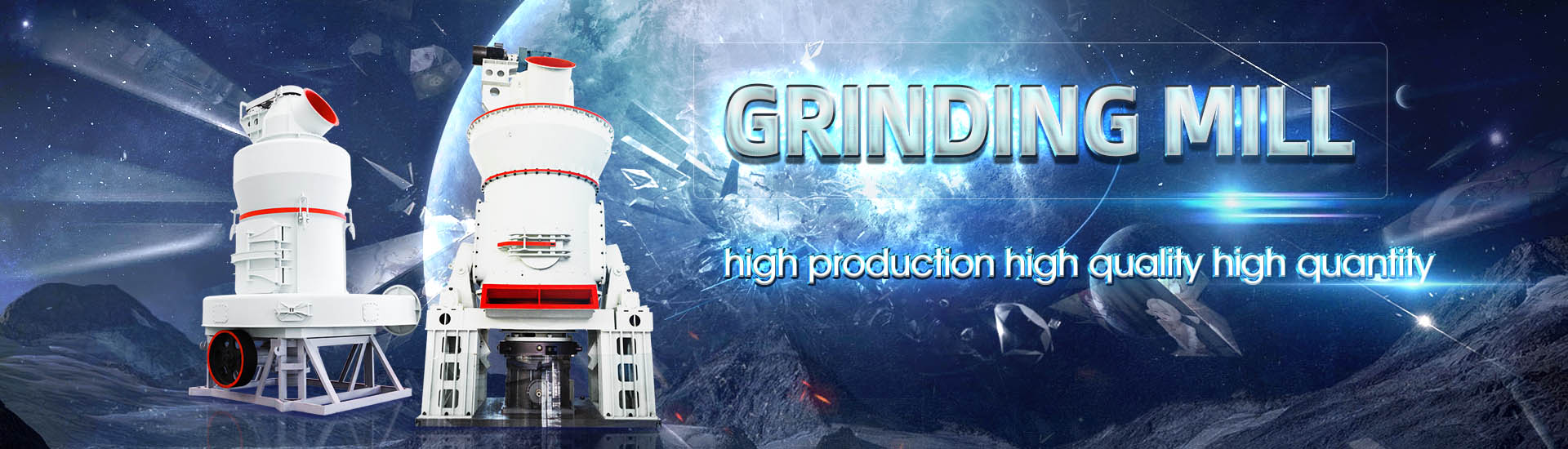
Quenching equipment for processing scrap steel slag
.jpg)
Processing and Reusing Technologies for Steelmaking Slag
3 Steelmaking Slag Processing Technology The iron/steel slag processing flow is schematically shown in Fig 2 Steelmaking slag is subjected to the following four processes: ① solidify and 2024年1月4日 We developed a process that enables simultaneous carbonation of steel slag, capture of flue gas carbon, and recovery of waste heat by utilizing lime kiln flue gas during the An Efficient Molten Steel Slag Gas Quenching Process: Integrating 2024年6月1日 The gas quenching granulation process, cooling rate of about 600℃/s, achieves efficient treatment of steelmaking slag while effectively reducing the free CaO content, which is Phase development in steelmaking slags during a gas quenching 2019年5月23日 When steel slag is slowly cooled or quenched, the slag and residual steel are bonded or packed together, which makes recycling of steel scrap via magnetic separation and Comprehensive Utilization Technology of Steel Slag

A review of waste heat recovery technologies towards molten slag
2013年12月1日 Molten slag exhausted with critically high temperature of about 1450–1550 °C is a potential resource of energy and raw materials Water quenching is a traditional heat 2020年7月16日 According to the current development of steel slag abrasives, an experimental device for gas quenching was developed to produce gasquenched steel slag abrasives The Structure characterization and grinding performance of gas 2024年9月15日 To address these challenges, a waste heat recovery process route has been developed for molten steel slag, which integrates CO 2 capture and fixation as well as efficient An efficient molten steel slag gas quenching process: Integrating With GK’s Dry Slag System, slag is conveyed, cooled indirectly, and transformed into a semisolid pancake slag The patented indirect cooling trough technology of the Dry Slag Cooling Conveyor means slag can immediately be containerized Dry / Wet Slag Cooling Conveyor General Kinematics
.jpg)
The steel production transformation process in
The main challenge of the steel industry for the next decade is the steel production transformation process, starting in Europe The CO 2 intensive blast furnace/basic oxygen furnace (BOF) route will be substituted by a combination 2021年8月5日 To solve the problem of difficult utilization of steel slag, the liquid steel slag was modified and the airquenching granulation process was carried out to make steel slag into a valueadded end product: airquenching granulated steel slag The granulated slag was tested to analyze the variation rule of slag properties under different modification conditions Based on Hightemperature modification and airquenching granulation of steel slag2005年5月31日 Request PDF Steel Slag — Its Production, Processing, Characteristics, and Cementitious Properties Steel slag is a byproduct from either the conversion of iron to steel in a basic oxygen Steel Slag — Its Production, Processing, Characteristics, and 2024年3月12日 Leading Technology: We have advanced steel slag processing technology and equipment that can efficiently and environmentally recycle steel slag Rich Experience: With over 40 years of experience in steel slag processing and machinery manufacturing, we have provided professional solutions and services to numerous clients in the fieldSteel Slag Recycling: The Definitive Processing Solution
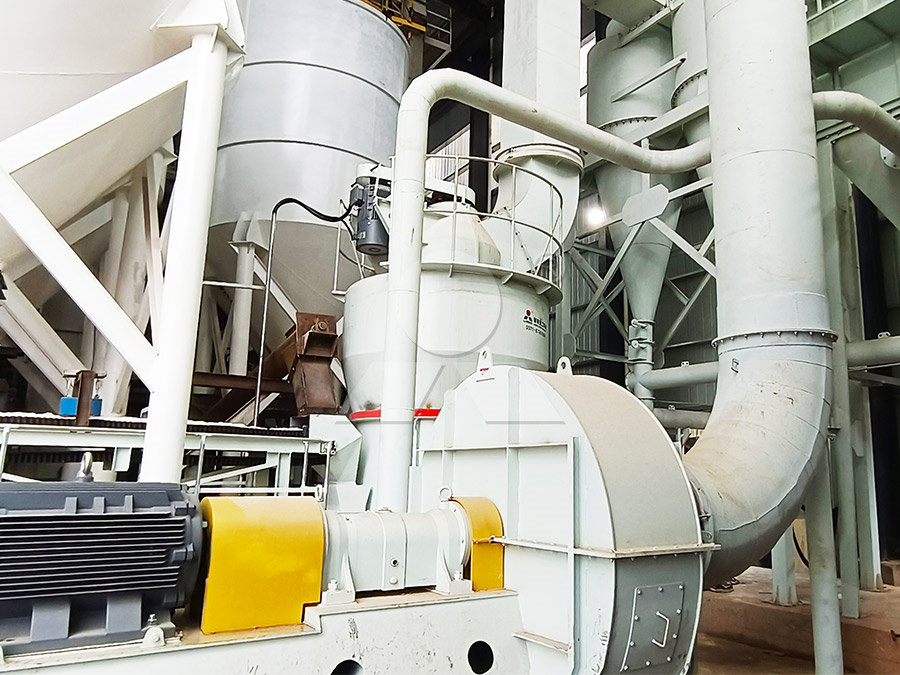
Pressurized steam aging process for steel slag ResearchGate
2011年1月1日 For the problems with volume expansion and disintegration, the hotstage slag treatment utilized in thyssenkrupp Stahl AG has been proved practically feasible; steam aging is also integrated in 2017年1月7日 Process and Equipment Design for the Dry Slag Granulation Technology: Proceedings of the International Conference on Environmental Science and Sustainable EnergyEdby ZhaoYang Dong January 2017 (PDF) Process and Equipment Design for the Dry Slag quenching slag is easy to explode, compared with the INBA method, the circulating water consumption is less, the power energy consumption is also lower, and the quality of the slag of water quenching slag is also relatively good However, due to the complex process, the large amount of equipment required for productionComprehensive utilisation of blast furnace slag Taylor Francis The main chemical compositions of steel slag are CaO, Fe2O3, SiO2, some MgO and the main phases are C3S, C2S and periclase, etc Because of its high alkalinity, it is difficult to form glassy phases in steel slag[5−6] Air quenching of steel slag is a process to use highpressure air to cool molten steel slag from hightemperatureComponent modification of steel slag in air quenching process
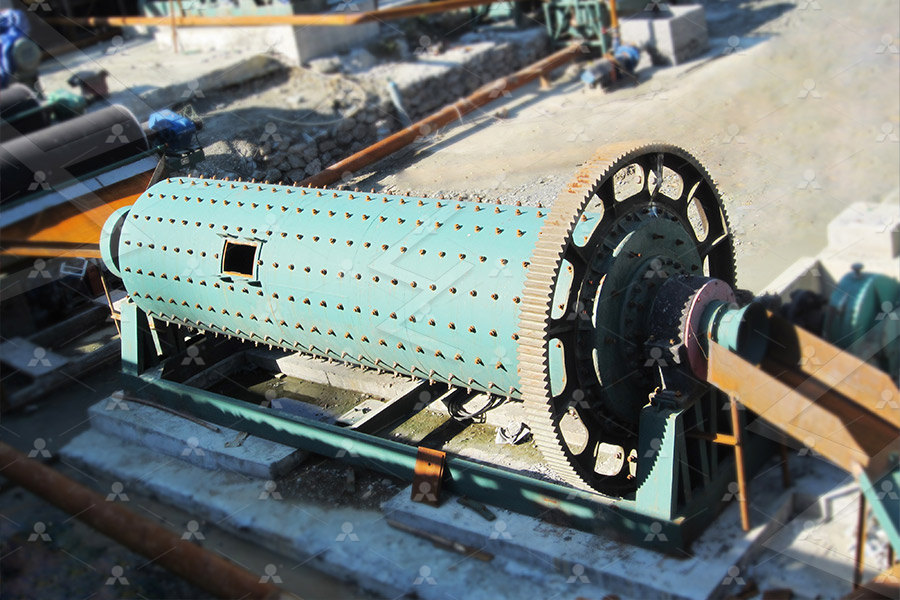
RESEARCH OVERVIEW ON RECOVERY OF WASTE HEAT FROM HIGH TEMPERATURE SLAG
waste heat recovery process of liquid slag into dry centrifugal granulation process and waste heat recovery process After dry centrifugal granulation, the temperature of blast furnace slag particles was about 900°C Then the particles entered the packed bed for heat transfer, resulting in hot air of 500600°C [5]2023年7月21日 Introduction China is the world's largest steel producer, with the China Iron and Steel Association estimating that the country's crude steel production in 2022 will be 935 million tonnes [Citation 1]Steel slag mainly refers to the blast furnace slag and converter slag produced in the process of iron making and steel making, and with the increase of steel production, the Comprehensive utilisation of blast furnace slag Taylor Francis 3 Steelmaking Slag Processing Technology The iron/steel slag processing flow is schematically shown in Fig 2 Steelmaking slag is subjected to the following four processes: ① solidify and cooling of the hot molten slag, ② crushing and magnetic separation treatment of the slag to recover the metal iron,Processing and Reusing Technologies for Steelmaking Slag2017年2月1日 Fe in the steel slag is usually found in the form of steel (Fe), iron oxides (FeO, Fe 2 O 3 , Fe 3 O 4 ) and ironbearing minerals, which can be separated from slag by applying mineral processing Optimization of magnetic separation process for iron recovery
.jpg)
Steel Scrap and Scrap Sorting and Preparation
2017年1月23日 As per the world steel association, the integrated steelmaking route, based on the blast furnace (BF) and basic oxygen furnace (BOF), uses 1,400 kg of iron ore, 800 kg of coal, 300 kg of limestone, and 120 kg of 2021年6月14日 Hightemperature molten steel slag is a large amount of industrial solid waste containing available heat energy and resources This paper introduces an efficient and comprehensive utilization process of hightemperature molten steel slag The waste heat energy in the hightemperature molten steel slag can be fully recovered through the threestage heat ThreeStage Method Energy–Mass Coupling HighEfficiency Utilization 2018年8月1日 Professional slag processing company: Layer pouring: Scrap, cement: Shanxi Antai Group: North China: Private: 12: 016: Selfinvestment: such as recycling metal by simply crushing and magnetic separation equipment melting process, steel slag treatment, and magnetic separation will affect the chemical composition, Steel slag in China: Treatment, recycling, and management2023年5月11日 In the heat recovery technology of molten slag granulation, gas quenching is one of the most promising and crucial technologies for highquality resource utilization This study performed numerical investigations on the slag granulation process through the realizable kepsilon model and volume of fluid methodology and gained deep insight into the breakup Numerical Simulation of the Slag Granulation Process in Gas Quenching
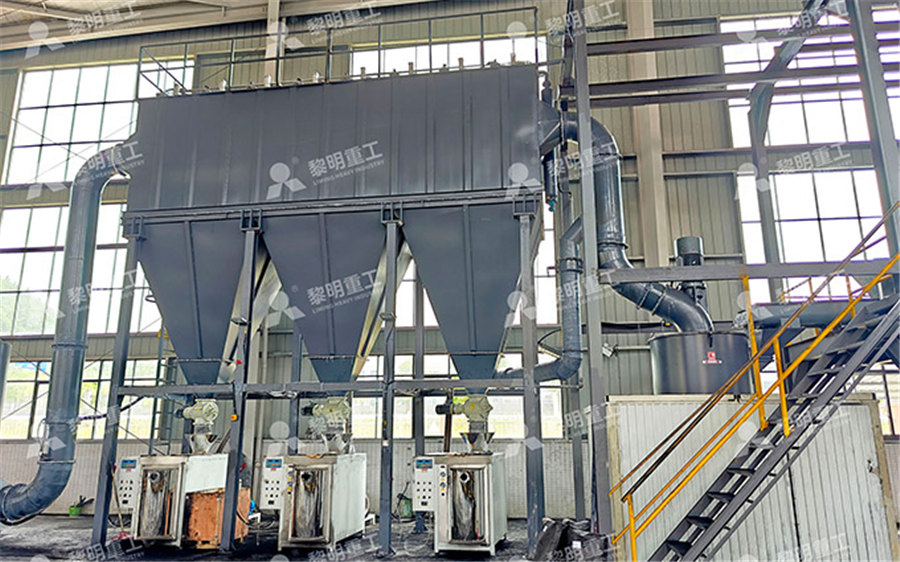
Process and Equipment Design for the Dry Slag Granulation
Process and Equipment Design for the Dry Slag Granulation Technology Abstract: The granulation of blast furnace (BF) slag with water quenching has many disadvantages, such as high water consumption and difficulty in heat recycling The dry granulation technology to treat the BF slag is very important The application of2005年2月1日 The importance of understanding slags, their reusability, their specific roles and improvements in functions to lead a significant reduction in slag volumes in iron and steel industry is discussed(PDF) Industrial uses of slag The use and reuse of iron and 2021年8月5日 To solve the problem of difficult utilization of steel slag, the liquid steel slag was modified and the airquenching granulation process was carried out to make steel slag into a valueadded end product: airquenching granulated steel slag The granulated slag was tested to analyze the variation rule of slag properties under different modification conditions Based on Hightemperature modification and airquenching granulation of steel slag2023年11月20日 Mineral process wastes, such as metallurgical slags nowadays, are of significant metals and materials resources in the circular economy The usability of ironmaking slag is well established; however, steel slag still needs to be utilized due to various physicochemical constraints In this context, we have reviewed the global steel slag A Review on Environmental Concerns and Technological
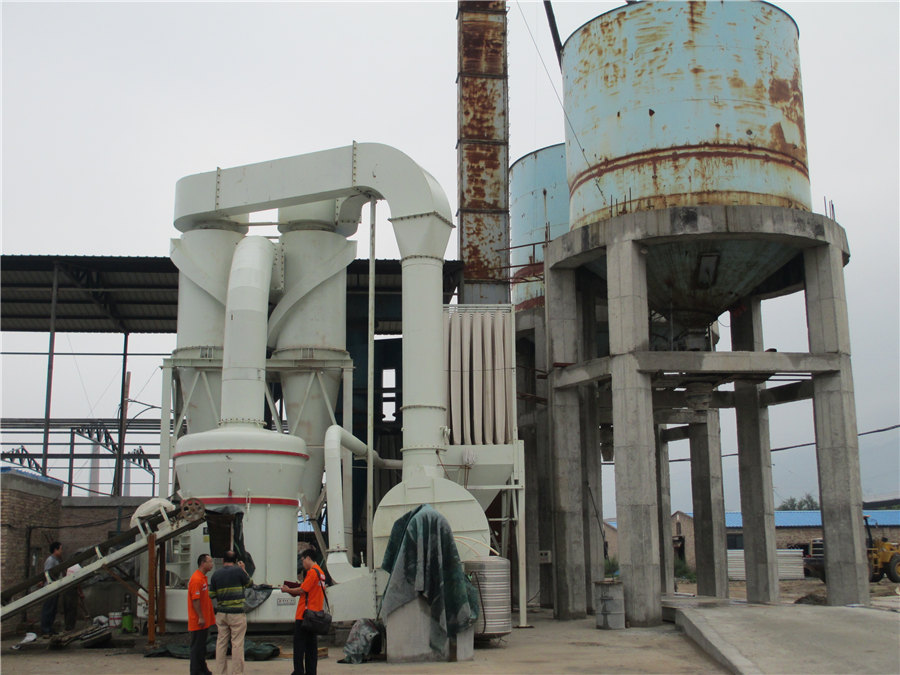
Phase development in steelmaking slags during a gas quenching
2024年6月1日 This method is considered to be able to establish the fastest cooling rate in the industry at present The average cooling rate of the slag in the hightemperature section (1500–1200℃) during the air quenching process can reach 520–670℃/s In contrast, gas quenching granulation produces slag particles less than 3 mm in size [20], [21]2006年9月26日 Steel slag has a lower silica content than blastfurnace slag and, hence, steel slag seldom vitrifies even when rapidly cooled Tossavainen et al [13] studied the effect of the cooling rate on the Characteristics of steel slag under different cooling conditionsThe invention relates to a gas quenching method for improving steel slag stability and recovering physical heat of molten steel slag, belonging to the environmental protection technical field of solid waste disposal, secondary resource recycling and the like in the metallurgical industry The technical scheme is as follows: utilizing CO in a large amount of coal gas generated by iron Gas quenching method for improving stability of steel slag and accidentally with other scrap metal in their EAF with a significant amount of the Cesium being expelled into the atmosphere and baghouse flue dust The airborne radioactive plume spread as far as Switzerland with several processors being contaminated after processing the steel plants’ radioactive slag and flue dustAn Early Warning System for Scrap Radioactivity
.jpg)
Analysis of blast furnace slag quenching dry granulation process
2007年5月1日 The process of granulation in blast furnace slag (BFS) by gas quenching can effectively recover the waste heat of BFS and improve the valueadded nature of the BFS byproductSteel Slag BOF slag, commonly known as steel slag is another waste from Iron Steel Industry It has shown potential for use as a raw mix component up to 10% in the manufacture of cement clinker Steel slag can also replace granulated blast furnace slag up to 10% in the manufacture of Portland Slag Cement Steel slags are produced at steel meltingSLAG IRON AND STEEL Indian Minerals Yearbook 2017 IBM2000年10月9日 1 Productivity of the unit for deformationfree hardening of races is limited by cooling rate of the quenching agent (industrial oil I20A) With a requirement for obtaining a productivity of PRACTICAL APPLICATION OF INTENSIVE QUENCHING PROCESS FOR STEEL 42 Air blast method High speed and high pressure air plays a pivotal role to discharge the molten slag with a rapid cooling in this process, along with absorbing the sensible heat [4]A Review of Granulation Process for Blast Furnace Slag
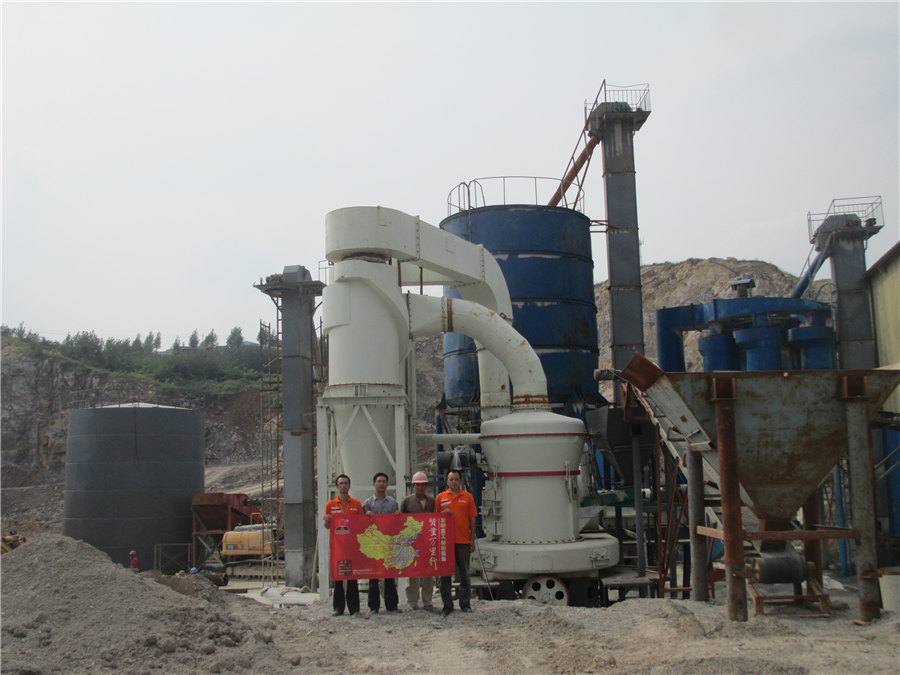
42CrMo4 Alloy Steel Manufacturing And Processing
Highquality alloy steel 42CrMo4 is an important material widely used in mechanical manufacturing and engineering fields, equivalent to AISI 4140 / JIS SCM440 42CrMo4 alloy steel can obtain excellent performance and quality through appropriate manufacturing and processing technology, making it suitable for more application scenariosnonmetallic steel slag abrasives and proposed a method for preparing these abrasives According to the current development of steel slag abrasives, an experimental device for gas quenching was developed to produce gasquenched steel slag abrasives The equipment directly breaks hot steel slag into particles by nitrogen gas owStructure characterization and grinding performance of gas 2020年9月14日 Molten slag is broken up by supersonic air into droplets through the air quenching dry slag granulation technique The breakup process of blast furnace slag directly determines the droplet diameter and the waste heat Numerical investigation of breakup process of molten 2002年4月1日 The slag foaming process is currently applied to some equipment for steel production [ie, electric arc furnace (EAF), basic oxygen furnace (BOF), etc] aiming to save energy, improve Stainless steel slag fundamentals: From furnace to tundish
.jpg)
Slag Recycling and Metal Recovery MEKA
As a result of growing environmental awareness, steel slag is now highly regarded as a recycled material that can reduce environmental impact due to its resourceconservation and energysaving properties MEKA is designing and 2021年3月8日 [vcrow][vccolumn][vccolumntext] Hot stuffing; Process characteristics and process: use the sensible heat of high temperature liquid slag to sprinkle water to produce physical and mechanical effects and the hydrolysis of free calcium oxide to fragment the slag Advantages: simple process, suitable for processing high basicity steel slag, steel slag has Advantages and disadvantages of steel slag treatment process 11ügranulated slag Figure 2 INBA process 4 Dry granulation process On the blast furnace slag treatment technology, for a long time, water quenching process has token the leading position However, there are many defects of waterquenching slag method, which can be roughly concluded as follow: a mass of sensible heat unrecovered, highA Review of Granulation Process for Blast Furnace Slag Semantic 2024年9月15日 Steel slag carbon fixation can be categorized into direct carbonation (dry carbonation, wet carbonation) and indirect carbonation (pH fluctuation, microbial carbonation)(Huang et al, 2024, Wang et al, 2021)Tian et al employed direct gas carbonation as a method to achieve a maximum carbonation conversion of 555 % and CO 2 sequestration An efficient molten steel slag gas quenching process: Integrating

Tata Steel Annual Report 20222023
Tata Steel’s firstofitskind scrap collection and processing unit at Rohtak was commissioned in 2020 and the plant clocked c 280 KT of scrap dispatch in FY202223 The Company's Steel Scrap Recycling Business aims to replicate the Rohtak model across India by setting up 810 fully mechanised scrap processing facilities, with a combined capacity of 5 MnTPA by 2030Request PDF On Jun 1, 2016, Hong Wang and others published Energy–environment–economy evaluations of commercial scale systems for blast furnace slag treatment: Dry slag granulation vs water Energy–environment–economy evaluations of commercial scale 2023年5月4日 The temperature of molten steel slag produced by the steelmaking process is 1500°c~1700°c, and the total amount of energy contained is considerableDevelopment of waste heat recovery technology from steel slag11ügranulated slag Figure 2 INBA process 4 Dry granulation process On the blast furnace slag treatment technology, for a long time, water quenching process has token the leading position However, there are many defects of waterquenching slag method, which can be roughly concluded as follow: a mass of sensible heat unrecovered, highA Review of Granulation Process for Blast Furnace Slag