsum, graphite, fluorite, phosphate Dolomite micro powder grinding mill is the equipment used to process ore such as Dolomite Micro Powder Grinding Mill2020年1月3日 Iron ores obtained from different sources differ in their chemical and physical properties These variations make the process of grinding a difficult task The work carried out in this context focuses on three different samples of iron ore, viz, high silica high alumina, low silica high alumina, and low silica low alumina The grinding process for all the three iron ores is Estimation of Grinding Time for Desired Particle Size Distribution Grinding Mills: Ball Mill Rod Mill Design PartsCommon types of grinding mills include Ball Mills and Rod Mills This includes all rotating mills with heavy grinding media loads This article focuses on ball and rod mills excluding SAG and AG Grinding Mills 911Metallurgist
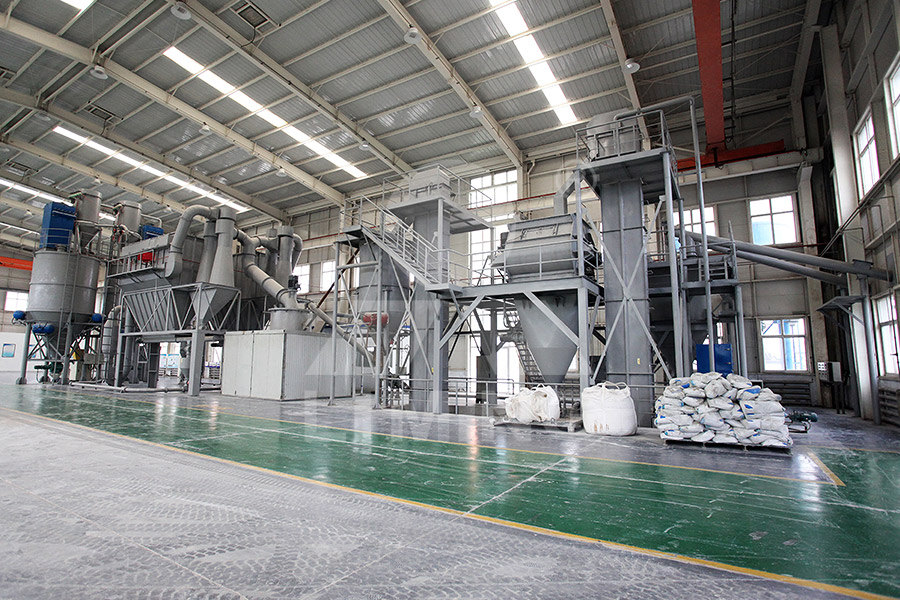
Understanding the SAG Mill in Copper Ore Mining
The Autogenous Mill, also known as AG Mill, is a type of grinding mill used in the mining industry This machine uses ore and rock itself as grinding media to perform its job Unlike other types of mills that use steel balls or rods for CLUM series of ultrafine gypsum powder vertical grinding mills are a new type of ultrafine industrial ore grinding equipment that integrates grinding, grading, powder collection and conveying +17CLUM Ultrafine Vertical Grinding Mill2015年4月9日 The mill is normally used for grinding of ores Lining of the cylinder plays very important role It protects the mill from abrasions and at the same time it helps in lifting of the material from the bottom of cylinder The types of lining are Grinding Mills and Their Types – IspatGuruRequest PDF On Mar 15, 2015, Mathis Reichert and others published Research of iron ore grinding in a verticalrollermill Find, read and cite all the research you need on ResearchGateResearch of iron ore grinding in a verticalrollermill
.jpg)
Reaction Kinetics of magnesite ore in dilute ethanoic acid
2016年7月1日 Effect of magnesite ore particle size on leaching process (3 M acetic acid, 60°C and 300 rpm) Download scientific diagram RosinRammler diagram of particle size distributions of talc, magnesite and talcmagnesite ore after two grinding stages and milling from publication: Collectorless RosinRammler diagram of particle size distributions of talc, magnesite 2016年5月10日 In the handling of wet, sticky ores such as encountered in tropical areas having distinct dry and rainy seasons, the crushing plant is a section of the mill which must be planned very carefully Unless this is done, crushing becomes a constant source of trouble resulting in lost production and high milling cost In some areas rainfall is high for prolonged periodsCrushing and Grinding Wet Sticky Ore 911Metallurgist2018年2月1日 In another study to investigate ball size distribution on ball mill efficiency by Hlabangana et al [50] using the attainable region technique on a silica ore by dry milling, a threeball mix of Effect of ball and feed particle size distribution on the milling
.jpg)
Factors affecting ores grinding performance in ball mills
Speed also plays a role in ore grinding; too high of a speed can cause damage to the mill gears and other components, while too low of a speed can cause excessive wear on these same components It is important to find a balance between these two variables in order to achieve optimal grinding performance2020年6月3日 The design of such grinding mills is extremely critical, requiring sophisticated software tools, proprietary calculation worksheets, and experienced technical engineers and drafters This blog will review how the mill design How grinding mill design changed over the last 30 years2016年6月3日 IsaMills, Tower Mill and Verti Mill Ultrafine Grinding in a Tower Mill The Tower Mill is a vertical “stirred” ball/pebble mill recently introduced in the Western Hemisphere This device offers a significant power savings on wet Tower Mill Operating Work Index 911Metallurgist2016年1月1日 In wet grinding practice, highstress abrasion occurs over a small region when ore particles are trapped between the grinding balls and the mill liner, and the load is sufficient to fracture A comparison of wear rates of ball mill grinding media
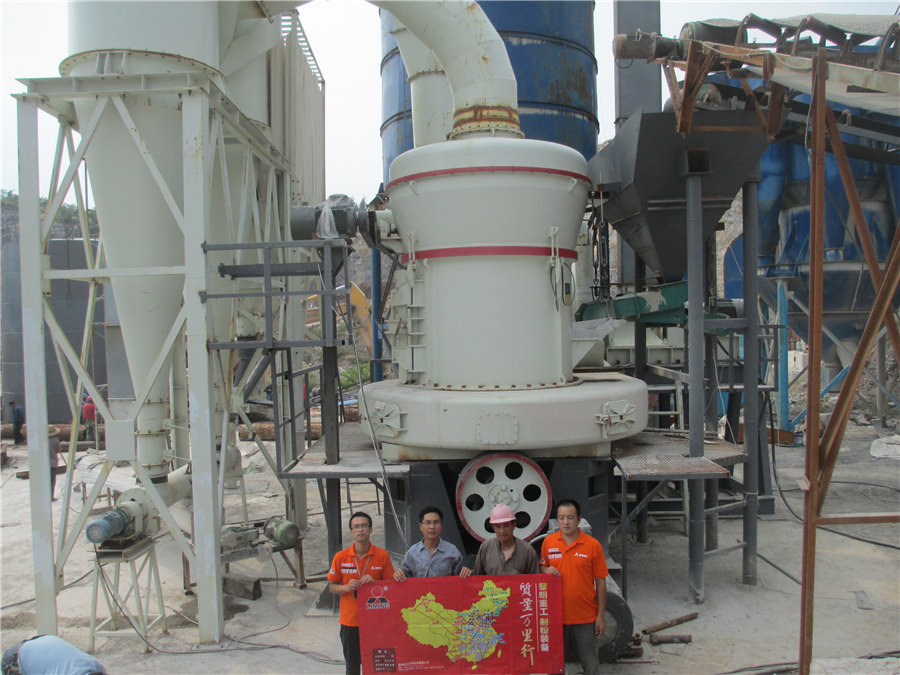
HGM Ultra Fine Grinding Mill
HGM Ultra Fine Grinding Mill Maxing Feeding Size: 20 mm Ouput Size: 745 micron (2002500 mesh) Capacity: 0555 t/h Applicable materials: Calcium carbonate The results show that the optimum process parameters for the vertical roller mill are as follows: a grinding fineness of 816wt% of particles less than 0074 mm, a dodecyl amine (DDA) dosage in magnesite reverse flotation of 100 gt −1 , and dosages of Na 2 CO 3 , (NaPO 3 ) 6 , and NaOL in the positive flotation section of 1000, 100, and 1000 gt −1 , respectivelyResearch on new beneficiation process of lowgrade magnesite Grinding Mill, Raymond Mill, Ball Mill manufacturer / supplier in China, offering Big Capacity Stone Quarry Plant Used Calcium Carbonate Gypsum Limestone Quartz Graphite Calcite Feldspar Fluorite Impact Crusher, Hot Sale Dolomite Pyrophyllite Mineral Phosphorite Marble Perlite Sepiolite Silica Powder Jaw Crusher Price with High Efficient Capacity, Low Cost Calcite Raymond mill; Superfine grinding mill; Vertical roller mill A crushing plant delivered ore to a wet grinding mill for further size reduction The size of crushed ore (F 80) was 40 mm and the SG 28 t/m 3 The work index of the ore was determined as 122 kWh/t A wet ball mill 1 m × 1 m was chosen to grind the ore down to 200 micronsGrinding Mill an overview ScienceDirect Topics
.jpg)
What is the best for grinding silica sand ball mill or vertical mill
silica sand ball mill is the key equipment for grinding after the crushing process, which is widely used in the manufacture industries, such as cement, silicate, new building material, refractory material, fertilizer, ferrous metal, nonferrous metal and glass ceramics and can be used for the dry and wet grinding for all kinds of ores and other grindable materials2023年4月23日 grinding media in a grinding mill with about 2630 wt% chrome by Chen et al [37] using a phosphate ore in a modified ball laboratory ball mill whose electrochemical potential could be controlled(PDF) Grinding Media in Ball MillsA Review ResearchGate